优秀毕业论文多产品多工艺路线半导体车间布局建模与优化Word文档下载推荐.docx
《优秀毕业论文多产品多工艺路线半导体车间布局建模与优化Word文档下载推荐.docx》由会员分享,可在线阅读,更多相关《优秀毕业论文多产品多工艺路线半导体车间布局建模与优化Word文档下载推荐.docx(140页珍藏版)》请在冰豆网上搜索。
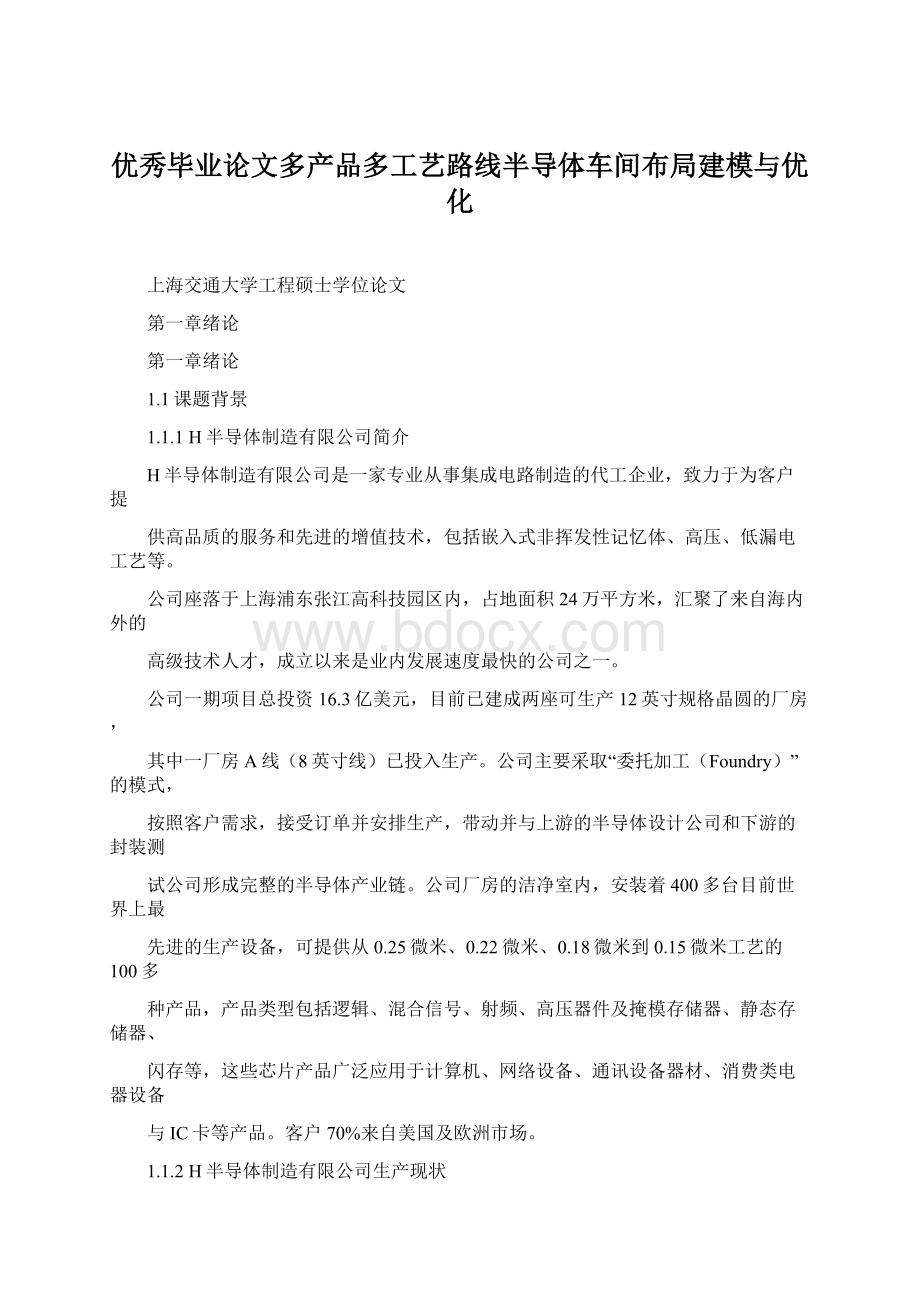
及其产品的发展越来越被世人所瞩目,在世界经济发展中起着举足轻重的作用。
1.2.1全球半导体产业发展日趋成熟
全球半导体产业日趋成熟,尤其是日、美、西欧等先进国家和地区已经进入稳定的
半导体增长时期,人们把目光更多的集中在中国国内半导体产业的发展。
一方面,中国
政府越来越重视高科技行业的发展,给予很多的优惠政策来扶植本土半导体产业的发
展;
另一方面,很多先进的半导体业者看好中国未来半导体市场发展的前景,同时为扩
大市场,降低营运成本,纷纷前来投资建厂,如英特尔、台积电、联电等。
在未来几年
内,半导体生产仍将向亚洲各国转移,这不仅给中国的半导体业发展注入了新的活力与
动力,同时也增加了同行业之间的竞争。
这种竞争不仅体现在技术上,也体现在成本方
面,如何满足客户需求,使产出与设备利用率最大化,成本最小化,是半导体业者不断
追求的目标[6]。
1.2.2半导体产业投入巨大
半导体行业是一个投入大、收益慢的产业,良好的设施规划是工厂顺利生产的基本
保障,半导体生产决策中,不仅需要考虑生产计划(planning)及调度(scheduling)计
划,还需要考虑车间布局优化。
主要原因一是布局优化是一个长期规划,将会对未来
生产的效率带来重要影响;
二是半导体属于技术及设备密集型企业,设备昂贵,单项设
备可高达3至4千万人民币,布局更改成本高昂。
2
1.2.3“空间利用率”的比较标杆效应
良好的厂房设施规划可以提高空间利用率,在有限的空间内摆放更多的机台,从而
提高整个厂房的生产率,降低成本。
尤其是半导体制造业不同于其他传统制造业,其先
进的工艺流程,对厂房、设施、环境都有极其严格的需求,其制程的复杂性、设备的昂
贵性和产品的精密性都决定了半导体厂房的设施规划也不同于一般的车间布置。
因此,
在建厂初期,半导体业者就会很重视厂房的设施规划,以减少物料搬运成本,使工厂更
有效的安排生产,以避免初期的不良规划给后续生产带来低效率生产,产生不可估量的
损失。
目前,半导体业者之间已把空间利用率(spaceproductivity)做为生产能力比较
的一个重要标杆[1]。
1.3相关领域研究现状
随着制造业的不断发展,对于制造车间设备布局的要求也越来越高,学者们在这方
面的研究也不断深入。
1.3.1布局及设备布局理论研究
首先,在布局问题及设备布局问题的理论研究方面,查建中、唐晓君等在其文章中
将布局问题按布局对象的几何形状和是否规则分为二维/三维规则物体布局、二维/三维
不规则物体布局,并指出布局问题除少数能获得最优解,其余的都属于NP完全问题;
并且将布局问题模型分为数学模型、图论模型和复合知识模型三种;
最后文章中还将目
前布局问题的求解方法进行归类,指出数学方法、图论方法、专家系统技术、人工神经
网络方法及启发式算法是目前解决布局问题的常用方法[9]。
曹振新、朱云龙等在其文章
中系统阐述了设备布局问题:
