对多种氨回收工艺的综述Word格式.docx
《对多种氨回收工艺的综述Word格式.docx》由会员分享,可在线阅读,更多相关《对多种氨回收工艺的综述Word格式.docx(12页珍藏版)》请在冰豆网上搜索。
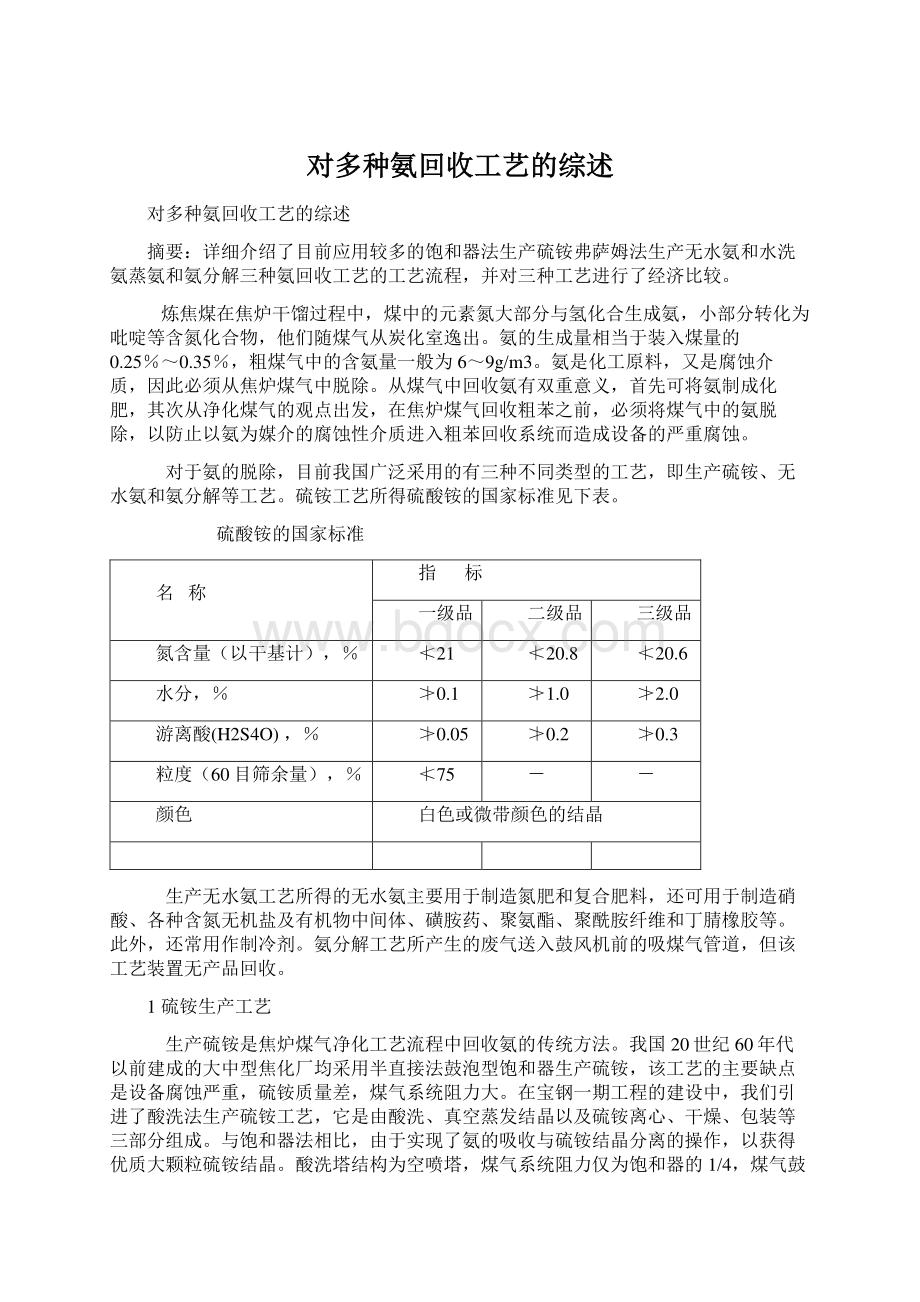
酸洗塔结构为空喷塔,煤气系统阻力仅为饱和器的1/4,煤气鼓风机的电耗可大幅度下降。
采用干燥冷却机将干燥后的硫铵进一步冷却,防止结块,有利于自动包装。
鞍山焦耐院将此工艺经改进后用于天津煤气二厂,装置投产后已通过了技术鉴定。
在宣钢和北焦的建设中,我们引进了间接法饱和器生产硫铵工艺,该工艺是从酸性气体中回收氨,其硫铵的质量比饱和器法好,但因在较高温度(100左右)下操作,对设备和管道材质的要求高,加之饱和器尺寸并不比半直接法小,因此投资高于半直接法。
在杭钢焦化厂,我们将此工艺用于蒸氨塔后氨汽生产硫铵,并已正常投产。
除上述方法外,鞍钢二回收从法国引进的二手设备喷淋式饱和器,以代替半直接法的鼓泡型饱和器。
喷淋式饱和器的特点是煤气系统阻力较小,设备尺寸可相对减小,硫铵质量有所提高。
国内已有不少厂家用其代替老式的鼓泡型饱和器。
但是,不管采用那种生产硫铵的工艺,从经济观点分析,其共同的致命缺点是硫铵的收入远远不够支付其生产费用。
下面重点介绍一下酸洗法和喷淋式饱和器生产硫铵的工艺。
(1)酸洗法生产硫铵工艺。
酸洗法硫铵生产工艺由氨的回收、蒸发结晶与分离干燥等3部分组成。
其工艺流程见图1.图1酸洗法生产硫铵工艺如图1所示,煤气自下而上经过酸洗塔,在酸洗塔分上下两段,均用含游离酸23的硫铵母液进行喷洒,煤气中的氨即与硫酸结成硫铵,从酸洗塔顶逸出煤气经除酸器分离出酸雾后送入煤气总管。
用泵将母液循环槽中的硫铵母液抽送至结晶槽,结晶槽的母液用循环泵抽出,经母液加热器加热后送入真空蒸发器,蒸发器在(绝压)11kPa压力和48下工作,母液因真空蒸发而浓缩,浓缩后的过饱和溶液经中心管自流至结晶槽底部。
含有小颗粒结晶的母液在结晶槽中部经循环泵抽出大量循环,使结晶不断长大,几乎不含结晶的母液在结晶槽上部溢流至满流槽,再用泵送回母液循环槽。
大颗粒结晶沉积在结晶槽底部用浆液泵送往供料槽。
蒸发器的真空是用二级蒸汽喷射造成的,蒸汽喷射器使用0.7MPa的中压蒸汽。
从蒸发器上部出来的汽体经第一凝缩器与第二凝缩器冷凝后排往热井。
含有大颗粒结晶的硫铵母液在供料槽内进行沉降分离,上部清液溢流回结晶槽,底部含有50结晶的母液进入离心机,滤液经滤液槽后再返回结晶槽。
硫铵结晶采用带冷风的干燥冷却器进行干燥、冷却。
酸洗法硫铵与老式饱和器硫铵工艺相比,有以下优点:
酸洗法工艺采用空喷塔,煤气系统阻力小,约为饱和器法的1/41/5,使风机电耗可以大大降低;
