热处理工艺及设备讲义Word格式文档下载.docx
《热处理工艺及设备讲义Word格式文档下载.docx》由会员分享,可在线阅读,更多相关《热处理工艺及设备讲义Word格式文档下载.docx(57页珍藏版)》请在冰豆网上搜索。
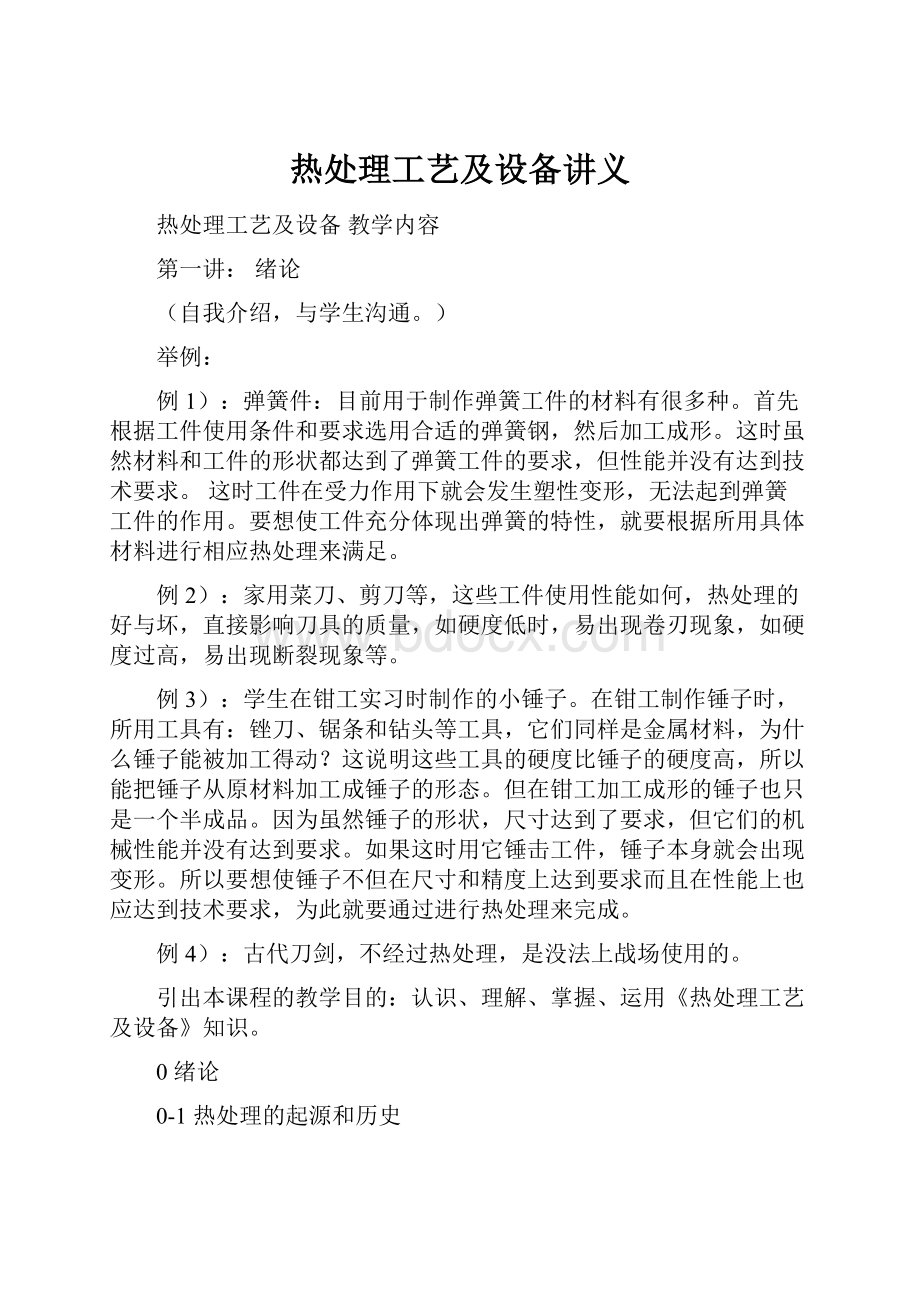
钢在常温下其内部有珠光体、铁素体、马氏体、上、下贝氏体等组织。
随着温度的升高,当达到727℃或超过727℃时,就发生了组织转变。
常温的组织开始转变为高温的组织,也就是向奥氏体转变。
2)保温的目的
使工件烧透且组织转变有充足的时间
(工件有尺寸、形状,加热有快慢,工件芯部与外表温度要求一致)
3)冷却的目的
将金属材料的高温组织以不同的冷却速度冷却到室温,获得不同的室温组织,从而达到不同的机械性能。
2、工艺特点:
热处理工艺是机械制造过程中一个重要的组成环节,与其它工艺相比,有其工艺特点:
1)热处理工艺不改变工件的外部形态,只改变内部组织形态,提高其内在质量,赋予各种使用性能;
2)热处理工艺不能独立存在,可在机械制造过程中任何一个位置存在,与前后工序起相辅相成的作用;
机加工之前的高温退火、铝合金成品前的固溶处理等)
3)操作温度和过程时间范围广;
(温度可高达工件的熔点,也可低至零下几十度,而时间短则几秒长则上百小时)
4)工艺控制精确;
(温度、时间的控制,冷去速度、方法的要求,热处理时工件的摆放及移动速度等)
5)加热、冷却介质的多样性和严格性;
6)加热冷却的均匀性和区分性。
0-3热处理的分类
1、按机械加工过程中的位置和作用分:
(1)最终热处理;
(为获得零件最后使用状态所需性能的热处理)
