冷轧无取向电工钢文档格式.docx
《冷轧无取向电工钢文档格式.docx》由会员分享,可在线阅读,更多相关《冷轧无取向电工钢文档格式.docx(15页珍藏版)》请在冰豆网上搜索。
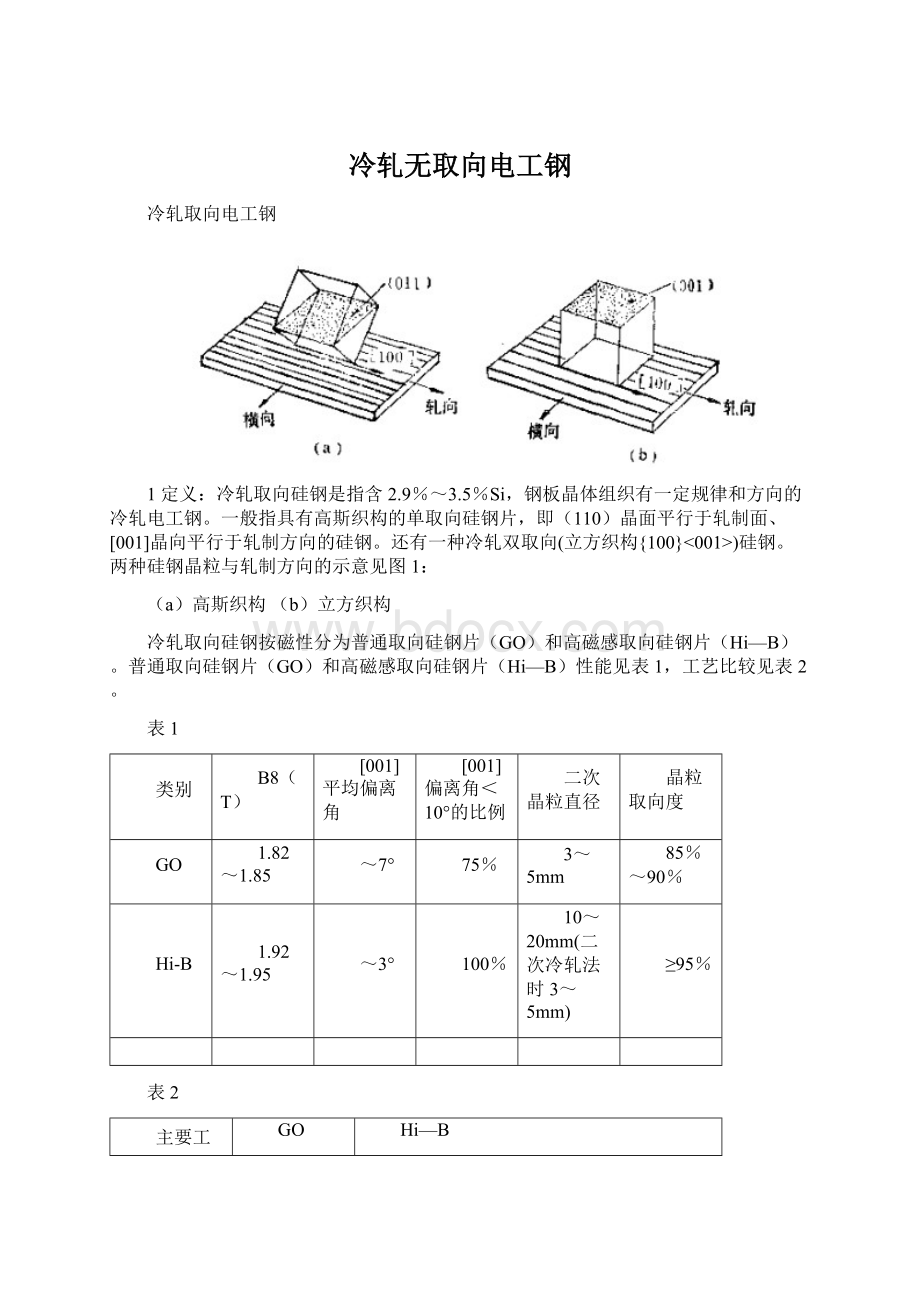
A方案
B方案
C方案
抑制剂
MnS(MnSe)
AlN+MnS
MnSe+Sb
N+B+S
铸坯加热温度℃
1350~1370
1380~1400
1250
常化温度℃
不常化或900~950
1100~1150
900~950
900~1025
第一次冷轧压下率%
70
85~87
60~70
中间退火温度℃
850~950
/
第二次冷轧压下率%
50~55
脱碳退火温度℃
800~850
湿H2+N2
高温退火温度℃
1180~1200
(820~900)×
50h+(1180~1200)
取向硅钢以追求其轧制方向上具有高取向度为出发点,力求获得具有{110}<
高斯织构的晶粒均匀的产品,以满足其使用时在长度方向上具有高磁性能的需要。
对于厚度大于0.3mm的普通取向硅钢(GO),目前比较流行的生产方法是采用抑制剂的二次再结晶法生产。
即以MnS(或MnSe)为抑制剂和二次中等压下率冷轧法。
Hi-B钢按采用的抑制剂和制造工艺不同可分为三种方案:
(A)日本新日铁发展的以AIN为主以MnS为辅的抑制剂和一次大压下率冷轧法,其磁性高且稳定,部分产品经激光照射细化磁畴。
是最通用的Hi-B产品制造工艺。
(B)日本川崎发展的以MnSe(或MnS)+Sb为抑制剂和二次中等压下率冷轧,最终退火经二次再结晶和高温净化二段式退火工艺。
其磁性略低于(A)方案且较不稳定。
高牌号中常加入少量钼。
(C)美国GE和ALC公司发展的以N十B+S晶界偏聚元素为抑制剂和一次大压下率冷轧法。
因为固溶硫含量较高,锰含量较低,Mn/S≤2.1,热轧板边裂严重,其磁性也较低且不稳定,现已很少采用。
2用途:
冷轧取向硅钢又称冷轧变压器钢,用于制造各类变压器的铁芯。
3轧制工艺流程:
冷轧无取向硅钢通用的轧制工艺流程如图2所示。
生产具有高斯织构的硅钢,关键在于利用二次再结晶。
为了实现二次再结晶,通常需要在合金中添加正常晶粒长大抑制剂,如MnS等。
晶粒长大抑制剂必须能以参杂的形式弥散地分布在合金基体内,在二次再结晶发生时,能够有效地阻止基体晶拉的正常长大,同时,又要求在最后的高温退火中可方便地消除掉,以免恶化产品的磁性能。
在二次再结晶中、二次晶粒长大的取向核主要依靠适当的冷轧工艺和再结晶退火来产生。
由于相变会破坏晶粒取向,因此在热处理过程中保持单相至关重要。
目前,工业上生产具有高斯织构硅钢的典型工艺可概述如下:
初始成分——约3.2%Si,≤0.03%C,0.06~0.10%Mn,0.03%S。
钢坯加热到1400℃进行热轧成厚度为1.1~2.5mm的薄板。
经常化及酸洗除去除氧化皮后,通过两次冷轧将薄板轧到0.25~0.36mm的最后厚度。
在两次冷轧之间,需将钢板在800~1000℃还原气氛中进行中间退火。
两次冷轧的总压下率为85%左右。
随后,钢板在800℃左右进行湿氢脱碳退火,以便把碳含量降低到0.003%的水平。
