最新质量检验员基础知识培训计划Word格式.docx
《最新质量检验员基础知识培训计划Word格式.docx》由会员分享,可在线阅读,更多相关《最新质量检验员基础知识培训计划Word格式.docx(12页珍藏版)》请在冰豆网上搜索。
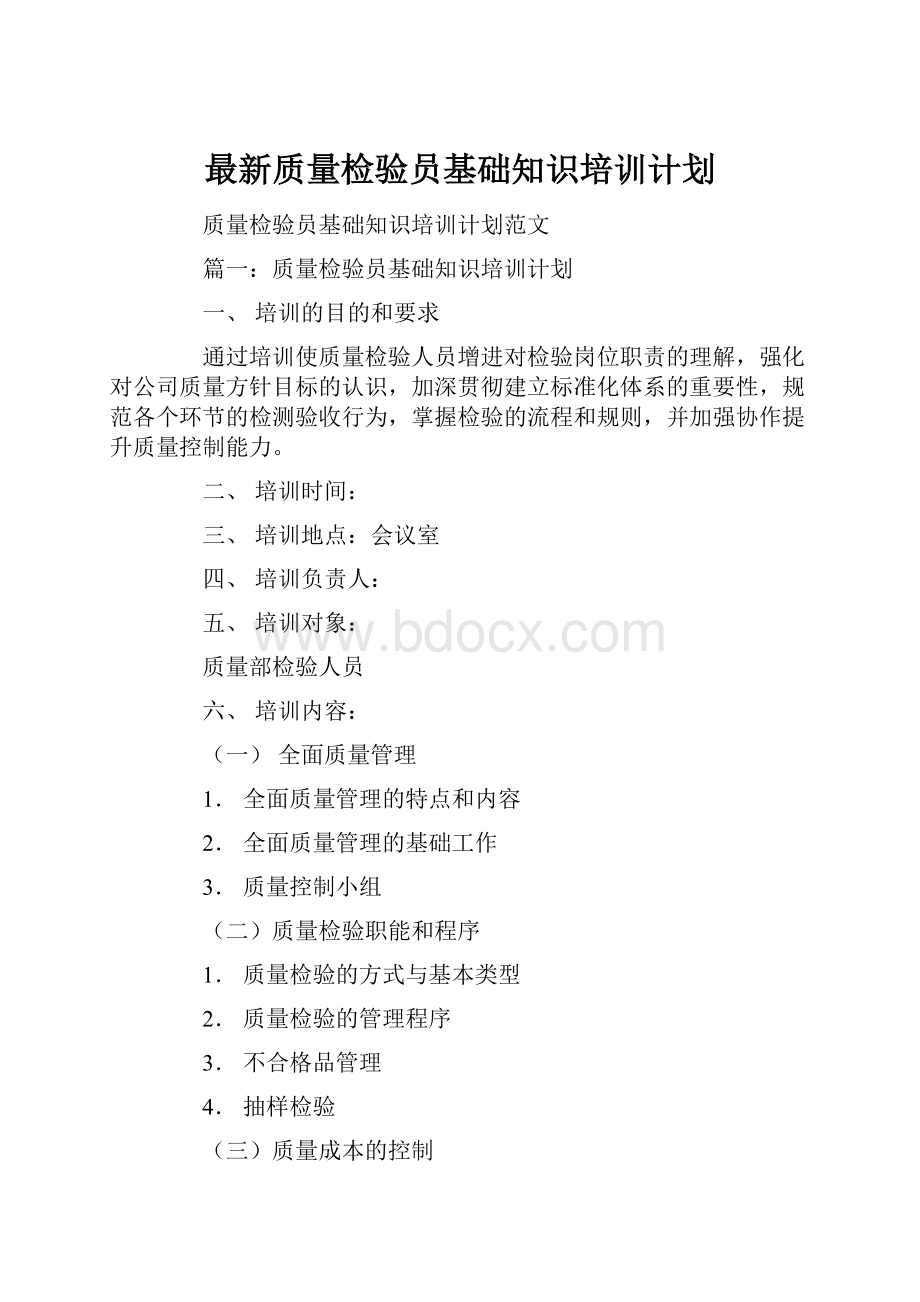
5.质量检验的主要管理制度
6.质量检验的组织工作
(五)常用检测设备的使用方法
1.游标卡尺的使用方法
2.千分尺的使用方法
3.百分表的使用方法
4角度尺的使用方法
5.硬度计的使用方法
6.碳、硫、镍等的测定方法
七.培训课程及时间安排
篇二:
质量检验人员专业培训管理制度
1目的:
规范质量检验人员的培训教育,提高其业务管理水平。
2依据:
《药品生产质量管理规范(2010年修订)》
3适用范围:
质量检验人员。
4责任:
办公室、质量管理部。
5内容:
5.1质量检验工作关系到企业的产品质量信誉,关系到企业的前途,质检人员除了按照正常的教育培训以外,还要进行本专业的特殊培训教育,其工作在公司办公室领导下由质量管理部负责全面工作。
5.2定期进行政治思想教育及职业道德教育,加强质量意识,坚持原则,注重事实,不能以领导的意志而改变事实上的检验结果。
5.3从事质量检验的人员必须是经过药学中等专业以上学习并且取得区药检部门颁发的检验员合格证书、经本公司岗前考核合格的人员。
5.4质量检验人员上岗前,必须经过质检部门安排的岗前专业技术培训,并由专人带教,检验结果经专人复核。
名称:
质量检验人员专业培训管理制度编码:
SMP-RY-015-00第2页,共2页
5.5不断学习先进的技术与管理经验,每年的十二月以前由质量管理部做好第二年的质量检验人员业务技术培训及学习计划,交由办公室审批。
5.6质量管理部按计划将质量检验人员送到市药检所、区药检所、药品监督局、研究所等单位学习培训,以提高其业务水平。
5.7质量检验人员主动要求参加业余学习培训的,须报经质量管理部初审通过后,报办公室审批,按公司《业余学习管理制度》办理。
5.8学习结束,将学习资料交由质量管理部存档,作为公司学习资料进行存档,同时将学习培训证书复印件交办公室存档。
篇三:
质量检验员培训教程
1.质量的定义
1.1狭义的定义:
质量(Quality)---产品、体系、或过程的一组固有特性满足顾客和其他相关方要求的能力。
注:
―质量‖可使用形容词如差、好或优秀来形容。
1.2广义的定义:
质量(Quality)---公司全面管理目标的实现。
如:
供方的控制、成本、顾客满意度、新产品开发周期、生产周期、库存周转频次等。
1.3常见的产品特性如:
–尺寸、外观、强度、寿命等。
常见的过程特性如:
–温度、压力、湿度、电流、电压等。
2.品质控制的演变
2.1操作者控制阶段:
产品质量的优劣由操作者一个人负责控制。
2.2班组长控制阶段:
由班组长负责整个班组的产品质量控制。
2.3检验员控制阶段:
设置专职品质检验员,专门负责产品质量控制。
2.4统计控制阶段:
采用统计方法控制产品质量,是品质控制技术的重大突破,开创了品质控制的全新局面。
2.5全面质量管理(TQC):
全过程的品质控制。
2.6全员品质管理(CWQC):
全员品管,全员参与。
3、不良的来源——变异
变异是宇宙现象,人类生活中任何过程都会有变异。
变异大,可以看出来,变异小,无法目视判别。
假如由生产线随机取出数个产品,测量产品的某些特性,如果测量仪器足够精确的话,必将发现这些产品的测量值各不相同。
3.1变异来源之一机器
如:
切割机器刀具锋利度冲压机冲程可能之变动
电镀处理液之变动空压机气压之品质
3.2变异来源之二材料
供应厂商更换材料(部件)替换
材料机械性质或化学性质之变动材料尺寸变动
3.3变异来源之三方法
流程之变更作业方法之变更
工具、夹具不当
3.4变异来源之四操作员
操作员熟练度操作员习惯性
操作员有没有依照操作标准作业操作员之体力与情绪
操作员的工作场所及使用工具
3.5变异来源之五环境因素
电源稳定度水质稳定度
温度、湿度空气粉尘
照明度地板及工作场所清洁
工作场所物品之摆放
3.6变异来源之六管理因素
紧急订单比例多机种更换频繁
人员流动频繁设计不妥当
4、防止不良品的要诀
4.1稳定的人员
人员流动率高低,往往可以反映员工对企业的认同程度,品质亦是如此。
一个新进的人员,除了因工作熟练度差而效率低下外,还有对于机器、工具的不了解,对材料的不了解,对作业方法的不熟练,对产品品质的要求也不认识等太多变因之存在,所以车间要有效地采取措施,尽量减少因管理原因造成的员工出走。
