第2章 钢的退火与正火Word文档格式.docx
《第2章 钢的退火与正火Word文档格式.docx》由会员分享,可在线阅读,更多相关《第2章 钢的退火与正火Word文档格式.docx(29页珍藏版)》请在冰豆网上搜索。
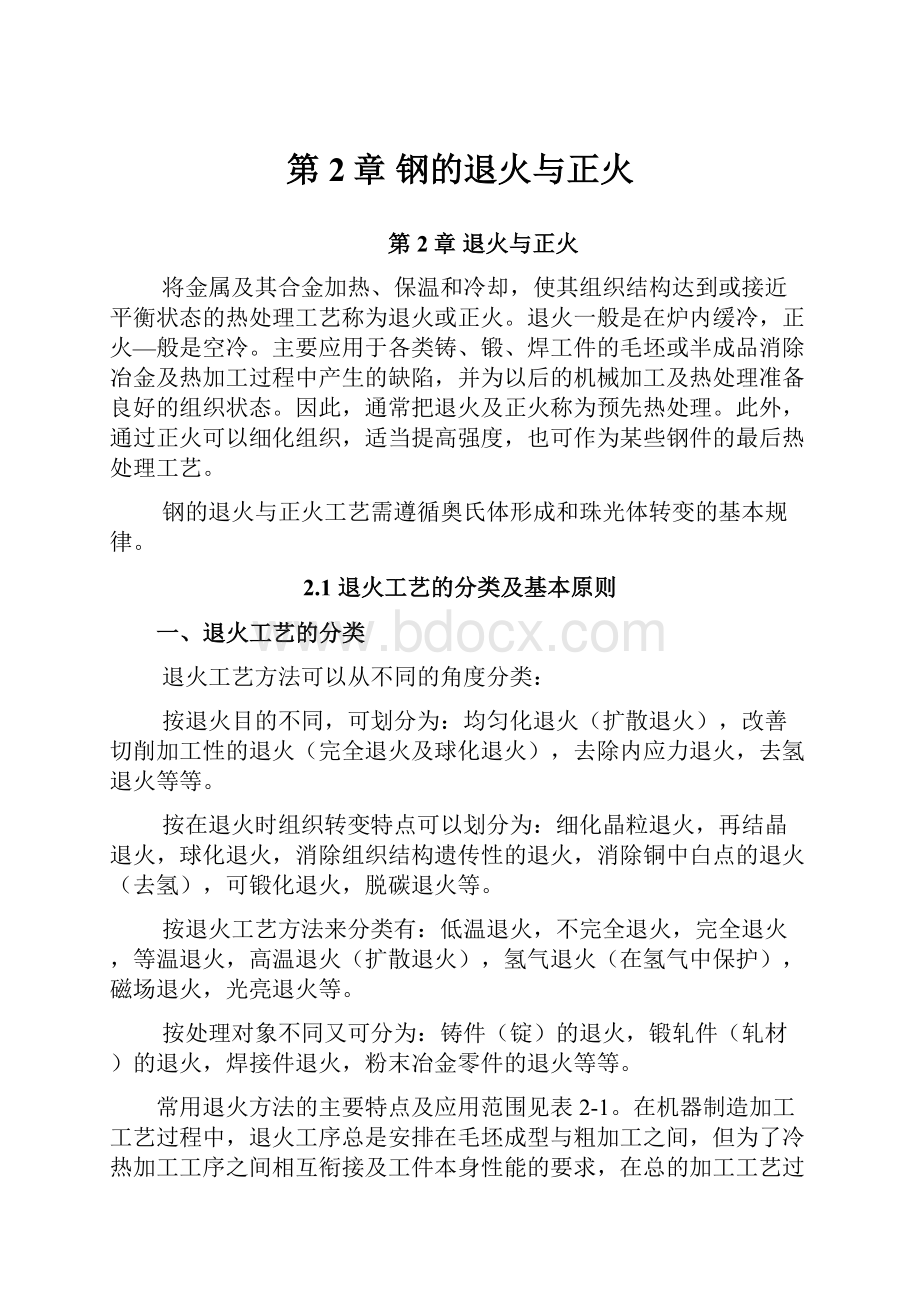
工艺特点
组织性能的变化
适用范围
低温退火
加热温度:
<
Al
碳钢及低合金钢550~650C
高合金工具钢600~750C
加热速度:
100~150C/h
保温时间:
3~5min/mm
冷却速度:
50~100C/h
消除铸、锻、焊及切削加工过程中的内应力,使其达到稳定状态
铸、锻、焊、机械加工等各类金属材料制品
再结晶退火
>
TR
TR+150~250C(TR0.4TM熔点)
0.5~1h
冷却:
空冷
发生恢复再结晶过程使变形晶粒为细小等轴晶粒消除冷作硬化效应及内应力
经冷加工成型的各类制品
扩散退火
Ac3·
Acm线
在固相线以下高温加热
碳钢1100~1200C
十几小时到几十小时
同完全退火
为细化晶粒往往还需补充退火
均匀化学成分消除改善显微组织的偏析
铸锭或铸件
完全退火
Ac3+30~50C
碳钢200C/h;
低合金钢:
100C/h;
高合金钢:
50C/h
碳钢15~2min/mm
300C空冷
细化晶粒、降低硬度、提高塑性,去除内应力
亚共析钢铸锻件C0.3~0.8%
等温退火
视对组织的要求而定,
可与完全退火相同或与球化退火
加热温度相同(Ac3~Acl)
等温温度:
由钢材成分及退火后
硬度要求而定
等温后冷却:
可空冷到室温,大
件需要缓冷到<
500C空冷
同上,可按工艺要求获得片状或粒状珠光体
C0.3~0.8%
亚共析钢铸锻件
C0.8~1.2%
过共析钢的球化退火
球化退火
Acm
1)加热到略高于Ac1长时间保温后缓冷到小于500C空冷
2)加热到Acl+20~30C透烧后快冷到Ar1-20~30C保温反复循环数次后缓冷到小于500C
3)等温球化退火,加热到Ac1+20~30C再快冷到Arl以下保温然后可空冷
使碳化物球化,可改善共折、过共析钢的切削加工性,降低硬度
共析,过共析钢的锻轧件
2.使钢经退火软化的最佳规范是将钢加热到临界温度以上约30~40C的温度(亚共析钢在AC3以上),然后在低于AC1不超过40C的温度范围令其发生珠光体转变,即
奥氏体化温度近似等于AC3(AC1)+(30~40C)
珠光休转变的温度近似等于Ar1-(30~40C)
3.实现上述软化退火必须缓冷才能保证在预期的过冷度条件下进行珠光体转变,但所需工艺周期很长,尤其是合金钢。
因此,可以采用奥氏体化后快冷到低于临界温度30~40℃的等温炉中施行等温分解,以缩短工艺周期。
奥氏体向珠光体转变的温度愈低,转变所需时间愈短。