最后,钢板需在1100~1200℃干氢中再进行一次高温退火。
在以上工艺中,钢板在800℃退火期间,细小的MnS颗粒是必要的晶粒长大抑制剂,而在最后的高温退火时,其中的S通过和氢反应生成硫化氢从基休中逸出,剩下的Mn将溶解在铁的晶格中。
用这样的工艺生产的硅钢片晶粒粗大,直径为1~5mm,而且90%以上的晶粒具有(110){001}取向。
因此,沿其轧向具有优异的磁性能。
例如,在磁场为0.8kA/m时,磁感应强度可达1.82T。
相近成分的非取向硅钢,在同样磁场下的磁感应强度只有1.45T。
冷轧
脱碳退火和
涂MgO
常化和酸洗
热轧
二次冷轧
中间退火
一次冷轧
平整拉伸退火和涂绝缘膜
高温退火
图2
4轧制工艺
4.1热轧工艺
1)铸坯
3%Si钢导热率低,铸坯急冷或急热都可能产生裂纹,甚至断坯。
铸坯冷到600℃以前以<20℃/h速度慢冷可防止裂纹。
铸坯切断至进入加热炉的时间要保证<10h,否则由于表层与中心区的温差而引起抑制剂固溶状态和组织状态不同,使成品P17增高。
为防止以后高温加热时柱状晶过于粗化,铸坯冷到650~750℃保温5~10h或以10℃/h速度慢冷使碳化物分布均匀,铸坯加热温度可降到1350℃以下,热轧板晶粒均匀。
铸坯冷到A1相变点附近或A1~950℃范围保温>30min,可在铸坯中形成小晶粒和使第二相溶解度发生变化,也可使加热温度降低约100℃。
2)加热
加热温度:
GO钢——l350~1370℃Hi-B钢——1380~1400℃
铸坯最好在铸坯表面冷到的>1000℃,中部>1200℃时装炉。
如不能做到,铸坯装炉时的表面温度应>250℃,当硅含量提高到3.25%~3.45%时最好>300℃,避免加热后出现晶界裂纹。
以MnS或MnSe为抑制剂的铸坯必须经高温加热,使铸坯中>1μm的粗大MnS固溶(主要存在于铸坯板厚方向的等轴晶中心区内),热轧过程中再以≤50nm的细小弥散状MnS析出。
按取向硅钢的成分,在平衡状态下MnS固溶温度约为1320℃(AlN固溶温度约为1280℃),因此GO铸坯加热温度规定为l350~1370℃。
MnS+A1N万案的Hi-B钢由于锰和碳含量高于GO,所以规定为1380~1400℃。
此时晶粒粗化到10~70mm。
为防止柱状晶反常长大,铸坯加热到约1250℃后,以>150℃/h速度快加热,使许多晶粒同时开始快速长大到彼此相碰,保证柱状晶尺寸小于30mm,以后不出现线晶。
实验证明,铸坯厚度方向中心区温度为1360℃时,晶粒100%长大,产品出现线晶;
铸坯厚度方向中心区温度为1345℃时,72%晶粒长大,产品无线晶。
因此,控制中心区温度为1310~1340℃保温15~70min。
按一般加热方式,铸坯下表面温度比上表面低,下表层(110){001}组分强度减弱,二次再结晶不完善,磁性不均匀,如果加热到1250℃以上,控制上下表面温差<70℃,最好<40℃,则热轧板上下表层(110){001}组分强度相近,二次再结晶完善。
3)粗轧
铸坯出炉后先除鳞,经4~6道粗轧和用立辊调整板宽。
每道压下率平均分配,第一道最好>30%来破坏柱状晶。
薄板坯厚度为30~40mm。
切头后进行精轧。