4.2良好的教育训练
4.3建立标准化
标准化,也可以说是种制度,或是说规定,或工作规则,更是工作方法。
有了标准化,每一项工作就是换了不同的人来操作,也不会因为不同的人,而出现太大的.差异。
因此建立工作标准,完善作业标准及检验标准,才是维持工作稳定,从而稳定品质的最彻底的工作。
4.4消除环境乱象
脏乱指的是机器摆放不当及缺乏保养整理,工具、夹治具的放置及整理,材料、半成品、成品、侍修品、报废品之放置及处理,工作台、办公桌的整理;
地上及通道紊乱摆放及不干净。
工作场所脏乱,代表的是效率低落、品质不稳定及种种的浪费。
因为脏乱,就会衍生许多工作困扰,要消除困扰,就得从最基础的消除脏乱着手。
4.5统计品管(SQC)
传统的品管方法是对产品进行检验,让良品继续流向下道工序,而将不良品予以剔除,并进行整修或报废处理。
这种做法只能得到被检验产品的品质讯息,而对于产品的品质改善却没什么意义。
应用统计的手法,分析不良的原因,寻找解决问题的对策,是以后我们要加强的工作。
4.6稳定的供料厂商
再好的技术,再好的机器设备,假如缺乏良好稳定的材料来配合,还是难以生产良好又稳定的产品。
5、怎么实施品质管理
5.1品质意识的灌输
品质本身是个很模糊的名词,但它却代表着企业的生命,再者,产品品质的好坏,往往都要看企业内每一个成员对品质的认识及心态。
因之品质教育的第一个要务是要唤起公司全体成员对品质的「重视」,尤其是我们各主管方面要树立起「品质意识」及「危机意识」。
譬如:
下面情况对企业来说已是危机:
a、客户的流失。
b、市场占有率的下降。
c、品质成本的扩大。
(失败成本d、经常的返工再修造成的交期延误。
)
e、在市场上品质差,所造成的企业形象损失。
品质意识灌输什么呢,主要是以下几下7个方面:
a、购入不好的材料,就难有好的成品。
b、不依照标准的作业方法操作,不良率会增高。
c、工作场所不讲究(清理),会造成更多的不良。
d、机器、工具、模具平时不保养,生产不出好产品。
e、不良品多,效率就低,生产奖金受影响。
f、不良品多,经常返修补货,交货就有问题,就得加班赶生产。
g、不良品多,是一种不光荣的事情。
如何强化基层员工的品质意识,主要强调如下问题。
a、你所做的工作,自己是否满意?
b、你所做的工作,后工序的人是否满意?
