工业硅的生产操作工艺Word文档格式.docx
《工业硅的生产操作工艺Word文档格式.docx》由会员分享,可在线阅读,更多相关《工业硅的生产操作工艺Word文档格式.docx(7页珍藏版)》请在冰豆网上搜索。
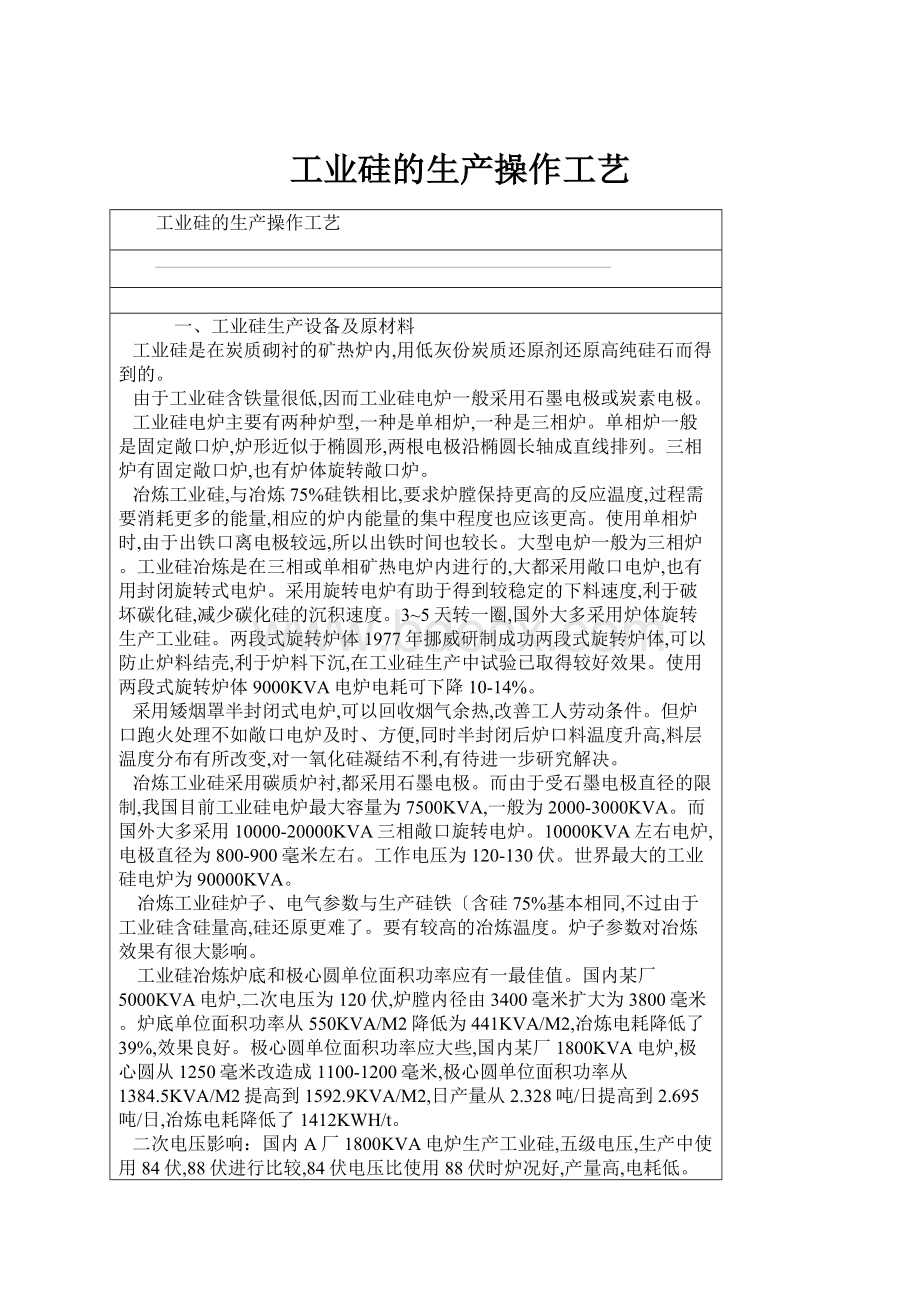
极心圆单位面积功率应大些,国内某厂1800KVA电炉,极心圆从1250毫米改造成1100-1200毫米,极心圆单位面积功率从1384.5KVA/M2提高到1592.9KVA/M2,日产量从2.328吨/日提高到2.695吨/日,冶炼电耗降低了1412KWH/t。
二次电压影响:
国内A厂1800KVA电炉生产工业硅,五级电压,生产中使用84伏,88伏进行比较,84伏电压比使用88伏时炉况好,产量高,电耗低。
冶炼工业硅时,炉料容易结壳,炉内容易积存SiC,炉况也比冶炼75%硅铁难控制。
大型工业硅电炉采用旋转炉体是必要的。
旋转炉体可使炉膛内能量分布比较均匀,增加炉料透气性,扩大坩埚区、防止或减少SiC结瘤,延长炉龄,提高硅的回收率和降低电耗。
为了改善熔炼指标,国外大型工业硅电炉也有采用六根电极的新式炉型的。
例如,美国建成投产的45000千伏安工业硅电炉,就是一个六电极的三相电炉。
工业硅电炉由于受石墨或炭素电极直径的限制,容量较小。
世界上工业硅电炉的最大容量是45000千伏安〔六电极。
我国现在普遍采用1800KVA以上电炉冶炼。
工业硅电炉比同容量的硅铁电炉,具有较高的二次电压和较小的电极圆心圆直径。
例如,容量9000千伏安的电炉冶炼75%硅铁时,采用140伏的二次电压,而容量6300千伏安的电炉冶炼工业硅时,则需采用155伏的二次电压。
冶炼工业硅的原料主要有硅石、石油焦、木炭〔或木块和烟煤。
由于对工业硅中Al、Ca、Fe含量限制严格,因而,必须采用杂质含量比冶炼硅铁更低的硅石。
一般要求硅石中SiO2>
98.5%、Al2O3<
0.8%、Fe2O3<
0.1%、CaO<
0.2%、MgO<
0.15%;
粒度为25-80毫米。
根据同样的原因,也必须采用低灰份的石油焦或沥青XX还原剂。
但是由于这种焦炭比电阻小,反应能力差,因而必须配用灰份低比电阻大和反应能力强的木炭〔或木块代替部分石油焦。
此外,为使炉料烧结,还应配入部分低灰份烟煤。
例如,某厂把这三者之间的比例控制为5:
3:
2。
必须指出,过多或全部配用木炭,不但会提高产品成本,而且还会使料面烧结性变差,引起刺火塌料,难以形成高温反应区〔坩埚;
炉底易形成SiC层、以及出铁困难等。
对各种炭质还原剂的要求如表所示。
炭质还原剂成份粒度要求
名称挥发份<
%>
灰分<
固定炭<
粒度<
毫米>
木炭25~30<
265~753~100
木块<
3<
150
石油焦12~16<
0.882~860~13