首先,建立了设备布局问题参考模型,将设备布局问题划
分为布局逻辑、布局建模和模型解法三个步骤。
然后指出设备布局逻辑可分为单元布局、
分布布局、可重构布局和鲁棒性四种;
设备布局模型可分为二次分配模型、图论模型和
混合整数规划模型[2]。
3
设备布局解法包括图论算法、结构算法、改良算法和混合算法等。
在设备布局建模
方面,Heragu和Sunderesh在其文章中系统阐述了设备布局建模问题,将物流费用最小
作为设备布局优化目标,并提出了模型的两个约束条件:
设备之间不相互重叠和设备布
局位置不超过车间范围。
另外,二次分配模型(QuadraticAssignmentProblemModel)
也是设备布局常见模型,即指定n个布局位置和n台设备,已知n个布局位置间的距离
以及n个布局设备之间的物流大小,然后为每个位置指派设备以使全部的物料运输费用
最小,且布局时要求一台设备只能赋给一个位置,一个位置只能布置一台设备。
对于设
备布局模型,有的学者还提出了将车间面积也作为模型优化目标,在设备布局时尽量提
高车间面积利用率,如在Liggett和Mitchell建立的面积利用模型中,将车间设备总面积
表示为n台设备所必须的面积与布局空间所需且未被使用的空余面积之和,将面积利用
率表示为n台设备所必须的面积之和与车间总面积之比,其中的设备所必须的面积包括
设备自身面积和设备与周围其它设施所设定的必要的间距面积之和,提高车间面积利用
率就是要尽量减少车间设备总面积[18]
。
在设备布局问题求解方法方面,由于布局问题属于NP完全问题,难以在可接受的
时间内获得满意解,而启发式算法因为不依赖具体的数学理论,来源于实际的工程应用,
所以启发式算法在设备布局问题的求解方面应用较为广泛。
如W.M.Chan等提出以设备
间的权重大小作为启发规则,每次从待布局设备中选出一个最佳条件的设备进行布局的
方法解决了单元布局(CellureLayout)中的单元内部设备指派(MachineAssignment)
问题;
应保胜等提出的利用深度优先的智能回溯策略,以设备间零件流的传输信息为启
发式知识,在多维解空间寻求可行解,并通过比较有限的可行解,从而得到设备布局的
最优解;
刘晖等在考查了生产线加工方式特点的基础上,提出了基于设备分类的车间布
局方案,在该方案中,所有设备按其物流交换数量,被分为:
输入设备、输出设备、中
间设备和独立设备,并以此为依据,得到了设备布局的定序和定位算法,较好地解决了
生产线设备布局问题[7]。
同时,遗传算法,模拟退火算法和蚁群算法由于其能对解空间
进行不断的搜索,从而可以在较短的时间内获得问题的近似解,所以在设备布局问题这
类NP完全问题方面的应用也较多,如Eduardo.V.G..F和Alexandre.J.T利用群组编码
(GroupEncode)方式代替简单的机器编码方式进行遗传算法编码用于解决单元布局中
4
的单元构建问题。
文献中均采取一种被称为“净间距(Clearance)”的编码方式的遗传算
法用于求解多行设备布局问题。
Ramkumar.A.S和Ponnambalam.S.G在其文章中提出一
种利用模拟退火算法和遗传算法相结合的方法用于解决柔性制造系统设备布局问题[17]
文献详细阐述了群体优化(ColonyOptimization)蚁群算法在设备布局方面的应用。
周