c、你所做的工作自己满意及后续的人满意,这是你的「责任」。
品质意识的灌输,除利用培训外,也可以利用开早会时。
5.2全员参与,全员改善
品质不是某一个部门的事,也不是某些人的专责,上自最高主管,下至每一个成员,把每一件事做好,这就是对品质负责,也就是对于任何一件事,不光是「做」,而且要尽力地去「做好」。
企业管理人员除了每天忙于日常工作以外,还要考虑如何训练自己,如何训练下属。
公司每一个部门,自市调、研发、设计、采购、物管、生产、检验、销售、售后服务,每一个环节均要有效地做好品质管理。
5.3品质管理程序及技术标准、检验标准的执行
一方面标准执行的不折不扣,另一方面根据产品的技术要求及质量控制计划,建立质量责任制,对影响生产过程质量的因素(人、机、料、法、环)进行有效控制。
车间管理人员及质检、技术人员还要做好车间生产人员的操作手法及工艺要求的指导工作。
重点工序、重点人员、关键控制点的控制。
6.品质检验定义及方法
6.1检验的定义:
采用某种方法(技术、手段)测量、检查、试验和计量产品的一种或多种质量特性并将测定结果与判定标准相比较,以判定每个产品或每批产品是否合格的过程。
6.2常用的判定标准:
如国家或行业标准,检验规范(质量计划、作业指导书等),技艺评定(限度样本、图片等)
6.3检验的分类
6.3.1按检验数量分:
全数检验、抽样检验;
6.3.1.1全数检验:
将送检批的产品或物料全部加以检验而不遗漏的检验方法。
适用于以下情形:
a.检验数量和项目较少,且费用较低;
b.产品必须是要求全部合格;
c.检验是非破坏性的;
d.生产中尚不够稳定的比较重要的特性项目;
e.产品中如有少量的不合格,可能导致该产品产生致命性影响,也就是影响产品质量的重要特性项目;
f.单件、小批生产的产品;
g.昂贵的、高精度或重型的产品;
h.能够应用自动化检验方法的产品。
6.3.1.2抽样检验:
从一批产品的所有个体中抽取部分个体进行检验,并根据样本的检验结果来判断整批产品是否合格的活动,是一种典型的统计推断工作。
适用于以下情形:
a.对产品性能检验需进行破坏性试验;
b.被检对象是连续批(如钢卷、胶片、纸张等卷状物或流程性材料),或批量太大,无法进行全数检验;
c.检验项目多,需较长的检验时间和较高的检验费用;
d.允许有一定程度的不良品存在。
6.3.2按流程分:
进货检验、过程检验、最终检验、出货检验;
6.3.3按判别方法分:
计数检验、计量检验;
6.3.4按产品检验后产品是否可供使用来分:
破坏性检验、非破坏性检验。
6.4关于抽样检验
6.4.1抽样检验是利用样本进行的检验,所抽取的样本只占批中的一小部分,样本的质量特性结果只能相对地反映整批产品的质量,不能把样本的不合格率与整批产品的不合格率等同起来;
6.4.2但是,我们所讲的抽样检验,是建立在数理统计的基础上的、可靠地反映整批产品的质量,在实际应用中,常常是可行的、多快好省的办法。
6.4.3抽样检验并不排斥全数检验,应根据实际情况进行分析,目的都是为了提高质量和降低成本。
6.5抽样检验中的有关术语:
6.5.1检验批:
同样产品集中在一起作为抽验对象;
一般来说,一个生产批即为一个检验批。
可以将一个生产批分成若干检验批,但一个检验批不能包含多个生产批,也不能随意组合检验批。
6.5.2单位产品(unitproduct):
为了实施检验的需要而划分的基本单元。
6.5.3批量:
批中所含单位数量;
6.5.4抽样数:
从批中抽取的产品数量;
6.5.5缺陷(Defect):
产品质量特性不满足预定使用要求。
6.5.6不合格判定数(Re):
Refuse的缩写即拒收;
6.5.7合格判定数(Ac):
Accept的缩写即接收;
6.5.8合格质量水平(AQL):
AcceptableQualityLevel的缩写。
通俗地讲即是可接收的不合格品率。
6.6如何确定抽样容量
6.6.1进货检验、最终检验及出货检验可选用GB2828-87或其它抽样标准.