烟煤<
30<
80~13
此外,炭质还原剂含水量要低且稳定,不能含有其他杂物。
冶炼工业硅时,用木块代替木炭,效果也很好。
二、熔炼操作
冶炼工业硅与冶炼硅铁相比较,需要更高的炉温。
此外,由于炉料中不配加钢屑,所以SiO2还原反应的热力学条件恶化,破坏SiC的条件也变得更加不利。
由此产生三个结果:
一是炉料更易烧结;
二是上层炉料中生成的片状SiC,积存后容易促使炉底上涨;
三是Si和SiO高温挥发的现象更加显著。
为此,在冶炼过程中必须做到:
1、减少热损失,控制高炉温
2、减少Si和SiO的挥发
在工业硅生产中采用烧结性能良好的石油焦,有利于炉内热量集中,但料面难以自动下沉。
因此,而采用一定时间的焖烧和定期集中加料的操作方法。
为了提高炉温,减少Si、SiO的挥发损失,必须千方百计地减少热损失,扩大"
坩埚"
。
及炉况等因素确定。
其中应该特别注意还原剂的使用比例和使用数量。
正确的配比应使炉面既松软又不塌料,透气性良好,能保证规定的焖烧时间。
炉料配比确定后,炉料应进行准确的称量〔称量误差不超过+1公斤和细致的拌料,然后入炉。
炉料配比不准或炉料拌和不匀,都会在炉内造成还原剂过多或缺少现象,影响电极下插,缩小"
破坏正常冶炼进程。
正常情况下炉料难以自动下沉,一般需强制沉料。
当炉内炉料焖烧到规定时间时,料面料壳下面的炉料基本化清烧空;
料面也开始发白发亮,火焰短而黄,局部地区出现刺火塌料。
此时应该立刻进行强制沉料操作。
沉料时,先用捣炉机从锥体外缘开始将料壳向下压,使料层下沉。
而后用捣炉机捣松锥体下部,捣松的热料就地推在下沉的料壳上,捣出的大块粘料和死料推向炉心,同时铲净电极上的粘料。
沉料时高温区外露,热损失很大,因而捣炉沉料操作必须快速进行。
捣炉沉料操作完毕后,应将混匀的炉料迅速集中加于电极周围及炉心地区,使炉料在炉内形成一平顶锥体,并保持一定的料面高度。
不准偏加料。
一次加入新料的数量相当于一小时的用料量,新料加完后,焖烧一小时左右。
焖烧的定时沉料的操作方法,有利于减少热损失、提高炉温和扩大"
集中加料时,大量生料加入炉内,使温度略有下降。
因而,在加料前期,炉温较低,反应进行得较缓慢,气体生成量不会太多。
在焖烧一段时间后,炉温迅速上升,反应趋于激烈,气体生成量也将急剧增加。
此时为了帮助炉气均匀外逸,有必要在锥体下部"
扎眼"
透气。
石油焦具有良好的烧结性能,集中加料焖烧一段时间后,容易在料面形成一层硬壳,炉内也容易出现块料。
为了改善炉料的透气性,调节炉内电流分布,扩大"
除了"
透气外,还应用捣炉机或铁棒松动锥体下部和炉内烧结严重的部位。
至于透彻的捣炉,则在沉料时进行。
炉内积存有一定量铁水后,应及时打开炉眼出铁。
出铁时热损失大,故出铁次数不宜过多。
6000千伏安左右的电炉,每二小时开一次炉,2000千伏安左右的电炉,每四小时开一次炉。
