挤塑Word文件下载.docx
《挤塑Word文件下载.docx》由会员分享,可在线阅读,更多相关《挤塑Word文件下载.docx(10页珍藏版)》请在冰豆网上搜索。
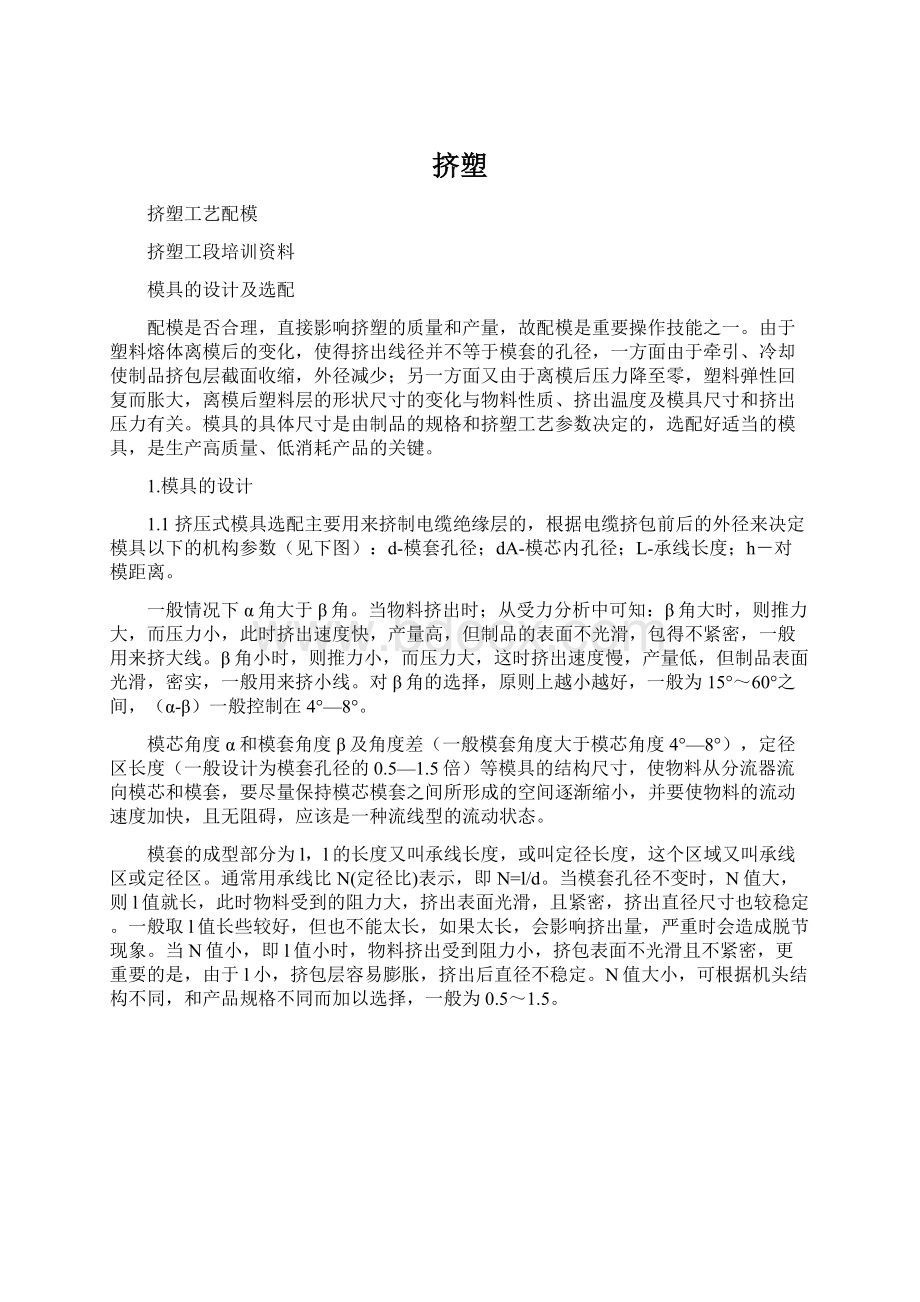
),定径区长度(一般设计为模套孔径的0.5—1.5倍)等模具的结构尺寸,使物料从分流器流向模芯和模套,要尽量保持模芯模套之间所形成的空间逐渐缩小,并要使物料的流动速度加快,且无阻碍,应该是一种流线型的流动状态。
模套的成型部分为l,l的长度又叫承线长度,或叫定径长度,这个区域又叫承线区或定径区。
通常用承线比N(定径比)表示,即N=l/d。
当模套孔径不变时,N值大,则l值就长,此时物料受到的阻力大,挤出表面光滑,且紧密,挤出直径尺寸也较稳定。
一般取l值长些较好,但也不能太长,如果太长,会影响挤出量,严重时会造成脱节现象。
当N值小,即l值小时,物料挤出受到阻力小,挤包表面不光滑且不紧密,更重要的是,由于l小,挤包层容易膨胀,挤出后直径不稳定。
N值大小,可根据机头结构不同,和产品规格不同而加以选择,一般为0.5~1.5。
对模间距h在挤压式模具中是一个非常重要的安装参数,用来调整机头内部压力,保证挤出外观的光滑型和同心性,一般根据不同的线径选取1~4mm。
模芯孔径尺寸要稍大于导体的外径,如果太小,在挤出过程中容易使导体表面划伤或拉断。
如果模芯孔径选择太大,挤出过程中容易产生偏芯,严重时会产生倒料现象。
一般模芯孔径比导体外径大0.3~0.7mm。
对于超大截面的导体,也可适当放大些。
模套孔径选取要稍大于标称挤出外径,通常大6~8%,这是因为塑料塑料在挤出后要收缩一些。
1.2挤管式模具主要用于电缆衬层和外护层的挤制,配模的依据主要是挤出塑料的拉伸比DDR和拉伸平衡比DRB。
拉伸比DDR的选取:
不同塑料一般不一样,如聚氯乙稀DDR=1.2~3.0、聚乙烯K=1.3~4.0。
选的过大或过小都会严重影响挤塑质量,过大可能导致脱胶,而过小挤制表面不光。
拉伸平衡比DRB的选取:
一般选在0.95~1.15之间,理想情况下为1。
它是衡量拉管式模具设计的一个最重要的指标,大于1为紧包,一般用来挤制厚壁型绝缘或护套,而过大可能导致熔体断裂,及脱胶。
小于1松包,一般用来挤制薄壁型绝缘或护套,而过小很容易产生竹节和偏心现象。
等于1时为平衡拉伸。
由以上两个方程可以此就可唯一的确定出模芯和模套的结构尺寸。
2.模具的选配方法
(1)测量半制品直径:
对绝缘线芯,圆形导电线芯要测量直径,扇形或瓦形导电线芯要测量宽度;
