铝电解炭素工艺教程Word文档下载推荐.docx
《铝电解炭素工艺教程Word文档下载推荐.docx》由会员分享,可在线阅读,更多相关《铝电解炭素工艺教程Word文档下载推荐.docx(18页珍藏版)》请在冰豆网上搜索。
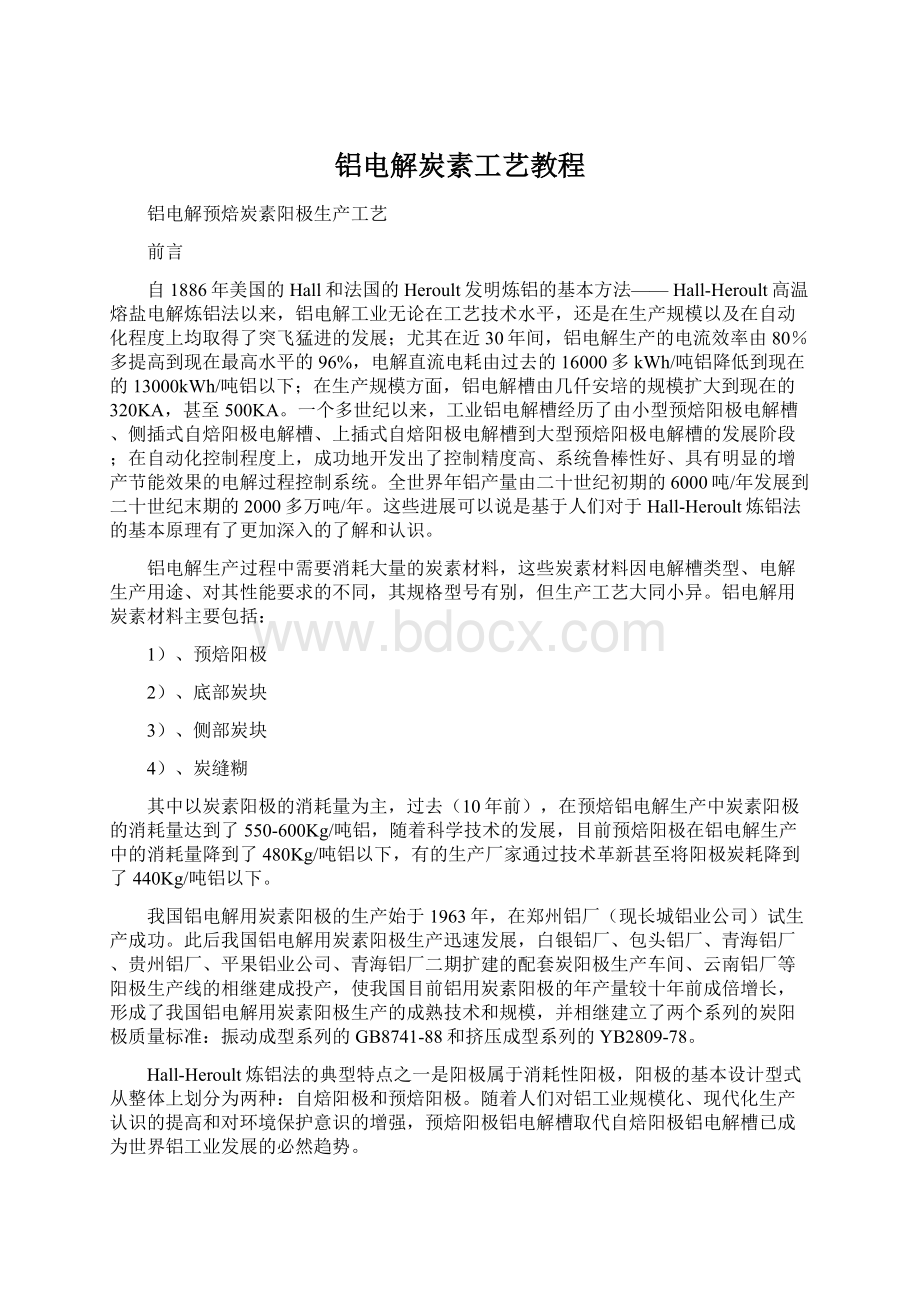
表1国际公认的预焙阳极性能指标
项目
单位
指标范围
备注
体积密度
电阻率
抗压强度
抗弯强度
热膨胀系数
导热系数
透气率
CO2反应余量
空气反应余量
杂质:
S
V
Si
Fe
Na
结构
g/cm3
Ωmm2/m
Mpa
10-6/K
W/mK
Npm
%RDC
%
ppm
\
1.53-1.58
52-60
40-48
5-12
3.5-4.0
3.5-4.5
0.5-1.5
84-92
70-85
1.2-2.4
80-350
100-300
100-500
250-600
越高越好
尽量控制低的电阻率
越低越好
剩余越多越好
没有掉块和裂纹
表2我国现行的电解铝用(预焙)炭阳极性能指标
牌号
灰分(%)
≤
(Ω·
mm2/m)
I抗压强度
≥(N/mm2)
≥
(g/cm3)
真比重
TY-1
0.5
55
29
1.5
2.0
TY-2
1.2
63
第二节原料
铝电解预焙炭素阳极的生产原料包括阳极主体组分(又称骨料)和粘接剂两大部分。
2.1骨料
1)种类:
石油焦。
国内炭素厂普遍采用延迟石油焦(简称延迟焦)。
2)来源:
炼油厂的炼油渣经过高温加热,采用延迟焦化工艺所得到的产品。
(焦化工艺分延迟焦化和流化床焦化,延迟焦化生产的焦因其孔隙度高而特别适用于制备铝电解用炭素阳极)
3)质量评价指标:
一般用灰分、硫分、挥发分和1300℃煅烧后的真密度(真比重)来衡量,具体指标见表3。
表3我国延迟石油焦的质量标准
一号
二号
三号
A级
B级
水分
(不大于)
3.0
灰分
0.3
0.8
硫分
1.0
挥发分
10
12
15
16
18
2.2粘接剂
沥青。
电解用炭素阳极一般用煤沥青做粘接剂。
是由钢铁工业烟煤制取焦炭时产出的煤焦油经高温分馏后的残渣,是多种碳氢化合物的混合体。
3)作用:
粘接固体炭粒(骨料),构成具有一定塑性的炭糊,并且在炭糊焦化过程中渗入骨料之间,使阳极具有足够的机械强度。
4)性能指标:
包括固定碳、挥发分和灰分等。
(固定碳的定义:
沥青在隔绝空气的条件下,加热到800℃,干馏3小时,排除全部挥发分后残留的总碳量,也称结焦残碳值)
沥青的主要性能指标见表4。
表4预焙阳极粘接剂沥青的性能指标
类别
中温沥青
高温沥青
软化点(℃)
挥发分(%)
结焦残碳值(%)
甲苯不溶物(%)
75-95
65-75
52-55
17-25
95-120
