模具毕业设计83切边冲孔复合模的设计.docx
《模具毕业设计83切边冲孔复合模的设计.docx》由会员分享,可在线阅读,更多相关《模具毕业设计83切边冲孔复合模的设计.docx(24页珍藏版)》请在冰豆网上搜索。
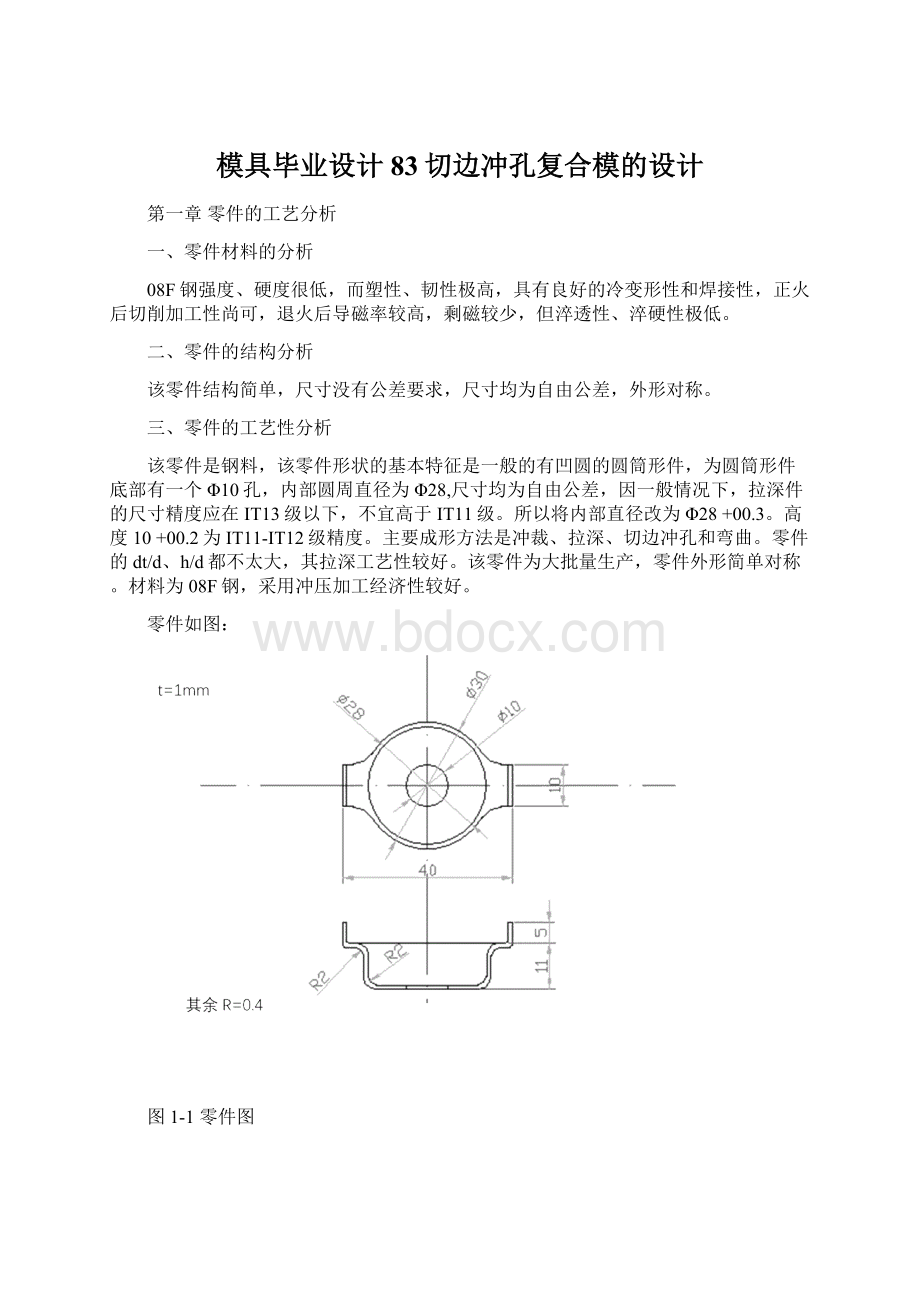
模具毕业设计83切边冲孔复合模的设计
第一章零件的工艺分析
一、零件材料的分析
08F钢强度、硬度很低,而塑性、韧性极高,具有良好的冷变形性和焊接性,正火后切削加工性尚可,退火后导磁率较高,剩磁较少,但淬透性、淬硬性极低。
二、零件的结构分析
该零件结构简单,尺寸没有公差要求,尺寸均为自由公差,外形对称。
三、零件的工艺性分析
该零件是钢料,该零件形状的基本特征是一般的有凹圆的圆筒形件,为圆筒形件底部有一个Φ10孔,内部圆周直径为Φ28,尺寸均为自由公差,因一般情况下,拉深件的尺寸精度应在IT13级以下,不宜高于IT11级。
所以将内部直径改为Φ28+00.3。
高度10+00.2为IT11-IT12级精度。
主要成形方法是冲裁、拉深、切边冲孔和弯曲。
零件的dt/d、h/d都不太大,其拉深工艺性较好。
该零件为大批量生产,零件外形简单对称。
材料为08F钢,采用冲压加工经济性较好。
零件如图:
图1-1零件图
第二章确定冲压工艺方案
冲压工艺方案的确定是制定冲压工艺过程的主要内容,需要综合考虑各方面的因素,有的还需要进行必要的工艺计算,因此,实际确定时通常先提出几种可能的方案。
再在此基础上进行分析、比较和择优。
从零件的结构和形状可知,所需基本工序为落料、拉深、冲孔、弯曲四种。
但工序模具生产效率低难以满足大批量生产的要求,为了提高生产效率主要采用复合冲裁或级进冲裁两种方式。
若采用级进模虽然生产效率很高,但模具的结构比较复杂,对制造精度要求较高,一般生产周期长,成本高维护也比较困难。
采用复合冲裁时,冲出的零件精度和平直度较好,生产效率也较高,模具结构较级进模简单生产成本也比级进模的低。
第一节零件毛坯的尺寸计算
(1)弯曲毛坯尺寸的确定
对于r<0.5t的弯曲件毛坯长度的计算公式
Lz=5+4+5+0.6t=5+5+4+0.6×1=14.6
(2)拉深次数的确定及尺寸计算
因板料厚度t为1mm故按厚度中线尺寸计算,如图所示。
2.1.1计算坯料尺寸
D=(d22+4d2H-1.72rd2-0.56r2)½
=(29*29+4*29*10.5-1.72*2.5*29-0.56*2.5*2.5)½=43.94mm
L1=Lz+2*2.5=19.6mm
L=L1+D=63.54mm
图2-1
2.1.2 确定拉深次数
根据坯料的相对厚度t/D=1/43.94=2.28%
拉伸系数m=d/D=29/43.94=0.66大于极限拉深系数[m],所以一次拉深成形。
第二节拟定冲压工艺方案
根据以上的分析计算,该零件的冲压加工需以下基本工序:
