毕业论文佳能复印机机芯零件冲压.docx
《毕业论文佳能复印机机芯零件冲压.docx》由会员分享,可在线阅读,更多相关《毕业论文佳能复印机机芯零件冲压.docx(52页珍藏版)》请在冰豆网上搜索。
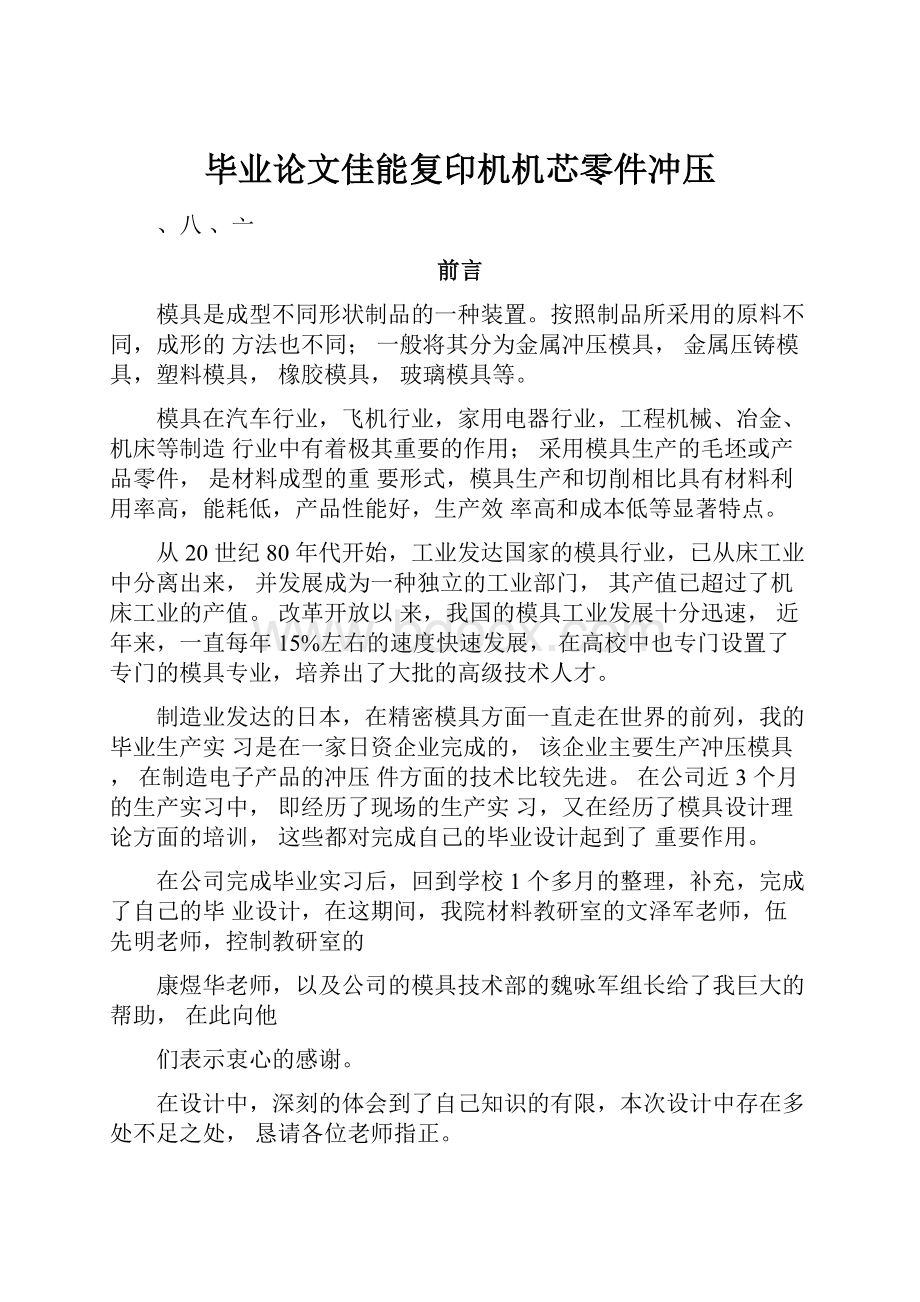
毕业论文佳能复印机机芯零件冲压
、八、亠
前言
模具是成型不同形状制品的一种装置。
按照制品所采用的原料不同,成形的方法也不同;一般将其分为金属冲压模具,金属压铸模具,塑料模具,橡胶模具,玻璃模具等。
模具在汽车行业,飞机行业,家用电器行业,工程机械、冶金、机床等制造行业中有着极其重要的作用;采用模具生产的毛坯或产品零件,是材料成型的重要形式,模具生产和切削相比具有材料利用率高,能耗低,产品性能好,生产效率高和成本低等显著特点。
从20世纪80年代开始,工业发达国家的模具行业,已从床工业中分离出来,并发展成为一种独立的工业部门,其产值已超过了机床工业的产值。
改革开放以来,我国的模具工业发展十分迅速,近年来,一直每年15%左右的速度快速发展,在高校中也专门设置了专门的模具专业,培养出了大批的高级技术人才。
制造业发达的日本,在精密模具方面一直走在世界的前列,我的毕业生产实习是在一家日资企业完成的,该企业主要生产冲压模具,在制造电子产品的冲压件方面的技术比较先进。
在公司近3个月的生产实习中,即经历了现场的生产实习,又在经历了模具设计理论方面的培训,这些都对完成自己的毕业设计起到了重要作用。
在公司完成毕业实习后,回到学校1个多月的整理,补充,完成了自己的毕业设计,在这期间,我院材料教研室的文泽军老师,伍先明老师,控制教研室的
康煜华老师,以及公司的模具技术部的魏咏军组长给了我巨大的帮助,在此向他
们表示衷心的感谢。
在设计中,深刻的体会到了自己知识的有限,本次设计中存在多处不足之处,恳请各位老师指正。
第一章制件的工艺分析
设计中的冲压制件是佳能复印机的一个机芯零件。
冲压件制件的电子图档是由客户提供,如图1-1所示。
由制件零件图可以知道:
制件的外形不规则,需要经过多次冲裁才能完成加工,制件有两个向上的L曲;因此采用切废料的排样方法。
通过对零件的初步分析可知,要完成该制件的生产,需要经过以下工艺:
冲孔、弯曲、落料,切舌等工艺。
