煤焦油加氢处理技术生产清洁轻质燃料油项目可行性研究报告.docx
《煤焦油加氢处理技术生产清洁轻质燃料油项目可行性研究报告.docx》由会员分享,可在线阅读,更多相关《煤焦油加氢处理技术生产清洁轻质燃料油项目可行性研究报告.docx(87页珍藏版)》请在冰豆网上搜索。
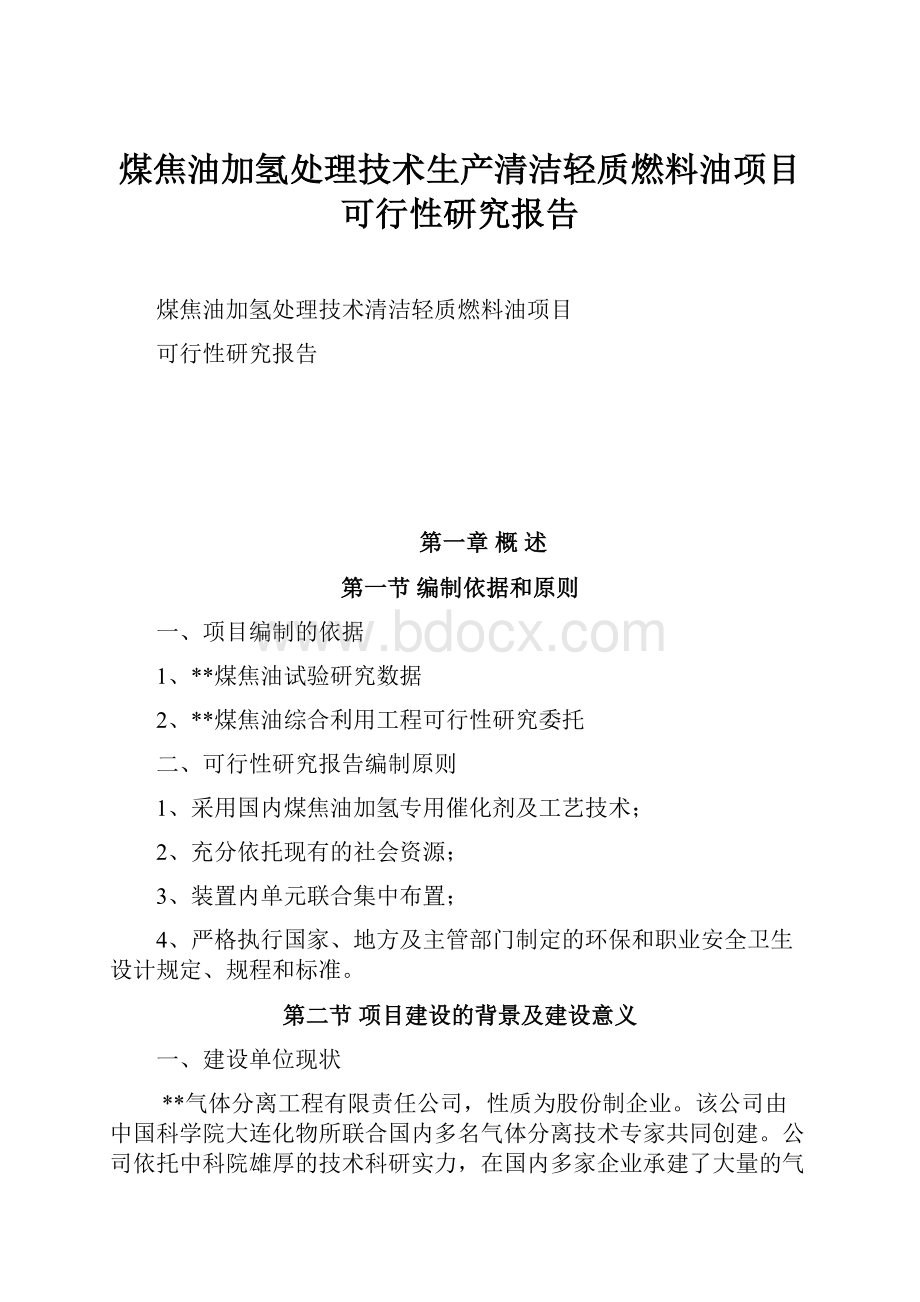
煤焦油加氢处理技术生产清洁轻质燃料油项目可行性研究报告
煤焦油加氢处理技术清洁轻质燃料油项目
可行性研究报告
第一章概述
第一节编制依据和原则
一、项目编制的依据
1、**煤焦油试验研究数据
2、**煤焦油综合利用工程可行性研究委托
二、可行性研究报告编制原则
1、采用国内煤焦油加氢专用催化剂及工艺技术;
2、充分依托现有的社会资源;
3、装置内单元联合集中布置;
4、严格执行国家、地方及主管部门制定的环保和职业安全卫生设计规定、规程和标准。
第二节项目建设的背景及建设意义
一、建设单位现状
**气体分离工程有限责任公司,性质为股份制企业。
该公司由中国科学院大连化物所联合国内多名气体分离技术专家共同创建。
公司依托中科院雄厚的技术科研实力,在国内多家企业承建了大量的气体分离装置。
本公司目前拥有高级职称员工20人,中级职称员工35人。
属于大连市高科技发展型企业。
公司响应国家大力提倡的环保及能源政策,针对煤焦油加氢制油品项目,进行了大量的调研工作,在优先考虑解决企业环保问题的情况下,同时解决了国家能源短缺的难题。
经过周密详细的调研之后,选定了上海博申工程技术有限公司作为合作伙伴,共同开发、设计及建设煤焦油加氢制油品的项目。
二、项目建设的背景及建设意义
㈠、项目建设的必要性
1、工业燃料油市场分析:
优质燃料油作为工业燃料是一种理想的汽柴油替代品,广泛用于电厂、电站、冶炼、锻压、锻造等工业窑炉进行燃烧。
据有关部门统计,全国仅用于工业窑炉使用的柴油就达2200万吨/年以上。
并且,随着环保要求的不断提高,燃煤炉窑将逐渐淘汰,同时工业燃油数量将逐步增加。
利用价格很低的原料油废油,生产优质工业燃油,就地销售或销向周边地区,是具有非常现实经济意义的。
2、煤焦油品质现状概述
本项目原料油主要来源于**市及周边地区炼焦过程中的副产煤焦油,年产量为20万吨/年左右,其它部分原料外购。
厂方提供的原料油性质见表2-1-1。
从表2-1-1表可以看出,焦炉副产燃料油硫含量高、酸度高、胶质含量高、安定性差。
如不进行改质(降低其硫含量、提高其安定性),无法作为优质燃油出厂,因此,必须对上述副产燃料油进行改质。
㈡、项目建设意义
建设本项目的意义在于:
1、焦炉副产煤焦油(即劣质燃料油),采用高压加氢改质技术,降低其硫含量、提高其安定性、并提高其十六烷值,满足优质燃料油指标要求。
根除现有工艺的弊端,搞好区域环保,合理利用资源,提高企业的经济效益。
2、利于发挥已有销售市场优势和生产管理技术力量优势
现有煤焦油作为劣质燃料油产品已进行过长期销售,已存在许多稳定用户。
3、我国优质燃料油短缺,燃料油进口数量逐年递增。
第三节项目设计范围
该项目建设内容包括以下部分:
