激光焊接在汽车行业的运用史.doc
《激光焊接在汽车行业的运用史.doc》由会员分享,可在线阅读,更多相关《激光焊接在汽车行业的运用史.doc(8页珍藏版)》请在冰豆网上搜索。
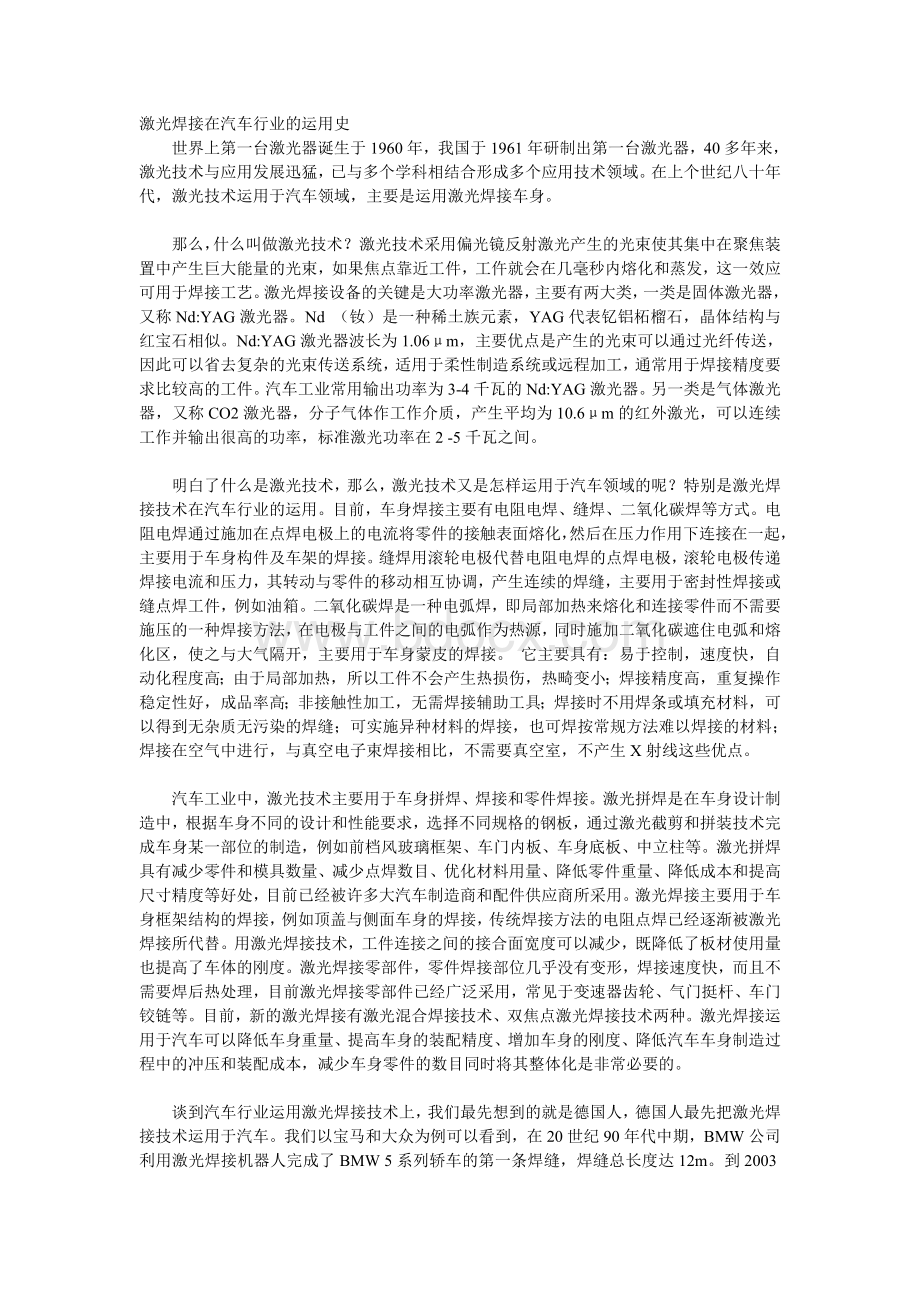
激光焊接在汽车行业的运用史
世界上第一台激光器诞生于1960年,我国于1961年研制出第一台激光器,40多年来,激光技术与应用发展迅猛,已与多个学科相结合形成多个应用技术领域。
在上个世纪八十年代,激光技术运用于汽车领域,主要是运用激光焊接车身。
那么,什么叫做激光技术?
