玻璃生产线及其温度控制系统设计Word格式文档下载.docx
《玻璃生产线及其温度控制系统设计Word格式文档下载.docx》由会员分享,可在线阅读,更多相关《玻璃生产线及其温度控制系统设计Word格式文档下载.docx(29页珍藏版)》请在冰豆网上搜索。
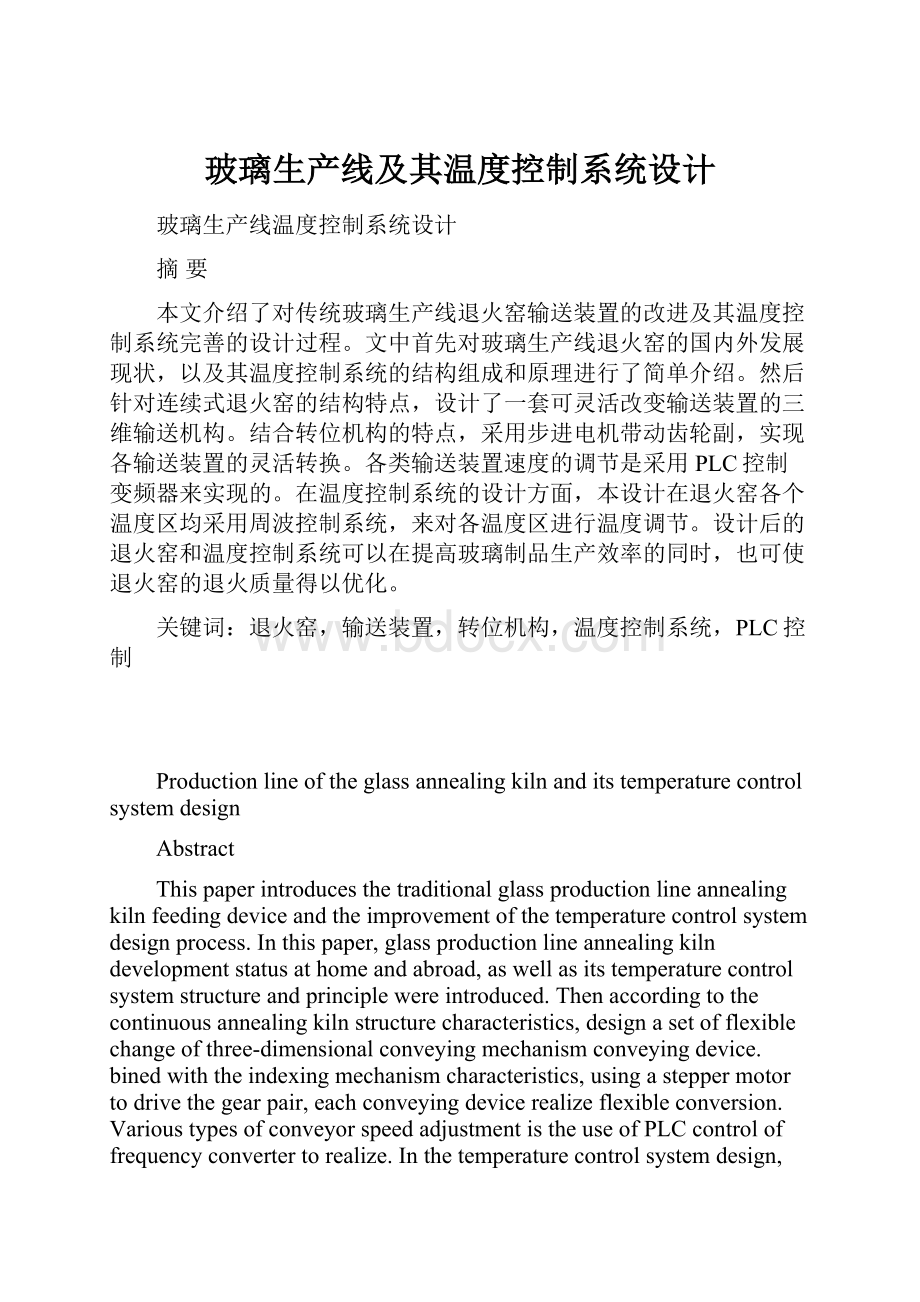
在确保退火质量的前提下尽可能使退火窑结构简单,操作方便。
因此玻璃的退火工艺是玻璃生产过程中的一个重要环节,其过程是将玻璃置于退火窑中,使其在某一温度下保持足够时间后再缓慢冷却,从而使玻璃应力不超过允许值。
当然要实现这一目的,就要对退火窑各区温度进行有效的控制。
温度控制系统可以实现对退火窑内保温区和非保温区的温度控制。
由各控制部分的协调配合,可以使玻璃的温度控制在需要的X围之内。
总之,退火窑性能的好坏直接影响玻璃制品的质量和生产成本,而退火窑温度控制系统不仅是生产高质量玻璃制品的前提,而且也是提高生产效率和退火窑寿命的必要保障。
因此,在保证退火窑性能的基础上,优化退火窑温度控制系统对玻璃制品的生产具有重要意义。
1.2国内外发展现状及趋势
我国目前的工厂广泛采用的是连续式退火窑,原因在于其生产效率高,连续性强,较易形成自动化管理运行模式,可以实现大批量生产。
其中输送装置则因玻璃制品的特点而定,但速度控制系统落后,不能实现灵活调节,因此存在综合性不强,生产品种单一的缺点:
即一个工厂只能对一种玻璃制品进行简单退火,若生产玻璃制品的品种增多,则需要相应增加退火窑的数量,这样不仅使投资成本增加,而且使车间的空间利用率降低。
对于退火窑内的加热方式,目前采用的有明焰式、隔焰式、半隔焰式和电加热式。
明焰式的火焰与制品直接接触;
隔焰式的火焰不与制品接触,通过薄片砖或退火窑外壳体间接传热;
半隔焰式的火焰部分与制品接触,另一部分对制品间接加热。
三种加热方式各有自己的优缺点。
针对冷却介质,由于空气的来源广泛,设备简单,经济效益性好,故在国内外得到普遍采用。
但由于空气中的杂质会对玻璃制品产生一定的影响,在实际中又不易通过改善风机的性能来得到净化空气的目的。
就这一缺陷,法国公司在生产质量要求较高的玻璃制品时,采取水冷的方式进行冷却,效果可靠、技术成熟,玻璃制品的质量可以得到保证,值得我国的借鉴与引用。
在退火窑结构方面,比利时克纳德(UD)式退火窑,增加了可以方便拆卸的喷镀区,其上可以安装喷镀设备来生产镀膜玻璃。
在加热区增加了抽屉式电加热器和管束式辐射冷却器,来更好地调节退火窑顶部、底部和边部的温度。
图1-1克纳德(UD)式退火窑A区结构简图
法国的斯坦因(STEIN)式在此方面采用热风循环逆流间接冷却玻璃板,其中电加热器不直接布置在窑内,而是安装在窑外的冷却风系统中,通过调节辐射冷却器进口的空气流量和初始温度来达到控制窑内温度的目的。
图1-2斯坦因(STEIN)式退火窑热风循环逆流冷却装置
1.3退火窑的基本结构和温度控制系统的工作原理
1.3.1退火窑的基本结构
玻璃生产线退火窑为钢壳隧道式结构,按退火特点可分为间歇式、半连续式和连续式。
就连续式退火窑而言,其结构一般由窑膛、传动装置、加热及温度控制系统组成。
