现代生产管理的最优方式精益生产Word下载.docx
《现代生产管理的最优方式精益生产Word下载.docx》由会员分享,可在线阅读,更多相关《现代生产管理的最优方式精益生产Word下载.docx(7页珍藏版)》请在冰豆网上搜索。
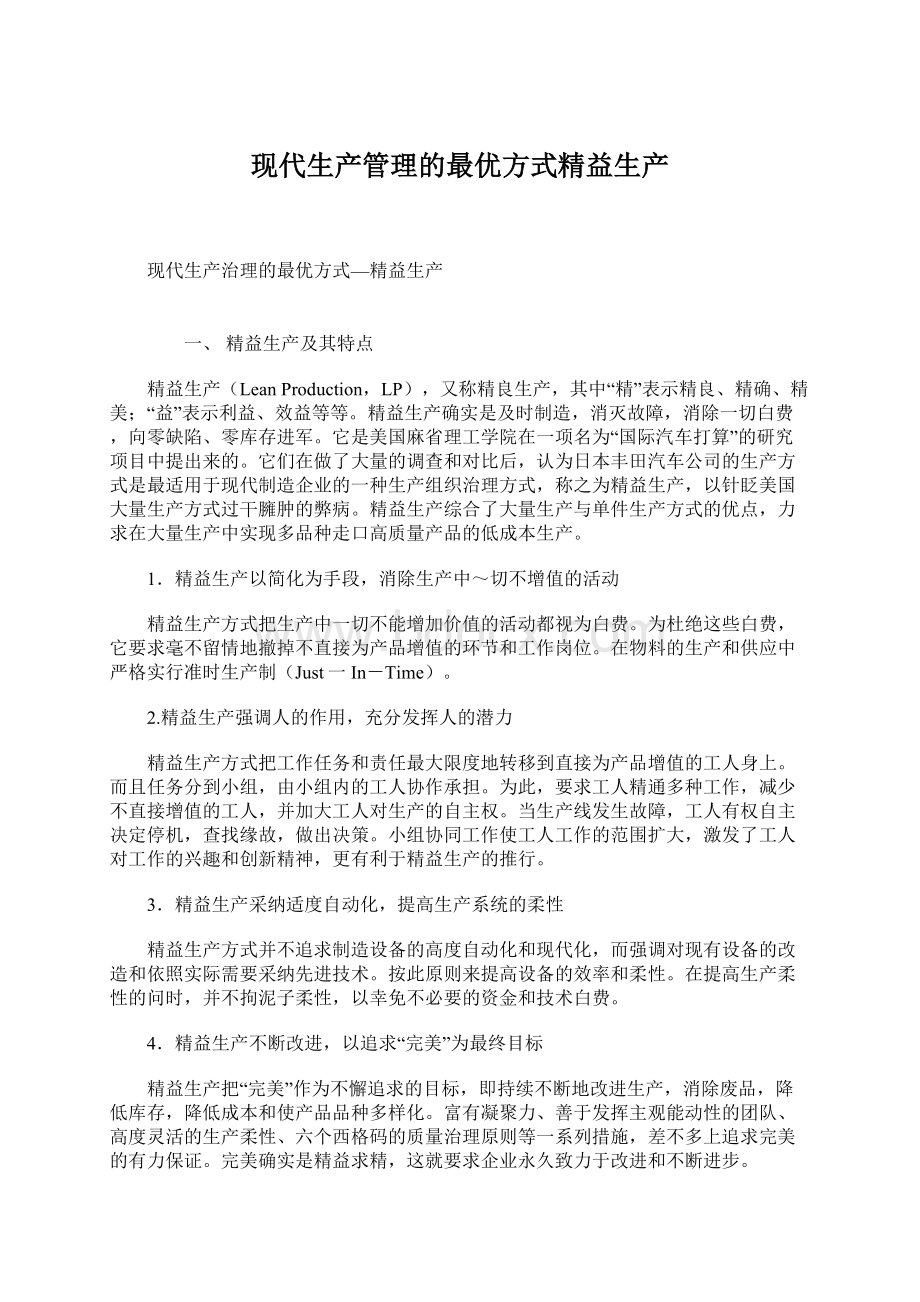
在物料的生产和供应中严格实行准时生产制(Just一In-Time)。
2.精益生产强调人的作用,充分发挥人的潜力
精益生产方式把工作任务和责任最大限度地转移到直接为产品增值的工人身上。
而且任务分到小组,由小组内的工人协作承担。
为此,要求工人精通多种工作,减少不直接增值的工人,并加大工人对生产的自主权。
当生产线发生故障,工人有权自主决定停机,查找缘故,做出决策。
小组协同工作使工人工作的范围扩大,激发了工人对工作的兴趣和创新精神,更有利于精益生产的推行。
3.精益生产采纳适度自动化,提高生产系统的柔性
精益生产方式并不追求制造设备的高度自动化和现代化,而强调对现有设备的改造和依照实际需要采纳先进技术。
按此原则来提高设备的效率和柔性。
在提高生产柔性的问时,并不拘泥子柔性,以幸免不必要的资金和技术白费。
4.精益生产不断改进,以追求“完美”为最终目标
精益生产把“完美”作为不懈追求的目标,即持续不断地改进生产,消除废品,降低库存,降低成本和使产品品种多样化。
富有凝聚力、善于发挥主观能动性的团队、高度灵活的生产柔性、六个西格码的质量治理原则等一系列措施,差不多上追求完美的有力保证。
完美确实是精益求精,这就要求企业永久致力于改进和不断进步。
从以上的特点能够看出,精益生产是一种适应现代竞争环境的生产组织治理方法。
它有着极强的生命力,受到各国企业的极大重视。
二、传统生产与杨益生产的区不
精益生产汲取了传统生产方式的大量优点,同时克服了传统生产方式的缺点。
表1列举了精益生产和传统生产的某些重要特征。
上述12个指标分不从不同的侧面反映了传统的批量生产和精益生产的特征差异。
精益生产显示了比传统生)“方式更为优秀的特点。
精益生产集准时生产制和柔性制造的优点干一体,在质量治理上贯彻六个西格码的质量治理原则,不是依靠检查,而是从产品的设计开始就把质量问题考虑到里面去,确保每一个产品只能严格地按照惟一正确的方式生产和安装;
在库存治理上,体现了节约成本的要求,在满足顾客的需求和保持生产线流淌的同时,做到了产成品库存和在制品库存最低;
在职员激励上,精益企业里职员被给予了极大的权利,真正体现了当家作主的精神,同时人事组织结构趋于扁平化,消除了上级与下级之间相互沟通的隔阂,做到全厂上下~条心。
所有这一切都体现了降低成本、提高产品竞争力的要求。
对那些早已实现了精益生产的企业来讲,它们早享受了精益化所带来的种种好处,如劳动利用率大幅度上升,产品市场竞争力的提高,库存降低,生产周期缩短,成本下降等等。
假如传统企业还在重复过去的生产方式,不进取,不创新,是难以与精益企业相抗衡的。
因此,传统企业只有探究精益之路,才能赢得竞争。
三、传统企业的精益之路