亦波等人在研究了基于成组技术的制造单元在车间平面内的布局问题时,提出了一种能
真实反映车间平面内布局特点和要求的布局模型,并利用模拟退火法进行求解试验结果
表明,该布局模型不仅能得到较优的单元布局,而且还能得到合理的物流路径。
以上这
些算法都是针对不同的生产背景及不同的优化模型而提出的,对于半导体车间设备布局
问题,并没有一种具体的求解算法。
1.3.2半导体车间设备布局研究
在半导体生产车间设备布局问题方面,学者们也进行了相应的研究,这些研究多集
中于对半导体生产车间设备布局形式的研究。
例如,ChristopherD等人通过比较几种单
元布局(CellularLayout)形式在半导体生产中的循环时间(CycleTime)表明:
当SetupTime
和TransferTime很高,机器可信度很高时,单元布局(CellularLayout)会有较好的性能。
BrettA在其文章中研究了隔间式布局(BayLayout)与车间搬运系统的整合问题;
俞静
等在其文章中阐述了半导体车间设施规划的相关问题;
HuangHan-Pang等在其文章中研
究了半导体车间自动物流系统的建模与评价方法。
Gaxiola.G.和Hennessy.L以搬运距离
为评价目标,用静态分析和动态分析相结合的方法对三种半导体车间自动化物料处理系
统进行了评估,指出了各自的优缺点[19]
由此可见,目前,对于半导体车间布局问题的
研究还相对较少,本文针对这一不足,分别建立了半导体车间布局优化模型,并研究了
相应的求解算法,同时选取典型数据进行了实例验证。
1.4课题研究的意义
由于半导体晶圆制造企业的产品组合复杂,生产流程多变,导致产能波动和瓶颈飘
移的现象时有发生,如何优化设施布置,使生产具有弹性,从而提升自身的产能利用率
5
是许多半导体业者所面临的难题,因此,建立一套科学的晶圆厂设施规划方法是十分必
要的。
1.5研究对象与内容
1.5.1研究对象
本课题只针对面向多产品多工艺路线的半导体布局问题,以降低物料搬运成本为优
化目标。
考虑物料搬运系统对人流、物流、机械流的约束,提出适应产品变化趋势的优
化布局方案,并以8寸晶圆厂洁净室为例,针对设备布局和自动物料传输系统设计两个
相互关联的内容展开研究。
1.5.2研究内容
具体研究内容包括分析产品需求及所要求的不同工艺流程,进行设备预测与分析;
分析布局优化目标与约束,建立优化布局模型;
提出布局优化算法;
自动传输系统
(AMHS)的合理布置。
6
第二章半导体与半导体生产制造
半导体制造业不同于其他传统制造业,由于其先进的工艺流程,对厂房、设施、环
境都有极其严格的需求,其制程的复杂性,设备的昂贵性和产品的精密性都决定了半导
体厂房的设施规划也不同于一般的车间布置,具有自身的特殊性。
H半导体制造有限公
司不同于其他半导体厂的独特性,产品组合的多样性,更增加了工厂布局的难度与挑战。
2.1半导体制程简介
2.1.1金属氧化半导体电晶体(MOS)
金属氧化半导体电晶体,简称MOS(Metal-Oxide-SemiconductorTransistor),就是
我们通常所说的半导体。
组成MOS的三种基本材料是:
金属层(Metal),氧化层(Oxide),
半导体层(Semiconductor),MOS就是由这三种厚度不同的材料依顺序堆垒之后形成。
