精品项目总装工艺方案.docx
《精品项目总装工艺方案.docx》由会员分享,可在线阅读,更多相关《精品项目总装工艺方案.docx(12页珍藏版)》请在冰豆网上搜索。
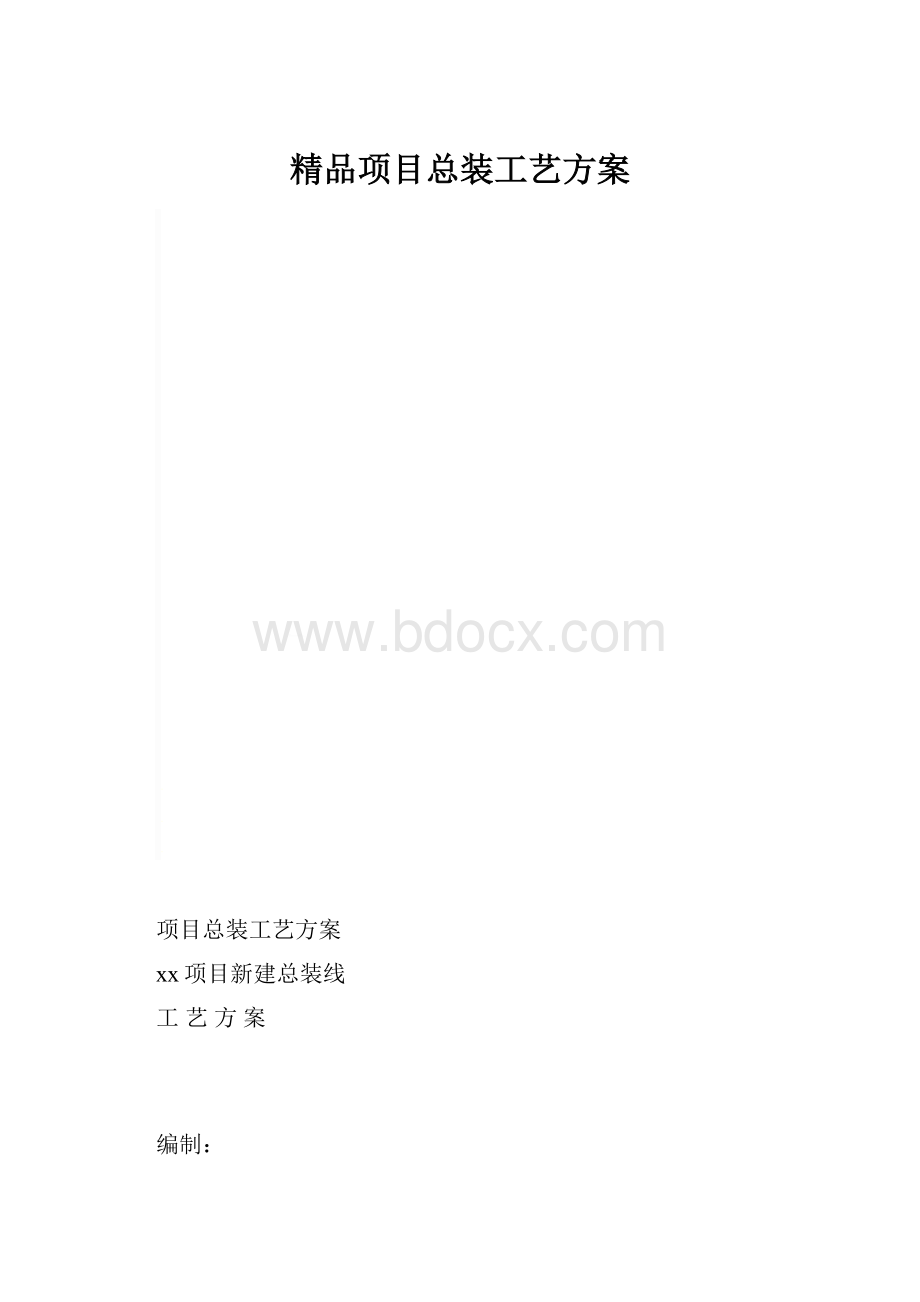
精品项目总装工艺方案
项目总装工艺方案
xx项目新建总装线
工艺方案
编制:
会签:
审核:
批准:
xxxx股份有限公司
xx项目总装线工艺方案
一、产品信息
序号
车型参数内容
xx
1
长度(mm)
2
宽度(mm)
3
高度(mm)
4
轴距(mm)
5
前后悬(mm)
6
整车轮距前/后(mm)
7
整车额定载质量(kg)
8
整车总质量(kg)
9
整车轴荷(kg)
1、根据规划,xx项目总装生产线主要生产xx系列车型:
其基本参数见下表:
二、工艺覆盖范围
整体覆盖
□冲焊工艺□涂装工艺
□机加工工艺■总装工艺
单一变动
□车架工艺□发动机工艺
□车身工艺■其他
三、工艺计算分析
新增总装线生产纲领为单班10万辆/年,按工作一年250天工作日,单班8小时计算,设备开动率90%(设备开动率包含辅助时间、等待时间、设备故障占用时间)。
1、工艺设计输入:
生产纲领:
单班年产10万辆/年;
生产车型:
xx系列车型;
工作制度:
250天/年;
产品参数见上表
2、工程计算:
生产节拍计算:
270,000*0.9/1200,000=xx分/台取整数为xx.4分/台;(设备开动率按90%计算)
工位数计算:
标准时间/节拍/人员工位密度=所需工位数;
内饰线工位数:
工位(考虑上、下线损失2个工位,设置2个检查工位取26工位);
底盘线工位数:
工位;
合装工位数:
工位;
总工位数:
工位
3、人员需求
操作人员需求:
项目
内饰线
底盘线
合装线
OK线
车门线
动力总成
备注
平均工位密度
1.8
1.8
1.8
2
2
1.2
工位数
小计人数
合计人数
车间总人数需求:
序
名称
人员数量(人)
备注
号
合计
Ⅰ班
Ⅱ班
1
基本工人
2
辅助工人
为基本工人的15%
工人小计
3
工程技术人员
占工人合计的6%
4
管理人员
占工人合计的4%
5
服务人员
占工人合计的1%
人员总计
检验人员
不属本车间编制
占基本工人数的5%
其中:
工人
4、车间面积组成
序号
部门名称
面积(m2)
备注
合计
新建
原有
I、生产面积
1
装配区
2
交检间、检测、返修区
小计
II、辅助面积
1
物料存储
2
车间通道
3
车间办公及生活
含二层生活间
小计
合计
四、工艺方案
1、项目背景
xx项目总装生产线要实现年产20万台生产能力,针对具体车型分析产能状态:
设计生产节拍:
xxUPH
设计年工作制:
年250天、单班工作8小时
A、按年生产250天最大产量:
20万台
2、设计原则