炉眼用石墨棒烧开〔直径为100mm或200mm。
在正常情况下,出铁过程为15分钟。
出铁完毕后,先用块状工业硅及夹渣铁填入出铁口空洞,而后用碎工业硅堆成斜坡将炉眼封住。
工业硅的渣铁比重相差不大。
为防止铁水夹渣影响质量和造成浪费,在铁锭铁水冲击处,应放一由石墨棒堆成的挡渣框,框内夹铁渣用于堵眼。
含钙量要求严格的工业硅,可以在熔体中吹入一定数量的氯气以除钙。
电炉生产工业硅,炉况容易波动,较难控制。
因此,必须正确判断炉况,并及时处理。
和生产75%硅铁一样,影响炉况的因素是很多的。
但是,在实际生产中,影响炉况最主要的因素还是还原剂的用量。
还原剂用量不当,会使炉况发生急剧变化。
一般来说,炉况变化通常反映在电极插入深度,电流稳定程度,炉子表面冒火情况,出铁情况及产品质量波动情况等几方面。
炉况正常的标志是:
电极深而稳地插入炉料,电流电压稳定,炉内电弧声响稳而低,料面冒火区域广而且均匀,炉料透气性好,料面松软而有一定的烧结性,各处炉料烧空程度相差不大,焖烧时间稳定,基本上无"
刺火"
塌料现象。
出铁时,炉眼好开,流头开始时较大,而后均匀地变小,产品产量质量稳定。
原料含水量波动,还原剂质量变化,称量准确程度较差,操作不当等各种因素,均会影响实际用炭量,使炉子出现还原剂过剩或还原剂不足现象。
炉子还原剂过剩的征状是:
料层松软,火焰变长,火头大多集中于电极周围;
电极周围下料,炉料不烧结,"
塌料严重;
电极消耗慢;
炉内显著生成SiC,锥体边缘发硬;
电流上涨,电极上抬。
当还原剂过剩严重时,仅在电极周围窄小区域内频繁"
塌料,其他地区的料层发硬不下料,"
大大缩小,热量高度集中于电极周围,电极高抬,热损失严重电弧声很响,炉底温度严重下降,假炉底很快上涨,铁水温度低,炉眼缩小,有时甚至烧不开炉眼,被迫停炉。
为消除还原剂过剩现象,及时扭转炉况,还原剂过剩不严重时,要在料批中减少一部分还原剂,同时配之以积极的炉况维护,即可使炉子恢复正常。
还原剂过剩严重时,应估计炉内还原剂过剩的程度,而后采取集中附加硅石或在炉料中附加硅石的方法处理。
作为临时措施,硅石附加量必须严格掌握,以防形成大量炉渣。
集中附加硅石,可在较短时间内破坏SiC和增大炉料电阻,促使电极稳定下插,逐渐扩大"
逐步扭转炉况。
炉子还原剂不足的征状是:
料面烧结严重透气性差,吃料慢,火焰短小而无力,"
严重。
缺炭前期,电极插入深度有所增加,炉内温度有所提高,铁水量反而增多,打开炉眼时,炉眼冒白火。
铁水有过热现象。
缺炭严重时,炉面发红变硬化,电流波动,电极难插,"
成亮白色火后,"
呼呼"
有声,难以消除,电极消耗显著增加,炉眼发粘难开,铁水量显著下降。
为消除还原剂不足现象,一般应追加还原剂。
还原剂不足不严重时,为迅速改善料层透气性,可在料批中附加一部分木炭。