(2)预先热处理;
(常在最终热处理之前进行,为其他工艺做好组织性能准备)
(3)补充热处理。
(常在最终热处理之后进行,为了消除应力或稳定加工效果)
2、按零件热处理部位不同分:
(1)整体热处理;
(2)局部热处理;
(3)表面热处理;
(4)区分热处理。
3、按零件化学成分是否要求变化分:
(1)普通热处理;
(2)化学热处理。
4、按热处理温度分:
(1)高温热处理;
(2)中温热处理;
(3)低温热处理;
(4)冷处理。
5、按工艺特点、组织转变及形状性能变化分:
(1)基本热处理----退火、正火、淬火、回火、冷处理、时效等;
(2)化学热处理----渗碳、渗氮、渗硼、渗金属、多元渗等;
(3)表面淬火----火焰淬火、感应淬火、渗液淬火、电接触淬火、激光淬火等;
(4)形变热处理----高温形变热处理、中温形变热处理、低温形变热处理;
(5)复合热处理----渗碳淬火、表面淬火自行回火、锻热淬火、焊接余热退火等。
0-4国内热处理工艺现状及发展趋势
1、现状:
与发达国家相比,工艺水平低、质量差、耗能大、成本高、产品缺乏竞争力;
工艺研究和设备开发方面远远落后于发到国家,高端精密的热处理工艺设备绝大部分从国外进口。
2、发展趋势:
(1)节能减排,降低能耗,加强热处理工艺过程的控制与管理,积极采用复合热处理等新热处理工艺;
(2)推广无氧化、防脱碳、防热裂的热处理工艺;
(3)改造和引进自动化热处理生产线;
(4)减少污染、采用清洁能源、采用高效热处理工艺。
第二讲:
金属的加热及钢在加热时的转变
提问学生:
1)热处理的定义?
热处理的工艺过程?
(画右图示意)
2)热处理按工艺、特点和形状性能角度如何分类?