酸洗法工艺在酸洗塔内母液始终控制在不饱和状态,结晶颗粒是在真空蒸发结晶系统内形成,由于采用了大流量的母液循环,控制了晶核的形式,并使结晶有足够的成长时间,因而,可以获得大颗粒的优质硫铵结晶。
酸洗法硫铵的设备与管道均采用了超低碳不锈钢(OOCrl7Nil4Mo2),较好地解决了稀硫酸的腐蚀问题,酸洗塔可不设备品,大大减少了设备的维修工作量。
我国自行设计的酸洗法硫铵生产装置,将酸洗塔由一台两段改为二台各一段的空喷塔,这样,两台可以互为备用,便于连续、稳定生产。
(2)喷淋式饱和器法硫铵工艺。
喷淋式饱和器硫铵生产工艺与鼓泡式饱和器流程基本一样,只是将喷淋式饱和器代替鼓泡式饱和器。
喷淋式饱和器是将饱和器和结晶器连为一体,流程更为简化。
在此流程中采用母液加热器,从结晶槽顶部一部分母液通过加热器加热,再循环返回饱和器喷淋。
在饱和器底部控制一定的母液液位,母液从满流管流入满流槽。
在满流槽中除去焦油的母液流入母液贮槽。
母液循环泵从结晶槽上部抽出母液,送到喷淋室的环形分配箱进行喷洒,母液循环量为15L/m3。
吸收氨后的母液通过中心降液管向下流到结晶槽底部。
饱和器内母液酸度控制2030,结晶段的结晶体积百分比上限为3540,下限为4。
晶比达到25时,启动结晶泵抽取结晶,送往结晶槽提取硫铵。
在保证饱和器水平衡的条件下,一般饱和器母液温度保持在5055,煤气出口温度4448。
喷淋式饱和器的阻力一般为10002000Pa,为旧式鼓泡型饱和器的1/51/4。
饱和器后的煤气含氨可达到3050mg/m3。
其流程见图2。
图2喷淋式饱和器法生产硫铵工艺喷淋式饱和器的结构有如下特点:
喷淋室由本体、外套筒和内套筒组成,煤气进入本体后向下在本体与外套筒的环形室内流动,然后由上出喷淋室,再沿切线方向进入外套筒与内套筒间旋转向下进入内套筒,由顶部出去。
外套筒与内套筒间形成旋风分离作用,以除去煤气夹带的液滴,起到除酸器的作用。
在喷淋室的下部设置母液满流管,控制喷淋室下部的液面,促使煤气由入口向出口在环形室内流动。
在煤气入口和煤气出口间分隔成两个弧形分配箱,在弧形分配箱配置多组喷嘴,喷嘴方向朝向煤气流,形成良好的气液接触面。
喷淋室的下部为结晶槽,用降液管与结晶槽连通,循环母液通过降液管从结晶槽的底部向上返,不断生成的硫铵晶核,穿过向上运动的悬浮硫铵母液,促使晶体长大,并引起颗粒分级,小颗粒升向顶部,从上部出口接到循环泵,结晶从下部抽出。
在煤气出口配置有母液喷洒装置。
煤气入口和出口均设有温水喷洒装置,可以较彻底清洗喷淋室。
饱和器材质,国外引进的设备其材质均采用耐酸不锈钢制造,所用材料牌号为URANUS50(法国牌号);
我国引进的酸洗法酸洗塔材质为SUS316L,目前国内采用的喷淋式饱和器和母液加热器均采用SUS316L,它可使用于接触介质硫酸酸度在10以下的设备。
