最新整理精益思想docWord文档格式.docx
《最新整理精益思想docWord文档格式.docx》由会员分享,可在线阅读,更多相关《最新整理精益思想docWord文档格式.docx(9页珍藏版)》请在冰豆网上搜索。
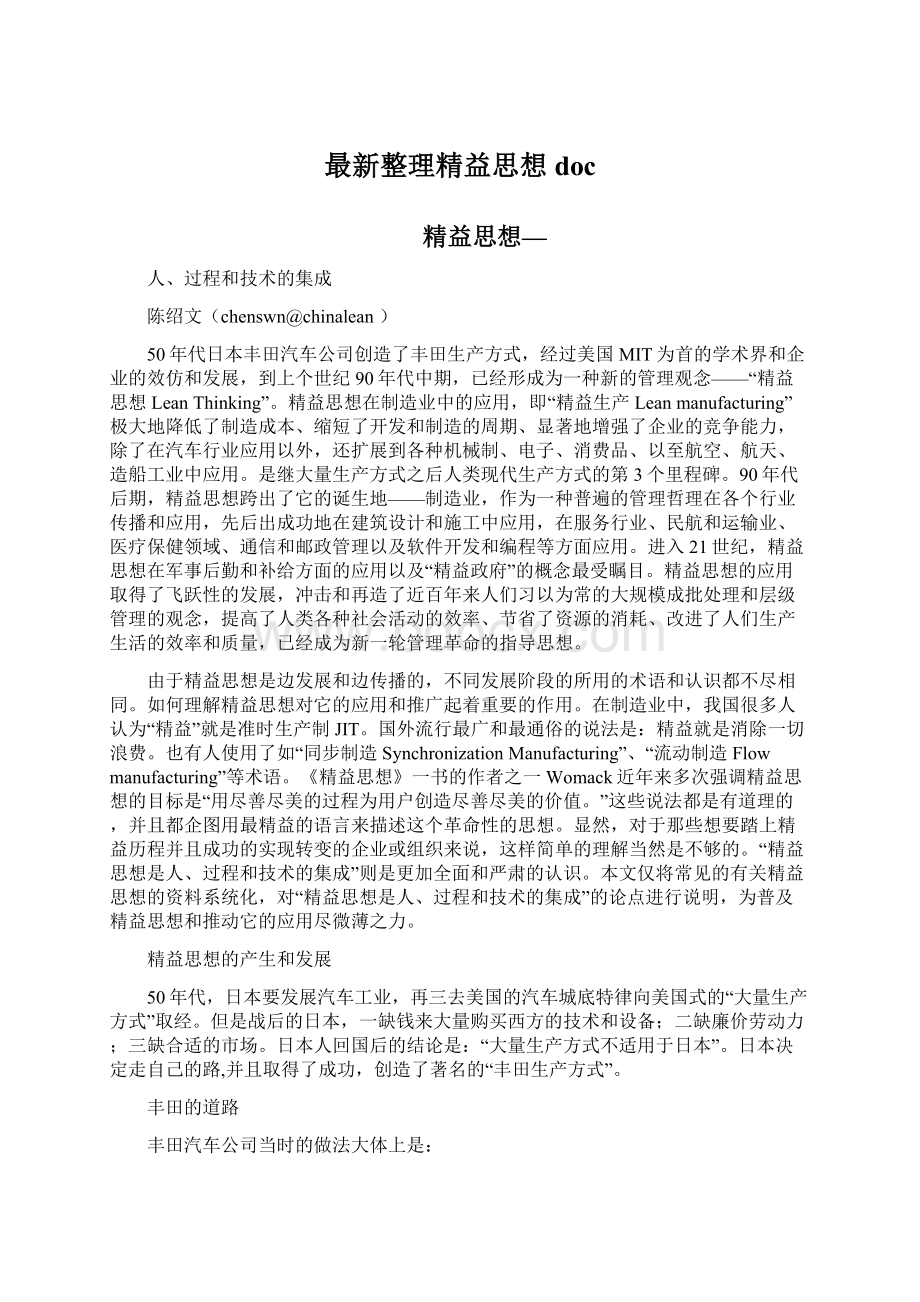
三缺合适的市场。
日本人回国后的结论是:
“大量生产方式不适用于日本”。
日本决定走自己的路,并且取得了成功,创造了著名的“丰田生产方式”。
丰田的道路
丰田汽车公司当时的做法大体上是:
在技术上,用少量设备加上快换装模具的轮番小批量生产替代大量的自动化设备上的连续生产。
2)生产现场的团队组织和作业决策权交给作业的职能员工
3)部门之间的协同、合作和全企业的过程贯通。
协作厂和零件厂组合成为一台协同运做的机器
4)采用由“看板”指令的准时化生产:
直接由用户的需求驱动、按日进度安排零件在协作厂之间的流动进程。
5)在协作企业之间建立紧密联系和合作的新型关系,增加沟通和信息的交流
6)工程领域打破了设计与制造的分工和分离
实行为制造而设计(DFM/DFA),
7)建立新型的客户关系
转向按订单组织生产。
销售成为生产系统中的一部分。
1)在技术上,用少量通用设备加上快换装模具的轮番小批量生产替代在大型自动化设备上的大量连续生产,
2)清理工作场地,更有秩序的生产,和节省辅助时间,
3)生产现场组织“团队化”,将作业决策权交给直接作业的团队和员工,
4)将部门之间看做为组合成一台协同运做的机器。
强调协同、合作和全企业的过程贯通,
5)采用由“看板”指令的准时化生产JIT,直接由用户的需求驱动、按日进度安排零件在协作厂之间的流动进程,
6)在协作企业之间建立紧密联系和合作的新型关系,增加沟通和信息的交流,
7)工程领域打破了设计与制造的分工和分离,实行为制造而设计(DFM/DFA),
8)建立新型的客户关系,转向按订单组织生产。
对丰田生产方式的分析
丰田生产方式为什么具有这样大的威力,能够打败以美国工业为代表的、近一个世纪以来确立的大批量生产方式,其中必然存在着创新的革命性的新思想。
透过表面的细节来分析丰田生产方式在技术道路、管理的观念和人和组织关系等3个方面都带给世界工业界以新思想。
日本人当时的创新是:
●技术路线由热衷于大型刚性的高效率专用设备转向为可快速调整的柔性技术。
丰田在快换模具和快速调整等技术的支持下,实现了更有优势的小批量甚至单件流生产。
新的方式省去了大量生产中由于大量库存成品零部件所引起的高库存和资金积压,减少了大批加工时多数制品的停滞和等待,反倒比大批量生产提高了效率和降低了成本;
丰田仅存有够工作2个小时或再少一些的中间库存,与美国企业储备2周的在制品形成鲜明的对照。
丰田的成功冲击和动摇了现代企业的“大批量出效益”的传统“金科玉律”。
●树起消除浪费的大旗。
精益思想将企业活动按照对最终用户需要的产品或服务是否增值划分为3类:
增值活动、不增值但目前的技术或社会环境下仍不可缺少的活动和不增值可以立即消除掉的活动。
丰田生产方式将生产过程中所有的非增值活动都视做浪费。
丰田汽车公司的经理大野耐一曾经指出了7类不增值的浪费(muda)。
如:
产品缺陷、不必须的过量生产、等待加工或消费的商品库存、不必要的过程、不必要的动作、多余的运输、停工待料或停工待机以及不符合用户需求的产品设计或服务(由Womack&
Jones增加的)等。
丰田消除浪费、减少非增值活动的各种措施,如5S、TQC等,为提高生产能力开辟了新的思路。
长期以来,人类对于加快过程速度的改革仅仅着眼于那些增值活动的速度,提高生产效率的努力主要作用于加工速度或加工方法的改进和提高,如发明效率更高的设备、减少工作量的新工艺和新方法等。
但真正对增值起作用的时间仅占总周期的1~5。
并且加工效率越高,非增值过程时间所占比例越大。
在仅仅1~5%的空间里的改进对于减少整个过程的周期的潜力越来越小。
丰田号召消除浪费的贡献就在于将改进的着眼点转移到非增值活动上去。
在占95%时间的非增值活动里挖掘潜力会收到事“半”功倍的效果。
●在员工的管理和企业结构方面,冲击和动摇了精细分工原则。
精细分工是现代企业制度的重要支柱。
严格的层级管理制度和精细分工,在工业化初期可能是降低劳动力成本和改进管理能力的必要原则。
但是,“阻碍知识和努力的发挥,是大量生产方式最突出的特征”。
丰田将若干质量监督、技术改进等现场决策的职责下放给操作工人、消除设计和工艺技术以至管理之间的隔阂和界限、开展全员设备管理等措施、组织由各个专业人员参与(注意!
