注射成型工艺讲解.docx
《注射成型工艺讲解.docx》由会员分享,可在线阅读,更多相关《注射成型工艺讲解.docx(15页珍藏版)》请在冰豆网上搜索。
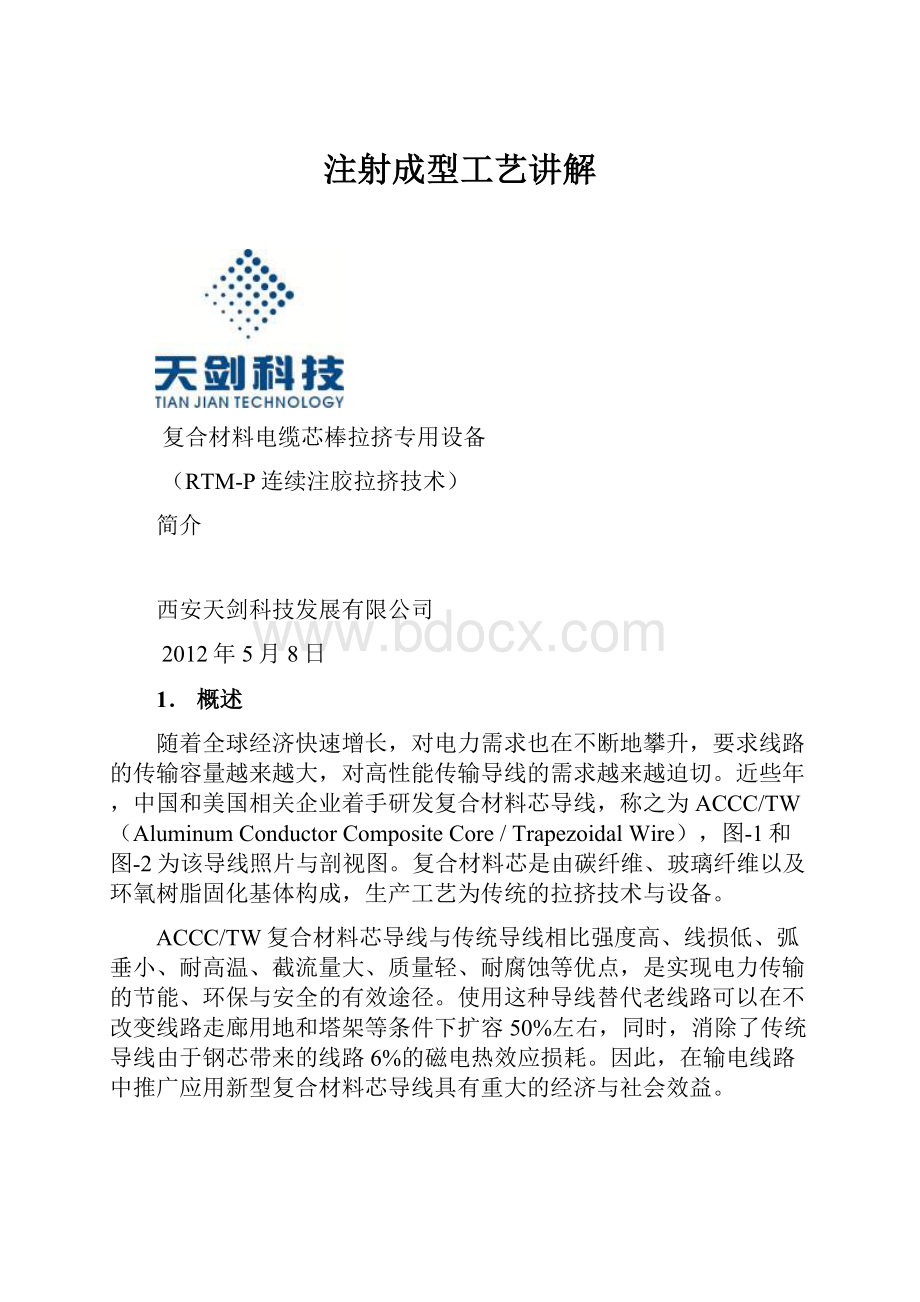
注射成型工艺讲解
复合材料电缆芯棒拉挤专用设备
(RTM-P连续注胶拉挤技术)
简介
西安天剑科技发展有限公司
2012年5月8日
1.概述
随着全球经济快速增长,对电力需求也在不断地攀升,要求线路的传输容量越来越大,对高性能传输导线的需求越来越迫切。
近些年,中国和美国相关企业着手研发复合材料芯导线,称之为ACCC/TW(AluminumConductorCompositeCore/TrapezoidalWire),图-1和图-2为该导线照片与剖视图。
复合材料芯是由碳纤维、玻璃纤维以及环氧树脂固化基体构成,生产工艺为传统的拉挤技术与设备。
ACCC/TW复合材料芯导线与传统导线相比强度高、线损低、弧垂小、耐高温、截流量大、质量轻、耐腐蚀等优点,是实现电力传输的节能、环保与安全的有效途径。
使用这种导线替代老线路可以在不改变线路走廊用地和塔架等条件下扩容50%左右,同时,消除了传统导线由于钢芯带来的线路6%的磁电热效应损耗。
因此,在输电线路中推广应用新型复合材料芯导线具有重大的经济与社会效益。
图-1美国CTC公司ACCC/TW导线照片图-2ACCC/TW导剖视图
2.传统架空导线复合材料芯棒生产中存在的问题
目前,中国和美国的相关企业生产ACCC/TW导线复合材料芯棒,依然是传统的复合材料材FRP(FiberReinforcedPlastic)生产工艺,主要特点是开放式胶槽。
生产工艺过程为:
纱架、集纱、除湿、开放胶槽浸胶、预成形(选项)、模具热固化、后固化、牵引、收卷。
在FRP的连续拉挤成形工艺中,多采用不饱和聚酯树脂,这种树脂的固化特点:
具有引发活化能低、引发温度低、收缩率大,这些特点非常适合FRP连续拉挤成形工艺。
而ACCC/TW导线复合材料芯棒采用环氧树脂体系,环氧树脂体系的固化剂一般为酸酐类和胺类,这类固化剂引发活化能较高,需要吸收较多的热能才能达到凝胶固化的程度,因此固化速度较慢;另外,由于树脂分子中环氧基是开环聚合反应,没有挥发性副产物放出,环氧树脂固化基体的收缩率明显小,环氧树脂固化收缩率仅1%-2%,而不饱和聚酯树脂却高达7%-8%。
环氧树脂体系的这两个特点加之开放式胶槽,使得ACCC/TW导线复合材料芯棒的连续生产存在许多问题,甚至某些关键性能参数不达标。
下面简单剖析一下,环氧树脂固化体系的这两个特点及开放式胶槽,给我们带来的麻烦和问题:
2.1固化速度慢带来的麻烦和问题
环氧树脂体系固化速度慢影响生产效率,要提高生产效率可由3个方面入手,如适当提高固化温度、加长固化模具、增加促进剂。
1)提高温度
对环氧树脂固化温度而言,模具固化点位置的温度一般设定在Tg温度附近,温度
再高一点会加快固化速度,但过高会影响树脂固化基体的力学性能。
2)加长固化模具
传统设备拉挤工艺中,模具长度在400mm~900mm。
针对环氧树脂基导线芯棒的