珠光体的片层间距(或粒子间距)与过冷度成反比,珠光体的硬度与片层间距(或粒子间距)成反比。
4.为了缩短退火工艺周期,钢在奥氏体化以后,只要使最终的组织与硬度符合规定,在可能范围内应当尽量使其从转变温度快冷到室温。
在炉内缓冷完成退火作业时,可炉冷到300~350C,然后空冷。
在等温退火时,从奥氏体化温度到等温炉中可快冷。
在等温炉中结束等温转变后可自炉中取出空冷。
5.为了确保含碳0.7~0.9%的工具钢及某些低合金中碳钢得到细粒状珠光体组织,在奥氏体化之前在低于A1温度20~30C,下预热几个小时,使碳化物部分球化再加热到略高于奥氏体化温度进行退火可促使最终得到细粒状珠光体。
6.过共析合金工具钢要得到最低的硬度,应在正常球化退火温度下延长保温时间(需10~15小时)以利于形成较粗的球化组织。
7.为了细化淬火的粗大过热组织,可以通过提高退火时的奥氏体化温度(高于临界点50~100C)和延长奥氏体化保温时间的办法,或采用中等加热速度进行奥氏体化,使奥氏体晶粒发生重结晶,从而消除组织结构的遗传性。
2.2扩散退火
为了改善或消除在冶金过程中形成的成分不均匀性而实行的退火称为扩散退火。
扩散退火的工艺过程是在适当的加热温度下长时间保温,然后再缓慢的冷却到室温。
通过扩散退火可以使在高温下固溶于钢中的有害气体(主要是氢)脱溶析出,这时称为脱氢退火。
扩散退火也可以将金属及其合金加热到接近或低于固相线的较高温度下长期保温,并用一定的速度冷却,可以改善或消除铸件中的枝晶偏析,轧材中的带状偏析。
因此,这种退火也称为均匀化退火。
通过退火改善钢的成分及其均匀性,必要的条件是在一定的加热温度下及足够长的保温时间。
显然,这些参量都直接关系到固溶体对溶质元素的溶解度,以及溶质原子在基体中的扩散速度和扩散过程进行的程度。
一、脱氢退火
溶解于固溶体中的氢,是造成钢中出现白点缺陷的主要危险。
存在于亚晶界、位错、晶粒边界及宏观区域中的分子氢,不易自钢中扩散逸出,也不会造成白点,这类分子状态的氢只能在以后的热轧、锻造等压力加工过程中消除。
用退火的方法可以使固溶氢脱溶,钢中加入与氢易形成化合物的钛、锆、钒、铌、镧、铈等元素亦可使固溶氢减少。
图2-1指出,氢在铁中溶解度随温度下降而降低,同时在同样温度下氢在体心立方点阵中(-Fe,-Fe)溶解度小,而在面心立方点阵的-Fe中溶解度高。
从图2-2可以看出氢在铁中的扩散系数除随温度升高而增大外,也与点阵类型有关。
由图2-2中还可看出氢在-Fe中扩散系数比在-Fe中大得多。
为了使钢中的固溶氢脱溶,应当选择在使氢的溶解度达到最小的组织状态,同时又应使氢在钢中的扩散速度尽可能高的温度,所以一般可在奥氏体等温分解的过程中长期保温来完成。
