检查表批量生产01Word文档格式.docx
《检查表批量生产01Word文档格式.docx》由会员分享,可在线阅读,更多相关《检查表批量生产01Word文档格式.docx(24页珍藏版)》请在冰豆网上搜索。
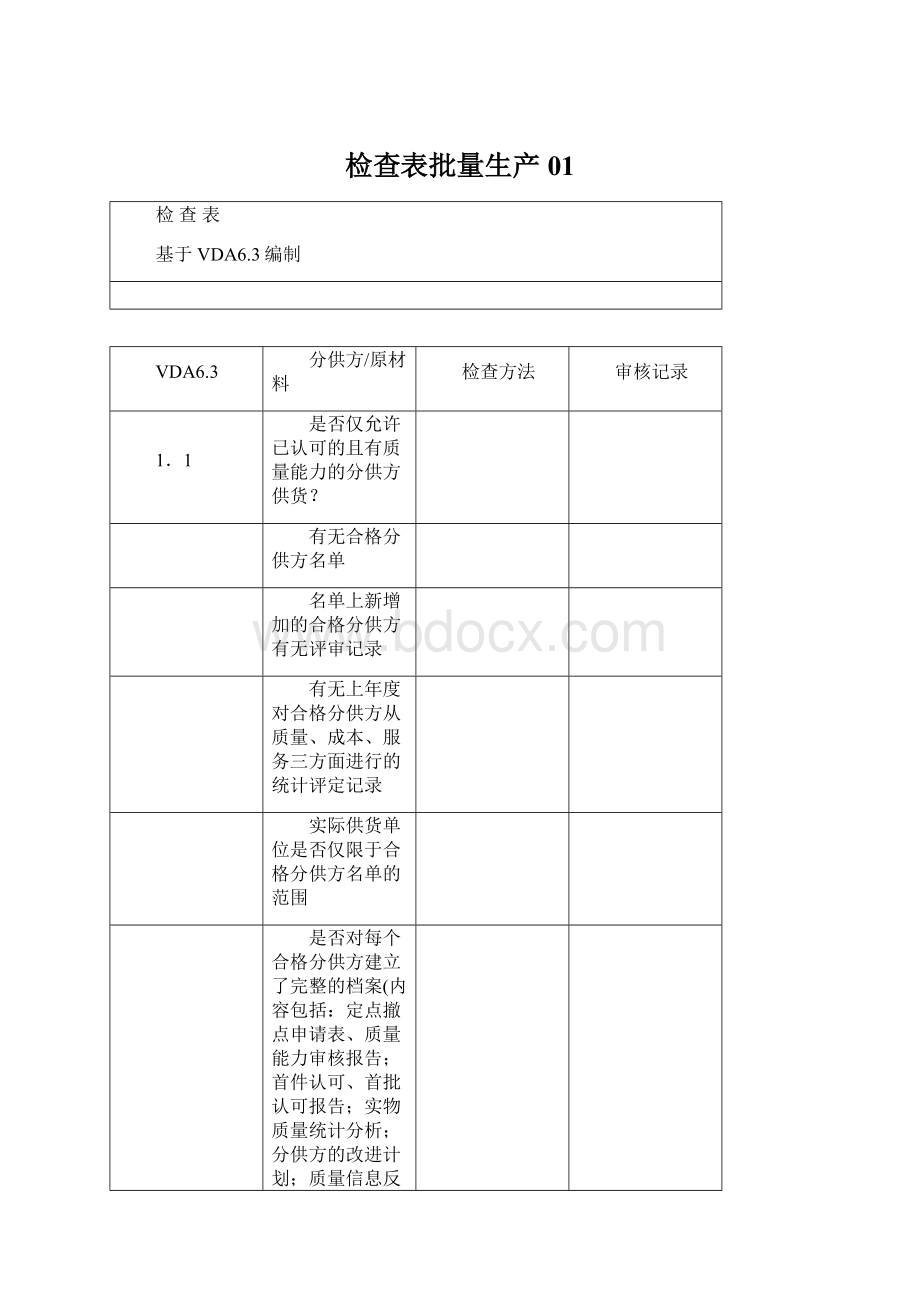
有无对分供方供货质量能力的审核计划及审核记录
1.3
是否评价供货实物质量,在出现与要求有偏差时是否采取措施?