并不是各个职能部门代表参与的)项目实施团队等。
鼓励和强调每一个参与者的积极性。
从而打破了传统的金字塔式的组织结构、精细分工的做法,连通了过去互不通气的部门“功能竖井”。
●与供应商之间建立的新型企业间的关系提高了企业相互之间的忠诚度,形成长期稳定的供求关系,促进供应商改进效率。
使持续改进的扩展到企业之间。
丰田生产方式的的这些内在或作用更深远的含义是对百年来建立大批量生产方式的基础的挑战,向劳动分工理论、层级的功能组织和集中的作业决策权、和大批生产提高生产率等。
由此造成制造企业的管理观念、组织和人际关系等方面根本性的变革,激发了生产率的大幅度提高。
丰田的变革获得了巨大的成功和丰田生产方式的扩散
丰田的这些试验获得了巨大的成功。
丰田生产方式对传统的大量生产方式在各方面的优势都是数倍至几十倍的,并且能以低的成本提供多样化的产品。
1973年发生了世界石油危机,当时庞大的美国公司拿不出低能耗的新型车,而被日本强占了势头。
到1989年日本汽车产量在世界汽车总产量中所占的份额几乎达到30%。
以日本本土为基地,日本的汽车出口稳定的增长。
美国的大量生产方式不能支持它继续处于领先地位了。
西方采用贸易壁垒阻止日本汽车工业的发展,但适得其反,日本开始通过在北美和西欧的直接投资办厂来增加在世界市场上的分额。
这在技术上的意义是促成了丰田生产方式向世界的传播。
日本在海外公司的获得了同样好的业绩。
当时美国人的头脑还是冷静的,他们排除了对日本取胜的偏见,开始研究日本竞争者采用的新方法。
于是美国人反过来到日本去取经了,福特、克莱斯勒、通用几个大公司都到了日本。
真正感到日本新生产方式的压力的福特公司,它的新联公司的弗里蒙特工厂成为在美国最先“复制”丰田制造方式企业,这里的管理人员都来自丰田,生产丰田设计的小型轿车。
从而开始了世界各地主动的向丰田生产方式学习的历史。
美国人学习了日本的工作方法以后,也取得了令人惊异的效果。
“精益生产”的诞生
丰田生产方式的扩散说明新的方法完全能够成功的移植到其它社会环境中去。
美国的学者已经明白,“丰田确实是在制造上完成了一场革命”。
美国人开始深入研究日本人的成功经验。
由麻省理工大学MIT组织了世界上14个国家的专家、学者,花费了5年时间和耗资500万美圆,在汽车工业中探索大量生产方式与丰田生产方式的差别。
最后在20xx年,由JamesP.Womack等人写了介绍丰田生产方式的《改造世界的机器TheMachineThatChangedtheWorld》一书。
书中给这种新的生产方式命名为:
“LeanProduction”。
“Lean”是“瘦”的意思,因为与大量生产方式相比这里一切的投入都大为减少。
随着这本书在全世界的畅销,“LeanProduction”也在全世界达到承认。
在中国将“LeanProduction”译作“精益生产”是“改造世界的机器”一书中文版的译法。
中文译者转“瘦”为“精”是一个成功之做。
《改造世界的机器》的意义是:
✧第一次将精益生产方式向人们做了详细的描述和介绍,
✧第一次将精益生产方式与100年来对西方经济产生决定影响的“大批量生产方式”相提并论,并第一次用精益生产方式对大批量生产方式进行批判,
✧宣布“精益生产方式的原理同样可以用于全世界每一种行业,向精益生产方式转变将对人类社会产生深远的影响,也就是说这一转变将真正地改变世界”,
✧预言了“精益生产方式必将在工业的各个领域取代大量生产方式与残存的单件生产方式,成为20世纪的标准的全球生产体系。
世界将变得大不一样,并将变得更加美好。
”
“改造世界的机器”的发表和传播对精益生产方式的发展产生了重要的作用。
但无论是丰田生产方式还是精益生产,所注重的是办公室或工厂的具体活动方法,而没有把所有的方法紧密联系形成一个完整的思想体系。
包括《改造世界的机器》这本书,也并没有说清楚精益生产的真谛。
又过了4年,Womack在他的另一本书“精益思想(LeanThinking)”的序言中写道:
“《机器》注意的是总过程—产品开发、销售和生产,而不是普遍的原则。
