玩具壳的模具设计和模具制造毕业设计.docx
《玩具壳的模具设计和模具制造毕业设计.docx》由会员分享,可在线阅读,更多相关《玩具壳的模具设计和模具制造毕业设计.docx(35页珍藏版)》请在冰豆网上搜索。
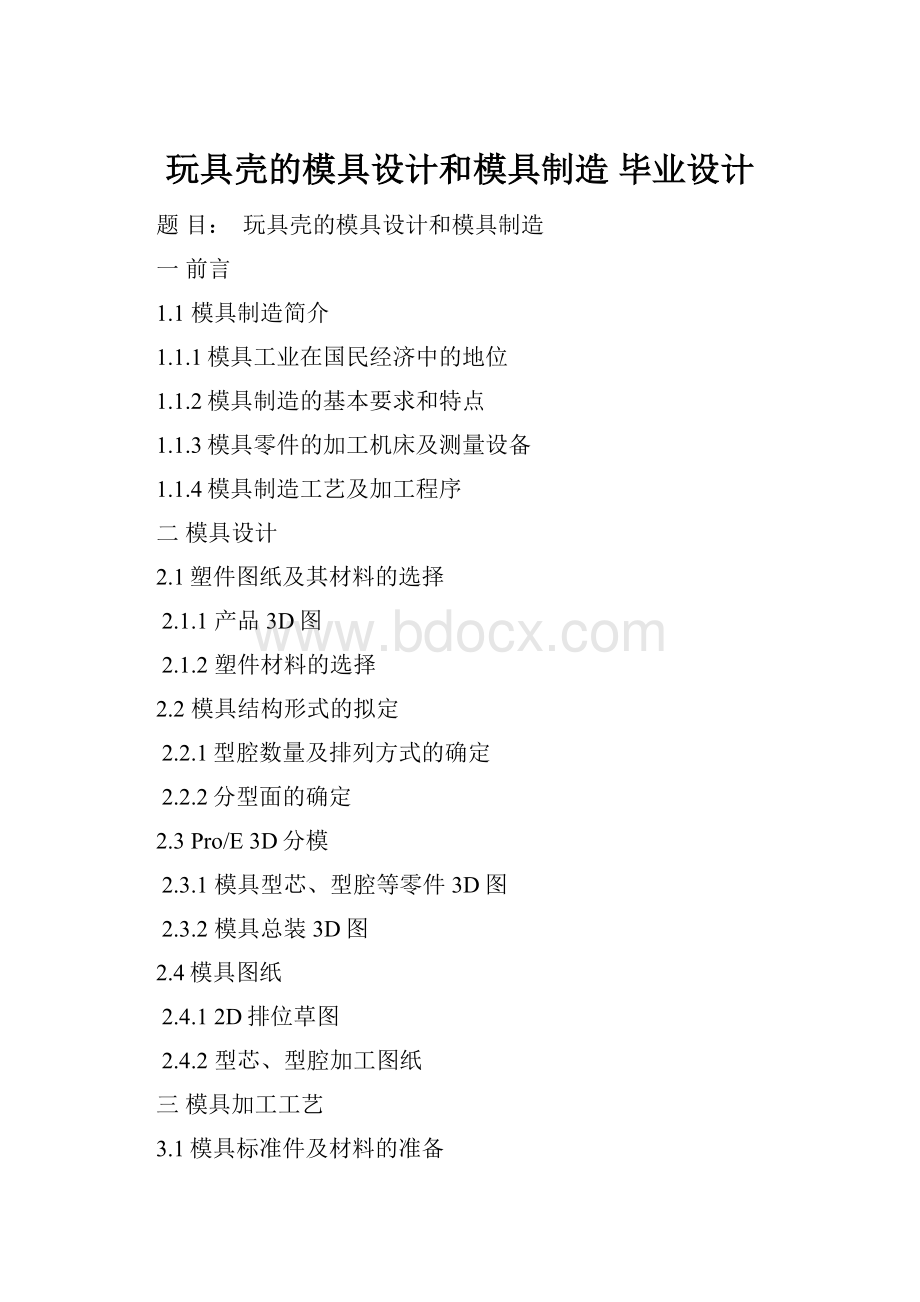
玩具壳的模具设计和模具制造毕业设计
题目:
玩具壳的模具设计和模具制造
一前言
1.1模具制造简介
1.1.1模具工业在国民经济中的地位
1.1.2模具制造的基本要求和特点
1.1.3模具零件的加工机床及测量设备
1.1.4模具制造工艺及加工程序
二模具设计
2.1塑件图纸及其材料的选择
2.1.1产品3D图
2.1.2塑件材料的选择
2.2模具结构形式的拟定
2.2.1型腔数量及排列方式的确定
2.2.2分型面的确定
2.3Pro/E3D分模
2.3.1模具型芯、型腔等零件3D图
2.3.2模具总装3D图
2.4模具图纸
2.4.12D排位草图
2.4.2型芯、型腔加工图纸
三模具加工工艺
3.1模具标准件及材料的准备
3.1.1标准模架的确定
3.1.2其他标准件准及材料的准备
3.2钻水路及螺纹孔的加工工艺
3.3型芯加工工艺
3.3.1装夹、对刀及刀具补偿值输入
3.3.2UG粗加工主要的刀轨参数设置
3.3.3热处理
3.3.4UG精加工主要刀轨参数设置
3.3.5型芯电火花加工
3.3.6型芯线切割加工
3.3.7模具的抛光
3.4模具的装配
3.5试模
四工艺卡片
五参考文献
六谢词
前言
毕业设计是高等职业教育教学计划的重要组成部分,是加强理论与实际相结合的重要实践学习环节。
光阴似梭,大学三年的学习一晃而过,为了具体体验这三年来的学习效果,综合检测理论在实际应用中的能力,我开始了信息学院最后一次的自我检验-----毕业设计。
本次毕业设计的课题来源与生活,应用广泛。
模具结构相对来说有点复杂,但这对我们来说是一个很好的考验。
它能加强我们对模具结构的理解。
同时论文中模具制造工艺的编写让我们对数控编程和工艺的编写有了更进一步的理解与加强。
本次设计以模具的加工工艺为主,综合了模具结构设计、模具制造,最后到模具总的装配等一系列模具生产过程。
起到很好的学以至用的效果。
在设计模具并编写模具加工工艺的同时把以前学过的基础课程综合应用到了本次设计中。
在设计中除了翻阅大量模具设计与制造的理论性书籍之外,还应用了CAD、cad燕秀外挂、Pro/E、EMX模具外挂、UG等专业软件,力求达到减小劳动强度,提高工作效率。
非常感谢张乐老师对本次设计由指导,同时也感谢信息学院各位老师的精心教诲。
由于实际经验和理论技术有限,设计之中难免有遗漏与错误,希望各位老师批评指正。
设计者:
龚亮
2010年11月2日
毕业设计任务说明书
1.1模具制造简介
1.1.1模具工业在国民经济中的地位
在现代生产中,模具是大批量生产各种产品和日用生活品的重要工艺装备,它以特定的形状通过一定的方式使原料成型。
现已在国民经济各个部门,特别是汽车、航天航空、仪器仪表、机械制造、家用电器、石油化工、轻工日用品等部门得到极其广泛的应用。
研究和发展模具技术,对于促进国民经济的发展具有特别重要的意义。
模具技术已成为衡量一个国家产品制造技术的重要标志之一。