有无分供方的自检报告和本厂进料检验的检验记录
有无定期对分供方的质量能力和实物质量进行统计评定的记录
若评定结果不佳,分供方有无质量改进计划以及对计划落实情况的验证记录
在出现与要求有偏差时,有无与分供方质量会谈的纪要
有无不合格品的退货程序及记录
有无改进后零件(含新开模和模具改进)的首件认可、首批认可记录
有无对重点缺陷/有问题的分供方的统计分析评定记录
1.4
1.4:
是否与分供方就产品与过程的持续改进商定质量目标并付之落实?
有无负责这项工作的由各相关部门组成的工作小组名单
有无与分供方商定的质量目标协议
协议中有无针对质量、价格、服务所规定的具体定量目标,包括质量能力>
85、一次合格率等
1.5
对已批量供货的产品是否具有所要求的批量生产认可并落实了所要求的改进措施?
对分供方的所有产品,在批量使用前必须对新产品、更改的产品及其生产过程进行认可。
有无认可报告
有无周期形式试验报告及由此制订的改进措施
主要特性的CPK是否符合>
1.67
1.6
是否对由顾客提供的产品执行了与顾客商定的方法?
有无就顾客提供的产品与顾客签订的质量协议
有无在出现缺陷、丢失、损坏等情况时与顾客的信息交流记录
有无反映顾客提供产品质量现状、质量历史的质量记录
1.7
原材料库存(量)状况是否适合于生产要求?
有无在原材料出现瓶颈时的紧急战略,是否采用一种材料有二家合格分供方
库存状况是否能满足合同中顾客提出的所有要求,保证生产计划进度,实现准时化生产
策划库存量时是否考虑了先进先出
对原材料库存是否规定了最高/最低库存量
1.8
原材料/内部剩余料是否有合适的进料和储存方法?
仓库环境条件是否适宜,有无漏雨、返潮、发霉
有无易受气候条件影响的原材料/内部剩余料清单
有无混批混料现象
是否执行了先进先出
下雨天厂内运输是否会淋湿原材料
标识是否完整齐全(包括批次号、检验状态、加工状态),有无可追溯性
账卡物是否相符
对不合格品,可疑物品有无隔离措施
材料包装是否符合要求
库房中的存放器具、运输器具是否适宜和干净,有无适合码放的托架、箱子
材料的有效期是否保证,如果过期如何处理
有无消防措施
1.9
员工是否具有相应的岗位培训?
是否接受过产品规范、顾客要求、包装知识、产品加工、统计方法、因果图、8D方法等内容的培训
有无采购员、外协评审员、包装检验员、库房管理员的培训记录
生产(人员/素质)
2.1.1
是否对员工委以监控产品质量/过程质量的职责和权限?
有无8D小组等明确员工参与改进项目的措施
过程自检的职责是否落实
过程认可、设备点检、首件检验、末件检验的职责是否落实
制作并分析控制图的职责是否落实,控制对象是否明确
有无关于终止生产权的规定,是否明确规定了检验员对不合格产品、可疑产品、紧急转序状态的隔离职责
2.1.2
是否对员工委以生产设备/生产环境的职责和权限?
保持生产环境整齐清洁的职责是否落实
设备日保养和报请维修的职责是否落实
设备零件准备和储存的职责是否落实
检测设备点检和报请检修校准的职责,计量器具校验和标定的职责是否落实
2.1.3
员工是否适合于完成所交付的任务,并保持其素质?
是否进行了必要的培训,包括应知应会,产品,产品缺陷,安全生产
操作工有无上岗证
从事某些特殊作业、过程、试验或检验的人员有无资格证书
从事SPC的员工是否接受过培训,他们要注意哪些偏差做哪些工作是否明确
2.1.4
是否有人员配置计划及有关岗位顶替的规定?
有无人员配置计划和顶岗计划
配置计划中是否考虑了缺勤因素
顶岗人员是否有资格证明
有无所有检验人员每年一次的视力测定记录
2.1.5
是否有效地使用了提高员工工作积极性的方法?
