基于BPR的车间布置设计Word格式.docx
《基于BPR的车间布置设计Word格式.docx》由会员分享,可在线阅读,更多相关《基于BPR的车间布置设计Word格式.docx(25页珍藏版)》请在冰豆网上搜索。
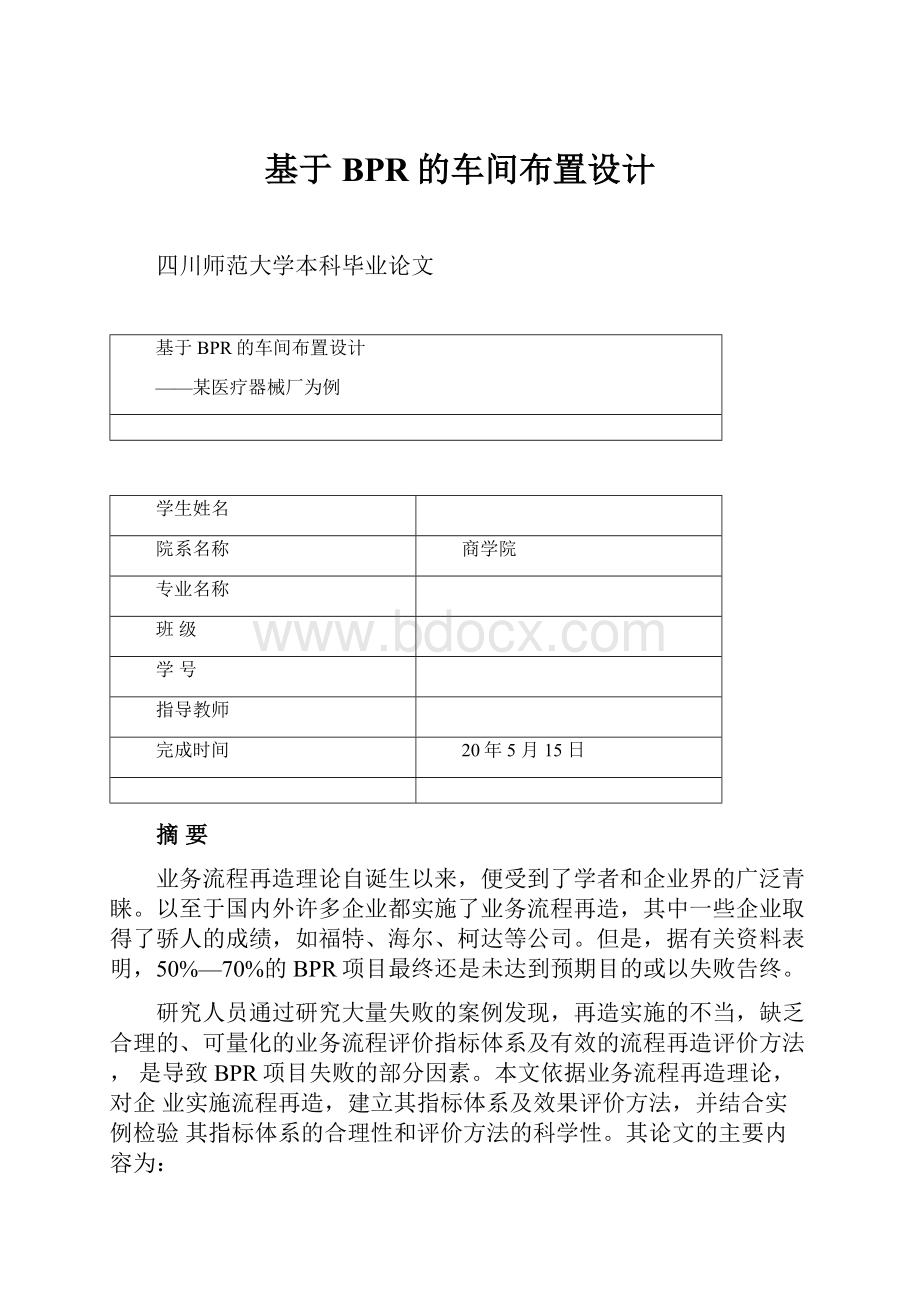
Finally,accordingtoimprovetraditionalAHPinuseofIntervalNumberandFuzzyEvaluationinuseofAverageSatisfactionLevel,FuzzyComprehensiveEvaluationmodelofBPRwasfounded.Andaccordingtoresearchthecompanyrealexample,theevaluationwaywasconfirmedtobescientificandreasonable.
