OQC岗位操作规范.docx
《OQC岗位操作规范.docx》由会员分享,可在线阅读,更多相关《OQC岗位操作规范.docx(30页珍藏版)》请在冰豆网上搜索。
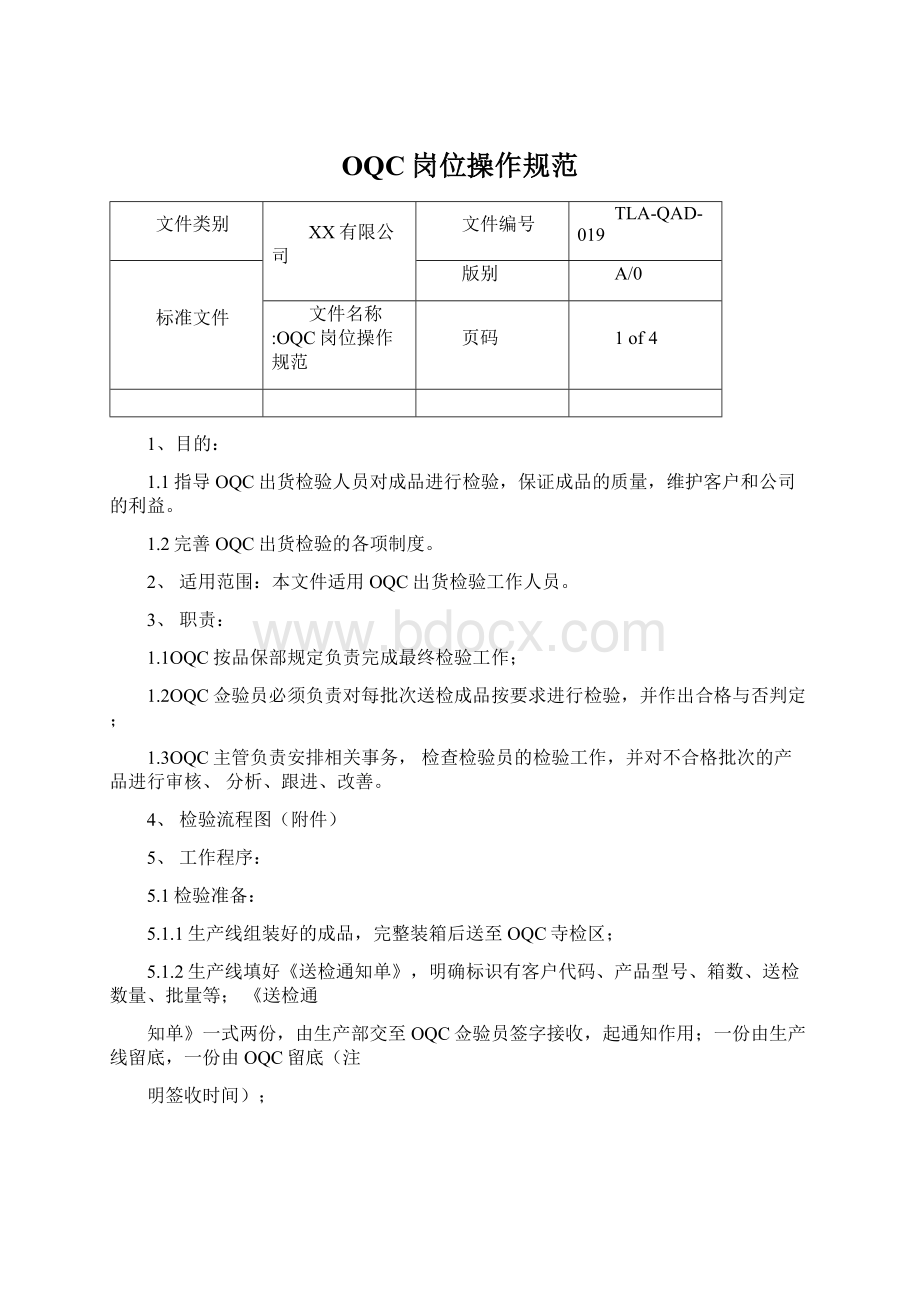
OQC岗位操作规范
文件类别
XX有限公司
文件编号
TLA-QAD-019
标准文件
版别
A/0
文件名称:
OQC岗位操作规范
页码
1of4
1、目的:
1.1指导OQC出货检验人员对成品进行检验,保证成品的质量,维护客户和公司的利益。
1.2完善OQC出货检验的各项制度。
2、适用范围:
本文件适用OQC出货检验工作人员。
3、职责:
1.1OQC按品保部规定负责完成最终检验工作;
1.2OQC佥验员必须负责对每批次送检成品按要求进行检验,并作出合格与否判定;
1.3OQC主管负责安排相关事务,检查检验员的检验工作,并对不合格批次的产品进行审核、分析、跟进、改善。
4、检验流程图(附件)
5、工作程序:
5.1检验准备:
5.1.1生产线组装好的成品,完整装箱后送至OQC寺检区;
5.1.2生产线填好《送检通知单》,明确标识有客户代码、产品型号、箱数、送检数量、批量等;《送检通
知单》一式两份,由生产部交至OQC佥验员签字接收,起通知作用;一份由生产线留底,一份由OQC留底(注
明签收时间);
5.1.3OQC检验员根据收到的《送检通知单》上标明的客户代码、产品型号、批量等信息,检索出对应的订单(检验标准)、工艺标准和出货检验报表及相关工具准备检验;
5.1.4OQC出货检验员在抽样后在检验状态卡上填写“正在检验”标识。
5.2检验:
5.2.1抽样箱数的确定:
根据箱数抽样计划确定抽样箱数,分层随机确定开箱的箱号;
5.2.2抽样样本的确定:
根据抽样计划,平均从抽样箱中抽样一定数量成品,作为检验的样本;
5.2.3抽样检验实施:
OQC检验员根据订单要求、工艺文件和样版,对产品工艺、尺寸、外观、功能及包装实施检验;检验过程中注意区分待检品、合格品及不合格品;
5.2.4判定:
根据抽样计划及缺陷分类标准,对每批检验成品作出最终判定。
5.2.5记录:
依据上述内容,及时填写检验记录,《OQCINSPECTIONREPOR》(OQC最终检验报告)由OQC
主管核准。
5.3合格:
判定为合格的成品批次,每箱加盖“OQCPASSED及日期印章,并在《成品入库单》上签字确认进仓。
5.4不合格:
检验员填写检验报告,并选出具有代表性之不良品样板交至主管或经理复批及批准,根据结果作出以下判
定:
5.4.1返工:
检验员填写《返工通知单》一式两份,由包装部生产领班/主管签字确认;一份由OQC留底,一份由生产线留底;由包装部负责返工,OQC负责跟踪返工直至改善;
5.4.2OQC检验员在返工批上注明不合格标识,并通知生产线转出进行隔离返工;
5.4.3生产部包装车间返工后,检验员进行复检;返工三次以上(含三次)则有OQC主管召集包装车间主管、
QA主管等到现场进行解决;
5.4.4不良返工复检必须加严抽检,具体检验标准为:
AQL^{Cr=0,Maj=0.25,Min=0.40}。
5.5报告存档:
在检验过程中所有的报告、报表等均须存档,作为质量记录以供查阅。
文件类别
XX有限公司
文件编号
TLA-QAD-019
标准文件
版别
A/0
文件名称:
OQC岗位操作规范
页码
2of4
6、抽样标准:
6.1抽样计划(抽样标准MIL-STD-105EH级水平,一次正常检验抽样方案)
致命缺陷:
Cr=0;严重缺陷:
Maj=0.40;轻微缺陷:
Min=0.65;
6.2开箱数抽样方案:
6.2.1开箱数
箱数
1
2
3-7
8-10
11-15
16-20
21-25
26-50
51-80
81-150
151-30
0
301以
上
开箱
数
1
2
3
4
5
6
7
8
10
12
15
16
6.2.2若以上开箱数不能
£满足抽样数需要可
「适当增加开箱数。
6.3客户有特殊要求时,按客户要求进行抽样检查及判定。
6.4返工复检的批次,须进行再次检验,合格后方可出货。
7、检查项目:
OQC寸成品检验的项目及标准主要参考对应客户包装生产工艺中的品质要求。
7.1产品工艺确认:
7.1.1核对产品所使用物料、产品组合方式是否与订单及工艺标准一致;
7.1.2同一批次产品,工艺标准应保持一致。
7.2规格尺寸:
7.2.1检查产品各项重要尺寸是否符合订单及工艺标准要求,必要时使用经确认的模具检查。
7.2.2重要尺寸主要包括:
高度、宽度、厚度及插头引线、外露焊片的外露长度,各产品需测量的重要尺寸参见对应的工艺标准。
7.2.3在检验报告上记录插头型号、线材及5组电池尺寸数据(若工艺中有条形码要求需记录条形码数据)。
7.3外观检查:
7.3.1外观:
7.3.1.1外观清洁:
外观清洁、无破损、污浊;
7.3.1.2PVC收缩:
PVC膜收缩平整、无破损、皱折、外膜须套到位;
7.3.1.3纸套位置及松紧度合适,即将电池倒立后电池不从纸套脱落;
7.3.1.4胶壳上无严重的刮花、溢胶、颜色一致。
7.3.2移印、喷墨标准:
字迹清晰、无墨团、断线。
7.3.3连接片:
7.3.3.1插头、引线:
