供热管网波管补偿器爆裂破损原因分析及解决方法.docx
《供热管网波管补偿器爆裂破损原因分析及解决方法.docx》由会员分享,可在线阅读,更多相关《供热管网波管补偿器爆裂破损原因分析及解决方法.docx(10页珍藏版)》请在冰豆网上搜索。
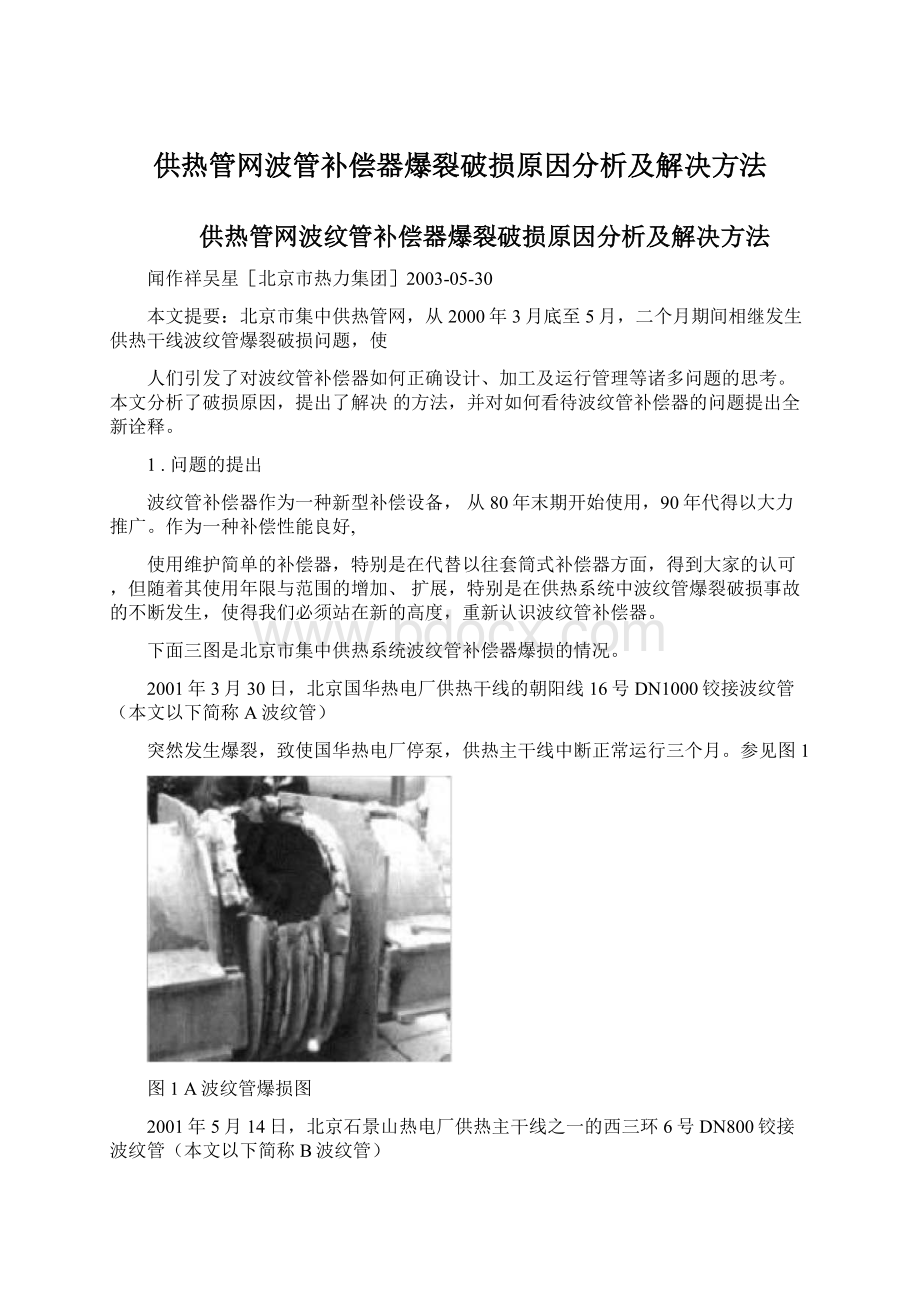
供热管网波管补偿器爆裂破损原因分析及解决方法
供热管网波纹管补偿器爆裂破损原因分析及解决方法
闻作祥吴星[北京市热力集团]2003-05-30
本文提要:
北京市集中供热管网,从2000年3月底至5月,二个月期间相继发生供热干线波纹管爆裂破损问题,使
人们引发了对波纹管补偿器如何正确设计、加工及运行管理等诸多问题的思考。
本文分析了破损原因,提出了解决的方法,并对如何看待波纹管补偿器的问题提出全新诠释。
1.问题的提出
波纹管补偿器作为一种新型补偿设备,从80年末期开始使用,90年代得以大力推广。
作为一种补偿性能良好,
使用维护简单的补偿器,特别是在代替以往套筒式补偿器方面,得到大家的认可,但随着其使用年限与范围的增加、扩展,特别是在供热系统中波纹管爆裂破损事故的不断发生,使得我们必须站在新的高度,重新认识波纹管补偿器。
下面三图是北京市集中供热系统波纹管补偿器爆损的情况。
2001年3月30日,北京国华热电厂供热干线的朝阳线16号DN1000铰接波纹管(本文以下简称A波纹管)
突然发生爆裂,致使国华热电厂停泵,供热主干线中断正常运行三个月。
参见图1
图1A波纹管爆损图
2001年5月14日,北京石景山热电厂供热主干线之一的西三环6号DN800铰接波纹管(本文以下简称B波纹管)
2。
发现已严重破损,四层中已有三层开裂,不能正常运行,被迫中断运行。
参见图
图2B波纹管破损图
2001年5月23日,北京华能热电厂蒸汽主干线DN1000波纹管补偿器(本文以下简称C波纹管),发生了大
量蒸汽泄漏,华能热电厂被迫调整工况,停止蒸汽外供,蒸汽干线停汽三周。
参见图3
图3C波纹管失稳图
接连不断的问题,引起供热界广大技术人员的关注,波纹管补偿器在目前供热管网中被广泛使用,仅北京市集中供热网中就有三千多个,特别是在大口径的供热主干线上,波纹管是目前唯一的补偿设备,一旦发生问题后果十分严重,必须引起高度重视。
本文试分析波纹管爆裂破损各种原因,及波纹管补偿器在设计、生产、施工和运行管理各方面存在的冋题,并在此基础上提出解决冋题的方法。
事故原因我们从6个方面进行了分析,试述如下:
2.1外观观察
A和B波纹管的外观观察呈现一样的特征,波纹管外层的外壁有少量腐蚀产物,但仍然保持银白色的金属光泽,裂纹很细,走向各异。
