洁净煤技术第05章洁净燃烧技术文档格式.docx
《洁净煤技术第05章洁净燃烧技术文档格式.docx》由会员分享,可在线阅读,更多相关《洁净煤技术第05章洁净燃烧技术文档格式.docx(13页珍藏版)》请在冰豆网上搜索。
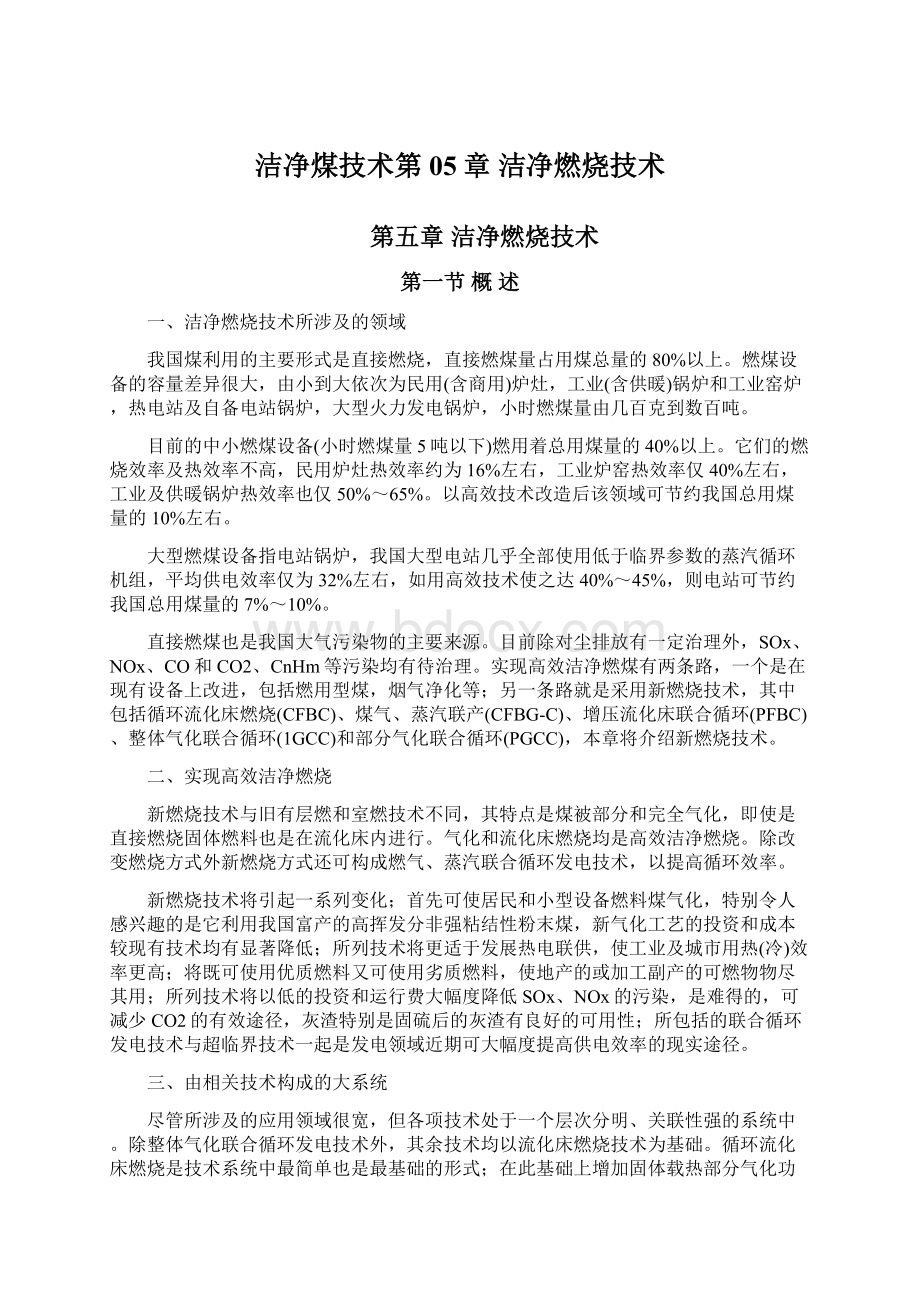
所列技术将以低的投资和运行费大幅度降低SOx、NOx的污染,是难得的,可减少CO2的有效途径,灰渣特别是固硫后的灰渣有良好的可用性;
所包括的联合循环发电技术与超临界技术一起是发电领域近期可大幅度提高供电效率的现实途径。
三、由相关技术构成的大系统
尽管所涉及的应用领域很宽,但各项技术处于一个层次分明、关联性强的系统中。
除整体气化联合循环发电技术外,其余技术均以流化床燃烧技术为基础。
循环流化床燃烧是技术系统中最简单也是最基础的形式;
在此基础上增加固体载热部分气化功能后构成煤气、蒸汽联产;
增压流化床联合循环是在压力下的流化床燃烧,然后构成联合循环发电;
部分气化与联合循环结合可构成一个难度较低、效果不错的联合循环系统;
将煤气、蒸汽联产结构增压可形成效率更高的第二代增压流化床联合循环发电;
高温净化则是IGCC和PFBC都需解决的问题。
调查表明:
所涉及的技术还可以用于在我国若干大煤田建设煤化工和天然气生产基地。
以储有高挥发分非强粘结性煤达数百亿吨的山西朔州地区为例,将现有煤产量的1/4以短回收期、低成本技术转化后即可生产数百万吨/年尿素和数亿m3/年天然气。
可以看出不同层次的技术将用于不同容量和不同目的,它们之间有很强的相关性,统一规划将有利于系统的发展。
第二节洁净燃烧技术的国内外发展历史及现状
一、循环流化床燃烧技术
循环流化床燃烧技术的前身是鼓泡流化床燃烧技术。
鼓泡流化床燃烧技术已显示燃料适应性强,能在燃烧中脱硫和降NOx的优点。
60和70年代鼓泡床技术在中国得到很大发展,但该技术也表现出严重缺点,如细颗粒(≤800P)燃烬度差;
床内浸埋受热面磨损严重;
脱硫时钙利用率仅为20%以下,床温超过900℃后,脱硫效率显著降低等,德国Lurgi公司首先推出循环流化床燃烧技术,它采用高操作气速(8~10m/s)和高携带率(8~12kg颗粒/kg烟气),同时设置炉外换热床,1987年首台270t/h炉投产。
芬兰Ahlstrom公司舍去炉外换热床,依靠炉内水冷壁换热,最初的锅炉出现水冷壁因高速高浓度而严重磨损,此后普遍采用中等气速(5~6m/s)和中等携带率(3~5kg/kg)。
Luigi公司的270t/h炉出现旋风分离器超温,经诊断确定其中燃烧份额过大,采取将燃料由全部≤900μ增至≤6mm获得解决。
目前Ahlstrom技术主要用于130~410t/h容量,再增大容量遇到炉内受热面不足的困扰,拟用鳍式水冷壁解决,结构过于复杂;
而Lurgi型技术(包括法国Stean和美国ABB-CE)更适于≥410t/h容量,特别是带再过热的锅炉。
瑞典Stucvick研究所首先采用槽形惯性分离器,后发现分离效率不够高,增加了中温区的二级分离,该炉型结构简单,但不适于大容量,Duich—Babcoke针对高温旋风分离器的缺点研制了中温分离循环床锅炉,可惜忽视了流化床中CO易偏高的弱点。