冲压件的精度要求较高,最小的误差要求在±0.1mm以内,平面度要求在±0.3mm以内,为了保证其平面度要求,在设计中有必要加入校平工位;制件的厚度为0.2mm,属于薄材料类冲裁,选用用卷料;冲压件的材料客户要求用SUS304,即我国的不锈钢材料。
查阅《模具设计手册》,将设计中的材料确定为:
Cr18Ni9材料。
另外,在设计中还应该考虑到不锈钢材料的冲裁工艺性,以及其纤维方向的特性。
在制件图技术要求中我们可以知道:
客户对模具的材料有严格要求,要求用环保材料,模具材料中不能够含有对自然环境有严重污染的金属元素,必须满足QS9000环保要求。
由《模具设计手册》可以知道:
制件在冲裁外形时要求两个相交边尽量避免锐角,严禁尖角,圆角半径R>=0.25t,冲裁件的凸出或凹入不宜太小,应避免长悬臂和窄臂和窄槽,要求悬臂和槽长L与其宽度B应有一定的比列。
钢板时,B>=(1.3至1.5)t,有色金属板时,B>=(0.75至0.8)t,L<=3B。
冲裁孔与孔之间、孔与冲件边缘之间的壁厚不应太小,否则会影响凹模强度、寿命和冲件质量。
通过对制件零件图分析,可知其满足以上要求。
由于制件材料是不锈钢材料,具有良好的弯曲工艺性,在设计中应该考虑到其纤维方向,以利于模具的设计与制造,弯曲时折弯线的方向不能够与带料的纤维方向一致,应该垂直带料的纤维方向或者与其纤维方向成一定的角度,最好的角度为成45度;弯曲件的弯曲半径不应过小或过大,如果弯曲半径过小,容易被弯裂;若弯曲半径过大,因受到回弹影响,弯曲成形角度和圆角半径的精度均不容易得到保证;同时,在设计中还应该考虑到弯曲件直边高度不宜太短,即使弯曲半径R=0时,也要使最小直边长度大于1.3T,一般弯曲件直边高度H大于2T。
由制件零件图资料可以知道:
制件弯曲工艺满足以上要求。
由于制件属于薄材料冲压加工,带料的厚度为0.2mm,因此对于弯曲半径小于0.2mm的90度角弯曲,在设计中可以将其看作弯曲半径为0mm的弯曲。
冲压制件的年产量为200万件,属于大批量生产;制件外观的最大长度为53mm,宽度为27mm,属小型制件,由于其形状较复杂,生产效率要求高,因此我们设计生产效率高的级进模来完成
此制件的生产
零件图
B-BA部放大
(2:
1)(2:
1)
40-6»t
46
30
0.0.
