2毕业设计说明书文档格式.docx
《2毕业设计说明书文档格式.docx》由会员分享,可在线阅读,更多相关《2毕业设计说明书文档格式.docx(32页珍藏版)》请在冰豆网上搜索。
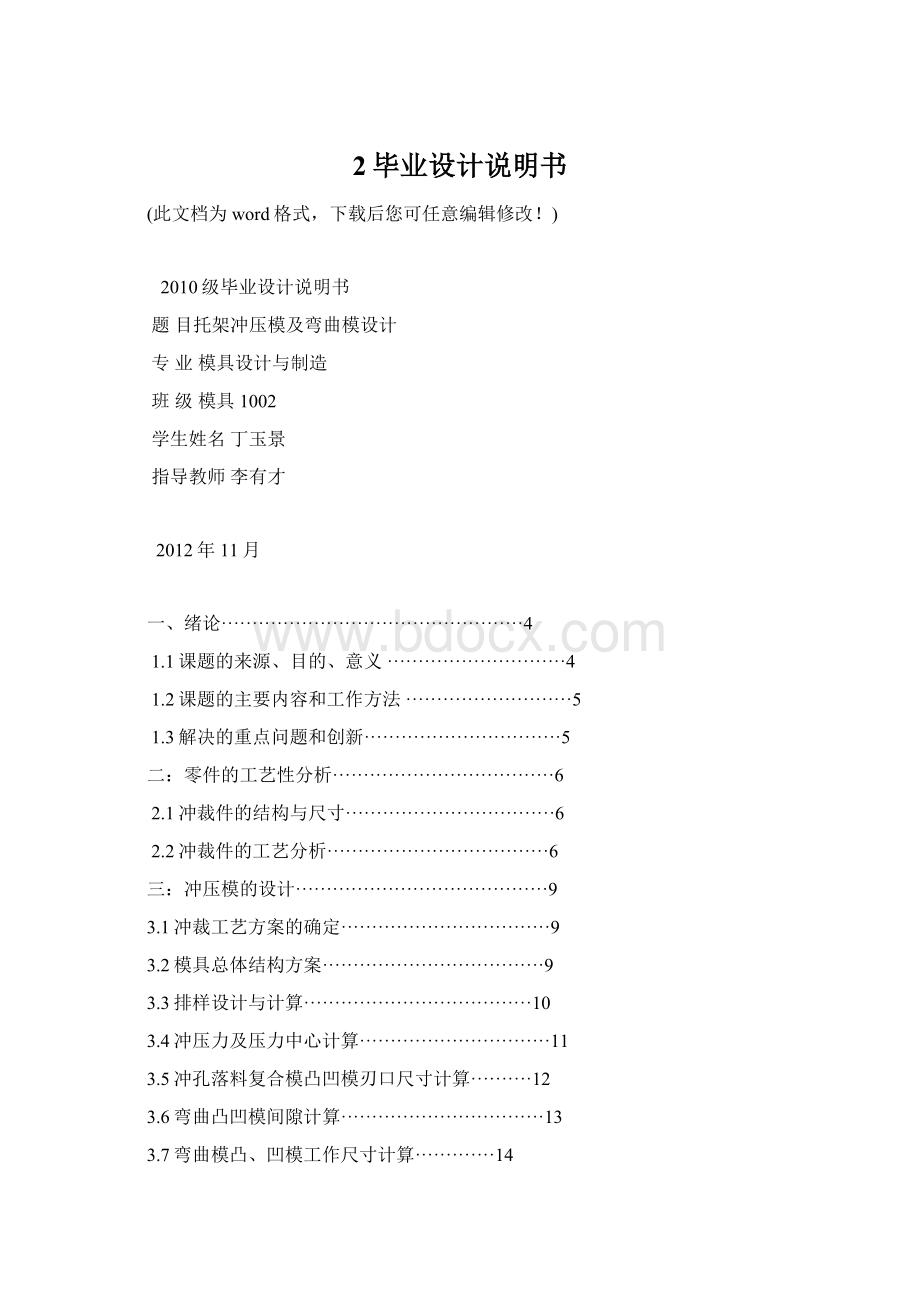
四:
主要零部件的设计·
4.1工作零部件的结构设计·
15
4.2定位零件的设计·
16
4.3卸料装置设计·
17
五:
模具总体结构设计·
24
5.1模具总体结构分析·
5.2模具总装图·
5.3冲压设备的选取·
28
六:
模具零件的制造与装配·
6.1凸模制造工艺·
6.2凹模制造工艺·
29
6.3凸凹模制造工艺·
30
6.4模具装配工艺·
31
七:
结束语·
32
八:
参考文献·
34
冲压模具设计说明书
第一章绪论
1.1课题的来源、目的、意义
1.模具行业发展前景分析
随着科学技术的不断进步和工业生产的迅速发展,许多新技术、新工艺、新设备、新材料不断涌现,因而促进了冲压技术的不断革新和发展。
冲压成形理论的研究是提高冲压技术的基础。
目前,国内外对冲压成形理论的研究非常重视,在材料冲压性能研究、冲压成形过程应力应变分析、板料变形规律研究及坯料与模具之间的相互作用研究等方面均取得了较大的进展。
特别是随着计算机技术的飞跃发展和塑性变形理论的进一步完善,近年来国内外已开始应用塑性成形过程的计算机模拟技术,即利用有限元(FEM)等有值分析方法模拟金属的塑性成形过程,根据分析结果,设计人员可预测某一工艺方案成形的可行性及可能出现的质量问题,并通过在计算机上选择修改相关参数,可实现工艺及模具的优化设计。
这样既节省了昂贵的试模费用,也缩短了制模具周期。
研究推广能提高生产率及产品质量、降低成本和扩大冲压工艺应用范围的各种压新工艺,也是冲压技术的发展方向之一。
冲模是实现冲压生产的基本条件.在冲模的设计制造上,目前正朝着以下两方面发展:
一方面,为了适应高速、自动、精密、安全等大批量现代生产的需要,冲模正向高效率、高精度、高寿命及多工位、多功能方向发展,与此相比适应的新型模具材料及其热处理技术,各种高效、精密、数控自动化的模具加工机床和检测设备以及模具CADCAM技术也在迅速发展;
另一方面,为了适应产品更新换代和试制或小批量生产的需要,锌基合金冲模、聚氨酯橡胶冲模、薄板冲模、钢带冲模、组合冲模等各种简易冲模及其制造技术也得到了迅速发展。
2.发展趋势分析
随着新兴学科的出现及材料加工学科与相关学科的交叉,必将促进板材成形技术的发展,对于板材,其总的发展趋势如下。
(1)节能,节约能源意识新时期经济发展的一个重要的课题,也是板材发展的重要方向。
其主要途径一个是在传统能源利用中,通过见底拘束系数、降低流动应力和减少成形力;
另一个途径就是新能源的开发利用。
(2)精密,“近净成形”技术可有效地减少后续加工,节省原材料,降低生产成本,已成为材料加工中的重点发展方向。
(3)柔性,为满足未来社会多样化的需求和不确定的市场环境,柔性成形技术对产品变化有很强的适应性,可有效、低耗地满足多种产品的需求。