由于CO排放偏高,在发达国家无市场,于是,转向不严格限制CO排放的我国,北京Bahcok锅炉厂就引进了此项技术。
美国FosterWheeler公司针对大型非冷却分离器的缺点研制了蒸汽冷却高温分离器,许多厂家纷纷效仿,但多在研制一台发现成本过高,难以运输的缺点后放弃此方案。
Ahlstrom公司采用水冷壁构成方形分离器有明显优势,技术出现后不久,该公司的循环床部分被FW公司兼并。
清华大学首先采用炉内冷却床技术,简化了换热床结构。
后为FW、Lurgi、Stean和ABB-CE效法。
清华大学和中科院工程热物理所是国内较先研究循环床技术的单位,清华大学在小容量锅炉采用低携带率平面流分离,目前广泛用于6~35t/h容量,结构简单,但埋管易磨损。
所研制的中等容量无埋管平面流分离循环床炉(35~75t/h),因循环量偏低而不易达到出力。
在总结已有经验基础上采用差速循环床,平面流两级分离或用水冷壁构筑的异形分离器等新技术形成新一代中小容量循环床锅炉。
75t/h带异形分离器循环床炉运转正常,结构显著优于非冷却旋风分离锅炉,分离效果甚佳,飞灰含碳远低于引进的炉型。
20~35t/h差速床锅炉在研制中。
中科院工程热物理所的第一代产品与Ahlstrom产品类似,其第二代产品采用了百叶窗两级分离。
一些单位引进了Ahlstrom型锅炉。
在燃用较高灰分和破碎粗糙的煤时,达到出力方面也出现困难。
脱硫技术在流化床燃烧技术中占重要地位,循环床技术可以使细颗粒石灰石发挥更大作用,因此在≥80%的脱硫效率时Ca/S可降到2。
清华大学对脱硫的微观结构进行深入研究,认为石灰石的孔反应特性既影响钙利用率又影响最佳脱硫温度,首创将石灰石粉粘制成高活性高温粒状脱硫剂,不仅Ca/S降到1.7以下,而且最佳脱硫温度由850℃提高到950℃,有利于传热、燃烧,更使困扰流化床燃烧技术的N20排放过高问题得以解决。
柳州市已按清华技术广泛用于流化床锅炉脱硫。
二、煤气一蒸汽联产技术
煤的气化包括完全气化和部分气化两类。
人们早已期盼将煤中不同组份加以合理利用,即使较易气化的挥发物变为煤气而将不易气化的固定碳(它的完全气化往往要求制氧、高温)用于燃烧70年代末期,美、英联合推出CO—Gas工艺,完成了中试。
其流程为:
煤先在650℃左右裂解以求多产油品,所余半焦被循环的热焦加热,其中的挥发分和碳与水蒸气发生水煤气反应生成以CO和H2为主的煤气。
加热段是一个能燃烬半焦的液态排渣旋风炉,残焦没有利用。
由于提升加热段效率不够高,残焦损失大,总效率不高,但已开创了一个较好的先例。
大连理工大学在80年代中后期,以鼓泡流化床烟气为热源加热半焦,实现在650℃载热裂解工艺。
因气化温度低,煤气产率不高,半焦又没能很好利用,经济上不能自持。
进入80年代后,循环床燃烧技术日益发展,已完全有能力燃烬焦粉,清华大学张绪棉在1985年初中国科协出版的《2000年的中国研究资料》中明确建议开发载热部分气化和蒸汽联产技术。
1990年后多个单位开始此项研究,研究的初级阶段是灰载热低温气化,即以循环床灰为载热介质,在650—750℃的床温下气化。