随着工业生产的迅速发展,模具工业在国民经济中的地位将日益提高,并在国民经济发展过程中发挥越来越大的作用。
1.1.2模具制造的基本要求和特点
1、模具制造的要求在模具生产中,除了正确进行模具设计,采用合理的模具结构外,还必须以先进的模具制造技术作为保证。
制造模具时,应满足以下几个基本要求:
(l)制造精度高为了保证制品精度,模具工作部分的精度通常要比制品精度高2一4级;模具结构对上、下模之间的配合有较高要求,因此组成模具的零件都必须有足够的制造精度。
(2)使用寿命长模具是比较昂贵的工艺装备,其使用寿命长短直接影响产品成木的高低。
(3)制造周期短为了满足生产需要,提高产品竟争能力,必须在保证质量的前提下尽量缩短模具制造周期。
(4)模具成本低模具成本与模具结构的复杂程度、模具材料、制造精度要求及加工方法等有关,必须根据制品要求合理设计模具和制定其加工工艺。
1.1.3模具制造的特点:
(l)单件生产用模具成型制品时,每种模具一般只生产1-2副,所以模具制造属于单件生产。
(2)制造质量要求高模具制造不仅要求加工精度高,而且还要求加工表面质量好。
一般来说,模具工作部分制造公差应控制在±0.01mm左右;工作部分的表面粗糙度Ra要求小于0.8μm。
(3)形状复杂模具的工作部分一般都是二维或三维复杂曲面,而不是一般机械的简单几何体。
(4)材料硬度高模具实际上相当于一种机械加工工具,硬度要求高,一般用淬火工具钢或硬质合金等材料,采用传统的机械加工方法制造有时十分困难。
1.1.4模具零件的加工机床及测量设备
模具零件绝大多数为金属材料,主要的加工方法有机械加工、特种加工和表面加工等。
所涉及的机床有:
刨床、铣床、车床、钻床、镗床、磨床、电火花线切割机床、抛光机等。
涉及的检测设备有:
手动三坐标、投影仪、精密千分尺、卡尺、硬度计、粗糙度仪、千分表、高度仪等。
五、模具制造工艺及加工程序
二模具设计
2.1塑件图纸及其材料的选择
2.1.1产品3D图
2.1.2塑件材料的选择
根据厂家要求以及此产品的特点,选用ABS材料。
因为ABS材料具有易成型,低蠕动性、优异的尺寸稳定性以及高抗冲击强度等特点。
根据厂家要求此产品规定产量为100万左右。
2.2模具结构形式的拟定
2.2.1型腔数量及排列方式的确定
根据产品尺寸的大小、生产批量,以及产品侧抽芯位置等特点确定此套模具为一模两腔的排列方式。
(见下图)。
2.2.2分型面的确定
注:
球标1:
侧抽芯分型面
球标2:
斜顶分型面
2.3Pro/E3D分模图
2.3.1模具型芯、型腔等零件3D图
2.3.2模具总装3D图(正面)
2.3.2模具总装3D图(背面)
2.4模具图纸
2.4.12D排位草图
型腔加工图纸:
型芯加工图纸:
三模具加工工艺
3.1模具标准件及材料的准备
3.1.1标准模架的确定
为了满足侧抽芯机构的设计以及浇口凝料自动脱落等要求,选用标准模架如下图所示:
FCI-2530-A60-B60-C80-L250
3.1.2其他标准件准及材料的准备
浇口套:
SBAΦ12xL60xH13xD35
定位圈:
LRAΦ100
顶针:
Φ3.0X150
型芯:
P20(150X180X31精料)
型腔:
P20(150X180X36精料)
滑块:
P20(40X30X47精料)
镶件:
P20(Φ4X50)
其余材料选用:
45#
P20特性:
1.硬度均匀,具有良好的抛光性能及光蚀刻花性能,加工性能佳。
2.真空脱气精炼处理钢质纯净,适合要求抛光或蚀纹加工塑胶模。
3.预硬状态供货,模具寿命在50万次以下无需在热处理可直接用于模具加工,缩短工期。
3.2钻水路及螺纹孔的加工工艺
型芯、型腔精料采购回来后第一件事就是检测精料六面的垂直度以及表面质量。
等检查完毕就开始根据模具设计师提供的图纸进行水路以及螺纹孔的加工。
1、机床的选择
模具制造中水路以及螺丝孔的加工精度以及定位精度要求不高,所以钻水路和螺丝孔一般选用钻床和简易数控铣床。
如型号为YL1632K3铣床和型号为Z3040x10(13)的摇臂钻床。
2、零件装夹与找正定位
钻孔时,零件装夹在机床导轨的虎口钳上,保证待加工孔的轴线与机床导轨垂直。
孔的定位如果在铣床上加工,可先对刀,确定零件的加工的中心基准,然后控制机床到待加工点的坐标。
为了避免麻花钻钻孔时的偏心,须先用中心钻钻一中心孔,然后换麻花钻加工水路及螺纹孔。
如果用摇臂钻床加工,孔的定位可通过划线找正的方法。
3、加工时的注意事项
a.应采用低转速低的进给速度,防止断刀和注意切屑的排出。
b.加工过程中应不断浇注冷却液,防止钻头的烧坏。
c.对于较深的水路,为了保证孔相对于导轨的垂直度,应尽量不
选用较长的钻头。
可以通过两头加工保证孔的精度。
4、攻丝
水路孔以及螺丝孔加工完以后就把零件交给钳工师傅攻丝。
此套模具,水路的水塞均采用带螺纹的铜水塞,型芯和型腔在上下模板中的定位也需要紧固螺丝固定,所以这些地方都得攻丝。
攻丝时,为了达到螺纹顺利配合要求,对一个孔必须重复攻丝。
攻丝时要注意用力。
保证与表面的垂直度。
注意防止丝锥断到孔中。
3.3型芯加工工艺
根据产品3D图形进行模具设计后,将模具型芯的3D实体图转换成STP图形格式,输入到UG中。
前模加工3D图,如下图图所示。
3.3.1装夹、校表、对刀及刀具补偿值输入
1)装夹
因为工件加工区域为整个面,为了便于机床走刀以及好找正,我们可以采用组合夹具装夹,如下图所示。
注:
工件与下面圆盘垫块的固定采用内六角螺丝,工件底面已在第一步加工出了型芯与上模板的定位螺丝孔。
在这里可利用那些螺丝孔进行装夹固定。
2)校表
因为模具要求加工精度较高,我们采用百分表找正。
找准工件与导轨平行,然后完全固定。
3)对刀
模具加工的对刀一般不直接用加工的刀具对刀,刀具对刀很难保证模具加工的精度。
模具加工常用的对刀工具有:
寻边器(对X、Y轴)和Z轴设定器。
通过对刀工具对刀后,确定工件的正中心为加工零点。
对刀时应注意:
(1)根据加工要求采用正确的对刀工具及方法,控制对刀误差;
(2)在对刀过程中,可通过改变微调进给量来提高对刀精度;
(3)对刀时需小心谨慎操作,尤其要注意移动方向,避免发生碰撞危险;
(4)对刀数据一定要存入与程序对应的存储地址,防止因调用错误而产生严重后果。
4)刀具的补偿值的设定。
根据刀具的实际尺寸和位置,将刀具半径补偿值和刀具长度补偿值输入到与程序对应的存储位置。
需注意的是,补偿的数据正确性、符号正确性及数据所在地址正确性都将威胁到加工,从而导致撞车危险或加工报废。