47-49
65-68
44-48
第三节预焙炭素阳极的生产工艺及设备
目前炭素厂主要的生产工艺流程如图1。
3.1原料的准备和煅烧
3.1.1原料的准备
包括内容:
原料的验收入库和煅烧前的准备。
进厂石油焦首先通过带网格的受料漏斗进行筛选,其中小于300mm的料进粗碎设备进行破碎,而大于300mm的料需经人工打碎后再进漏斗过筛。
粗碎设备:
主要有齿式对辊破碎机或颚式破碎机。
其技术要求是:
石油焦破碎完毕后粒度控制在50-70mm。
进厂的沥青经破碎后送入沥青熔化槽进行熔化,使其成为液体沥青。
一般破碎沥青的设备多为环锤式破碎机。
3.1.2石油焦煅烧
1、煅烧的目的:
1)、排除原料中的水分和挥发分;
2)、促使单体硫气化和化合态硫的分解;
煅烧的结果:
提高原料的真密度、机械强度、导电性和抗氧化能力。
2、煅烧的主要技术参数
控制煅烧带温度不低于1250℃,不高于1350℃。
3、煅烧设备
煅烧设备主要有回转窑、罐式煅烧炉、电热煅烧炉等三种,目前,大多数炭素厂采用回转窑,在此重点介绍回转窑。
1)回转窑的优缺点:
优点:
结构简单,产能大,生产机械化程度高,投资相对少,容易清扫。
缺点:
原料的烧损比较大(一般有10%左右)。
2)回转窑的结构
主体:
回转窑和冷却机组成
回转窑:
窑尾装置、窑体、窑头装置、燃烧装置、二次风装置、引风机、除尘设施及排烟管路、烟囱等。
冷却机:
结构类似于回转窑窑体,但简单许多,其作用是:
一方面冷却物料,另一方面也可空气,节省热能。
石油焦沥青
粗碎破碎
煅烧
中碎熔化
筛分分级
球磨
粗粒中粒细粒球磨粉残极生碎
预热
混捏
成型
焙烧
图1预焙阳极生产流程简图
预焙阳极
3)物料煅烧程序及工艺参数
原料石油焦(俗称生焦)经窑尾流入回转窑,在窑内与逆流的热空气接触加热,由于窑体是倾斜转动,物料随窑体转动的同时向窑头移动,并依次经过窑内的预热带、煅烧带、冷却带,最后从窑头流出进入冷却机。
预热带:
最高温度:
800-1100℃,进料口温度:
500-600℃。
热源:
从煅烧带流过的热烟气。
物料变化:
脱水并排出挥发分及硫分。
煅烧带:
1250-1350℃,物料可加热到1200℃以上。
重油或煤气燃烧,二次风助燃。
生焦焦化,石油焦形成碳原子的平面网格,呈两维空间的有序结构排列,达到增加石油焦的物化性能(如电阻率、真密度、机械强度等)的目的。
冷却带:
窑头温度:
小于1000℃。
物料在此段自然冷却。
采用喷水方式对物料进行强制冷却。
冷却机出口煅后焦温度:
小于60℃。
3.2筛分与配料
包括工序:
筛分、球磨、配料。
3.2.1筛分
1、目的:
将煅后焦破碎分成不同粒级,以符合科学配料的要求。
2、筛分设备:
一般在炭素厂多使用震动筛,此外还有回转筛、摇摆筛等。
3.2.2球磨
将部分煅后焦磨成细粉,以满足配料要求。
2、设备:
球蘑机
3、工作原理:
采用某种介质(如钢球),在筒体内与物料一起旋转,介质在运动中将物料磨碎。
3.2.3配料
1、定义:
将不同粒级的焦粒(包括粉料)按一定的比例配合。
2、目的:
为了得到堆积密度较大而气孔率较小的炭素材料。
3、配料技术参数
对于预焙阳极,其生产中的基本配方为:
粗颗粒料(6-12mm):
14-20%;
中颗粒料(3-6mm):
8-10%;
细颗粒料(-3mm):
45-54%;
粉料:
(-0。
074mm):
22-25%;
残极:
1-30%;
生碎:
0-7%;
粘接剂沥青:
14-17%
4、配料设备:
料仓和电子秤。
3.3成型
预热、混捏、成型
3.3.1预热
将各种粒级的骨料混合均匀并加热,为混捏工序打基础。
2、技术参数:
要求骨料从预热螺旋出口的温度要达到140-160℃。
3.3.2混捏
将各种粒级的骨料与粘结剂在一定温度下搅拌、混合,从而获得塑性糊料。
1)物料混合均匀;
2)不同颗粒达到合理堆积,提高密实度;
3)粘接剂渗透到各种骨料的空隙中,提高了物料的粘接性和密实度。
3、混捏设备
双(单)轴搅拌混捏锅:
是间歇生产方式,比较适合于规模不大的炭素厂。
双轴搅拌连续式混捏机:
是连续生产方式,适合于规模较大的炭素厂。
目前混捏设备的加热方式(热源)主要是蒸汽或电热。
4、主要技术参数
该工艺的主要技术参数是混捏温度和混捏时间。
混捏温度应该选定比沥青的软化点高出50-80℃。
铝用预焙炭素阳极一般选用高温改质沥青做粘接剂,其软化点为110℃左右,则混捏温度应该选择160-180℃,且必须达到要求。
因为温度高,沥青粘度小,流动性好,浸润效果好,同时容易渗透到空隙中去;
反之,温度不够,沥青粘度大,混捏时搅刀转动费力,粘接剂与骨料难以混合均匀,影响阳极的物理性能。
当然,温度也不能过高,因为温度太高,沥青受热开始变化,部分轻质组分逐渐挥发,还有部分组分手空气中氧的作用,发生缩聚反应,使糊料的塑性变差,导致挤压成型的成品率降低。
粘接剂沥青是在加入混捏机前,必须先经过预热,且温度高于混捏机内的物料温度,一般要求大于170℃。
至于混捏时间,一般在40-60分钟范围内,但要视具体情况而定。
在实际生产中可遵循如下规则:
1)沥青软化点稳定,混捏机温度稳定,混捏配料用量符合工艺要求,混捏时间不应延长或缩短;
2)沥青软化点变化时,依沥青粘接剂的软化点高低适当改变混捏时间;
3)混捏温度低时,可适当延长混捏时间,反之,则可适当缩短。
4)混捏细粉料时,可适当延长混捏时间;
5)加入生碎料时,也要适当延长混捏时间;
6)混捏过程因故停机,应保温并延长混捏时间;
