塑料桶注射模具毕业设计Word格式文档下载.docx
《塑料桶注射模具毕业设计Word格式文档下载.docx》由会员分享,可在线阅读,更多相关《塑料桶注射模具毕业设计Word格式文档下载.docx(39页珍藏版)》请在冰豆网上搜索。
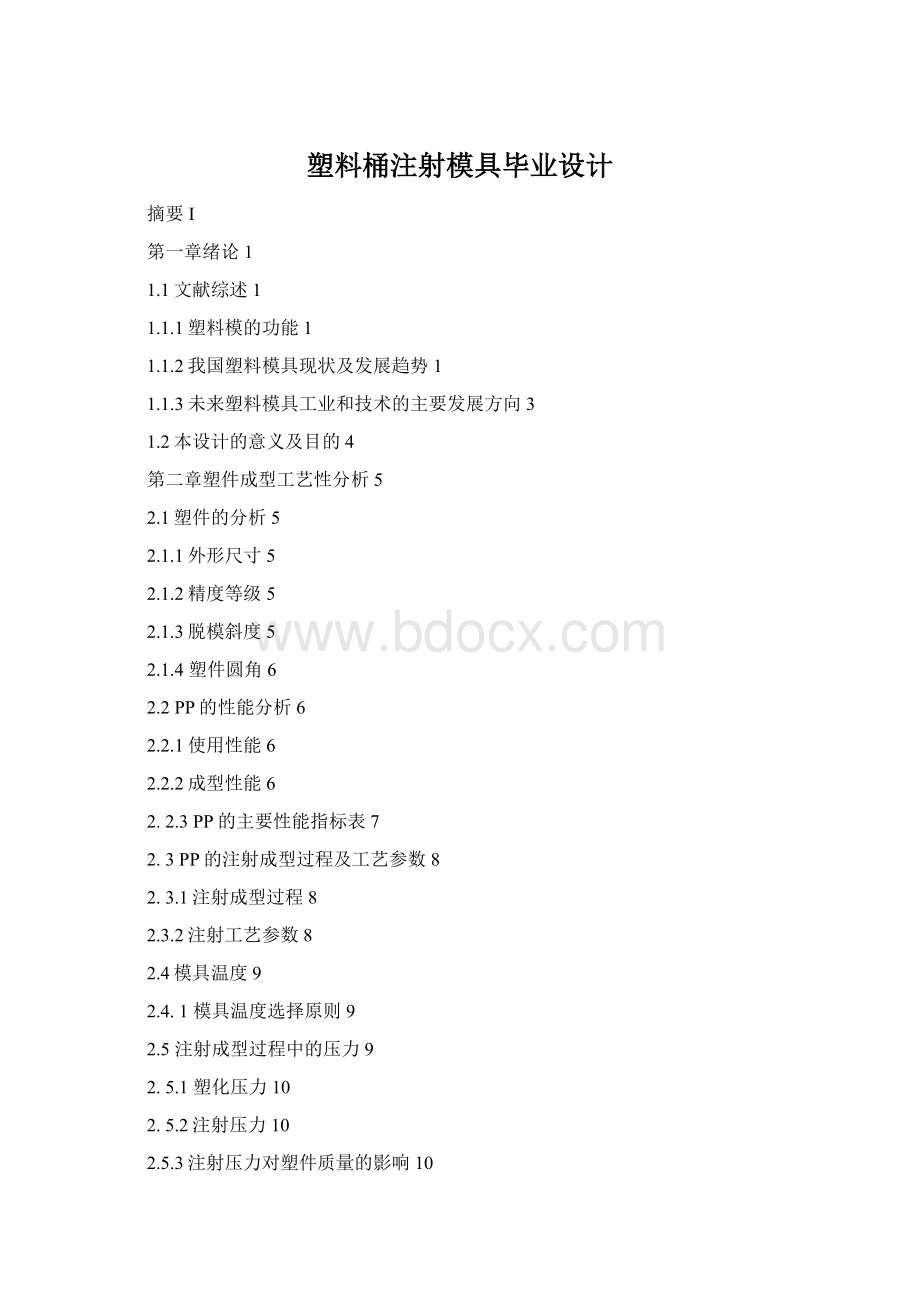
3.3.4最大注射压力与模腔压力的计算16
3.3.5锁模力的计算16
3.3.6注射机型号的选定17
3.3.7注射机有关工艺参数的校核17
第四章浇注系统的设计19
4.1浇注系统的组成19
4.2浇注系统的作用及设计影响因素19
4.3主流道的设计20
4.3.1主流道的材料21
4.3.2主流道的表面精度21
4.3.3主流道尺寸21
4.3.4主流道当量半径21
4.4分流道的设计21
WOrd格式.