引线无破损而露出线芯,特别是在插头打端子处;轻拉单根框子引线,检查框子有否扣紧;
7.3.3.2点焊、锡焊:
点焊无披锋、炸火现象,焊点均匀分布于焊片上,不得损伤电池,焊点牢固,锡焊平整无虚焊。
文件类别
XX有限公司
文件编号
TLA-QAD-019
标准文件
版别
A/0
文件名称:
OQC岗位操作规范
页码
3of4
7.4电性能检查:
741电压检查:
7.4.1.1根据工艺标准进行测量。
7.4.1.2在检验报告上记录5组实测电压数据。
7.4.2内阻检查:
若工艺中有内阻要求,需按工艺标准进行内阻测量,并在检验报告上记录5组实测内阻数据,
7.4.3容量检查:
容量的抽检数量为批量抽检20组,测试结果满足工艺要求才能判定为合格批次。
7.4.4其它特性的检查:
客户对某项特性有特殊要求时,按客户要求进行检查,结果满足客户要求时才能
判定为合格批次;
7.5装箱检查:
7.5.1装箱数量:
箱内装的电池数量应符合工艺要求(若该送检批次有尾箱,检验员必须对该批次尾箱进行数量全检);
7.5.2包装唛头:
包装外箱应有唛头标识,唛头应符合订单生产说明书要求;
7.5.3包装方式:
内包装应有保护措施以防止电池可能发生的短路危险;内包装密封、防潮良好;包装盒、
箱底无粘接剂;包装后,电池应保持紧凑,无晃动现象。
7.6印章管理:
印章只能由OQC佥验员使用,并对印章判定合格的产品质量负责。
&人员资格及场地要求:
8.1OQC出货检验员上岗前必须培训,合格后持上岗证上岗。
8.2OQC出货检验场地需保持清洁,各种物料/产品需标识清楚。
8.3OQC出货检验员在检验工作时必须保持办公室的光线充足,一般情况下,由主管作出是否合格判断,如果
光线不足应停止检验。
9、相关记录:
9.1
《OQC出货检验日报表》
MCR-QAD-028
9.2
《OQCINSPECTIONREPORT
MCA-QAD-021
9.3
《返工通知单》
MCR-QAD-027
10、相关文件:
《OQC出货检验标准》
MCR-QAD-603
文件类别
XX有限公司
文件编号
TLA-QAD-019
标准文件
版别
A/0
文件名称:
OQC岗位操作规范
页码
4of4
OQC出货检验流程图
样品科
重新确
定装箱
OQC出货检验
生产线
填《送检通知单》
确定检验抽样样本数
N
N
返工重检数量
签字确认送检,并根据送检单信息,准备订单生产说明书、工艺标准等文件
产品区抽样:
随机开箱,每箱抽样数保持平均,抽样后放置
正在检验标识卡
*
根据箱数抽样方案,确定开箱数
纸箱尺寸、装箱合适?