消灭白费是精益企业始终不渝的追求。
白费在传统企业内无处不在:
生产过剩、零件不必要的移动、操作工多余的动作、待工、质量不合格/返工、库存、其他各种不能增加价值的活动等等。
向精益化转变,差不多思想是通过持续改进生产流程,消灭一切白费现象,其重点是消除生产流程中一切不能增加价值的活动,传统企业的精益之路能够形象地表示为图1。
1.改进生产流程
精益生产利用传统的工业工程技术来消除白费,着眼于整个生产流程,而不只是个不或几个工序。
(1)消除质量检测环节和返工现象。
假如产品质量从产品的设计方案开始,一直到整个产品从流水线上制造出来,其中每一个环节的质量都能做到百分百的保证,那么质量检测和返工的现象自然而然就成了多余之举。
因此,必须把“出错爱护”(Poka-Yoke)的思想贯穿到整个生产过程,也确实是讲,从产品的设计开始,质量问题就差不多考虑到里面去,保证每一种产品只能严格地按照正确的方式加工和安装,从而幸免生产流程中可能发生的错误。
(2)消除零件不必要的移动。
生产布局不合理是造成零件往返搬动的根源。
在按工艺专业化形式组织的车间里,零件往往需要在几个车间中搬来搬去,使得生产线路长,生产周期长,同时占用专门多在制品库存,导致生产成本专门高。
通过改变这种不合理的布局,把生产产品所要求的设备按照加工顺序安排,同时做到尽可能的紧凑,如此有利于缩短运输路线,消除零件不必要的搬动,节约生产时刻。
(3)消灭库存。
把库存当作解生产和销售之急的做法犹如饮鸩止渴。
因为库存会掩盖许多生产中的问题,还会滋长工人的惰性,更糟糕的是要占用大量的资金。
在精益企业里,库存被认为是最大的白费,必须消灭。
减少库存的有力措施是变“批量生产、排队供应”为单件生产流程(l-piece-flow)。
在单件生产流程中,差不多上只有一个生产件在各道工序之间流淌,整个生产过程随单件生产流程的进行而永久保持流淌。
理想的情况是,在相邻工序之间没有在制品库存。
实现单件生产流程和保持生产过程的流淌性还必须做到以下两点:
同步一在不间断的连续生产流程里,必须平衡生产单元内每一道工序,要求完成每一项操作花费大致相同的时刻。
平衡一合理安排工作打算和工作人员,幸免一道工序的工作荷载一会儿过高,一会儿又过低。
然而,在某些情况下,还必须保留一定数量的在制品库存,而那个数量就取决于相邻两道工序的交接时刻。
实施单件生产流程、同步和平衡这些措施,其目标是要使每项操作或一组操作与生产线的单件产品生产时刻(Tacttime)相匹配。
单件产品生产时刻是满足用户需求所需的生产时刻,也能够认为市场的节拍或韵律。
在严格的按照Tacttime组织生产的情况下,产成品的库存会降低到最低限度(在下面的。
个例子中,将会深入研究Tacttime)。
2.改进生产活动
仅仅对生产流程予以持续的改善,还不足以实现精益化生产,还要进一步改善生产流程中的个不活动,以更好的配合改进过的生产流程。
在没有或专门少库存的情况下,生产过程的可靠性至关重要。
要保证生产的连续性,必须通过减少生产预备时刻,机器检修、待料的停工时刻和减少废品的产生。