细小MnS是在精轧阶段析出,因此必须控制好粗轧后和进入精轧的薄板坯温度、时间和厚度。
一般采用大压下率高速轧制以保证薄板坯温度高。
对G0钢来说,进入精轧的温度控制在1160±
20℃。
对AlN+MnS方案Hi-B钢控制在≥1190℃,目的是在尽量少析出AlN。
4)精轧
开轧温度:
GO钢1160℃±
20℃;
Hi-B钢≥1190℃。
终轧温度:
GO钢950℃±
10℃;
Hi-B钢1000℃~1060℃。
卷取温度:
550℃。
精轧一般采用六机架四辊连轧机轧6道,每道压下率递减,轧制速度尽量快并增大冷却水量和提高冷却速度。
MnS从约1200℃开始析出,在1100~1150℃的γ相数量最多的温度下析出速度最快,<950℃基本停止析出。
在1200℃到950℃轧制时间控制企50~180s,在精轧过程中产生的大量位错成为MnS析出核心,促使MnS以细小弥散状更快和更均匀析出。
精轧后立即喷水冷却到约550℃卷取。
这可使碳化物弥散分布在晶粒内(针状Fe3C),有利于以后获得细小均匀初次晶粒。
轧后急冷也防止析出AlN。
4.2常化
GO钢热轧板一般不经常化处理。
以A1N为抑制剂时热轧板或最后冷轧前必须在氮气下高温常化。
常化的作用:
为析出大量细小AlN。
同时使热轧板组织更均匀和再结晶晶粒数量更多。
具体来说有:
a)常化前后织构无明显变化,通过同位再结晶使再结晶比例增多;
b)升温和保温时热轧板中Fe3C、珠光体、Si3N4和细小AlN固溶,淬在100℃水中后在晶粒内析出许多10~20nm细小ε—碳化物、Fe3C、Fe16N2和A1N。
金相组织为铁素体、珠光体和硬的贝氏体;
c)冷轧时细小析出物(主要为ε—碳化物)、固溶碳和氮以及贝氏体都可钉扎位错,使位错密度明显增高和更快地加工硬化,再结晶生核位置增多,初次再结晶晶粒细小均匀;
d)脱碳退火后沿晶界附近形成更多的{111}<
112>
晶粒,过渡带的{110}<
晶粒数量减少,也就是Σ9重合位向晶粒增多,同时AlN抑制能力加强,{110}<
,二次晶粒容易长大;
e)高温常化后采用二次冷轧法(第二次经大压下率冷轧)时,中间退火后原热轧板中粗大的{211}<
011>
~{100}<
晶粒减少,{110}和{111}晶粒增多,晶粒细小均匀。
因为常化后粗大晶粒中含更多的固溶碳和ε—碳化物,冷轧时位错密度更高,更容易再结晶。
再经大压下率冷轧和脱碳退火后{111}晶粒更多和{110}晶粒减少。
一般常化制度:
1050~1150℃(最好1100~1120℃)×
4~5min。
常化后严格控制开始急冷温度和冷却速度,因为10~50nmAlN就是在冷却过程中通过γ→α相变而析出。
一般在空冷到约900℃后喷水冷却。
常化温度、时间、开始快冷温度和冷却速度与钢中Als和氮含量有关。
如Als含量高,应慢冷;
Als含量低,采用快冷。
常化温度过高或时间过长,热轧板中细小MnS聚集粗化、使磁性降低。
4.3酸洗
常化处理后进行喷丸处理和在80~90℃的2%~4%HCl中酸洗1~2min,并将热轧带每边剪掉20~30mm准备冷轧。
4.4冷轧
热轧板常化和酸洗后应尽快冷轧,如果停放时间长,钢中固溶碳和氮析出形成不稳定第二相,使冷轧时碳和氮钉扎位错作用减弱,退火后再析出的AlN尺寸增大,磁性降低。