3业
TH
图1-1制件图
第二章制件的排样
排样是模具设计的核心部分,排样的方式决定了模具结构,凹模的分布等方面内容。
在进行排样之前,首先需要对制件的电子图档进行展开,其过程如下。
第一节制件产品图的展开
展开原理:
材料在弯曲时,一边压缩变形,另外一边会拉伸变形,
但在材料弯曲过程中,有一层不发生压缩和拉伸变形其长度在整个弯曲过程中不发生变化,叫做中性层。
中性层示意图如图
其长度等于制件的
图2-1中性层示意图
展开长度。
中性层计算公式为:
[9*2(R+r)*3.14]/360=pT
上式中B表示制件弯曲的角度;R表示弯曲半径;p表示弯曲系数,由于弯曲是薄材料弯曲,且弯曲半径小于0.2mm;根据APS模具设计标准,将其看作弯曲半径R=0mm的弯曲,对于弯曲半径为0mm的薄材料弯曲,系数p取0.4;T表示带料的厚度,设计中为0.2mm;r表示中性层的半径。
则可以求得中性层的半径为:
r=0.255T
设计中制件的中性层半径为:
r=0.255*0.2=0.051mm
产品图的展开需要经过以下步骤:
一、目标值的选取
冲压件零件各部分的作用不同,其在精度和工艺等方面的要求也不同,设计中根据冲压件零件图的公差确定目标值。
制件目标值的选取原则如下:
1、冲圆孔、异形孔目标值的确定原则:
孔在冲裁时,冲头易磨损,加工过程中越来越小,为此孔(包括圆孔,异形孔)的尺寸目标值取其公差偏上限,结合APS设计标准,此情况下的目标值L=基本尺寸L1+(1/2倍公差的上偏差值)+0.05mm至0.1mm的余量。
2、外形尺寸的确定:
外形在成型中,因凹模在冲裁过程中由于摩擦方面的原因,其外形会逐渐变大,为了保证冲压制件的精度,延长模具的使用寿命,提高其的经济性,其目标值的确定时在误差范围内应该尽量取下限值,结合APS设计标准,在此情
况下的目标值的取法为:
目标值L=基本尺寸L1—(1/2下偏差)
由制件图的技术要求和尺寸公差可以知道,客户在制件的夕卜形尺寸上要求不是很严格。
因此,对于无公差要求的外形尺寸其目标值取为其基本尺寸即可以满足设计要求。
为了方便叙述,首先将制件各部分进行分区,冲压件分区图女口图2-2所示
图2-2制件冲裁区分类图
设计中目标值确定的相关计算为:
对于A区的基本尺寸2.5mm的目标值:
L=L1+(1/2)
取法相同
E
区的基本尺寸31mm
的目标值:
K=L1+
(1/2)
△
-0.05=31
-0.3/2-0.05=30.08mm;
E
区基本尺寸10mm
的目标值:
L=L1+
(1/2)
△
+0.05=10+0.3/2+0.05=10.20mm;
E
区基本尺寸3mm
的目标值:
L=L1+
(1/2)
△
-0.05=3
-0.3/2-0.05=2.98mm;
E
区基本尺寸1.4mm
的目标值:
L=L1+
(1/2)
△
+0.05=1.4+0.3/2+0.05=1.60mm。
制件的外形基本尺寸为49mm,则其目标值L=L1-(1/2)△=49-0.2/2=48.90mm。
制件取目标值后和原图的比较如图2-2所示:
注:
L表示目标值;L1表示基本尺寸;△表示上偏差或下偏差;对于冲孔尺寸较小部分为制件原来的尺寸,扩大后的尺寸为取目标值后的尺寸,对于外形尺寸缩小部分为目标值。
二、产品图的展开
展开方法:
以AUTOCAD电子的图档为基础,将制件图改画为
加工状态的平面图。
展开过程:
(1)确定展开基准面,设计中以主视图为其基准面。
(2)以折弯线内侧线为基准,计算折弯部分的补偿尺寸。
补偿尺寸△L=0.4*T=0.2*0.4=0.08mm
(3)对弯曲面进行拉伸,由上面的计算得到设计中拉伸量为
