注塑模具毕业设计论文Word文档格式.docx
《注塑模具毕业设计论文Word文档格式.docx》由会员分享,可在线阅读,更多相关《注塑模具毕业设计论文Word文档格式.docx(31页珍藏版)》请在冰豆网上搜索。
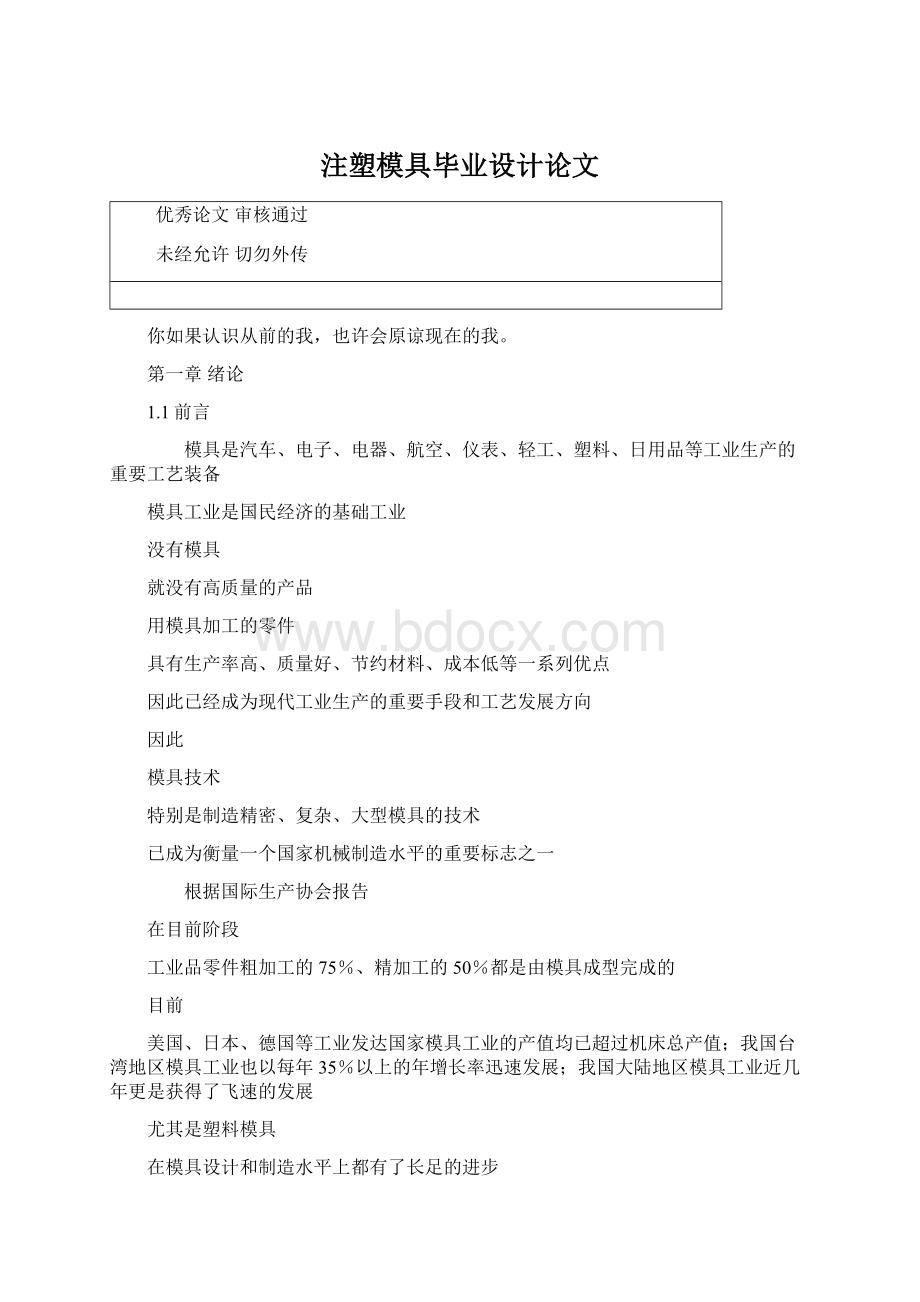
大大缩短设计周期及制造周期
降低生产成本.最大限度地提高模具制造业的应变能力满足用户需求
模具企业在技术上实现了专业化
在模具企业的生产管理方面
也有越来越多的采用以设计为龙头、按工艺流程安排加工的专业化生产方式
降低了对模具工人技术全面性的要求
强调专业化
国外注塑成型技术在也向多工位、高效率、自动化、连续化、低成本方向发展
模具向高精度复杂、多功能的方向发展
例如:
组合模、即钣金和注塑一体注塑铰链一体注塑、活动周转箱一体注塑;
多色注塑等;
向高效率、高自动化和节约能源
降低成本的方向发展
叠模的大量制造和应用
水路设计的复杂化、装夹的自动化、取件全部自动化
我国注塑模具行业与其发展需要和国外先进水平相比
主要存在五大问题:
1.发展不平衡
产品总体水平较低
虽然有个别企业的部分产品已达到或接近国际水平
但总体来看
模具的精度、型腔表面粗糙度、生产周期、寿命等指标与国外先进水平相比尚有较大差距
2.工艺装备落后
组织协调能力差
虽然部分企业经过近几年的技术改造
工艺装备水平已比较先进
但大部分企业工艺装备仍比较落后
企业的组织协调能力差
难以整合或调动社会资源为我所用
从而就难以承接比较大的项目
3.多数企业开发能力弱
一方面是技术人员比例低、水平不够高
另一方面是科研开发投入少
观念落后
对开发不够重视
4.供需矛盾一时还难以解决
2003年国产塑料模具国内市场满足率只有74
7%
其中大型、精度、长寿命模具满足率还要低