喷淋式饱和器结构见图3。
图3喷淋式饱和器结构图综上所述,喷淋式饱和器工艺综合了旧式饱和器法流程简单,酸洗法有大流量母液循环搅拌,结晶颗粒大的优点,又解决了旧式饱和器法煤气系统阻力大,酸洗法工艺流程长,设备多的缺点。
其工艺流程和操作条件与现有的鼓泡型饱和器相接近,易于掌握,设备材料国内能够解决。
不但可以在新建厂采用,而且更适于老厂的大修改造。
2生产无水氨的工艺另一种可供选择的脱氨方法是弗萨姆法生产无水氨。
弗萨姆工艺是由美钢联开发的,它可以从焦炉煤气中吸收氨(半直接法),也可以从酸性气中吸收氨(间接法)。
宝钢二期工程从美国U.S.S公司引进了一套从焦炉煤气中吸收氨的弗萨姆装置,焦炉煤气导入吸收塔与磷酸铵溶液直接接触,吸收煤气中的氨,然后经解析、精馏制取产品无水氨。
该工艺的特点是利用磷酸二氢铵具有选择性吸收的特点,从煤气中回收氨精馏制得高纯度的无水氨(纯度可达99.98)。
但由于介质具有一定的腐蚀性,且解吸、精馏要求在较高的压力下操作,故对设备材质要求较高。
除此之外,该工艺具有一定的经济规模限制,规模过小既不经济也不好操作。
攀钢焦化厂在引进AS法脱硫的同时引进了一套间接法弗萨姆无水氨装置,它是将脱酸塔顶的酸性气体引出送入间接法弗萨姆装置的吸收塔,用磷酸溶液吸收酸性气中的氨。
由于该工艺不与煤气直接接触,几乎不产生酸焦油,与半直接法相比,酸焦油分离和处理设施可大为简化。
弗萨姆装置生产出的无水氨纯度高,产值较高,经济效益较好。
由于是液体产品储运不方便。
弗萨姆法吸收氨的原理是用磷酸的一铵盐和二铵盐的水溶液从焦炉煤气中选择性吸收氨,吸收了氨的磷铵母液在再生工序的压力下用蒸汽汽提,得到含氨约20的氨汽,再生后的磷铵母液返回吸收部分循环使用。
含氨20的氨汽经精馏得到99.98的无水氨。
这种方法由吸收、解析、精馏三个部分组成其工艺流程见图4,吸收和再生的代表性化学反应式为:
图4弗萨姆法吸收氨的工艺流程1)氨的吸收。
焦炉煤气从吸收塔底进入,吸收塔为上下两段空喷塔,吸收液与煤气逆流接触,分上下两段单独循环喷洒吸收液,上段吸收液NH3/H3PO4分子数比为1.25,在自身循环过程中吸收了煤气中的氨,循环液的分子数比上升为1.35,上段循环液的一部分从塔内溢流到下段作为下段吸收液的补充。
下段吸收液循环吸收氨以后,分子数比达到1.85,抽出循环量的3送往再生工序。
塔的操作温度为55,塔后煤气含氨可达0.lg/m3。
吸收塔的阻力为1.01.5kPa。
塔的材质为SUS304L。
2)磷铵母液的再生。
吸收了氨的磷铵母液进入解析塔,先要经过预处理除油,再与解析塔底贫液换热至104后进入接触器。
富液除油的方式采用泡沫浮选除焦油器。