3.3.2UG粗加工主要的刀轨参数设置
1)开粗用Φ20圆角半径为2mm的飞刀开粗,预留1mm的切削余
(1)UG中主要的刀轨设置参数:
选择加工类型为:
型腔铣
加工方法:
粗加工
切削模式:
步距:
距离:
全局每刀深度:
2mm
切削参数设置为:
余量设置:
非切削移动参数设定:
进刀类型:
沿形状斜进刀
倾斜角度:
5°
退刀:
与进刀相同
进给和速度:
主轴转速:
2000(rpm)进给率:
300(mmpm)
(2)刀具路线如下图
2)换Φ16圆角半径为2mm的飞刀二次开粗
各参数设置与上基本相同。
不同之处为:
加工类型:
残料铣削
,主要加工上把Φ20刀具无法加工到的部位。
余量设置:
使用“底部面和侧壁余量一致”余量为0.5mm
全局每刀深度为:
1mm
刀具路线为:
3)用Φ8的平底刀对垂直面、前面的加工留下的圆角进行清角加工。
加工类型:
等高轮廓铣
陡峭空间范围:
角度:
设置80°是因为型芯有较大的拔模角度,设置90°,会导致某些地方铣削不到。
层之间走刀设置为:
走刀路径如下图:
3.3.3热处理
为了延长模具的使用寿命,达到客户要求的生产量需要对材料进行热处理。
P20材料热处理工艺:
加硬处理:
为提高模具寿命达到80万模次以上,可对预硬钢实施淬火加低温回火的加硬方式来实现。
淬火时先在500-600℃预热2-4小时,然后在850-880℃保温一定时间(至少2小时),放入油中冷却至50-100℃出油空冷,淬火后硬度可达50-52HRC,为防止开裂应立即进行200℃低温回火处理,回火后,硬度可保持48HRC以上。
氮化处理:
氮化处理可得到高硬度表层组织,氮化后的表层硬度达到650-700HV(57-60HRC)模具寿命可达到100万次以上,氮化层具有组织致密,光滑特点,模具的脱模性及抗湿空气及碱液腐蚀性能提高。
热处理时,要严格按照P20材料热处理工艺进行。
避免因热处理不当引起材料过大的变形,硬度达不到要求甚至引起材料的开裂导致材料的报废。
3.3.4UG精加工主要刀轨参数设置
热处理后,型芯、型腔达到了比较高的硬度值。
对于热处理产生的微量变形,在精加工时可以消除,以达到模具设计的要求。
对模具型芯精加工时,需要针对型芯的结构特征,进行数控加工。
型芯的装夹、校表、对刀等于粗加工相同,这里不做叙述。
1)型芯UG加工参数以及走刀路径如下:
(1)刀具选择
因为型芯已经过热处理,表面硬度值增加,切削性能下降,刀具应选择硬质合金刀具。
对于底面及顶面选择Φ8的硬质合金平底刀,对于圆弧面的加工选择Φ8的硬质合金球刀。
(2)底面精加工刀轨主要参数设置
选择加工类型为:
型腔铣
加工方法:
精加工
切削模式:
步距:
距离:
切削层设置:
公差设置:
拐角处刀轨形状:
主轴转速:
3000rpm
进给率:
1200mmpm
加工刀轨如下图:
(3)顶面精加工刀轨主要参数设置
顶面精加工刀轨参数设置于底面刀轨设置差不多,在这里不做阐述。
刀轨路径如下图:
(4)与底面垂直的侧面精加工刀轨主要参数设置
侧面精加工与侧面粗加工加工刀轨基本相同,参数设置只要设置加工余量为0,设置公差为±0.03即可。
刀轨路径图请参照侧面粗加工刀具路径图。
(5)圆弧面精加工刀轨主要参数设置
刀具:
Φ8的硬质合金球刀
加工类型:
轮廓区域铣
指定切削区域为:
所有圆弧面
区域铣削驱动设置:
公差设置:
延伸刀轨设置:
刀轨减少到原来1/6的效果图如下:
到这里,型芯的在数控铣床上的加工已完毕,型腔的加工与型芯的加工工艺大同小异,在这里就不做叙述。
3.3.5型芯电火花加工
由于数控铣床加工刀具大小以及加工工艺的局限性,型芯上有很多细小的地方,以及小的直角区域无法用铣床铣出来,对于那些加工不到的盲区,我们将用电火花进行进一步的加工。
1)电火花加工原理:
电火花加工基于电火花腐蚀原理,是在工具电极与工件电极相互靠近时,极间形成脉冲性火花放电,在电火花通道中产生瞬时高温,使金属局部熔化,甚至气化,从而将金属蚀除下来。
电火花数控线切割加工的过程中主要包含下列三部分内容
(1)电极丝与工件之间的脉冲放电。
(2)电极丝沿其轴向(垂直或Z方向)作走丝运动。
(3)工件相对于电极丝在X、Y平面内作数控运动。
2)电火花加工特点:
(1)脉冲放电的能量密度高,便于加工用普通的机械加工方法难于加工或无法加工的特殊材料和复杂形状的工件。
不受材料硬度影响,不受热处理状况影响。
(2)脉冲放电持续时间极短,放电时产生的热量传导扩散范围小,材料受热影响范围小。
(3)加工时,工具电极与工件材料不接触,两者之间宏观作用力极小。
工具电极材料不需比工件材料硬,因此,工具电极制造容易。
(4)可以改革工件结构,简化加工工艺,提高工件使用寿命,降低工人劳动强度。
3)放电间隙对加工精度的影响
电火花加工模具时,工具电极与工件之间发生脉冲放电需要保持一定的放电间隙,使加工出的工件型孔尺寸与电极尺寸相比,沿加工轮廓上要相差一个放电间隙。
放电间隙主要决定加工稳定性,一般增大脉冲放电间隙时间可提高加工稳定性。
而提高峰值电流将使生产率提高,但电极损耗将加大。
4)对加工表面粗糙度的影响
电蚀表面的粗糙度评定参数Ra随脉冲宽度和电流峰值增大而增大。
在一定加工条件时,脉冲宽度和电流峰值增大会使单个脉冲能量增大,使电蚀凹坑的断面尺寸增大,因此表面粗糙度主要取决于单个脉冲能量的大小。
要减少表面粗糙度Ra的值,则必须减少单个脉冲的能量。
数控铣床加工后,一些加工盲区如下图所示,标记区域需用电火花加工。
5)电极材料的选取
电极材料的选取直接关系到放电加工的效果,在很大程度上,材料的选取是否恰当,决定了放电速度、加工精度以及表面粗糙度的最终情况。
6)电极材料必须具备的特点
在电火花加工的过程中,电极用来传输电脉冲,蚀除工件材料。
电极材料必须具有导电性能良好、损耗小、加工成形容易、加工稳定、效率高、材料来源丰富、价格更便宜等特点。
7)电极材料的选择原则
合理选择电极材料,可以从下列方面进行考虑:
电极是否容易加工成形;电极的放电加工性能如何;加工精度、表面质量如何;电极材料的成本是否合理;电极的重量如何。
根据电极材料所应具备的特点和电极材料的选择原则,我们选定紫铜为电火花加工电极。
8)紫铜
紫铜是目前在电加工领域应用最多的电极材料。
紫铜材料塑性好,可机械加工成形、锻造成形、电铸成形及电火花线切割成形等,能制成各种复杂的电极形状。
紫铜加工稳定性好,在电火花加工过程中,物理性能稳定,能比较容易获得稳定的加工状态,不容易产生电弧等不良现象,在较困难的条件下也能稳定加工。
