双螺杆组合排列原则Word格式文档下载.docx
《双螺杆组合排列原则Word格式文档下载.docx》由会员分享,可在线阅读,更多相关《双螺杆组合排列原则Word格式文档下载.docx(11页珍藏版)》请在冰豆网上搜索。
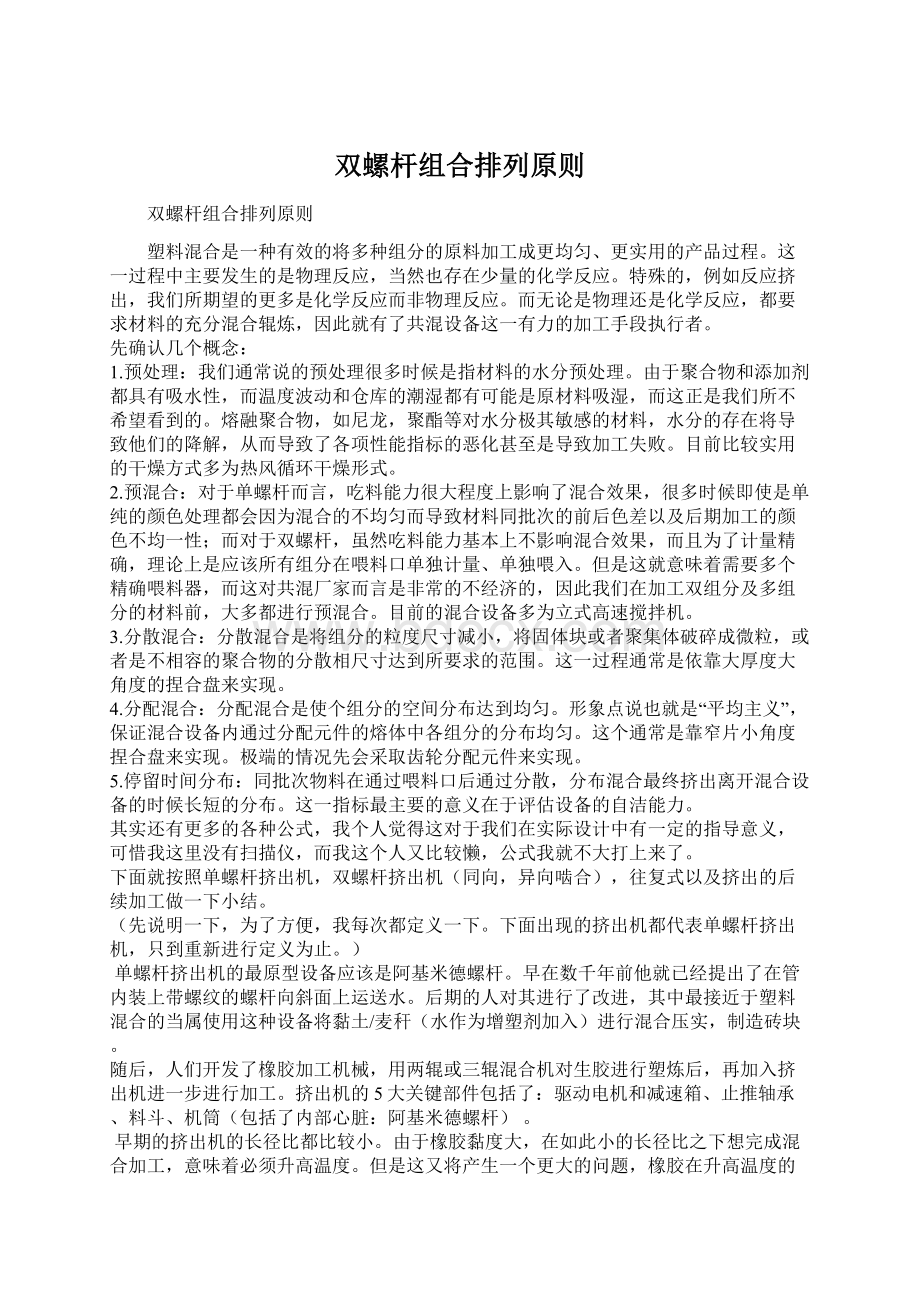
早在数千年前他就已经提出了在管内装上带螺纹的螺杆向斜面上运送水。
后期的人对其进行了改进,其中最接近于塑料混合的当属使用这种设备将黏土/麦秆(水作为增塑剂加入)进行混合压实,制造砖块。
随后,人们开发了橡胶加工机械,用两辊或三辊混合机对生胶进行塑炼后,再加入挤出机进一步进行加工。
挤出机的5大关键部件包括了:
驱动电机和减速箱、止推轴承、料斗、机筒(包括了内部心脏:
阿基米德螺杆)。
早期的挤出机的长径比都比较小。
由于橡胶黏度大,在如此小的长径比之下想完成混合加工,意味着必须升高温度。
但是这又将产生一个更大的问题,橡胶在升高温度的情况下将产生交联。
而此时人们发现增加长径比不但能够获得加工热塑性聚合物熔体所需要的高温,同时还能够改善混合性能和熔体的均匀性能。
随着长径比的进一步提高和挤出设备的进一步完善,挤出机逐渐转到了最终用户。
研磨回收和破碎以及废旧塑料回收的出现成为挤出机运用的最大市场。
挤出机的心脏,标准螺杆通常分为三段:
喂料段、转化段和计量段。
当然混合螺杆还通常具有其他的组成部分以完成加工中更为复杂的过程。
在整个加工过程中挤出机必须完成:
喂料、固体输送、压实、熔融、泵送、均化、排气(可选)到最终的挤出成型。
一般的单螺杆挤出机的长径比为:
24、28、30和32;
而双螺杆挤出机的长径比为:
36、40、42和52;
喂料段:
在挤出机中,喂料段的主要功能是吃进物料和进行固体输送;
同时喂料段对压实固体床(物料在进入螺杆后在螺槽内形成的物料段称之为固体床)以及开始塑化有很大的影响。
在进行喂料段设计时必须注意:
螺杆有效扭矩、螺杆材料、螺槽深度与宽度比(纵横比)、摩擦系数等。
同时还应当考虑原材料的尺寸、外观、本体密度和物料的性状。
另外对于添加到混合体系中的添加剂,还需要考虑喂料段是否能够有效吃进这些添加剂。
一般来说,加工结晶性混合物时,喂料段的深度和长度比加工非结晶性材料的喂料段要大。
由于挤出机的输送大部分是靠摩擦拖拽输送,因此喂料区的温度设置一般控制在120-160度之间。
如果该区温度过低,树脂就无法黏附在机筒内壁上,而仅仅是随着螺杆旋转而空转,从而导致了熔融区的缺料;
如果该区温度过高,物料会提前熔融塑化,在机筒内壁形成一个环行的熔融膜,起到润滑作用,同样也也引起缺料现象