对大型锻件,为锻后尽快消除白点,应冷却到珠光体转变速度最高的那个温度范围(C曲线上的“鼻尖”温度区),以尽快获得铁素体与碳化物混合组织。
同时,在此温度区长时间保温或再加热到低于A1的较高温度下保温,进行脱氢处理。
对于高合金钢,也可在锻后首先进行一次完全退火,以改善组织,细化晶粒,使氢的分布更加均匀,并降低奥氏体的稳定性,从而有利于白点的消除。
二、均匀化退火
(一)偏析的形成及其有害影响
在铸锭、铸件结晶过程中将形成某些缺陷,例如偏析是钢液选择性结晶及与铸件冷却条件有关的冶金缺陷。
它主要表现为化学成分的不均匀性以及非金属夹杂物的不均匀分布。
此外,在偏析区还形成大量显微的及宏观的气泡、气孔。
在化学成分的偏析中又可分为枝晶偏析及区域偏析,后者对造成缺陷的影响更大。
在偏析中,碳的偏析具有最重要的意义,因为它直接涉及到钢的热处理及其机械性能。
国外根据152种碳钢及合金钢的偏析资料,用统计分析的方法分析了化学成分,铸锭尺寸对碳区域偏析的影响。
碳的偏析率用
表示:
所测钢锭尺寸为直径0.6~2.25m,重3.5~190吨,高径比H/D=1.05~3.2,含碳为0.1~0.54%的碱性平炉或碱性电炉钢铸锭。
式中,Cmax锭身轴线上最大含碳量(%);
Cmin锭身轴线上最小含碳量(%);
CP盛钢桶钢液的平均含碳量(%)。
研宄表明,钢锭中碳的偏析与钢锭尺寸之间呈直线比例增长,钢锭直径愈大,碳偏析率愈高。
在钢锭轴线上某处的含碳量等于其平均含碳量时,该处称为零偏析。
零偏析一般出现在锭高30%处,但有时也可低到15%,高到75%。
合金元素对碳的偏析率影响程度不同,其中硫、磷、硅显著提高碳的偏析率,钼、钒则降低碳的偏析率,这些影响可定量地表示为:
式中,D钢锭直径;
H钢锭高度。
因此,为使钢中的碳的偏析减少,必须尽量降低钢中硫、磷的含量。
钢中合金元素本身可能产生的偏析倍数为:
镍1.1~1.4,铜1.3~1.7,铬1.2~1.6,锰1.2~2.0,钼2~7,磷4~10,硫4~10,砷18。
此外,在大型铸、锻件中还存在着氧化物、硅酸盐、硫化物、磷化物等夹杂物的偏析。
它在铸锭的A形、V形及过渡偏析区分布最多。
同时,也广泛地分布在枝晶的晶界上,这主要由于难溶的氧化物夹杂首先从熔融钢液中析出并沿着晶界聚集,然后熔点较低的硫化物或氧化物的共晶体也在晶界附近集中,当它们呈链状沿晶界分布时,对钢的性能危害甚大。
铸锻件中形成的偏析,给以后的热处理及钢的性能带来以下的不良影响:
1.由于偏析的存在,造成大型铸件,锻件各部份成分相差较大,从而使相变过程产生差异,它将导致大型铸件组织与性能极不均匀,同时产生很大的组织应力。
2.偏析区内碳、硫、磷及钼的不均匀分布,易在压力加工及热处理时形成废品,氢及其它氧化物、硅酸盐、氮化物夹杂物在偏析区富集则更增加了形成开裂的危险。
