本科毕业设计柴油机凸轮轴设计.docx
《本科毕业设计柴油机凸轮轴设计.docx》由会员分享,可在线阅读,更多相关《本科毕业设计柴油机凸轮轴设计.docx(43页珍藏版)》请在冰豆网上搜索。
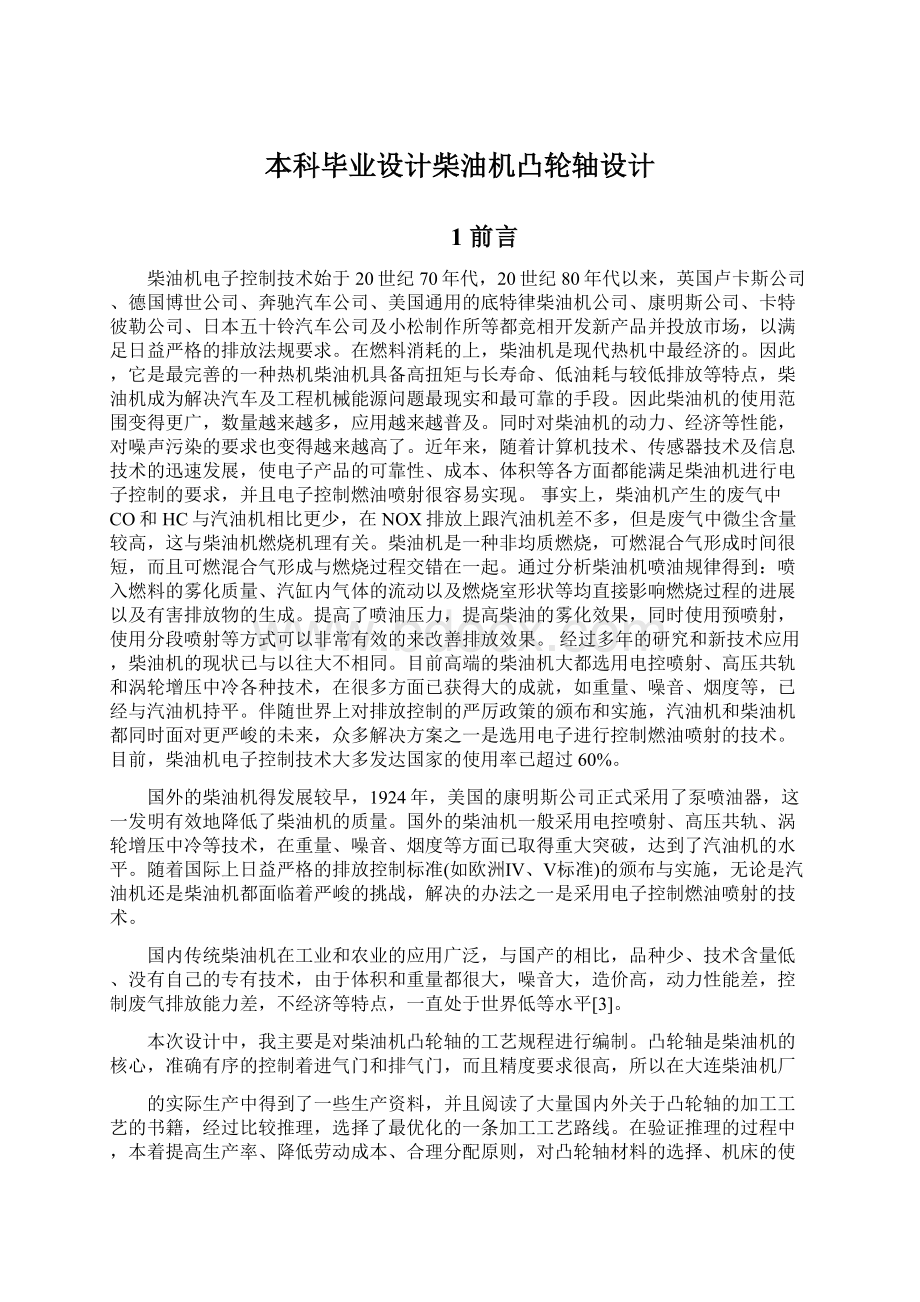
本科毕业设计柴油机凸轮轴设计
1前言
柴油机电子控制技术始于20世纪70年代,20世纪80年代以来,英国卢卡斯公司、德国博世公司、奔驰汽车公司、美国通用的底特律柴油机公司、康明斯公司、卡特彼勒公司、日本五十铃汽车公司及小松制作所等都竞相开发新产品并投放市场,以满足日益严格的排放法规要求。
在燃料消耗的上,柴油机是现代热机中最经济的。
因此,它是最完善的一种热机柴油机具备高扭矩与长寿命、低油耗与较低排放等特点,柴油机成为解决汽车及工程机械能源问题最现实和最可靠的手段。
因此柴油机的使用范围变得更广,数量越来越多,应用越来越普及。
同时对柴油机的动力、经济等性能,对噪声污染的要求也变得越来越高了。
近年来,随着计算机技术、传感器技术及信息技术的迅速发展,使电子产品的可靠性、成本、体积等各方面都能满足柴油机进行电子控制的要求,并且电子控制燃油喷射很容易实现。
事实上,柴油机产生的废气中CO和HC与汽油机相比更少,在NOX排放上跟汽油机差不多,但是废气中微尘含量较高,这与柴油机燃烧机理有关。
柴油机是一种非均质燃烧,可燃混合气形成时间很短,而且可燃混合气形成与燃烧过程交错在一起。
通过分析柴油机喷油规律得到:
喷入燃料的雾化质量、汽缸内气体的流动以及燃烧室形状等均直接影响燃烧过程的进展以及有害排放物的生成。
提高了喷油压力,提高柴油的雾化效果,同时使用预喷射,使用分段喷射等方式可以非常有效的来改善排放效果。
经过多年的研究和新技术应用,柴油机的现状已与以往大不相同。
目前高端的柴油机大都选用电控喷射、高压共轨和涡轮增压中冷各种技术,在很多方面已获得大的成就,如重量、噪音、烟度等,已经与汽油机持平。
伴随世界上对排放控制的严厉政策的颁布和实施,汽油机和柴油机都同时面对更严峻的未来,众多解决方案之一是选用电子进行控制燃油喷射的技术。
目前,柴油机电子控制技术大多发达国家的使用率已超过60%。
国外的柴油机得发展较早,1924年,美国的康明斯公司正式采用了泵喷油器,这一发明有效地降低了柴油机的质量。
国外的柴油机一般采用电控喷射、高压共轨、涡轮增压中冷等技术,在重量、噪音、烟度等方面已取得重大突破,达到了汽油机的水平。
随着国际上日益严格的排放控制标准(如欧洲Ⅳ、Ⅴ标准)的颁布与实施,无论是汽油机还是柴油机都面临着严峻的挑战,解决的办法之一是采用电子控制燃油喷射的技术。
国内传统柴油机在工业和农业的应用广泛,与国产的相比,品种少、技术含量低、没有自己的专有技术,由于体积和重量都很大,噪音大,造价高,动力性能差,控制废气排放能力差,不经济等特点,一直处于世界低等水平[3]。