由于磷铵母液在吸收氨的过程中吸收了微量酸性气体(H2S,HCN,CO2等)与吸收液中的氨反应生成的铵盐,易在后工序精馏塔内造成堆积而堵塔,所以酸性气体就必须从吸收液中蒸出,这就是接触器的目的。
104的富液在接触器中靠精馏工序来的废蒸汽加热至沸点,将溶解在吸收液中的酸性气体蒸出,这些含氨的酸性气体由接触器排出返回吸收塔,接触器材质为SUS316L。
富液经接触器后用泵经气液换热器与解析塔顶的浓氨汽换热,然后再经加热器加热至187后进入解析塔顶部,塔底通入直接蒸汽,塔的操作压力约为1.4MPa。
含氨气体以184离开塔顶,经过换热、冷却调节至131后进入接受槽作为精馏塔的原料。
脱氨后195的贫液其分子数比为1.25,从塔底引出,经换热和冷却至55后送至吸收塔上段循环使用。
整个吸收、再生形成完整系统,系统中的磷酸保有量是一定的,系统的水分必须保持平衡,吸收液中的部分水分在吸收过程中蒸发到煤气中,部分水分由解析塔顶随浓氨汽带走,保持系统水分平衡的关键是控制解析塔底的再生液(分子数比1.25)中磷酸浓度为31(W)。
解析塔材质为SUS304L。
3)氨的精馏。
由解析塔接受槽来的131、含氨20左右的氨液送入精馏塔中部精馏。
塔顶得99.98纯氨汽,经冷却后部分作为回流送往塔顶,控制塔顶温度在3334,其余部分作为产品。
精馏塔操作压力1.7MPa,冷凝冷却水温为30,精馏塔底排出的废水含氨0.1(W),塔底通入直接蒸汽,操作温度约为194。
在精馏塔进料层附近送入20(W)NaOH水溶液,将进料中微量的CO2,H2S等酸性组分除去,以防止产生铵盐而引起堵塞。
另外,在精馏塔进料层附近可能会积聚油分,必须在适当高度从侧线引出,返回到吸收塔煤气中去。
4)半直接法与间接法弗萨姆生产无水氨的对比。
半直接法弗萨姆生产无水氨,即磷铵母液吸收塔设置在煤气系统。
这种方法存在以下问题。
其一,由于与煤气直接接触,很易污染吸收液,后工序必须设置除焦油装置,并造成解析与精馏操作的复杂化;
其二,弗萨姆吸收塔的操作温度约40,后面必须连接终冷系统,煤气系统能耗高。
且解析塔底出来的贫液换热后也必须冷却到相应温度,冷却面积大、能耗高。
吸收塔的循环吸收液多(喷淋密度要求)、电耗高;
此外,由于吸收塔直径大,所需特殊钢材多,投资也高。
而间接法生产无水氨,吸收塔设置在脱酸塔后从酸性气体中回收氨,酸性气体已经经过蒸馏相对来说杂质少,可不必增加除油装置,酸性气体相对量小得多,含氨浓度高,吸收塔直径小,循环液量少,完全可避免半直接法的缺点。
从酸性气体中吸收氨的操作温度高,从解析塔底返回的吸收贫液不需冷却到半直接法那样低,从而有利于节能。
3氨分解工艺脱氨的第三种方法是氨分解工艺。
由洗氨、蒸氨和氨分解二部分组成。
其工艺流程见图5。
图5氨分解工艺流程1)水洗氨、蒸氨。