所谓MOS,是由经掺杂的多晶硅与SiO2和Si底材所组成的电子元件[20]
多晶硅+杂
SiO2
硅晶片
图1金属氧化半导体电晶体模型
Fig.1ThemodelofMOS
2.1.2制程
(1)薄膜沉积(ChemicalVaporDeposition)是将多层材质厚度均不同的薄膜覆盖
在晶体上所需要的技术。
薄膜沉积的步骤是:
1,长晶(Nucleation);
2,晶粒成长(Grain
7
Growth);
3,晶粒聚结(Coalescence);
4,缝道填补(Fillingofchannels);
5,沉积膜
长成(FilmGrowth)。
化学气象沉积:
ChemicalVaporDeposition(CVD)和物理气象
沉积:
PhysicalVaporDeposition(PVD)都是薄膜沉积(ThinFilm)的方式。
(2)溅镀(SputteringDeposition):
利用电浆独特的粒子轰击,以动量转换的原理,
在气相中制备沉积元素以便进行薄膜沉积的PVD技术。
(3)微影(Photolithography):
1,光阻覆盖;
2,曝光;
3,显影。
为了加强图案
传送的准确性与可靠性,整个微影过程还包括:
去水烘烤,涂底,软烤,硬烤。
几乎所有半导体元件所组成的主要材料,都必须经过薄膜沉积,微影,然后蚀刻这
个流程,以便一层一层的进行元件的制作。
(4)蚀刻(Etching):
使要将进行微影制程前所沉积的薄膜,厚度约在数千到数百
纳米之间,把所有被光阻覆盖及保护的部分,以化学反应或是物理作用的方式加以去除,
已完成转移光罩图案到薄膜上面的目的。
(5)扩散(Diffusion)制程:
是要利用参质在高温下对硅所具备的较高的扩散能
力,来制作半导体元件所需要的P型和N型的半导体区域。
(6)离子植入法(IonImplante):
先将参质离子化,而后借加速器的加速,把这
些经离子化的参质,直接打入硅晶片里来进行参质的预置。
(7)化学机械研磨(CMP):
目的是使金属表面平整化,使薄膜沉积时质量更好。
图2典型IC截面图
Fig.2TypicalsnapshotofIC
8
2.2半导体制造的特殊性
2.2.1半导体厂房造价昂贵
H半导体制造有限公司厂房是由国际著名的集成电路工厂设计公司IDC按12英寸
硅片的生产规格设计的,在设计与建设过程中,对工程的细节和可靠性都作了严格的管
控。
在厂房、办公室及配套设施区域共打桩11,000套,桩深达30.5米,使建筑的抗
震能力达到里氏八级;
此外,厂房还采用了独特的防微振动设计,可达到65纳米时代
的技术要求。
半导体厂房一般都是二到三层的多层建筑,一方面是由于半导体制造过程
中需要使用大量的水、电、气体和化学品,这些厂务主系统需要布置在二层和一层,对
应于三层主机台的下方,根据机台性能不同输送各种气体,化学品,并通过管路进行回
收与利用,同时还有各种用于电力、照明、控制等目的的电气管线,它们均与三层生产
区的各种机台一一对应,布线极为复杂。
另一方面,是因为三层生产区的洁净室造价更
为昂贵,一般只放置直接用于生产的主机台,而作为支持主机台运转的附属机台由于对
洁净等级的要求并不高,则被分别放置在二层和一层的工作区域内。
2.2.2半导体成品对环境要求较高
半导体产成品晶圆不同于其他产品,对生产区的洁净度、温湿度,抗干扰度等都有
较高的要求。