对护套缆芯,铠装电缆要测量缆芯的最大直径,对非铠装电缆要测量缆芯直径。
(2)检查修正模具:
检查模芯、模套内外表面是否光滑、圆整,尤其是出线处(承线)有无裂纹、缺口、划痕、碰伤、凹凸等现象。
特别是模套的定径区和挤管式模芯的管状长嘴要圆整光滑,发现粗糙时可以用细纱布圆周式摩擦,直到光滑为止。
(3)选配模具时,铠装电缆模具要大些,因为这里有钢带接头存在,模具太小,易造成模芯刮钢带,电缆会挤裂挤坏。
绝缘线芯选配的模具不易过大,要适可而止,即导电线芯穿过时,不要过松或过紧
(4)选配模具要以工艺规定的标称厚度为准,模芯选配要按线芯或缆芯的最大直径加放大值;
模套按模芯直径加塑料层标称厚度加放大值
3.配模的经验公式
上边介绍的是模具设计理论,在实际生产过程中,显然不实用,因此一般按照以下经验公式进行现场配模。
(1)模芯D1=d+e1
(2)模套D2=D1+2δ+2△+e2
式中:
D1――模芯出线口内径;
D2――模套出线口内径;
d――生产前半制品最大直径;
δ――模芯嘴壁厚;
△――工艺规定的产品塑料层厚度。
e1――生产外护套电缆用模芯的放大值,对于铠装电缆为2~6mm,非铠装为2~4mm,导体为1.5~3mm。
e2――生产外护套电缆用模套的放大值,一般选取1~3倍的绝缘厚度。
4.举例说明模具的选配
(1)生产绝缘线芯3×
185mm的实心铝导体扇形电缆,其扇形(标称)宽度为21.97mm(其最大宽度允许值22.07mm),绝缘层标称厚度为2.0mm。
(其最小厚度允许值为2.0×
90%-0.1=1.7mm,芯嘴壁厚为1.0mm,选用模具。
模芯D1=d+e1=21.97+1.5=23.47(mm)考虑到实体扇形及最大宽度,选取D=24mm。
模套孔径D2=D1+2δ+2△+e2=24+2×
1+2×
2+4=34(mm)
(2)生产电缆外护套,其型号为VLV,规格为1×
240mm,电压为0.6/1kV选用模具。
该电缆成缆后直径为23.6mm,护套标称厚度为2.0mm,取模芯嘴壁厚为1.5mm。
模芯孔径D1=d+e1=23.6+3=26.2≈27mm
模套孔径D2=D1+2δ+2△+e2=27+2×
1.5+2×
2+4=38mm
(3)在实际生产过程中,模具的选配往往在操作规程中给出一定的经验公式,
如φ65挤塑机给出的挤压式模具选配公式:
对于单根导体:
模芯孔径取导线直径+0.02~0.1;
模套孔径一般按照绝缘外径取。
对于绞合导体:
模芯孔径取导线直径+0.05~0.2;
当线芯或缆芯外径不均时,放大值取上限;
反之取下限。