3.偏析将导致机械性能的恶化,热轧后的偏析区将形成带状组织分布。
4.夹杂物的偏析,特别是脆性夹杂物呈粗大的、密集的形式分布,将造成以后冷热加工变形及热处理时的废品。
据统计,因夹杂物导致的大锻件报废率可高达50%。
(二)偏析的改善与消除
为了改善及消除有害的偏析,单纯利用热处理的方法是不可能完全解决的。
区域偏析只能依靠合金化,控制与改善浇注工艺及进行必要的压力加工等措施加以解决。
均匀化退火的任务在于消除枝晶成分偏析,改善某些可以溶入固溶体夹杂物(如硫化物)的状态,从而使钢的组织与性能趋于均匀。
扩散退火的效果在很大程度上决定于钢的纯度和偏析的发展情形。
扩散加热对硫、磷含量低而偏析程度又小的优质钢是没有实际意义的。
但是,对于含有较高硫、磷,偏析较严重夹杂物又较多的钢来说,扩散退火又无能为力。
因此,不能盲目地采用扩散退火来消除严重偏析。
铸锭在脱模后一般在均热炉中长时间保温,以减少枝晶偏析。
经过热轧、热锻以后的钢坯,由于偏析区经过形变,沿着变形方向伸展,而使扩散途径大大缩短,因此,在这种情况下进行扩散退火的效果是最为显著的。
扩散退火温度的上限一般不高于平衡图上的固相线,同时也要考虑到不使奥氏体晶粒过于粗大。
在此条件下应当尽量采取加热温度的上限以提高扩散效果。
而保温时间则应考虑钢材成分、尺寸、偏析程度等因素。
图2-3指出了合金元素在奥氏体中的扩散系数与温度的关系。
可看出呈间隙原子存在的碳、氮,在奥氏体中的扩散系数最大,易于均匀化。
铬、锰、钼、镍等元素因扩散激活能较大在奥氏体中的扩散系数小,均匀化较困难。
强烈形成碳化物的铬、钨、铝、钒等元素将阻碍碳在奥氏体中的均匀化过程,因此,对这类合金钢的扩散退火周期将更长,为了缩短高碳高合金钢中的非平衡共晶碳化物,可以在共晶温度以上进行扩散退火。
在该温度下由于部份伪共晶首先熔化,通过固-液相界面扩散均匀化过程大大加速。
2.3退火规范对钢的组织的影响
一、临界点以下加热的影响
退火前在临界点以下较长时间保温,并不发生相变重结晶过程,但是却可以改变显微组织结构的状态。
它可以发生这样一些变化:
对冷变形的钢来说,可进行回复再结晶过程,从而回复多边形晶粒、位错密度减少、亚结构的集合内应力的消除,对于共析碳化物来说,可以发生碳化物聚集的过程。
这两个过程都需要通过铁的自扩散及碳在铁中的扩散才能完成,因此,温度愈高,过程进行得愈充分。
图2-4为冷变形钢在加热时组织结构与性能变化的示意图。
在金属学中我们已经知道,在T2~T3温度范围将发生再结晶过程,通过再结晶退火可使冷变形晶粒多边形化,内应力消除,硬度、强度下降,塑性显著提高。
当温度越接近临界点,多边形晶粒越粗化。
对于未经冷加工变形的某些亚共析钢及某些低合金过共析钢,为了要得到粒状珠光体,在低于临界点10~30C的温度先进行较长时间保温,可以使共析碳化物聚集而增加在以后奥氏体化时的未溶碳化物核心数量,增加不均匀奥氏体中碳的浓度梯度,从而有利于球化组织的形成。