拉挤生产而言,其使用模具的长度在1200mm~1500mm时,最佳性能与速度结合点可以达到1000mm/min以上,但制造这样的模具难度大。
3)增加促进剂
增加促进剂的比例的确有助于固化速度,但它也同时造成了胶的操作期的缩短,使
胶槽里的胶黏度很快变大,影响纤维浸胶质量。
为了更好照顾操作期,促进剂的比例要适当,因此,环氧树脂体系固化速度不允许太高。
2.2固化基体收缩率低带来的麻烦和问题
环氧树脂固化基体收缩率为1%-2%,不饱和聚酯树脂为7%-8%,相对而言前者拉挤固化时模具内部压强要大大高于后者,因此,给环氧树脂拉挤带来两个麻烦:
1)模具内压对固化物表面影响
由于环氧树脂拉挤固化工艺模具内部压力大,造成环氧树脂凝胶固化区与模具内表
面的摩擦力加大,这就要求凝胶状态转变至固化状态的环氧树脂基体具有足够的抗剪切能力,否则,在模具的这一区域环氧树脂固化物容易脱皮起粉末,严重时会造成堵模。
2)模具内压对模具镀层影响
原理同上,由于摩擦力大,模具内表面镀层容易磨损、脱落。
从目前使用情况看,
现有模具对环氧树脂芯棒的拉挤生产不是很理想,镀铬层非常容易脱落。
2.3开放式胶槽带来的麻烦和问题
传统拉挤工艺中胶槽为开放式,或者说增强纤维的浸胶是在大气环境中完成的,这种浸胶方式对环氧树脂拉挤而言有如下麻烦和问题:
1)胶槽容积
胶槽容积的大小直接影响着胶液质量和操作期,从效果来讲胶槽容积越小越有利于
胶液的质量,但会增加添加胶液的次数,加大操作工人劳动量和出错的机率;如果胶槽过大会导致胶液粘度随着时间而加大,从而影响纤维的浸胶质量乃至芯棒的性能,同时也会造成模具内的树脂凝胶点前移,严重时会堵模。
2)胶液回流
开放式胶槽产生回流是不可避免的现象。
浸了胶的纤维进入模具内势必被挤压出一部分胶液返回胶槽(或浪费掉,该部分胶液占用较量的70%以上),从模具口返回到胶槽的那部分胶液由于已被热模具加热,其温度比胶槽内的胶液温度要高,如此循环往复,胶槽内的胶总体上温度会升高些,这也导致胶液的操作期缩短,胶液黏度加大,影响浸胶质量,进而影响芯棒的性能。
3)纤维杂质
架空导线复合材料芯棒的增强纤维有碳纤维和玻璃纤维,碳纤维在中心主要起承担
载荷的目的,玻璃纤维在表层主要起绝缘作用,结构参见图-2。
在浸胶过程中,碳纤维和玻璃纤维在各自的胶槽内和回流胶中存有少许含量的纤维杂质,在处理回流时或将纤维杂质滤掉二次使用回流胶液,或将两种回流胶液直接用于碳纤胶槽(这样不影响绝缘性能),回流的再次使用更加严重地影响胶液的质量和操作期。
产生纤维杂质的主要原因是胶槽内的排纱器和旋转压胶辊,再好的纤维也会有少许毛絮,这些毛絮绝大部分被胶液粘在旋转压滚上越积越多,给操作人员带来麻烦,不小心也会酿成断纱停机的事故。
4)影响Tg
架空导线复合材料芯棒的一个核心指标是耐热性能,既玻璃化转变温度(Tg)的高低。
目前,国内研发单位所选用的环氧树脂体系配方繁多,有进口、国产,各家配方特性与性能各有不同。
大部分配方的Tg或多或少受到开放式胶槽的影响,具体表现是随生产时间的延续,芯棒的Tg前高后低,有时低到不可接受程度。
3.精密注胶拉挤芯棒生产工艺与设备
上述传统芯棒生产设备存在的问题,有些通过树脂配方和结构设计调整可以解决,如芯棒表面不光滑起粉末、结构性力学性能差等问题;而其他的问题均与设备的胶槽有关,所以,解决问题的重点也要从胶槽开始。