这些方案都在寻找用户。
为提高煤气产率,尽量降低焦油产率和焦炭热量,以减少净化困难,降低单位煤气量的投资额,清华大学煤燃烧工程研究中心提出了快速床提升焦载热气化方案。
目前在清华大学电厂建立了一个小时处理2吨煤的工业试验装置,已于1997年5月建成产气。
高煤气产率和较高烃含量为在某些地区将煤转化为化工产品及天然气创造条件。
三、整体煤气化联合循环发电技术(1GCC)
早在1972年,世界上第一个工业规模的煤气化联合循环发电机组在德国Lunen市克尔曼电厂内建成,容量为170MW,采用Lurgi固定床气化炉,完成预定试验后于70年代末停运。
1984年,在美国加州Coolwater电厂建成100MW机组,该机组采用Texa—co气流床气化工艺。
1984~1989年间曾对四种煤进行一系列试验研究,累计运行27100小时。
试验证明,该机性能良好,运行可靠,污染排放很小。
电站效率仅为31.2%(HHV),在完成示范运行后停运。
美国的另一座IGCC示范电站位于路易斯安那州的LGTI电厂,于1987年投产,运行至今。
该机组采用Destec气流床气化工艺,电站总折算功率为160MW,净效率为34.2%(HHV)。
荷兰Buggenum电站于1994年3月投产的IGCC机组采用Shell气流床气化工艺,净功率达253MW,净功率为43.2%。
进入1994年后,国际上IGCC电站建设速度明显加快。
机组容量均在250~500MW,净效率提高到40%~45%,燃气轮机进口初温提高到1250~左右,初投资降到2000美元/kW左右。
国内于1979年曾立项在苏州电厂建设一座10MW级的IGCC电站,所用气化工艺,燃机、汽机均不先进,后工程中止。
但国内许多单位如电力部西安热工研究院、清华大学、中科院工程热物理所、上海发电设备成套设计研究所等都继续进行相关研究。
第三节洁净燃烧技术原理及特点
一、流化床与智环流化床燃烧
固体颗粒在自下而上的气流作用下具有流体性质的过程称为流化。
颗粒尺度较大而操作气速较小时在床下部形成鼓泡流化床,即其连续相是气固乳化团,其分散相是以气为主的气泡。
在气泡上浮力作用下床内颗粒团之间有较强的质交换。
颗粒尺度较小、操作气速甚高,加以使用分离器使逸出物料不断返回时,形成另一流化形态,称快速流化床,其分散相为气固乳化团,连续相为含少量颗粒的气体。
早期的循环床是快速流化床,当时,燃料颗粒≤90μ,操作气速为8—10m/s,炉膛出口气固携带率为10~20kg/kg。
过细的燃料颗粒造成旋风分离器内燃烧份额过大,易超温结渣,燃料粒度增为≤6mm后有所改善。
过高的气速和浓度造成水冷壁磨损,为此气速降为5~6m/s。
如此变化之后,流动形态变化很大,在炉膛下部形成鼓泡床,炉膛上部的快速流化床特征也不再明显,只有在炉膛出口气流折转区,因颗粒失去上举力而浓缩,在炉膛出口下部和部分边壁附近出现乳化团。
目前的循环床是有灰循环过程的流化床炉的总称。
在循环床诸过程中,组织好沿循环路线的各区域内发热与放热间的正常平衡是首要任务,即组织好燃烧、对受热面传热和物料载热。
气速和浓度的降低对炉内燃烧及传热工况产生影响。
