6压力管道焊接作业指导书详解.docx
《6压力管道焊接作业指导书详解.docx》由会员分享,可在线阅读,更多相关《6压力管道焊接作业指导书详解.docx(17页珍藏版)》请在冰豆网上搜索。
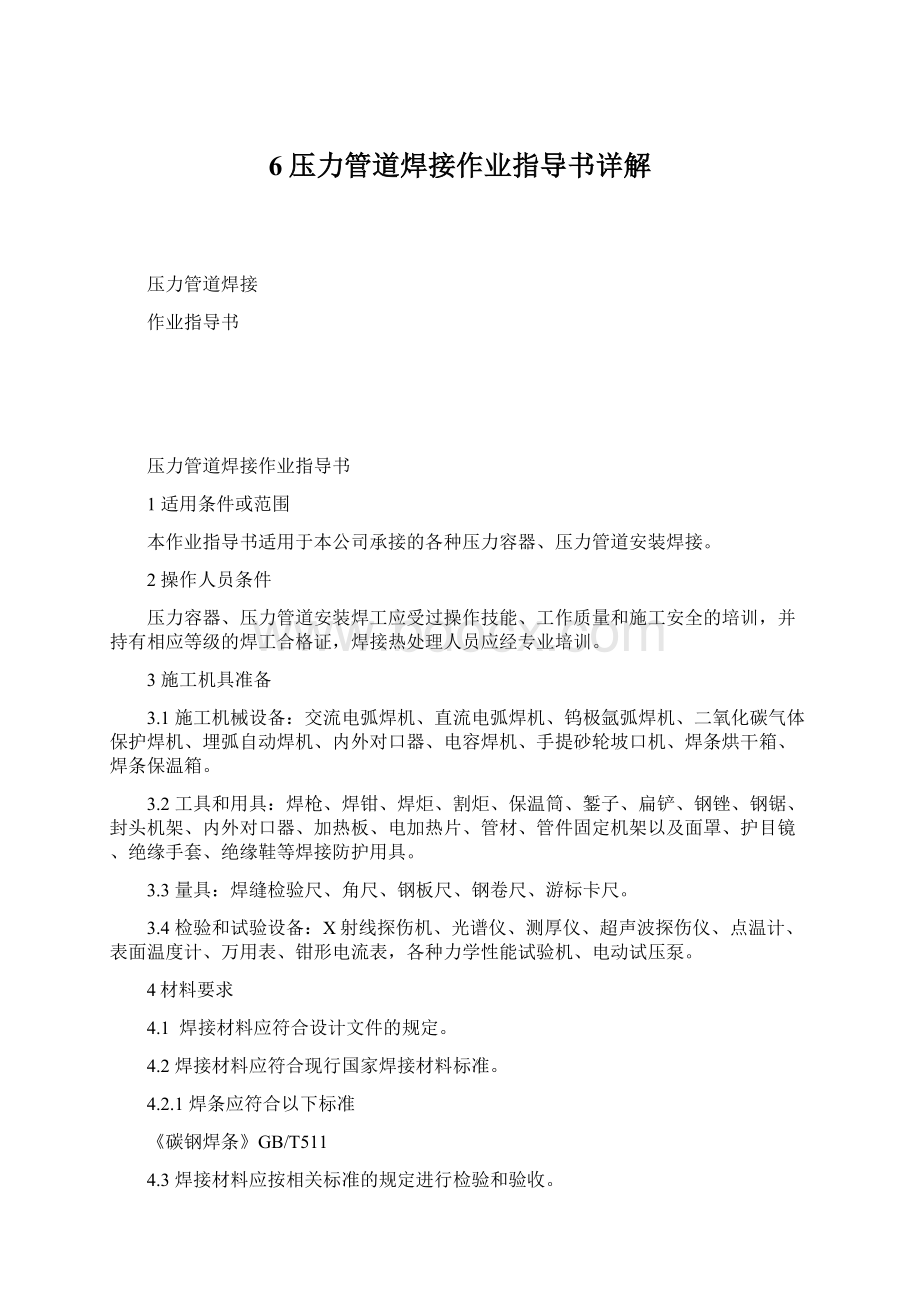
6压力管道焊接作业指导书详解
压力管道焊接
作业指导书
压力管道焊接作业指导书
1适用条件或范围
本作业指导书适用于本公司承接的各种压力容器、压力管道安装焊接。
2操作人员条件
压力容器、压力管道安装焊工应受过操作技能、工作质量和施工安全的培训,并持有相应等级的焊工合格证,焊接热处理人员应经专业培训。
3施工机具准备
3.1施工机械设备:
交流电弧焊机、直流电弧焊机、钨极氩弧焊机、二氧化碳气体保护焊机、埋弧自动焊机、内外对口器、电容焊机、手提砂轮坡口机、焊条烘干箱、焊条保温箱。
3.2工具和用具:
焊枪、焊钳、焊炬、割炬、保温筒、錾子、扁铲、钢锉、钢锯、封头机架、内外对口器、加热板、电加热片、管材、管件固定机架以及面罩、护目镜、绝缘手套、绝缘鞋等焊接防护用具。
3.3量具:
焊缝检验尺、角尺、钢板尺、钢卷尺、游标卡尺。
3.4检验和试验设备:
X射线探伤机、光谱仪、测厚仪、超声波探伤仪、点温计、表面温度计、万用表、钳形电流表,各种力学性能试验机、电动试压泵。
4材料要求
4.1焊接材料应符合设计文件的规定。
4.2焊接材料应符合现行国家焊接材料标准。
4.2.1焊条应符合以下标准
《碳钢焊条》GB/T511
4.3焊接材料应按相关标准的规定进行检验和验收。
4.4焊接材料必须具有制造厂的质量证明书。
4.5现场具有焊接材料储存场所及烘干、去污设施,并应建立保管、烘干、清洗、发放制度。
4.6氩气应符合现行国家标准《氩》GB/T4842的规定,且纯度不应低于99.96%
4.7钨极宜采用铈钨极或钍钨极。
4.8二氧化碳气体的纯度不应低于99.5%,含水量不应超过0.005%,使用前应预热或干燥。
当瓶内气体压力低于0.98Mpa时,应停止使用。
4.9氧乙炔焊所采用的氧气纯度不应低于98.5%,乙炔气应符合现行国家标准《溶解乙炔》GB6819的规定。
5作业条件
5.1施工项目部已配备专业焊接技术人员、焊接检验人员、无损探伤人员。
5.2焊接工装设备、检验实验手段能满足工程项目的技术要求。
5.3已进行相应的焊接工艺评定。
5.4施焊环境符合GB50236规定。
6操作工艺
6.1碳素钢焊接操作工艺
6.1.1本工艺适合于含碳量小于或等于0.30%的碳素钢的现场手工电弧焊、氩弧焊、二氧化碳气体保护焊、埋弧焊及氧乙炔焊。
6.1.2焊缝的设置应避开应力集中区,便于焊接和热处理,并应符合下列规定:
6.1.2.1组对时,相邻两纵向焊缝间的距离应大于壁厚的3倍,且不应小于100mm。