综合来看,传统拉挤工艺中的胶槽随着时间延长导致环氧树脂胶质量越来越差,换言之,环氧树脂胶越来越不新鲜,影响芯棒质量;另一方面胶槽的排纱器、压胶辊严重损伤玻纤和碳纤,使毛絮脱落到胶液中,并却大量纱线被压胶辊缠绕造成麻烦。
既然胶槽带来这么多问题和麻烦,干脆就不使用胶槽,这一点也正是本工艺设备的核心之处,即采用RTM连续注胶拉挤(RTM-P,ResinTransferMolding-Pultrusion)方式,这种方法不仅可以保持胶的随时新鲜,又不损伤纤维纱线。
因此将设备命名为:
“精密连续注胶拉挤芯棒生产设备”。
3.1精密注胶拉挤芯棒生产工艺
就目前来看,RTM连续注胶拉挤架空导线复合材料芯棒生产工艺,在该行业内都将是一次革命性的改进。
核心技术是“取掉传统胶槽,采用精密连续注胶”。
1)工艺过程
碳纤维和玻璃纤维在牵引装置的作用下,纱线束经过集纱器、除湿箱,进入密闭浸
胶装置,装置内有两个独立通道,一个走碳纤,一个走玻纤,浸好胶后通过预成型再直接进入与装置同样密闭相连的固化模具中热固化定型,定型的芯棒从固化模具出来后进入后固化箱,然后由牵引机导出输送给收卷机。
这就是无胶槽精密连续注胶的基本过程。
另外,单独解释一下密闭浸胶装置工作过程:
密闭浸胶装置内的胶液供给,是由一台精密自动控制的连续注胶机实现,保障装置内的胶液实时新鲜充裕。
图-3为无胶槽RTM-P连续注胶拉挤芯棒生产工艺流程图。
2)精密连续注胶原理
碳纤维和玻璃纤维(或布带或编织层)通过各自通道进入封闭式浸胶装置
,浸胶
后由预成形机构将碳纤维和玻璃纤维按设计要求定位,然后进入固化模具
成型。
为了使封闭式浸胶装置
内的碳纤维、玻璃纤维(或编织层或布带)有更好的浸润效果,RTM精密连续注胶机
将胶液注入封闭式浸胶装置
之前进行胶液加热,这样胶液黏度会大大降低有利于浸润纱线。
同时,由于胶液处于较高的温度,进入固化模具
后有助于快速均匀固化;另外,要保持封闭式浸胶装置
内的胶液实时充裕,RTM精密连续注胶机
采用自动平衡压力注胶,这样既保障了胶液充裕,又增加了纤维纱线的浸润效果。
采用RTM-P连续注胶拉挤工艺对布带或纤维编织包敷层的实现更为容易,摈弃了传统编织浸胶方式,大大减便工艺过程、提高工作效率。
功能原理图参见图-4、-5、-6。
图-3无胶槽RTM-P连续注胶拉挤芯棒生产工艺流程图
3)精密连续注胶工艺带来的好处
PIRP精密注胶连续拉挤工艺与传统开放式胶槽拉挤工艺相比,从结构特征上看,最大的特点是没有胶槽。
由于去掉了胶槽,给架空导线环氧树脂基拉挤芯棒的生产带来许多好处,并解决掉前面提到的诸多问题。
具体优点如下:
a.芯棒性能全程一致
由于浸胶过程实时都是新鲜胶液,不存在操作期的问题。
因此,芯棒的性能从生产开始到结束(如1m~5000m长度范围内),其力学性能(抗拉强度、绕曲率等关键参数)、耐热性能(Tg)等均保持一致,不会随时间变化而性能起伏。
b.不需要人工混胶
传统工艺中需要人工混胶、向胶槽倒胶、清洗胶槽等诸多环节,给操作人员带来不
便,而且容易出错。