(4)绿色,随着制造业的发展,绿色环保将是材料材料技术面临的重要课题。
减少和消除成形过程中对环境的污染是绿色制造的主要原因之一。
(5)信息化、智能化,现代计算机技术、信息技术不但促进传统技术的发展,而且不断产生新的特种成形技术。
计算机模拟成形技术(CADCAMCAECAPPPOM)在成形技术中的大量应用已经是工艺设计、模具设计与制造更加科学化、自动化。
变形预测、组织预测已经成为可能。
成形技术已从“经验型”逐渐走向科学化、信息化和智能化。
该课题中的外形状较为简单的U形件。
有冲孔落料弯曲,做起来有一定的难度。
1、可以较全面的综合运用和巩固冲压模具设计与制造等课程的基础知识和专业知识,培养从事冲压模具设计与制造的初步能力。
2、通过该设计可以培养我分析问题和解决问题的能力,了解和熟悉冲压模具设计与制造的一般步骤,更深入的认识冲压模具零件的设计和加工过程,达到“知己知彼”的效果。
3、通过该设计可以培养我在模具设计过程中认真负责、踏实细致的工作作风和严谨的科学态度,强化质量意识和时间观念,养成良好的职业习惯。
1.2课题的主要内容和工作方法
由于冲压加工的零件种类繁多,各类零件的形状、尺寸和精度要求又各不相同,因而生产中采用的冲压工艺方法也是多种多样的。
概括起来,可分为分离工序和成形工序两大类;
分离工序是指使坯料沿一定的轮廓线分离而获得一定形状、尺寸和断面质量的冲压(俗称冲裁件)的工序;
成形工序是指使坯料在不破裂的条件下产生塑性变形而获得一定形状和尺寸的冲压件的工序。
上述两类工序,按基本变形方式不同又可分为冲裁、弯曲、拉深和成形四种基本工序,每种基本工序还包含有多种单一工序。
在实际生产中,当冲压件的生产批量较大、尺寸较少而公差要求较小时,若用分散的单一工序来冲压是不经济甚至难于达到要求。
这时在工艺上多采用集中的方案,即把两种或两种以上的单一工序集中在一副模具内完成,称为组合的方法不同,又可将其分为复合-级进和复合-级进三种组合方式。
复合冲压——在压力机的一次工作行程中,在模具的同一工位上同时完成两种或两种以上不同单一工序的一种组合方法式。
级进冲压——在压力机上的一次工作行程中,按照一定的顺序在同一模具的不同工位上完面两种或两种以上不同单一工序的一种组合方式。
复合-级进——在一副冲模上包含复合和级进两种方式的组合工序。
冲模的结构类型也很多。
通常按工序性质可分为冲裁模、弯曲模、拉深模和成形模等;
按工序的组合方式可分为单工序模、复合模和级进模等。
但不论何种类型的冲模,都可看成是由上模和下模两部分组成,上模被固定在压力机工作台或垫板上,是冲模的固定部分。
工作时,坯料在下模面上通过定位零件定位,压力机滑块带动上模下压,在模具工作零件(即凸模、凹模)的作用下坯料便产生分离或塑性变形,从而获得所需形状与尺寸的冲件。
上模回升时,模具的卸料与出件装置将冲件或废料从凸、凹模上卸下或推、顶出来,以便进行下一次冲压循环。
而本课题的主要内容是根据零件的形状确定冲压工艺类型和选择工序顺序。
冲压该零件的基本工序有剪切(落料)、冲圆孔、一次弯曲、二次弯曲。
然后对零件进行工艺分析,进行工序组合,选择合适的工艺方案。