估计不足60%
市场需求旺盛
生产发展一时还难以跟上
供不应求的局面还将持续一段时间
5.体制和人才问题的解决尚待时日
在模具这样竞争性行业中需依赖于特殊用户
需单件生产的行业
国有和集体所有制原来的体制和经营机制已越来越显得不适应
人才的数量和素质水平也跟不上行业的快速发展
各地都重视这两问题
解决尚待时日
1.2.2国内外注塑模具的发展趋向
由于塑料模具工业快速发展及上述各方面差距的存在
因此我国今后塑料模具的发展必将大于模具工业总体发展速度
塑料模具生产企业在向着规模化和现代化发展的同时
"
小而专"
、"
小而精"
仍旧是一个必然的发展趋势
从技术上来说
为了满足用户对模具制造的"
交货期短"
精度高"
质量好"
价格低"
的要求
以下的发展趋势也较为明显
展望我国塑料模具的未来
笔者以为应从提高技术水平着手
一方面发展专业模具厂的技术优势
使之进一步提高对某一类模具的设计制造水平;
另一方面
要不断采用新技术、新工艺
提高模具产品的技术含量
要提高我国的模具技术水平
必须在以下方面加大努力:
1.开发精密、大型、复杂、长寿命的模具
实现模具国产化;
2..加速模具标准化、专业化、商品化生产;
3.大力发展CADCAMCAE、RPM等先进模具设计和制造技术;
4.加大人才培养的力度
使他们尽快掌握模具设计和制造中的先进技术
1.3本课题的内容和具体要求
1.3.1本课题的内容
根据节流阀接头样品
设计一套注射模具
1.3.2具体要求
a、本设计中要注意的问题:
塑件的精度要求为六级
其中配合部位为七级
b、计预期的效果:
通过本次设计
熟练掌握模具开发的基础知识
并能熟练应用Auto-CAD
第二章零件材料分析及方案论证
2.1零件的材料及材料的特性
2.1.1零件的材料
此零件的材料是增强型PA6.