a.采用精益生产方式。
本车间内各生产工序间设置一定量的中间存放,但为保证生产的连续性,在关键的工序间设有少量的缓冲。
是否采用较为先进的SPS配送模式需进一步确认(物流规划介入)
b.车间按均衡生产的原则组织生产,考虑到车型的多样性及生产中各种因素的影响,生产线的选用具有柔性和灵活性,以适应多品种的生产。
c.设备选用立足于国内,涉及产品质量和效率的关键设备采用进口。
3、新建生产线内容简介
序号
项目
内容
备注
1
车型确认
xx系列车型(暂定)
2
纲领确认
双班20万(生产节拍xx,设备开动率95%)
3
可用场地
总装车间,规划占地面积S=xx平方米
4
物流配送
内饰线、车门线采用SPS配送方式试点,是否采用SPS需进一步确认
5
PBS线
储存白车身数量100(暂定
6
内饰、合装线、OK线
采用板链线,需要挖地坑
7
底盘线
采用摩擦线(日系多采用)
摩擦线
8
车门分装线
采用积放链/CPC链和摩擦链
9
座椅输送线
采用滚道线/物流台车
10
轮胎输送线
采用滚道线/物流台车
11
动力总成线
采用滚道线
12
检测线
包含淋雨线在内
13
补漆室
是否建设(待定)
14
返修区
4、各段生产线任务分工:
按产品结构特点和工艺要求,本车间划分为以下几个工段,分别负责整车的内饰装配、底盘装配和合装装配、调整、整车检测及返修等项工作。
a.内饰工段:
负责车身的内、外饰零部件装配工作
b.底盘工段:
负责整车底盘零部件装配工作
c.合装工段:
负责整车的部分内饰及最终装配、油水加注、下线前的检查和调整。
d.整车检测调整工段:
负责整车下线后的出厂检测、调整、故障排除等项工作。
e.分装工段:
负责部件分装工作,包括车门、发动机、动力总成、副车架、轮胎、仪表板、前后保杠、油箱以及制动管路等。
5、新总装线位置及工艺平面图
总装车间占地面积xx平方米,总长度xx米,详细平面布局图在20xx年x月xx日完成。
6、设备选用
在保证产品质量和满足效率要求的前提下,优先选用国产设备,但对于国内技术尚不成熟的关键设备以及能够提高工艺水平、提高生产效率的设备从国外引进。
7、物料搬运系统
仓储、物料搬运系统应与产量、生产节拍相适应。
因此,本车间采用精益生产方式组织生产,物流配送模式需进一步分析和探讨。
8、油、水供给系统
整车下线前加注的燃油从厂区内的原有地下油库通过管道输送至定量加油机;制动液、制冷剂、防冻液(自动配比)、洗涤液、发动机润滑油和变速箱润滑油等以原包装形式放至加注机旁直接加注。
(加注是否采用集中加注的方式以及加注的具体工位布局需在LAYOUT确定后定版)
9、质量保证体系
a.外协件需按类别经不同程度的检验,合格品才能进入车间。
b.关键螺纹连接件采用定扭矩扳手拧紧,以便准确达到产品的设计要求。