精加工中采用低损规准可获得轮廓清晰的型腔。
但因本身材料熔点低(1083℃),不宜承受较大的电流密度,一般不能超过30A电流的加工。
紫铜热膨胀系数较大,在加工深窄筋位部分,较大电流下产生的局部高温很容易使电极发生变形。
紫铜电极通常采用低损耗的加工条件,由于低损耗加工的平均电流较小,其生产率不高,故常对工件进行预加工。
9)拆电极的原则
(1)铜料成本。
电极基准板厚度5mm左右,若两个电极部位距离较大时,不要拆成一个整体式电极。
(2)加工效率。
为缩短电火花加工时间,若两个电极部位距离较小,应拆成一个整体式电极。
(3)电极加工的可行性。
若拆分的电极无法加工则电极是无用的。
10)拆电极的注意事项
(1)电极基准板的厚度应设定为大于或等于15mm,若以夹紧方式固定电极时,可设定为5mm左右。
(2)校表位即是基准板边缘与电极脚的距离,可设定为5mm左右。
(3)EDM冲水位的高度即是基准板与模具最高处的距离,可设定为5mm左右,以便于电火花加工时冲走残渣。
(4)基准板中心与工件中心的距离应为整数,以便于工作校表和减少操作错误。
根据以上注意事项及拆电极原则,制作型芯的部分电极3D图如下:
拆电极时,要综合考虑电极的加工可行性(如下图),对于左边电极,出现了直角区域,这些地方铣床刀具是不能铣出来的,我们应该把左边电极拆为两个电极,如右图所示;
此副模具电极制作中还有很多类似以上问题,在这里就不多做阐述。
为了保证电火花加工区域的精度,每一个电极都要加工两个,一个用于粗加工,一个用于精加工。
11)在给电火花加工编程时必须注意如下问题:
(1)加工余量。
该参量的最小值要求大于放电间隙,超精加工时加工余量并不为零,且前一道工序要给后一道工序留下余量。
(2)加工方式。
在轮廓加工或挖槽加工时可以选择生成圆弧段程序。
而在沿曲面加工时必须选择直线加工方式,包括切入切出程序,即程序段必须是空间微直线段,这也有利于电极损耗补偿计算。
(3)加工精度。
加工精度越高,弦线对空间曲线的逼近度越高,空间微直线段越多,程序越长。
实际加工时,粗加工可以选择低一点的精度,以减少程序段数。
(4)残余波峰高。
该参量指刀具横向进给量,其值越小,加工曲面越光顺。
(6)电参量和电极长度补偿。
电参量的选择要参考加工余量,电极损耗补偿值依工艺经验而定,它与电参量、电极材料对及工作液等相关。
电极损耗补偿值均匀插入每个微直线段端点上。
3.3.6型芯线切割加工
模具顶针孔的加工可以选择钻孔和线切割,要综合考虑然后选择合适的加工方法方案。
对于本套模具顶针孔、镶件孔均用线切割加工。
1)快走丝与慢走丝的选择:
此副模具,为了保证镶件与型芯的配合精度,镶件孔我们采用慢走丝加工,对于其他的大部分顶针孔加工,从配合精度以及制作成本上考虑,我们选用快走丝。
在线切割之前,我们先加工穿丝孔。
以前的穿丝孔一般选用钻孔的方式加工,对于细小的穿丝孔,钻头加工速度很慢且很容易断在工件中,然后用电火花把钻头蚀除。
这在一定程度上给穿丝孔的制作带来很大的麻烦。
现在随着各种先进机床的更新出
现,穿丝孔的加工已没有以前加工那么麻烦。
现在对穿丝孔采用专门的打孔机加工。
这种机床的大量运用,提高了模具制造的加工效率,解决了很多加工难题。