就发热而言,燃料变粗和气速降低使燃烧份额下移,即炉膛下部密相区产热量增加,一旦吸热不足,床温将升高,许多锅炉达不到出力的主因即在于此。
因此,当气速降低后,降低燃料粒度(或提高挥发分)是保持密相区较低燃烧份额的重要手段。
从吸热角度看,循环量对传热和载热过程有重要影响。
对于以灰为主循环物料的锅炉,循环量c与燃料燃烧所形成的灰颗粒粒度分布即成灰特性有关。
设某一粒度的成粒量为e,依灰平衡e=a+b,a为由分离器逸出的某一粒度颗粒量,b为排渣带出的某一粒度颗粒量,一般称
为分离效率ηa,相类比
为排渣的选则效率ηb,而
,这一表达式说明ηa与ηb对循环量同样重要,实际上对细粒度ηb接近于1,循环量主要取决于ηa;
对粗粒度ηa接近于1,则循环量主要取决于ηb。
不同粒度颗粒间也相互影响,例如燃料还生成一些不能参与循环的大颗粒,当它们被排出时将携带部分可参与循环颗粒,对于能参与循环但粒径偏粗的颗粒,a(c)与不参与循环的大颗粒量接近反比,大的不参与循环颗粒量,将抑制循环量,这就部分说明了为什么国外炉型在使用高灰和粗破碎燃料时出力不足。
减少不参与循环的颗粒量,可显著提高循环量。
强化破碎固然可达此目的,但电耗和细微难燃颗粒量将增加。
气速将影响可参与循环的粒度,高气速时可参与循环的粒度增大。
另一方面,气速的提高将增加a:
b,速度越高在渣中带出的份额越少,循环量越大。
高气速可造成循环物料的宽筛分和高浓度,这两点都更有利于炉膛上部产生乳化颗粒团,而乳化团将增强传热,延长颗粒停留时间,改善分离特性。
实测表明在0.5~3kg/k8范围内,对流换热系数几乎与携带率呈线性关系。
图5-1循环床物料平衡模型
≥150μ的颗粒有着高的分离效率,颗粒在炉内停留时间长,气固相对运动速度大,燃烧速率较高,燃烬程度高;
≤lOOμ的颗粒因粒度小,周围温度低,气固相对运动速度小,处于表面动力反应区,其反应速度甚低,加之分离效率低,所以燃烬程度差,是造成不完全燃烧损失的主要原因。
提高床温和延长停留时间可减少未燃烬损失,但作用有限,结合脱硫将飞灰成粒再燃是解决飞灰未燃烬损失的根本途径。
除小颗粒难以燃烬外,另一个值得注意的是气相未燃烧损失,由于给煤点集中,挥发份释放集中,如不能与氧充分混合将难燃烬,另一方面,乳化团内往往氧不足而气泡或非乳化团区的氧过剩,因此流化床常出现CO和O2浓度同时很高的现象。
高温分离过程中气体间能强烈混合燃烬度提高,中温分离达不到燃烬气相可燃物的目的。
差速循环床是认真研究各种过程后出现的依照规律组织过程的典型。
它将床下部某区域的气速恢复到8~12m/s,但在上升约3m以后截面扩大,气速迅速降为≤6m/s,由于高速而带起的粗颗粒将回落,与高速区并列的是一个床速仅为lm/s左右的低速区,颗粒将自然地落入该区,在上升与回落过程中颗粒间相互作用明显,又提供了团聚的条件。
低速床内埋设足够的受热面,因颗粒细、流速低有高的换热系数,又保证受热面不磨损。
自然,高速区内的燃烧份额将明显降低。
与仅依靠分离器分离的锅炉不同,主循环颗粒不再仅为300μ左右的一个狭窄粒度带,。