落料、拉深、冲Φ10mm的孔、切边、弯曲。
根据以上基本工序,拟定一下冲压工艺方案。
方案一:
落料与拉深复合→其余按基本工序。
方案二:
落料与拉深复合→冲孔与切边复合→弯曲。
方案一工序组合程度较低,生产率较低。
不过各工序模具结构简单,制造费用低,对中小批量生产是合适的。
方案二制作出的零件尺寸精度高,需要两个复合模具,可获得高的生产率,而且操作方便。
模具的结构复杂,制作周期长,生产成本高。
因此,只在大批量生产中才较适宜。
此次生产就是大批量生产故决定采用方案二的冲压工艺方案。
冲压工艺方案为:
落料与拉深复合→冲孔与切边复合→弯曲
第三章模具总体结构方案
在冲压工艺方案确定以后,根据零件的形状特点、生产批量、模具制造条件、操作与安全要求、以及利用现有设备的可能,确定每道工序所用模具的总体结构方案。
模具总体结构方案的确定包括以下内容:
(1)模具类型
模具类型主要是指单工序模、复合模、和级进模三种,模具类型应根据生产批量、冲件形状与尺寸等因素确定。
及根据冲压工艺方案确定采用复合模。
(2)操作与定位方式
根据生产批量确定采用手工操作、半自动操作或自动化操作;根据坯料或工序件的形状、冲件精度要求、材料厚度、模具类型、操作方式等确定采用坯料的送进导向与送料定距方式或工序件的定位方式。
虽然此零件的生产批量较大但合理的安排生产可用手工送料方式能够达到批量要求,且能降低模具成本,因此采用手工送料。
为了便于操作和保证零件的精度且零件不太小所以采用挡料销、导料销作为定位方式。
(3)卸料与出件方式
根据材料的厚度、尺寸与质量要求、冲压工艺性质以及模具类型等,确定卸料选用弹性卸料装置,出件选用刚性顶件装置。
(4)模架类型及精度
根据冲压件尺寸与精度,材料厚度、模具类型、送料与操作等因素确定,由于零件厚度薄,冲裁间隙较小且零件为对称的回转体拉深件,则冲裁时一般不会承受大的偏心载荷又是复合模,因此选用中间导柱圆形模架。
考虑到零件的精度要求不高但冲裁间隙较小,所以采用级模架精度。
第四章主要工艺参数的计算
第一节确定排样与裁板方案
板料规格拟选用1×900×1800mm(08F钢板)因为坯料长L=63.54mm、宽b=43.94mm,不算太小考虑到操作方便采用条料单排,取搭边值a=1.8mma1=1.5mm,则
进距:
S=b+a1=43.94+1.5=45.44mm
条料宽度:
B=L+2a=63.54+2×1.8=67.14mm
4.1.1采用纵裁
每板条料数:
n1=900÷67.14≈13条余27.18mm
每条零件数:
n2=(1800-1.5)/45.44≈39件余26.34mm
每板零件数:
n1×n2=13×39=507件
材料利用率:
η=(507×1725.5456)/900×1800=54%
4.1.2采用横裁
每板条料数:
n1=1800÷67.14≈26条余54.36mm
每条零件数:
n2=(900-1.5)/45.44≈19件余42.10mm
每板零件数:
n1×n2=26×19=494件
材料利用率:
η=(494×1725.5456)/900×1800=52%
由此可件,纵裁有较高的材料利用率,且该零件没有纤维方向行的。
故决定采用纵裁法。
图4-1排样图
现对切边冲孔复合模进行设计与加工
第二节计算该工序的冲压力及选择设备
毛坯如图所示:
1、冲压力计算
切边力:
F1=Ltσb=135.7×1×304×1.3=53628.64N
卸料力:
Fx=KxF1=0.05×53628.64=2681.432N
推件力:
FT=KTF1=0.055×53628.64=2949.58N
冲孔力:
F3=LtσB=10π×2×395=24806N
F1——冲裁力(N)
L——冲件周边长度(mm)
t——材料厚度(mm)
σb——材料抗拉强度(MPa)
Kx——卸料力系数,数值可查表
2、压力机标称压力的确定
标称压力是指滑块在工作行程内允许承受的最大负荷,而滑块必须在到达下止点前某一特定距离内允许承受标称压力。
标称压力是压力机的主要技术参数。
对于冲裁工序,压力机的标称压力应大于或等于冲裁时总冲压力的1.1~1.3倍,即Fg≥(1.1~1.3)×FΣ
冲压工艺总力:
FΣ=F1+Fx+FT+F3=84065.652N
标称压力Fg≥1.3×FΣ=110KN
因为本工序是切边冲孔复合,因此压力机标称压力时应考虑压力机的许用压力曲线,本工序可选用开式双柱可倾式压力机J23-16压力机。
J23-16压力机的主要技术规格为:
公称压力:
160KN
滑块行程:
55mm
滑块行程次数:
120次/min
最大封闭高度:
220mm
封闭高度调节量:
45mm
垫块尺寸:
40mm
模柄孔尺寸:
直径40mm深度60mm
第四节弹性卸料装置的选用
弹性卸料装置由卸料板、卸料螺钉和弹性元件(弹簧和橡胶)组成。
本设计选用弹性元件是橡胶。
弹性卸料板的平面外形尺寸等于或稍大于凹模板的尺寸,厚度取凹模厚度的0.6~0.8倍。
卸料板与凸模的双边间隙根据冲件料厚确定,一般取0.1~0.3mm(料厚时取大值,料薄时取小值)。
为了便于可靠卸料,在模具开启状态下卸料板工作表面应高出凸模刃口端面0.3~0.5mm。
卸料螺钉一般采用标准的阶梯形螺钉,取数量按卸料板形状与大小确定。
卸料螺钉的直径根据模具大小可选用8~12mm,各卸料螺钉的长度应一致,以保证装配后卸料板水平和均匀卸料。
考虑到模具的结构,选用6个圆筒形的聚氨酯橡胶,则每个橡胶所承受的顶件力为Fy=Fx/n=2681.432/6≈447N
确定橡胶的横截面积A:
取hy=10%h0,查表的p=1.1MPa,则
A=Fy/p=447N/1.1N/mm2≈406.4mm2
确定橡胶的截面尺寸:
选用直径为10mm的卸料螺钉,取橡胶上螺钉过孔直径d=12mm,则橡胶外径D根据