喂料段的另一功能--压实是是固体床的压缩比足够大,保证物料充分密实,达到熔融所需要的状态。
通常情况下粒子或者是破碎的片状材料在压缩后容易在表面发生变形而与机筒内壁贴合在一起,因此也比较容易压缩;
而粉体材料由于滑动性较大,因此压缩熔融在时间上和位置上会比粒子或者片状材料滞后。
同时由于粉体材料的空隙面积大,物料密度比较小,在物料中会残留大量的空气,隔离了固体床。
这将进一步减缓熔融过程以及在增大后期的排气工作。
由于挤出机目前比较常见的是屏障形转化熔融段螺杆,比较常见的是在熔融区附加上另外一条螺纹,其螺纹宽度要比原来的窄,而且还进行了根切。
采用这种方式最直观的目的是使熔融的熔体与未熔融的固体床分离,通过避免熔融部分对未熔融的固体床的润滑作用来改善输送能力,同时也降低了熔体的热耗散、熔体过分受热分解以及保证热传递/剪切传递对固体床的热/摩擦能,提高了塑化速度。
计量段:
螺杆的计量段长短,螺槽的深浅都属于可变。
不是所有的挤出机的螺杆都是一致的。
如果仅仅是单纯的熔融挤出(例如回收破碎材料),一般采用增大计量段的螺槽深度,这种情况下产量会比较可观,但是混合效果不太理想;
如果需要好的混合效果,多采用浅槽螺杆。
这种情况下熔体温度会相应提高,混合质量也相对于深槽要好。
总的思路,计量段的长度应该保证固体床完全塑化,并能够奖励起足够的压力。
因此很多人在设计螺杆是,往往在计量段后面紧接一个混合器。
这里也许有朋友会问:
我是采用了浅槽,但是我的产品混合质量还不是非常的理想。
这里存在一个设计产量与实际产量的问题。
一个设计产量远小于你要求的实际产量的设备,即使你进行了必要的改动,但是如果你不放低你的产量要求,这很难保证你的产品质量。
通俗点,就是所谓的一分钱一分货了。
混合段:
由于共混加工中仍然有很大一部分涉及到添加剂的混合分散,因此混合段的必要性是不言而喻的。
混合段的主要工作就是在计量段之后帮助提高物料温度、颜色、黏度和添加剂的均匀程度,也有助于确定气体在熔体内发泡的位置。
这对于接下来的排气设置是非常重要的。
除此之外,混合段还将第一计量段隔离开来,建立了一个稳定的排气环境。
所有的塑料颗粒都有其固有的弹性模量,在一定的作用里范围内,粒子会在喂料段和转化段发生形变,而且即使在计量段也部分保持该形变(部分形变粒子会由于固体床破碎后形成的随便在熔体池中呈现游离状态而重新聚集成更大的粒子)。
计量段之后,物料熔融所需要的能量很大一部分是来源于热传递。
由于计量段本身的几何形状限制,在这个区域内很难提供足够的剪切应力。