”没有精确的理论的指导,对精益生产所作的预言和褒奖,都是感性的。
精益生产处于有实践和成就、但缺少理论根基的不成熟时期。
从“精益生产”到“精益思想”
20世纪90年代美国进行了一系列的对精益生产的研究和实践。
这其中包括美国军方20xx年出台的美国“国防制造企业战略”、“精益航空计划LeanAerospaceInitiative”等政府指令性的活动。
除了汽车行业又有更多的美国企业如波音、洛克希德马丁、普惠等投入到实施精益生产的大潮中来。
在这个过程中,日本人提供了基本的思考和方法,用出色的实践证明了精益生产的强大生命力;
美国学者的研究、美国企业、乃至美国政府的研究和实践,则证明了精益思想在世界上的普遍意义,并升华为新一代的生产哲理。
终于在20xx年JamesWomack和DanielJones的《精益思想(LeanThinking)》一书问世,精益生产方式由经验变成为理论,新的生产方式正式诞生。
从上述精益思想发展的历程说明,精益思想是人、过程和技术的集成。
无论是丰田生产方式、还是后来的精益生产,都是从技术的改变和技术的可行开始的。
过程的思想则是丰田生产方式产生的基础。
而人则是决定性的因素。
精益思想比大批量生产关键性的改革是组织结构和分工原则的变化,这是解放被大量生产的分工和等级制度所束缚着的员工积极性的重要进步。
基于过程的“精益思想5项基本原则”
Womack/Jones在《精益思想》中,将由丰田开创的精益生产方式总结出5个基本原则,成为所有踏上精益道路的组织不厌其繁地理解和实行的基本原则。
这些原则是:
正确的确定价值
✧正确的确定价值就是以客户的观点来确定企业从设计到生产到交付的全部过程,实现客户需求的最大满足。
✧以客户的观点确定价值还必需将生产的全过程的多余消耗减至最少,不将额外的花销转嫁给用户。
✧精益价值观将商家和客户的利益统一起来,而不是过去那种对立的观点。
✧以客户为中心的价值观来审视企业的产品设计、制造过程、服务项目就会发现太多的浪费,从不满足客户需求到过分的功能和多余的非增值消耗。
当然,消灭这些浪费的直接受益者既是客户也是商家。
与之对照的是,
企业过去的价值观都是以自己为中心的。
完全由商家设计和制造的产品、完全由商家设计好的服务项目,大吹大擂那些目的在于增加赢利的、额外的、甚至是“画蛇添足”的功能,并不一定是用户所需要的、或必需的。
最后将大量的浪费以成本的方式转嫁给了用户。
而用户享受到的仅仅是为实现这个转嫁的殷勤。
识别价值流ValueStreammapping
价值流是指从原材料转变为成品、并给它赋予价值的全部活动。
这些活动包括:
从概念到设计和工程、到投产的技术过程,从订单处理、到计划、到送货的信息过程,和从原材料到产品的物质转换过程,以及产品全生命周期的支持和服务过程。
精益思想识别价值流的含义是在价值流中找到那些是真正增值的活动、那些是可以立即去掉的不增值活动。
精益思想将所有业务过程中消耗了资源而不增值活动叫做浪费。
识别价值流就是发现浪费和消灭浪费。
识别价值流的方法是“价值流分析ValueStreammapAnalysis”——首先按产品族为单位画出当前的价值流图,再以客户的观点分析每一个活动的必要性。
价值流分析成为实施精益思想最重要的工具。
价值流并不是从自己企业的内部开始的,多数价值流都向前延伸到供应商,向后延长到向客户交付的活动。
按照最终用户的观点全面的考察价值流、寻求全过程的整体最佳,特别是推敲部门之间交接的过程,往往存在着更多的浪费。
流动Flow
如果正确的确定价值是精益思想的基本观点、识别价值流是精益思想的准备和入门的话,“流动Flow”和“拉动Pull”则是精益思想实现价值的中坚。
精益思想要求创造价值的各个活动(步骤)流动起来,强调的是不间断地“流动”。
“价值流”本身的含义就是“动”的,但是由于根深蒂固的传统观念和做法,如部门的分工(部门间交接和转移时的等待)、大批量生产(机床旁边等待的在制品)等等阻断了本应动起来的价值流。
