塑料模具复习资料.docx
《塑料模具复习资料.docx》由会员分享,可在线阅读,更多相关《塑料模具复习资料.docx(19页珍藏版)》请在冰豆网上搜索。
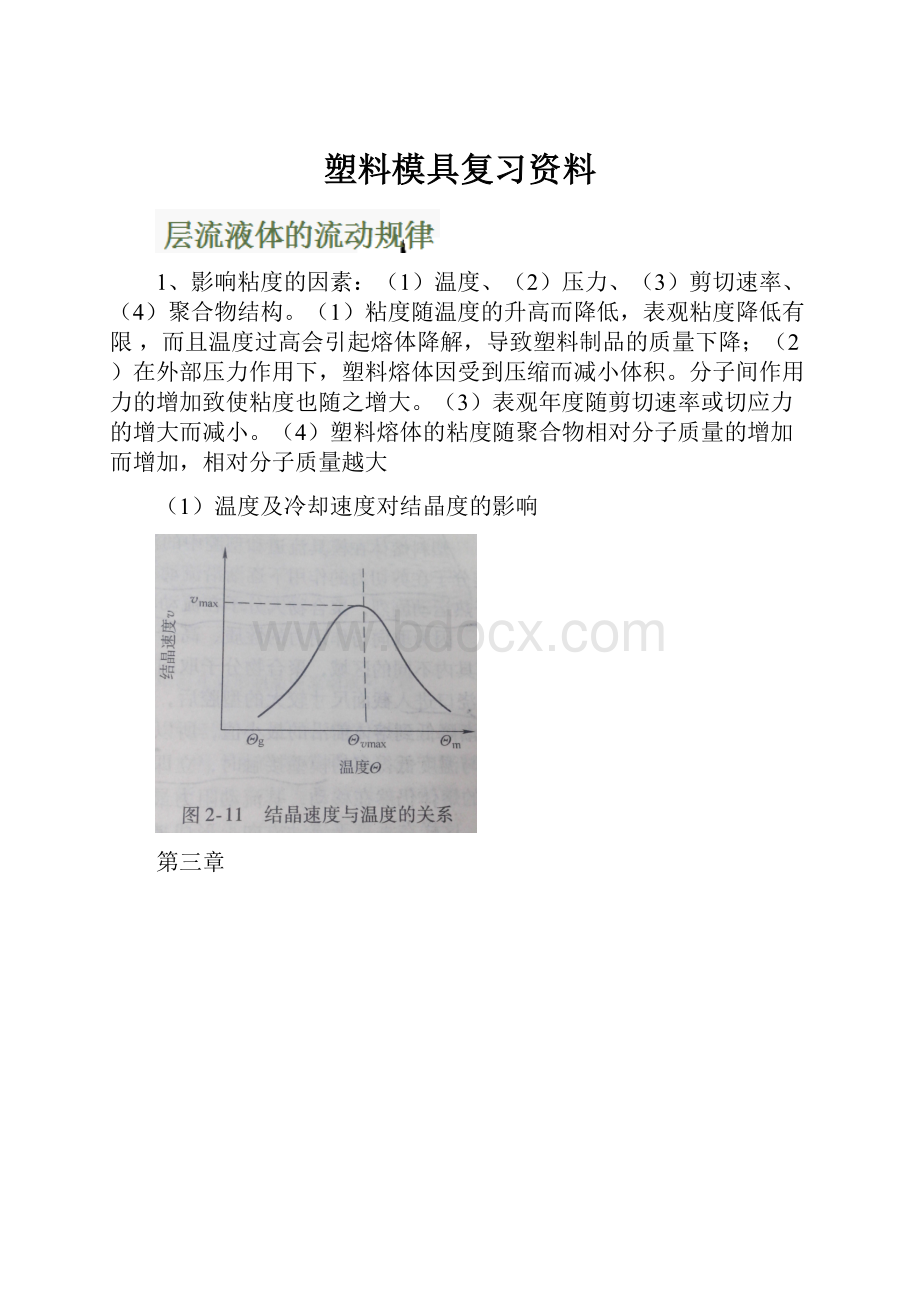
塑料模具复习资料
1、影响粘度的因素:
(1)温度、
(2)压力、(3)剪切速率、(4)聚合物结构。
(1)粘度随温度的升高而降低,表观粘度降低有限,而且温度过高会引起熔体降解,导致塑料制品的质量下降;
(2)在外部压力作用下,塑料熔体因受到压缩而减小体积。
分子间作用力的增加致使粘度也随之增大。
(3)表观年度随剪切速率或切应力的增大而减小。
(4)塑料熔体的粘度随聚合物相对分子质量的增加而增加,相对分子质量越大
(1)温度及冷却速度对结晶度的影响
第三章
2.柱塞式注射机
柱塞式注射机示意图1.注射模2喷嘴3料筒4.分流锥5.料斗6.注射柱塞
柱塞在料筒内仅作往复运动,将熔融塑料注入模具。
分流锥将筒内流经该处的塑料分成薄层,使塑料分流,以加快热传递。
同时塑料熔体分流后,在分流锥表面流速增加,剪切速率加大,剪切发热使料温升高、粘度下降,塑料得到进一步混合和塑化。
柱塞式注射机的注射量不宜过大,一般为30~60g,而且不宜用来成型流动性差、热敏性强的塑料制品。
螺杆式注射机:
螺杆的作用是送料、压实、塑化与传压。
当螺杆在料筒内旋转时,将料斗中的塑料卷入,逐步将其压实、排气、塑化,并不断地将塑料熔体推向料筒前端,积存在料筒顶部与喷嘴之间,螺杆本身受到熔体的压力而慢慢后退。
当积存的熔体达到预定的注射量时,螺杆停止转动,并在液压缸的驱动下向前推动,将熔体注入模具。
优点:
①塑化效果好②注射量大③生产周期短、效率高④容易实现自动化生产⑤设备价格较高。
3.注射工艺过程包括成型前的准备、注射过程和制品的后处理
包括:
加料、塑化、充模、保压、倒流、冷却和脱模等步骤。
4.模具温度和注射压力对塑料成型性能的影响
有利于提高制品的强度和刚度
P43最小壁厚及推荐值表
1、脱模斜度:
一般脱模斜度取0.5°,最小为15′~20′
脱模斜度的选择原则:
1)脱模斜度取决于塑件的形状、壁厚及塑料的收缩率,一般
取
2)成型型芯越长或型腔越深,则斜度应取偏小值
3)塑件高度不大(小于2~3mm)时可不设计脱模斜度
4)当使用上有特殊要求时,脱模斜度可采用外表面(型腔)
为,内表面(型芯)为
5)开模后为了使塑件留在凹模内(凸模上),往往有意地减小
凹模的脱模斜度(或者相反)
6)热固性塑料一般较热塑性塑料收缩要小一些,故脱模斜度
也应相应小一些
脱模斜度的取法:
1)外形以大端为基准,斜度由缩小方向取得2内形以小端为基准,斜度由扩大方向取得
2、塑件的圆角
5、塑件上孔的设计
塑件上的固定孔与其它受力孔的周围应采用凸边予以加强。
有些斜孔或形状复杂的孔可采用拼合的型芯成型,以避免侧向抽芯