5.选配模具的经验
1)16mm以下的绝缘线芯的配模,要用导线试验模芯,以导线通过模芯为宜。
不要过大,否则将产生倒胶现象。
2)抽真空挤塑时,选配模具要合适,不宜过大,若大,绝缘层或护套层容易产生耳朵、起棱、松套现象。
3)安装模具时要调整好模芯与模套间的距离,防止堵塞,造成设备事故。
三、模具的调整
1.模芯的安装:
模芯是安装在模芯支撑器上的,目前模芯与支撑器有两种结合方法。
一种是靠螺纹连接,即将模芯支撑器卡在台钳上,将选配好的模芯拧紧在支撑器上,然后再将模芯支撑器装在机头上
2.模具的调整:
调整模具的原则是,面对机头,先松后紧,拧紧螺钉的方向为左上、右下、左下、右上;
经常检查对模螺钉是否松动和损坏,如有损坏应立即更换;
注意拧螺钉时谨防碰着加热片电插头,以免触电或碰坏插头,为防触电,调整模具时,可先关掉模口段加热电源;
调模时,模套的压盖不要压的太紧,等调整好后再把压盖压紧,防止压盖进胶,造成塑料层偏芯或焦烧。
模具的调整方法如下:
(1)空对模:
生产前把模具调整好,用肉眼把模芯与模套间距离或间隙调整均匀,然后把对模螺钉拧紧。
(2)跑胶对模:
塑料塑化好后,调整对模螺钉,根据模口出胶圆周方向的多少,一面跑胶,一面调整,调整时应先松动薄处螺钉,再拧紧跑胶厚的螺钉;
同时取样检查塑料厚度是否偏芯,直到调均匀为止,然后把对模螺钉分别拧紧。
(3)走线对模:
适合小截面的电线电缆的调模。
把导线穿过模芯,与牵引线接好,然后跑胶,进行微调。
等胶跑好后,调整好螺杆和牵引速度,起车走线取样,然后停车,观察样品的塑料层厚度是否均匀,反复几次,直到调均匀为止,再把螺钉拧紧
(4)灯光对模:
适合聚乙烯塑料电线电缆。
利用灯光照射绝缘层和护套层,观察上、下、左、右四周厚度,调整对模螺钉,直到调均匀为止,然后把螺钉拧紧。
(5)感觉对模:
它是经验对模的方法。
利用手摸感觉塑料层厚度,调整模具。
适用于大截面电线电缆的外护层。
(6)其他对模方式
1)利用游标卡尺的深度尺测量塑料层厚度,调整模具。
2)利用对模螺钉的螺纹深度调整模具
3)利用取样测量塑料层厚度调整模具。
另外,模芯与模套间轴向模口相对距离的调整也很重要。
调整不当,会造成设备事故。
再有,模芯与模套孔径合理选配之后,还应注意模芯外锥与模套内锥角度差的选定,一般必须使模套的内锥角大于模芯的外锥角3~10°
,这个角差是及其重要的。
只有这样的角度差才能使塑料挤出压力逐渐增大,实现塑料层组织密实、塑料与线芯结合紧密的目的,但这个角度差不宜过大,否则使挤出压力增大而降低挤出量。
技术设备科:
xxxx