打孔机其实就是电火花加工机床,工作原理与电火花加工原理一样,打孔机所用电极如右图所示。
2)型芯的线切割图纸下
3)线切割加工时注意事项:
(1)移动工作台或主轴时,要根据与工件的远近距离,正确选定移动速度,严防移动过快时发生碰撞。
(2)线切前必须确认程序和补偿量是否正确无误。
(3)检查电极丝张力是否足够。
在切割锥度时,张力应调小至通常的一半。
(4)检查电极丝的送进速度是否恰当。
(5)根据被加工件的实际情况选择敞开式加工或密着加工,在避免干涉的前提下尽量缩短喷嘴与工件的距离。
密着加工时,喷嘴与工件的距离一般取0.05~0.1mm。
(6)检查喷流选择是否合理,粗加工时用高压喷流,精加工时用低压喷流。
(7)加工过程中,要经常对切割工况进行检查监督,发现问题立即处理。
(8)加工中因断线等原因暂停时,经过处理后必须确认没有任何干涉,方可继续加工。
此套模具其他镶件、滑块、顶针、斜顶的加工工艺跟普通零件加工工艺大同小异,在这里就不再做复述。
3.3.7模具的抛光
抛光不仅增加工件的美观,而且能够改善材料表面的耐腐蚀性、耐磨性,还可以使模具拥有其它优点,如使塑料制品易于脱模,减少生产注塑周期等。
因而抛光在塑料模具制作过程中是很重要的一道工序。
1)机械抛光
机械抛光是靠切削、材料表面塑性变形去掉被抛光后的凸部而得到平滑面的抛光方法,一般使用油石条、羊毛轮、砂纸等,以手工操作为主,特殊零件如回转体表面,可使用转台等辅助工具,表面质量要求高的可采用超精研抛的方法。
2)机械抛光基本方法
在塑料模具加工中所说的抛光与其他行业中所要求的表面抛光有很大的不同,严格来说,模具的抛光应该称为镜面加工。
它不仅对抛光本身有很高的要求并且对表面平整度、光滑度以及几何精确度也有很高的标准。
表面抛光一般只要求获得光亮的表面即可。
镜面加工的标准分为四级:
AO=Ra0.008μm,A1=Ra0.016μm,A3=Ra0.032μm,A4=Ra0.063μm。
精密模具的镜面加工是以机械抛光为主。
3)机械抛光基本程序
要想获得高质量的抛光效果,最重要的是要具备有高质量的油石、砂纸和钻石研磨膏等抛光工具和辅助品。
而抛光程序的选择取决于前期加工后的表面状况,如机械加工、电火花加工,磨加工等等。
机械抛光的一般过程如下:
(1)粗抛经铣、电火花、磨等工艺后的表面可以选择转速在35000—40000rpm的旋转表面抛光机或超声波研磨机进行抛光。
常用的方法有利用直径Φ3mm、WA#400的轮子去除白色电火花层。
然后是手工油石研磨,条状油石加煤油作为润滑剂或冷却剂。
一般的使用顺序为#180-#240-#320-#400-#600-#800-#1000。
为了节约时间我们可以选择从#400开始。
(2)半精抛半精抛主要使用砂纸和煤油。
砂纸的号数依次为:
#400-#600-#800-#1000-#1200-#1500。
实际上#1500砂纸只用适于淬硬的模具钢(52HRC以上),而不适用于预硬钢,因为这样可能会导致预硬钢件表面烧伤。
(3)精抛精抛主要使用钻石研磨膏。
若用抛光布轮混合钻石研磨粉或研磨膏进行研磨的话,则通常的研磨顺序是9μm(#1800)-6μm(#3000)-3μm(#8000)。
9μm的钻石研磨膏和抛光布轮