1金属的加热及钢在加热时的转变
1-1热处理的加热过程
1、加热物理过程:
热的传递方式:
传导——温度不同的接触物体间或同一物体中各部分之间的热能传递过程;
(举例:
烤红薯、用暖水袋暖手等等)
对流——流体流动时,流体质点运动引起的热能传递过程;
(比如:
暖气管、空调、吹风扇等等)
辐射——物体间通过热辐射在空间中传递热能的过程。
微波炉、太阳光等等)
2、加热影响因素:
1)加热介质(画出书中的表1-1,加以说明)
一般来说,传导比对流的加热速度要快一倍以上(举个例子:
烧水)
2)钢件(或合金)成分(画出书中的表1-2,加以说明)
钢的化学成分不同决定了其比热、密度和导热系数有差异,则影响着加热速度;
一般来说,加热速度与导热系数成正比、与比热、密度成反比,即:
v∝λ/cρ。
(举例,铝锅、铜壶。
合金元素越多,则导热系数越小、密度越大,不宜快速加热)
3)钢件(或合金)形状
有效受热表面积与体积之比,F/V,其越大,则加热速度越大。
3、加热规范的一般原则:
与零件有关,也与加热设备、加热方式、装炉量及工艺要求有关
1)加热温度确定(画图1-2加热温度优选示意图)
过烧——金属或合金在热处理加热时,由于加热温度接近其固相线附近,晶界氧化和开始部分熔化的现象。
过热——金属或合金在加热时,加热温度超过相变所需温度,使组织和性能异常的现象。
氧化——
脱碳——
2)加热速度选择
采用小的(慢速)加热速度:
脆性大的工件、导热性差的工件、大尺寸工件、复杂形状的工件、残余应力大的工件、固体渗碳和退火工艺、具有严重偏析和夹渣物的工件。
没有以上因素的工件,从生产效率、节约资源考虑,都应采用大的加热速率。
3)加热方法选择(画出书中图1-3示意)
(1)冷炉装料:
需要加热速度小的工件、装炉量较多的情况;
(2)到温装炉:
加热速度大、操作方便,截面温差大,退火、正火、淬火等普遍采用的加热方法;
(3)高温装炉:
炉温比加热温度高100~150℃、加热速度大、热应力大、操作不方便,锻件退火或正火,碳钢或低合金钢锻件的淬火。
(4)低温装炉:
低于600℃、加热速度中等、温差较小,热处理温度较低的工件,大型铸锻件,淬火不合格返修件,经过预热要进行高温热处理的、为了减少高温氧化和脱碳的工件。
4)加热时间确定
理论计算法:
一般来说,加热时间包括:
工件升温时间、均热时间、保温时间;
但理论计算时,加热时间仅指升温时间。
(1)表面热流密度恒定时:
(传给工件的热量与工件吸收而升温的热量相等)
(2)炉温恒定时:
(dτ时间内传递给工件表面的热量)
经验计算法:
τ=a×
d
常用有效厚度计算方法(画图1-4表示)
1-2热处理的加热介质:
1、固体介质:
木炭、烟煤、石墨、刚玉砂、石英砂、碳化硅等,主要应用于固体渗碳、渗金属等固体化学热处理及无氧化加热。
2、液体介质:
熔盐、熔碱、熔融金属、各种油类等,主要应用于加热质量要求高的高碳高合金钢的小零件、工模具的加热及某些液体化学热处理,也可用于等温淬火冷却。
熔盐——温度140~1300℃,价格低、易于清除,使用广泛;
熔融金属——有毒、易污染、不易清理,几乎不用;
油浴——200℃以下,主要用于回火加热。
3、气体介质:
1)一般炉气:
CO、CO2、H2、O2、N2、CH4等,具有较大氧化性,普通工件加热。
2)放热型(DX型)气体:
液化石油气、天然气、城市煤气等,与空气混合燃烧发生反应后制得,常用于保护性气体,光亮退火、光亮淬火、光亮热处理。
3)吸热型(RX型)气体:
丙烷、丁烷、甲烷等,与少量空气混合后,在高温反应罐中,经触媒作用反应制得,常用于钢件防止氧化脱碳,如气体渗碳等。
4)氨分解气体:
常用于不锈钢、硅钢片、低碳高合金钢的光亮热处理。
5)氮基气体、氢气及木炭发生气
6)真空气体
1-3钢在加热过程中的转变
1、奥氏体的形成过程:
形核和长大两个基本过程,可分为四个阶段(画图书中9-2示意)
1)奥氏体的形核:
Ac1温度以上,珠光体不稳定,在F和Fe3C的界面上优先出现奥氏体的晶核;
(这是因为相界面上碳浓度分布不均、原子排列不规则、能量较高状态)
2)奥氏体晶核长大:
稳定了的奥氏体晶核开始逐渐长大,依靠Fe、C原子的扩散,晶格改组为面心立方晶格;
3)残余渗碳体的溶解:
铁素体优先溶解消失于奥氏体中,残余的渗碳体需要时间来溶解消失;
4)奥氏体均匀化:
浓度不均,则需要长时间的C原子继续扩散均匀,同时伴有奥氏体的合并现象。
2、奥氏体的晶粒长大及控制
1)奥氏体晶粒度:
衡量奥氏体晶粒大小的尺度,对冷却后钢的组织和性能有着重要影响。
表示方法有:
经理尺寸表示法(晶粒截面的平均直径或单位面积内的晶粒数目);
晶粒度级别指数G表示法——分8级,1最粗、8最细,一般5以上为细晶粒。
2)奥氏体晶粒长大:
起始晶粒度、实际晶粒度
3)晶粒度大小的控制:
(1)加热温度和保温时间的控制;
(2)加热速度的控制;
(快速加热,短时间保温细化晶粒)
(3)钢的化学成分;
(可抑制晶粒长大的元素:
Al、V、Ti、Zr、Nb、W、Cr、Mo等)
(4)钢的原始组织;
(越细的组织越有利于晶粒长大)
第三讲:
钢在冷却时的转变
提问复习:
(1)加热时间的确定?
加热温度的确定?
加热速度的确定?
(2)钢在加热过程中发生了哪些转变?
1-4钢在冷却时的转变
1-4-1冷却条件对钢性能的影响(画书上表9-1)
连续冷却:
将奥氏体化后的钢件以一定的冷却速度从高温一直连续冷到室温。
等温冷却:
把奥氏体化后的钢件迅速冷到临界点以下某个温度,等温保持一定时间后再冷至室温。
1-4-2过冷奥氏体等温转变曲线(C曲线)
1、过冷奥氏体:
临界点以下暂时存在的奥氏体,是介稳定相。
TTT曲线(Time-Temperature-Transition):
反映过冷奥氏体等温转变动力学的实验曲线,C曲线。
(残余奥氏体:
未发生转变的过冷奥氏体)
2、共析碳钢C曲线分析(画出书上图9-4C曲线图)
(1)C曲线中,A1温度线是奥氏体向珠光体转变的
临界温度;
左边和右边的C曲线分别为过冷奥氏体
转变开始线、终了线。
(2)共分几个区域:
高于A1的奥氏体稳定区、转变
开始线以左的过冷奥氏体区、转变终了线以右和Ms点
以下为转变产物区、转变开始线与终了线之间为过冷
奥氏体和转变产物的共存区。
(3)过冷奥氏体在不同温度等温转变时,都要经过一段孕育期,即为纵坐标到转变开始线之间的距离。
550℃为鼻温,孕育期最短、转变时间最短。
(4)发生三种转变:
高温的珠光体转变、中温的贝氏体转变、低温的马氏体转变。
1-4-3影响因素
1、奥氏体成分的影响:
碳浓度、合金元素
2、奥氏体化状态的影响:
晶粒度、均匀化、晶体缺陷密度等
3、应力和塑性变形的影响:
1-4-4过冷奥氏体连续冷却转变曲线
1、CCT曲线(continuous-cooling-transition)(画图书上9-8)
CCT曲线的临界冷却速度(Vc)、TTT曲线的临界冷却速度(Vk)、上下临界冷却速度
(这里,提问学生:
a、要获得全部马氏体,冷却曲线如何画?