激光技术采用偏光镜反射激光产生的光束使其集中在聚焦装置中产生巨大能量的光束,如果焦点靠近工件,工仵就会在几毫秒内熔化和蒸发,这一效应可用于焊接工艺。
激光焊接设备的关键是大功率激光器,主要有两大类,一类是固体激光器,又称Nd:
YAG激光器。
Nd(钕)是一种稀土族元素,YAG代表钇铝柘榴石,晶体结构与红宝石相似。
Nd:
YAG激光器波长为1.06μm,主要优点是产生的光束可以通过光纤传送,因此可以省去复杂的光束传送系统,适用于柔性制造系统或远程加工,通常用于焊接精度要求比较高的工件。
汽车工业常用输出功率为3-4千瓦的Nd:
YAG激光器。
另一类是气体激光器,又称CO2激光器,分子气体作工作介质,产生平均为10.6μm的红外激光,可以连续工作并输出很高的功率,标准激光功率在2-5千瓦之间。
明白了什么是激光技术,那么,激光技术又是怎样运用于汽车领域的呢?
特别是激光焊接技术在汽车行业的运用。
目前,车身焊接主要有电阻电焊、缝焊、二氧化碳焊等方式。
电阻电焊通过施加在点焊电极上的电流将零件的接触表面熔化,然后在压力作用下连接在一起,主要用于车身构件及车架的焊接。
缝焊用滚轮电极代替电阻电焊的点焊电极,滚轮电极传递焊接电流和压力,其转动与零件的移动相互协调,产生连续的焊缝,主要用于密封性焊接或缝点焊工件,例如油箱。
二氧化碳焊是一种电弧焊,即局部加热来熔化和连接零件而不需要施压的一种焊接方法,在电极与工件之间的电弧作为热源,同时施加二氧化碳遮住电弧和熔化区,使之与大气隔开,主要用于车身蒙皮的焊接。
它主要具有:
易于控制,速度快,自动化程度高;由于局部加热,所以工件不会产生热损伤,热畸变小;焊接精度高,重复操作稳定性好,成品率高;非接触性加工,无需焊接辅助工具;焊接时不用焊条或填充材料,可以得到无杂质无污染的焊缝;可实施异种材料的焊接,也可焊按常规方法难以焊接的材料;焊接在空气中进行,与真空电子束焊接相比,不需要真空室,不产生X射线这些优点。
汽车工业中,激光技术主要用于车身拼焊、焊接和零件焊接。
激光拼焊是在车身设计制造中,根据车身不同的设计和性能要求,选择不同规格的钢板,通过激光截剪和拼装技术完成车身某一部位的制造,例如前档风玻璃框架、车门内板、车身底板、中立柱等。
激光拼焊具有减少零件和模具数量、减少点焊数目、优化材料用量、降低零件重量、降低成本和提高尺寸精度等好处,目前已经被许多大汽车制造商和配件供应商所采用。
激光焊接主要用于车身框架结构的焊接,例如顶盖与侧面车身的焊接,传统焊接方法的电阻点焊已经逐渐被激光焊接所代替。
用激光焊接技术,工件连接之间的接合面宽度可以减少,既降低了板材使用量也提高了车体的刚度。
激光焊接零部件,零件焊接部位几乎没有变形,焊接速度快,而且不需要焊后热处理,目前激光焊接零部件已经广泛采用,常见于变速器齿轮、气门挺杆、车门铰链等。
目前,新的激光焊接有激光混合焊接技术、双焦点激光焊接技术两种。
激光焊接运用于汽车可以降低车身重量、提高车身的装配精度、增加车身的刚度、降低汽车车身制造过程中的冲压和装配成本,减少车身零件的数目同时将其整体化是非常必要的。
谈到汽车行业运用激光焊接技术上,我们最先想到的就是德国人,德国人最先把激光焊接技术运用于汽车。
