超低碳奥氏体不锈钢焊接.docx
《超低碳奥氏体不锈钢焊接.docx》由会员分享,可在线阅读,更多相关《超低碳奥氏体不锈钢焊接.docx(12页珍藏版)》请在冰豆网上搜索。
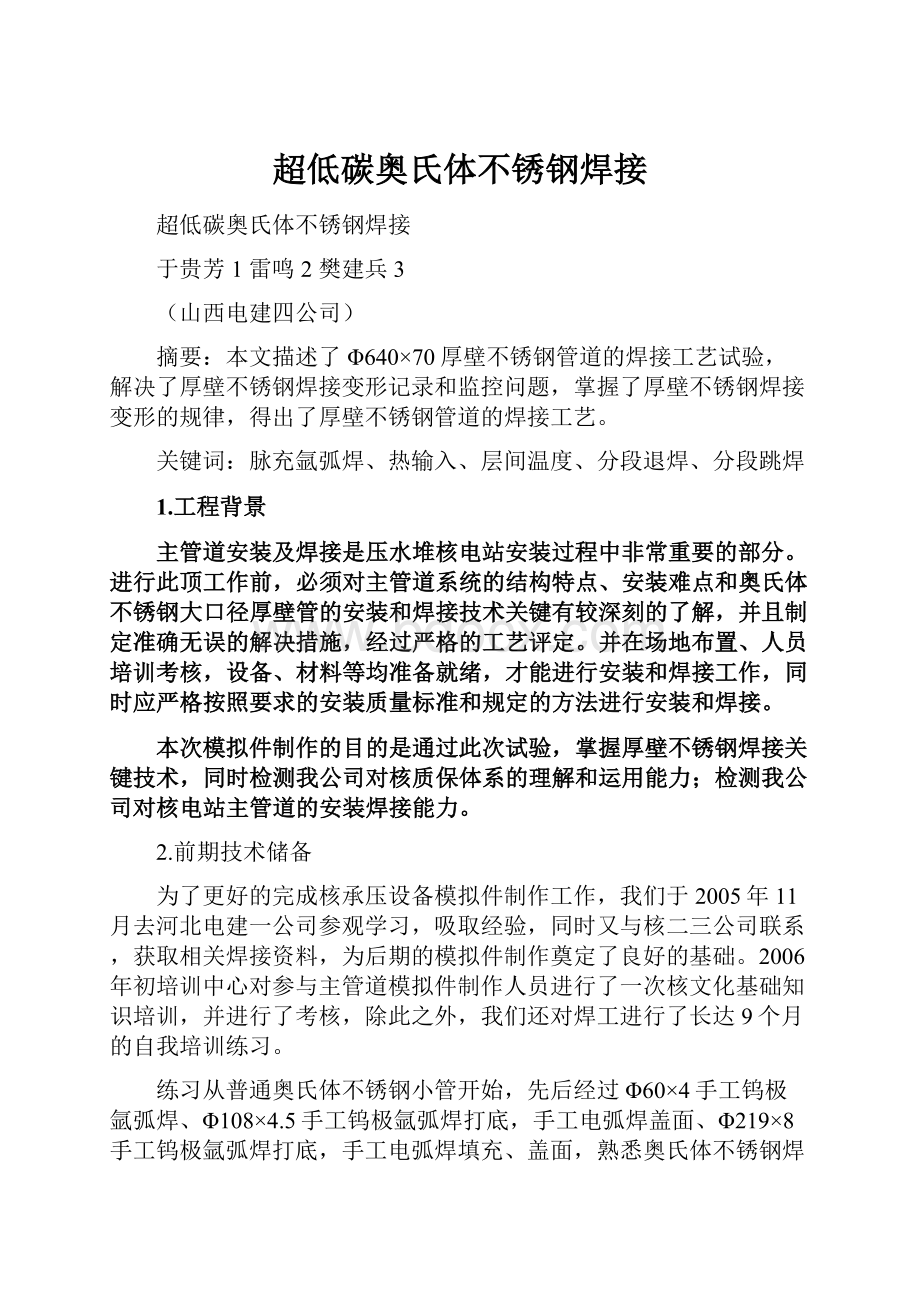
超低碳奥氏体不锈钢焊接
超低碳奥氏体不锈钢焊接
于贵芳1雷鸣2樊建兵3
(山西电建四公司)
摘要:
本文描述了Φ640×70厚壁不锈钢管道的焊接工艺试验,解决了厚壁不锈钢焊接变形记录和监控问题,掌握了厚壁不锈钢焊接变形的规律,得出了厚壁不锈钢管道的焊接工艺。
关键词:
脉充氩弧焊、热输入、层间温度、分段退焊、分段跳焊
1.工程背景
主管道安装及焊接是压水堆核电站安装过程中非常重要的部分。
进行此顶工作前,必须对主管道系统的结构特点、安装难点和奥氏体不锈钢大口径厚壁管的安装和焊接技术关键有较深刻的了解,并且制定准确无误的解决措施,经过严格的工艺评定。
并在场地布置、人员培训考核,设备、材料等均准备就绪,才能进行安装和焊接工作,同时应严格按照要求的安装质量标准和规定的方法进行安装和焊接。
本次模拟件制作的目的是通过此次试验,掌握厚壁不锈钢焊接关键技术,同时检测我公司对核质保体系的理解和运用能力;检测我公司对核电站主管道的安装焊接能力。
2.前期技术储备
为了更好的完成核承压设备模拟件制作工作,我们于2005年11月去河北电建一公司参观学习,吸取经验,同时又与核二三公司联系,获取相关焊接资料,为后期的模拟件制作奠定了良好的基础。
2006年初培训中心对参与主管道模拟件制作人员进行了一次核文化基础知识培训,并进行了考核,除此之外,我们还对焊工进行了长达9个月的自我培训练习。
练习从普通奥氏体不锈钢小管开始,先后经过Φ60×4手工钨极氩弧焊、Φ108×4.5手工钨极氩弧焊打底,手工电弧焊盖面、Φ219×8手工钨极氩弧焊打底,手工电弧焊填充、盖面,熟悉奥氏体不锈钢焊接性能;随后又进行了Φ350×55合金钢大管的焊接练习,采用钨极氩弧焊打底,手工电弧焊填充、盖面。
焊接过程中采用不锈钢焊丝和焊条进行焊接,熟悉焊接材料性能,练习多层多道焊接的熟练度,适应层间温度的控制,调整两名焊工焊接速度基本相同,探索小熔合比的坡口尺寸,以减小焊接工作量,减小焊接变形;2006年4月到8月是自我培训的最后阶段,在此期间先后进行了8道Φ273×31的厚壁不锈钢管的焊接。
为了更好的控制焊接热输入和根部焊缝的成型,采用脉冲钨极氩弧焊打底。
脉冲钨极氩弧焊与普通手工钨极氩弧焊相比有以下特点:
1.脉冲钨极氩弧焊采用高频脉冲引弧,不易产生夹钨等缺陷。
2.脉冲钨极氩弧焊通过脉冲频率有效的控制了焊接过程中的热输入。
它分为基值电流和峰值电流两个区间:
基值电流用于维持电弧燃烧,对焊缝不熔化;峰值电流用于焊接保证了送丝的稳定性,减少了焊接过程中对焊缝的加热,既减少了焊接热输入。
3.脉冲钨极氩弧焊结束时采用焊接电流衰减收弧,收弧时弧坑出不易产生缩孔等缺陷。