π(D2-d2)/4=A
求得D=(d2+4A/π)½=(122+4×44)½≈18mm
为了保证足够卸料力,可取D=20mm。
卸料板为圆形的常选用3-4个,但由于卸料力比较大经计算选用6个。
卸料螺钉的直径根据模具选用10mm。
第五节出件装置
出件装置的作用是从把零件从模具内卸出来。
把装在上模内的出件装置称为推件装置,装在下模内的称为顶件装置。
因本设计的模具装在下模内所以称之为顶件装置。
此模具选用的是刚性出件装置利用推件板和推杆把零件从模内推出。
在顶件装置中,推件板与凹模空口配合并作相对运动,对它的要求是模具处于闭合状态时,其背后应有一定的空间,以备修模和调整的需要.
第五章模具工作部分尺寸的计算
第一节切边冲孔凸、凹模计算
查表的Zmin=0.100,Zmax=0.140。
因为为自由尺寸可按IT14级精度处理查得Δ=0.36mmZmax-Zmin=0.040mm系数x=0.5
5.1.1切边
δp=0.020δd=0.030
5.1.2冲孔(Ф10mm)
x=0.5δp=0.02δd=0.02
校核间隙:
因为δp+δd=0.02+0.02=0.04mm所以符合δp+δd≤Zmin-Zmax
dp=(dmin+xΔ)-0δp=(10+0.5×0.84)-00.02=10.42-00.02
dd=(dp+Zmin)+0δd=(10.42+0.246)+00.02=10.67+00.02
dd、dp——落料凸、凹模刃口尺寸
x——磨损系数,差表冲件精度为IT14时,x=0.5
dmax——落料件的最小极限尺寸
Δ——冲件的制造公差(mm)
δp、δd——凸、凹模制造公差(mm)
Zmin——最小合理间隙(mm)
第三节凹模轮廓尺寸的确定
凹模轮廓尺寸包括凹模板的平面尺寸及厚度尺寸。
从凹模刃口至凹模外边缘的最短距离为凹模的壁厚c。
对于简单的对称形状刃口的凹模,压力中心及为刃口对称中心。
由于该零件为圆形拉深件为对称件,所以压力中心即为刃口对称中心,所以凹模的平面尺寸即可沿刃口型孔向四周扩大一个凹模壁厚来确定。
因落料凹模的刃口尺寸为Φ91.88,查表的凹模壁厚c=42~54mm因落料为圆件,所以选凹模轮廓为圆形及
D=d+2c=91.88+2×(42~54)=Φ176~200mm,经查表确定凹模轮廓D=200mm。
第四节模架的选择
模架包括上模座、下模座、导柱和导套。
冲压模具的全部零件都安装在模架上。
为了缩短模具制造周期,降低成本所以选用标准模架。
选择模架结构时要根据工件的受力变形特点,坯件定位、出件方式、送料方向,导柱受力状态操作是否方便等方面进行综合考虑。
选择模架尺寸时要根据凹模的轮廓尺寸考虑,一般在长度上及宽度上都应比凹模大30-40mm。
模架厚度一般等于凹模厚度的1-1.5倍。
冲压模具的闭合高度应大于压力机的最小装模高度,小于压力机的最大装模高度。
模具的闭合高度