Keywords:
BPR,AverageSatisfactionLevel,FuzzyEvaluatio
目录
一、我国BPR研究现状1
二、业务流程再造的方法2
2.1全新式再造法2
2.2渐进式再造法2
三、济南某医疗器械厂车间布置实例分析2
3.1.背景及其研究目的2
3.1.1研究的背景和意义2
3.1.2研究的目的和内容3
3.2公司车间布置和经路现状的描述与分析3
3.2.1企业概况3
3.2.2三氧治疗仪的生产工艺流程3
3.2.3公司车间布置和经路的现状4
3.3公司车间布置和经路存在的问题及分析6
四公司车间布置和经路优化方案设计及效果评价7
4.1三氧治疗仪生产流程的分析与优化7
4.2应用布置经路分析对车间布置和经路进行改进11
4.3对车间布置进行分析改进12
4.4优化方案的效果评价19
结论20
参考文献21
致谢22
基于BPR的车间管理布置研究
——以某医疗器械厂为例
一、我国BPR研究现状
在激烈的竞争环境中,企业要具有强大的市场竞争力并生存下来将变得更加艰难。
如果企业进行科学的变革,则企业有可能获得重生,不仅能解决上述问题,甚至有可能进入新的发展阶段;
如果企业未能及时变革,对出现的问题听之任之,或注意到了问题的出现却做出了不科学的变革和调整,企业有可能就此一蹶不振。
因此,改变现状是迫切的、必须的,也只有改变现状才能有立足之地。
而业务流程再造(BusinessProcessReengineering,以下简称BPR)则将成为其化梦想为现实的有效途径之一。
随着市场经济的发展,为适应卖方市场向买方市场的转变,企业的生产模式发生了变化,即从大批量少品种向多品种小批量或大规模定制生产转换。
从20世纪末开始到今后一段时间,制造业竞争的焦点将不仅仅是价格的竞争,而是适应市场需求、客户快速反应、准时供货等方面的竞争。
然而据统计,在工厂的生产活动中,从原材料进厂到成品出厂,物料真正处于加工检验的时间只占生产周期的5%-10%,而其余时间都处于停滞和搬运状态。
在制造业中,总经营费用的20%-50%是物料搬运费用,而优良的工厂平面布置可使这一费用至少减少10%-30%。
工厂布置的方法和技术一直是工业界不断探索的问题。
本文即应用BPR法对某厂的机加工车间设施布置进行优化,有效地提高了系统效益。
BPR是近年来我国的热门研究课题之一,有关BPR的文章、出版物很多,大致的研究内容包括以下三个方面:
理论研究、实施研究、评价研究
目前对于业务流程再造的实施方法、步骤以及流程再造效果评价指标体系的研究不够深入。
他们所提出的业务流程分析指标体系中,有的仅提出业务流程再造的目标,而没有提出业务流程评价指标体系;
有的只涉及到业务流程的某一方面,缺乏系统的考虑。
根据当前业务流程再造的需要,有必要建立一套科学的评价指标体系进行评价。
二、业务流程再造的方法
业务流程再造是一种不断改进的哲理,它以利用信息技术、重新设计组织业务流程为手段,以着眼于顾客利益、流程增值最大化为目标,通过重新设计组织运作流程来改善组织的绩效,最大限度地提升提供附加价值活动的效率,并尽量减少不提供附加价值活动的消耗,根据许多成功实施的案例表明,业务流程再造的方法可以分为全新式再造法和渐进式再造法。
2.1全新式再造法
为了使目标得到几倍甚至几十倍的改进必须以完全不同的方式做事。
全新式再造法将从目标开始,逐步倒推,设计能够达到要求的流程。
组织采取全新式再造法的原因可能是由于他们认为已经到达“危机点”状态,也可能是由于他们先前采取渐进式的再造努力未能取得显著的业绩改善。
总体说来,这种方式的优点是抛开现有流程中所隐含的全部假设,从根本上重新思考企业开展业务的方式。
这种方式提供了业绩飞跃的可能性,使得所求结果成倍地改变。
缺点是这种方式的风险高,组织经历的痛苦深,对正常运行干扰大。
2.2渐进式再造法
渐进式再造法通过对现有流程进行分析的基础上,对现有流程不合理处进行改进,它是一种“无创伤性再设计”,这种方式的优点在于改变可以逐渐地一点一滴地积累实现,因此能够迅速取得收效,并且风险较低,对正常运营干扰小。
当在大范围基础上应用时,这种渐进方式的确能够产生显著的业绩改善。