还原剂不足严重时,除在料批中附加部分木炭外,在沉料或捣炉时应附加适量不易烧损的石油焦,以有效地消除还原剂不足现象。
此外,为保持炉况稳定,减少热停炉是必要的。
三、冶炼工艺
1、配料
料批以200公斤硅石为基础,还原剂数量根据原料化学成分、经验数据经计算而定。
各种还原剂按一定比例搭配,木炭用量控制在不少于纯碳量的四分之一。
灰份不小于4%,挥发份高,反应活性好,比电阻高的烟煤和褐煤,要适当配入。
其用量不得超过四分之一。
配料时要注意原料变化及时调正配料。
要注意原料的清洁,清除异物,防止杂质混入料内。
称量必须准确,每批误差不得超过+0.5公斤。
2、烘炉
〔1烘炉前的准备工作。
1检查供电、炉子绝缘、液压、铜瓦、把持器、卷扬机等各系统,并进行空载运行。
运转正常后才能开始烘炉。
2在电极下部放置三支长度适当〔2700kVA炉子其长度400毫米左右直径为100毫米的电极石墨电极棒,在铺垫一层厚度为150~200毫粒度为40~80毫米的焦炭,在炉子极心圆内再撒一层5~20毫米厚的焦末便于起弧,并保护炉底。
〔2烘炉操作。
烘炉方法较多,可先用木柴烘,再加焦炭用电烘,也可直接用电烘。
1采用电烘炉的电压较常用电压低1~2级。
工作电流从小逐渐增大。
并间隙停电进行均热,同时,扒动焦炭并补充焦炭。
电烘时间为36~48小时,用电量为3~5万kWh。
2电烘炉时,同时用木柴和焦炭烘出铁口流槽。
到出铁前要烘好锭模。
3烘炉结束后,将炉内残渣杂物和炉墙保护砖挖出去。
4清理炉内杂物后,拔掉炉眼烟囱管,并将堵眼泥球堵好出铁口。
3、开炉,炉衬烘好后,设备已经检查试运转正常,一切准备工作完成后,即可开炉。
用料制度:
先配几批料,或减少硅石用量逐渐达到正常批料。
用烘炉电压开炉,一直到电炉情况正常为止。
引弧后向炉底三支电极周围投入木块和石油焦,数量视炉自容量而定,一般5000kVA以下的炉子可投入800公斤左右的木块,100公斤左右的石油焦。
严格控制料面上的上升速度,加料速度要和输入电量要一致。
引弧后第一次加料要多投要轻,这样可以盖住电弧。
以后加料要根据耗电量控制加料量,开炉操作尽量少动电极,加料要轻,以免炉料塌入电极下,使电极上抬。
造成炉底上涨。
新炉料面一定要维护好,一切操作都要轻,尽量减少下料量又不要跑火塌料,使炉内多蓄热,给形成正常炉况打下基础。
炉口料面要平稳上升。
第一、二炉更要注意,不许捣炉,使坩埚尽快更好的形成。
对2700kVA电炉加料后12~20小时出第一炉产品,电耗3.5万千瓦时左右。
第二炉6-10小时出产品。
第三炉恢复正常出产品时间。
4、加料按配料要求配好料、运到炉前木块单独堆放。
称料次序:
木炭、石油焦、硅石。
搅拌均匀后加到炉内。
操作上要采用出铁或沉料后集中加料的方法,其余少量地采用勤加薄盖的方法,在调火焰时加入。