本次设计中,我主要是对柴油机凸轮轴的工艺规程进行编制。
凸轮轴是柴油机的核心,准确有序的控制着进气门和排气门,而且精度要求很高,所以在大连柴油机厂
的实际生产中得到了一些生产资料,并且阅读了大量国内外关于凸轮轴的加工工艺的书籍,经过比较推理,选择了最优化的一条加工工艺路线。
在验证推理的过程中,本着提高生产率、降低劳动成本、合理分配原则,对凸轮轴材料的选择、机床的使用类型、刀具的选材和类型都做了详细的计算和科学说明,最后绘制出凸轮轴的毛坯图、零件图、工艺流程图。
2轴类零件加工
2.1轴类零件的毛坯
轴类毛坯锻造方式有自由锻和模锻两种。
中小批量生产时多采用自由锻,大批量生产时则常采用模锻方式。
自由锻的特点是不用锻模,设备简单,靠手工制作,容易投产。
但该方法锻造出的毛坯精度差,加工余量大,材料利用率低,从经济效益观点出发,自由锻只用于单件和小批量生产。
模锻的特点是采用锻模形成毛坯形状,因而设备复杂,需要较长的生产周期。
毛坯精度高,加工余量小,材料利用率高,可以锻造出形状复杂的毛坯,模锻适用于大批量生产。
在实际生产中,柴油机是大批量生产的,所以凸轮轴选择的是锻造[4]。
2.2轴类零件的材料及热处理
一般轴类零件最常用的材料是45Cr,并根据不同的工作条件采用不同的热处理规范,从而获得需要的强度、硬度、韧性和耐磨性。
对于在高速、重载荷条件下工作的轴,可选用18CrMnTi、20CrMnTi、20MnB及20Cr等低炭合金钢[5]。
所以柴油机的凸轮轴选用的是45Cr。
2.3轴类零件的主要技术要求
2.3.1轴径尺寸精度
一般的主要的支撑轴径的直径精度根据使用要求通常为IT6—IT7,特殊精度的轴可达IT5。
次要的配合表面精度可选用IT8—IT9。
2.3.2几何形状精度
几何形状精度(如圆度、圆柱度、直线度)应限制在直径公差范围内。
当图上对轴的几何公差没有标注时,习惯上取尺寸公差的一半,若对几何公差要求较高时,可在零件图上直接注出允许的偏差[6]。
2.3.3相互位置精度
对支撑轴径间应有同轴度要求,一般情况下支撑轴径的同轴度公差确定为0.01mm,精度的可定到0.005mm。
配合轴径与支撑轴径间也应该有同轴度要求,通常将配合轴径对支撑轴径的径向圆跳动公差定为0.01—0.03mm,高精度的轴可定为0.001—0.005mm。
2.3.4表面粗糙度
一般的支撑轴径的表面粗糙度Ra值可为1.25—0.32mμ,特精密的Ra值可为0.16—0.08mμ。
配合轴径的表面粗糙度Ra值为2.5—0.63mμ。
3设计计算
3.1毛坯的选择
选用45Cr,这种钢与40Cr相比,钢的强度、耐磨性及淬透性均提高。
该钢价格适中,加工容易,经适当的热处理后,可获得一定的韧性、塑性和耐磨性,且该钢的淬透性高于45号钢,适合于高频淬火,火焰淬火等表面硬化处理。
3.2工艺路线