渐进式改造应该最终成为组织整体生命的一部分。
缺点是仍然以现有流程为基础,创新流程虽然不是不可能,但与全新设计方式相比,则不大容易实现。
三、济南某医疗器械厂车间布置实例分析
3.1公司车间布置和经路现状的描述与分析
3.1.1企业概况
此医疗有限公司成立于2001年,地处济南市商务港,交通便利,地理环境优越,是一家集医疗新技术、医疗器械、医院策划营销的一所专业医疗科研机构,公司下属四家私立医院,以疼痛微创介入治疗、妇科臭氧、输卵管介入、子宫肌瘤等国内外最新治疗技术为主,赢得了广大用户的青睐和支持。
本公司生产的主要产品为“三氧治疗仪”。
三氧治疗仪主要用于治疗各种原因引起的体表损伤性创面以及和病毒性肝炎的辅助治疗,并广泛应用于快速恢复,提高血氧浓度,缓解疲劳,预防癌基因突变及早期尚未发现病人的控制和遏制。
三氧治疗仪的原材料主要以外购为主,公司将采购的原材料在生产车间进行加工和组装,最后完成产品的包装并进行入库。
3.1.2三氧治疗仪的生产工艺流程
企业的产品--三氧治疗仪的主要部件为真空泵、还原盒、点火线圈、电离管、转子流量计、主机箱、智能控制系统、治疗舱。
原材料从原材料库和成品仓库进入总装区后已基本组装在机器上,故各作业单元之间的物流量变化不大。
总装区之后剩下的加工环节主要是进行气路、电路连接、检验和包装。
产品从开始生产到完成入库共需要15道工序,从原材料领用开始到成品入库结束。
具体内容如图3-1所示。
成品入库
图3-1产品工艺流程图
3.1.3公司车间布置和经路的现状
此公司的生产车间较大,长约80m,宽约50m。
各个分区都被分配在车间的某个平面上。
每个分区用临时性材料相互间隔,以避免原材料等物品的丢失,并且对于各个分区位置的变动也提供了方便。
此公司生产车间内共有10个分区,依次为原材料库和成品仓库、半成品库、气路装配区、总装区、裁切固定区、包装区、合格证发放区、安全检测区、性能检测区、办公区。
各个生产区域的面积为:
裁切固定区=310m2;
总装区=375m2;
原材料库和成品仓库=186m2;
半成品库=138m2;
气路装配区=124m2;
包装区=379m2;
合格证发放区=173m2;
性能检测区=173m2;
安全检测区=163m2;
办公区=260m2。
图3-2为该公司生产车间的平面布置图。
办公区
图3-2生产车间的平面布置图
将车间内产品的生产流程表示在车间布置图上可以得到车间的物流线路图,如图3-3所示。
6
图3-3车间内的线路图
通过图3-3了解到车间内总体的物流经路状况为:
原材料库和成品仓库→总装区→裁切固定区→气路装配区→总装区→安全检测区→性能检测区→合格证发放区→包装区→原材料库和成品仓库。
3.2公司车间布置和经路存在的问题及分析
经过提问分析表的分析可知车间布置和经路存在许多问题。
具体来说主要有:
1、企业生产车间布置存在着许多问题。
由于济南优科医疗有限公司是租赁的别人的厂房,为利用原有的生产条件所以并没有对车间做合理的规划与布置,故车间布置和经路上存在许多问题。
通过分析,发现车间布置存在以下问题:
(1)各区域位置过于分散造成搬运距离太长,在制品库存过多。
由于车间内搬运距离有292m,不仅造成了人力、物力的大量浪费,而且还造成了车间内在制品的积压。
(2)车间内存在的半成品库不仅占用车间面积,并且也造成了搬运距离的增加。
未加工完的产品在加工时间结束时必须搬运到半成品库,同时待第二天开始生产时又必须搬运到相应车间,造成了搬运距离的大大增加。
(3)各生产单位的位置没有考虑产品的生产工艺流程,从而导致了产品在生产中的搬运距离加大,同时易造成搬运的碰撞和混乱。
2、车间布置的不合理同时导致了车间内的经路存在着许多问题,具体来说主要有:
(1)气路装配区的位置不合理造成搬运距离过长。
从裁切固定区加工完成之后,需要经过很长的距离并跨越总装区才能到达气路装配区,搬运距离增加,同时也很容易造成气路装配区的等待。
(2)合格证发放区、性能检测区以及安全检测区三者的位置不合理。
流经三者的物流构成了一个循环,这样很容易造成车间阻塞,从而导致在制品数量增多。
(3)包装区与原材料库和成品仓库的距离过远造成搬运距离过长。