2.1.2增强型PA6材料的特点
尼龙简写PA、属结晶材料
其特点如下:
优点:
(1)机械强度高
韧性好
有较高的抗拉、抗压强度;
(2)耐疲劳性能突出
经受多次反复屈折仍能保持原有机械强度;
(3)表面光滑
摩擦系数小
耐磨;
(4)耐腐蚀
耐碱和大多数盐液
还耐弱酸
机油、汽油;
(5)无毒
对生物侵蚀呈惰性
有良好抗菌、抗毒能力;
(6)耐热
使用温度范围宽
可在45~100℃下长期使用
短时耐热温度达120~150℃;
(7)有优良电气性能
具有较好的电绝缘性;
(8)制件重量轻
易染色
易成形
缺点:
(1)易吸水;
(2)耐光性较差;
(3)不耐强酸、氧化剂;
(4)设计技术要求较严
加工要求:
一般宜取低模温、低料温、时间长、注射压力大的成形条件
2.1.3增强型PA6的注射成型工艺参数
密度(gcm3):
1.36;
计算收缩率(%):
0.3~0.7;
摩擦系数:
1.3;
弯曲弹性模量E:
8000(Mpa)3.0×
103Ncm3;
适用注塑机类型:
螺杆式、柱塞式均可
后处理:
利用油、水、盐水均可
在温度为90~100℃时
放置4小时
2.2增强型PA6注射成型的原理及工艺过程
2.2.1注射成型的原理
将塑料颗粒定量注入
加入到注塑机的料筒内
通过料筒的传热
以及螺杆转动时产生的剪切摩擦作用使塑料逐渐融化成流动状态
然后在柱塞或螺杆的推挤下熔融塑料以高压和较快的速度通过喷嘴注入到温度较低的闭合模具的型腔中
由于模具的冷却作用
使膜腔内的熔融塑料逐渐凝固并定型
最后开模取出塑件
2.2.2热塑性注射成型工艺过程
注射装备准备装料
注射装置准备注射
图2.2.2注射成形工艺示意图
2.3注射模具的基本组成
2.3.1基本组成
a、浇注系统;
b、成型零件
包括凹模(型腔)、凸模和型芯等;
c、脱模系统
包括推出和抽芯机构等;
d、导向系统;
e、冷却系统;
f、固定和安装部分等;
3.3方案的论证和初步确定
a、第一种该种方案采用斜滑块垂直分型脱模机构
其浇口套设在定模固定板上
用顶杆实现脱模
浇口设在定模固定板上
采用环形浇口
用垂直分型镶块来成型型腔
但去除浇口比较困难
垂直分型镶块密封性不好
易发生边缢边
b、第二种采用外螺纹对合滑块模具结构
其浇口设在定模板上
用顶板实现脱模
用对合滑块来和抽芯机构来成型型腔
采用爪形浇口
使用于管状塑件
在成型时可起到定位作用
使塑件有较篙的同心度
但采用爪形浇口时
进料口越多则熔接痕数量也越多
排气性差
c、第三种采用三板式结构
利用斜导柱侧抽芯
弯销开模
因为塑件结构较复杂
故采用一模一腔
该方案结构简图如下
图3.3.1斜导柱侧抽芯结构图
该方案采用三板式结构
利用斜导柱和弯销拉动侧抽芯运动
与上两种方案相比
结构简单
各个机构的实现比较简单
利于实现
第三章注射成型机的选择与成型腔数的确定
3.1注射成型机的选择
3.1.1估算零件体积
塑件的体积为:
V1=πR12H1+πR22H2+πR32H3+πR42H4
=π×
302×
10+π×
(572)2×
42+π×
(272)2×
45+π×
102(29-272)
=3.14(9000+34114.5+8201.25+1550)
=165998.445㎜3
V2=πR52H5+πR62H6+πR72H7+πR82H8
=π×
(532)2×
50+π×
72×
30+π(18.52)2×
15+π×
(5.52)2×
(29-7)
=3.14×
(35112.5+1470+1283.4375+166.375)
=119421.4613㎜3
同理
浇道体积
V3=πR02H0+πR92H9
(82)2×
65+4×
π×
(62)2×
18
(814×
65+36×
18)
=6167.745㎜3
3.1.2估算零件的质量
因为PA6的密度为1.14g㎝3
所以:
M=ρV=1.14×
46.577=53g
浇道质量:
m=ρV3=1.14×
6.2=7g
即
M+m=60g
3.2锁模力
型腔总的投影面积为:
A=πR2=3.14×
302=28.26cm2
计算其所需锁模力为:
F=1.5×
P×
A×
0.01=9.0KN
3.3选择注射机及注射机的主要参数
3.3.1选择注射机
查《塑料模具设计手册》P15
可知PA6的注射压力为700~1200公斤厘米2
宜用螺杆式注射机
螺杆带止回环
喷嘴宜用自锁式
初选XS-ZY-125型
3.3.2XS-ZY-125型注塑机的主要参数如下
型号:
XS-ZY-125
螺杆直径:
?