可向粗粒径延伸到1.5mm左右,是一个很宽的带,而且由于分离器入口的较粗颗粒增加,分离效率提高,因此,循环量甚大。
大循环量、强传热和高速燃烧区低的燃烧份额,使锅炉的出力和燃料适应特性改善。
在没有采用差速循环床的条件下,用水冷壁构筑的异形分离器是循环床锅炉结构的重大进展。
现有高温旋风分离器有不冷却与汽冷两种。
不冷却分离器内耐火衬里很笨重,只能采用下支撑结构,它与燃烧室的上悬吊结构有矛盾,总重也太重,启动时也容易损坏,人们一直想改变它。
FW公司首先采用过热器构筑汽冷分离器,将分离器制成圆形,后发现难以运输和安装。
以水冷壁构筑的分离器外形是方形,制造运输方便,内部四角抹圆,分离效果相当好,与不冷却筒一样能达到高燃烬度和较大循环量,其优势是特别适于大型化。
由于差速床已完全解决了炉内燃料与传热问题,分离器的任务将有所改变,即它首先应保证气相可燃物燃烬,至于细颗粒的燃烬可以用设于低温区的第二级分离和飞灰制粒再燃解决,对高温分离效率的要求可以降低,预计,这一变化将形成新一代大型循环流化床锅炉。
加入到流化床燃烧室中的石灰石受热分解,在适宜的温度下氧化钙与SO2和O2反应生成硫酸钙,即:
CaCO3→CO2+CaO↑
CaO+SO2+1/2O2→CaSO4
由于硫酸钙与碳酸钙和氧化钙的分子体积比大约为3:
2:
1,而CO2逸出时生成的孔隙体积过于纤细,在颗粒表面的孔隙端口处一旦生成CaSO4就很容易将小孔堵塞,外界的S02和02将不再能继续向孔内扩散,与颗粒内部的CaO反应。
有关研究者曾对美国各种典型石灰石进行测定,当粒径为lmm左右时,其钙利用率很少超过20%,含MgCO2较多的白云石虽可籍MgO生成时的孔而使CaO利用率提高,但总的重量份额利用率也不高。
有鉴于此,清华大学用粘结细石灰石粉的方法重组了颗粒孔分布,获得了40%以上的钙利用率。
所用粘结剂是脱硫时的飞灰,它有较好的胶凝性。
用飞灰作粘结剂还可使飞灰中的碳得以燃烬,许多情况下,飞灰含碳高达10%~20%。
清华大学研究还发现温度对脱硫效果的影响实际也是孔堵塞作用的结果。
当温度增高时,化学反应速度的增大快于扩散速率增加,即孔口更易堵塞。
对于重新组织孔结构的颗粒,孔长缩短,温度增高的影响不再显著。
这一结论使最佳脱硫温度由通常认定的850℃提高到950℃。
温度提高有利于燃烧、传热。
流化床燃烧过程中CO含量偏高,温度偏低,其NOx生成量仅为常规燃烧方式的25%左右,但人们还发现过低的燃烧温度使NOx排放增加,一度因此怀疑到流化床燃烧是否适于发展。
当燃烧温度由850℃提高到950℃时N20排放显著降低,NOx增加不显著。
二、煤气、燕汽联产
煤中挥发分受热分解产生煤气、焦油和焦或半焦。
煤种、加热温度、加热方式和气氛等条件不同,煤气产率不同;
焦油和焦在高温下还可与水蒸汽反应再次生成煤气,它们是吸热反应。
用固体载热是一种加热方式,其特点是可将燃烧加热过程与气化过程分别在两个容器中完成,两侧气体分开而固体物料在其中循环。
焦或半焦燃烧生成热既加热物料,又产生蒸汽。
利用循环床锅炉循环灰为热源称为灰载热,以燃料生成的焦载热称为焦载热。
前者成粒量较少,颗粒偏细,床速偏低,因而循环量较小。