1)以AlN为主要抑制剂的大压下率冷轧法
a)预热:
冷轧前硅钢带一般预热到50~80℃。
b)道次压下率:
3%Si钢变形抗力大,一般在20辊轧机冷轧,经5~7道冷轧到0.30~0.35mm厚,平均每道压下率为25%~33%。
合适的压下率为82%~90%,最好为85%~88%。
c)冷轧时效:
为进—步降低铁损,现在生产上广泛采用冷轧时效工艺。
前几道使用粗面工作辊,每道经约30%大压下率冷轧,关闭润滑系统和快速轧制。
依靠轧制时的变形热将冷轧钢带温度提高到200~250℃。
冷轧时效的作用是使硅钢中固溶碳和氮数量增多,就是使钢中存在的不稳定碳化物和氮化物在时效处理时固溶。
冷轧时固溶碳和氮聚集在位错处,阻碍位错运动,位错群成直线排列,改变了正常滑移系统,促使形成更多的过渡带,冷轧后使再结晶织构发生变化。
同时由于固溶氮(约10ppm)更均匀分布在基体中,以后退火时新形成一批细小AlN加强抑制力。
2)以MnS为主要抑制剂的二次冷轧法
冷轧前钢卷温度控制在50~80℃。
b)第一次冷轧:
经3—4道冷轧,总压下率为60%~70%。
c)中间退火:
中间退火制度为850~950℃×
2.5~4.0min。
温度过低,初次再结晶不完善。
温度过高,初次晶粒粗大、使冷轧和脱碳退火后初次晶粒不均匀,不利于二次再结晶发展。
GO钢和MnSe十Sb方案Hi—B钢在二次冷轧之间在连续炉内进行中间退火。
目的是通过再结晶消除第一次冷轧产生的加工硬化,便于第二次冷轧并保证合适的压下率;
进行部分脱碳,将碳控制在合适范围;
使细小MnS数量增多。
中间退火前冷轧带在70~80℃的2.5%~3.0%NaOH水溶液中去油、刷洗和烘干。
中间退火时快升温到再结晶温度以上,使再结晶前回复和多边化过程消耗的储能减少、初次晶粒细小均匀和改善磁性,同时可缩短炉长和提高产量。
钢带入炉,先通过煤气明火焰高温加热段,炉温控制在1200~1250℃。
再经辐射管加热段,使钢带迅速升到规定温度。
采用的煤气必须是经过脱硫处理的富煤气(<0.05%S),这可减轻钢带表面氧化和不阻碍脱碳。
退火气氛为d.p.=20~30℃的20%H2+N2。
控制PH2O/PH2可控制脱碳程度和氧化程度。
一般要求中间退火时部分脱碳,使钢中保留120~400ppm碳,目标为250ppm碳。
退火后需快冷。
快冷可采用喷气或喷水冷却法。
950℃中间退火后从770℃在30s内快冷到100℃和150~250℃×
2~60s时效处理,或以<20s时间快冷到330℃,并在300~150℃之间冷却8~30s,在晶粒内析出10~50nm细小弥散碳化物(以{100}为习面的ε-碳化物)。
d)第二次冷轧:
冷轧道次为2~3道,总压下率为50%~55%。
e)冷轧时效:
采用MnS方案的GO钢和MnSe十Sb方案Hi—B钢在第二次冷轧过程中经约250℃时效处理,也可使磁性提高。
4.5脱碳退火
冷轧到成品厚度的钢带在连续炉内进行脱碳退火。
脱碳退火的目的是:
完成初次再结晶,使基体中有足够数量的(110){001}初次晶粒(二次晶核)以及有利于它们长大的初次再结晶织构和组织;
