汽车覆盖件拉伸起皱开裂分析及控制DOCWord格式.docx
《汽车覆盖件拉伸起皱开裂分析及控制DOCWord格式.docx》由会员分享,可在线阅读,更多相关《汽车覆盖件拉伸起皱开裂分析及控制DOCWord格式.docx(16页珍藏版)》请在冰豆网上搜索。
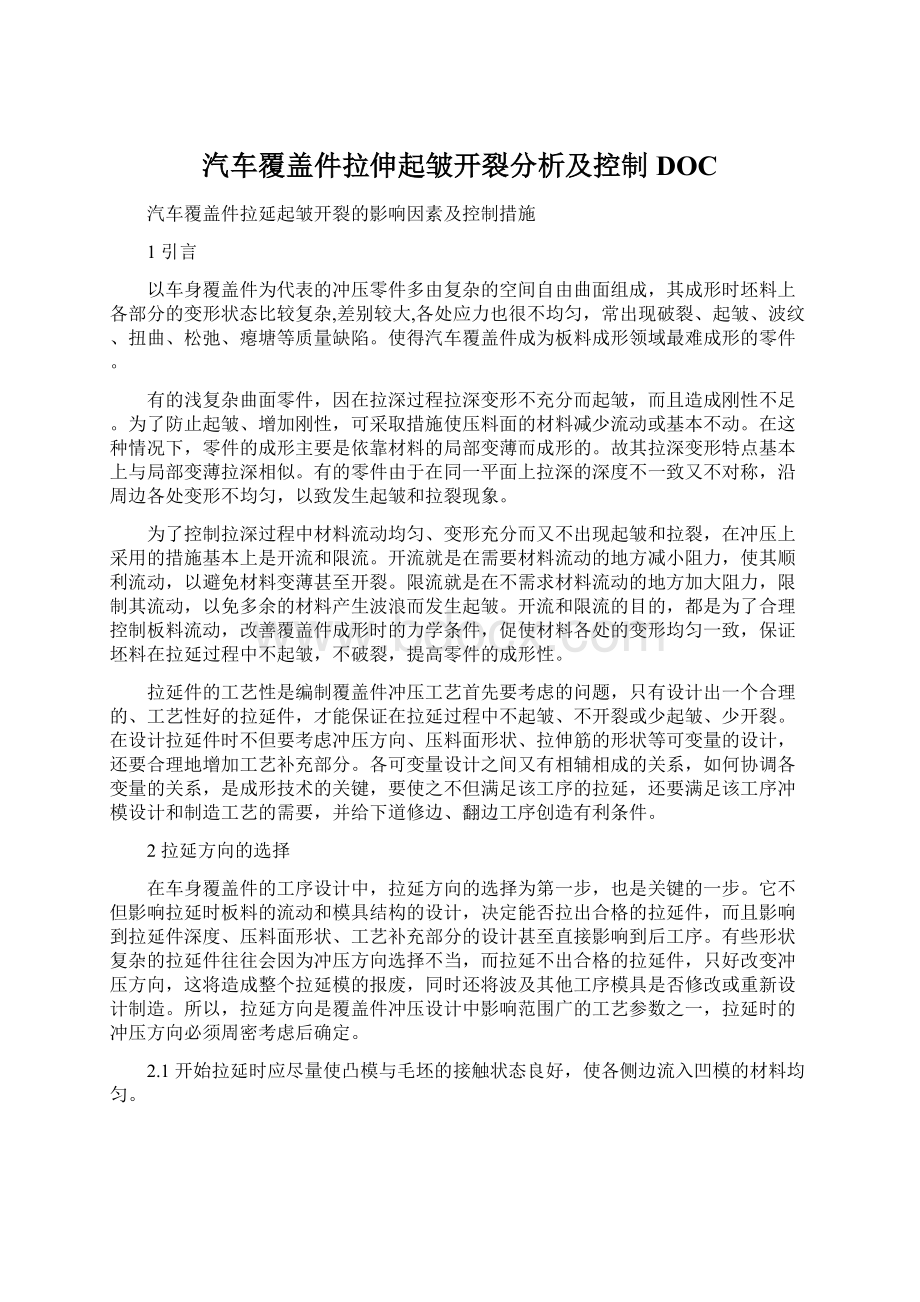
2.1开始拉延时应尽量使凸模与毛坯的接触状态良好,使各侧边流入凹模的材料均匀。
当凸模与坯料为点接触时,应适当增大接触面积,防止材料因应力集中而造成局部破裂,如图2-1a。
但也要避免凸模表面与坯料以大平面接触的,否则由于平面上的拉应力值降低,材料得不到充分的塑性变形,影响零件的刚性,并容易起皱。
凸模与毛坯接触的地方应尽量靠近中间,如图2-1b
凸模与毛坯的接触点要多而分散,并尽可能分布均匀,防止坯料窜动,如图2-1c
2.2拉延方向的选择应使压料面各部位进料阻力均匀
拉延深度是保证压料面各部位进料阻力的主要条件,因此,选择拉延方向时,应保证拉延深度均匀,深度合理,如图2-2。
2.3拉延方向有利于后工序的加工
设计拉延件形状还必须考虑后工序的加工难度,现以一个零件为例说明:
图2-3为一左右对称冲压加工的零件,若按(a)图的合并所决定的拉延方向,则造成零件拉延深度较深,容易拉毛,而且修边困难;
若按图(b)、(c)的形式合并后所决定的冲压方向进行拉延,需拉延两次,拉延深度变浅,修边加工容易,其实仔细分析方案(b)、(c)可以看出,(b)在拉延时,从压料面上补充进材料较为困难,材料容易产生局部变形,而且在冲孔时,斜锲布置空间紧张,而(c)则无上述问题。
2.4应保证凸模能将零件需拉深的部位在一次拉延中完成,不应有凸模接触不到的死角或死区,即尽量使拉深件形状能一次拉深成形。
3工艺孔和工艺切口
当覆盖件的中间部位或成双拉深的连接部位,由于拉深过程中不能从毛坯的外部得到材料的补充而导致零件的局部破裂时,可考虑在工艺补充的适当部位冲出工艺孔或工艺切口,使容易破裂的区域得到材料的补充,克服开裂现象。
如图3-1是D310车型左/右侧边梁,其采用成双拉延的形式生产,但由于中间联结处深度与宽度的比值较大,成型困难,用AUTOFORM模拟时反成型的R部位开裂,在反成型的中间废料部位需增加两处工艺孔,以使材料向外流动。
工艺切口必须设置在容易破裂的区域附近,而这个切口必须布置在工艺补充上,修边线以外,在修边冲孔时将它们冲掉。
工艺切口一般在成形过程中切出,它可充分利用材料的塑性,即在成形开始阶段利用材料径向延伸,然后切出工艺切口,利用材料切向延伸,这样成形深度可以深一些。
在成形过程中切工艺切口时,并不希望切割材料与制件本体完全分离,切口废料可在以后的修边工序中一并切除。
否则,将产生从冲模中清除废料的困难。
工艺切口
图3-1左/右侧边梁反成型处增加工艺切口
工艺孔一般在拉深前的落料冲孔工序中完成,如D310车型门里板的侧窗处。
图3-2门里板的落料冲孔毛坯
工艺切口、工艺孔的布置及其大小和形状要视其所处的区域情况和其向外补充材料的要求而定。
一般应注意以下几点:
(1)切口应与制件局部形状相适应,以使材料合理流动。