由于玻璃制品的不同,又可将连续式退火窑分为网带式、辊轮式和蜗杆式。
网带式退火窑的网带用钢丝编织而成,在退火窑的高温段,网带由无缝钢管或钢轨托住,在低温带由钢辊托住。
网带的传动装置包括主动轮、X紧装置和纠偏装置等。
图1-3网带式退火窑传动装置简图
辊轮式退火窑的辊子由吊挂式轴承支承,通过无级调速驱动传动轴,由固定在传动轴和辊子轴端的螺旋齿轮副带动。
窑的宽度取决于玻璃制品的产量及窑长,一般从1.2m~2.5m,不希望大于2.5m。
窑膛的长度根据退火曲线、网带移动速度及厂房条件等因素来确定。
退火窑沿长度方向可分为A区、B区、C区、D区、E区、和F区。
其中,A、B、C区的钢壳内有保温层,内设电加热器和辐射冷却器,故称为保温区;
D和E区为封闭钢壳结构,内设热风循环冷却装置,故为缓冷区;
F区有封闭式和敞开式两种类型,内设强制冷却装置,故为快冷区。
退火窑的长度可以根据季节和外部环境气温来调节。
1.3.2温度控制系统的工作原理
就目前广泛采用的连续式退火窑而言,其工作特点是玻璃制品在退火窑内连续移动,但退火窑内各区温度恒定不变。
因此,合理控制玻璃的温降速度,保持各区温度的连续均匀性,成为退火窑在退火操作中的关键。
在退火窑工作时,通过输送装置的连续移动,将玻璃制品以特定的速度输送到退火窑内进行退火。
退火过程是很严格的一项操作,之所以这么说,是因为对于不同的玻璃制品,其厚度、形状、大小、质量等因素不尽相同,这就决定了其退火曲线的不同。
退火曲线又与温度和时间有着密不可分的联系,其中温度与时间的比值称为温降速度(
),用公式表示为:
(1-1)
在玻璃制品退火之前要先明确它们的退火曲线,并根据玻璃制品的形状和尺寸选择合适的输送装置。
退火曲线与输送装置的合理选择是很重要的,然而控制合理的温降速度才是关键的。
其中时间改变量:
(1-2)
其中玻璃退火曲线如图1-4所示:
图1-4玻璃退火曲线举例
由式(1-1)和(1-2)可得:
(1-3)
式中:
:
温度变化量(℃)
时间改变量(
或
)
退火区间的长度(
)
输送装置的移动速度(
由(1-3)式可得温降速度
与温度变化量
及输送装置的移动速度
成正比,与退火区间的长度
成反比。
然而对于特定的退火窑,其退火区间的长度
是固定的;
对于同样的玻璃制品,由于化学成分的构成大致相同,所以温度控制区间的温度变化
也可以认为大致相同,故在(1-3)式中可以将退火区间的长度
和温度变化量
认为是常量。
从而得出:
玻璃的温降速度
主要取决于输送装置的移动速度
,为使速度能灵活控制调节,可以采用无机变速系统,输送装置的速度采用变频器调节,从而实现输送装置速度的灵活控制。
然而,要保证各温度区之间温度的合理控制,需要靠温度控制系统发挥作用。
温度控制系统的控制原理大致可以概述为:
先通过温度检测元件对退火窑内温度进行检测,然后检测的实际温度和设定的温度进行比较,比较后的结果输送到温度控制回路,最后再通过温度控制回路对退火窑内的温度值进行检测、控制,使各区温度值都能控制在设定的X围内。
1.4设计方案的改进
首先是输送装置的改进,针对目前玻璃生产线连续式退火窑中普遍使用的输送装置(网带式、辊轮式、蜗杆式)的结构特点,可将以上输送装置集中在一个退火窑中,使该退火窑对大多数玻璃制品都能实现良好退火。