1.3解决的重点问题和创新
(1)通过对托架工件的工艺分析,确定工作的重点主要集中在模具工作部分零件的设计(凸模,凹模,凸凹模)各种固定板的设计和相关尺寸的计算和校核。
(2)设计前后工序的关联性以及模具的关联性,合理安排工序,模具的结构更紧密,同时在模具的设计过程中加工性,要尽量多的选用标准件,达到规范设计的要求成为毕业设计的难点。
(3)针对此次模具设计工作量大,工作难度大的特点,拟采用计算机辅助设计AutoCAD、UG等相关软件来完成模具设计,从而节省时间和精力;
收集相关文献、期刊论文来加以辅助设计;
针对自身理论上的不足抽出时间向辅导老师请教学习;
当然,在具体的设计中也要不断的去实践所设计模具的实用性与经济性,使设计更趋近于精确化、规范化、系统化。
设计中所提供材料的厚度1.5mm的20钢,该零件冲孔落料弯曲成形。
一般冲制该零件需落料、冲孔、弯曲等基本工序来完成。
为了减少工序,对该零件进行详细分析研究,并查阅有关资料,认为要达到零件的精度要求,我们采用四副模具来完成零件产品的成型,及冲孔落料、弯曲一、弯曲二、冲孔四副模具。
第二章零件的工艺性分析
2.1冲裁件的结构与尺寸
1.设计要求
生产数量80000件,属中批量生产。
材料为20#钢,厚度t=1.5mm。
2.设计图纸及要求
零件图如下图所示:
2.2冲裁件的工艺分析
1.结构工艺性
(1)该零件形状呈U形,结构较复杂的对称件。
(2)该零件端部四角为尖角,若采用落料工艺性较差,但图纸上无特殊要求,故可采用落料方式。
(3)该零件的腿较长,若能有效地利用过弯去和校正弯曲来控制回弹,则得到形状和尺寸比较精确的零件。
(4)该零件两边脚对称而距零件顶端的高度值不同。
(5)中心孔到弯曲半径R圆心的距离为L1=.5=6.5≥R1+0.5t=2.25;
L2=5-2.5=2.5≥R1+0.5t=2.25因此中心圆孔位于变形区之外,弯曲时能保证其不变形,故该孔可在弯曲前冲出,而两边的孔的中心有精度要求,它的36±
0.05在弯曲时不能保证,并且最小孔边距a=2.5<
2t=3安全值,所以这两个孔放在最后冲孔形成。
而分析该零件的形状结构可知,该零件是一个不对称的零件,所以一次弯曲成型是不可能达到技术要求的,并且由于它的不对称会在一次弯曲过程中由于板料的受力不均匀会使得中心的大孔拉伤,从而影响精度要求。
在弯曲过程中,弯曲一是对称弯曲,其很容易达到技术要求,而弯曲二虽然不是对称弯曲,但是由于受力位置是两边线,其不会影响到中间大孔的精度。
故我们采用先冲中心孔并落料的单工序复合膜,再对称弯曲,须而进行弯曲二,组后再冲孔。
其步骤及图形如下:
1.冲孔落料复合。
2.弯曲一
3.弯曲二
4.冲孔二
2.公差和断面粗糙度的确定
(1)公差
该零件的尺寸公差除250.05和360.05接近于IT10级以外,其余尺寸均IT14级无其他特殊要求,从《冲压模具与设备》表4-5可知利用普通冲裁方式可以达到零件图样要求。
(2)断面粗糙度
本例未作特殊要求。
3.材料
牌号
力学性能
硬度HBS
抗拉强度σbMP