塑件内侧凹较浅并允许带有圆角时,则可以用整体凸模采取强制脱模的方法使塑件从凸模上脱下
注射模具的组成
根据模具上各部件所起的作用,可细分为以下几个部分。
(1)成型部件:
(2)浇注系统:
(3)导向机构(4)侧向分型与抽芯机构5)推出机构(6)温度调节系统(7)排气系统(8)标准模架
注射模均由动模、定模两大部分构成。
注射模的结构
1-动模板2-定模板3-冷却水道4-定模座板5-定位圈6-浇口套7-凸模8-导柱9-导套10-动模座板11-动模垫板12-限位钉13-推板14-推杆固定板15-拉料杆16-推板导柱17-推板导套18-推杆19-复位杆20-垫块21-注射机顶杆
注射模具的分类
单分型面注射模、双分型面注射模、带侧向分型与抽芯机构的注射模、单型腔注射模、多型腔注射模、自动卸螺纹注射模、无流道注射模等
按浇注系统结构形式可分:
普通浇注系统注射模、热流道浇注系统注射模
按塑料性质可分为:
热塑性塑料注射模具、热固性塑料注射模具
按成型技术可分为:
低发泡注射模、精密注射模、气辅成型注射模、双色注射模、多色注射模
单分型面注射模
注射模中较简单的一种结构形式。
这种模具只有一个分型面
双分型面注射模
A-A分型面取出浇注系统凝料;
B-B分型面取出塑件
双分型面增加一块中间板(浇道板),所以也叫三板式注射模(动模板、浇道板、定模板)。
常用于针点浇口进料的单腔或多腔模具。
双分型面注射模
1—垫块2—动模垫板3—动模板(型芯固定板)
4—推件板5—导柱6—限位销7—弹簧
8—定距拉板9—型芯10—浇口套11—定模座板
12—定模板13—导柱4—推杆15—推杆固定板
16—推板
三板模之特性:
结构较复杂,模具成本较高,寿命不长。
成品不需剪水品
进浇位置易调整,表面质量好
成型周期较长,塑胶残料较多
二板模与三板模的比较
模具结构上三板模多了块脱料板、拉杆、开闭器,导柱放置的方向性也与二板模不同。
侧向分型与抽芯注射模
当塑件侧壁有孔、凹槽或凸起时,其成型零件必须制成可侧向移动的,否则塑件无法脱模。
侧向抽芯机构由斜导柱10、侧型芯滑块11、楔紧块9、挡块5,滑块拉杆8、弹簧7、螺母6组成
定位装置:
由挡块5、滑块拉杆8、螺母6、弹簧7和垫片等组成。
作用:
保证滑块不侧向移动,合模时斜导柱能顺利地插人滑块的斜导孔中使滑块复位
楔紧块的作用:
防止注射时熔体压力使侧型芯滑块产生位移,楔紧块的斜面应与侧型芯滑块上斜面的斜度一致.楔紧块的斜度较斜销大2~3°
斜导柱侧抽芯注射模
1—动模座板2—垫块3—支承板4—动模板5—挡块6—螺母7—弹簧8—滑块拉杆
9—锁紧楔10—斜导柱11—滑块12—型芯13—浇口套14—定模板15—导柱16—动模板
17—推杆18—拉料杆19—推杆固定板20—推板
带有活动镶块和嵌件的注射模