第五章成型零件的结构设计及计算23
5.1注射模具型腔的结构设计23
5.2注射模具型芯的结构设计24
5.3成型零件的力学分析24
第六章模架的确定25
6.1标准模架25
6.2注射模的典型结构25
6.3各模板尺寸的确定25
第七章排气槽的设计27
7.1排气系统的作用27
7.2排气结构设计27
7.3排气槽的尺寸28
7.4间隙排气28
第八章导向与定位机构设计29
&
1导向机构的设计29
2导柱设计29
3导柱的校核30
4导套设计31
5定位机构设计32
第九章脱模推出机构的设计34
9.1脱模推出机构的设计原则34
9.2脱模机构的确定34
第十章冷却系统的设计35
10.1温度调节系统35
10.2冷却介质35
10.3冷却系统的简单计算35
10.3.1单位时间注入模具中的塑料熔体的总质量M。
35
10.3.2确定单位质量的塑件再凝固时所放出的热量Qs,36
10.3.3计算冷却水的体积流量么36
10.3.4确定冷却水的直径d36
10.3.5冷却水在管的流速卩37
10.3.6求冷却管壁与水交界面的膜传热系数h37
10.3.7计算冷却水通道的导热总面积A37
10.3.8计算模具所需冷却水管的总长L37
10.3.9冷却水路的根数X37
10.4冷却系统设计37
第十一章装配39
11.1模具的装配39
11.1.1具体的工艺要求39
11.1.2模具的装配方法39
11.2模具的安装及加工要点39
参考文献41
致42
本次设计的题目是PP塑料桶注射成型工艺与模具设计,要求设计出用于生产PP塑料桶的注射模具。
初步对该塑件的结构分析可知:
由于该塑件的面积较大,因此采用直浇口和顺序分型,并且采取一模一腔的结构形式。
本次设计的具体过程如下:
首先对塑件的成型工艺性能进行分析。
这包括对塑件的结构尺寸的分析和成型塑件的材料PP各项性能的分析。
其次,就是如何合理的选择注射机。
选择正确的注射机是本次设计的基础。
再次,就是拟定模具的结构形式。
模具的结构形式必须根据塑件的结构尺寸,通过计算进行合理的选择。
第四步就是浇注系统的设计。
第五步是本次设计的重点,成型零部件的设计和计算。
通过本次设计,使我对注塑模具的结构和性能有了全面的了解,并且学到了模具设计的基本知识,为以后踏入社会工作打下了基础,可以说是受益匪浅。
关键词:
塑料模具,注射机,浇注系统
AbStraCt
ThiSdesignisentitledPPPlaStiCbarrelinjectionInOIdingPrOCeSSandIIlOIddesign,todesignforthePrOdUCtiOnOfPPinjectionmoldPlaStiCbucket・ThrOUghtheinitialStructuralanalysisOfPlaSticparts,WeCarISeethatasaresultOftheIargerPlaStiCparts,SOWeCantaketheUSeOfStraightgateandtheOrderOfsub-type,andtotakeaIIIOIdformaCaVityStrUCture.
ThePrOCeSSeSOftheSPeCificdesignareasfollows:
FirStOfal1,analyzingPlaStiCmoldingPrOCeSSPerfOrInanCe.ItincludesanalysisOftheStrUCtUreOfPlaStiCPartSandanalysisOfthePerfOnnanCeOfPP.TheSeCOndStePishowtoch∞seareasonableinjectionmachine・ChOOSingtherightinjectionIlIaChineisthebasisOfthisdesign・ThethirdStePistodeveloptheStrUCtUre
OftheformOfInOld・TheStrUCtUreOftheformOfmoldPIaStiCPartSmustbebasedontheStrUCtUreSiZe・ThefourthStePisthedesignOfgatingSyStem・ThefifthStePisthefocusOfthisdesign.