精益将所有的停滞作为企业的浪费,号召“所有的人都必须和部门化的、批量生产的思想做斗争”,用持续改进、JIT、单件流(one-pieceflow)等方法在任何批量生产条件下创造价值的连续流动。
当然,使价值流流动起来,必需具备必要的环境条件。
这些条件是:
✧过失、废品和返工都造成过程的中断、回流。
实现连续的流动要求每个过程和每个产品都是正确的。
全面质量管理和后来的6Sigma都成为精益思想的重要组成部分。
✧环境、设备的完好性是流动的保证。
3P、5S、全员维修管理(TPM)都是价值流动的前提条件之一。
✧有正确规模的人力和设备能力,避免瓶颈造成的阻塞。
拉动Pull
“拉动”就是按客户的需求投入和产出,使用户精确的在他们需要的时间得到需要的东西。
实行拉动以后用户或制造的下游就象在超市的货架上一样地取到他们所需要的东西,而不是把用户不太想要的产品强行推给用户。
拉动原则由于生产和需求直接对应,消除了过早、过量的投入,而减少了大量的库存和现场在制品,大量的压缩了提前期。
拉动原则更深远的意义在于企业具备了当用户一旦需要,就能立即进行设计、计划和制造出用户真正需要的产品的能力,最后实现抛开预测,直接按用户的实际需要进行生产。
实现拉动的方法是实行JIT生产和单件流。
当然,JIT和单件流的实现最好采用单元布置,对原有的制造流程做深刻的改造。
流动和拉动将使产品开发时间减少50%、订货周期、减少75%、生产周期降低90%,这对传统的改进来说简直是个奇迹。
尽善尽美Perfection
奇迹的出现是由于上述4个原则相互作用的结果。
改进的结果必然是价值流动速度显著的加快。
这样就必须不断地用价值流分析方法找出更隐藏的浪费,作进一步的改进。
这样的良性循环成为趋于尽善尽美的过程。
近来Womack又反复地阐述了精益制造的目标是:
“通过尽善尽美的价值创造过程(包括设计、制造和对产品或服务整个生命周期的支持)为用户提供尽善尽美的价值”。
“尽善尽美”是永远达不到的,但持续地对尽善尽美的追求,将造就一个永远充满活力、不断进步的企业。
在《精益思想》一书发表前后,精益思想跨出了它的诞生地——制造业,作为一种普遍的管理哲理在各个行业传播和应用,先后出现了精益建筑(leanConstruction)、精益服务(LeanServices)、军事精益后勤(LeanLogistics)和补给(Leansustainment)、精益医保健(Leanhealthcare)、精益软件开发(LeanProgramming)和精益政府(LeanGovernment)的概念,精益思想的应用取得了飞跃性的发展。
基于人的“精益思想生产关系”
Womack/Jones的精益思想5项基本原则从过程的目标出发,主要强调了过程的本身的特征。
但是如果将精益思想作为一种新的生产方式,还必须有对它的生产关系作明确的定义。
虽然无论是丰田还是美国人自己都有丰富的实践经验,但在《精益思想》这本书里,尚缺少明确的总结或描述。
精益思想的组织原则可以概括为“参与者(stakeholders—客户、供应商、投资者和员工)的主动”。
“主动”是指发挥所有的过程参与者的主观能动性。
实现流动和消除一切浪费的结果是过程的流动加快。
在快速流动的环境中,必然增加了过程参与者的精神和体力上的压力。
没有过程参与者的主观能动性,所有的增值流都不可能不间断地流起来。
在向精益企业转变的过程中,发挥那些过去最受压抑的部分人的积极性最为重要。
这些人是直接作业的工人和供应商。
实现“参与者的主动”的措施有3条:
用团队替代金字塔式的层级组织
在精益组织里,为满足客户需求而组成的综合各个专业人员的项目团队是企业完成所有过程的基本单位。
企业对团队的权力和责任有明确的规定,团队的决策权和职权与团队承担的责任相统一,领导层给予团队的决策和活动所需的与实现其业务实践相一致的资源,领导层对团队职权内的决策和活动不进行干预。
生产第一线的团队或员工在作业中遇到问题时,团队可以决定如何解决,不必请示。
团队有责任对所在价值链的部分进行持续改进。
企业鼓励和支持各层次员工通过质量循环和持续改进使团队得以发展。