42
最大理论注射量:
95g
注射压力:
150MPa
最大注射面积:
320
最大模具厚度:
300最小模具厚度:
200
合模力:
900000N
模板大小:
160×
250
模板最大距离:
600模板行程:
300
喷嘴圆弧半径:
12喷嘴孔径:
4喷嘴移动距离:
210
定位孔直径:
100
注射机顶出杆(两侧):
孔径
22孔距:
230
3.5注塑机的校核
(1)最大注塑量效核材料的利用率为6095=0.63
符合注塑机利用率在0.3~0.80的要求
(2)注射压力的效核所选注塑机的注塑压力需大于成型塑件所需的注射压力
PA6塑件的注塑压力一般要求为70~176MPa
所以该注塑机的注塑压力符合条件
(3)锁模力效核高压塑料熔体充满型腔时
会产生使模具沿分形面分开的胀模力
此力的大小等于塑件和流道系统在分形面上的投影等于型腔压力的成积
胀模力必须小于注塑机额定锁模力
型腔压力Pc可按下式粗略计算:
Pc=kP(MPa)(3.5.1)
式中Pc为型腔压力
MPa;
P为注射压力
K为压力损耗系数
通常在0.25~0.5范围内选取
所以Pc=KP=0.3×
1500=450MPa
型腔压力决定后
可按下式校核注塑机的额定锁模力:
T〉KPcA(3.5.2)
式中T为注塑机的额定锁模力
KN;
A为塑件和流道系统在分形面上的投影面积
mm2;
K为安全系数
通常取1.1~1.2;
KpcA=1.1×
450×
28.26=13988.7N=13.99KN
所以T=900〉KPcA成立
即该注塑机的锁模力符合要求
(4)模具厚度校核初定模具厚度为290mm
在该注塑机要求的厚度范围(200~300mm)之内
(5)模具安装尺寸校核模具安装固定有两种:
螺钉固定、压板固定
采用螺钉直接固定时(大型模具多采用此法)
模具动定模板上的螺孔及其间距
必须和注塑机模板台面上对应的螺孔一致;
采用压板固定时(中、小型模具多用此法)
只要在模具的固定板附近有螺孔就可以
有较大的灵活性;
该模具采用压板固定
(6)开模行程的效核开模取出塑件所需的开模距离必须小于注塑机的最大开模行程
对于双分形面的注塑模具
其开模行程按下式效核
S=SK-HM≥H1+H2+a+(5~10)(mm)(3.5.3)
式中S为注塑机的最大行程
mm;
H1为塑件的脱模距离(此模具中为50)
H2为包括流道在内的塑件高度(此模具中为97)
a为定模板与浇口板的分离距离(此模具中为50)
所以上式成立(300>
204)
即该注塑机的开模行程符合要求
由以上对各参数的效核可知该注塑机(XS-ZY-125型)符合要求
3.6成型腔数的确定
以机床的注射能力为基础
每次注射量不超过注射机最大注射量的80%
计算:
(3.6.1)
=
N----型腔数
S----注射机的注射量(g)
W浇----浇注系统的重量(g)
W件----塑件重量(g)
因为
N=1.75<
2
所以
此模具型腔为一模一腔结构
第四章浇注系统的设计
4.1浇注系统的作用
浇注系统是塑料熔体由注塑机喷嘴通向模具型腔的流动通道
因此它应能够顺利的引导熔体迅速有序地充满型腔各处
获得外观清晰
内在质量优良的塑件
对浇注系统设计的具体要求是:
(1)对模腔的填充迅速有序;
(2)可同时充满各个型腔;
(3)对热量和压力损失较小;
(4)尽可能消耗较少的塑料;
(5)能够使型腔顺利排气;
(6)浇注道凝料容易与塑料分离或切除;