抗剪强度τMP
屈服点σsMP
伸长率σ10%
未经处理
20
427
245
330
25
≤156
20#钢,软态,抗剪强度τb=330MP,断后伸长率σ10=25%。
此材料具有较高的弹性和良好的塑性,其冲裁加工性较好,一般用于制造受力不大的冲裁件。
根据以上分析,该零件的加工性加好,可以冲裁加工。
第三章冲压模设计
3.1冲裁工艺方案的确定
1.确定基本工序及数量
工件(上图)外形比较复杂,包括落料、冲孔和弯曲三种基本工序,可采用的冲裁工艺方案有单工序冲裁、复合冲裁和级进冲裁三种。
第一道工序外形可以切断,也可以落料,内形可以冲中心孔的单工序模;
第二道工序对称弯曲模;
第三道工序继续不对称弯曲;
第四道工序再冲两小孔。
2.确定工序顺序
第一道工序有两种情况采用单工序模应为先落料后冲孔;
其二是采用复合模工序一般为冲孔落料同时进行。
第二种方法很简单,而且节约制造成本且节约时间,故采用冲孔落料复合模。
3.进行工序组合,确定工艺方案。
方案一,落料冲孔同时进行,采用复合模。
弯曲两次。
方案二,先落料冲大孔,采用复合模。
再进行弯曲成形,最后再冲两小孔。
方案三,落料冲孔同时进行,采用复合模。
再对称弯曲,接着再次弯曲成形,最后冲两小孔。
方案四,先落料,再弯曲对称脚,然后再次弯曲成形,最后冲孔。
其中,方案一和方案二的模具虽能良好的保证生产效率,但方案一在冲完两小孔的时候再弯曲时就不能保证两小孔的孔间距。
而方案二采取一次弯曲成形模具结构较复杂且不能保证零件精度要求;
方案三最大的特点冲件精度高,不受送料误差影响,内外性相对位置一直性好。
适宜冲薄料,可充分利用短料和边角余料,冲模面积又小。
而方案四工序较多,在弯曲时难以定位不能很好保证精度要求,既耗时间,生产效率又低,难以满足实际生产要求。
通过以上四种方案的比较分析,采用方案三较好。
3.2模具总体结构方案
复合模有两种结构形式,正装复合模和倒装复合模。
分析该零件成型后脱模方便性:
正装复合模成形后工件留在下模,需要上推出工件,取件不方便。
倒装复合模成型后工件留在上模,只要在上模装一副推件装置,且操作简便能自动拨料装置,技能提高生产效率又能满足生产。
故采用倒装复合模。
3.3排样设计与计算
1.排样方式的确定
该零件材料厚度较薄,尺寸小,图形为规则的长方形,且四边无断面粗糙度要求和四角都为尖角,因此可采用直排排样的少、无废料的排样方式和有废料排样方式,然而根据条料的尺寸规格标准只能采用有废料排样方式。
2.毛坯展开尺寸的计算
毛坯展开尺寸(查工具书)按图分段计算毛坯展开长度。
弯曲处的最小圆角半径r=1.5≥0.5t(其中t=0.25mm),由于圆角半径较大,弯曲变形区料厚变薄不严重,断面畸变较少,可以按毛坯长度等于中性层展开长度的原则计算毛坯长度。
查得计算公式:
L=2a+b+c+d+3.14(r1+x1t)+3.14(r2+x2t)
查冲压模具设计指导书表3-6得a=9mmb=9mmc=14mmd=19mmt=1.5mm
查冲压模具设计指导书表3-8得x1=0.41x2=0.42
计算可得L=72.68mm