1、装置界区内工程包括10万吨/年煤焦油加氢改质单元、7000Nm3/h净焦炉气氢提纯单元、成品油罐区单元和公用工程设施。
10万吨/年煤焦油加氢改质单元、7000Nm3/h净焦炉气氢提纯单元联合布置,界内设中心控制室、车间办公室、配电室、分析化验室等。
2、装置界区外配套的放空火炬及公用工程,由建设单位负责。
第四节研究结果
一、项目概况
该项目采用上海博申工程技术有限公司的成套煤焦油加氢工艺及催化剂,以焦炉副产煤焦油为原料,生产优质燃料油。
充分考虑热量合理回收,降低装置能耗。
为保证装置运转“安、稳、长、满、优”,关键设备设计充分考虑装置原料特点。
装置的氢气由净焦炉气氢提纯单元生产。
二、主要工艺、技术经济指标见表1-4-1
表1-4-1主要工艺技术指标
序号
项目
单位
指标
备注
1
主要原材料
(1)原料油
(2)净焦炉气
(3)保护剂
(4)加氢改质催化剂
(5)缓蚀剂
万吨/年
104Nm3/a
吨/
m3
吨/年
13.00
12800
2
25
2
(加氢进料按77%计)
(氢气含量按60%计算)
一次装入量,寿命1年
一次装入量,寿命3年
2
主要产品
石脑油
燃料油
沥青
万吨/年
万吨/年
万吨/年
1.742
8.32
3.000
(含大于360℃未转化油)
3
4
5
6
消耗指标
燃料气
循环水
电
净化风
脱盐水
非净化风
氮气
蒸汽
能耗指标
装置总占地面积
定员
104Nm3/a
104t/a
104kwh/a
104Nm3/a
104t/a
104Nm3/a
104Nm3/a
104t/a
MJ/t原料
m2
人
296
400.0
2427.2
648
2.88
3200.0
5600.0
8.0
3845
50000
30
1.0MPa
7
总投资
万元
15849
8
建设投资
万元
14000
9
建设期利息
万元
275
10
销售收入
万元
32886
生产期内年均
11
总成本
万元
17307
生产期内年均
12
流转税及附加
万元
2774
生产期内年均
13
利润总额
万元
12804
生产期内年均
14
所得税
万元
3959
生产期内年均
15
税后利润
万元
8845
生产期内年均
16
投资利税率
%
98.3
17
投资利润率
%
80.79
18
借款偿还期
年
3.03
含1.5年建设期
19
财务内部收益率
%
49.4
所得税后
20
净现值(I=12%)
万元
41896
所得税后
21
投资回收期(所得税后)
年
3.32
含建设期1.5年
三、结论
㈠本项目采用上海博申工程技术有限公司的成套煤焦油加氢工艺和成熟的工程技术,投资合理,可确保装置“安、稳、长、满、优”运转。
装置环保、职业安全卫生及消防等设施的设计符合标准规范。
本项目在技术上是可靠的。
㈡本项目总投资15849万元(含各种费用),其中建设投资14000万元。
年均销售收入32886万元,年均总成本费用17307万元,年均所得税后利润8845万元,投资利润率为80.79%,静态投资回收期为3.32年(含建设期1.5年)。
各项经济评价指标远好于行业基准值,项目经济效益较好,并具有一定抗风险能力,在经济上是完全可行的。