二、临界点以上加热时温度及时间的影响
奥氏体化温度及保温时间决定了奥氏体的晶粒大小及奥氏体成分的均匀性。
从而对以后的珠光体转变有很大影响。
由于奥氏体晶粒大小影响珠光体的形核率(Nv),从而影响着层状珠光体形成领域的尺寸。
当过冷度一定时,奥氏体晶粒大小对珠光体的片层间距无直接影响,但奥氏体的均匀性则不仅影响到非自发核心的数量,而且也直接影响着以后转变产物的金相形态。
奥氏体晶粒大小和均匀性改变着奥氏体转变动力学的规律。
晶粒愈粗,奥氏体越均匀,过冷奥氏体稳定性越高。
从而在相同的退火冷却速度下,与细晶粒钢比较,珠光体转变产物的弥散度相应增大,硬度适当提高。
奥氏体化温度对退火后组织形态的影响见图2-5。
当过冷奥氏体分解温度一定时,奥氏体化温度低于GG'
线时获得粒状珠光体,高于GLI'
线则全部为层状珠光体。
因此,在球化退火的奥氏体化温度应稍高于A1点(不超过AC1点20C),而当奥氏体化温度较高时,则完全获得层状珠光体组织。
延长奥氏体化时间,则奥氏体趋向于均匀化,碳化物溶解渐多直至达到在该温度下的饱和溶解度。
由于碳的浓度梯度下降,因而增加了形成层状珠光体的趋势。
实验表明,在A1+10C温度下长时间保温相当于在高于AC1以上40C短时间加热的效果。
对于过共析钢,在略高于A1温度长时间保温还使残余未溶碳化物聚集,硬度略有降低(HB241~229),塑性提高,改善了切削加工性和冷冲压加工工艺性。
表2-2是碳钢锻轧件完全退火推荐的奥氏体化温度与过冷奥氏体等温分解的转变温度范围。
一般结构钢锻件升温时间(在箱式炉内)大致是1h/25mm,保温时间0.5h/25~50mm。
在某些高合金钢中碳化物有较高的稳定性,在正常奥氏体化温度它们很难溶解并均匀化,因此在退火时形成层状珠光体就更困难。
表2-2碳钢推荐的完全退火温度
含碳量,C%
奥氏体化温度,C
奥氏体分解温度范围,C
硬度,HB
含碳量,C%
0.20
860~900
860~700
111~149
0.60
790~870
790~650
156~217
0.25
111~187
0.70
790~840
0.30
840~880
840~650
126~197
0.80
167~229
0.40
137~207
0.90
790~830
0.45
0.95
0.50
三、过冷奥氏体的分解温度、停留时间和冷却速度的影响
在图2-5中可以明确的看到过冷奥氏体的分解温度对组织形态的影响,在一定的奥氏体化温度下,分解温度决定着珠光体转变产物的弥散度。
以1.19%碳钢为例,若经750C奥氏体化,再冷到小于A1温度等温,等温温度在690C以上到A1点范围得到粒状珠光体,在低于630C时得到索氏体粗织,在690~630C之间得到粒状珠光体与索氏体的混合组织。