4.脉冲钨极氩弧焊具有滞后送气功能,对接头起到了良好的保护作用。
3.奥氏体不锈钢焊接性分析
不锈钢是在普通碳的基础上,加入一组铬的质量分数大于12%合金元素的钢材,它在空气的作用下保持金属光泽。
不锈钢按照化学成分可以分为:
铁素体型不锈钢,马氏体型不锈钢,奥氏体型不锈钢,奥氏体-铁素体双相不锈钢,奥氏体-马氏体双相不锈钢和沉淀化不锈钢。
奥氏体不锈钢一般属于耐蚀钢,是应用最广泛的一类,他具有较好的力学性能,便于机械加工、锻压和焊接。
在氧化性环境中有良好的耐腐蚀性和耐热性,但是对于溶液中有氯离子的介质特别敏感,易于发生应力腐蚀。
奥氏体不锈钢都具有良好的塑性和韧性,这类钢不会发生任何淬火硬化,所以在焊接过程中极少出现冷裂纹,而且具有很强的加工硬化能力,所以即使受焊接热影响而软化的区域,其抗拉强度仍然不低,只要不误用焊接填充材料,焊接接头强度不是焊接性的重要之点。
这类钢的导热率约为碳钢的1/4,导致热量传递速度缓慢,热变形增大,其线膨胀系数比碳钢大40%,更引起焊接时热膨胀量和冷却时收缩量的增加,因此焊后变形量就显得更为突出。
焊接过程中主要存在的问题是焊接热裂纹和焊接后变形量大。
焊接热裂纹产生的原因主要有三点:
1.由于奥氏体型不锈钢的导热率低,线胀系数大,在焊接区降温期焊接接头必然要承受较大的拉应力,会促成各类热裂纹的产生;2.方向性强的焊缝柱状晶组织,有利于有害杂质的偏析及晶间液态夹层的形成;3.有害元素的存在,会形成易熔共晶间层。
4.主管道焊接试验
4.1母材材质、规格、化学成分:
母材材质为SA249-TP316L,规格Φ640*70
表1母材化学成分
%
C
Si
Mn
P
S
Ni
Cr
Mo
Co
Cu
V
Fe
N
Ti+Nb
δ铁素体
计算值
标准值
0.03
0.32
0.86
0.033
0.008
11.73
17.4
2.36
0.09
0.26
/
/
0.035
/
5.5
复验值
4.2焊接材料材质、规格、化学成分:
焊丝为ER316L,规格为Φ1.6;焊条为E316L-15,规格为Φ2.5、Φ3.2
表2焊丝化学成分
%
C
Si
Mn
P
S
Ni
Cr
Mo
Co
Cu
V
Fe
N
Ti+Nb
δ铁素体
计算值
标准值
0.012
0.35
1.86
0.018
0.010
12.0
18.1
2.54
/
0.05
/
/
/
/
6
复验值
0.01
0.41
1.81
0.016
0.012
11.77
18.32
2.57
0.18
/
/
/
/
/
5.3%
表3Φ2.5焊条化学成分
%
C
Si
Mn
P
S
Ni
Cr
Mo
Co
Cu
V
Fe
N
Ti+Nb
δ铁素体
计算值
标准值
0.022
0.28
1.42
0.017
0.10
12.15
18.15
2.81
/
0.08
/
/
/
/
5
复验值
0.03
0.26
1.42