ThrOUghthisdesign,IIearrltheStructureandPrOPertieSOfPlaStiCmold,andIgotthebasicknowledgeOfInOIddesign・ThiSisVerygoodformetoWOrkinSOCietyinfuture.
KeyWOrdS:
PIaStiCMold,injectionmachine,runnerSyStenl.
第一章绪论
1.1文献综述
1.1.1塑料棋的功能
模具是工业产品生产用的重要工艺装备,在现代工业生产中,60%-90%的工业产品需要使用模具,模具工业已经成为工业发展的基础,许多新产品的开发和研制在很大程度上都依赖于模具生产,特别是汽车、摩托车、轻工、电子、航空等行业尤为突出。
而作为制造业基础的机械行业,根据国际生产技术协会的预测,21世纪机械;
制造工业的零件,其粗加工的75%和精加工的50%都将依靠模具完成,因此,模具工业已经成为国民经济的重要基础工业。
模具工业发展的关键是模具技术的进步"
。
1.1.2我国塑料模具现状及发展趋势
近年来,我国的模具工业一直以每年13%左右的增长速度快速发展。
据预测,我国模具行业在“十五”期间的增长速度将达到13%〜15%。
模具钢的需求量也将以年12%的速度递增,全国年需求量约70万吨左右,而国产模具钢的品种只占现有国外模具钢品种的60%,每年进口模具钢约6万吨。
我国每年进口模具约占市场总量的20%左右,已超过10亿美元,其中塑料与橡胶模具占全部进口模具的50%以上;
冲压模具占全部进口模具约40%。
中国的模具企业大都是中小企业,从作坊式的企业成长起来,甚至目前仍有许多模具企业是作坊式的管理,在模具交货期、成本、质量的控制方面问题层出不斷。
面对激烈的市场竞争,落后的管理手段和水平,使模具企业中的管理和技术人员只有疲于奔命。
因此,模具制造企业要提高管理水平,具备快速反应和及时调整的能力,没有一套先进的管理系统实现管理的信息化是很难做到的。
通过信息化建设,实现模具制造.所谓信息化的模具企业,就是在模具企业应用INTERNET、ERP等信息化技术,把模具企业上下游业务过程,技术沟通过程,以及模具企业部业务管理过程,以IT形式固定下来,最终提高模具企业的经营管理水平,提高模具企业运转的效率。
目前国的模具制造企业相当一部分为民营企业或个体户,受资金、场地、技术、信息交流等诸多因素的局限,相当一部分是依靠传统设备和手工加工制造完成,以至难以形成规模,只能生产一些中、低档模具,很难引进先进的制模技术及先进的制模设备。
这就造成了中低档模具市场竞争加剧。
有些模具企业为了揽活,不惜互相降低价格,而低价格必然影响产品质量,结果是坑了客户,误了同行,也害了自己。
模具企业应该通过协作、整合等方式,化单打独拼、恶性竞争为竞合共赢,打破"
同行是冤家"
的狭隘思想,通过行业自律来维持模具市场的公平、良性竞争。
现代模具工业早已走出以前手工制模的时代,进入了数字化时代,实现了无图化生产,靠电脑设计,通过电脑输入数据加工制作模具。
而国大多数模具生产企业沿用的生产模式,依靠传统设备加工制造,依靠实物测绘代替模具设计,依靠老师傅的技术经验培养人才,依靠作坊式经营打天下,依靠低价竞争求生存、求市场。
国模具工业的落后,也与政府相关部门对模具在现代制造业中的重要性认识不够有关。
国家自1997年起,对达到一定规模的专业模具生产企业给予了一定的扶持政策,但能够享受的企业毕竟有限,而且今年是政策执行的最后一年,模具行业目前迫切需要一个长久的扶持政策。
国家对工业产品实行的是增值税制,模具的原材料价格低,而成品模具的售价却很高,增值率惊人,因而缴纳的增值税也高得很。
据国家税务局的统计,模具行业的实际税负比其他行业要高出5.07个百分点。
但模具在人力、技术、设备等方面却需WOrd格式.