7)若有特殊添加剂的加入,改变一般常规产品的混捏制度,也要考虑混捏时间的变化。
3.3.3成型
成型是将混捏好的炭素糊料用加压设备压制成具有一定形状和具有较高密度的半成品(生块)。
2、成型设备
在炭素材料生产中常用的成型方法有挤压法和模压法,还有振动成型法、等静压成型法和捣固法。
铝用炭素阳极的成型方法多用振动成型法,使用的设备为振动成型机。
3、成型原理
利用高速振动(每分钟达2000-3000次,振幅为1-3mm)的振动机组,使装在成型模内的糊料处于强烈的振动状态,使炭糊获得相当大的触变速度和加速度,在颗粒间的接触边界产生应力,引起颗粒的相对位移,使糊料内部空隙不断降低,整体密度逐渐提高,达到成型的目的。
4、成型工艺及技术参数
每一块炭素阳极的成型生产周期包括固定成型模、加料、振动、脱模等操作过程。
在生产中常采用一边加料,一边振动的操作方法,当料加到一定的高度即压上重锤,同时继续振动,振动时间视阳极规格的大小而不同。
如用于160KA预焙槽的阳极炭块振动成型时间为1分钟左右。
振动时间结束即脱模,阳极生块制备完毕。
3.3生块焙烧
3.3.1焙烧工艺的作用
焙烧是影响炭素制品物理化学性能很大的一道关键工序。
它是将压型后的炭块在隔离空气的条件下进行热处理,使粘接剂转变为焦炭。
由于生块中的沥青牢固地包裹在炭素颗粒之间的过度层,当高温转化为焦碳后,就在半成品中构成界面炭网格层,具有搭桥、加固的作用。
经过焙烧的炭素阳极其机械强度稳定,并能显著提高其导热性、导电性和耐高温性。
焙烧过程是一个复杂的过程,伴随着许多化学变化,影响焙烧工艺的关键技术参数是焙烧温度。
3.3.2焙烧过程中的物理化学变化
一般情况下,在焙烧过程中,预焙阳极受热将发生一系列的变化。
该变化大致分为四个阶段:
第一阶段:
当阳极加热到200~250℃时,由于粘接剂沥青开始软化,导致阳极坯体变软,体积增大,但质量并不减少;
第二阶段:
随着焙烧温度的继续增加,粘接剂沥青中的易挥发组分挥发逸出。
在温度400℃左右,沥青的粘结能力降低;
第三阶段:
在500-600℃时,阳极开始硬化,同时体积收缩,导电性与机械强度增加;
第四阶段:
焙烧温度超过600℃,挥发分已基本排出,再继续加热,阳极本身的化学变化逐渐停止,外部与内部收缩微弱。
但阳极的真密度、气孔率以及强度、硬度和导电性继续增加,阳极颜色由黑色变为灰色。
3.3.3、焙烧工艺及设备
1、焙烧曲线
阳极炭块的焙烧过程是通过一个从升温到降温的温度制度的实行而完成的。
因此,在焙烧工序开始前必须制定一个合理的焙烧曲线。
确定焙烧曲线的依据:
A、焙烧炉型;
B、焙烧产品的规格;
C、焙烧操作水平。
2、焙烧工艺
焙烧工艺因炉型不同而有所区别,但基本工序包括:
装炉、点火升温、保温、冷却、出炉、清砂、检测。
上述工序都不难理解,只是对清砂工序稍作解释。
在炭素阳极被焙烧的过程中,因粘接剂沥青的软化,有可能使炭素阳极变形,因此,在生块入炉时,在其周围缝隙中填满一些细颗粒的炭素填充料(称其为焙砂)来支撑阳极,同时,填充料还可以阻止炭块与空气接触,以免在高温焙烧过程中被空气氧化。
在阳极焙烧完毕出炉时,阳极表面会附着一些填充料颗粒,须对其进行清除才能成为最终的焙烧熟块。
3、焙烧设备
铝用炭素阳极的焙烧设施有隧道窑、导焰窑和多室环式焙烧炉(也称为轮窑)等,对于当前规模化、集团化生产的企业,采用多室环式焙烧炉比较合算。
1)多室环式焙烧炉的工作特点
多室环式焙烧炉分封闭式(带活动炉盖)和敞开式(不带炉盖)两种。
多室环式焙烧炉属于连续作业炉,而就每个单体炉室而言是周期性的循环作业炉。
多室环式焙烧炉的优点是:
焙烧产品质量较好,热效率比导焰窑高,装出炉机械化程度高,从整炉来看,生产连续性强,产量高。
多室环式焙烧炉的缺点是:
基建投资大,厂房结构要求高,不适合小规模生产。
多室环式焙烧炉的炉室数有:
18室、20室、30室、32室等几种规格。
例如:
广西平果铝业公司炭素厂使用的是18室环式焙烧炉,其中预热焙烧5室,冷却8室,装炉、出炉各1室,密封2室和检修1室。
焙烧炉使用的燃料有煤气和重油。
2)多室环式焙烧炉的工作原理
多室环式焙烧炉从整体上可划分为三个带:
预热带、焙烧带和冷却带。
如图2所示,以32室环式焙烧炉为例,它是由32各单独的炉室彼此串联组成,需要焙烧的炭素阳极装入炉室内,用烟气间接加热,为了使烟气能从一个炉室进入到另一个炉室,在相连的炉室之间设有连接烟道,烟气通过烟道的顺序可以用闸门来控制。
图2中的的32个炉室按两排平均布置,每排16个,燃烧系统也分为两组。
在第一个系统中燃料由燃烧装置引入9#和10#炉室,并在此与空气混合后燃烧。
9#和10#达到最高温度(这样的炉室称为火室)。
燃烧的产物并不立即排入烟囱,而是依次通过一系列炉室,即图中11#至16#炉室,预热装入这些炉室的制品后,以较低的废气温度排出,燃烧气体所经过的炉室数量,应该使排出的废气温度降到100-150℃。
燃烧所需的空气,应经过装有焙烧制品的各炉室如图中的5#至8#进行预热,这些炉室刚刚经过高温阶段,其中制品温度接近1000℃,经过这些炉室的空气既冷却了制品,有达到了预热的效果,使得它们在进入“火室”前已被加热到700-800℃,经过冷却后的制品温度应低于制品的氧化温度,就可以出炉,即4#、3#炉室为空炉室,可以进行维护检修,1#、2#炉室为装料炉室。
在9#炉室焙烧结束后,将燃烧架向前移动一个炉室,即10#与11#炉室进入“火室”,焙烧系统相应向前移动一个炉室,5#炉室充分冷却后,又可以与焙烧系统切断,进入出料阶段。