将钢中碳脱到0.003%以下,保证以后高温退火时处于单—的α-相;
发展完善的二次再结晶组织和去除钢中硫和氮,并消除产品的磁时效;
钢带表面形成致密均匀的SiO2薄膜(2~3μm厚)。
脱碳退火工艺:
退火前冷轧钢带用碱洗去掉油污并烘干,碱洗工艺和对连续炉的要求与中间退火相同。
快速升温到835~850℃×
3~4min,保护气氛为湿的20%H2+80%N2,d.p.=+35~45℃(水温60~65℃),PH2O/PH2=0.35~0.45,冷却段通干的20%H2+80%N2、d.p.<-20℃,PH2O/PH2=0.03,再喷氮气快冷。
4.6涂MgO隔离剂
涂MgO目的:
防止钢带成卷高温退火时粘接;
高温退火升到约1000℃时Mg0与钢带表面Si02氧化膜起化学反应(2Mg0+Si02→Mg2SiO4),形成硅酸镁玻璃膜底层;
高温净化退火时促进脱硫和脱氮反应。
MgO涂层通常与连续炉脱碳退火在同一条作业线上进行。
钢带脱碳退火和冷却到室温后通过涂层机组,辊涂或喷涂Mg0悬浮液并烘干。
4.7高温退火
高温退火的目的:
升温到850~1050℃通过二次再结晶形成单一的(110)[001]织构;
升温到1000~1100℃通过MgO与表面氧化膜中Si02起化学反应,形成Mg2SiO4(硅酸镁或铁橄榄石)玻璃膜底层;
在1200±
20℃温度下保温进行净化退火,去除钢中硫和氮,同时使二次晶粒吞并分散的残余初次晶粒,二次晶粒组织更完整,晶界更平直。
二次再结晶基本完成后,抑制剂的有利作用已结束并分解。
分解出的硫和氮本身对磁性和弯曲性有害,必须在高温退火时去掉。
通用的高温退火制度:
涂好MgO的钢卷通常放在电加热罩式炉的底板上并加内罩进行高温退火。
首先通入含O2<10ppm的氮气赶走空气,以约50℃/h速度升到350~450℃时MgO中Mg(OH)2分解放出化合水。
升到550~650℃时换成含O2<10ppm的75%H2+25%N2气并保温1~1.5h去除化合水。
测定气氛露点d.p.,控制d.p.<0℃,否则表面氧化膜中FeO和Fe2SiO4含量增多,对以后形成的玻璃膜质量不好。
然后以15~20℃/h速度升到850~950℃(以MnS为主的GO和Hi-B钢)或950~1050℃(以AlN为主的Hi-B钢)时发生二次再结晶。
升到约1000℃以上形成玻璃膜底层。
此时d.p.控制在<-7℃,最好事<-7℃(G0钢)或-10~+30℃(AlN为主的Hi-B钢)。
升到约1150℃时开始换为d.p.=-60℃和O2<10ppm的纯干氢,并在约1200℃保温约20h进行净化退火,排出的氢气d.p.≤-10℃,最好事≤-20℃。
断电后再换为75%H2+25%N2气冷到约700℃,再换为氮气冷到<300℃出炉。
在冷到约700℃时去掉外罩加速冷却。
罩式炉一般用石英砂双密封。
最好用结砂密封,因为它的热稳定性好,在高温下不会被氢气还原。
按MnSe+Sb或MnS+Sb方案生产Hi-B钢时大多采用二段式高温退火工艺,即800~920℃×
约50h+1200℃×
20h。
前段称为二次再结晶退火,后段称为净化退火。
4.8平整拉伸退火和涂绝缘膜
成卷高温退火后由于热应力作用使钢带变形,需进行平整拉伸退火。