全部为珠光体呢?
1-5珠光体转变
1-5-1定义:
在高温时发生的扩散性相变,生成铁素体与渗碳体的机械混合物(写出反应式)
典型的扩散型转变,退火、正火和索氏体化处理时,发生的主要相变为珠光体转变。
1-5-2组织形态、结构和性能
1、片状珠光体:
由具有一定厚度的片状铁素体与片状渗碳体交替排列堆叠而成;
分为片状珠光体、细片状珠光体(索氏体S)、极细片珠光体(屈氏体T)
2、球状珠光体:
在铁素体基体上分布着粒状渗碳体组织;
(球化退火)
3、性能:
片间距和粒度越小,则强度、硬度越高,塑性、韧性越好。
一般来说,退火后球状珠光体的性能比片状珠光体的性能好。
魏氏体组织会降低钢的力学性能,应该避免,或经过正火、退火、锻造来消除。
1-6马氏体转变
1-6-1定义:
在较低的温度下发生的无扩散性相变,生成碳在α-Fe中过饱和的间隙固溶体。
典型的无扩散相变、淬火处理时,发生的主要相变为马氏体转变。
1-6-2主要特点:
1、无扩散性相变、以共格切变的方式进行;
2、具有一定的位向关系和惯习面;
3、表面浮凸现象,说明是切变转变;
4、转变在一个温度范围内完成,必须冷却到Mf以下,才能转变完成,否则都会存在残余奥氏体;
5、高速长大,不需要孕育期。
1-6-3形态及其亚结构
1、板条马氏体:
一般为低碳钢、中碳钢、不锈钢的典型马氏体组织,扁条状和薄板状;
2、片状马氏体:
一般为高碳钢、中碳钢、高镍的铁镍合金的典型马氏体组织,双凸透镜或竹叶状;
3、亚结构:
孪晶
4、影响因素:
奥氏体的碳含量、马氏体形成温度。
1-6-4性能
1、高强度、高硬度:
固溶强化、相变强化、时效强化、细晶强化
2、塑性和韧性:
受碳含量及亚结构影响
马氏体的强度主要取决于碳含量,塑性和韧性主要取决于亚结构。
1-7贝氏体转变
1-7-1定义:
在中温条件下进行碳原子扩散和铁原子不扩散性转变,形成残余奥氏体与珠光体的混合物;
1-7-2形态
上贝氏体:
350-550℃转变,形成羽毛状的贝氏体;
下贝氏体:
350℃以下转变,形成针状的贝氏体;
粒状贝氏体:
贝氏体形成温度最上部。
1-7-3性能
性能主要受到形成温度、化学成分影响;
下贝氏体具有良好的综合力学性能,尤其韧性更加。
第四讲退火与正火
提问:
a、画出C曲线;
画出CCT曲线;
b、指出哪条是连续冷却曲线,哪条是等温冷却曲线?
并说明它们最终的相变产物。
c、什么是马氏体转变?
主要特点?