(l)减少生产预备时刻。
减少生产预备时刻一般的做法是,认真细致地做好开机前的一切预备活动,消除生产过程可能发生的各种隐患。
·
列举生产预备程序的每一项要素或步骤;
辨不哪些因素是内在的(需要停机才能处理);
哪些是创、在的因素(在生产过程中就能处理)
尽可能变内在因素为外在因素;
利用工业工程方法来改进技术,精简所有阻碍生产预备的内在的、外在的因素,使效率提高。
(2)消除停机时刻。
全面生产维修(TotalProductiveMaintenance,TPM)是消除停机时刻最有力的措施,包括例行维修、预观个性维修、预防性维修和立即维修四种差不多维修方式。
例行维修--一操作工和维修工每天所作的维修活动,需要定期对机器进行保养。
预测性维修--利用测量手四分析技术预测潜在的故障,保证生产设备可不能因机器故障而造成时刻上的损失。
其意义在于未雨绸缪,防患于未然。
预防性维修--一为每一台机器编制档案,记录所有的维修打算和维修纪录。
对机器的每一个零部件都做好完全、严格的保养,适时更换零部件,保证机器不发生意外故障。
立即维修--一当有故障发生时,维修人员要召Z即来,随叫随到,及时处理。
由于在连续生产流程中,两道工序之间少有库存,若机器一旦发生故障,整个生产线就会瘫痪,因此消除停机时刻对维持连续生产意义重大。
TPM的目标是零缺陷、无停机时刻。
要达到此目标,必须致力于消除产生故障的根源,而不是仅仅处理好日常表现的症状。
(3)减少废品产生。
严密凝视产生废品的各种现象(比如设备、工作人员、物料和操作方法等),找出根源,然后完全解决。
此外,那些消除返工的措施也同样有利于减少废品的产生。
3.提高劳动利用率
提高劳动利用率,有两个方面,一是提高直接劳动利用率,二是提高间接劳动利用率。
提高直接劳动利用率的关键在干一人负责多台机器,这就要求对操作工进行交叉培训,交叉培训的目的是使生产线上的操作工能够适应生产线上的任何工种。
交叉培训给予了工人极大的灵活性,便于协调处理生产过程中的异常问题。
实现一人多机的前提是建立工作标准化制度。
工作标准化是通过对大量工作方法和动作进行研究,以决定最有效和可重复的方法。
工作时职员必须严格的按照标准化进行,其意义不仅在于直接劳动的利用率的提高,而且也提高了产品的质量,因为出错爱护和防止废品产生等一系列技术措施的采纳,确保了每一项操作只能按照惟一正确的方法进行。
在生产设备上安装自动检测的装置同样能够提高直接劳动利用率。
生产过程自始至终处在自动检测装置严密监视下,一旦检测到生产过程中有任何异常情况发生,便发出警报或自动停机。
这些自动检测的装置一定程度上取代了质量检测工人的活动,排除了产生质量问题的缘故,返工现象也大大减少,劳动利用率自然提高。
间接劳动利用率随生产流程的改进和库存、检验、返工等现象的消除而提高,那些有利于提高直接劳动利用率的措施同样也能提高间接劳动率。
库存、检验、返工等环节所消耗的人力和物力并不能增加产品的价值,因而这些劳动通常被认为是间接劳动,若消除了产品价值链中不能增值的间接活动,那么由这些间接活动引发的间接成本便会显著降低,劳动利用率也相应得以提高。