6.1.2.2加热炉受热面管子的焊缝中心与管子弯曲起点,联箱外壁及支、吊架边缘的距离不应小于70mm;同一直管段上两个对接焊缝间的距离不应小于150mm。
6.1.2.3除焊接及成型管件的其他管子对接焊缝的中心到管子弯曲起点距离不应小于管子外径,且不应小于100mm;管子对接焊缝与支、吊架边缘之间的距离不应小于50mm。
同一直管段上两对接焊缝中心面间的距离;当公称直径大于或等于150mm时不应小于150mm;公称直径小于150mm时不应小于管子外径。
6.1.2.4不宜在焊缝及其边缘上开孔,当不可避免时,应符合GB50236的规定。
6.1.2.5焊缝的坡口形式和尺寸应符合设计文件和焊接工艺文件的规定。
当没有特别规定时,埋弧焊焊缝坡口形式及尺寸应符合《埋弧焊的推荐坡口》规定,其他焊缝坡口形式和尺寸应符合《气焊、焊条电弧焊、气体保护焊和高能束焊的推荐坡口》的规定。
6.1.3焊前准备
6.1.3.1焊件的切割和坡口加工宜采用机械方法,也可采用气割等热加工方法,在采用热切割方法加工坡口后,必须除去坡口表面的氧化皮,溶渣及影响接头质量的表面层,并应将凹凸不平处打磨平整。
6.1.3.2焊件组对前应将坡口及其内外侧表面不小于10mm范围内油、漆、垢、锈、毛刺及镀锌层清除干净,且不得有裂纹、夹层等缺陷。
6.1.3.3除设计规定需要进行冷拉伸或冷压缩的管道外,焊件不得进行强行组对。
6.1.3.4管子或管件对接焊缝进行组时,内壁应齐平,内壁错边量不宜超过管壁厚度的10%,且不应大于2mm。
6.1.3.5不等厚对接焊件组对时,薄件端面应位于厚件端面之内。
当内壁错边量超过。
6.1.3.4条规定或外壁错边量大于3mm时,应对焊件按GB50236《现场设备、工业管道焊接工程施工及验收规范》进行加工。
6.1.4焊接工艺要求
6.1.4.1焊材选用,应按照母材的化学成分、力学性能、焊接接头的抗裂性,焊前预热、焊后的热处理、使用条件及施工条件等因素综合确定,且焊接工艺性能良好。
6.1.4.2定位焊接缝应符合下列规定:
a.焊接定位焊缝时,应采用与根部焊接道相同的焊接材料和焊接工艺,并应由合格焊工施焊。
b.定位焊缝的长度、厚度和间距,应能保证焊缝在正式焊接过程中不致开裂。
c.在焊接根部焊道时,应对定位焊缝进行检查,当发现缺陷时应处理后方可施焊。
d.与母材焊接的工卡具其材质宜与母材相同或同一类别号。
拆除工卡具时不应损伤母材,拆除后应将残留焊疤打磨修理至与母材表面齐平。
6.1.4.3严禁在坡口之外的母材表面引弧和试验电流,并应防止电弧擦伤母材。
6.1.4.4焊接时应采取合理的施焊方法和施焊顺序。
6.1.4.5施焊过程中应保证起弧和收弧处的质量,收弧时应将弧坑填满。
多层焊的层间接头应错开,管子施焊时,管内施焊时应防止穿堂风。
6.1.4.6除工艺或检验要求需分次焊接外,每条焊缝宜一次连续焊完,当因故中断焊接时,应根据工艺要求采取保温缓冷或后热等防止产生裂纹的措施,再次焊接前,应检查焊层表面确认无裂纹后,方可按原工艺要求继续施焊。