c.整车下线后在室内检测线上进行安全环保性能检测,然后经过路试和淋雨试验。
(淋雨线在路试前还是路试后呢?
北仑总装二厂淋雨在路试前,淋雨在路试前,其他工厂基本都是淋雨在路试前)
10、工艺说明:
主要工艺如下
a.工艺流程概述
车身从PBS系统通过升降机送到内饰线的起点。
车身内饰采用窄板链送线,由地下返回。
该段内饰的主要装配内容包括:
拆车门、装配发动机仓线束、侧围衬垫、ABS、离合制动踏板总泵、仪表板、变速操纵杆、支架、暖风机、蒸发器、前后保险杠、天窗和前后大灯等。
内饰线的车身通过升降机转到底盘线(摩擦线)上(车身裙边距地面1700mm)。
底盘装配主要内容包括:
油箱油管、前后轮罩、制动管路连接、动力总成、排气消声器总成、导流板、管线连接和整理、备胎和轮总成等。
装好车轮的整车,通过升降机落至最终装配线,该线采用板链输送机,装配内容包括:
前后座椅、方向盘、车门、油液加注、外观初检,最后启动发动机至调整线进行检查、调整。
最后进行整车性能检测,内容包括包括四轮定位、前大灯和转鼓试验、废气分析、电器检测和底盘检查、淋雨测试等。
如果没有问题,整车开至试车跑道进行路试,路试后在外观检查线上完成车身表面质量检查。
在以上测试过程中,有不合格项目出现的汽车进入返修区进行故障排除,然后重新测试,直至合格。
所有项目均已合格的汽车开往停车场。
b.制动液、防冻液、制冷剂、动力转向器油加注采用国内(国外)抽真空定量加注机,燃油、洗涤液加注采用国产定量加注机、机油和齿轮油加注采用进口气动柱塞泵和定量加注枪组成的输送、加注系统完成。
c.车门、座椅、仪表板、车轮、蓄电池等采用助力机械手辅助工人完成装配,可减轻工人劳动强度,并能保证装配质量。
d.车轮装配采用多头定扭矩组合拧紧机,一次完成,可提高生产效率,保证拧紧质量。
其他螺纹拧紧根据要求,分别采用单头定扭矩扳手和冲击式扳手。
11、工艺设备选用
为满足本车间批量生产要求和高质量的生产目标,本次设计采用机械化的、自动化程度较高的生产设备。
11.1车身储存编组线(PBS)
PBS滑撬或者是工艺吊具
11.2内饰装配线
本次设计车身的第一内饰线采用窄板链输送机,由地下返回;车身由储存编组线通过升降机自动转到内饰线上,进行内饰的装配工作。
该线全长米,共XX个
工位,工位间距米,采用连续运行生产方式。
11.3底盘装配线
内饰完成后车身通过升降机转到底盘装配线进行底盘装配工作。
该线全长
米,共工位,工位间距米。
车身裙边距地面1700mm,便于底盘装配,动力总长合装采用静止式装配(合装时车身和动力总成保持相对静止,便于操作)。
11.4最终装配线
车身从底盘线通过升降机落至最终线,该线采用采用地面板链输送机,进行最终内、外饰的装配工作。
该线全长xxm,共xx个操作工位,工位间距xxm,连续运行。
11.5部件装配线