3.2.1锻造
选择毛坯,锻造多阶轴
3.2.2热处理
正火
为减小其加工后的应力变形,并消除其锻造而产生的残余内应力,提高了凸轮轴的耐磨性和表面硬度。
3.2.3铣断面
打中心孔Ф14.2,深16.5;钻铰定位销孔Ф8,深32
1.铣断面1:
(1)确定键槽铣床:
选用专机
(2)确定铣刀:
Ф100面铣刀D=100mm,B=60mm,Z=12
(3)确定加工余量:
z=2mm
(4)确定切深:
t=1mmSz=0.2mm,T=180,Cv=73.5
(v=)[7]=66.4m/min
(n计=1000v/πD)[7]=1000*66.4/3.14*68=311r/min
取机床主轴转速315r/min(1:
1.26)
(5)确定加工时间:
l2=1.2
(T0=)[7]=1.5/0.2=7.5min
(t辅=1/4t基)[7]=1.88min
(t服+t休=5%(t基+t休))[7]=0.47min
(t单=t基+t辅+t休+t服)[7]=9.85min
2.铣断面2:
(1)确定键槽铣床:
选用专机
(2)确定铣刀:
Ф100面铣刀D=100mm,B=60mm,Z=12
(3)确定加工余量:
z=2mm
(4)确定切深:
t=1mm
Sz=0.2mm,T=180,Cv=73.5
v==66.4m/min
n计=1000v/πD=1000*66.4/3.14*52=407r/min
取机床主轴转速390r/min(1:
1.26)
(5)确定加工时间:
l2=1.2
T0==1.2/0.2=6min
t辅=1/4t基=1.5min
t服+t休=5%(t基+t休)=0.38min
t单=t基+t辅+t休+t服=7.88min
3.钻中心孔:
(1)确定钻床:
选用专机
(2)加工余量:
z=14.2mm
(3)确定切深:
ap=7.1mm
进给量f=0.3mm/r,v=29.4m/min
n计=1000v/πD=1000*29.4/3.14*14.2=657r/min
取机床主轴转速660r/min(1:
1.26)
(v实=πDn/1000)[4]=3.14*14.2*660/1000=29.4m/min
(4)确定加工时间:
取l1=4.3,l2=1.5
(t基=(l+l1+l2)/s.n实)[7]=16.5+3+2+5/0.3*660=0.13min
t辅=1/4t基=0.05min
t服+t休=5%(t基+t休)=0.01min
t单=t基+t辅+t休+t服=0.19min
4.钻铰定位销孔:
(1)确定钻床:
选用专机
(2)加工余量:
z=8mm
(3)确定切深:
ap=4mm
进给量f=0.2mm/r,v=28.7m/min
n计=1000v/πD=1000*28.7/3.14*8=1142r/min
取机床主轴转速1120r/min(1:
1.26)