产品包装完成之后,必须经过很长的距离才能进入成品库,这样大大增加了搬运成本。
(4)气路装配区和总装区还有安全检测区的构成了一个搬运回路,安全检测区和合格证发放区以及包装区构成一个回路。
回路的出现会造成车间内搬运的碰撞,减慢搬运的速度,应该加以改进。
总之,车间布置和经路是很不合理的:
搬运距离长,搬运时间耗费过多,车间内物流经路混乱,在制品数量多,等待时间长,检查次数多。
因此急需用工业工程的有关方法加以改进,以缓解车间内混乱和低效的状况。
四公司车间布置和经路优化方案设计及效果评价
对生产流程进行优化是进行车间布置和经路优化的基础,只有先消除产品生产流程中存在的浪费,才能保证优化完成后车间布置和经路的合理性,故本文先对三氧治疗仪的生产流程进行优化。
4.1三氧治疗仪生产流程的分析与优化
4.1.1现行产品生产流程程序图
根据产品的工艺流程图和现场的调研,我得出了三氧治疗仪的现行生产流程程序图,该产品现有流程程序图共有29项,加工次数为7次,加工时间为42.9min,搬运次数为292m,检查次数为8次,产品生产总时间为151.3min。
具体内容如表4-1所示。
表4-1三氧治疗仪生产流程程序图
工作名称:
三氧治疗仪编号:
01
制造
开始:
结束:
方法:
现行方法
研究者:
张瑞日期:
2010年05月15日
审阅者:
日期:
年月日
统计
项别
次数
时间/min
距离/m
加工○
9
42.9
检查□
8
27.7
搬运→
72.4
585
等待D
2
5.1
储存▽
1
3.2
工作说明
人数
工序系列
加工
检查
搬运
等待
储存
1、原材料领用
6.3
○
□
→
D
▽
2、搬运至总装区
18
4.5
3、台车预处理
4、电子元器件安装
10.5
5、搬运至裁切固定区
20
6、导线裁剪
2.2
7、检验
3.5
8、焊接
4.7
9、裁管
10、检验
3.0
11、搬运至气路装配区
50
12.5
12、气路连接
4.2
13、检验
3.7
14、搬运至总装区
26
6.4
15、调试检验
4.4
16、外观检验
2.0
17、搬运至安全检测区
42
10.1
18、排队等待
2.1
D
19、检验
4.1
20、搬运至性能检测区
15
3.8
21、排队等待
22、检验
3.9
23、搬运至合格证发放区
14
3.4
24、发放合格证
25、搬运至包装区
27
6.5
26、装箱检验
3.1
27、装箱
5.3
28、搬运至原材料库和成品仓库
81
20.1
29、储存
由表4-1中的统计分析得知生产流程存在着许多问题:
1、从各个项目的次数上来看,三氧治疗仪制造过程共有9次加工,8次检查,9次搬运,2次等待和1次存储,其中搬运和检查次数较多。
2、产生生产过程中所经过的搬运距离较长。
由流程程序图的统计可知搬运距离为292m,距离较长。
3、从各个项目所占用的时间上来看,产品生产的总时间为97.2min。
其中检验占用了14.2%,搬运占用了大约37.2%。
4.1.2优化完成后的生产流程程序图
根据上述改进措施可以得到优化完成后的生产流程程序图,如表4-3所示。
表4-3优化完成后的生产流程程序图
02
改进方法
2010年05月16日
38.5
4
20.6
69.8
274
6.1
7、焊接
8、裁管
9、搬运至气路装配区
12.7
10、气路连接
6.2
11、搬运至检验区
17
5.5
12、进行裁切固定检验、气路检验
13、搬运至总装区
14、调试检验
15、搬运至安全性能检测区
10.4
16、检验
6.0
17、搬运至包装区
32
8.1
18、装箱检验并发放合格证
19、装箱
20、搬运至原材料库和成品仓库
21、储存
4.2应用布置经路分析对车间布置和经路进行改进
4.2.1基于布置经路分析改进后的车间布置和经路
根据提出的改善方案,可以得到基于布置经路分析改进的车间布置图,如图4-1所示。
图4-1基于布置经路分析改进的车间布置图
基于布置经路分析改进后的车间布置将安全检测区和性能检测区合并,同时新增加了一个检验区,专门负责导线裁剪、焊接以及气路连接的检验,同时将合格证发放区的功能归并到包装区。
将优化完成后的生产流程程序图(表