主要的部件装配有:
内饰段车门分装;
底盘段副车架、发动机总成及动力总成分装。
车门分装采用轻型积放式悬挂输送机,共X工位,装配间距~4m,采用连续运行生产方式,速度连续可调。
后副车架分装采用机动辊道输送机或物流台车(工作台),X工位;然后吊到到合装台车上,通过地下通道至底盘线合装工位进行合装;
前副车架分装采用工作台预装,共X工位;发动机总成分装线采用带托盘链式输送机,共X工位;分装好的副车架、发动机总成通过KBK输送至合装线上。
合装线采用机动辊道线输送,共X工位;
11.6真空加注机
为保证装配质量,降低损耗,避免不必要的浪费,整车的油液均采用定量加注,对于处在密闭系统,且管路细小,用一般方法难以加注的液体,比如制冷剂、制动液、防冻液,动力转向机油,采用国产的真空式加注机加注,这种加注机在加注前,先将整个系统抽成近似真空状态,然后进行系统检漏,如果未发现管路泄露,快速将油液加满。
11.7助力机械手
为提高装配质量和效率并降低工人劳动强度,对于较重零部件和人力较难装配的零部件采用助力机械手辅助操作工人完成装配工作,主要零件有:
车门,仪表台总成,风挡玻璃,车轮,座椅等。
五、公用动力需求
1、压缩空气耗量:
一般气动工具消耗量为:
0.3~0.5m3/min;车间压缩空气总耗量,按每个使用点耗量总和的20%~40%计算。
本车间主要为气动工具消耗量。
按5.9m两个气点布置,共有用气点约300个,小时平均消耗量为:
60×0.4×300×0.3=2160m3/h;小时最大耗量为:
60×0.5×300×0.4=3600m3/h。
2、车间耗电量;
各个设备及用电点的耗电量之和,参照设备明细表进行估算。
公用动力需求具体数值如下:
序号
项目
耗量
1
电力
设备总功率
1200kW
2
压缩空气
小时平均耗量
2160m3
小时最大耗量
3600m3
六、环境保护要求
本项目要求环保、消防、劳动安全、职业卫生等设施与主体工程同时设计、同时施工、同时投入使用,切实做到“三同时”
1、环境保护
本项目产生的大气污染物主要来自汽车尾气的排放,主要含有NO、CO、HC微粒及碳烟,同时散发大量热量.本项目采用地下烟道排放方式,汽车尾气经与空气混合降温后由风机排放到大气中稀释.
2、劳动安全
(1)劳动安全卫生采用JBJ18-88<<机械工业职业安全卫生设计规定>>.
(2)所有的电气劳动采用GB4046-83<<电气设备安全设计导责>>.
(3)物流运输、道路的安全采用GB4387-84<<工业企业厂区运输安全规定>>.
(4)放火防爆执行GBJ16-87<<建筑设计防火规范>><2001年版>的规定.
(5)防尘、防毒劳动卫生设计执行TJ36-79<<工业企业设计卫生标准>>的规定.
(6)噪声控制执行GBJ87-85<<工业企业噪声控制设计规范>>的规定.