采用RTM精密连续注胶,就不需要混胶、倒胶着两个环节,将环氧树脂AB两个组份胶液罐分别灌满即可,通过各自的泵按设计流量比例泵入静态混合器,再注入封闭式浸胶装置中。
精密连续注胶系统(包括封闭式浸胶装置)的清洗有专门自动清洗系统完成,人工参与清洗工作量较小。
清洗方式有专用清洗液和气体吹除两种并用。
c.不伤纱
由于没有排纱器和压胶辊,纤维束不会受到损伤,同时也大大降低了胶液内的纤维
杂质含量。
d.浸胶效果好
由于胶液是高温高压注入封闭式浸胶装置中,浸润效果远好于开放式胶槽常压浸
胶,保障了芯棒的内部质量;同时,封闭注胶没有胶液溢出,胶液利用率100%,对于传统方式而言可以节约大量用胶成本。
e.提高拉挤速度
由于胶液是高温高压注入封闭式浸胶装置中,这将有利于胶液在固化模具内的快速
凝胶和固化。
将模具设计成1500mm时,可以实现拉挤速度1000mm/min以上。
图-4单向纱RTM连续注胶系统原理图
图-5布带包裹层RTM连续注胶系统原理图
图-6纤维编织包敷层RTM连续注胶系统原理图
3.2精密连续注胶拉挤芯棒生产设备构成
传统的架空导线芯棒生产设备有:
纱架、集纱器、除湿箱、开放胶槽、预成形模具、固化模具、后固化箱、牵引机、收卷机、以及监控系统。
精密连续注胶拉挤芯棒生产设备与传统的芯棒拉挤生产设备不同之处是浸胶功能部分,传统设备浸胶是由开放式胶槽完成,而该设备浸胶是由高温高压封闭式浸胶装置完成。
所以,精密连续注胶拉挤芯棒生产设备构成有:
纱架、集纱器、除湿箱(选项)、封闭式浸胶装置、纤维编织机构、精密连续注胶机、固化模具、后固化箱、牵引机、收卷机、以及监控系统。
设备系统功能结构参见图-7,各部分功能如下:
1)纱架
碳纤维原丝纱盘被有序安装在纱架上,玻璃纤维放置在碳纤维纱架两侧的托架上,纱盘运动是被动形式,在牵引机构的拖动下碳纤维转动放纱,玻纤为内抽纱。
纱架和托架上设有张力调解机构,在放纱过程中令碳纤维和玻璃纤维处在不同的恒张力状态,有利于芯棒拉伸力学性能充分发挥,同时纤维在绷紧状态下有利于空间排序和定位。
根据目前架空导线复合材料芯棒的规格,碳纤维纱架最多挂直径75mm的纱轴100个,玻璃纤维最多放置重20kg左右80团,可以满足多规格使用。
2)除湿箱(选项)
除湿箱内部空间尺寸为长1500x宽400x高400,外围轮廓尺寸为长1500x宽600x高600。
恒温范围可在RT~200℃任意设定。
集纱器与除湿箱设计于一体,位置处在除湿箱出入口,集纱器材料为聚四氟乙烯板制成。
板的尺寸为400x400,在300x300见方内均匀布置180个直径3mm孔。
3)封闭式浸胶装置
封闭式浸胶装置
是该设备关键技术之一。
装置
内设有碳纤维
浸胶通道、玻璃纤维
浸胶通道、以及预成型模具,装置
与固化模具
密封连接,构成一个完整的密封系统。
装置
的结构尺寸不随芯棒规格变化,预成型模具与芯棒规格一一对应。
装置外部设有加热保温层,以便注入进来的胶液保持设计温度。
4)纤维编织包敷机构
芯棒外表绝缘层设计有多种结构形式,单向纤维层、布带包裹层、编织包敷层等常
见结构层。
后两种方式的实现要与封闭式浸胶装置一并考虑,具体结构细节这里暂不多讲。
结构示意图参见图-5、图-6。
5)精密连续注胶机