这样就可以实现由以往的一维输送改为三维输送,退火制品的X围也可以大大增加。
其中各个输送装置在结构上是一体的,但在速度调节上是单独执行的,即当一个输送装置处于工作状态时,其余的输送装置的传动机构不工作。
这样的无锁结构除可以节约电能外,还有一定的安全性和可靠性。
又由于各输送装置所需要的速度不尽相同,为此可采取无级变速系统,较以往单一的输送速度,更灵活、方便,可以实现速度调节的最优方案,达到提高退火质量的目的。
其次,对于控制系统方面,采用PLC控制生产过程的起动与停止,较以往的手动控制更灵活、自动,同时也提高了整个控制系统的稳定性和安全性。
并引入变频器来灵活调节输送装置的输送速度,从而实现无级变速的效果。
最后,在温度检测控制方面,采用周波控制系统来对退火窑内的温度进行检测,这样可以大大提高温度控制系统的灵敏度和可靠性,实现各温度区温度的准确控制与调节。
1.5本设计的主要完成的任务
(1)设计一个综合性强的三维输送装置;
(2)利用PLC控制变频器实现无级调速;
(3)采用周波温度控制系统,提高温度控制效果。
第二章关于玻璃生产线退火窑的设计
2.1玻璃的退火与退火窑
2.1.1退火的概念、目的和过程
所谓玻璃的退火主要是指:
将玻璃制品置于退火窑中,经过足够长的时间,在退火温度X围以特定的速度,即按一定温度曲线进行冷却的过程。
退火的目的则是消除或减弱玻璃内部的残余应力至允许值,并防止产生新的应力,实现光学的均匀性。
玻璃的退火过程可以分为两个主要过程:
一是减弱或消除内应力;
二是防止产生新的应力[7]。
2.1.2玻璃制品内应力的类型及成因
待退火的玻璃制品中的应力有热应力、结构应力和机械应力之分,其中结构应力属于永久应力;
机械应力属于暂时应力;
热应力又有暂时应力和永久应力之分。
暂时应力是随温度差(温度梯度)的存在而存在,随温度差的消失而消失的热应力,亦即是暂时存在的,不需要人为操作即可减弱或消失的应力。
永久应力是当高温玻璃经退火到室温,并达到温度均衡后,玻璃中仍然存在的热应力,也称为残余应力。
玻璃退火后的残余应力随玻璃的厚度增加而增加。
应力产生的原因在于:
玻璃制品在加热或冷却的过程中,由于其导热性能的差异,在其表面层和内层之间必然产生温度差,因而在内外层之间就会产生应力。
玻璃制品在冷却时,由于内外层存在温度差,即玻璃外表层温度低于内层,从而使外表层的收缩大于内层,这就导致外表层产生拉应力,内表层产生压应力。
当外表层不在降温,内层却随着温度的不断降低而继续收缩,所产生的应力与前期相反,若两者大小相等,则温度差消失后,就没有应力产生,若不相等,则产生永久应力。
应力产生的原因与温度区域的冷却速度、温度差、黏度和玻璃厚度有关[11]。
2.2退火窑的分类及要求
2.2.1退火窑的分类
退火窑分为间歇式退火窑、半连续式退火窑和连续式退火窑三种类型。
间歇式退火窑是指:
玻璃制品固定,窑内温度按工艺要求随时间变化,通常与坩埚窑配合退火。
加热方式又分为明焰式和隔焰式两种形式。
半连续式退火窑是指:
玻璃制品间歇移动,窑内各处温度基本按退火曲线确定,且恒定不变。