由于冷却速度影响了过冷度,因此冷速的影响与上述规律一致,冷速越慢,过冷度越小,奥氏体分解温度越高。
则珠光体转变产物的弥散度将越小。
在过冷奥氏体等温分解时停留时间决定了珠光体转变的程度。
将充分奥氏体化的钢缓慢冷却而完成重结晶过程的退火称为完全退火。
将奥氏体用较快速度冷却到临界点以下较高温度范围进行珠光体等温转变的退火称为等温退火。
完全退火一般在炉中冷却,对碳钢冷速一般是100~200C/h;
低合金钢50~100C/h;
高合金钢为20~60C/h;
过共析钢在不完全退火时的冷速约为20~60C/h。
等温退火的分解温度由钢材所需的硬度决定,一般选择在低于临界点30~100C,等温退火的保温时间应当包括在等温转变曲线上规定的组织转变时间与钢材截面降到等温温度时的均温透冷时间。
等温退火由于总的工艺周期短,在等温转变时沿截面组织转变比较均匀一致,因此特别适用于大件及合金钢件的退火。
2.4退火规范对钢中残余应力的影响
经过冷热加工后的工件,在室温下内部均保留着一部分残余应力。
残余应力的大小、分布、方向对工件的尺寸稳定性及力学性能有很重要的影响。
因此,在工件加工过程中,我们希望消除有害的残余应力。
钢材及各类合金为消除内应力而施行的退火称为去应力退火。
去应力退火一般在稍高于再结晶温度下进行,如钢铁材料一般在550~650C。
对热模具及高速钢则可使去除内应力退火温度提高到750~650C。
为了不致在冷却时再次发生附加的残余应力,在保温后缓慢冷却到500C以下再空冷。
大型工具或机械部件则应采取更慢的冷却速度,甚至要控制为每小时几度(C),待冷到300C以下时才能空冷。
这对于在较高温度下钢的屈服点较低而截面尺寸大的工件来说尤为重要。
因为冷却过快,截面温差大造成的附加应力,可能使前功尽弃。
罗森斯坦(A.H.Rosentein)等提供了估算碳钢及一般合金钢去除内应力退火规范与钢中残余应力关系的图表(图2-6)。
譬如在450C退火保温一小时,从图中可查出残余应力尚存的相对值(残余应力值/屈服强度100%),若使残余应力全部去掉,在650C需1小时,在600C则需15小时。
在应力-温度曲线图中的虚线为与钢材有关的残余应力变化幅度。
2.5球化退火
球化退火主要适用于含碳大于0.60%的各种高碳工模具钢、轴承钢等。
为改善冷变形工艺性,有时也用于低中碳钢。
钢中碳化物的球化可以提高塑性、韧性、改善切削加工性和减少最终热处理时的变形开裂倾向。
球化退火后的硬度取决于钢中碳及合金元素的含量,随着钢中含碳量升高,碳化物数量增加。
退火后硬度也相应升高(图2-7)。
细小均匀,圆形的碳化物分布在马氏体基体上将使耐磨牲、接触疲劳强度、断裂韧性得到改善与提高.