平整拉伸退火主要目的:
通过水刷洗和70℃的5%H2SO4轻酸洗,去除表面残留的MgO和其它污物.使表面活性化;
烘干后涂绝缘涂料和在<500℃烘干;
在连续炉中氮气氛下加适当张力经约800℃平整拉伸退火和将绝缘涂层烧结好。
平整拉伸退火工艺:
一般在约800℃经0.25%~0.75%伸长率的拉伸退火可使钢带干整。
伸长率过大,二次晶粒变形,取向度和磁性变坏。
钢带平整张力在约3~7MPa。
绝缘涂层:
高温退火后形成的玻璃膜(硅酸镁)底层具有一定的绝缘性、而蚀性和在钢中产生拉应力。
可满足卷铁芯配电变压器的需要,不用再涂绝缘膜。
美国出售这种产品,并将玻璃膜称为C—2涂层。
其层间电阻>4Ω·
cm2/片。
对叠片铁芯的中大型变压器来说,C—2涂层的绝缘电阻还不够大,最后必须涂绝缘膜。
涂绝缘膜与平整拉伸退火在同一条作业线完成。
5新品种的进展
5.1含铜GO钢和含铜及锡的AlN+MnS方案Hi-B钢
近年来,提高硅含量和减薄产品厚度是进一步降低G0和Hi-B钢铁损的重要措施,但硅含量提高到上限和钢带减薄到0.20~0.23mm厚都使二次再结晶发展更加困难。
新日铁为了加强抑制能力、使二次再结晶完善,在0.18~0.20mm的G0钢中加0.15%~0.20%Cu,生产了Z8、Z7、Z6和Z54种新牌号。
在0.18~0.30mm厚AlN+MnS方案Hi-B钢中加入0.06%~0.15%Cu和0.06%~0.14%Sn,生产了Z7H、Z6H、Z5H以及0.18mm厚度新产品。
5.2含钼的MhSe(或MnS)+Sb方案Hi-B钢
川崎钢公司采用MhSe(或MnS)+Sb方案生产Hi-B钢(RG-H牌号),锑加入量为0.02%~0.05%。
锑沿品界偏聚,加强了抑制力,使第二次冷轧压下率提高到60%~70%,有防止表层抑制剂过早分解固溶的作用。
热轧板厚度为2.5~3.0mm。
脱碳退火后初次晶粒细小,(110){001}组分加强,二次再结晶温度降低,850℃×
20h二次再结晶退火后B8提高。
硒的扩散系数比硫小,在热轧过程中,MnSe比MnS需要更长时间冷却才能以细小弥散状质点析出。
但MnSe比MnS质点更细小,而且更稳定。
MnSe+Sb方案的Hi-B产品磁性比AlN+MnS方案的Hi-B产品磁性更低,也更不稳定。
特别是硅含量提高到3.1%以上和成品厚度减薄到0.30mm以下时,磁性更不稳定,热轧板易出现裂纹,产品表面缺陷增多。
为解决这些问题,在MnSe+Sb方案中加入0.013%~0.018%Mo。
加钢的作用是:
a)提高MnSe或MnS的抑制能力,热轧板表层(110)[001]组分强度比GO钢提高3倍,二次晶核数量增多,二次晶粒尺寸减小,位向更准确。
而且加钼不影响脱碳效果;
2)铸坯高温加热时,钼在表面富集可防止晶界氧化,或在表面附近形成细小Mo2S3阻止FeS的形成,防止晶界裂纹(硫或晒在α-Fe中固溶度低,在表面偏聚使热加工性能变坏),这对3.2%~3.5%Si钢更重要;
3)钼在表面富集可抑制氧化,减少Fe2SiO4和FeS形成量,形成的玻璃膜质量好。
5.3含铬、钛、铌、锌、锗和镍的取向硅钢
1)铬的作用:
铬与锡和锑的作用相似。
可细化二次晶粒,但使玻璃膜质量降低。
提高AlN+MnS方案中Als量可降低热轧温度和在常化后进行快冷(淬入60℃水中),二次晶粒小,但二次再结晶不易完善。
如果Als量提高到0.028%~0.031%,并加O.08%~0.11%Cr和0.08%~0.10%Cu,二次再结晶完善,0.3mm厚板的P17≤1.0kW/kg,B8≈l.92T,达到Z6H水平。
0.23mm厚板(加0.004%Sn)的P17=0.89W/kg,玻璃膜质量改善。
2)钛、铌的作用:
在MnS方案中加0.005%~00.188%Ti和0.002%~0.012%Nb,形成TiN和NbN加强抑制力。
热轧板经950~1000℃×
2~3min常化和一次冷轧到0.3mm厚时,二次再结晶完善,B8≈l.89T,P17=1.18~1.25W/kg。
在AlN+MnS+Cu+Sn方案中,加0.004%~0.005%Ti,可使脱碳退火后表面40μm区域(110)极密度提高,二次晶粒细小,磁性提高。
0.3mm厚板的P17降低0.13~0.20W/kg,B8提高约0.05T。
推想是因钛与碳和氮形成TiC和TiN,加强了抑制力。
Ti>0.01%时形成TiN过多,使AlN量减少,成品出现混晶。
6新工艺的进展
6.1热轧
粗轧改变压下率使粗轧后薄板坯前段厚度较薄,后段厚度较厚并且厚度连续性变化,可使大铸坯制成的成品长度方向磁性均匀。
因为这保证了粗轧时间短的薄板坯前段发生再结晶而防止出现线晶,也防止薄板坯后段由于温度低而使精轧时析出的抑制剂弥散度变坏。
当铸坯烧损量W与粗轧开轧温度T(℃)满足关系式T=-50×
W+(1275±
75)时,二次再结晶完善。
连续测定烧损量并据此调整粗轧开轧温度,可保证产品磁性稳定。
铸坯出炉到粗轧结束期间,由于板宽方向的两边温度低于中部,精轧时析出的MnS更粗大,二次再结晶不易完善。
如果在此阶段将两边l00mm宽内用绝缘材料保温或经感应加热或直接通电加热,使边部温度比中部高50℃以上,并经5~100mm宽度压下,破坏边部伸长晶粒,促进再结晶,可使板宽方向的磁性更均匀。
6.2铸坯直接热轧法
200~250mm厚铸坯切断后用罩盖上并及时热送到热轧厂,铸坯表面温度在1200~1250℃。
铸坯端部冷却快,经感应快加热到1150~1200℃,然后直接热轧,这可节省大量热能、无烧损,成品表面无缺陷。
MnS方案铸坯直接进行热轧,控制精轧的开轧温度>900℃,析出细小MnS,成品二次再结晶完善。
6.3薄铸坯直接冷轧法
为了省掉高温加热和热轧工序以及生产≤0.3mm厚度钢带,新日铁按A1N+MnS方案的成分,采用双辊快淬法制成1~4mm厚的薄铸坯。
调整冷却条件(冷却辊压力和二次冷却速度)来控制铸坯厚度。
辊子压力控制在490MPa以上。
铸坯厚度方向中心区冷却速度>50℃/s,快速凝固后,在1300~900℃之间的冷却速度(二次冲却速度)>10℃/s时(相当于弱水冷却),产生再结晶晶粒,为混乱位向的铸态组织,并获得细小MnS和AlN析出质点。
铸坯在高温常化后经一次或二次冷轧法(>80%压下率)都可使二次再结晶完善和B8提高。
6.4铸坯感应加热工艺
铸坯中心硫偏聚区(可