目前半导体生产以8英寸晶圆为主,直径为200mm,是非常薄(0.75mm
左右)的圆盘,通常用硅的单晶切片来作为半导体生产的材质,通过制程加工后的晶圆,
上面集成有大量的元器件,用于手机、电脑、数码相机、汽车、随身听等电子产品。
污
染是导致产品报废的重要因素,作为主要生产区的洁净室可以达到Class100的洁净等
级。
所有人员须穿戴符合规定的洁净衣、帽、鞋、口罩、PVC手套,通过空气洗净室
清洗后,才能进入生产区[8]。
生产区内常年的平均温度都控制在22摄氏度正负加减0.3
度,湿度为43%正负加减3%。
由于半导体制造过程中,晶圆对洁净度有着极为苛刻的
要求,因此需要尽量减少其与外界接触的时间。
而如果由于设施布置不合理,就很容易
造成物料搬运时间延长,这样不但会增加在制品数量,降低劳动生产率,还会增加晶圆
9
暴露在空气中的时间,也就会加大其被污染的可能性,而使良率降低,直接导致产品报
废的几率增大。
2.2.3半导体设备安装复杂
半导体设备为精密仪器,价格昂贵,生产周期长,运输、安装复杂。
为了给客户提
供先进的工艺技术和优质的制造服务,H公司的洁净室内安装着最为先进的设备,其中
尼康的深紫外光刻机解析度可达0.1微米,为工艺的提升留下了相当大的空间,它的生
产周期最短要6个月以上,在运输过程中,全程采用温控和气垫设备,不能倾斜与震动,
从机台进厂安装到调试成功用于生产要2个月左右的时间,对工作条件要求比较苛刻。
每套设备由一个主机台和若干个附属机台组成,分别放置于不同楼层,由水、电、气、
化等厂务系统和管线相连接,布线极为复杂。
一经安装完成,不会轻易变更位置,否则
将牵动下层的附属设备,管路和管线的变动。
而且,半导体制造机台极为昂贵,性能极
为精密,对这类设备的位置移动,除可能造成设备损坏外,也会造成人力、物力和财力
上的很大损失。
如果因添加新设备或初始布局欠优化,需要重新布局,则会带来昂贵的
重新布局成本,因此,现今半导体车间里的设施布局一经确定一般不会再有大的改变,
并且要为将来添加新设备预留足够的空间[4]。
2.2.4半导体设备特殊敏感
半导体设备的特殊性及敏感性,工艺流程的复杂性决定了半导体车间设施规划时要
考虑到很多限制条件。
为了方便操作,减少在制品(WIP)传输距离,按照工艺流程对机台进行分区规划,
同时相同功能的机台要尽量摆放在一起。
这样既便于统一管理,使专项技术工人更容易
对该区的机器进行控制,及时发现问题,及时维修,也便于计算机CIM系统统一下达
生产计划资讯;
由于各区对作业工人的要求不同,工人亦不可以随意走动,有利于扩大
工人的作业技能,发挥班组合作精神;
同时,不同机台需要多种不同化学物品,稳定气
压,适当温度等条件的支持,而这些原料几乎完全以管道形式进行传送,因此,相同机
10
台摆放在一起有助于管线的统一设计,以保证各种水、电、气、化等厂务原料的有效供
给,避免重复配管造成的不必要的浪费[10]
没有或具有较少附属设备的机台摆放在单层式车间。
ET,TF区的主机台具备很多
的附属设备,需要摆放在多层式车间,尤其是拥有具有可燃性的附属设备,如local
scrubber,出于安全的考量,需要与洁净室完全隔离,摆放在FAB一层。
IMP,DF,PH
区的附属设备数量远远少于ET和TF的机台,只需要利用到FAB二层的空间,这样,
位于其区域下方的一层空间就可以用来放置厂务设备及挪做它用。