㈢本项目的建设不仅可以解决副产劣质煤焦油污染问题,同时也可解决部分国内油品紧张。
总之,本装置的建设是必要的,应加快建设速度。
第二章原料来源、生产规模、产品方案
第一节原料来源及生产规模
一、原料来源
煤焦油原料主要来自**等地焦化厂的焦炉副产煤焦油13万吨/年作为本装置原料(加氢进料10万吨/年),其性质见表2-1-1。
二、生产规模:
公称规模:
10万吨/年;实际加工量10万吨/年;最大加工量12万吨/年。
加氢装置实际处理煤焦油馏分10万吨/年。
三、年开工时数8000小时。
表2-1-1原料油全馏份性质表
项目
全馏分原料油
密度(20℃)/g·cm-3
1.1380
残炭,m%
19.59
S,m%
0.26
N,m%
1.13
C,m%
86.77
H,m%
6.44
组成,m%
烷烃
0
环烷烃
0
芳烃
87.7
胶质及其他
12.3
金属含量μg·g-1
其中:
Cu
0.20
Ca
22.75
Mg
2.67
Ni
0.78
V
0.01
Fe
11.2
Na
0.95
∑
38.56
第二节产品方案
根据**焦炉焦油分析数据,本装置以焦炉焦油为原料,主要产品石脑油(C5~177℃)硫、氮、烯烃含量及其它杂质均很低,可作为石脑油出厂;燃料油(>177℃)安定性好、硫含量低,可作为优质燃料油出厂;煤沥青作为沥青调和组分出厂或调和重质燃料油。
第三节产品市场分析
优质燃料油作为工业燃料是一种理想的汽柴油替代品,广泛用于电厂、电站、冶炼、锻压、锻造等工业窑炉进行燃烧。
据有关部门统计,全国仅用于工业窑炉使用的柴油达2200万吨/年以上。
并且,随着环保要求的不断提高,燃煤炉窑将逐渐淘汰,同时工业燃油数量将逐步增加。
根据周边地区市场调查,仅本地区工业燃油即达20万吨/年。
本项目投产后,10万吨/年煤焦油加氢改质单元,生产的的8.32万吨/年轻质燃料油及1.742万吨/年石脑油产品,其产量对当地及周边市场需求而言,可实现当地销售,不存在市场问题。
10万吨/年煤焦油加氢改质单元原料预分馏塔底重油作为沥青。
10万吨/年煤焦油加氢改质单元副产气体可作装置燃料气使用,属于公司内部物料,不存在市场问题。
7000Nm3/h净焦炉气氢提纯单元尾气也可以作为装置自用燃料。
第三章10万吨/年煤焦油加氢改质单元工艺技术方案
第一节工艺技术方案选择
一、确定技术方案的原则
1、采用上海博申工程技术有限公司提供的成套工艺技术。
2、采用配套的工艺技术和成熟、可靠、先进的工程技术,确保装置设计的整体合理性、先进性和长周期安全稳定运转。
3、合理用能,有效降低装置的能耗,合理回收装置余热,达到合理的先进水平。
4、提高环保水平,加强安全措施,环保设施与主体工程同时设计、同时施工、同时投产。
5、在保证性能可靠的前提下,降低装置投资,最大限度实现设备国产化。
6、提高装置操作灵活性,增强对市场的适应能力。
二、原料加工目的
焦炉副产焦油的汽、柴油馏份含有大量的烯烃、多环芳烃等不饱和烃及硫、氮化合物,酸度高、胶质含量高。
采用加氢改质工艺,可完成脱硫、不饱和烃饱和、脱氮反应、芳烃饱和,达到改善其安定性、降低硫含量和降低芳烃含量的目的,获得优质石脑油和燃料油。