在波纹管的第一层内壁以及第二、三层的内外壁有大量腐蚀产物附着,不锈钢薄板已经完全失去了金属光泽,坠落地
面已无金属声响,层间堵塞大量腐蚀产物已无结合力,第四层外表面有少量腐蚀产物和小裂纹,内表面附着均匀的薄水垢,无腐蚀产物,表面呈银灰色。
裂纹情况与腐蚀产物相近,以第二、三层裂纹最多、最粗,第一层其次,第四层相对较少、较细。
裂纹扩展方
向具有发散特征,向各个方向开裂。
以上观察我们可以判断:
波纹管的腐蚀开裂应是外层逐层向内各层波纹管发展的,只是各层波纹管腐蚀破坏在
时间上的先后关系,才出现各层腐蚀开裂程度上的明显差异。
腐蚀来自波纹管外,在进入波纹管层间后,连续并加快了腐蚀的产生。
C波纹管内外各层均无腐蚀,但已严重变形,经着色分析未发现层间进汽现象。
由此我们可以排除腐蚀及层间进汽原因而产生的破坏。
2.2腐蚀产物分析
从波纹管一至四层裂纹及断口处取腐蚀产物,用X射线荧光分析仪,在实验条件下查明,腐蚀产物中主要元素
为O,Fe,Cr,Ni,Si,Al,Mg等,所有腐蚀产物均含有Cl元素。
对腐蚀产物作能谱分析,其结果参见表1。
表1波纹管第1层裂纹及断口处腐蚀产物能谱分析结果
1
2
3
4
外层
内层
外层
内层
外
层
内层
外层
内层
1.49
4.22
4.24
1.12
0.82
0.43
2.47
0.29
5.53
0.72
1.29
0.35
2.58
1.33
0.47
CI
1.07
2.35
1.25
0.67
12.15
12.15
3.44
24.29
4.02
16.46
6.45
9.77
3.39
1.93
31.13
1.11
11.72
9.89
0.75
5.69
0.17
Si
3.81
2.88
3.31
3.76
1.90
17.51
4.11
1.76
0.61
9.01
1.35
1.35
0.24
1.15
2.38
0.23
S
1.66
0.82
0.39
0.31
0.31
0.98
4.11
2.21
10.63
50.88
1.29
3.54
5.67
1.50
0.67
Ca
6.16
2.02
4.13
2.83
0.57
1.11
1.01
2.37
4.06
1.87
3.42
1.02
3.28
1.34
22.82
2.58
60.27
5.04
7.65
20.28
27.35
17.72
Cr
51.11
34.53
17.87
44.25
18.23
从表1可以看出,从外层至内层均有Cl元素的分布及富集,并大大超出了导致304不锈钢应力腐蚀开裂临界