(2)切口之间应留有足够的搭边,以使凸模张紧材料,保证成形清晰,避免波纹等缺陷,而且修边后可获得良好的窗口、翻边、孔缘质量。
(3)工艺切口在拉深过程中冲出时,要注意冲孔的时间,如果过早切口会使拉深件出现皱纹;
太晚则达不到切口的目的。
(4)切口或冲孔的数量、大小和形状,要根据所处的位置和变形要求,通过试料来确定。
(5)切口的切断部分应临近容易破裂的区域,使各处材料变形趋于均匀,否则不一定能防止裂纹产生。
4压料面的选择
在复杂曲面大型零件的拉深与成形中,在模具上都要设有压料面。
压料面是工艺补充部分的一个组成部分,即凹模圆角半径R凹以外的一部分。
凸模对坯料开始拉深前,压料圈将拉深坯料压紧在凹模压料面上。
压料面的形状不但要保证压料面上的材料不皱,而且应尽量造成凸模下的材料能下凹以降低拉延深度,并保证拉入凹模里的材料不皱不裂。
压料面一般有两种:
一种是压料面就是零件本身的法兰面,另一种则是由工艺补充部分而形成,压料面的形状多数是曲面的。
选择压料面的原则:
1)压料面应尽量平整,不能有鼓起、凹坑和皱褶,在坯料被压紧时,应不产生折皱。
2)压料面应尽量处于水平位置。
这样有利于金属流动,便于拉深工作,如图4-1所示。
3)压料面应与凸模的形状保持一定几何关系,保证在拉深过程中,坯料始终处于张紧状态,并能平稳地、逐次地包拢凸模,以防产生裂纹及皱纹。
因此压料面在展开后应保证如下关系:
L>
L1β>
α
式中L——凸模表面展开长度;
L1——压料面展开长度;
α—凸模表面夹角,α<
180°
;
β—压料面平面夹角,β<
。
如图4-2所示为压料面展开长度比凸模表面展开长度短(L>
L1)示意图。
这样凸模对毛坯可以拉深,但还不一定保证最后不形成波纹及起皱。
如图4-3所示的压料面形状,虽然L>
L1,但压料面夹角β比凸模表面夹角α小,因此凸模从开始拉深到最后的过程中,几个瞬间位置的压料面展开长度比凸模表面展开长度长,形成的皱纹比较大。
故这样的压料面是不能采用的。
故防皱条件是:
L1及β>
α。
若不能满足这一条件,要考虑改变压料面,或在拉深件底部设置筋或反成形形状吸收余料。
4)压料面应使成形深度小且各部分深度接近一致。
这种压料面可保证各部分进料阻力均匀,使材料流动和塑性变形趋于均匀,减小成形难度。
进料阻力不均匀,在拉深过程中毛坯可能沿凸模顶部窜动,严重时会产生破裂和皱纹。
而达到进料阻力均匀的一个前提条件就是拉深深度均匀。
5)压料面应使毛坯在拉深成形和修边工序中都有可靠的定位,并考虑送料和取料的方便。
在实际工作中,上述各项原则不能同时达到时,应根据具体情况决定取舍。
5.工艺补充形状
覆盖件的形状复杂,结构不对称,为了获得成形性良好的拉延件,有时需将覆盖件上的翻边展开,将孔补满,再加上工艺补充部分使覆盖件形成一个封闭的零件,通过这些措施,使覆盖件的成形条件得到改善,从而保证覆盖件的拉延质量。
但是,因为拉延后要将工艺补充部分修掉,所以要在能够拉延出满意的拉延件的条件下,尽可能地减少工艺补充部分,降低材料消耗。
5.1拉延台阶的设定
拉延台阶属于工艺补充设计的一个重要内容,它具有以下作用:
1)若按覆盖件凸缘设定压料面,就可能使压料面凸凹不平,当深度差剧烈时,会出现开裂、起皱现象,设定拉延台阶,可获得加工性良好的压料面,利于成形质量。
2)对于一些覆盖件,其侧壁易出现体皱纹,滑伤、冲击线、翘曲、松弛等缺陷,解决这些缺陷的办法,一般是通过拉延台阶,使材料充分变形。
3)在后工序中,零件次村往往在修边时,零件与模具形状不易重合,设定拉延台阶有利于零件定位,同时可将那些需要斜锲修边的地方,改成垂直修边。
5.2拉延台阶高度和宽度的关系
图5-1表示了拉延台阶在拉延过程中的情况:
W>
H:
即拉延台阶宽,其效果减弱,故易出现冲击线和滑伤。
W≈H:
为理想的拉延台阶。
W<
即拉延台阶相对于深度大,材料在凸模与凹模的约束中,会在加工是出现破裂。
5.3几个案例
图5-2所示的零件边缘有很大的高差,故设定了拉延台阶,压料面的形状得到了缓和,成形效果较好。
但将压料面完全取成平面,则会在零件后部R处也会出现拉延台阶,R处将出现皱纹,同时台阶相对其宽度较深,反而不利于拉延。
图5-3所示零件周围边缘的修边形状凸凹不规矩,可通过设定拉延台阶,得到平坦的压料面。
图5-4所示碟形零件,修边时,拉延件不易与模具重合,设计拉延台阶利于修边时定位,而且台阶设定后,材料变形充分,零件刚性好,不易回弹。
必须注意的是,圆角R易出现皱纹,因此,R1<
R2,这对防止皱纹出现是重要的。
图5-5所示零件,冲击线较易出现在零件侧壁,对外观质量有所影响,若增设拉延台阶,可扩大凹模口,使冲击线出现在零件的底部,同时产生较强的拉力。
总之,应根据覆盖件的具体情况,综合考虑压料面、拉延深度、拉延方向等诸多因素,上述设定拉延台阶方法,只是工艺补充方面一些典型的例子,在实际工作,还需灵活掌握应用。
6拉延筋技术
6.1拉延筋的作用
拉延筋是板料拉深成形中的主要控制手段之一,较之其它控制手段具有简单方便,易于实现等优点。
它能更加稳定、有效、灵活、均匀地控制压料力。
随着冲压制件的复杂程度和难度的不断增加,拉深筋的设置和调整已成为拉深模具设计及试模过程中的关键技术。
其作用描述如下:
(1)增加进料阻力。
拉延筋阻力是由坯料通过拉延时的弯曲反弯曲变形力、摩擦力以及因变形硬化引起的再变形抗力增量二部分组成的。
如图6-1所示,板料流经拉延筋时,在点1到点6之间发生了弯曲、回复、弯曲的反复变形,这些变形所需要的变形力加上筋与板料表面的摩擦力都直接作用在板料上,增加了板料流动的进料阻力。
拉延槛也是拉延筋的一种,由于其弯曲更剧烈,所以其进料阻力大得多,更适用于曲率较小、平坦的或深度小的覆盖件,使板料成形不仅靠压边圈外材料的流入与补充,更依靠材料本身的塑性变形来成形。
图6-1 板料流过半圆筋所发生的形变
(2)调节进料阻力的分布。
通过对拉延筋的位置、根数和形状的适当配置,使拉延过程中各部分流动阻力均匀,坯料流入模腔的量适合制件各处的需要,从而调节材料的流动情况,增加坯料流动的稳定性。
(3)降低对压料面精度的要求。
不用拉延筋时,压料面表面精度要求较高,即要求平整、光滑、贴合、均匀。
使用拉延筋后,压料面间隙可适当加大,表面精度可适当降低,从而减少模面制造工作量,减少压料面的磨损。