0.08mm,得其展开图,如图2-3所示:
图2-3制件展开和原图对比
在展开过程中需要注意以下三个方面的问题:
(1)折弯的形式不同,弯曲的系数也就不同。
(2)同样的形式,材料不同,弯曲系数也不同。
(3)折弯角度和R值变化,则计算方法也发生变化。
第二节制件成形工艺的设计和工位确定
由制件的结构形状可以知道,要冲压出该制件需要的经过的基本工序为:
冲孔,落料和弯曲等工艺过程。
经过分析,有三种工艺方案可以实现该冲压件的加工,分别如下:
方案一:
冲裁导正孔一冲裁外形C区,冲裁工艺孔A区,冲裁
工艺孔B区,冲裁外形D区和冲裁下一工位制件的D区-冲裁工艺孔E区一向上弯曲F区,切舌A区,切舌B区一冲裁外形G区和下一制件的G区,冲裁外形H区-向上弯曲I处-空工位-校
平-切断连样区J和K两处。
方案二:
冲裁导正孔-冲裁工艺孔A区,冲裁工艺孔B区,冲
孔裁E区-冲裁外形C区,冲裁外形D区和冲裁下一工位制件的
D区一向上弯曲F处,切舌A区,切舌B区一冲裁外形H区,冲裁外形G区和下一制件的G区—向上弯曲I处—空工位—校平—切断连样区J和K两处。
方案三:
冲裁导正孔一冲裁外形C区,冲裁工艺孔A区,冲裁工艺孔B区,冲裁外形D区和冲裁下一工位制件的D区-冲裁工艺孔E区一冲裁外形G区和下一制件的G区,冲裁外形H区一空工位-向上弯曲F处,切舌A区,切舌B区-向上弯曲I处-校平-切断连样区J和K两处。
经分析,可知道:
方案一的优点是模具结构比较简单,易加工,制造周期短,制件的弯曲精度,平面度,尺寸、外观形状等容易得到保证,在设计中设置空工位即有利于调节又有利于产品的变更时模具的改进设计。
方案二具有方案一的某些优点,但在第二工位处,由于孔和孔之间的距离比较小,不利于凸模在卸料板上的固定,且由于冲裁带料薄,冲裁量大过大,容易使带料产生畸形变形。
方案三同样具有方案一某些优点,但其弯曲设置在最后两个工位,弯曲处处于悬臂状态,弯曲强度不够,不利于制件的弯曲成形,且弯曲成形的精度也不容易得到保证。
综合以上分析,确定工艺方岸方案一为最佳工艺方案。
下一步确定个各工位的内容:
由上面工艺过程分析,可以设计出级进模各冲压工位的冲裁内容。
根据工艺分析将各工位的冲裁内容设计如下:
工位一设计为:
冲导正孔;工位二设计为:
冲裁外形C区,冲工艺孔A区,冲工艺孔B区,冲裁外形D区和冲裁下一工位制件的D区;工位三设计为:
冲裁工艺孔E区;工位四设计为:
向上弯曲F处,切舌A区,切舌B区;工位五、六设计为:
冲裁外形G区和下一制件的G区,冲裁外形H区;工位七设计为:
向上弯曲I处,工位八设计为:
空工位;工位九设计为:
校平工位;工位十设计为:
切断连样区J和K两处。
第三节制件的排样
在冲压件的成本中,材料的费用占60%以上,因此材料的经济利用有非常重要的意义。
冲压件在材料或板料上的布置方法称为排样。
衡量排样经济性的指标是材料的利用率。
不合理的排样方式会浪费材料,并且还可能影响到制件的质量,影响模具的结构设计的合理性;影响模具的使用寿命,制件的生产效率和模具的成本等技术、经济指标等。
排样的常用方法有:
有废料排样法;少废料排样法;无废料排样法。
设计中由于制件的外形比较复杂,采用裁搭边法,将制件的加工通过分次裁切来完成。
分次排样法设计加工出来的具有制件精度高,便于模具凹模、凸模的排布等优点。
制件的排样的具体过程如下;
一、制件的排样方法
排样方法:
可制作冲压件展开毛坯样板(3至5个),在图面上反复试排,综合考虑材料利用率,带料纤维性等因素,确定初步方案,再在AUTOCAD软件中对制件展开图进行排布,在初步的排样图中按照冲压工序设计的基本原则,进行冲裁工位设计。