而对于某些没有或具
有较少附属设备的机台则可以摆放在单层式车间,如CMP,WS(waferstart),Wafer
Recycle,BG,OQA,WAT的机台,这样可以充分利用FAB内各个楼层的有效空间。
光刻设备要在黄光下操作,需要单独隔间,目的是防止光阻材料在日光下曝光而降
低解析度,从而影响曝光效果。
易产生磁场及震动的设备要远离对磁场和震动敏感的机台。
芯片需要裸露在空气中操作的设备要放置在Class1的环境中,单独隔间,与
Class100的环境过渡要有缓冲区,以避免交叉污染,如Waferstart(产品下线),mask
inspection(光罩检测)区。
机台摆放区一侧要预留设备搬运空间,另一侧摆放物料搬运系统(AMHS)。
要根据机台进厂顺序,调整机台摆放设计,避免先进来的机台阻挡后续进厂设备的
搬运动线。
每条操作通道(intrabay)宽度的设置要视该走道机台特性及操作需求而定,同时要符
合安全法规及人因因素的要求,最小为1.2米。
2.2.5半导体制造过程繁复
在半导体制造中,通常要经过离子植入、清洗、掺杂、光刻、蚀刻、物理与化学气
象沉积、研磨等多种主要工序,平均500个以上的操作步骤并且要多次经过同一机台的
加工才能完成(多重入),且各工序处理时间不同,因此,物料搬运所需的时间和费用
都是十分可观的。
一个合理优化的布局设置可以减少在制品搬运距离,缩短产品生产周
期(CycleTime),降低物料搬运成本,充分利用工厂空间,增加产品生产灵活性。
相反,
11
如果初期规划不良,在以后的生产过程中就将面临低效生产,物料搬运费用增加等问题,
而直接导致运营成本的增加。
企业要想生存,必须在一个可接受的制造周期下有足够高
的产量。
建厂设计阶段的设施规划布局和物料搬运系统决定了投产以后的制造周期和产
量,为了寻求生产系统的最优运行效果,必须在系统设计时就优化其布置方案。
可见,要做好一个半导体厂房的设施规划并不是一件容易的事情,而一个不良的布
局设计会给整个工厂的运作带来无法估量的损失。
2.3半导体制造基本生产布置方式
生产布置方式受工作流的形式限制,它有三种基本类型(工艺原则布置,产品原则
布置和定位布置)和一种混合类型(成组技术或单元布置)[3]。
工艺原则布置(也称车间或功能布置),是一种将相似设备或功能放在一起的方式,
比如将所有的车床放在一处,将冲压机床放在另一处。
被加工的零件,根据预先设定好
的流程顺序,从一个地方转移到另一个地方,每项操作都由适宜的机器来完成。
医院是
采用工艺原则布置的典型,每个科室只能完成特定的医疗服务,如产房和加护病房。
产品原则布置(也称装配线布置)是一种根据产品制造的步骤来安排设备或工作过
程的方式。
实际上每种产品的加工路径都是直线型的,鞋、化工设备和汽车清洗剂的生
产都是按产品原则布置的。
成组技术(单元式)布置是将不同的机器组成加工中心(工作单元)来对形状和工
艺相似的零件进行加工。
成组技术布置和工艺原则布置的相似点是加工中心用来完成特
定的工艺过程,加工中心生产的产品种类有限(成组技术有时指的是零件的分类编码系
统)。
定位布置中,产品(由于体积和重量庞大)停留在一个地方,生产设备转移到要加
工的产品处,而不是产品转移到设备处,造船厂、建筑工地和电影外景制片场都是这种
方式的实例。
许多制造厂都将两种布置类型结合起来。