(4)增加零件的刚性。
通过增加径向拉应力,促使板料承受足够的拉胀成形,对于大曲面平坦零件成形时易出现的松弛回弹及波纹等缺陷,设置筋(槛)可产生很大的径向拉应力使材料充分变形,减少由于变形不足而产生的回弹、松弛、扭曲、波纹、收缩等。
(5)提高零件表面质量。
可防止因凸缘周边材料不均匀流动造成的不可避免产生的皱纹进入修边线内,减轻或消除大底角筒形件、球形件、锥形件等零件(凸凹模之间有较大的间隙)中间悬空部分因材料集中发生的内皱现象。
(6)合理设置拉深筋可在一定程度上降低对压床吨位的需求。
通过增加胀形成分和增大进料阻力,可减小板料外形尺寸,提高材料利用率。
(7)稳定生产,降低废品率。
使用拉延筋可建立所需的应力状态,增大径向拉应力,减小切向压应力,减少由于起皱、压边力以及板料厚度变化等原因而产生的废品,使拉延过程稳定。
(8)对板料有校整作用,纠正坯料的不平整缺陷,提高材料的拉延性能。
6.2拉延筋的种类、结构形式与设置
拉延筋的种类与结构形式在相关资料中有详细的描述。
相对而言,拉延筋的设置,包括筋的大小、位置、根数等,更能影响到拉延筋所起的作用,而拉延筋的设置也正是根据希望它要起到的作用来完成的。
概言之,就是在需要增加和调节进料阻力的地方设置拉延筋。
设置筋应注意以下几点:
(1)零件压料后应保证不起外皱、不起内皱、不拉裂。
(2)如图6-2所示,考虑到筋所处位置的形面形状、后续模具结构的合理性,当筋的位置处在平坦部位时,一般按图6-2(a)设置。
当筋的位置处在形面时,考虑到修边模的凹模刃口,一般按图6-2(b)或图6-2(c)所示设置。
对于深拉延件,其侧壁易出现波纹,应使拉延筋离凹模口远一些,从而在一定程度上使经过拉延筋的坯料在流入凹模口前被校平。
(a)(b)(c)
图6-2 拉延筋的位置
(3)在绝大多数情况下,拉延筋(槛)的走向要与坯料流动方向垂直,但在某种情形下,筋的走向可与坯料流动方向成一定角度或平行于坯料流动方向,以防止走料过程中的窜料或厚度变化转移。
(4)考虑到拉延的经济性,采用最小可行的筋边距和筋间距,但如果对材料利用率没有影响,拉延筋位置应取大一些。
(5)对外覆盖件,筋的位置应设置在拉延筋拉痕不会影响产品的位置上。
(6)考虑到制造维修的方便性,应尽可能采用整体筋,在本体上直接加工出来。
在不能事先设定拉延筋具体位置时,可采用镶筋。
以便于调试时的变更。
在平的压料面上最好采用镶筋结构,可望将压料面的数控铣加工改为磨削加工,减少加工成本。
(7)拉延筋的高度变化应注意缓慢过渡。
比如在圆角区的拉延筋高度为1~3mm,从圆角结束位置处,在40mm范围内,缓慢变成一般位置拉延筋的高度。
在拉延筋的端头,筋的高度渐变至0的过渡区段应在30mm长左右,且端头在平面以圆角收尾。
在调整时,拉延筋槽可以加深,但必须保证槽宽。
(8)对于多排的拉延筋,应使筋的高度有所变化。
随着坯料从外向里流入,在伸长变形区和直线弯曲变形区,料厚变薄,压料面间隙相对增大,减小了压料力,或料厚虽无明显变化,但随着坯料的流动压料面减少,压料力也相应减少,应使筋的高度由外向里逐渐增高,使筋的进料阻力由小到大,以补偿压料力的减少。