但各处温度变化是不连续的,即跳跃式的。
其中按结构形式又分为牵连式和隧道式两种。
连续式退火窑的特点是:
玻璃制品连续移动,窑内各处温度恒定不变。
是目前工厂中普遍采用的一种形式。
而连续式退火窑又分为网带式、辊轮式和蜗杆式三种类型。
网带式退火窑是用网带输送玻璃制品,玻璃制品放在网带上,网带的移动是连续的,适用于单件玻璃制品的退火。
辊轮式退火窑是在窑内有一系列辊道,玻璃制品在辊道上向前移动,适用于平板玻璃、压延玻璃的退火。
蜗杆式退火窑类似于辊道式结构,其特点是在窑内有一系列蜗杆,通过蜗杆的旋转将玻璃制品输送到窑内,此类退火窑适用于管状类玻璃制品的退火。
图2-1网带结构图图2-2辊轮简图
2.2.2对退火窑的要求
无论什么类型的退火窑都应该满足以下要求:
(1)保证玻璃制品的退火质量;
(2)尽量降低能量消耗;
(3)在确保质量、降低能耗的基础上加快生产速度,提高生产效率;
(4)退火窑的结构也要求简单、操作也要方便。
2.3退火窑的分区
按玻璃制品的退火工艺要求将退火窑分为保温区、缓冷区和快冷区。
2.3.1保温区(A区、B区、C区)
退火窑前区(A区)是在退火窑的最前端为退火作准备的区段,在正常生产的情况下,玻璃制品进入退火窑的温度一般在580~600℃,此温度高于玻璃的最高退火温度,可以不再加热。
退火区(B区)是紧接A区之后的区段,玻璃制品在该区段内通过缓慢冷却至退火下限温度,该区域也是退火过程中最关键的区域,这是因为经退火后的玻璃制品中的永久应力大小及其分布状况,主要取决于玻璃制品在该区的冷却速度和温度分布状况。
B区的主要作用是消除玻璃中的残余应力。
温度一般控制在510~520℃左右。
冷却区(C区)亦称后退火区,是在玻璃退火的下限温度以下进行冷却的区段。
冷却的速度较A区、B区增加,但不能太快,此阶段玻璃制品的产生的应力为暂时应力。
若冷却速度过快,则会使暂时应力过大而使玻璃破裂,出C区的温度一般在410~420℃左右。
2.3.2缓冷区(D区、E区)
图2-3退火窑整体结构简图
过渡区(D区)是C区和E区之间的过渡区域,该区段内退火窑没有保温设施,靠钢壳体散热。
出D区的温度为370~380℃左右。
热风循环冷却区(E区)是紧接过渡区(D区)的区段,玻璃制品在该区段内采用热风循环冷却,对玻璃制品进行吹风对流冷却,能使冷却速度较后退火区(C区)有所提高,使玻璃制品的表面温度由370~380℃降到220~240℃。
实践证明,此区段不能用室温空气直接冷却玻璃,以免玻璃冷却温度过大而引起炸裂。
2.3.3快冷区(F区)
快冷区(F区)也称为强制冷却区,是整个退火区的最后一个区段。
玻璃制品在该区段内被强制冷却。
相应的冷却方式可以为自然冷却和强制冷风冷却。
温度差△T在200℃左右,故可以使最终退火后的玻璃制品的温度控制在20~40℃左右。
2.4退火窑输送装置的改进
2.4.1传统退火窑输送装置的介绍
连续式退火窑输送装置是根据玻璃制品的特点而确定的。
例如:
对于形状较小的玻璃制品宜采用网带式输送装置;
对于像玻璃板、压延玻璃等大型玻璃制品,宜选用辊轮式输送装置;
对于管状类玻璃制品,宜采用蜗杆式输送装置。
