塑料碗模具毕业设计Word下载.docx
《塑料碗模具毕业设计Word下载.docx》由会员分享,可在线阅读,更多相关《塑料碗模具毕业设计Word下载.docx(27页珍藏版)》请在冰豆网上搜索。
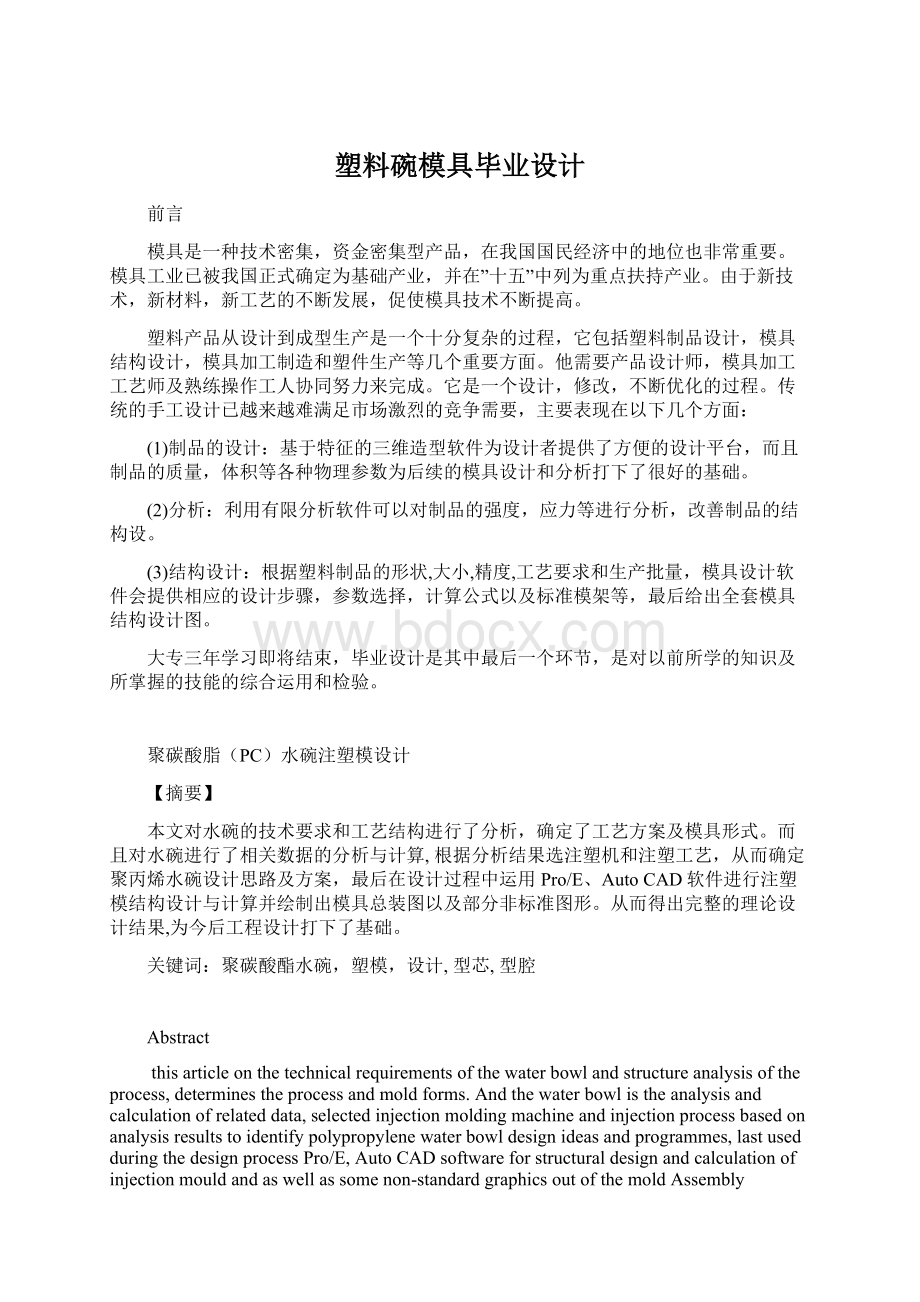
图1-1-1塑件
2.塑件成型工艺分析
2.1基本特点[3]
聚碳酸酯是一种性能优良的热塑性工程塑料,它在工程技术中的应用广泛,仅此于聚酰胺,它韧而刚,抗冲击性在热塑性塑料中名列前茅。
抗蠕变、耐磨、耐热、耐寒。
成型零件可达到很好的尺寸精度并在很宽的温度范围内保持其尺寸的稳定性。
脆化温度-100℃以下,长期工作温度达120℃。
聚碳酸酯吸水性较低,并能在较宽的温度范围内保持良好的电性能。
耐室温下的水、烯酸、氧化剂、还原剂、盐、油、脂肪烃,但不耐碱、胺、酮、芳香烃,并有良好的乃气候性。
成型收缩率恒定
为0.5﹪-0.8﹪,容易得到精度高的塑件。
其最大的缺点是塑件易开裂,耐疲劳度较差。
用玻璃纤维增强聚碳酸酯,可克服上述缺点,使聚碳酸酯具有更好的力学性能,更好的尺寸稳定性,更小的成型收缩率,并提高了耐热性,降低了成本。
2.2塑件材料成型性能[3]
聚碳酸酯虽然吸水性小,但高温时对水分比较敏感,所以加工前必须进行干燥处理,否则会出现银丝、气泡及强度下降现象;
聚碳酸酯熔融温度高,熔融粘度大,流动性差,所以,成型时要求有较高的温度和压力,且其熔融粘度对温度比较敏感,所以一般用提高温度的办法来增加熔融塑料的流动性。
当冷却速度较快时,其制件容易产生内应力。
聚碳酸酯成型收缩小,容易得到精度高的零件。
聚碳酸酯可采用注射、挤出、吹塑、真空成型等方法生产塑件制品。
注射成型时,浇注系统尺寸应粗大。
其制品还应进行退火处理。
2.3零件的工艺性分析
制件的最大尺寸为160mm,属于中小型制件,比较适合采用一模一腔的模具结构。
由于制件外观制造要求,浇口应该选取在水碗的底部。
为了保证水碗的壁厚一致,模具设计成4根导柱的形式;
并且还要对顶出板和顶杆固定板进行导向。
2.4塑件成型工艺参数的确定[3]
表2-4-1塑件成型工艺参数。
密度
1.20g∕cm3
模具温度
90-110℃
收缩率
0.5%-0.8%
注射压力
110-140Mpa
溢边值
0.06mm
注射时间
0-5s
保压时间
:
20-80s
喷嘴温度