而对于压缩变形区材料在流动过程中料厚有增大的趋势,使压料面间隙相对减少而增大了进料阻力,此时使多排筋的高度由外向里逐渐降低,以适应压料力的变化。
(9)为便于模具调试维修,不论是单动拉延还是双动拉延,原则上将拉延筋设置在上模上(上模为凸筋),而将拉延筋槽做在下模,因为调试拉延模时拉延筋一般不打磨,拉延筋槽做在下模便于研配,也便于放料,与拉延筋槽做在上模相比,它的抑制力较弱,而且易出现翘曲的缺陷。
如图6-3,在情形(a)时,材料的弯曲变形在R1、R2处相抵消,拉延侧壁的翘曲小。
在情形(b)时,没有拉延筋,凹模口R的弯曲变形仍然残留,侧壁会产生翘曲。
在情形(c)时,R1、R2的弯曲变形属同一方向,翘曲更严重。
所以有时候拉延筋距凹模口的距离要适当大一些,特别是对于深拉延件的侧壁易出现回弹时更要如此,使坯料流过拉延筋后再经过一段被校平的区域。
(a)(b)(c)
图6-3 筋对翘曲的影响
(10)拉延筋一般设置在压料面上,但根据它所起的作用,在某些场合亦可设置在其它需要的地方。
比如:
①在深斜拉延侧面上,容易出现波浪,可用或横或竖之闲筋以消之。
②在拉延件中,若有较深的反拉延时,在反拉延凹模口外边的材料,容易起皱,应视必要和可能而设置内筋以舒皱,即在凹模口以内设置拉延筋,如图6-4所示,在主拉延面上设内筋,并在反拉延面上也设内筋,只要在主拉延面与反拉延面上的内部闲筋互相配合恰当,便能起到舒平防皱的效果。
图6-4 内筋
③鞍形拉延件中部易起皱。
同样可以用内筋舒皱,但产品应允许有筋存在。
(11)对空间曲面变化小的浅拉延件,若后续工序件需用拉延筋(槛)定位,设置拉延筋(槛)位置时要考虑后续定位块结构尺寸,修边凹模强度等,还要使定位稳定可靠。
6.3拉延筋的局限性
作为冲压成形的控制方法,拉延筋并不是唯一的措施。
在实际生产中必须根据零件的几何形状及精度要求等方面的情况灵活地采取各种不同的方法解决其成形的问题。
拉延筋的局限性如下:
(1)必须依赖于足够的压边力才能使拉延筋起作用。
当压边力不足时,在压边圈与凹模面接触的过程中,拉延筋自身成形不足,不仅不能增加材料流动的阻力,随着材料向里流动,凸缘面将产生皱纹,皱纹产生的阻力及皱纹通过筋时的反作用力会导致压边圈上浮,皱纹还将拉毛模面。
另外即使压料时筋的成形充分,如果压边力不足,材料通过筋时的反力也会造成压边圈上浮。
生产过程中常常出现气压不足或波动等引起压边力不足而造成废品率上升的现象。
因此使拉延筋起作用的必须条件是:
①初始压力足以使筋成形。
②确保在板料流入凹模的全过程中,随着材料硬化加剧引起弯曲力不断上升,使筋不被抬起。
(2)当零件对称变形或者变形接近均匀及不需要很大的胀形成分等情况下,不设置筋而采用平面压边形式。
(3)材料的相对厚度大时,不用拉延筋甚至不用压料。
(4)多次拉延时,一般只在最后一次拉延时设置拉延筋。
(5)需借助数字仿真分析软件对拉延筋的设置及更改作出快速评估,减少物理试模,降低制造成本,缩短制造周期。
7CAE技术的运用
随着非线形理论、有限元方法和计算机软硬件的迅速发展,薄板冲压成型过程的CAE分析技术日渐成熟,并在冲压工艺与模具设计中发挥了重要的作用。