(无短
数量正确?
(全检尾相)
Y
联系生产线拉重
**联系样品科装箱
箱唛料号、单号正确?
(无箱
唛情况应上报)
路隐患)
在《返工通知单》上签字并返工重检
N
产品工艺检查
产品外观检查;产品尺寸检查;产品电压(内阻)检测
不良品隔离并标识清楚
打包进仓
N
不良品数是否在接收范围
加盖OQCPASSE[及日期印章
(容量测试结果必须达到出货要求才能盖章)
在《成品入库单》上签字确认
文件类别
XX有限公司
文件编号
TLA-QAD-603
标准文件
版别
A/0
文件名称:
OQC岗位检验标准
页码
1of6
1、目的:
结合我司生产之各电池,为成品电池出货检验提供标准、依据,以便于对公司生产的各种电池做出正确判断。
2、范围:
适用于本公司成品电池(包括赠品)、外购电池、光身电池及组合电池。
3、定义:
3.1致命缺陷(CR):
所有出现功能失效可能导致不安全之缺陷,严重损害公司声誉之不良现象。
3.2严重缺陷(MA):
所有削弱产品性能或严重损害产品正常外观的缺陷。
3.3轻微缺陷(Ml):
不会降低产品设定的使用性能,关系产品外观的轻微缺陷。
4、程序:
4.1本标准针对一般客户未有特别要求的按此标准进行判定,若客户有特殊要求,按客户的特殊要求进行判
4.2抽样方法按《OQC佥验操作标准》进行,若客户有特别要求,按客户要求进行。
文件类别
XX有限公司
文件编号
TLA-QAD-603
标准文件
版别
A/0
文件名称:
OQC岗位检验标准
页码
2of6
5.
光身电池出货检验标准:
检验项目
检验仪器
判定标准
致命
严重
轻微
规格
尺寸
尺寸
卡尺
电池组的长、宽、高任一尺寸超过《包装生产工艺》要求
V
外观
电池光身
目测
单体电池焊缝处漏液
V
底部(盖帽)腐蚀点或污渍超过两点,腐蚀面积大于0.5mm且不易辨出。
V
底部(盖帽)腐蚀点或污渍不超过两点,腐蚀面积小于0.5mnf且不易辨出。
V
对着光线,眼睛离物体距离为30cm,可明显辨
出有凸、凹点
V
面垫
目测
面垫明显翘起、起皱、变形、缺角或漏贴面垫
V
用错其它面垫
V
面垫贴不牢,易脱落、歪斜
V
喷码
目测
喷码内容与订单或《包装生产工艺》要求不一致,或印错字或漏印字。
V
字体严重墨点、缺笔少划,不可辩认。
V
字迹有重影,断笔、版面轻微模糊但不影响辨认,印字字体歪斜或排列疏密不当。
V
喷码有毛刺,空心,弯曲,在正常光线下,眼睛离物体距离为30cm字迹可辨别,无明显弯曲
V
电性能测试
内阻
内阻仪
单体电池内阻咼于标准要求。
V
电池内阻咼于《包装生产工艺》要求。
V
电压
万用表
电池电压值低于订单或《包装生产工艺》的电压要求。
V
0电压(0V
容量
新威测试柜
电池的容量低于《包装工艺标准》的2%M内。
V
电池的容量低于《包装工艺标准》的2河上。
V
包装
外箱、内盒
目测
外箱、内盒严重破损或有大块污渍。
V
外箱或内盒规格与订单或《包装生产工艺》