常见质量问题原因分析及预防措施
序号
问题
原因分析
处理办法及预防措施
1
焦烧
1、温度控制超高造成塑料焦烧。
2、螺杆长期使用而没有清洗,焦烧物积存,随塑料挤出。
3、加温时间太长,塑料积存物长期加温,使塑料老化变质而焦烧。
4、停车时间过长,没有清洗机头和螺杆,造成塑料分解焦烧。
5、多次换模或换色,造成塑料分解焦烧。
6、机头压盖没有压紧,塑料在里面老化分解。
7、控制温度的仪表失灵,造成超高温后焦烧。
1、经常的检查加温系统是否正常。
2、定期地清洗螺杆或机头,要彻底清洗干净。
3、按工艺规定要求加温,加温时间不宜过长,如果加温系统有问题要及时找有关人员解决。
4、换模或换色要及时、干净,防止杂色或存胶焦烧。
5、调整好模具后要把模套压盖压紧,防止进胶。
6、发现焦烧应立即清理机头和螺杆。
7、更换仪表
2
塑化不良
1、温度控制过低或控制的不合适。
2、塑料中有难塑化的树脂颗粒。
3、操作方法不当,螺杆和牵引速度太快,塑料没有完全达到塑化。
4、造粒时塑料混合不均匀或塑料本身存在质量问题。
1、按工艺规定控制好温度,发现温度低要适当的把温度调高。
2、要适当地降低螺杆和牵引的速度,使塑料加温和塑化的时间增长,以提高塑料塑化的效果。
3、利用螺杆冷却水,加强塑料的塑化和至密性。
4、选配模具时,模套适当小些,加强出胶口的压力。
3
疙瘩
1、由于温度控制较低,塑料还没有塑化好就从机头挤出来了。
2、塑料质量较差,有难塑化的树脂,这些没有完全塑化就被挤出。
3、加料时一些杂质被加入料斗内,造成杂质疙瘩。
4、温度控制超高,造成焦烧,从而产生焦烧疙瘩。
5、对模压盖没有压紧,进胶后老化变质,出现焦烧疙瘩。
1、塑料本身造成的疙瘩,应适当地提高温度。
2、加料时严格检查塑料是否有杂物,加料时不要把其它杂物加入料斗内,发现杂质要立即清理机头,把螺杆内的存胶跑净。
3、发现温度超高要立即适当降低温度,如果效果不见好,要立即清洗机头和螺杆,排除焦烧物。
4、出现树脂疙瘩和塑化不良的疙瘩,要适当调高温度或降低螺杆和牵引的速度。
5、压紧模压盖
4
塑料层
正负超差
1、芯或缆心不圆,还有蛇形,而外径变化太大。
2、半成品有质量问题,如:
钢带接头不好,钢带松套等。
3、操作时,模芯选配过大,造成倒胶而产生塑料层偏芯。
4、调整模具时,调模螺钉没有扭紧,产生倒扣现象而使塑料层偏芯。
5、螺杆或牵引速度不稳,造成超差。
6、加料口或过滤网部分堵塞,造成出胶量减少而出现负差。
1、经常测量电缆外径和检查塑料层厚度,发现外径变化或塑料层不均匀,应立即调整。