6.1.4.7需预拉伸或预压缩的管道焊缝,组对时所使用的工卡具在整个焊接及热处理完毕并经检验合格后方可拆除。
6.1.5焊前预热及焊后热处理
6.1.5.1碳素钢焊接时,一般不采用焊前预热及焊后热处理,只在下述情况时才进行预热及焊后热处理。
6.1.5.2当焊件温度低于0℃时,钢材的焊缝应在始焊处100mm范围内预热到15℃以上。
6.1.5.3对有应力腐蚀的焊缝,应进行焊后热处理。
6.1.5.4焊前预热的加热范围,应以焊缝中心为基准,每侧不应小于焊件厚度的3倍;焊后热处理的加热范围,每侧应不小于焊缝宽度的3倍,加热带以外部分应进行保温。
6.1.5.5焊前预热及焊后热处理中,焊件内外壁温度应均匀。
6.1.5.6焊前预热及焊后热处理时,测量和记录温度的部位和数量应合理,测温仪表应经计量检验合格。
6.1.5.7焊前的预热和后热处理温度应符合设计要求或焊接工艺文件的规定,当无规定时,碳素钢的焊前预热及焊后热处理温度宜符合表1的规定。
碳素钢管材焊前预热及焊后热处理工艺条件表1
钢种
焊前预热
焊后热处理
壁厚δ(mm)
温度℃
壁厚δ(mm)
温度℃
C
≥26
100~200
>30
600~650
6.1.5.8对热处理后进行返修的焊缝,返修后重新进行热处理。
6.2合金钢焊接操作工艺
6.2.1适用范围:
本工艺适用于低合金结构钢、低温钢、耐热钢、耐热耐蚀高合金等合金钢的手工电弧焊、氩弧焊、二氧化碳气体保护焊、埋弧焊及氧乙块焊。
6.2.2焊缝的设置应避开应力集中区,便于焊接和后热处理,并应符合6.1.2.1、6.1.2.2、6.1.2.3、6.1.2.4、6.1.2.5的规定。
6.2.3焊前准备
合金钢的焊接前的准备工作与6.1.3的要求相同。
6.2.4焊接工艺要求
6.2.4.1焊材选用应按照母材的化学成分、力学性能、焊接接头的抗裂性、焊前预热、焊后热处理、使用条件及施工条件等因素综合确定,且焊接工艺性能应良好。
6.2.4.2定位焊缝应符合6.1.4.2的规定。
6.2.4.3严禁在坡口之外的母材表面引弧或试验电流,并应防止电弧擦伤母材。
6.2.4.4对含铬量大于或等于30%或合金元素总含量大于5%的焊件,氩弧焊打底焊接时,焊缝内侧应充氩气或其他保护气体,或采取其他防止内侧焊缝金属被氧化的措施。
6.2.4.5焊接时应采取合理的施焊方法和施焊顺序。
6.2.4.6施焊过程中应保证起弧和收弧的质量,收弧时应将弧坑填满,多层焊的层间接头应错开。
管子施焊时,管内应防止穿堂风。
6.2.4.7除工艺或检验要求需分次焊接外,每条焊缝宜一次连续焊完,当因故中断焊接时,应根据工艺要求采取保温缓冷或后热等防止产生裂纹的措施,再次焊接前应检查焊层表面,确认无裂纹后,方可按原工艺要求继续施焊。
6.2.4.8低温钢、耐热耐蚀高合金钢接头焊接时,应符合下列规定:
a.应在焊接作业指导书规定的范围内,在保证焊透和熔合良好的条件下,采用小电流、短电弧、快速焊接多层多道焊工艺,并应控制层间温度。
b.对抗腐蚀性能要求高的双面焊缝,与腐蚀介质接触的焊层应最后施焊。
c.低温钢焊接完毕,宜对焊缝进行表面焊道退火处理。
6.2.5焊前预热及焊后热处理。
6.2.5.1进行焊前预热及焊后热处理应根据钢材的淬硬性、焊件厚度、结构刚性、焊接方法及使用条件等因素综合确定。
6.2.5.2要求焊前预热的焊件,其层间温度应在规定的预热温度范围内。
6.2.5.3当焊件温度底于0℃时,所有钢材的焊缝应在始焊处100mm范围内预热到10℃以上。
6.2.5.4对有应力腐蚀的焊缝,应进行焊后热处理。
6.2.5.5调质钢焊缝的焊后热处理温度,应低于其回火温度。
6.2.5.6焊前预热的加热范围,应以焊缝中心为基准,每侧不应小于焊件厚度的3倍;焊后热处理的加热范围,每侧不应小于焊缝宽度的3倍,加热带以外部分应进行保温。
6.2.5.7焊前预热及焊后热处理中,焊件内外壁温度应均匀。
6.2.5.8焊前预热及焊后热处理时,应测量和记录其温度,测温点的部位和数量应合理,测温仪表应经计量检定合格。
6.2.5.9对容易产生焊接延迟裂纹的钢材,焊后应及时进行焊后热处理,当不能及时进行焊后热处理时,应在焊后立即均匀加热到200~300℃,并进行保温缓冷,其加热范围应与焊后热处理要求相同。
6.2.5.11当采用钨极氩弧焊打底时,焊前预热温度可按表2规定的下限温度降低50℃。
6.2.5.12焊后热处理的加热速率、热处理温度下的恒温时间及冷却速率应符合GB50236的规定。
6.2.5.13对热处理后进行返修的焊缝,返修后应重新进行热处理。
6.3金属管道全位置下向焊工艺
6.3.1本工艺适合于大直径低碳钢、低合金钢管道的全位置下向焊。
6.3.2用于下向焊的纤维素型焊条因药皮含有大量有机物,应妥善保管以防受潮。
焊条一旦受潮应在70℃~80℃下烘烤0.5~1.0小时,烘烤温度最多不能超过100℃。
烘烤次数不能超过2次。
低氢型下向焊条则应按产品说明书要求严格烘干。
6.3.3焊前应将坡口两侧50mm范围内的油、锈、水等杂质清除干净。
按设计要求或表3的规定进行焊口组对。
下向焊管口组对尺寸表3
采用的下向
焊条种类
单边坡口
角度
钝边高度
对口间隙
错边量
错边长度
纤维素型
30~35°
1.2~2.0mm
1.2~2.0mm
≤0.8mm
≤周长的10%
低氢型
30~35°
0.8~1.6mm
2.4~3.2mm
≤1.2mm
6.3.4焊前按本指导书表1和表2的要求进行预热。
6.3.5管径≥400mm的管道,采取二人对称焊法;管径≥700mm的管道;采取三人对称焊法。
6.3.6焊条运条角度可按表4选取(表中12点、3点等指钟点位置)。
焊条运条角度表4
焊道
焊