要高投入,加上是单件生产,形不成批量,因此,模具的净值虽高,所获的真正利润却不高。
因此,政府对模具行业的扶持十分重要。
政府部门可通过协调划出部分土地,由行业部自筹资金,在各地建立一些模具加工区。
这种加工区可引入三类企业。
一是潜力大、发展速度快的企业;
二是基础差、在加大投入中促变化、求发展的企业;
三是具有专业设备加工能力的原材料设备供应商。
通过提供相关服务达到整合资源,互相配套的目的。
这样才有可能使模具业走出目前的不利境地。
目前,CAD/CAM技术的推广已由“甩图板”阶段跨入到了深化应用阶段。
CAPP技术的应用,可以大大提高企业工艺编制的效率和准确性;
Pl)M系统的应用,可以对产品开发数据进行有效的管理JIIS/ERP系统的应用,则可以从根本上降低企业的成本,提高生产和管理效率。
这些系统之间实现信息的集成和功能上的配合,并逐步实现企业的全面信息化,已成为CAD/CAM技术深化应用的主题,是模具发展的第二次变革。
网络企业的建立,总的来讲是基于INTERNET技术和计算机管理技术,并触合了
EPR、CRM、SCM、PM等技术,以及一些行业标准化的规。
通过INTERNET技术,模具企业可以跟国外客户建立联系,开拓更广阔的市场;
进行企业与国外客户业务、技术的沟通;
建立企业和客户之间的接口。
ERP技术帮助企业规和管理部业务流程,提升模具企业的管理水平;
并且极优化和缩短企业部的流程,提高竞争力。
把INTERNET技术和ERP技术结合起来,还可以实现远程异地办公,提高企业的快速反应能力,更加有效地管理企业。
CRM技术可以帮助模具企业加强管理客户关系,对客户的需求做出快速反应和处理。
SCM技术帮助模具企业加强供应商的管理,进一步降低采购成本和开拓更多的供应渠道“。
1.1.3未来塑料模具工业和技术的主要发展方向
目前,全世界模具的年产值约为650亿美元,我国模具工业的产值在国际上排名位居第三位,仅次于日本和美国。
虽然近几年来,我国模具工业的技术水平已取得了很大的进步,但总体上与工业发达的国家相比仍有较大的差距。
例如,精密加工设备还很少,许多先进的技术如CAD/CAM/CAE技术的普及率还不高,特别是大型、精密、复杂和长寿命模具远远不能满足国民经济各行业的发展需要。
纵观发达国家对模具工业的认识与重视,我们感受到制造理念旧则是我国模具工业发展滞后的直接原因。
模具技术水平的高低,决定着产品的质量、效益和新产品开发能力,它已成为衡量一个国家制造业水平高低的重要标志。
因此,模具是国家重点鼓励与支持发展的技术和产品,现代模具是多学科知识集聚的高新技术产业的一部分,是国民经济的装备产业,其技术、资金与劳动相对密集。
目前,我国模具工业的当务之急是加快技术进步,调整产品结构,增加高档模具的比重,质中求效益,提高模具的国产化程度,减少对进口模具的依赖。
现代模具技术的发展,在很大程度上依赖于模具标准化、优质模具材料的研究、先进的设计与制造技术、专用的机床设备,更重要的是生产技术的管理等。
21世纪模具行业的基本特征是高度集成化、智能化、柔性化和网络化。
追求的目标是提高产品的质量及生产效率,缩短设计及制造周期,降低生产成本,最大限度地提高模具行业的应变能力,满足用户需要。
可见,未来我国模具工业和技术的主要发展方向将是:
——大力普及、广泛应用CAD/CAM/CAE技术,逐步走向集成化。
现代模具设计制造不仅应强调信息的集成,更应该强调技术、人和管理的集成。
——提高大型、楮密、复杂与长弃命模具的设计与制造技术,逐步减少模具的进口量*增加模具的出口量。
——在塑料注射成型模具中,积极应用热流道,推广气辅或水辅注射成型,以及高压注射成型技术,满足产品的成型需要。
——提高模具标准化水平和模具标准件的使用率。
模具标准件是模具基础,其大应用可缩短模具设计制造周期,同时也显著提高模具的制造精度和使用性能,大提高模具质量。