6.6.2对过程检验,由质量策划人员根据产品的稳定情况及过程能力等因素确定抽样容量及频次.
6.6.3抽样方案的确定:
采用的抽样方案是根据国家标准GB2828《逐批检验计数抽样程序及抽样表》来设计的。
具体应用步骤如下:
a.确定产品的质量判定标准:
b.选择检查水平:
一般检查水平分Ⅰ、Ⅱ、Ⅲ;
特殊检查水平分S-1、S-2、S-3、S-4,
一般情况下,采用一般水平Ⅱ。
c.选择合格质量水平(AQL):
AQL是选择抽样方案的主要依据,应由生产方和使用方共同商定。
d.确定样本量字码,即抽样数。
e.选择抽样方案类型:
如一次正常抽样方案,加严抽样方案,还是多次抽样方案。
f.查表确定合格判定数(AC)和不合格判定数(Re)。
7.检验作业控制
7.1进料(货)检验(IQC)(IncomingQualityControl):
是工厂制止不合格物料进入生产环节的首要控制点。
7.1.1主要职责:
按质量策划的结果(如质量计划、进货检验指导书、国家或行业标准等)实施检验;
做好记录并保存好检验结果;
做好产品状态的标识;
进行不合格品统计和控制;
异常信息反馈。
7.1.2检验方法:
验证质保书;
进货检验和试验;
在供方处的验证;
委外检验和试验。
①进料检验项目及方法:
a外观:
一般用目视、手感、对比样品进行验证;
b尺寸:
一般用卡尺、千分尺等量具验证;
c特性:
如物理的、化学的、机械的特性,一般用检测仪器和特定方法来验证。
②进料检验方法:
a全检,b抽检
③检验结果的处理:
a接收;
b拒收(即退货);
c让步接收;
d全检(挑出不合格品退货);
e返工后重检;
④依据的标准:
《原材料、外购件技术标准》、《进货检验控制程序》、《图纸》等等。
7.2生产过程检验(IPQC)(InprocessQualityControl):
一般是指对物料入仓后到成品入库前各阶段的生产活动的品质控制。
而相对于该阶段的品质检验,则称为FQC(FinalQualityControl)。
7.2.1主要职责:
按质量策划的结果(如质量计划、作业指导书等)实施检验;
做好产品状态的标识;
进行不合格品统计和控制;
异常信息反馈。
7.2.2检验方法:
①过程检验的方式主要有:
a.首/末件检验、作业员自检、互检、专检相结合;
b.过程控制与检验员抽检、巡检相结合;
c.多道工序集中检验;
d.逐道工序进行检验;
e.产品完成后检验;
f.抽样与全检相结合;
②过程品质控制(IPQC):
是对生产过程做巡回检验。
a.首件检验;
b.材料核对;
c.巡检:
保证合适的巡检时间和频率,严格按检验标准或作业指导书检验。
包括对产品质量、工艺规程、机器运行参数、物料摆放、标识、环境等的检验;
d.检验记录,应如实填写。
③过程产品品质检验(FQC):
是针对产品完工后的品质验证以确定该批产品可否流入下道工序,属定点检验或验收检验。
a.检验项目:
外观、尺寸、理化特性等;
b.检验方式:
一般采用抽样检验;
c.不合格处理;
d.记录;
《作业指导书》、《工序检验标准》、《过程检验和试验程序》等等。
7.2.3三―不‖原则:
不接受不合格品;
不生产不合格品;
不流转不合格品。
只有质量计划中规定的所有检验项目都完成且合格之后,产品才能转序或入库。
7.3最终检验控制:
即成品出货检验。
(OutgoingQ.C)
7.3.1主要职责:
按质量策划的结果(如质量计划、出货检验指导书)实施检验;
做好记录并保存好检验结果;
对不合格品进行登记、隔离并采取措施;
对采取
【质量检验员基础知识培训计划范文】