三、国内外相近加氢技术现状
目前国内煤焦油加氢处理装置仅有上海博申提供成套技术而建成的一套5万吨/年装置。
国外相关的煤焦油加工技术未见报道,但日本存在煤沥青加氢生产炭材料的报道和相关装置。
四、该装置使用的加氢工艺技术主要操作条件
根据煤焦油分析数据,该装置反应器主要操作条件如下:
表3-1-1工艺条件
反应总压/MPa
15.7
保护剂体积空速/h-1
0.75
保护剂平均反应温度/℃
345
主精制剂体积空速/h-1
0.3
主精制剂平均反应温度/℃
375
精制油硫含量/gg-1
179
精制油氮含量/gg-1
954
*注:
采用专用焦油加氢催化剂。
表3-1-2<177℃汽油馏分性质
S/gg-1
15.0
N/gg-1
30.5
组成分析/%
烷烃
2.6
环烷烃
81.4
芳烃
16.0
芳潜/%
92.75
表3-1-3177~360℃柴油馏分性质
密度(20℃)/g·cm-3
0.9621
馏程/℃
IBP/10%
175/198
30%/50%
231/264
70%/90%
302/339
95%/EBP
341/359
粘度(20℃)/mm2·s-1
4.549
凝点/℃
<-50
残炭,%
<0.01
闪点/℃
83
十六烷值(计算值)
23.0
S/gg-1
37
N/gg-1
360
本可研按上海博申的煤焦油加氢专用催化剂考虑。
五、工艺流程选择
热分流程与冷分流程:
由于装置规模较小,热分流程较冷分流程流程复杂、投资高、不便操作,故选用冷分流程。
循环氢脱硫:
加氢装置原料氮含量7132PPm,硫含量4369PPm,为氮多硫少的情况,循环氢硫化氢含量很低,不必设置投资昂贵的循环氢脱硫系统。
分馏塔系统:
采用“分馏塔+稳定塔”流程
分馏塔设置重沸炉,使分馏塔具备精馏段和提馏段,实现汽油与柴油的清晰分割,柴油收率高,与蒸汽汽提操作方式相比,可避免柴油雾浊问题,并因减少水存在量大大减弱或避免了分馏塔顶系统和稳定塔顶系统有液态水存在位置的湿硫化氢腐蚀,利于保证分馏部分的“安、稳、长、满、优”操作。
主要核心工艺条件
装置生产灵活性和可靠性的核心在于反应空速的控制及原料芳烃含量的控制。
装置设计基础数据
试验提供原料基础数据,经优化试验后才能确定完整的装置工程设计基础数据。
六、主要操作条件
根据建设单位所提供的原料油分析数据及对产品的要求,装置的主要操作参数见表3-1-4。
柴油改质目标是加氢柴油十六烷值达到33以上。
表3-1-4精制方案模拟计算的工艺条件
催化剂
专用催化剂
反应器入口氢分压MPa
15.7
进料量104t/a
10
催化剂床层个数
3
催化剂装填比例
第一床层
第二床层
第三床层
10%
35%
55%
主剂体积空速h-1
0.30
反应温度℃
催化剂床层平均温度℃
总温升℃
初期
340
125
末期
385
121
催化剂运转周期,年
催化剂总寿命,年
1
3
3、分馏塔操作条件
T1原料预分馏塔
塔顶压力MPaG:
0.05
塔顶温度℃:
120
塔底温度℃:
180
汽提蒸汽t/h:
0.5
T2原料预分馏塔
塔顶压力kPaG:
1.0
塔顶温度℃:
180
塔底温度℃:
360