240-250℃
冷却时间
20-50s
料筒温度
前段270-300℃、后段260-290℃
⒊成型设备的选择及校核
3.1注射机的初选
3.1.1计算塑件的体积[1]
根据制件的三维模型,利用三维软件(pro-e)直接求得塑件的体积为V1=59638mm3,其中浇注系统凝料体积为V2=2308mm3故一次注射所需的塑件的总体积为V=61946mm3。
3.1.2计算塑件的质量[3]
取PC的平均密度为:
ρ=1.20g/cm3,则塑件的质量为:
M1=ρv1=59.63X1.20≈72(g)
浇注系统凝料质量为:
M2=Ρv2=2.33X1.20≈2.8(g)
塑件和浇注系统凝料总质量为:
M=M1+M2=72+2.8=74.8(g)
3.1.3选用注射机[3]
根据总体积即初步选取SXY-300型螺杆式注射机。
表3-1-1注射机的主要参数
理论注射量
320cm3
注射压力
77.5Mpa
注射行程
150mm
锁模力
1500KN
最大成型面积
90mm
最大开模行程
340mm
喷嘴圆弧球半径
12mm
模具最小厚度
285mm
模具最大厚度
355cm3
动,定模固定板尺寸
620mmX520mm
3.2注射机的终选
3.2.1模具注射量的校核[3]
注射量的校核公式是:
nm+m1≤Kmp
式中:
n-型腔数目
mp-注射机允许的最大注射量﹙g或cm3﹚
m-单个塑件的质量或体积﹙g或cm3﹚
m1-浇注系统凝料及飞边质量或体积﹙g或cm3﹚
k-注射机最大注射量利用系数,一般K=0.8
如上所述,塑件及浇注的总体积V=61.9cm3(飞边体积相对特小,可忽略不计)。
Kmp=0.8×
320=256cm3
nm+m1=61.9﹤256
即nm+m1≤Kmp﹙满足条件﹚
3.2.2模具注射压力的校核[3]
注射压力校核公式:
Pmax≥P
Pmax-为注射机最大注射压力(MPa)Pmax=119MPa
P-为塑件成型时所需注射压力(MPa),一般取P=40-120MPa
如上所述:
Pmax≥P﹙满足要求﹚
3.2.3锁模力的校核[3]
锁模力的校核公式:
Fs=P(nA+A1)<
Fp
Fs-高压塑料熔体产生的胀模力(N)
Fp-注射机的公称锁模力(N)
n-模具型腔数目
A-单个塑件在分型面上的投影面积﹙mm2﹚
A1-浇注系统在分型面上的投影面积﹙mm2﹚