在排样图的开始端一般安排冲孔、切废料等分离工位,再向另外一端依次安排成形工位,最后安排制件和载体的分离工位。
在安排工位时,要尽量避免冲小半孔,以防凸模因受力不均而折断。
二、制件件的排样原则
1、第一工位一般安排冲孔和冲工艺导正孔,第二工位设置导正销对带料导正,在以后的工位中,视其工位数和易发生窜动的工位设置导正销,也可以在以后的工位中每隔2至3个工位设置
导正销,本设计制件的精度要求较高,为了保证制件的精度,每
一个工位均设计导正销。
第三工位根据带料的定位精度,可以设置步距的误送检测装置。
结合排样图,考虑到模具的整体布局,在第五工位设置步距的误送检测装置。
2、冲压件上孔数较多,且孔的位置相隔太近时,可以分布在不同的工位上冲出,但孔的位置不能因后续成形工序而影响变形。
对位置要求高的多孔,应考虑同步冲出。
3、为提高凹模镶块、卸料板和固定板的强度,便于产品的变更和保证各成形零件安装位置不发生干涉,可在排样中设置空工位。
其数量根据模具的结构要求设定。
4、为了提高材料利用率,在不影响制件使用性能指标的前提下,可以适当的改变制件的形状。
5、排样时应考虑使设计出来的模具使用方便,劳动强度小且
安全。
6、模具结构应该尽量简单。
7、保证制件质量和制件对条料纤维方向的要求。
三、搭边值的确定
排样时制件与制件之间以及制件与侧边之间留下的工艺材料,叫做搭边。
其作用是补偿定位误差,保证条料强度,以保证在冲裁过程中带料的送料顺畅。
搭边应选择适当,过大会造成材料的浪费,过小不利于制件的成形,或者冲裁不出合格的制件。
搭边值的大小通常是由经验所确定的。
设计中搭边值的确定参照APS模具设计标准确定。
四、排样的步骤
1、由制件制件的外观形状和制件材料的特点,将设计的排样方式设计为斜排方式。
用纸做出制件的展开样品,进行试排,经过比较将制件的排样图确定为排样图所示的排样方式,在AUTOCAD软件中确定其中心与水平线的角度,经过计算比较可知当其与水平线成45度角时,材料的利用率最高;且由于带料是不锈钢材料,与水平线成45度角刚好满足不锈钢材料纤维方向的要求,同时经比较,这样的排样方式也有利于模具的设计。
2、带料宽度的确定:
带料宽度的确定要经过搭边值的确定,异形凸模刃口间隙的确定等过程;查阅APS模具设计标准,制件的搭边值的确定方法如下:
侧搭边值的确定:
侧搭边是指在级进模中将每个产品沿料宽方向连接起来的部分叫侧搭边。
其确定方法为:
最小侧搭边值Zmin=1*T(0.8mm=6*T(0.4mm=3mm(0.2mm式中T表示带料的厚度
特殊情况下,当T小于0.2mm时,为了保证带料在冲裁过程中送料的顺畅性,在送料方向做两条加强筋。
由于带料为不锈钢材料,强度较高,最小搭边值取3mm即可以满足强度要求。
间隙搭边值的确定:
间隙搭边是指相邻两个制件之间的间隙,查阅模具设计标准,对于薄的不锈钢材料取2mm,即可以满足两个相邻制件在冲裁时的强度要求。
异形凸模最小宽度的确定:
异形凸模最小宽度Bmin=3.0~6.0mm(0.8mm=1.5~2.5mm(0.2mm对于不锈钢条料冲头宽度应该适当的取大些。
在设计中将最小搭边值确定为2.5mm。
参照以上标准,设计中各值确定如下:
带料的宽度:
制件侧搭边尺寸为3mm,异形凸模最小宽度为2.5mm。
则可以确定条料的宽度B。
B=制件宽度+搭边距离*2=53.84+(3+2.5)*2=64.84mm
在设计生产中为了方便带料的采购,需要对其调整为整数,将带料做适当放大,可将料宽度确定为66mm。
3、步矩的确定:
间隙搭边值的确定通常是根据经验确定,在不影响产品质
量的情况下尽量取小些。
在本设计中,制件之间的搭边距离