我们以宝马和大众为例可以看到,在20世纪90年代中期,BMW公司利用激光焊接机器人完成了BMW5系列轿车的第一条焊缝,焊缝总长度达12m。
到2003年7月,激光焊接焊缝的总长度累计达到150万米。
在新的激光焊接技术方案上,德国大众Touran轿车就是一个很好的例证。
在这一新型轿车中,激光焊点的数量达到了1400个、焊缝的总长度达70m。
同时,奥迪也采用了激光焊接技术来焊接车身。
在舒适、美观的敞蓬轿车的生产中,VW公司的技术人员与奥地利的焊接专家Fronius公司合作研制开发了一种激光混合焊接技术。
在高级敞蓬轿车的车门上,激光混合焊接焊缝的长度达到了35.7m,是纯激光焊接焊缝长度的3倍。
在中国即将上市的一汽大众生产的紧凑车型Sagitar,又叫速腾,即使是“小车”,可是速腾的激光焊接却达到了30多米长。
高尔夫的焊接长度方面,激光焊接也长达52.5m,Polo的全车身激光焊接总长度也达到6591毫米,
在激光混合焊接技术上,德国大众的材料专家认为:
与纯激光焊接技术相比,利用激光混合焊接技术可大大提高板金件缝隙的连接能力。
从而使得VW公司可以更加充分地利用激光高速焊接时电弧焊接的工艺稳定性,大众的PhaetonD1所有车门都采用激光-MIG复合焊。
另一个应用实例是BMW5系列的宝马轿车的铝合金隔板采用这种激光混合焊接技术与内高压变形加工的铝合金支架焊接在一起。
在双焦点激光焊接技术上BMW公司采用了双焦点激光焊接技术。
因为该技术在铝合金材料的焊接过程中有很好的性能,因此广泛应用于BMW公司的大批量生产过程中。
采用激光焊接的车身提高了车身30%多的钢度,从而提升了车身的安全性;同时也减轻了车身重量,还可以达到省油的目的;焊接的精度也大大得到了提高。
这些,都帮助降低了汽车的生产成本,最终还是消费者受益,正所谓“科技以人为本”。
目前,在国外,德国大众公司在AudiA6、GolfA4、Passat等品牌的车顶均采用激光焊接,宝马、通用公司在车架顶部也采用激光焊接,通用、丰田、福特、宝马、菲亚特、奔驰、大众公司均采用激光拼焊板技术,美国三大汽车公司、德国奔驰公司则采用激光焊接传动部件,大众公司、通用公司、奔驰公司、日产公司应用了激光切割技术,菲亚特和丰田公司用激光涂覆发动机排气阀,大众公司发动机凸轮轴实现激光表面硬化处理。
在国内,从国内国产高品质车型,如:
帕萨特、别克、奥迪等都采用激光拼焊板向激光焊接的转变上,国内开始了采用激光焊接技术的转变,在国内首先采用激光焊接技术(而不是激光焊接)方面,走在前列的还是一汽大众,同时部分国内汽车厂商也渐渐开始采用这种技术。
激光技术目前在一汽的应用方面,一汽大众AudiA6顶盖和BORA后罩盖采用激光焊接,速腾(Sagitar)分别在车身的顶部、后罩盖等多处采用了激光焊接技术,焊接长度达到30多米。
一汽使用的设备为德国HassYAG3KW激光器和Kuka机器人,一汽轿车公司轿车车身覆盖件采用激光切割,使用设备为德国ARNOLD3KW三维五轴CO2激光加工机,一汽底盘零件厂刹车蹄片采用激光硬化处理,使用设备为国产2KWCO2激光加工机,一汽模具中心薄板件为激光切割,使用设备为国产1.5KWCO2激光加工机。
随着激光焊接技术的成熟和激光焊接机的价格下降,中国的奇瑞汽车也开始采用激光焊接技术。
激光跟踪系统如何同机器人控制器接口?