P-型腔内熔体压力取P=40MP
分别计算A和A1的数值:
A=πr2=3.14Х802=20096mm2
主流道截面直径取D1=5mm,D2=7mm
所以主流道在分型面上的投影面积A2=π(D2∕2)2=3.14×
3.52=38.465mm2。
一般主流道长度L不超过60mm。
因为采用点浇口且无分流道,所以浇注系统在分型面上的投影面积
A1=A2=38.465mm2
代入以上数据得:
Fs=P(nA+A1)=40×
﹙20096+38.465﹚
=80544N≈805KN<
即:
Fs=P(nA+A1)<
Fp(满足要求)
3.2.4开模行程的校核[3]
模具开模行程的校核公式为:
H1+H2+a+(5-10)≤S
S-注射机的最大开模行程(mm)
H1-塑件脱模所需的推出距离(mm)
H2-塑模板之间的最大开距S件高度﹙不包括浇注系统高﹚(mm)
a-取出浇注系统凝料所需的定模座板与中间板之间的距离﹙mm﹚
根据塑件的尺寸取H1=55mm,H1=60mm,a=60mm
代入数据:
H1+H2+a+(5-10)=55+60+60+6=181mm≤340mm
即:
H1+H2+a+(5-10)≤S(满足要求)
3.2.5型腔数目的确定[3]
考虑到技术、经济、质量、设备、批量等多方面的因素,按注射机的额定锁模力确定型腔数目n,有
npA≤Fp_PA1
式中Fp-注射机的额定锁模力(N)
A-单个塑件在分型面上的投影面积(mm2)
A1-浇注系统在分型面上的投影面积(mm2)
P-塑件熔体对型腔的成型压力(MPa),其大小一般是注射压力的80%.
代入数字得n×
62×
20096≤1500000-62×
38.465
即n≤12
本套模具采用一模一腔,即n=1(满足要求)
⒋分型面选择及浇注系统的设计
4.1分型面的选择[3]
根据分型面应设在最大水平截面的原则,该塑件的分型面应该选在水碗的口部,即水碗的口部顶端水平面,如图4-1-1中的B-B。
由于采用点浇口,要取出浇注系统凝料,所以又设一分型面,如图4-1-1中的A-A。
图4-1-1分型面
4.2浇注系统的设计[3]
因为水碗的外表面不可以留下浇口的痕迹,所以之可以在水碗的底部浇注,且采用圆锥浇道点浇口。
4.2.1主流道的设计[3]
SZY-300型注射机喷嘴有关尺寸:
喷嘴孔直径:
d1=2mm喷嘴圆弧球半径:
R1=12mm.