T3分馏塔
塔顶压力MPaG:
0.35
塔顶温度℃:
178
塔底温度℃:
310
塔顶冷却负荷KW:
-523
塔顶冷却负荷KW:
264
T4稳定塔
塔顶压力MPaG:
0.80
塔顶温度℃:
120
塔底温度℃:
217
塔顶冷却负荷MMKal/h:
-187
塔顶冷却负荷MMKal/h:
255
七、工程技术主要特点
1、反应部分采用炉前混氢、冷高分流程。
2、为尽量减少换热器结垢和防止反应器顶部催化剂床层堵塞,以及提高换热器传热效率和延长运转周期,要求罐区原料油储罐采用惰性气体保护。
原料油进装置经过滤器(反冲洗介质为自身原料油),脱除大于25微米的固体杂质颗粒。
3、反应进料加热炉采用纯辐射型圆筒炉。
4、精制柴油高于100℃以上热量用于加热稳定塔重沸液和低分油。
5、催化剂采用分级装填技术,有效降低反应器的压降,降低床层温差,提高催化剂效率。
6、高压换热器采用混合原料,提高换热效率,减少换热面积。
7、采用新型加氢反应器分布器技术,更均匀的分散物流,使催化剂床层的径向温差更小。
8、高分液位控制采用高低液位开关方式,安全可靠,准确性高。
9、催化剂预硫化采用湿法硫化方法。
10、正常操作反应器入口温度通过调节换热器操作来实现,第二、第三反应器床层入口温度通过调节急冷氢量来控制。
11、采用三相(油、气、水)分离的立式冷高压分离器。
12、催化剂再生采用器外再生方式。
13、分馏部分采用“分馏+稳定”流程,分馏塔按设重沸炉方式操作。
第二节产品的主要技术规格
产品性质
表3-2-1<177℃汽油馏分性质
S/gg-1
15.0
N/gg-1
30.5
组成分析/%
烷烃
2.6
环烷烃
81.4
芳烃
16.0
芳潜/%
92.75
表3-2-2177~360℃柴油馏分性质
密度(20℃)/g·cm-3
0.9621
馏程/℃
IBP/10%
175/198
30%/50%
231/264
70%/90%
302/339
95%/EBP
341/359
粘度(20℃)/mm2·s-1
4.549
凝点/℃
<-50
残炭,%
<0.01
闪点/℃
83
十六烷值(计算值)
23.0
S/gg-1
37
N/gg-1
360
第四节物料平衡
表3-3-110万吨/年煤焦油加氢改质单元物料平衡
wt%
万吨/年
t/h
入方
原料油
100
10
12.5
化学氢
6.31
0.631
0.789
小计
106.31
10.631
13.289
出方
H2S
0.25
0.025
0.031
NH3
1.25
0.125
0.156
H2O
2.5
0.25
0.313
C1
0.12
0.012
0.015
C2
0.09
0.009
0.011
C3
0.62
0.062
0.078
iC4
0.5
0.05
0.063
C4
0.36
0.036
0.045
石脑油
17.42
1.742
2.177
轻质燃料油
83.20
8.32
10.40
小计
106.31
10.631
13.289
第四节工艺流程简述
㈠、生产流程简述
装置主要包括原料预分馏部分(脱水和切尾)、反应部分和分馏部分。
1、原料预分馏部分