我国模具商品化、标准化率均低于30%,而先进国家均高于70%,每年我们要从国外进口相当数量的模具标准件,其费用约占年模具进口额的3%〜8%。
——发展快速制造成型和快速制造模具,即快速成型制造技术,迅速制造出产品的原型与模具,降低成本推向市场。
——积极研究与开发模具的抛光技术、设备与材料,满足特殊产品的需要。
——推广应用高速统削、超精度加工和复杂加工技术,满足模具制造的需要。
——开发优质模具材料和先进的表面处理技术,提高模具的可靠性。
——研究和应用模具的高速测量技术、逆向工程与并行工程,最大限度地提高模具的开发效率与成功率。
在科技发展中,人是第一因素,因此我们要特别注重人才的培养,实现产、学、研相结合,培养更多的模具人才,搞好技术创新,提高模具设计制造水平。
在制造中积极采用多媒体与虚拟现实技术,逐步走向网络化、智能化环境,实现模具企业的敏捷制造、动态联盟与系统集成。
我国模具工业一个完全信息化的、充满着朝气和希望而又实实在在的新时代即将到来'
1.2本设计的意义及目的
当今世界工业界认为“模具是进入富裕社会的原动力”“模具是材料加工业中的帝王”“模具就是黄金”。
作为五大经济支柱产业之一,模具行业的发展水平反映一个国家的经济水平。
特别是在汽车、家电、玩具等行业,模具水平更是起到决定其命脉的作用。
模具工业发展的关键是模具技术的进步⑶。
第二章塑件成型工艺性分析
2.1塑件的分析
2.1.1外形尺寸
从零件图上分析,该零件为斜圆柱筒形,塑件成型壁厚为2.OmIn,壁厚的选择对注塑成型有利。
该零件高度为150ιιmι,口径15Omm,主体直径IIOnli】】。
注塑深度适中。
外沿有圆弧状翘起,在各处转角处均有圆角。
本零件有足够的脱模斜度,对模具设计有利。
综上所述,本零件的模具设计为简单难度。
2.1.2精度等级
影响塑件精度的因素很多,塑料的收缩、注塑成型条件(时间、压力、温度)等,塑件形状、模具结构(浇口、分型面的选择),飞边、斜度、模具的磨损等都直接影响制品的精度。
按SJ1372—1978标准,塑料件尺寸精度分为8级,由此査塑料模具设计手册可知,本塑件宜选用一般精度5级,每个尺寸的公差不一样,有的属于一般精度,有的属于高精度,该按实际公差进行计算[4]。
2.1.3脱模斜度
由于塑件冷却后产生收缩,会紧紧地包住模具型芯、型腔中凸出的部分,使塑件脱出困难,强行取出会导致塑件表面擦伤、拉毛。
为了方便脱模,塑件设计时必须考虑与脱模(及轴芯)方向平行的、外表面,设计足够的脱模斜度。
只有塑件高度不大、没有特殊狭窄细小部位时,才可以不设计斜度。
最小脱模斜度与塑料性能、收缩率、塑件的几何形状等因素有关。
一般型芯的脱模斜度要比型腔大,型芯长度及型腔深度越大,则斜度越小。
在不影响外观的情况,脱模斜度尽量大一点,以便脱模。
不同材料的推荐脱模斜度,见表2-1[,4]o
表2-1各种材料推荐的脱模斜度
材料脱模斜度
聚乙烯,聚丙烯,软聚氯乙烯30'
〜1'
ABS,尼龙,聚甲醛,氯化聚瞇,聚苯瞇40'
〜「30'
硬聚氯乙烯,聚碳酸酯,聚砚,聚苯乙烯,有机玻璃50~〜2'
热固性塑料20'
2.1.4塑件圆角
塑料制件除了使用上要求采用尖角之处外,其余所有转角处均应尽可能采用圆弧过渡,因为当制件带有尖角时,往往会在尖角处产生应力集中,在受力或受冲击振动时会发生破裂。
塑件制品设置圆角,能使其成型流动性能好,成型顺利进行。
当塑件结构无特殊要求时,塑件的各连接处均应有半径不小于0.5-1.OnlnI的圆角
2.2PP的性能分析
2.2.1使用性能
PP是一种半结晶性材料。
它比PE要更坚硬并且有更高的熔点。
由于均聚物型的PP温度高于0°
C以上时非常脆,因此考虑使用的PP材料是加入了1~4%乙烯的无规则共聚物或更高比率乙烯含量的钳段式共聚物。