为了便于凝料从主流道中拔出,主流道设计成圆锥形,由于PC熔体黏度高,主流道锥角取α=3°
-6°
,内壁表面粗糙度Ra小于0.8um.设计主流道截面直径时,应注意喷嘴轴线和主流道轴线对中,为了补偿对中误差并解决凝料的脱模问题,主流道进口端直径应比喷嘴直径大0.5-1mm,主流道进口端与喷嘴头部接触的形式:
一种是平面,另一宗是弧面,由于平面连接密封时需要有很高的压力,实际中很少采用,一帮情况下是采用弧面(球面)接触定位,通常主流道进口端凹下球面半径R2比喷嘴球面半径R1大1-2mm,凹下深度3-5mm。
通常主流道进口端直径应根据注射机喷嘴孔径确定,取D1=5mm,D2=7.5mm(课本P132表3-3)主流道与分流道结合处采用圆角过渡,其半径R为1-3mm,以减少料流转向过渡时的阻力,在保证塑件成型良好的前提下,主流道的长度L应尽量短,为了减少废料及熔体压力损失,一般主流道长L不超过60mm。
常用的主流道衬套有A,B两种。
B型是为了防止衬套在熔体反压力作用下推出定模,使用时用固定在定模板上的定位圈压住衬套大端台阶,再用2-4个M6-M8的螺钉将定位环紧固在定模座板上,主流道衬套选用T8类优质钢材,热处理后硬度为53-57HRC,衬套长度与定模版配合部分的厚度一致,但主流道出口处的端面,不得凸出于分型面,衬套与定模板之间的配合采用H7/m6。
主流道及主流道衬套的形状尺寸如图4-2-2。
图4-2-2浇注系统
4.2.2浇口的设计[3]
一般情况下多采用长度较短(0.5-2mm)而截面又很狭窄的小浇口。
浇口截面的厚度通常可取塑件浇口处壁厚的1/3-2/3(或0.5-2mm)。
浇口的截面宽度b,矩形截面的浇口对于中小型塑件通常取b=(5-10)h,对于大型塑件取b>
10h。
浇口长l=(0.5-2)mm。
⒌导向机构的设计
5.1动定模之间的导向机构设计[2]
水碗模具必须要保证其位置精度高,只有这样才可以生产出壁厚均匀的水碗。
所以要采用4根导柱导向。
由于该模具采用两次分模,所以要在导柱上设置限位孔。
同时,导套的相应位置也应设置小孔。
具体模具结构如图5-1-1所示。
图5-1-1动定模之间的导向机构
5.2推出机构的导向机构设计[2]
为了确保水碗底部的壁厚均匀,使顶杆的顶出过程平稳,顶杆不至于弯曲或卡死,应用导向机构,具体形式如图6-1-1所示。
这种导向机构是采用两根导柱的,安装在中心线上,并对动定模其支承作用。
⒍冷却和排气系统的设计
6.1冷却系统的设计[3]
水碗是一种较大的中小型塑料制件。
该制件的壁厚较小,并且分布均匀,对该塑件的冷却造成了不便。
仅仅通过定模板上的冷却水管,不能使制件均匀冷却,
并且冷却速度较慢。
可以在动模板上的型芯中做水碗的内部冷却系统,来改善其冷却系统的不足。
图6-1-1推出机构的导向机构
为了使模具冷却更快,且制件的不同部位冷却速度相等,必须采用较为复杂的冷却系统。
该冷却系统可以分成两部分。
一部分是凹模型腔板上的冷却系统。
该部分是环绕凹模型腔一周的一个正方形的教浇道,具体如图6-1-2所示。
另一部分是动模板和型芯上的冷却系统,是由动模板的两条与分型面平行的水道、与上述平面上的水道垂直相交的两条短水道和型芯上的环形凹槽以及橡胶垫片等组成。
水道的直径都是10mm,水道的外端口上都有螺纹,螺纹大径为12mm,螺纹深30mm,并且安装有水嘴、水管和水塞。
水嘴规格为M12。
6.2排气系统的设计[3]
型腔内气体的来源,除了型腔内原有的气体外还有因塑料受热或凝固而产生的低分子挥发气体,塑件熔体向注射模型腔填充过程中,尤其是高速注射成型和和热固性塑料注射成型时,必须把这些气体顺序推出,排气槽一般设在型腔最后被充满的地方。
由于塑件的布局和设计是型腔由动、定模两部分组成,且采用点浇口,则排气槽开设在分型面上,由于分型面上因排气槽而产生的飞边,易随塑件脱出,而且还方便设计与加工,降低了设计与加工要求(此排气槽深度为0.03mm)。
图6-1-2冷却系统
⒎成型零件的设计
7.1型芯和型腔的结构和固定方式[3]
型芯采用镶块式结构,其优点为:
1有利于温度控制,冷却充分;
2零件更换方便;