(1)KUKA机器人
激光寻位系统(MTF系统):
-KUKA控制器同MTF系统的通讯是通过串行RS232连接。
需要在机器人控制器中编制相应的程序来对MTF进行通讯。
MTF安装手册中有关于同MTF的通讯协议。
激光跟踪系统(MTR)-KUKA意大利公司开发了KUKA控制器同MTR系统的接口,另一家德国公司也开发了模拟和数字通讯接口同MTR通讯。
(2)FANUC机器人
激光寻位系统(MTF系统):
对于FANUC的RJ2和RJ3控制器-通过采用Karel软件运行在控制器上,能够同MTF系统通讯。
在选型之前需要知道FANUC控制器的软件版本,因为Karel软件需要在控制器上重新编译。
不需要添加额外的附件。
两者之间通过串行口来通讯。
激光跟踪系统(MTR):
对于FANUC的RJ3控制器,.目前仅仅用于外部轴移动工件,而机器人焊枪保持不动,进行焊枪位置的微调。
将来会开发全功能的软件来完成此功能。
(3)ABB机器人
控制器的型号应该为S4C或者S4C+,需要配备ABB提供的程序,来计算传感器提供的偏差值,并将其计算入程序示教的主路径中,形成当前的实际焊缝路径。
同ABB机器人的接口是ABB德国研发中心开发的,在2004年早些时间完成。
在德国戴姆勒-克莱斯勒公司应用了好几套,焊接速度达到2-3m/min。
同样在澳大利亚也有ABB的机器人配备MTR跟踪系统。
(4)CLOOS机器人
CLOOS公司提供相应的软件和硬件来配置激光跟踪系统,很成熟。
(5)Motoman机器人
对于XRC控制器,需要配备XCP02通用传感器基板。
对于最新型NX100控制器,相关的接口板Motoman正在开发,2005年初应该推出。
MTR或者MTF系统同控制器采用模拟和数字通讯接口,为示教程序提供当前焊缝偏差的校正量。
国内焊接机器人技术的发展
我国开发工业机器人晚于美国和日本,起于20世纪70年代,早期是大学和科研院所的自发性的研究。
到80年代中期,全国没有一台工业机器人问世。
而在国外,工业机器人已经是个非常成熟的工业产品,在汽车行业得到了广泛的应用。
鉴于当时的国内外形势,国家“七五”攻关计划将工业机器人的开发列入了计划,对工业机器人进行了攻关,特别是把应用作为考核的重要内容,这样就把机器人技术和用户紧密结合起来,使中国机器人在起步阶段就瞄准了实用化的方向。
与此同时于1986年将发展机器人列入国家“863”高科技计划。
在国家“863”计划实施五周年之际,邓小平同志提出了“发展高科技,实现产业化”的目标。
在国内市场发展的推动下,以及对机器人技术研究的技术储备的基础上,863主题专家组及时对主攻方向进行了调整和延伸,将工业机器人及应用工程作为研究开发重点之一,提出了以应用带动关键技术和基础研究的发展方针,以后又列入国家“八五”和“九五”中。
经过十几年的持续努力,在国家的组织和支持下,我国焊接机器人的研究在基础技术、控制技术、关键元器件等方面取得了重大进展,并已进入使用化阶段,形成了点焊、弧焊机器人系列产品,能够实现小批量生产。
我国焊接机器人的应用状况
我国焊接机器人的应用主要集中在汽车、摩托车、工程机械、铁路机车等几个主要行业。
汽车是焊接机器人的最大用户,也是最早用户。
早在70年代末,上海电焊机厂与上海电动工具研究所,合作研制的直角坐标机械手,成功地应用于上海牌轿车底盘的焊接。
“一汽”是我国最早引进焊接机器人的企业,1984起先后从KUKA公司引进了3台点焊机器人,用于当时“红旗牌”轿车的车身焊接和“解放牌”车身顶盖的焊接。
1986年成功将焊接机器人应用于前围总成的焊接,并于1988年开发了机器人车身总焊线。
80年代末和90年代初,德国大众公司分别与上海和一汽成立合资汽车厂生产轿车,虽然是国外的二手设备,但其焊接自动化程度与装备水平,让我们认识到了与国外的巨大差距。
随后二汽在货车及轻型车项目中都引进了焊接机器人。
可以说90年代以来的技术引进和生产设备、工艺装备的引进使我国的汽车制造水平由原来的作坊式生产提高到规模化生产,同时使国外焊接机器人大量进入中国。
由于我国基础设施建设的高速发展带动了工程机械行业的繁荣,工程机械行业也成为较早引用焊接机器人的行业之一。
近年来由于我国经济的高速发展,能源的大量需求,与能源相关的制造行业也都开始寻求自动化焊接技术,焊接机器人逐渐崭露头角。
铁路机车行业由于我国货运、客运、城市地铁等需求量的不断增加,以及列车提速的需求,机器人的需求一直处于稳步增长态势。
据2001年统计,全国共有各类焊接机器人1040台,汽车制造和汽车零部件生产企业中的焊接机器人占全部焊接机器人的76%。
在汽车行业中点焊机器人与弧焊机器人的比例为3:
2,其他行业大都是以弧焊机器人为主,主要分布在工程机械(10%)、摩托车(6%)、铁路车辆(4%)、锅炉(1%)