焦炉煤气经过鼓风机后,温度为45左右,在洗氨前必须冷却到最佳的洗涤温度,一般要求25,冷却是在洗氨塔底部的冷却段进行。
冷却后的煤气进入洗氨塔与塔顶下来的洗涤水逆向接触进行氨的吸收。
冷却后的剩余氨水进入洗氨塔的下一层。
由于氨的吸收为放热反应,为了保持洗氨的等温状态,要设置中段循环将反应热用冷却水除去。
离开洗氨塔的富氨水中除氨外,还有H2S、HCN、CO2等酸性气体,塔后煤气含氨应达到0.lg/m3。
富氨水经换热后送到蒸氨塔,在这里挥发氨从液体中汽提出去。
汽提后的蒸氨废水返回洗氨塔顶部。
多余的废水送到固定铵蒸氨塔,在此塔内通入蒸汽,在较高的pH值下(约10.5)除去固定铵,固定铵塔的蒸氨废水送往污水处理站。
从两个蒸氨塔出来的氨汽合并后在分缩器中部分冷凝,除去大部分水蒸汽,得到的浓氨汽需进一步处理。
它可以采用硫酸吸收氨制成硫铵,也可以采用弗萨姆法生产无水氨,还可通过氨汽的部分冷凝生产浓氨水,生产出来的浓氨水贮存起来,作为备用装置。
除了上述处理方法外,氨分解也是一项值得重视的处理氨汽的方法。
2)氨分解。
氨分解是处理氨汽的热催化技术。
氨汽通过专用的混合室进入反应器,在进入反应区前,先在混合室内与参加反应的空气和补充用的焦炉煤气混合。
在反应器顶部空间内,反应温度达10001150时,分解反应立即开始,在底部大约900的催化床内反应结束。
主要的化学反应为:
在系统温度1000时,式
(1)式(4)反应在11.5秒内达到平衡,可以产生99.99以上的转化效果,即剩余的氨和氰化氢的浓度将低于10ppm。
式(6)的反应可在约0.2秒内完成,释放出维持反应温度所需要的热量。
式(5)的反应在混合室附近进行。
由于式(6)迅速消耗所供给的氧,所以式(5)在反应器顶部就结束,式(7)、(9)将少量不需要的SO2和S在反应物到达催化床之前转化成硫化氢。
氨分解的基本条件之一是补充一定量的焦炉煤气。
此煤气不是作为燃料,而仅作为氢源以平衡式(7)和式(9)反应,使反应向右侧进行。
另外,氢浓度不够时,硫化氢和二氧化硫之间将发生式(8)反应而产生元素硫,在尾气冷却过程中将会造成堵塞问题。
在低负载条件下,从氨中分解出来的氢不足以维持反应温度时,必须燃烧一部分补充的焦炉煤气。
反应温度和氢浓度是氨分解整个系统两个十分重要的控制参数。
一般反应温度维持在11001200,炉温不能超过1200,否则催化剂镍的蒸汽压明显升高,流失速度加快,大大缩短催化剂的使用寿命,但不要低于1100,温度过低容易形成铵盐。
炉温是靠串接到焦炉煤气增值装置中的温度控制器来完成的。
补充的焦炉煤气量是通过尾气中氢含量来调节的,尾气中氢的理论含量大约是3(V)。
为了适应氨汽组成的各种变化,尾气中氢的含量必须保持稍高一些。