③缩短模具制造周期。
型腔和型芯固定方式:
采用台肩固定,其优点为:
①加工方便;
②减少安装过程中出现的偏差
7.2成型零件工作尺寸计算[3][2]
因为PC得收缩率为0.5%-0.8%,所以平均收缩率为:
Scp=(0.5-0.8)∕2=0.65%=0.0065
根据塑件尺寸公差的要求:
模具的制造公差去δz=Δ∕3
成型零件尺寸的计算如表7-4-1所示
表7-4-1成型零件尺寸的计算
塑件尺寸
计算公式
型芯或型腔的工作尺寸
径
向
尺
寸
型腔径向尺寸
φ1600-2.5
LM=
φ159.17+0.630
φ820-1.5
φ81.48+0.380
φ78+1.50
φ77.38+0.380
型芯径向尺寸
φ1500-1.24
M=
φ151.600-0.31
轴向尺寸
型腔轴向尺寸
550-1.5
HM=
54.36+0.380
10+1.50
9.070.380
8+1.50
7.05=0.380
型芯轴向尺寸
450-1.3
44.420.330
7.3模具型腔壁厚的确定[2]
采用经验数据法,查阅设计手册中的相关数据,得该型腔的推荐壁厚为60m。
7.4标准模架的确定[2]
本塑件采用点浇口注射成型,根据模具结构形式,型腔数目,塑件尺寸等因素。
查资料知基本型模架组合尺寸选择标准模架的型号为C型3540---20Χ25Χ50GB/T12555-2006.
7.5模具闭合高度的确定[2]
组成模具闭合高度的模板及其他零件的尺寸有关:
定模座板:
H4=45mm
型腔板A=70mm
型芯固定板B=50mm
垫块C=110mm
动模座板H1=30mm
则该模具闭合高度为:
H=H4+A+B++C+H1=45+70+50+110+30=305mm
7.6模具闭合高度的校核[2]
由于SZY-300型塑料注射机所允许的模具最小厚度为285mm模具最大厚度为355mm,因计算得模具闭合高度为305mm,所以模具闭合高度满足Hmin≤H≤Hmax的安装要求。
7.7模具安装部分的校核[2]
该模具的外形最大部分尺寸为450mmΧ500mm,SZY-300型塑料注射机模具最大安装尺寸为625mmХ520mm,故能满足模具安装的要求。
⒏模具工作过程[2]
由于水碗注射模是采用两次分模的塑料模具,所以该模具的动作原理较为复杂。
当模具被注射后,制件得到冷却一段时间后,动模板和凹模型腔板2都在动模板23的带动下,开始离开定模板1,此时制件与浇口断开;
当凹模型腔板2上限程螺钉12阻挡住限位板13的继续运动时,这时凹模型腔板2与定模板1之间存在最大间距,可以取出浇注系统凝料。
由于凹模型腔板2是由导柱9上的凹槽与弹簧11顶压的滚珠10配合,实现其与动模板的同步运动;
因导柱9受到的牵引力远远大于弹簧11通过滚珠10带给它的阻力,滚珠10将会被挤出导柱9上的凹槽,从而凹模型腔板2将静止下来,然而,动模板15将继续向下运动,这时模具型腔里的塑料制件将同动模一起运动。
这就是该塑料模具注射过程中的开模过程。
当动模板行走完行程时,由注射机的顶出机构推动模具的顶出板22,带出顶杆26和頂料片3,使制件脱离动模板和型芯14.当顶出达到最大值时,就可以取出制件。
这便是该塑料模具注射过程中的脱模过程。
接下来,顶杆26、頂料片3等部件的复位,动模底板23带动动模板开始向定模运动,先和凹模型腔板2吻合,继续前进将会使凹模型腔板2和动模板1相吻合。
这便是该塑料模具注射过程中的合模。
合模之后,注射机将会注射塑料,进行下一个注射过程。
(如图8-1-1所示)
图8-1-1水碗注射模具结构
1-定模座板2-型腔板3-弹簧4-顶料片5定位圈6-内六角螺钉7-浇口套8-导套9-导柱10-限位钉11-定距拉12-型芯13-型芯固定板14-内六角螺钉15-垫块16-复位杆17-顶杆固定板
17-顶杆固定板18-顶出版19-导套20-导柱21-顶杆22-内六角螺钉
23-内六角螺钉24-圆柱销25-内六角螺钉26-圆柱销27动模座板
结束语
时至今日,几个礼拜的毕业设计终于可以画上一个句号了,但是现在回想起来做毕业设计的整个过程,颇有心得,其中有苦也有甜,不过乐趣尽在其中呀!