目前的金属板料成形CAE系统已能提供多方面的分析和模拟结果:
材料的流动、厚度的变化、破坏、起皱、回弹,以及残余应力和应变,用以预测产品设计和加工工艺的合理性。
工艺人员可以根据模拟分析的结果对工艺方案进行优化、对产品设计提出修改意见,从而有效地缩短模具设计周期,大大减少试模时间,帮助企业改进产品质量,降低生产成本,从根本上提高企业的市场竞争力。
(1)通过对零件的可成形工艺性分析,做出零件是否可制造的早期判断,通过模拟分析,及时向研发部门提出产品改进方案,减少实际试模次数,缩短开发周期。
如D530一排半薄顶侧顶盖是在D310标准车侧顶盖的基础上简单地降低80mm而成的,由于其深度与宽度的比值加大,且后部存在局部突起,通过通过CAE分析,发现其成形过程中严重拉裂,在距离下死点50mm时已经开裂,即使使用DC06级别的材料,仍不能解决;
多次修改工艺补充部分、调整工艺参数效果也不明显。
根据以往CAE在D310零件中的应用经验,模拟开裂的产品,在实际生产时肯定会裂,反之却不一定。
因此得出结论,该产品在现有工艺条件下,不可能一次拉深成形。
于是与研发部门协商,对产品设计提出修改意见,在保证产品使用功能的前提下,局部修改产品造型(如图7-1),后部深度减小,R放大,如图7-2断面所示,通过几次修改后,终于得出了满意的结果,局部材料减薄率降至20%以下。
采用AUTOFORM分析的料厚减薄情况如图7-3。
更改后
更改前
图7-1D530侧顶盖产品更改前后造型对比图
图7-2D530侧顶盖产品更改前后断面对比图
图7-3D530侧顶盖CAE分析结果-料厚减薄图
(2)通过缺陷预测来制定缺陷预防措施,改善模具结构设计以及冲压方案的可靠性,从而减少生产成本。
图7-4是D530-T2R30左右地板成双拉延件实物,其后角部明显起皱,在模具调试时通过增加吸料筋的方法解决(如图7-5),这样增加了模具调试周期和加工成本。
在D530-T2R30车型中存在类似的零件,通过CAE分析,存在同样的问题,我们吸取了T2R30的经验和教训,对拉延造型的分模线进行调整,如图7-6,起皱情况得到改善,CAE分析的起皱情况如图7-7所示。
皱纹
图7-4D530-T2R30左右地板拉延工序件
图7-5D530-T2R30左右地板增加吸料筋后的数模
T2R30地板分模线
T2R40地板分模线
图7-6D530-T2R40与T2R30地板分模线对比
图7-7D530-T2R40与T2R30地板模拟结果起皱情况对比图
合理应用CAE技术在板料设计中的应用,可以避免和减少传统模具设计方法产生的浪费、失误甚至报废,有效地提高模具开发的效率,降低开发成本。
8结束语
以上仅是从工艺设计过程中冲压方向的选择、压料面形状、合理设置工艺补充、合理利用拉延筋等几个方面讨论了如何防止或解决覆盖件的拉延皱裂问题,并通过D530车型应用实例阐述了在工艺分析阶段采用CAE技术预测覆盖件的拉延皱裂问题及解决问题的思路。
引起拉延件皱裂的原因很多,但只要对发生的现象仔细研究和分斩,不同情况用不同的方法去解决,就会拉出表面质量好的覆盖件。