3.确定搭边值
经多次排样计算决定采用直对排法,查最小搭边值表可知,厚度1.5的长大于50mm的搭边值a=2.0mm,a1=1.8mm初图如下图。
4.确定板料规格和裁料方式
根据条料的宽度尺寸,选择合适的板料规格,使剩余的边料越小越好。
查《冲压模具与设备》表2-5知,该零件的宽度用料为710,宜选择1.5mm×
710mm×
1000mm的板料规格为宜。
裁料方式既要考虑所选板料规格,冲制零件的数量,又要考虑裁料操作的方便性,该零件以纵裁下料为宜。
对于较大型的零件,则着重考虑冲制零件的数量,以降低零件的裁料费用。
5.计算条料的利用率
代入数据得η=〔288×
(76.68×
30-π4(10×
10+2×
5×
5)〕﹙710×
1000)=87.73%
3.4冲压力及压力中心计算
1.第一道工序倒装复合模冲裁力计算
1)冲裁力F。
查表钢20的抗拉强度为:
=427Mpa
由
已知:
L=76.68×
2+30×
2+2×
5π+10π=276.16mm
所以:
Fp=1.3Lt=274.8×
1.5×
427=176009.4N
2)卸料力Fx
Fx=KxFp,Kx=0.04
Fx=KxFp=0.04×
176009.4=7040.376N
3)冲孔推件力Ft
Ft=nKtFp
式中n-梗塞件数量,取n=4
Kt-推卸料力系数,取Kt=0.05
代入公式得Ft=4×
0.05×
176009.4=35201.88N
4)第一道工序压力机公称压力的确定。
本模具是采用弹性卸料装置和下出料方式的冲裁模
Fz=Fp+Fx+Ft=218KN
根据以上计算结果,冲压设备拟选JH23-25。
2.弯曲力的计算
1)弯曲力的计算
在课本中查得,对于该四角弯曲件的自由弯曲力公式为:
F自=2.4btbαβ
式中:
σb-材料的抗拉强度k-安全系数α,β-系数b-弯曲件宽度
t-弯曲件厚度r-内弯曲半径
查得α=0.615β=0.675b=30σb=427MPak=1.3
代入公式得:
F自=2.4×
30×
427×
0.675×
0.615=12.76KN
2)弯曲力的计算
F校=P.A
其中,A-校正部分投影面积P-单位校正力(MPa)
根据图3-2计算得A=73×
30-π(52+2×
2.52)=2072.25mm2
查表知q=50MPa
代入公式计算得:
F校=50×
2072.25=103612.5N=103.6KN
3)顶件力或压料力计算
F=(0.3~0.8)F自=3.828~10.208KN
取F=6KN
4)弯曲时压力机的校核
a.对于有压料的自由弯曲:
F压力机≥F自+F
计算得:
F压力机≥12.76+6=18.76KN
b.对于校正弯曲:
F压力机≥F校
计算得F压力机≥F校=103KN
根据计算所需的冲压力,选用公称压力为160KN的压力机J23-16F
3.冲裁压力中心的确定
该工件的形状简单且比较规则,它的压力中心不在几何中心,经过计算获得计算如下:
X0=(L1X1+X2L2+L3X3)(L1+L2+L3)
因为其Y轴方向是对称的,所以Y轴的坐标是0.