是否开展了质量管理的宣传活动,促进员工的投入意识
有无员工提出的书面改进建议
有无员工在参加培训、开展质量小组方面的志愿行动
病假率是否低
对质量改进的贡献是否进行鼓励
生产(生产设备/工装)
2.2.1
生产设备/工装模具是否能满足产品特定的质量要求?
有无针对产品重要特性或过程参数进行的机器能力调查记录和过程能力调查记录
有无对重要参数实施强制控制/调整的规定
设备的上下料装置是否能保证满足产品质量要求
有无设备/工装模具的维修保养计划
设备有无偏离规定值时的报警、自动断电装置
2.2.2
在批量生产中使用的检测、试验设备是否能有效地监控质量要求?
检测设备、试验设备是否都处在正常工作状态,设备是否够用
有无重要检测设备测量精度/检具能力的调查记录
有无对试验数据的采集和分析记录
有无检具标定的证明
有无标样管理制度
2.2.3
生产岗位、检验岗位是否符合要求?
各工作岗位(包括返工岗位)是否都符合整齐清洁,能方便地进行零部件鉴定、样件存放、文件阅读、填写记录、更换工具
各工作岗位(包括返工岗位)的照明是否都符合要求,如何检验照明度够否
各工作岗位(包括返工岗位)是否会对环境带来污染
各工作岗位(包括返工岗位)以日产量所需部件数为尺度,有无足够的周转货架、容器,有无防止混批混料的措施
有无安全生产的措施,员工知道否
有无机器失效、工伤事故等出现时的紧急处理规程,员工知道否
2.2.4
生产文件和检验文件中是否标出所有的重要技术要求,并坚持执行?
在生产岗位和检验岗位上有无相应的工艺文件、检验文件、操作指导书
检验规范中是否对特性值、检验设备、检验方法、检验频次作了明确规定
过程参数和检验特性是否都标明了公差
是否明确了关键工序,有无关键尺寸、功能特性、工艺参数
对关键项目是否作了控制图,控制图的控制界限是如何确定的
如果没有合适的SPC设施,文件要求的关键项目是否仍得到控制
有无机器能力证明和过程能力证明
有无发现偏差时的记录以及为此而采取的措施记录
2.2.5
对产品调整/更换是否有必备的辅助器具?
有无产品调整计划
有无灵活的模具更换装置
有无极限标样
2.2.6
是否在生产开始时进行岗位点检/认可,并记录调整参数或偏差情况?
有无批量生产认可的检验指导书
岗位点检/认可的职责是否落实
下列情况是否都作了认可,有无记录(新产品、更改过的产品、过程中断半天以上、更换材料批次号、修理设备、更换设备、更改模具检具、更改生产参数)
如果在抽取检验样品后生产继续进行,有无将这些产品在样件认可前隔离的证明
返修件的物流是否清楚地固定下来,有无返修指导书
2.2.7
是否按时落实要求的纠正措施并检查其有效性?
纠正措施是否涉及到从原材料到顾客使用的整个生产过程链
有无对纠正措施有效性的检查记录
有无过程FMEA分析表
有无针对风险分析,缺陷分析,内部审核而制订的改进计划并按时落实
有无内部抱怨记录
顾客抱怨记录是否按程序规定执行
用户调查表是否按程序规定执行
生产(运输/搬运/储存/包装)
2.3.1
产品数量/生产批次的大小是否按需求而定,是否有目的地运往下道工序?
有无足够、合适的运输器具
产品摆放是否实行定置库位
各工序之间是否执行了先进先出
是否向下道工序只供合格件
是否实现了最小/无中间库存
2.3.2
产品/零件是否按要求储存,运输方式/包装方法是否按产品/零件的特性而定?
对产品/零件的储存时间有无控制措施
每个包装箱及单个货次是否有明确清楚的标识
是否符合整齐清洁,不超装的要求
包装是否经过审核,是否符合防损伤的要求
储存时是否实行零件定置
生产作业场地是否规定了产品通道,发货仓库是否适宜发货操作
下雨天发货运输是否会淋湿货物
2.3.3
废品、返修件和调整件以及车间内的剩余料,是否坚持分别储存与标识?