新的氨分解装置在刚开始操作期间,氢的含量必须接近15%(V),然后逐渐减少到安全极限值,一般为10(V)。
如果氢浓度太低,一定量的元素硫见式(8),式(9)反应。
则将通过分解炉进入尾气冷却器,沉淀的固体硫将水变成浅黄色和混浊体,引起反应器内部和冷却器等地方的堵塞。
4三种氨回收工艺的比较根据有关资料报导,在下列基本参数相同的条件下,对三种类型的氨回收工艺进行对比分析。
焦炉煤气处理量km3/h100.5煤气温度25煤气压力kPa14煤气杂质含量H2Sg/m38NH3g/m36HCNg/m30.60.7CO2(V)2剩余氨水量m3/h55氨水分析g/L游离氨3.5固定铵3H2S0.3CO22.5HCN0.2净化后煤气NH3g/m30.05H2Sg/m30.5废水含氨mg/L150三种工艺均包括剩余氨水蒸馏。
在生产硫铵和无水氨的工艺中,煤气进粗苯吸收塔前的终冷也作了考虑。
由于饱和器内压力损失较大(按鼓泡式),所以鼓风机所增加的能耗也包括在内。
三种脱氨工艺的原材料、能源消耗和产品的计算结果见表1。
项目硫铵(半直接法鼓泡型)弗萨姆无水氨(半直接法)水洗氨、蒸氨、氨分解消耗蒸汽t/h0.2MPa88182.0MPa111电KWh/h45024090焦炉煤气m3/h900冷却水m3/h970930660硫酸(100)t/h2.7H3PO4(100)t/h324334324产品无水氨t/h0.93硫铵t/h3.6蒸汽2Mpat/h5.8*包括约5kPa压力损失而增加的电能*包括煤气终冷的耗水量根据表1数据,三种脱氨工艺的投资、维修费用和操作费用比较结果见表2。
项目硫铵无水氨氨分解基建投资万元223018601500维修费220180150蒸汽(净)420.48946.08641.23电157.6884.1031.54焦炉煤气157.68冷却水339.9325.87231.26硫酸2317.9碱液567.65585.17567.65磷酸30.66费用总和4023.612151.881779.36硫铵3153.6无水氨1385回收尾气210.94生产费用870.01766.881569.42元/1000m39.3478.23916.851根据表2可见,配有氨分解的水洗氨系统,其基建投资和消耗费用较低,但由于氨分解装置没有正式产品,其生产费用较高。
/DIV内容总结
(1)对多种氨回收工艺的综述摘要:
详细介绍了目前应用较多的饱和器法生产硫铵弗萨姆法生产无水氨和水洗氨蒸氨和氨分解三种氨回收工艺的工艺流程,并对三种工艺进行了经济比较
(2)图3喷淋式饱和器结构图综上所述,喷淋式饱和器工艺综合了旧式饱和器法流程简单,酸洗法有大流量母液循环搅拌,结晶颗粒大的优点,又解决了旧式饱和器法煤气系统阻力大,酸洗法工艺流程长,设备多的缺点