0.019
0.007
11.83
18.22
2.78
/
/
/
/
/
8.80%
表4Φ3.2焊条化学成分
%
C
Si
Mn
P
S
Ni
Cr
Mo
Co
Cu
V
Fe
N
Ti+Nb
δ铁素体
计算值
标准值
0.020
0.25
1.33
0.016
0.009
12.18
17.92
2.60
/
0.04
/
/
/
/
4
复验值
0.03
0.27
1.44
0.019
0.007
12.01
17.84
2.66
/
/
/
/
/
/
8.84%
选择焊接材料时从限制有害元素角度出发,选用超低碳,S、P含量得到严格限制的焊丝和焊条。
尽量使用小直径的焊丝和焊条,以控制焊接热输入。
焊材库的温度≥10℃、相对湿度≤60%,保证焊材良好的使用性能。
焊材应严格按照厂家规定的温度进行烘干,在使用时放入50-150℃的保温桶内随用随取,烘干次数不得超过两次。
3接头形式
接头形式为对接U形坡口,为了减少填充金属用量和减小焊接变形采用如下图所示的坡口尺寸:
图1坡口尺寸图
4.3焊接方法
焊接过程中采用脉充氩弧焊打底,氩弧焊填充2、3层,其余焊层采用手工电弧焊进行焊接。
4.3.1氩弧焊
采用脉充氩弧焊即可以减少热输入,又可以增大熔深。
氩弧焊三层的目的是为了解决手工电弧焊电流较大容易烧穿而电流小容易在侧壁或层间产生未熔合缺陷这一矛盾,以及一定熔敷金属厚度时手工电弧焊不用充氩。
4.3.2手工电弧焊
操作过程中,要注意侧壁未熔合的情况,即运条过程中,“U”型坡口两边都有一定的停留时间。
还要注意焊条应保持短弧操作。
而E316L-15属于碱性焊条,必须采用短弧,另一方面短弧也是为了防止合金元素烧损,保持合适的化学成分并防止空气中氮的侵入,氮的侵入可导致焊缝中铁素体的减少,进而可能产生裂纹和降低耐蚀性。
4.4焊接
4.4.1管件的固定
管件一端放置与自制的架子上,另一端用弹簧制作支撑,弹簧制作所能承受的力刚好等于管件的自重,使管件处于水平。
这样管件处在一个相对平衡的状态下,可以上、下、左、右、前、后6个方向自由收缩和变形,减小拘束度。
4.4.2焊缝的点固及点固棒的去除
图2焊缝点固图3对口卡子
焊缝点固位置见图
(2),点固棒选用与母材相同材质的不锈钢棒,尺寸为R=17mm,L=45mm。
对口卡具如图(3)所示。
点固棒使用前应用丙酮清洗干净,点固时与坡口两侧紧密接合不得有间隙,这样才能充分起到防止收缩变形的作用。
打底完毕后,在去除点固棒时,为了防止发生角变形,应对称去除点固棒,对称焊接。
去除点固棒时,不应损伤母材,并将其残留焊疤清除干净,打磨修整。
在焊接至封口时应适当的调小充氩的流量。
4.4.3充氩
不锈钢焊接过程中为了防止氧化,打底焊接时必须进行背后充氩。
充氩装置见图(4),将五合板制成与管子内径一样的圆板,塞在管子内部,周围用高温胶带进行封堵,并在五合板上开一个四方形窗口,用于观察焊接打底及充氩状况。