球化退火可以使高碳工具钢的硬度进一步降低,如T10钢经球化退火后可由原来热轧退火后的硬度HB255-321下降到HB≤197,从而使切削加工性提高。
球状碳化物的形状及分布对于钢的断裂韧性有很大影响。
图2-8是片状、球状及混合型珠光体的形态对含碳1.0%的碳钢疲劳裂纹扩展速率的影响。
在相同的应力强度因子下,球状珠光体的裂纹扩展速率远低于片状珠光体组织。
低碳钢经球化退火后硬度过低,在切削时发粘不易达到好的光洁度,因此,不适合作为切削加工前的预先热处理。
但是此类钢中碳化物的球化可以大为改善冷变形的加工性。
碳化物的球化有它独特的规律,国内外对此进行了广泛的研究,并不断改善各种球化退火的工艺方法,但迄今人们对球化微观机制的了解和研究还不够透彻。
一、影响碳化物球化的因素
(一)化学成分的影响
碳对钢中碳化物球化具有重要影响。
如前所述,钢中含碳越高,碳化物数量越多,可在较宽的奥氏体化温度范围内加热并易于球化。
高碳钢较低碳钢更容易获得球状珠光体。
合金元素对碳化物球化过程影响的规律比较复杂,因为合金元素(特别是形成碳化物的合金元素)将影响碳化物的成分、结构,和在奥氏体中的溶解度,碳在钢中的扩散以及合金元素本身的再分配等过程,从而对球化过程发生复杂影响。
目前系统地研究合金元素对球化过程影响的工作还很少。
在含有合金元素硅、镍、锰、铬、铜、铝、钼、钴、钒、钨(含量0.5~2%)的过共析钢(含碳0.9~1.0%)中,对碳化物球化的一般规律研究表明,钢中若没有碳化物形成元素,则球化较快;
反之,加入碳化物形成元素将使球化变慢。
其阻碍作用的程度与合金元素形成碳化物的强烈程度成正比。
显然,减慢作用首先是由于合金元素本身在奥氏体中的扩散激活能较高;
其次,它们将降低碳在奥氏体中的扩散系数有关。
(二)原始组织的影响
球化退火前原始组织的类型、晶粒粗细、以及自由铁素体、碳化物的大小、形状、数量和分布等均显著影响球化过程。
淬火马氏体是均匀的过饱和固溶体,在A1以下的较高温度回火时将使碳化物析出,并聚集长大而获得球状碳化物。
在这种状态下,球化速度比较快,而且球化组织均匀。
当采用缓慢冷却法进行球化退火时,球化退火的效果与原始组织有很大关系,如亚共析钢原始组织为大块状铁素体与珠光体的混合组织,经过缓冷球化退火后,在组织中碳化物分布极不均匀。
增加循环退火的次数可使晶粒细化,并使亚共析钢碳化物分布有所改善。
原始组织为贝氏体、屈氏体时,则比粗片状珠光休容易获得均匀细小的球状碳化物。
而过共析纲中的二次碳化物呈网状存在时很难球化,为了消除网状碳化物,可在球化退火前进行一次正火处理或高温固溶处理。
原始组织若经过冷变形、温锻形变加工,将显著促进球状碳化物的形成。
(三)加热温度与保温时间的影响
提高加热温度及延长保温时间,可增加碳化物在钢中固溶度,残余碳化物减少,有可能导致形成层状珠光体。
因此,若采用缓冷、等温退火或循环退火等球化工艺时,务必严格控制奥氏体化温度使其在最适当的范围内。
不同含碳量的碳钢合适的球化温度见图2-9。
虚线部分是推荐的球化温度范围。
钢的含碳量愈高,允许的球化加热温度范围愈宽。
若采用<
A1温度长时间保温的球化退火,提高球化温度,则球化速度可增加,特别当原始组织是马氏体或贝氏体时尤为显著。
片状珠光体在<
A1温度长期保温进行球化,则较上述组织要困难得多,除非经过冷加工形变使片状碳化物预先碎化.
当球化温度一定时,球化退火时间过长,碳化物粒度变粗,硬度下降,相同的球化时间,球化温度低的硬度较高。
(四)冷却速度的影响
用缓冷法进行球化退火时,冷却速度是能否得到球化组织的重要因素之一。
由于冷却速度决定了过冷奥氏体转变的温度Ar1