v实=πDn/1000=3.14*8*1120/1000=28.1m/min
(4)确定加工时间:
取l1=4.3,l2=1.5
t基=(l+l1+l2)/s.n实=32+3+2+5/0.2*1120=0.19min
t辅=1/4t基=0.15min
t服+t休=5%(t基+t休)=0.01min
t单=t基+t辅+t休+t服=0.25min
3.2.4粗车主轴径及小头并倒角1.3545o
1.车大端主轴:
(1)确定加工余量:
取总加工余量6mm
取精加工余量1.1mm
取半精磨余量0.4mm
取精磨余量0.4mm
粗车余量:
z=7-1.1-0.4-0.4=4.1
(2)确定切深:
ap=5.1mm
进给量f=0.6mm/r,n实=560r/min,v实=118m/min
(3)确定加工时间:
取l1=3,l2=2,l3=5(游标卡尺)
t基=(D/2+l1+l2+l3)/fn实=31.45+3+2+5/0.6*560=0.12min
t辅=1/4t基=0.03min
t服+t休=5%(t基+t休)=0.008min
t单=t基+t辅+t休+t服=0.158min
车主轴内端面:
(1)确定加工余量:
取总加工余量3.55mm
取精加工余量1.1mm
取半精磨余量0.4mm
取精磨余量0.4mm
粗车余量:
z=3.55-1.1-0.4-0.4=1.65mm
(2)确定切深:
ap=1.65mm
进给量f=0.6mm/r,n实=560r/min,v实=118m/min
(3)确定加工时间:
取l1=3,l2=2,l3=5(游标卡尺)
t基=(D-d/2+l1+l2+l3)/fn实=8.95+3+2+5/0.6*560=0.07min
t辅=1/4t基=0.018min
t服+t休=5%(t基+t休)=0.004min
t单=t基+t辅+t休+t服=0.092min
2.车中间主轴:
(1)确定加工余量
取总加工余量7mm
取精加工余量1.1mm
取半精磨余量0.4mm
取精磨余量0.4mm
粗车余量:
z=7-1.1-0.4-0.4=5.1mm
(2)确定切深:
ap=z/2=5.1/2=2.55mm
进给量f=0.6mm/r,v=111m/min
n计=1000v/πD=1000*111/3.14*62.9=562r/min
取机床主轴转速560r/min
v实=πDn/1000=3.14*62.9*560/1000=118m/min
(3)确定加工时间:
取l1=3,l2=2,l3=5(游标卡尺)
t基=(l+l1+l2+l3)/f.n实=39.5+3+2+5/0.6*560=0.15min
t辅=1/4t基=0.04min
t服+t休=5%(t基+t休)=0.01min
t单=t基+t辅+t休+t服=0.2min
车主轴端面:
(1)确定加工余量
取总加工余量7mm
取精加工余量1.1mm
取半精磨余量0.4mm
取精磨余量0