没有接受任务以前觉得毕业设计只是对这几年来所学知识的单纯总结,但是通过这次做毕业设计发现自己的看法有点太片面、太偏激了。
毕业设计不仅是对前面所学知识的一种检验,而且也是对自己能力的一种提高。
下面我对整个毕业设计的过程做一下简单的总结。
第一,接到任务以后进行选题。
选题是毕业设计的开端,选择恰当的、感兴趣的题目,这对于整个毕业设计是否能够顺利进行关系极大。
好比走路,这开始的第一步是具有决定意义的,第一步迈向何方,需要慎重考虑。
否则,就可能走许多弯路、费许多周折,甚至南辕北辙,难以到达目的地。
因此,选题时一定要考虑好了。
第二,题目确定后就是找资料了。
查资料是做毕业设计的前期准备工作,好的开端就相当于成功了一半,到图书馆、书店、资料室去虽说是比较原始的方式,但也有可取之处的。
总之,不管通过哪种方式查的资料都是有利用价值的,要一一记录下来以备后用。
第三,通过上面的过程,已经积累了不少资料,对所选的题目也大概有了一些了解,这一步就是在这样一个基础上,综合已有的资料来更透彻的分析题目。
第四,有了研究方向,就应该动手实现了。
其实以前的三步都是为这一步作的铺垫。
一步步地做下去之后,你会发现要做出来并不难,只不过每每做一会儿会发现一处错误要修改,就这样在不断的修改,再修改。
我的心得也就这么多了,总之,不管学会的还是学不会的的确觉得困难比较多,真是万事开头难,不知道如何入手。
还得出一个结论:
知识必须通过应用才能实现其价值!
有些东西以为学会了,但真正到用的时候才发现是两回事,所以我认为只有到真正会用的时候才是真的学会了。
谢辞
时间似箭,一闪而过。
毕业设计至此将告一段落,这也将标志着大学生活已到此画上了一个圆满的句号。
经过这些日子的努力奋战和指导老师的辛勤教导,终于在今天我以将大学所学的所有知识以毕业设计的形式表现出来。
看着这份杰作我兴慰不已,但更多的还是设计过程中酸甜苦辣。
在设计的完成过程中,王波老师他严谨的治学态度、渊博的知识和执着的敬业精神给我留下了深刻印象。
激励我克服困难,广泛涉猎新思想、新理论,不断地探求新的设计思路。
同时也是我更好,更快的完成了本次毕业设计。
更主要的是,也让我懂得如何去兢兢业业地工作、勤勤恳恳地做人。
于此同时在此,向所有关心和帮助过我的领导、老师、同学和朋友表示由衷的感谢!
衷心地祝愿在百忙之中评阅论文和参加答辩的各位老师在新的一年里,身体健康工作顺利,心想事成!
,
参考文献
[1]王岷主编.机械制图与AutoCAD.西安:
西北大学出版社,2006
[2]杨占尧主编.塑料模具课程设计指导与范例.北京:
化学工业出版社,2009
[3]杨安主编.塑料成型工艺与模具设计.北京:
北京理工大学出版社,2007
[4]罗洪涛,万征主编.中文AutoCAD2007机械设计教程.西安:
西北工业大学出版社,2007
[5]乔金莲,刘广瑞主编.新编中文AutoCAD2007实用教程.西安:
模具专业相关英语词汇大全
来源:
广西阳朔欧文中英文书院
一
.模具加工方法英语词汇
barrel
滚筒(加工)
bending
波纹加工
broaching
拉刀切削
centering
定中心
cutting
切削
cylindrical
lathe
外圆车削
electric
discharge
machine
放电加工
electrolytic
grinding
电解研磨
embossing
压花加工
facing
面车削