与此同时灰与气体的分离点在炉膛出口,灰温偏低。
低温和低循环量造成低气化室温度,气化室采用流化床时,气体焓增较大,气化室温度更低。
低气化室温度使焦油量增加,半焦中挥发分含量大,加之床层含碳低,水煤气反应不旺盛、气化率不高。
低气化率、高半焦热份额使单位煤气量的蒸汽产率增加,增加了单位煤气量的总投资。
该工艺的细灰往往集中于煤气中,增加了净化的难度。
焦载热工艺成粒量较多,颗粒偏粗,燃烧提升床无受热面,床速可很高,因而循环量很大,物料温度高达1000℃左右,气化室温度可达950℃左右,焦油含量减到很少,焦中不含挥发分,加之床层含碳量高,水煤气反应旺盛,煤气产率很高。
用不同流化介质可调整水煤气反应量,从而可调整煤气成分和热值。
高热值时,可适于城市煤气,较低热值时,可适于煤化工及联合循环发电。
煤气比例较大时,煤气中H2及CO含量可达70%一80%,CH4(含CnHm)含量约为10%~12%,可以通过分离手段将二者分离,前者是合成化工原料,而且其氢碳比接近2:
1,适于合成甲醇,后者是优质城市煤气,所余焦燃烬产生蒸汽,可用于化工过程或发电。
该工艺的成灰主要在锅炉中完成,所成细灰不再进入气化室,净化相对简单。
在不太需要热电的情况下,残焦是优质无烟燃料,所制型煤具有高的反应活性,上火快、火力旺盛。
高煤气产率甚至多产焦而少产电,都将大幅度降低单位煤气量的总投资。
三、部分气化联台循环发电
载热部分气化的煤气具有≥12.5MJ/m3的热值,经湿净化加压后送入燃气轮机燃烧室燃烧,空气经压缩机加压后在循环床锅炉低速床内加热到600℃以上,燃气在燃气轮机内作功后进入锅炉,用其中的氧燃烧焦粉产生蒸汽,蒸汽推动蒸汽轮机,这样就构成了一个联合循环发电技术。
提高煤气产率和空气预热温度都可提高燃气轮机进口温度从而提高循环效率。
燃烧焦粉的循环床锅炉应采用差速循环床:
一方面是由于焦粉已失却挥发分,其燃烧分额易下移,采用差速床可相对降低高速燃烧区燃烧份额;
另一方面低速传热床的换热系数很高,是布置空气加热管及再热器的理想场所。
从近期看本工艺是改造现有电站的理想方案,从远期看本工艺能吸纳高燃气轮机进口温度和超临界技术,实现高循环效率。
用它来改造125MW机组可使供电效率由32%提高到38%以上。
四、整体煤气化联合循环
图5—2给出了一个典型的整体煤气化联合循环系统。
图5-2整体煤气化联合循环系统简图
其联合循环系统与一般的以天然气为燃料的余热锅炉型联合循环相同,只是煤需要一个气化及煤气换热和净化系统。
气化炉的型式有若干种,目前都使用氧和水蒸汽作为气化介质,因此需要空气分离设备,目前的净化工艺都是湿式净化。
就联合循环系统而言,该技术有很高的成熟度,目前的难点及潜力主要集中在煤气化系统。
第四节洁净燃烧技术的工艺及设备
一、循环流化床燃烧(CFBC)
循环流化床燃烧技术的主要设备是循环流化床锅炉。
循环床锅炉有着与常规锅炉类似的水汽系统,差异主要表现在燃烧系统,在辅属系统中煤制备系统、鼓风及引风除尘系统、脱硫剂系统、排渣系统、仪表控制系统均不尽相同。
循环流化床锅炉包括燃烧室和尾部受热面,其汽水系统与常规燃烧方式锅炉类似,由于压力及温度参数而区分为单汽包炉(≥3.82MPa)和双汽包炉(≤2.45MPa)。