有的塑料制品带有内侧凸、凹槽或螺纹等,为简化模具结构,需要在模具上设置活动镶件:
活动型芯、螺纹型芯、型环或哈夫块等。
应注意:
1.活动镶件在模具中应有可靠的定位和正确的配合
2.推杆先复位,否则活动镶件将无法放人安装孔内
3.省去了斜导柱、节约了空间,但工作安全性差、生产效率低。
带有活动镶块的注射模
1—定模座板(兼凹模)2—导柱3—活动镶块
4—型芯座5—动模板6—动模垫板7—模底座
8—弹簧9—推杆10—推杆固定板11—推板
角式注射模用注射模
主流道、分流道开设在分型面上,而且主流道截面的形状一般为圆形或扁圆形,注射向与合模方向垂直,特别适合于一模多腔、塑件尺寸较小的注射模具。
定模设置推出机构的注射模(塑料衣刷注射模)
因推出机构一般设在动模一侧,所以注射模开模后,塑件应留在动模一侧。
但有时因塑件的特殊要求或受塑件形状的限制,开模后,塑件留在定模上(或有可能留在定模上),则应在定模一侧设置推出机构。
常选用定距分型推出机构.所示为塑料衣刷注射模。
动作过程:
动模部分向后退,动模和推件板分型,动模部分继续后退至螺钉4碰到拉板左端,动模再继续后退,拉板后退碰到螺钉6,拉板两端卡住,拉板带动推件板继续左移,推出制件,之后再合模机构下模具合模。
定模一侧设推出机构的注射模
1—模脚2—支承板3—成型镶块4、6—螺钉5—动模板7—推件板8—拉板9—定模板
10—定模座板11—型芯12—导柱
型腔数目的确定
1.按技术参数确定型腔数目
(1)根据注射机的额定锁模力确定型腔数目
(2)根据注射机的最大注射量确定型腔数目
(3)根据制品精度确定型腔数目(4).根据经济性确定型腔数目
a、与开模方向垂直的分型面b)斜分型面c)阶梯分型面d)曲面分型面
模具钢性能:
1、可加工性好,热处理变性好,可淬透性好
2、抛光性能好,加工后的成型部位表面应该光滑美观
3、耐磨性好,以便延长模具模具寿命
4、具有足够的机械强度
5、耐腐蚀性好,在使用中不易生锈。
模具钢材:
碳素钢、合金钢、塑料模具钢
1—推杆,推出塑件;2—推杆固定板,固定推杆等;3—推板导套;4—推板导柱;5—推板;6—拉料杆;7—复位杆8—限位钉,
传递太大的力,动作不可靠,弹簧易失效,只适用于小型制品的注射模。
(4)依靠棘爪二次推出
(3)机动脱模方式
在机动脱模机构中,经常利用齿轮与齿条或者锥齿轮等装置,将开模的直线运动转变为旋转运动,以便将带有螺纹的制品脱模,如图,通过齿轮齿条及锥齿轮装置退出螺纹型芯。
1、按侧抽芯机构的动力来源将其分为手动、气动、液压和机动四种类型。
2、怎样减少熔合纹?
(书)
气体辅助注射成型、共注射成型、低发泡塑料注射成型、水辅助注射成型、模内装饰、微发泡、高光注射、模内装配、反压成型、模内监控。
第13章缺陷,选一种会考与,,,有关大,小的影响
答:
短射、熔合纹、喷射流、凹陷、翘曲、气泡、飞边、烧焦、流痕、银线痕、裂纹、表面剥离。