总而言之,精益生产是一个永无止境的精益求精的过程,它致力于改进生产流程和流程中的每一道工序,尽最大可能消除价值链中一切不能增加价值的活动,提高劳动利用率,消灭白费,按照顾客订单生产的同时也最大限度的降低库存(见图2)。
精益是一种全新的企业文化,而不是最新的治理时尚。
由传统企业向精益企业的转变不能一蹴而就,需要付出一定的代价,同时有时候还可能出现意想不到的问题,让那些热衷于传统生产方式而对精益生产持怀疑态度的人,能举出如此或那样的理由来反驳。
然而,那些坚决不移走精益之路的企业,大多数在6个月内,有的甚至还不到3个月,就能够收回全部改造成本,同时享受精益生产带来的好处。
四、传统生产向杨益生产转变示例
现某企业的生产车间接到任务,要生产一组产品,需要通过铣、钻、磨、装配和打包等六道工序,每周生产3200件。
所有这些产品的加工过程相似,需要的工人相同。
该企业每周工作5天,每天工作8小时。
生产指定产品每道工序的单位加工时刻如表2。
目前该生产单元按照工艺专业化布置。
尽管这些产品具有一定的相似性,不需要大量的生产预备时刻,然而,因为加工次序和优先级不不同,使生产专门难达到应有的熟练程度,生产拖拖沓沓,有时还需要推迟交货时刻,要么就经常需要工人加班加点才能完成生产任务,使生产成本提高,同时顾客对推迟交货的意见专门大。
现对该生产单元进行精益化改造,以完全改变目前生产拖沓、效率低下的状况。
通过大量的调查,发觉铁、钻、磨床尚有剩余生产能力,因此在不阻碍车间内其他产品生产的条件下,能够对这些设备进行适当的调整,安排到一个生产单元内。
此外,所有的装配线和包装依靠手工完成,只需要提供一些台子和某些工具就能够完成。
步骤1:
计算单件产品生产时刻(Tacttime)
(取2个工作台,尚有生产能力剩余)
铣、钻、磨:
因为这几道工序的加工时刻有长有短,为了保证按照连续流程生产,必须平衡各道工序的劳动利用程度,提高劳动生产率,因而能够在生产车间内设置一个微型加工单元,把铣、钻、磨这三道工序有机地组合起来,同时只要一个工人就能够独立完成这三项操作。
完成铣、钻、磨这三道工序所需的加工时刻为170秒。
因此,每小时能够完成21.2单位的产品,同时只需4个工作台。
计算
计算过单件产品生产时刻和完成指定生产任务所需的工作台后,便能够开始规划精益生产单元的布置。
在实际设计生产精益生产单元时,能够考虑设置两个铣、钻、磨加工区,每个加工区由两个工作台组成,每个工作台配备一名工人(见图3)。
图3是严格按照单件产品生产时刻(45秒),或者是按照每J。
时的生产能力(80单位)而设计的生产单元。
由于包装、l号装配线、铣/钻/磨等工序都存在着一定的生产剩余,制约整个生产单元的瓶颈是2号装配线。
假如要加大生产量,或季节性的需要订单增加,那么,必须把2号装配线的工作适量的分配给包装、l号装配线,或者通过寻求提高劳动生产率、降低2号装配线生产时刻的手段来解决。
假如需要减小生产单元的生产能力,那么需要裁减工人来重新平衡生产线。