充氩时焊缝坡口用高温胶带封堵,焊接过程中随焊随撕。
打底完毕后,熔敷金属厚度只有3-4mm左右,为了防止烧穿,再用手工钨极氩弧焊填充两边,方可用手工电弧焊进行焊接,焊接时直到焊缝背面不发红为止,才可以停止充氩。
氩弧焊见图(6)
图4充氩装置
4.4.4焊接方向
焊接方向如图(5)所示。
由于奥氏体不锈钢的导热率低,约为碳钢的1/4,在焊接过程中温度升高得比较快,降低较慢,应严格监视层间温度,使其不要太高,控制在100℃以下,避免焊接过程中在450-850℃区间停留时间太长,产生贫铬现象,导致晶间腐蚀。
为了大到以上目的我们采用双人对称焊接,焊接时,为防止局部温度过高,除了采用小电流,快速焊,薄焊道,小摆动或无摆动的焊接方法来控制焊接线能量以外,还采用了不同的焊接方法来控制局部层间温度的升高。
在平焊到立焊部位采用分段退焊法,即在平焊部位起头,后一根焊条的收头部位为第一根焊条的起头部位;在仰焊到立焊部位采用分段跳焊的方法,每焊一根焊条就跳开一段距离。
这两种方法都可以使收头处温度有足够的时间降低,从而有效地控制了局部层间温度的过高,避免了敏化区的产生。
无论手工钨极氩弧焊还是手工电弧焊可按如下施焊顺序进行操作,且焊接时,两人应同时起弧,同时灭弧,不可一人单独施焊,以防止角变形的产生。
象限1--------象限3
1象限
2象限
象限2--------象限4
4象限
3象限
图5焊接方向
4.4.5填充和盖面
填充层除了第二和第三层外,其余各层采用手工电弧焊进行焊接。
填充时为了使坡口边熔合良好,焊接时应特别注意坡口两边的熔化,焊条可以微做摆动,尽量使电弧吹向坡口边。
切记单道焊层的厚度不得超过焊条直径,单层焊道的宽度不得超过焊条直径的2.5倍,一旦坡口宽度超过焊条直径的2.5倍,应采取分道。
由于焊接仰焊时铁水重力的作用,使得仰焊位置相比平焊位置要厚,盖面前应先找平。
盖面时,根据坡口的宽度计算焊道数和焊道之间的搭接尺寸,先焊坡口两边,后焊中间部位。
焊缝外观图(7)
图6图7
4.4.5焊接参数记录
焊接过程中,为了更为准确的记录焊接参数,使用WHJ型焊接参数记录仪,进行跟踪记录。
焊接时,每间隔6秒记录一次参数。
在脉冲钨极氩弧焊时,还可以准确记录其焊接峰值电流、基值电流和脉冲频率。
保证记录的客观真实。
4.4.6焊接变形的测量及控制
在管子的3、6、9、12钟点位打四个点,在这四个点位置设置百分表测量焊缝的横向收缩。
在管件的自由端焊一块盲板,在盲板上再焊一根延伸管Ф108×4.5的管子。
在延伸管外壁x、y方向设置一块百分表监测x、y方向的收缩偏移。
据了解,大壁厚管道焊接收缩量传统经验公式的计算结果一致如下:
最大焊接收缩量Lmax=0.2×AH/t;
最小焊接收缩量Lmin=0.2×AH/t-0.5;
(式中AH为焊缝坡口截面积,t为管道壁厚。
)
焊接前将百分表的数值调至8mm,若百分表数值增大则为膨胀,百分表数值缩小则为收缩。