沉料时三支电极同时进行,根据闷烧情况,一般50~80分钟基本化空后,在刺火前集中沉料,沉料时可用沾水铁制工具快速进行,严禁工具熔化,影响产品质量。
大沉料后先在紧靠电极周围处加木块,并且要立即用热料盖住木块,在盖新料。
加料要匀,不允许偏加料。
料面要加成平顶锥体,锥体高200-300毫米,炉心处略低于料面100-150毫米,加料后根据炉口火焰情况,加料调正火焰,保持均匀逸出,这样可以延长焖烧时间、扩大坩埚。
不要等火焰过长甚至刺火才盖料。
要根据炉内还原下料情况加料,使供给负荷、还原速度、加料速度相适应,以控制正确的加料量,保持正常料面高度并控制炉温。
加料速度超过熔化、还原速度,料面会抬高,炉温下降,加料不足或电极度上抬、硬性控制料面,炉口温度就会升高,此时热损失大,造成硅的挥发损失过大。
5、沉料、捣炉、透气
经过集中加料,小批调整火焰加料,保持炉气均匀逸出,一段时间后电极及周围炉料被熔化、还原出现较大空腔,此时,料层变薄,在大塌料前应该进行沉料。
沉料就是主动集中下料。
一般负荷正常、配比正确、下料量均衡,炉子需要到集中下料的时间是基本一定的。
对2500KVA电炉,约加400公斤硅石的混合料批,约一小时左右沉一次料。
如果超出正常沉料时间,应分析原因及时调整,有时是负荷不足,上次下料过多,还原剂不足,炉料还原不好等。
如下料过多,要适当延长时间进行提温,如果还原剂不足应进行强迫沉料,同时撒入炉内少量还原剂。
要学会掌握沉料时间,根据炉况和声音判断确定沉料时间。
每班沉料约5-6次。
炉况正常时可做到全炉集中沉料加料。
使三相坩埚还原均匀,电极插的深,若因加料不均匀,透气性不好,还原剂量不当造成局部严重刺火时,可采取局部沉料加料的方法处理。
沉料时,捣松就地下沉,尽量不要翻动炉料层结构顺序,若遇大块粘料影响炉料下沉和透气时,应碎成小块或将其推向炉中心。
每次出炉后应用捣炉机或人工进行捣炉,捣炉可以疏松料层,增加炉料透气性,扩大反应区,从而延长焖烧时间,刺火少,使一氧化硅挥发量减少,提高硅的回收率。
捣炉时操作要快,下钎子方向角度要掌握好,不要正对准电极。
当炉况正常时,沿每相电极外侧切线方向及三个大面深深的插入料层。
要迅速挑松坩埚壁上烧结的料层,捣碎大块就地下沉。
不允许把烧结大块拨到炉外〔遇有特大硬壳除外,然后把电极周围热料拨到电极根部,加木块〔或木屑后盖住新料。
每炉冶炼时间一般四小时,正常炉口维护操作如下〔以2500KVA电炉为例。
出炉后彻底捣炉,先加部分木块,盖热料,再集中加盖新料,将木块盖信,进行焖烧提温。
同时对炉口火焰较大处盖新料。
约20分钟后对冒火为好处轻轻透气,调整炉口火焰,使整个炉口火焰都很活跃。
焖烧50-80分钟后,待料面变成较薄的烧结层,估计炉内已还原较空时,再沉料一次。
沉料后加木块,盖热料再盖新料。