值的Cl含量(500ppm=0.050%)可以认为在含有Cl的环境中,再加上温度,应力及材质因素,构成了304材质应力腐蚀开裂(SCC)方面的很大敏感性。
随着Cl浓度增加,不锈钢的应力腐蚀敏感性增加,能谱分析测到的氯元素重量百分比最低为4300ppm,最高为120000ppm,已经完全具备了发生应力腐蚀的条件。
2.3材质及微观金相分析
对波纹管基材的化学成分分析结果如表2。
表2开裂波纹管基材化学万分分析%
C
Si
Mn
P
S
Cr
Ni
Fe
开裂波纹管
0.054
0.55
1.01
0.0035
0.0030
17.98
8.07
余
基材
量
304SS
<0.08
<1.0
<2.0
<0.0035
<00
18.00〜
8.00〜
余
(AISI)
0030
20.00
10.50
量
0Cr19Ni9
<0.08
<1.0
<2.0
<0.0035
18.00〜
8.00〜
余
(GB1220-92)
0.0030
20.00
10.50
量
对金相试样我们同时进行了扫描电镜分析,对这两项的分析表明:
2.3.1.材质是符合304不锈钢标准的,但Ni元素含量接近标准成分的下限,降低了304不锈钢奥氏体组织
的稳定性,外力将导致马氏体相变。
2.3.2•逐层金相组织观察均发现形变马氏体。
2.3.3•金相裂纹在微观上以穿晶为主,是典型的应力腐蚀裂纹特征,应力腐蚀破裂是引起波纹管腐蚀开裂失效的重要原因。
2.4应力分析
应力的存在是导致应力腐蚀开裂的必要条件之一,应力的来源主要有:
波纹管加工成型过程中产生的形变应力
和残余应力;在服役期间的工作应力;装配不当导致的装配应力过大;腐蚀产物引起的楔入应力。
采用非线性有限元对设计和工作工况下的波纹管作应力分析。
波纹管变形应力分布状况如图4所示。
图4波纹管变形及应力分布状况图
A区域或凸边B区域上,将各种工况条件下波纹管
波纹管的最大应力区出现在角位移平面内即波纹管的凹边
角位移平面内凸侧最大拉力OBMAX作一对比,如表3所示
表3四种工况下波纹管的&MAX值
内压P/MPa
角位移
怎max/MPa
设计工况
1.6
9。
543.14
工作工况
0.86
7。
446.2
0.86
8。
535.7
0.86
9。
638.6
以上分析表明,波纹管总体应力水平虽然很高,仍不足以导致波壳的爆裂。
但由在波纹管层间的大量腐蚀产物体积远远大于原有金属的体积,这样在裂纹尖端便产生了不可忽视的楔入应力,有效地促进了应力腐蚀裂纹的发生和发展。
2.5设计运行参数分析
2.5.1A、B波纹管原始设计参数:
设计压力:
1.6Mpa
设计温度:
350°C