焊接过程中百分表具体显示数值见下表:
从工艺评定表中可以看出,变形主要发生在前50%,前35%平均变形量为0.53mm,从35%到50%平均变形量为0.138mm。
过了50%以后基本不再发生变化,平均变形量只有0.074mm。
从模拟件见证件变形记录表中可以看出,变形同样主要发生在前50%,前35%平均变形量为0.4975mm,从35%到50%平均变形量为0.102mm。
过了50%后也基本不再发生变化平均变形量只有0.02mm
通过两个表的对比我们得出,随着管子长度的增加,温度传递增加,散热加快,变形量有所减小。
无论是工艺评定还是模拟件见证件变形记录表其平焊位置的横向收缩变形都要比仰焊部位的横向收缩变形要大,通过分析其原因有二:
一是平焊位置焊接电流相对要比仰焊位置大5到10A左右,二是温度向上传播,导致平焊位置温度高于仰焊位置,使得管子发生较大的横向收缩变形。
5焊接注意事项
5.1对口应将焊口表面及面侧15mm母材内,外壁的油、漆、垢、及氧化层等清理干净,直至露出金属光泽,并对坡口表面进行检查,不得有裂纹、重皮、毛刷及坡口损伤等缺陷。
对口前还应对坡口表面进行液体渗透探伤。
5.2焊接时焊接材料必须放在插上电源的保温桶内。
保温桶使用前应先预热到75℃以上,防止焊条骤冷。
5.3焊接宜采用小电流、短电弧、小摆动、小线能量的焊接方法。
5.4前三层采用钨极氩弧焊进行焊接。
5.5为了保证根部质量应用外径为Ф12的长喷咀。
5.6氩弧焊前,先通入氩气30min待空气全部排除后再进行打底焊接.
5.7氩弧焊时,断弧后应滞后关气,喷嘴在收头处停留5秒以上,以免焊缝氧化。
5.8氩弧焊打底焊接时,背面应充氩保护。
5.9焊接的层间温度不大于100℃。
焊接时每焊完一根焊条,应对即将焊接的部位进行温度测量,温度不大于60℃方可继续施焊,若温度高,应停止焊接,待温度降低到60℃以下才能进行焊接。
5.10两名焊工应具有相同的焊接速度。
5.11仰焊位置电弧应尽量短,防止铁水下坠。
5.12焊口焊完后,应清除焊缝表面及附近表面区域的焊渣、氧化皮、油脂等物质,经焊工自检合格后方可进行RT检验,RT检验时应用专用记号笔。
5.13PT和RT结束后,必须对焊缝进行清洁度检查,确保焊缝不被污染的情况下,进行下一步焊接工作。
5.14层间清理和表面清理采用不锈钢丝刷和非铁基砂轮片,而且这些工具只能用来处理不锈钢。
5.15加速焊缝冷却,空冷即可。
5.16若中途因某些原因停焊较长时间时应作相应的保护。
6存在的问题
6.1本试验所用的充氩装置不够合理,保护效果不是很好,而且对于现场施工使用性不高。
6.2手工电弧焊时,应选用普通逆变焊机,尤其是在仰焊位置,适当的调大焊接推力,可以有效的防止铁水下坠,保证焊缝成型良好。
6.3焊缝张口测量不准确,应该在周向4个方向都安装百分表。
6.4焊接时两名焊工的焊接速度,不是很接近,导致焊后有一定的角变形。