有无用于废品、可疑品、返修件的隔离库或隔离区
有无标识明显的废品箱,返修品箱,调整设备件箱
返修工位是否确定
缺陷产品上有无标明缺陷特性的标识,
2.3.4
整个物流是否能确保不混批不混料,并保证追溯性
整个物流有无批次号、工作状态、检验状态、使用状态的标识
有无物料超过有效期的情况
无效标识是否都去除干净
是否能保证整个物流链的可追溯性
2.3.5
模具/工装、设备、检具是否按要求存放?
对不使用的和未认可的模具/工装、设备、检具是否进行了管理
模具、设备的存放是否符合防受损的要求
模具、设备的存放是否符合整齐清洁
是否执行了定置存放
有无模具、设备发放的管理规定
存放的模具、设备上有无标识
存放的模具、设备有无明确的认可状态与更改状态
生产(缺陷分析/纠正措施/持续改进)
2.4.1
是否完整记录质量数据/过程数据并具有可评定性?
是否及时收集了全部质量数据和过程数据(包括流转卡、过程参数运行记录、首检记录、巡检记录)
有无缺陷收集卡
有无控制图
有无记录特殊事例(设备停机、参数更改、停电)的当班记录本
2.4.2
是否用统计技术分析质量数据/过程数据并由此制订改进措施?
是否应用了SPC、排列图、因果图等质量统计分析方法
是否通过分析明确了问题的责任部门
有无责任部门负责制订的改进措施
2.4.3
在与产品要求/过程要求有偏差时,是否分析原因并检查纠正措施的有效性?
有无出现产品缺陷/过程缺陷时的工作程序
有无质量小组活动记录
有无FMEA表
有无过程能力分析报告
有无补充的尺寸、材料、功能及耐久试验报告
有无纠正措施有效性的验证记录
有无8D报告
2.4.4
对过程和产品是否定期进行审核?
有无过程审核计划
有无产品审核计划
审核中发现的偏差是否报告给责任者
有无对改进措施进行跟踪的记录
2.4.5
对产品和过程是否进行持续改进?
有无针对降低成本、减少浪费、减少返修返工、改进过程控制状态、提高过程能力指数、提高设备利用率、降低生产流转周期、降低库存量、提高出勤率等等方面的持续改进计划
2.4.6
对产品和过程是否有确定的目标值,并监控是否达到目标?
对出勤率、生产数量、成品率、流转时间、缺陷成本、过程能力指数等有无明确的目标值(包括中长期目标)
有无反映目标值和实际完成对照情况的图表
目标值是否更新
服务/顾客满意程度
3.1
在发货时产品是否满足了顾客的要求?
是否满足了和顾客签订的质量协议
是否满足了顾客在对供方审核时提出的要求
是否通过了耐久试验、功能检验
检测设备是否处在合格状态
是否采用了商定的检测方法
是否实施了发货审核
3.2
是否保证了对顾客的服务?
有无和顾客各部门对口的人员名单
有无顾客访问纪要
有无关于改进措施的通知
有无关于产品更改/过程更改/移地生产(包括分供方)的通知
有无试制样品认可报告、首批认可报告,重新认可报告
有无与要求出现偏差的信息记录
3.3
对顾客抱怨是否能快速反应并确保成品供应
有无出现意想不到问题时的紧急情况计划(其它生产可能、包装、运输)
3.4
在与质量要求有偏差时是否进行了缺陷分析并实施改进措施?
有无对使用中出现的失效产品进行分析的记录,分析是否及时
有无对缺陷特性所作的排列图
有无证明各有关部门(内部/外部)介入的记录
有无解决问题的8D报告
有无改进措施有效性的检查记录
对不合格产品能否确保准确无误的可追溯性
3.5
执行各种任务的员工是否具备所需的素质?
是否接受过产品规范、顾客要求、产品加工过程、产品使用方法、缺陷统计方法、因果图、8D方法等内容的培训
有无所有各类人员,包括管理人员的培训记录