(7)不会使冷料进入型腔;
(8)浇口痕迹对塑料外观影响很小
4.2浇注系统的组成
浇注系统组成是:
主流道、分流道、浇口、冷料井
4.3主流道设计
主流道通常位于模具的入口处
其作用是将注塑机喷嘴注出的塑料熔体导入分流道或型腔
其形状为圆锥形
以便于塑料熔体得流动及流道凝料的拔出
热塑性塑料注塑成型用的主流道
由于要与高温塑料及喷嘴反复接
所以主流道常设计成可拆卸的主流道衬套
定位环和浇口套的装配:
图4.3.1定位环和浇口套的装配
浇口套的尺寸设计要求:
(1)浇口套与注射机喷嘴接触处球面的圆弧度必须吻合
设模具浇口套球面半径为R
注射机球面半径为r
其关系式如下:
R=r+0.5~1mm;
(2)浇口套进口的直径d应比注射机喷嘴孔d1直径大1~2mm
4.4分流道设计
(1)分流道是主流道与浇口之间的通道
多型腔膜局一定要设置分流道
大型塑件由于使用多浇口进料也许设置分流道
(2)分流道的截面形状常用的分流道截面形状有圆形、梯形、六角形和U字型等
为减少流道内的压力损失
希望流道的截面积大;
从热传导角度考虑
为减少热损失
要求流道的比表面及(截面积与外周之比)最小
用流道的截面积与周长的比值来表示流道的效率
各种截面的效率为:
圆形0.25D
正方形0.25D
六角形0.217D
U字型0.153D
梯形0.195D
D为截面大端宽度
当分型面为平面时
可采用圆形或六角形截面的分流道;
当截面不是平面时
常采用梯形或半圆形截面的流道
塑料熔体在流道中流动时
表层冷凝冻结
其绝缘作用
熔体仅在流道中心部分流动
一次分流道的理想状态是其中心与浇口中心一致
圆形截面流道可实现这一点
而梯形截面流道就难以实现
但是
由于梯形分流道易于加工
热量损失和压力损失都不大
因此是最为常用的形式
其断面尺寸比例关系为:
D为梯形的下地面宽度
)Ls(5.5.2-a)
式中δs为塑件收缩波动而引起的塑件尺寸误差(mm);
Smax为塑料的最大收缩率(%);
Smin为塑料的最小收缩率(%);
Ls为塑件尺寸(mm)
一般情况下
由收缩率波动而引起的塑件尺寸误差要求控制在塑件尺寸公差的13以内
b、模具成形零件的制造误差:
实践证明
如果模具的成形零件的制造误差在IT7~IT8级之间
成形零件的制造公差占塑件尺寸公差的13
c、零件的磨损:
模具在使用过程中
由于种种原因会对型腔和型芯造成磨损
对于中小型塑件
模具的成形零件最大磨损应取塑件公差的16
而大型零件
应在16之下
d、模具的配合间隙的误差:
模具的成形零件由于配合间隙的变化
会引起塑件的尺寸变化
模具的配合间隙误差不应该影响成形零件的尺寸精度和位置精度
综上所述
在模具型腔与型芯的设计中
应综合考虑各种影响成形零件尺寸的因素
在设计时进行有效的补偿
由于影响因素很不稳定
补偿值应在试模后进行逐步修订
通常凹模、凸模组成的模腔工作尺寸简化后的计算方法有平均收缩率法和公差带法两种
其中平均收缩率法以平均概念进行计算
从收缩率的定义出发
按塑件收缩率、成形零件制造公差、磨损量都为平均值的计算
公式如以下:
(1)凹模的內形尺寸:
D腔=(ds+dsQcp-34Δs)+Δs3(5.5.2-b)
式中D腔型腔內形尺寸(mm);
ds为塑件外径基本尺寸(mm)
即塑件的实际外形尺寸;
Δs为塑件公差
成型零件精度等级取6级;
Qcp为塑料平均收缩率(%)
此处取0.5%;
所以型腔尺寸如下:
D1=(60+60×
0.005-34×