从罐区来的原料油经原料油过滤器除去25的固体颗粒,与预分馏塔顶汽换热升温后,与预分馏塔中段回流液换热升温,然后与预分馏塔底重油换热升温,最后经预分馏塔进料加热炉加热至~180℃进入原料油预分馏塔(脱水),塔顶汽经冷凝后进入预分馏塔顶回流罐并分离为汽油和含油污水,一部分汽油作塔顶回流使用,一部分汽油作加氢单元原料使用;预分馏塔(脱水)的拔头油由塔底排出,再经过换热和加热炉加热达到~360℃后进入预分馏塔(切尾),预分馏塔(切尾)底重油,作为沥青出装置,而其他馏出馏分混合后作加氢单元原料使用。
2、反应部分
经过预处理后的煤焦油进入加氢原料油缓冲罐,原料油缓冲罐用燃料气气封。
自原料油缓冲罐来的原料油经加氢进料泵增压后,在流量控制下与混合氢混合,经反应流出物/反应进料换热器换热后,然后经反应进料加热炉加热至反应所需温度,进入加氢改质反应器。
装置共有三台反应器,各设一个催化剂床层,反应器间设有注急冷氢设施。
自反应器出来的反应流出物经反应流出物/反应进料换热器、反应流出物/低分油换热器、反应流出物/反应进料换热器依次与反应进料、低分油、反应进料换热,然后经反应流出物空冷器及水冷器冷却至45℃,进入高压分离器。
为了防止反应流出物中的铵盐在低温部位析出,通过注水泵将冲洗水注到反应流出物空冷器上游侧的管道中。
冷却后的反应流出物在高压分离器中进行油、气、水三相分离。
高分气(循环氢)经循环氢压缩机入口分液罐分液后,进入循环氢压缩机升压,然后分两路:
一路作为急冷氢进反应器;一路与来自新氢压缩机的新氢混合,混合氢与原料油混合作为反应进料。
含硫、含氨污水自高压分离器底部排出至酸性水汽提装置处理。
高分油相在液位控制下经减压调节阀进入低压分离器,其闪蒸气体排至工厂燃料气管网。
低分油经精制柴油/低分油换热器和反应流出物/低分油换热器分别与精制柴油、反应流出物换热后进入分馏塔。
入塔温度用反应流出物/低分油换热器旁路调节控制。
新氢经新氢压缩机入口分液罐经分液后进入新氢压缩机,经两级升压后与循环氢混合。
3、分馏部分
从反应部分来的低分油经精制柴油/低分油换热器、反应流出物/低分油换热器换热至275℃左右进入分馏塔。
塔底设重沸炉,塔顶油气经塔顶空冷器和水冷器冷凝冷却至40℃,进入分馏塔顶回流罐进行气、油、水三相分离。
闪蒸出的气体排至燃料气管网。
含硫含氨污水与高分污水一起送出装置。
油相经分馏塔顶回流泵升压后一部分作为塔顶回流,一部分作为粗汽油去稳定塔。
从分馏塔顶回流罐来的粗汽油经稳定汽油(精制石脑油)/粗汽油换热后进入汽油稳定塔。
稳定塔底用精制柴油作稳定重沸器热源,稳定塔塔顶油气经稳定塔顶水冷器冷凝冷却至40℃,进入稳定塔顶回流罐进行气、油、水三相分离。
闪蒸出的气体排至燃料气管网。
含硫含氨污水与高分污水一起送出装置。
油相经稳定塔顶回流泵升压后大部分作为塔顶回流,小部分作为轻油排入不合格油中出装置。
塔底稳定汽油作为石脑油去罐区。
为了抑制硫化氢对塔顶管道和冷换设备的腐蚀,在分馏塔和稳定塔塔顶管道采用注入缓蚀剂措施。
缓蚀剂自缓蚀剂罐经缓蚀剂泵注入塔顶管道。
分馏塔塔底精制柴油经精制柴油泵增压后与低分油换热至100℃左右,然后进入柴油空冷器冷却至50℃后出装置作为优质燃料油去罐区。