取为2mm,则:
步距D=制件的排样宽度+2=40.32+2=42.32mm
将其最终调整为整数得步距为43mm(由初步排样图可知,步距可以适当的取小些,可以保证冲裁的顺利进行,也有利于材料利用率的提高)。
4、接刀点的确定:
制件完整外形的形成需要经过分段切除才能完接成,各分段点即为制件的接刀点。
由冲压工位的确定,可知设计中共有八个接刀点,且均为直线型接刀,为了避免制件在冲裁过程中产生毛刺,带料等不赖现象,查阅APS模具设计标准,将接刀点设计为如图3-1所示形状,各接刀点的位置如图所示。
相关数据如下表所示:
图2-4制件接刀示意图
数据表格:
(单位:
mm)
0.81.5-2.0
0.2-0.3
0.41.0-1.5
0.2
0.21.0
0.1-0.2
T
A
B
T:
表示带料的厚度;A表示:
接刀长度;B表示:
接刀宽度
设计中带料的厚度为0.2mm,由上表数据得,接刀处的长度A=1mm;接刀处的宽度B=0.2mm;前后两次冲裁凸模的高度差值H=0.5mm;前后两次冲裁凸模之间的间隙差值L=1mm。
设计中各接刀点的分布图如图2-5所示:
图2-5制件接刀点分布图
5、凹模、凸模刃口形状的确定:
由制件展开图可以知道,要完成制件的加工,需要将带料上的废料冲裁掉,各工位冲裁掉废料的外观形状即为凹模、凸模的刃口形状;对于冲孔凸模,展开图中所取的目标值即为凸模刃口的形状尺寸。
对于制件外观形状不规则部分的成形,其
成形凸模、凹模叫做异形凸模或者异形凹模。
异形凹模或凸模的刃口形状没有固定的设计标准,在满足制件外形的情况下刃口形状可以自己确定,但必须考虑以下条件:
异形凹模、凸模的最小宽度应该大于2.5mm;形状应该力求简单,以利于材料的合理利用,同时要避免细长悬臂结构;转角处要尽量避免尖角,尖角处应该用圆弧连接,以起到避免尖角处因应力集中而使冲模裂开的危险。
对于不锈钢材料,其最小圆角半径的选取标准为:
(T表示带料的厚度)
落料部分:
当圆弧角大于或等于90度时,最小圆角半径
=0.25*T;当圆弧角小于90度时,最小圆角半径=0.5*T;
冲孔部分:
当圆弧角大于或等于90度时,最小圆角半径
=0.30*T;当圆弧角小于90度时,最小圆角半径=0.6*T。
对于弯曲凹模和凸模的设计结构参照APS模具设计标准即可。
各凹模和凸模的刃口形状如AUTOCAD中的排样图档所示。
6、带料的定位方式:
参照APS模具设计标准,对于卷料的定位方式,选用托料钉粗定位,导正销精确定位相结合的定位方式。
托料钉在排样图中分布的相关参数标准为:
第一个托料钉到模板边缘的距离必须为0.5的倍数,取值范围为:
20mm>D>5mm,在设计中将其确定为D=12mm。
其余的托料钉的分布根据排样图来排布,在不和其他零件发生干涉的情况下,托料钉的分布应该尽量均匀,以利于保证带料在冲裁时送料的顺畅。
为了保证加工精度,其必须满足相互之间的距离为0.5的倍数要求。
导正销与托料钉之间的距离必须为0.5的倍数,相互之间不发生干涉,两相邻导正销之间的距离为一个步距,设计中为43mm。
以上就完成了整个制件的排样设计。
第三章力的计算和冲裁间隙的确定
第一节力的计算
一、冲裁力的计算
计算冲裁力的目的是为了选择合适的压力机,设计和检验模具的强度。
压力机的吨位必须大于所计算的冲裁力,以适应冲裁工艺的需求。
冲裁力的计算公式为:
P=KtLSN
上式中各字母的含义分别为:
S表示材料的抗剪强度(MPa);
L表示冲裁周边的总长(mm);
t表示材料的厚度(mm);
K表示安全系数K是考虑到冲裁模具刃口的磨损,凸模、凹模间隙之间波动,润滑情况,材料力学性能与公差的变化等因素而设置的