距出铁40-50分钟时再根据炉况沉料到次,拨新料至电极周围,再盖些不带木块的新料。
透气操作一般要在加料后20分钟左右进行,用沾水的圆钢〔30MM左右向冒火弱处插入,直到冒出白色火焰,再向外抽出并向上挑松炉料。
6、出炉、浇注及取样精整出铁前先将流槽清理干净,在铸模底部垫上一块炭砖,锭模内刷石灰或石墨粉浆,上面放些碎合金块,以保护锭模。
出铁时间,应根据炉子容量、生产条件、管理水平等确定最佳时间。
每班出铁次数多,热损失就大,出铁次数少,又影响冶炼效果,影响产量。
对6000KVA电炉,每二小时出铁一次;
2000KVA电炉,每3-4小时出铁一次。
用石墨棒的烧空器进行开眼,铁水直接流到锭模中。
待大流结束后用木棍通眼,炉眼内粘有渣时〔一般工业硅有2.5%的炉渣可用烧穿器将熔渣昼熔化,使坩埚底部铁水边烧边流出。
要修理炉眼适当扩大空洞体积,使冶炼过程稳定。
在正常情况下,出铁过程只需要15分钟左右。
出铁结束后,把炉眼四周及炉内残渣扒净,再堵炉眼。
堵眼时,先用合格块状工业硅堵内眼,最后用泥球堵眼。
堵眼时尽量往里堵,保持50-100毫米深。
堵眼泥配比为耐火泥:
石墨粉、碎电极糊、石灰浆为1:
1:
0.5:
0.5,混拌均匀捏成球不散为好。
浇注:
铁水连续浇注到一个平的带衬板的锭模上,然后破碎去渣。
取样和精整:
产品分析检验规则、包装贮运按国家标准进行。
在锭模上取分析试样。
取样方法按合金上、中、下平面对角取样法进行,试样不得代夹渣。
成品须精整后装桶入库。
出格品不能回炉冶炼,更不能垫锭模,以免再度报废。
停炉操作:
停炉前应出尽铁水,料批中适当增加木块配入量。
若停炉超过八小时,应在停炉前适当降低料面;
为保持炉子温度,停炉前先捣松料面加入木块,加入量视停炉时间长短而定,一般加50-100公斤。
停炉时间长,还可以加一定数量的木炭或石油焦保温;
这防止炉料将电极粘住,停电后上提电极,然后向电极四周的空隙内加入木块,再下插以原来位置。
停电时,要活动电极,以免炉料粘住电极,开炉时不能送电。
第五节生产工业硅存在的问题及能量平衡
目前工业硅生产中的2个问题:
1炉底上涨:
生产中生成炭化硅容易,破坏难;
由于冶炼操作使生料入坩埚,加快了碳化硅的生成和生料的沉积。
要控制炉底上涨速度,应精选炉料、选择和摸索合适的炉子参数,合理的工艺操作创造和扩大坩埚,取得最佳作业状态,减少炉底上涨速度,延长冶炼周期。
2能量平衡:
能量收入:
俄罗斯中国〔6300KVA炉
电能8295.98
碳燃烧74.02
炉料物理热1
合金与渣化合热
其他10
能量支出:
氧化物还原69-72%52.57
废渣代走热损4-9%6.32
金属带走热4-6%5.98
渣带走热0.2-0.3%0.17
炉体热损失2-4%3.69
炉口热损9-12%6.18
冷却水代走热损失1-5%16.64
与电耗有关热损失10%8.45