第二章退火与正火
退火与正火是生产中常用的预备热处理工艺。
一般为了消除铸、锻和焊件的内应力以及成分、组织的不均匀性,为下道工序做好组织准备。
2-1退火的定义及分类
一、退火:
把钢加热到适当温度,保温一定时间,然后缓慢冷却,以获得接近于平衡组织的热处理工艺。
温度:
高于Ac3、Ac1,或低于A1;
(画出书上图9-1,并与铁碳相图对比说明A1A3Acm等温度点)
冷却方式:
随炉冷却;
组织:
平衡组织,珠光体组织。
二、目的:
在于均匀化学成分、改善机械性能及工艺性能、消除或减少内应力并为零件最终热处理作好组织准备。
要消除的组织缺陷一般有:
魏氏体组织、带状组织、粗大晶粒等;
后续的工艺操作一般有:
切削加工、淬火等。
三、分类:
再结晶退火:
加热到再结晶温度(低于A1),靠生成新晶粒及晶粒长大以消除由冷变形所引起的晶格歪曲与性能变化的一种热处理工艺。
相变重结晶退火:
在相变温度以上发生结构、组织与性能变化的一种热处理工艺。
低温退火:
加热到相变温度以下,进行消除内应力,防止变形,降低硬度,恢复塑性和消除加工硬化,改善切削与冲压加工性等的热处理工艺,亦称之为软化退火或去应力退火。
2-2退火工艺(画图9-43)
1、完全退火:
为改善热锻、热轧、焊接或铸造过程由于温度过高在钢件内出现的不良组织,提高机械性能,或为使钢件软化,以改善加工性能与消除内应力,而采用的热处理工艺。
a、加热温度:
一般采用Ac3+(20~50℃)
b、加热速度:
不同钢种采用不同加热速度,一般的,碳钢选150~200℃/h,低合金钢选100℃/h,高合金钢选50℃/h。
对于大型工件及装炉量大的工况,因透热性差,宜在550~650℃停留一段时间,再继续升温。
c、保温时间:
为使工件透烧,保证内外组织转变完成和均匀化,一般的,碳钢选1.5~2min/mm,低合金钢2~2.5min/mm,高合金钢2.5~3min/mm。
装箱保护退火时,应根据箱子大小和箱内填充剂进行适当延长,一般需增加1~4h。
d、冷却速度:
控制冷却速度保证奥氏体向珠光体转变全部完成、又不获得高的弥散度。
碳钢选100~200℃/h,低合金钢选50~100℃/h,高合金钢选20~50℃/h。
e、冷却方式:
为了提高设备利用率,并使组织充分转变,由退火温度至550℃为炉冷,550℃以下取出空冷。
f、应用:
碳素结构钢和合金钢的锻件、轧件、铸件和焊接件,不宜用于过共析钢件。
2、不完全退火:
为消除碳素结构钢和低合金结构钢因热加工所产生的内应力,使钢件软化或改善工具钢被切削性而采用的热处理工艺。
由于加热温度在两相区进行,仅发生部分相变重结晶,铁素体或碳化物形态、分布仍保留。
Ac1~Ac3或Ac1~Ac3
同完全退火
碳素结构钢、碳素工具钢、低合金结构钢和低合金工具钢的热锻件和热轧件。
3、球化退火:
是不完全退火的一种特例,使钢中碳化物球化并均匀分布在铁素体基体上,获得粒状珠光体的退火工艺。
目的:
改善工具钢的可切削性;
为淬火作好金相组织准备。
a、球化退火工艺(画图2-2)
(1)主要用于淬火或冷加工后钢的球化;
(2)多次重复使钢中原晶界上的碳化物和珠光体中渗碳体经过溶解和重新析出、聚集而达到球化目的;
此方法适用于原始组织为珠光体的钢;
(3)主要使碳化物溶解,而后快速冷却,以防网状碳化物析出;
(4)过共析钢最常用的球化;
(5)使网状碳化物或大块碳化物完全溶解,以利其后球化;
(6)与(5)类似。
b、影响球化质量因素:
化学成分:
碳含量增加有利于球化,加入可形成碳化物的元素不利球化;
原始组织:
网状碳化物很难球化,马氏体、细小的珠光体或贝氏体有利于球化,冷变形后组织有利于球化;
加热温度与等温温度:
加热温度过高或过低、等温温度过高或过低,都不利于球化;
球化时间:
不宜过长,否则球化碳化物变粗,硬度下降;
冷却速度:
冷却速度会影响碳化物的弥散度,冷却速度小有利于球化,采用缓慢冷却进行球化退火是保证得到理想组织的重要因素。
c、应用:
广泛应用于工具钢、轴承钢和量具钢,作为预先热处理。
4、等温退火:
与完全退火相同,但可有效缩短生产周期
Ac3+(20~50℃)或Ac1+(20~50℃)
d、等温温度:
根据C曲线及硬度要求确定
e、冷却速度:
大件随炉冷却,小件空冷
f、冷却方式:
>
500℃随炉冷,<
500℃空冷
g、应用:
球化退火不少是采用等温退火缩短生产周期,用以消除Cr-Ni钢及Cr-Ni-Mn钢锻件中的白点。
5、扩散退火(均匀化退火):
为了消除和降低铸件凝固时所引起的成分偏析,达到成分、组织均匀化的热处理工艺。
特点:
高温长时间加热、能耗大、成本高,工件易过热和烧损
根据合金元素含量及偏析程度而定,一般采用1050~1200℃
低合金钢选100℃/h,高合金钢选20~50℃/h
2.5~3min/mm
低合金钢选50~100℃/h,高合金钢选20~50℃/h
优质合金钢铸件;
另外,经扩散退火的铸钢件晶粒粗大,韧性塑性差,需要一次完全退火或正火来重新细化组织,提高机械性能。
6、再结晶退火:
把冷变形后的金属加热到再结晶温度以上,保持适当时间,使变形晶粒重新转变为均匀的等轴晶粒,以消除加工硬化和残余应力的热处理工艺。
消除冷作硬化、提高塑性、改善切削及压延成型性能。
Tr+(150~250℃),Tr为再结晶温度,0.4×
熔化温度,大部分钢件取600~700℃
b、保温时间:
1~4h
c、冷却方式:
空冷
d、应用:
冷作加工(冷挤、冷拔、冷轧、冷弯等)件、成型加工件
7、软化或去应力退火:
为消除因变形加工及铸造、焊接过程中引起的残余内应力而进行的热处理工艺。
消除内应力、降低硬度、提高尺寸稳定性、防止工件开裂和变形
一般的,铸铁500~600℃,碳钢及低合金钢550~650℃,高合金钢600~700℃
100~150℃/h
2~6h
50~100℃/h
500℃为炉冷,<
500℃为空冷(适用于钢)
>
400℃为炉冷,<
400℃为空冷(适用于铸铁)
碳钢与合金钢的锻件、机加工件,铸铁件,焊接结构件。
第五讲:
退火与正火的应用及其选择
退火温度、冷却方式、组织?
退火的目的?
退火的分类?
45#钢的完全退火工艺?
2-3退火工艺控制组织的基本原则
(1)退火处理后珠光体的形状决定于退火加热温度;
(一般的,退火温度高,奥氏体成分越均匀,可获得片状珠光体,反之,退火温度低,组织成分不均匀,可获得粒状或球状珠光体)
(2)退火温度过低,且保温时间不足,原始组织中片状组织没有被破坏,则退火组织仍可能保留细片状珠光体;
(3)退火温度过低,且冷却速度过快,致使碳化物结晶核心细而多,退火组织可获得点状珠光体;
(4)冷却速度不影响珠光体的形状,但决定了碳化物的弥散度,因而决定了退火后的硬度;
(5)欲获较软组织,可将钢加热到临界点(Ac1)以上30℃处保温,然后冷却到Ac1以下30℃处保温;
(6)退火缓冷到500℃左右,就可以放置于空气中冷却,对组织转变已无影响;
(7)欲细化淬火的粗大过热组织,可通过提高退火时的奥氏体化温度(Ac3+60~100℃)或延长奥氏体化保温时间的办法或适当提高加热速度进行奥氏体化,使奥氏体晶粒发生再结晶,从而消除组织结构的遗传性。
2-4正火工艺
一、正火概念
将钢加热到Ac3或Acm以上适当温度,保温一定时间后在空气中冷却,从而得到珠光体型组织的热处理工艺。
加速合金碳化物的溶解和奥氏体均匀化,为了消除热加工所造成组织缺陷,消除网状碳化物,细化晶粒,为淬火作好准备,同时也可为不重要零件作为提高机械性能的最终热处理而采用正火处理。
二、工艺规范
亚共析钢Ac3+40~60℃,过共析钢Acm+40~60℃
1.5~2min/mm
空冷,对大件可用吹风、喷雾和调节工件