计算可得X0=34.56mm
其压力中心图如下。
3.5.冲孔落料复合模凸凹模刃口尺寸计算
1.加工方法的确定。
结合模具及加工形状的特点此模具制造宜采用分开加工
法,将凸凹模分别进行加工时应考虑凸凹模的磨损方向,使其磨损之后还能
保证冲孔尺寸的要求。
2.分析尺寸的变化情况。
从冲孔落料的磨损状态中可以获得以下三类尺寸,
如下表。
磨后变小
磨后变大
磨后不变
冲孔
Φ10+0.360
63±
0.05
落料
730-0..52
3.具体计算:
(1)查表确定初始间隙:
Zmin=0.20×
1.5=0.30
Zmax=0.25×
1.5=0.375
ΔZ=Zmax-Zmin=0.0375-0.30=0.075
(2)计算凸凹模制造公差:
δ凸=0.4ΔZ=0.4×
0.075=0.03
δ凹=0.6ΔZ=0.6×
0.075=0.045
(3)代入公式计算各尺寸:
尺寸Ⅰ:
2XΦ5+0.30为冲孔磨后边小Δ=0.3,其中IT14级X=0.5
B凸=(Bmin+XΔ)
=(5+0.5×
0.3)
=5.150-0.03
B凹=(B+Zmin)
=(5.15+0.3)+0.0450=5.45+0.0450
尺寸Ⅱ:
Φ10+0.360为冲孔磨后边小Δ=0.36
B凸1=(B1min+XΔ)
=(10+0.5×
0.36)0-0.03=10.180-0.03
B凹2=(B凸1+Zmin)
=(10.18+0.3)+0.0450=10.48+0.0450
尺寸Ⅲ:
730-0.74300-0.52落料后变大
A凹1=(A1max-XΔ)
=(73-0.5×
0.74)+0.0450=72.63+0.0450
A凸1=(A凹1-Zmin)
=(72.63-0.30)0-0.0.3=72.330-0.03
A凹2=(A2max-XΔ)
=(30-0.5×
0.52)+0.0450=29.74+0.0450
A凸2=(A凹2-Zmin)
=(29.74-0.30)0-0.03=29.440-0.03
尺寸Ⅳ:
0.05为磨后不变尺寸,其中Δ=0.1mm
C=(Cmin+Δ∕2)±
Δ∕8=(62.95+0.1∕2)±
0.1∕8=63±
0.0125mm
3.6弯曲凸凹模间隙计算
弯曲U形时,必须选择适当的凸凹模间隙。
间隙过大,会造成U形件两边不半径,上宽下窄,降底工件的尺寸精度,间隙过小,使弯曲力增大,直边壁厚变薄,容易擦伤工作表面,加速凹模的磨损,降低凹模使用寿命,弯曲凸、凹模间隙是指单边间隙。
为了能顺利地进行弯曲,间隙值应梢大于板料的厚度。
同时应考虑下列因素的影响,弯曲件宽度较大时,受模具制造与装配误差的影响,将加大间隙的不均匀程度,因此间隙值应取大些。
宽度较小时间隙值可以取小些,硬材料则应取大些,弯曲件相对弯曲半径rt较小时可以取大些。
此外还应考虑弯曲件尺寸精度和板料厚度偏差的影响
综上所述,对于尺寸精度高要求一般的弯曲件板料为黑色金属时,单边Z可按下式计算:
Z2=(n+1)t
t-材料厚度n为间隙系数
查表得t=1.5mmn=0.1
计算得Z=1.65mm
3.7弯曲模凸、凹模工作尺寸计算
弯曲凸、凹模工作尺寸的计算与工件尺寸的标注形成有关。
一般原则是:
当工件标注外形尺寸时,应以凹模为基准件,间隙取在凸模上,当工件标注内行尺寸时,应以凸模为基准件,间隙取在凹模上,并来用配作法制模。
该弯曲一是标注为外形尺寸,应以凹模为计算基准,间隙取在凸模上。
其并没有什么特殊尺寸要求,故没有什么太大精度要求。
计算公式为:
Ld=46.67mmLp=45.02mm
对于弯曲模二,因为其注重的是外形尺寸25±
0.05mm,应以凹模为基准件,间隙取在凸模上。
其计算公式为:
Ld=(Lmax-0.75Δ)+σd0Lp=(Ld-Z)0-σp
σdσb-凸凹模制造公差,去(13-14)Δ
Z-凸凹模双面间隙
σd=σb=0.03Lmax=25.005Δ=0.1
Ld=24.9225+0.030Lp=24.82250-0.03
3.8凸模与凹模的圆角半径
(1)凸模圆角半径
弯曲件的相对弯曲半径rt较小时,凸模角半径rp可取弯曲件的内弯曲半径r,但不能小于允许的最小弯曲半径。
如果rt值小于最小相对弯曲半径,应先弯成较大的圆角半径,然后再用整形工序达到要求的圆角半径。
当弯曲件的相对弯曲半径rt较大