这是目前工厂中广泛采用的各类退火窑输送装置。
2.4.2改进后的退火窑三维输送装置
连续式退火窑三维输送装置是在传统的输送装置的基础之上,将各类输送装置进行整合在一起的复合型输送装置。
其改进后的结构简图如图2-4所示。
图2-4退火窑三维输送装置简图
从图2-4中可以看出,改进后的复合型输送装置是用固定旋转支座将各类传统的输送装置连接在一起的。
固定旋转支座设计成等边三角形的形状,对于网带轮和辊轮两端都添加轴承及轴承支座装置,从而保证输送轮的良好旋转。
各类输送装置的转换是通过中心转轴的转动实现的,而中心转轴的转动又是通过中心转轴两端的齿轮副结构完成的。
齿轮副是由大小两个直齿轮外啮合组成的,其中小齿轮直接固定在减速器的输出轴上,通过编码器来调整小齿轮转动的角度,从而带动大齿轮转过合适的角度,使输送装置准确地转到所需要的位置,此时导通该输送装置所对应的行程开关SQ2(SQ3或SQ4)。
主动轮传动机构在压力继电器的作用下导通主动轮处行程开关SQ1。
并通过摩擦式离合器装置将主动轮与输送轮的转动连接在一起,达到稳定转动的目的。
当切换到蜗杆机构时,由于其转动方向与网带轮和辊轮都相差90°
,因此采用锥齿轮传动副将传动方向进行合理的调整,为简化加工工艺,将锥齿轮的传动比设定为1:
1,可以实现蜗杆机构良好转动的效果。
其中锥齿轮的结构简图如图2-5所示。
由于锥齿轮结构的增加,主动轮传动机构处也要安装相同的锥齿轮来实现蜗杆机构的良好旋转,只是在其他传动状态主动轮处的锥齿轮不参与啮合而已。
图2-5锥齿轮结构简图
考虑到蜗杆机构在整个退火窑中的长度及同轴度要求,在固定旋转支座上安装蜗杆导向支座。
在蜗杆导向支座的设计上,一要保证蜗杆的输送作用不受影响;
二要保证在蜗杆机构不处于工作状态时的稳定性。
因此将蜗杆导向支座设计成3/4个圆弧的形状,这样不仅可以解决上述问题还可以有效地解决蜗杆机构由于重力而产生的偏心现象,同时也保证玻璃制品在退火窑内退火的过程中高度达到一致,从而提高退火窑退火的质量。
主动轮传动结构与从动轮的传动是通过链传动实现的,当然这仅是针对辊道式输送机构而言。
链传动无弹性滑动和整体打滑现象,因而能保持辊轮准确的平均传动比,传动效率较高。
又因链条在传动中不需要X得很紧,所以作用于轴上的径向力较小,对轴承的压力也相应的减小。
链条采用金属材料制造,适合在退火窑内高温的环境中工作。
为保证主动轮与各从动轮的转向一致性,采用双排链结构,在增加传动效率的同时,也使链的承载能力有所增强。
2.4.3主要零部件的设计计算与说明
目前工业中的退火窑的长度一般在15~20m左右,宽度一般在2.5~3m左右。
输送装置的材料大部分为钢材,为减少整个输送装置的整体质量,在满足刚度和强度的条件下,将网带轮、辊轮以及蜗杆机构都设计成铝管结构。
网带轮和辊轮的最大直径在50~60mm左右,铝管厚度在8~10mm左右。
在计算整体质量时,直径取
,长度取
,厚度
。
每隔2m安装一个该转位机构,需要8~10个,以
计算,则每个辊轮(网带轮)的质量:
(3-1)
蜗杆的直径在30~40mm,由于强度要求较低,厚度在5~8mm。
直径
,厚度取
则每根蜗杆在
长度上的质量:
(3-2)
加上蜗杆导向支座的质量,可近似认为各类输送装置的质量相等,均取
粗略估计固定旋转支座的质量在20kg左右,中心转轴的质量在50kg左右。
每组输送装置的质量
,并结合(3-1)和(3-2)式计算总质量为:
(3-3)
根据本设计的传动要求,传动装置的减速器的传动比
,大小齿轮的齿数比
根据转位时间,设定电机转速为
,采取两对齿轮副结构,电机功率取20KW,计算转矩为:
(3-4)
考虑到网带轮到中心转轴的距离及大小齿轮啮合的转动情况,设计大齿轮直径为800mm,小齿轮直径为250mm,可以满足转矩的要求。
其中大齿轮的结构简图如2-6所示:
电动机和减速器固定安装在两个固定旋转支座之间的一个横梁上,该横梁的大小、形状和刚度根据电动机和减速器的质量而定。
在整个输送装置的两端均设有转位机构固定支座,来承担整个输送装置的大部分质量。
为使输送装置的转动更加灵活,在中心转轴的两端均增加一对深沟球轴承,这样可以明显减小整个输送装置转动时产生的摩擦力,也达到减少大齿轮转矩的目的,保证转位机构整体的稳定性。
图2-6大齿轮零件图
退火窑的底座为半圆结构,为保证退火窑整体的稳定性,在半圆的外壳体上安装钢板来对整体进行固定。
退火窑的半圆底座下面设有一定数量、大小适中的孔洞,这样的结构可以实现对玻璃碎屑的及时清理,避免由于碎屑积累过多对转位机构造成影响,也进一步满足生产过程的安全性。
钢板和退火窑底座之间留有空间区域,可以对玻璃碎屑进行暂时存储,当增加到一定量时可以进行集中清理。
改进后的退火窑输送装置,可以满足对各类玻璃制品进行退火的要求,转动灵活、操作方便。
但是在减轻整体质量方面,仍需要在具体的生产过程中予以逐步完善。
结合以上各零部件的设计,完成最后装配图如图2-7所示:
图3-7装配图
第三章温度控制系统的硬件组成及软件设计
3.1温度控制系统的硬件组成
3.1.1可编程控制器(PLC)的简介、选用及端口分配
可编程控制器(PLC)是一种以计算机技术为基础的新型工业控制装置,它通常由中央处理单元(CPU)、存储器(RAM、ROM)、输入输出单元(I/O)、电源和编程器等几部分组成。
采用循环扫描的工作方式,编程语言可采用梯形图、控制流程图、指令表等多种方式。
由于可编程控制器是一种无触点设备,通过改变程序即可改变生产工艺,适合批量生产,且具有抗干扰能力强、可靠性高、体积小等优点,因此可编程控制器自问世以来,很快受到工业控制部门的欢迎,并得到广泛的推广与应用。
根据本设计的控制要求,整个控制系统的可编程控制器的输入点及输出点分别为14点和14点。
根据PLC中I/O分配使用原则,以及考虑到要预留出一些I/O点作为扩展使用。
当然,在需要其他一些控制模块(如检测、报警功能模块等)时,预留出I/O点对使用是很方便的。
鉴于以上几点的考虑,选用三菱Fx2N-48MR型PLC,其输入及输出点总数为48,其中输入点为24,输出点为24。
各输入、输出I/O点的分配如表3-1所示:
其中主动轮行程开关SQ1是在压力继电器工作的情况下由于压力作用而导通的,它可以保证在输送过程中的压力稳定,传动平稳。
输送轮处行程开关SQ2(SQ3/SQ4),则是转位机构在转动过程