0.64)+0.643=59.82+0.2130mm
D2=(57+57×
0.64)+0.643=56.81+0.2130mm
D3=(27+27×
0.005+34×
0.48)+0.483=26.78+0.155-0.005mm
D4=(20+20×
0.44)+0.443=19.77+0.1470mm
型腔深度的尺寸计算:
H腔=(Hs+HsQcp+23Δs)+Δs3(5.5.2-c)
式中=4;
E为顶杆材料的弹性模量(MPa)该材料为8000
由于d=4mm
对推杆进行强度校核如下:
б=4Qnπd2≤[б](6.3.2-c)
式中б为顶杆所受的应力
[б]为顶杆材料的许用应力
MPa
由上式得出б=345.563Ncm3<
[б]=8000Ncm2
所以推杆满足强度要求
6.3.3顶杆的形式
顶杆可以分为普通顶杆、成形顶杆、锥面顶杆
该模具的顶杆形式选择普通顶杆
如下图所示
图6.3.3顶杆
顶杆长度的计算顶杆总长度为
表示顶杆端面应比型腔的平面高出;
б2为顶出行程富裕量
一般为3~6mm
根据以上公式计可得
顶杆的总长度为152.5mm
6.4复位杆的结构设计
6.4.1复位杆的作用
反推杆的作用是使推出机构恢复原位
当开模时推杆在推板的推动下将塑料制品推出
反推杆也同时凸出模板表面
当再次注射时
在模具闭合过程中
定模表面与反推杆接触
并使反推杆推动推出机构一起返回原始位置
6.4.2复位杆的结构
由《模具设计与制造简明手册》查的反推杆的结构如下图所示:
图6.4.2复位杆
6.5推板导柱导套的结构设计
6.5.1推板导柱导套
推板导柱为推板动作导向
成滑动配合;
推板导套与推板导柱配合
为了防止推板导套的磨损
应制成便于更换的淬火套
由《模具设计与制造简明手册》查的推板导柱导套的结构如下图所示:
图6.5.1-a推板导柱
图6.5.1-b推板导套
第七章侧向分型与抽芯机构的设计
7.1斜导柱抽芯机构设计原则
a、活动型芯一般比较小
应牢固装在滑块上
防止在抽芯时松动滑脱
型芯与滑块连接部位要有一定的强度和刚度;
b、滑块在导滑槽中滑动要平稳
不要发生卡住、跳动等现象;
c、滑块限位装置要可靠
保证开模后滑块停止在一定位置上而不任意滑动;
d、锁模块要能承受注射时的侧向压力
应选用可靠的连接方式与模板连接
锁模块和模板可做成一体
锁紧块的斜角θ1应大于斜导柱的倾斜角θ
一般取θ1-θ>
2°
~3°
否则斜导柱无法带动滑块运动
e、滑块完成抽芯运动后
仍停留在导滑槽内
留在导滑槽内的长度不应小于滑块全长的23
否则
滑块在开始复位时容易倾斜而损坏模具
f、防止滑块和推出机构复位时的相互干涉
尽量不使推杆和活动型芯水平投影重合
g、滑块设在定模的情况下
为保证塑料制品留在定模上
开模前必须先抽出侧向型芯
最好采取定向定距拉紧装置
7.2抽芯机构的确定
由于该模具比较简单
抽芯力不大
故采用斜导柱外侧抽芯机构
7.3斜导柱抽芯机构的有关参数计算
7.3.1抽芯距S
抽芯距指型芯从成型位置抽至不妨碍脱模的位置时
型芯或滑块在抽芯方向所移动的距离
图7.3.1
由西工大《塑料模具设计》P177查的抽芯距的计算公式为:
S=(R-r)+(3~5)毫米(7.3.1)
式中R---塑件的最大伸出长度(毫米);
r---塑件轴的内圆半径(毫米)
所以S=(R-r)+(3~5)毫米=(29-7)+(3~5)毫米=28(毫米)
7.3.2斜导柱倾斜角α的确定