共聚物型的PP材料有较低的热扭曲温度(IOOoC)、低透明度、低光泽度、低刚性,但是有有更强的抗冲击强度。
PP的维卡软化温度为150°
C。
由于结晶度较高,这种材料的表面刚度和抗划痕特性很好,PP不存在坏境应力开裂问题;
低MFR的PP材料抗冲击特性较好但延展强度较低,PP也不像PE那样在高温下仍具有抗氧化性。
聚丙烯(PP)是常见塑料中较轻的一种,其电性能优异,可作为耐湿热高频绝缘材料应用。
2.2.2成型性能
(1)结晶性塑料,吸湿性小,可能发生熔体破裂,长期余热金属接触已发生分解;
(2)流动性极好,溢边值0.03mm左右;
(3)冷却速度快,浇注系统及冷却系统的散热应适度;
(4)成型收缩围大,收缩率大,易发生缩孔、凹痕、变形,取向性强;
(5)注意控制成型温度,料温低时取向性明显,尤其低温高压时更明显,模具温度低于50°
C以下塑件无光泽,易产生熔接痕、流痕;
90°
C以上时易发生翘曲、变形;
(6)塑件应壁厚均匀,避免缺口、尖角,以防止应力集中。
2.2.3PP的主要性能指标表冋
表2.2PP的性能指标
密度
g/cu】3
0.90〜0.91
质量体积
cm^/g
1.10〜1.11
吸水率
24h
0.01〜0.03
熔点、
OC
170〜176
熔融指数
g/1Omin
3.25
与钢摩擦因数
0.23
热变形温度
oC/0.45MPa
102〜115
泊松比
0.38
比热容
J∕(kg∙K)
1930
热导率
W∕(m∙K)
0.126
抗拉屈服强度MPa
37
弹性模量
GPa
0.89
2∙3PP的注射成型过程及工艺参数
2.3.1注射成型过程
(1)成型前的准备:
对PP的色泽、粒度和均匀等进行检验。
(2)注射过程:
塑件在注射剂料筒经过加热、塑化达到流动状态后,由模具的浇注系
统进入模具性强成型,其过程可分为冲模、压实、保压、倒流和冷却五个阶段O
(3)
塑件的后处理:
包括喷涂,热处理,雕刻等等。
2.3.2注射工艺参数同
表2.3PP注射工艺参数
注塑成型机类型
螺杆式
g∕cπι^
计算收缩率
%
1.0〜2.5
温度OC
80〜100
预热
时间h
1〜2
料筒温度OC
后段
160〜180
中段180〜200
前段200〜220
续表2.3
模具温度
°
C
80〜90
注塑压力
MPa
70〜140
注塑时间
20〜60
高压时间
0〜3
成形时间S
冷却时间
20〜90
总周期
50〜160
螺杆转速
r∕πιin
48
方法
——
后处理
时间h
2.4模具温度
2.4.1模具温度选择原则
(1)对于高粘度塑料,由于塑料熔体流动性差、充模能力弱,为了获得致密的组织,模具温度必须较高。
(2)对于粘度较小、流动性好的塑料,模具温度可以较低,这样可以缩短冷却时间、提高生产率。
(3)塑件壁厚较大或塑件较复杂时,充模和冷却时间较长,宜采用较高的模具温度,以减少塑件出现凹陷、减小塑件的应力。
(4)在满足注射要求的前提下,应采用尽可能低的模具温度,缩短冷却时间,提高生产率。
2.5注射成型过程中的压力
压力可分为塑化压力和注射压力。
塑化压力又称螺杆背压(针对螺杆式注射机),为注射机螺杆头部熔料在螺杆转动后退时所受到的压力。
注射压力是指注射时螺杆(柱塞)头部对塑料熔体所施加的压力。
2.5.1塑化压力
塑化压力的作用:
主要体现塑料的塑化效果及塑化能力。
增加塑化压力将提高熔体密实程度,增大熔体压力,增加剪切作用从而提高熔体温度,并使温度分布均匀。
但增大塑化压力若不提高螺杆转速,熔体在螺杆槽中将会产生较大的逆流和漏流,降低塑化能力。
通常情况下,塑化压力应在保证塑件质量的前提下越低越好,一般不超过2MPa。
2.5.2注射压力
注射机上常用压力表表示注射压力的大小,一般热塑性塑料在40〜130MPa之间,热固性塑料在100〜170MPa。
可以通