对于双汽包炉,多采用低矮炉膛,炉膛又多采用重型或半重型炉墙,锅炉全部采取支撑结构;
对于单汽包炉,炉膛可以采用膜式壁结构和悬吊结构。
循环床炉膛的底部设有布风板和风室,布风板上布有许多风帽,风帽分为多孔及单孔两大类。
大型锅炉多用膜式壁延长构成布风板及风室,这样就可以实现床下油点火、点火成功率很高。
非水冷壁结构锅炉多用钢板制作布风板,只能采取床上点火,点火技巧决定其成功率。
炉膛底部是密相燃烧床,上部是稀相炉膛,几种特殊炉型设有炉外换热床或并联换热床。
密相燃烧床内埋设的受热面是低携带率锅炉的主要蒸发受热面;
无换热床锅炉的主要蒸发受热面是膜式水冷壁;
换热床内既可以布置蒸发受热面,也可以布置过热器、再热器、空气加热器。
在炉膛上部布置的高温过热器使锅炉具有良好的负荷调节性。
循环床锅炉与常规燃烧方式和鼓泡床锅炉的最大差异是它有着物料循环系统。
物料分离循环系统分为三大类:
常用高温分离器完成分离,中低温分离和炉内重力分离则作为高温分离器分离的补充。
单纯的中温分离虽可缩小分离器体积,但CO排放偏高。
差速循环床强化了炉内重力分离。
高温分离器有许多类型,非冷却旋风筒是目前最常用的形式,它的分离效率高,但结构特性差,它要求支撑结构,因此需解决与悬吊式炉膛间的膨胀密封问题,它的耐火耐磨层很厚,总重很大,抗热震性差。
在大容量范围内,以膜式壁构成的水冷旋风分离器大有取代非冷却旋风筒的可能,其耐火耐磨层减薄,总重减轻,可以悬吊,膨胀问题易解决。
平面流动惯性分离在结构上有着占地少、重量轻、结构简单的优势,由它们构成的锅炉很类似传统结构形式,也可以使炉身矮化,由于分离效率不高,有时需与中低温分离复合或与重力分离复合以保证循环量和燃烬程度。
采用复合结构后其优势更加明显。
预计在重力分离可以解决循环量问题后,适于大型化的平面流动惯性分离可能取代各类旋风筒。
被分离的物料往往通过一个阀返回燃烧区,最常用的阀是非机械的J形阀,它的驱动需要较高风压。
对中小容量,低携带率循环床炉,采用翼形阀也很成功。
谈及循环床锅炉的燃料适应性,必须分别两个概念,一个是泛指在常规燃烧方式锅炉上难以燃用的多种劣质燃料,如高水分、高灰分、低挥发分和低灰熔点燃料,可以利用循环床锅炉燃用,但这并不等于任何一个循环床锅炉在燃用性质差异很大的燃料时都能维持设计参数,这首先因为对于不同燃料而言,它们的理论空气量和理论烟气量差异可能很大,当燃料热值低的时候,差异更显著;
其次,循环床锅炉中沿气流路程的不同区域,特别是密相燃烧区的正常热平衡是正常运行的关键,而燃料的变化可能影响各处的平衡状态。
燃料的发热量、挥发分和粒度分布都影响密相区燃烧份额,所以不同炉型,不同燃料其燃料制备系统应不同。
为保证供煤可靠性,中大型锅炉用燃料应先行干燥,使外在水分低于7%,燃料的干燥可以与破碎筛分系统结合。
电力部西安热工研究院和清华大学煤燃烧工程研究中心在“八五”攻关中分别设计了两种燃料干燥与破碎系统,前者以热风为热源,在提升段干燥和筛分颗粒,配以锤式破碎机;
后者以蒸汽为热源,以流化床干燥和筛分颗粒,配以环锤和辊式破碎机,两者都注意到对粒度