额定角位移:
9°(A、B波纹管)
角位移刚度:
3562N-rm/°
许用疲劳寿命:
1000次
波纹管材质:
304不锈钢
单层厚度:
1.2mm
从波纹管服役期间运行参数来看,A、B波纹管是热水管网,运行参数远小于设计参数
2.5.2C波纹管原始设计参数
设计压力:
1.6Mpa
设计温度:
300°C
轴向补偿量:
270mm
许用寿命:
1000次
波纹管材料:
316
经重新核实计算,该波纹管补偿器轴距80米,实际运行中最高温度达到290°C以上,补偿量已超过设计补偿
量。
另外,设计补偿器已临近产品补偿量极限,也是重要原因之一。
2.6工程情况分析
B波纹管安装示意如图5所示。
y
142m
A117m
105m
30irr
图5B波纹管安装示意图
经工程现场与设计图纸核实,发现有两大缺陷:
第一是设计的两个绞接型波纹管均为6波。
但工程实际中使用
的是一个4波波纹管,另一个是6波波纹管,设计与工程实际不符;第二是固定支架未安装卡板。
经分析,这两个缺陷是B波纹管破损的重要原因,虽然经计算,在固定支架无卡板时,仍能补偿相应的热伸长
4波波纹管的刚度较小,致使应力主要集中在4波波纹
量,但补偿量已接近极限,同时,由于两个波纹管型号不一,
管,造成在相同使用环境(cl-浓度相同)下,4波波纹管发生破损
C波纹管在施工安装过程中,考虑各方面因素未预拉伸,致使波纹管运行中的安全系数大大下降。
2.7分析结论
2.7.1A、B波纹管的爆损是由应力腐蚀造成的,腐蚀主要来源于外部的cl元素。
A波纹管的破损主要来
自环境。
而对B波纹管,由于增加了施工所带来的不利影响而加快了应力腐蚀。
cl-元素主要来自两部分,一是流入管道的天然水、化雪盐水及污水,二是施工中所用含Fecl3的防水剂、防冻
剂等。
2.7.2加工过程中所产生的形变马氏体不仅对材料的组织和结构,而且对材料力学性能和腐蚀行为产生明显影响。
形变马氏体建立了一条对氯脆敏感途径,成为应力腐蚀裂纹扩展的活性通道。
2.7.3304不锈钢Ni元素含量影响组织的稳定性,易导致形变马氏体产生。
2.7.4应力是腐蚀的条件,特别是腐蚀产物的楔入应力,加快了腐蚀的速度。
2.7.5位移应力对波纹管设计的影响不容忽视,另外,运行参数过高,安装时未预拉伸及设计参数接近设备极限,都是重要影响因素。
3.解决方法
3.1产品设计、加工方面
3.1.1改变以往304不锈钢材,选用耐腐蚀的超低碳奥氏体不锈钢(如316L)。
3.1.2充分认识加工过程形变马氏体对波纹管带来的各方面的影响,尽可能减少形变马氏体的生成。
为降低加工残余应力和受载应力,推广首