通过发挥团队的主动性,企业将改变原先等级森严的金字塔式的结构。
这种层级制度是造成的压抑工人或任何作业执行者的思考和改进、产生官僚主义、拖拉、反应迟钝、不流动和高成本的根源。
对员工的信任与关怀
企业按照整个价值链的结构和顺序进行重构,每一个员工按其工作角色分配到企业的价值链结构中去。
然后赋予员工与他岗位职责相对应的决策权,制度化的给员工对他相关工作过程以持续改进的建议的机会。
对员工进行精益思想和各种业务培训,多技能和轮岗培训。
企业向员工公布企业的订单和交付状况、企业和每一个人的质量情况,公布企业的成本和员工对企业的满意度的评价等等。
这一切都是让企业中从上到下的每一个人都知道自己为什么工作,树立员工对自己团队的忠诚、荣誉感和责任心。
例如波音公司就有一整套发挥员工积极性的活动,如“AIW”加速车间改进、AMM自主维修和LMA精益制造评议活动。
组织间的合作与协同
多数制造企业的采购成本往往占到它的销售收入的50~70%,乃至更多。
减低采购成本就成为多数企业追求的目标。
在传统的大批量生产中,把供应商视做敌人,拼命压低价格、转嫁库存和损失。
而精益思想将供应商作为价值流的起点。
供应商是整个价值流过程中的一员,组织供应商和客户有可能尽早的了解企业的产品/过程/项目,并且请供应商和客户适时地参与企业的产品、过程或项目的团队,请供应商和客户参与对企业产品、过程或项目发展的定期评审,有效的鼓励供应商、企业和客户,奖励他们对共同业绩的改进等等都是降低全过程成本的有效因素。
结果精益企业与供应商的关系成为协同与合作的新型伙伴关系,共同为减少整个价值流的浪费而努力。
帮助供应商实现精益生产是这种新型伙伴关系的又一种体现。
波音公司在进行新机X32的研制中,与供应商的新型伙伴关系成为用最低成本、100%的及时得到需要的配件和原材料的保证。
精益的企业文化
在企业过程观的指导下,精益企业形成体现新的人际关系、组织间关系和员工责任感的新型的文化氛围。
这些新的企业文化成为企业在竞争中取胜的精神力量和法宝。
✧一次无故障交付的质量意识
✧全员设备维护的意识,建立有效的计划预防维修系统,所有的设备按规定的周期进行适当的维修
✧“不相互责备”原则,是建立相互信任与支持的基础,
✧当短期目标与精益进步不一致时,管理者选择的是坚持精益原则
✧持续不断改进的努力
✧工作环境应该清洁、组织有序符合标准的5S要求产品和工艺过程的设计是全集成的团队的共同的行为
✧设计和工艺的结合,全面遵守DFM/DFA(DesignforManufacturing/DesignforAssembly)和价值工程等原则。
精益思想的技术支持
历史上任何一种新生产方式的出现,都是由于技术发展所引发的。
19世纪初,福特发明了互换性原则和高效率设备组成的流水线才促成了大规模批量生产方式的诞生。
同样,新的技术发展是精益思想诞生的物质基础。
支持精益生产的技术是柔性化的设备和构建面向产品族的生产单元。
柔性化的设备
推行精益思想时,进行设备的改造和更新是重要的内容之一。
有人在描述精益生产时用了“精益生产=JIT+自动化”的公式。
还有学者强调精益制造的自动化是有人干预的“智能自动化”。
其实自动化并没有突出精益生产的特点。
和大批量生产的高效率设备相对比,实现精益制造的设备是便于更换或调整的柔性化设备。
在柔性设备上,更换产品只需要很少的时间,以至于可以大大地降低所谓“经济规模”的阈值。
各种数控设备,特别是数控加工中心和柔性制造系统FMS是拉式生产系统首选的柔性设备。
注意首推数控设备并不是由于它们是“自动化”的,而是看中了它们“柔性化”的特征。
用普通的通用设备加日本式的快速换装的模具系统、或在前苏联推广过的成组夹具或组合夹具,也是效果很好的柔性化设备方案。
相反,刚性自动化设备最能体现大量生产方式的优势,但用他们进行精益的小批量甚至单件流生产、而又企图获得高效率和低成本是不可能的。
因而,在向精益企业转变过程中,体积庞大而不易搬动、需要按批量作业的“超大设备”成为新的浪费而失去它的生命力。