此时相应的排气烟道也应向前移一炉室再通向烟囱。
如此依次按闭路循环,连续向前推进。
同样的操作也在第二个燃烧系统中完成。
从以上操作可以看出,在环式焙烧炉的生产操作中既利用了燃烧气体的热量,也利用了正在冷却的炭素阳极散发的余热,故热量的利用率比较合理。
在生产循环过程中,炭素阳极始终处于静止状态,只是带燃烧系统的火焰架及烟囱抽气装置按生产进程移动,故这种炉又称为移动火焰带的燃烧炉。
多室环式焙烧炉分为三个带:
预热带、焙烧带和冷却带,每个炉室都要依次经过烟气预热、焙烧和最后用助燃空气慢慢冷却阶段。
32室的焙烧炉共有25个炉盖,除加热室要加盖炉盖外,开始进入冷却阶段的炉室为了保温,提高制品的质量也要加盖炉盖。
装卸料与维修的炉室是不需要炉盖的,炉盖可以用车间的起重天车吊装。
与焙烧炉配套要设置有烟气净化系统,因为烟气中除少量粉尘外,主要含有焦油,据测定焦油质生成物含量可达0.8g/Nm3烟气,这种生成物经烟囱排入大气中冷凝,以焦油滴形式散落而污染周围环境,一台炉每昼夜可产焦油250—300公斤,这些焦油能使周围周围植物枯死,焦油的异臭也破坏环境卫生,但焦油又可引入燃烧系统,作为补充燃料,因此生产必须回收焦油,焦油的回收系统是在烟囱排放烟气之前加设用水喷淋的冷却塔,大部分焦油经冷却喷淋回收,其次再经电收尘器,回收剩余的焦油,经冷却塔和电收尘器后的烟气可以达到排放的要求。
空气重油燃烧装置火焰架抽气烟囱
1
装
料
2
3
待
修
4
出
5
冷
却
6
7
8
9
加
热
11
13
14
32
31
30
28
27
26
25
24
23
22
21
20
19
17
抽气烟囱火焰架重油燃烧装置空气
图2环式焙烧炉操作示意图
焙烧炉的温度是预先根据工艺条件确定的,在制定温度制度时,应考虑焙烧炉的结构特点,实现焙烧炉的温度制度,这是一项相当复杂的任务,因为必须确定用几个炉室点火,几个炉室预热,几个炉室冷却。
燃烧过程可以这样进行,一个炉室通煤气(点火)后面的炉室利用燃烧产物的热量预热,从冷却室来得空气已经预热,可以保证煤气燃烧,在生产中为了达到焙烧温度不仅在头一个炉室加煤气燃烧,也可在第二和第三炉室加煤气燃烧,使用重油为燃料时,还可加入回收的焦油以节省燃料消耗。
预热炉室的数量通常为6—8室,炉室少,会降低焙烧炉产能,同时势必将温度为200℃以上的烟气排入大气,造成浪费,有时安排10个或更多的炉室预热,但由于从一个火室出来的载热体不足,而必须在辅助室点火,结果会降低热空气的利用率,从而降低了热效率。
冷却炉室为3—4个。
有时可为5个,必须待电极制品温度冷却到300℃时,才能将此炉室切断。
对焙烧条件不仅要确定升温曲线