封闭式浸胶装置
与RTM精密连续注胶机
有机组合构成设备的技术核心,也是连续注胶拉挤工艺设备的精髓,是在RTM技术的基础之上加以改进完善。
精密连续注胶机工作时,将环氧树脂和固化剂两组份分别由各自的计量泵,按照设计按比例泵到静态混合器中,然后进入封闭式浸胶装置
。
RTM注胶机具有胶液加热和压力自动控功能,高温、高压状态下胶液有利于增加纱线浸润效果。
环氧树脂(A)和固化剂(B)的两个胶桶配有液位报警,提醒操作人员及时填加A、B组份。
6)固化模具
由于环氧树脂拉挤固化工艺模具内部压力大,造成环氧树脂凝胶固化区与模具内表
面的摩擦力加大,模具内表面镀层容易磨损、脱落。
从目前使用情况看,传统模具对环氧树脂芯棒的拉挤生产不是很理想。
传统拉挤模具长度在900mm左右,这里建议使用非镀层模具,长度在1200mm~1500mm左右,即不会发生度层脱落,又可以提高拉拔速度,性能与速度结合点可以达到1000mm/min以上。
7)后固化箱
芯棒从固化模具出来后,其固化度并没有达到完全固的程度,仍需进一步固化。
后
固化箱为组合式,单个长度为1m,为了穿线方便箱体为开合方式,通径为50mm,数量配置4台或根据实际需要令配。
8)牵引机
为了提高牵引机的可靠性,采用电机驱动齿轮和蜗轮蜗杆施加压力,并提升链条规格。
在压力方向设有蝶簧和力值传感器,蝶簧起到缓冲作用不至于刚性压实,力值传感器可实时显示夹持力的大小。
牵引力数字显示功能为可选项。
9)收卷机
收卷采用横张力控制、自动排线,并配有芯棒首尾自动装订机构。
收线盘内径为1500mm、宽度为800mm、缠绕高度为500mm,一盘可卷绕芯棒总长度为5000m。
10)监控系统
监测系统主要巡检设备各功能区的测试点,如温度、压力、张力、速度等,发现异
常情况时,系统自动报警提示操作人员注意并及时处理。
监控系统设计成操作面板形式,安装在生产线上实时监测生产状况,测控核心部件采用单片机。
4.现场抗拉强度试验装置
ACCC/TW导线复合材料芯棒在研制初期和生产过程中,芯棒抗拉性能指标希望能在生产现场即刻得到验证,以便及时修改或完善芯棒设计。
为此,专门设计了可拆卸(重复使用)拉力试验金具及相关试验设备,即现场拉伸试验机。
4.1重复使用金具
重复使用金具具备可拆卸功能,由3部分构成:
外锥套、内锥、拆装螺帽、拉伸连杆、清理工具。
结构示意参见图-8。
金具装卸时采用液压或电动扳手,根据复合材料芯棒直径不同,施加的扭矩有所不同,基本依据是扭矩产生的握力要大于芯棒的破断力。
液压或电动扭矩可以设计成自动控制方式,事先根据芯棒规格设定停机扭矩。
4.2现场拉伸试验机
现场拉伸试验机结构较为简化,但功能完善。
它由支撑框架、液压位移机构、破断力检测仪、手动液压泵、重复使用金具装卸机构。
结构示意参见图-9。
试验时,先将芯棒与金具在装卸机构上装好,卸下拆装螺帽并将拉伸连杆连接好,然后将其连到拉伸机上。
在拉伸试验过程中,芯棒的承载拉力在检测仪上实时显示,直至拉断仍保留此时力值,即该芯棒的破断力值。
之后,取下金具清理,准备下一次试验。
图-7精密连续注胶拉挤芯棒生产设备功能图
图-8可拆卸重复使用金具示意图
图-9现场拉伸试验机示意图