2、半成品修复后使用。
3、配模具要合适,调好模具后要把调模螺钉拧紧,把压盖压紧。
5、注意螺杆和牵引的电流和电压表,发现不稳,要及时找电工、钳工检修。
6、检查加料口或更换过滤网。
5
电缆外径粗细不均和竹节形
1、收放线或牵引的速度不均。
2、半成品外径变化较大,模具选配不合适。
3、螺杆速度不稳,主电机转速不均,皮带过松或打滑。
1、经常检查螺杆、牵引、收放线的速度是否均匀。
2、模具选配要合适,防止倒胶现象。
3、经常检查机械和电器的运转情况,发现问题要立即找钳工、电工修理。
6
合胶缝不好
1、控制温度较低,塑化不良。
2、机头长期使用,造成严重磨损。
3、机头温度控制失灵,造成低温,使塑料层合胶不好。
1、适当地提高控制温度,特别是机头的控制温度。
2、机头外侧采用保温装置进行保温。
3、更换温控仪。
7
气孔、气泡或气眼
1、局部控制温度超高。
2、塑料潮湿或有水分。
3、停车后塑料中的多余气体没有排除。
4、自然环境潮湿。
1、温度控制要合适,发现温度超高要立即调整,防止局部温度超高。
2、加料时要严格地检查塑料质量,特别是阴雨季节,发现潮湿有水,应立即停止使用,然后把潮料跑净。
3、在加料处增设预热装置,以驱除塑料中地潮气和水分。
4、经常取样检查塑料层是否有气孔、气眼和气泡。
8
脱节或断胶
1、导电线芯有水或有油
2、线芯太重与模芯局部接触,造成温度降低,使塑料局部冷却,由于塑料低拉伸而造成脱节或断胶。
3、半成品质量较差,如钢带和塑料带松套,接头不牢或过大。
1、模具选配要大些,特别是选配护套地模具,要放大6mm~8mm。
2、适当缩小模芯嘴的长度和厚度。
3、降低螺杆和牵引的速度。
4、适当调高机头的控制温度。
9
坑和眼
1、紧压导电线芯绞合不紧密,有空隙。
2、线芯有水、有油、有脏物。
3、温度控制较低。
1、绞合导体的紧压要符合工艺规定。
2、半成品不符合质量要求,应处理好后再生产。
3、适当调整温度
10
塑料层起包、棱角、耳朵、皱褶及凹凸
1、塑料包带和钢带绕包所造成的质量问题。
2、模具选配过大,抽真空后造成的。
3、模芯损坏后产生塑料倒胶。
1、检查半成品品质量,不合格品不生产。
2、模具选配要合适。
适当降低牵引的速度,是塑料层完全冷却。
3、装配前要检查模具,发现问题要处理后再使用。
11
塑料表面出现痕迹
1、模套承线径表面不光滑或有缺口。
2、温度控制过高,塑料本身的硬脂酸钡分解,堆积在模套口处造成痕迹。
选配模具时要检查模套承线径的表面是否光滑,如有缺陷应处理。
把机头加温区的温度适当降低,产生硬脂酸钡后要立即清除。