㈡、催化剂预硫化与再生部分
1、催化剂预硫化流程
为了使催化剂具有活性,新鲜的或再生后的催化剂在使用前都必须进行预硫化。
本设计采用气相硫化方法,硫化剂为CS2。
2、催化剂再生
催化剂在运转过程中将逐渐失去活性,为了使失活的催化剂恢复活性,本装置考虑器外再生方法。
之所以不考虑催化剂器内再生方式,是为了保护装置设备安全,防止出现反应系统高压设备被腐蚀破坏,同时减少碱渣排放量。
㈢、开工、停工条件
开工时,开工油从罐区来,经原料油脱水、过滤后,经原料油缓冲罐、加氢进料泵进入系统,待高分、低分建立液位后,反应部分建立循环。
反应部分催化剂预硫化的同时,开工油引至柴油/低分油换热器,向分馏部分进油,待柴油汽提塔建立液位后,分馏部分可以建立循环,这样可以缩短开工时间。
停工时,原料油缓冲罐中存油经不合格油线出装置。
反应部分油从低压分离器经不合格油线出装置。
分馏部分油经产品线或不合格油线出装置。
第五节自控水平
一、采用的标准、规范
GB2625-81《过程检测和控制流程图用符号和文字代号》;
GB50058-92《爆炸和火灾危险环境电力装置设计规范》;
GB50160-92《石油化工企业设计防火规范》(1999年版);
SH3005-1999《石油化工自动化仪表选型设计规范》;
SH3006-1999《石油化工控制室和自动分析器室设计规范》;
SHJ3018-1990《石油化工企业信号报警、联锁系统设计规范》;
SHJ3020-1990《石油化工企业仪表供气设计规范》;
SHJ3021-1990《石油化工企业仪表保温及隔离、吹洗设计规范》;
SH3019-1997《石油化工仪表配管配线设计规范》;
SH3063-1999《石油化工企业可燃气体和有毒气体检测报警设计规范》;
SH3082-1997《石油化工仪表供电设计规范》;
SYJ1010-82《炼油厂自动化仪表安装设计技术规范》;
SH/T3092-1999《石油化工分散控制系统设计规范》;
SHB-Z06-1999《石油化工紧急停车及安全联锁系统设计导则》。
二、自动控制水平
根据10万吨/年煤焦油加氢改质单元工艺过程的特点、规模及目前国内外仪表生产及应用状况,该装置所设计的仪表自动控制系统将达到国内外同类型装置的先进水平,以实现集中控制、强化管理、平稳操作、安全生产,提高产品产量和质量,降低能耗,从而使工厂实现“安、稳、长、满、优”生产操作,提高经济效益,增强企业在市场上的竞争力。
根据目前仪表自动化技术不断更新、仪表自动化水平不断提高的特点和今后仪表的发展趋势,结合该项目的具体情况,确定本装置的控制系统采用当前技术先进、成熟可靠的集散控制系统(以下简称DCS),工艺装置DCS的操作站、控制站及附属设备全部置于中心控制室,进行集中操作、控制和管理。
1、10万吨/年煤焦油加氢改质单元采用DCS进行集中监视、控制和操作。
DCS融合了计算机技术、通讯技术和图形显示技术,以微处理器为核心,对生产过程进行集中操作管理和分散控制,具有精确度高,可靠性好和维护工作量少等特点,可为实现先进控制和优化控制创造良好的环境。
2、根据工艺特点和要求,设置性能可