上游输送过来的未熔融的部分中,一部分由于热传递的作用发生熔融,其余的大部分都被直接输送到下游的混合段。
而分散混合区域则通过剪切应力的作用,将所有进入第二喂料段(排气段之前的一小段区域)的为熔融部分完全塑化,为接下来的排气做好准备工作。
很多在生产过程中出现排气段冒料的个案,绝大部分都是因为混合塑化段未能够充分的塑化熔融而导致在排气区域排气不畅或者冒料等情况。
(也有部分是因为排气段设计不合理导致)。
如前所说,混合塑化段的熔融塑化能力绝大部分是来自于剪切。
而剪切力的产生及其大小主要依赖螺杆的转速和螺杆与机筒之间的间隔。
高的转速和小的间隔意味着更大的剪切应力。
这也就说明了为什么我们在进行增强的时候(这里假设加工的是增强材料),通常我们是在熔融完成后才加入纤维。
纤维在固体床存在的情况下,不可避免的存在着纤维与固体床、纤维与机筒之间的摩擦。
在这种情况下,纤维长度的完成性和设备的磨损就不可避免的产生了。
而在混合塑化段以后加入纤维,这时存在的是螺杆/熔体/纤维/熔体/机筒。
即使存在剪切。
纤维的长度还是能够很大程度的得以保持。
这也同时能够说明为什么我们在做增强材料的时候建议预热纤维(经过预热的纤维不容易在表面形成相对坚固的包复层)。
为了下游有效的排气,就必须是进入第二喂料段(假如存在)或者排气段的物料完全熔融。
本身从熔体中排除挥发分就比较困难,特别是当熔体中还含有未熔融的物质,这种情况下排去挥发分就更困难
一般为了改善排气,在排气段一般采用大螺距浅槽的螺纹组合。
同时为了保证螺槽充满度不至于过大而导致冒料或者排气不畅,在排气段的上游一般都采用滞留元件。
例如之前提到的混合器等。
如果物料的分子量比较高,对应着熔体黏度较高,挥发份不容易排脱,这种情况下适当增大真空压力和适当提高排气段的熔体温度。
排气口的方向一般采取垂直式,也有少量是采取水平式或者倾斜式。
考虑的普适性,大多数排气多采用垂直式。
通过排气段后,熔体进入第二计量段。
随着挥发份的排出,此段的熔体压力会随之增高,因此需要的泵送压力也随之增大。
只有在第一/第二计量段的螺槽深度比(泵送比)达到一定程度,第二计量段才能够顺利的克服排料压力顺利的把熔体向下游输送。
调节泵送比可以通过调整螺槽深浅比例或者调节设备的转速来拉开比值。
而在实际生产中通常很难在线改变螺槽深浅,这个时候通常采用局部的螺杆冷却、调整转速或者使用节流阀。
如果对输送压力有更高的要求,例如比较精细的挤出成型,则多数会用到齿轮泵来代替螺杆设计。
几种常用塑料及添加剂加工的一些问题及建议:
ABS:
ABS的喂料比较容易,而且输送方面由于它与金属具有较好的亲和力,一般比较少出现喂料及输送的问题。
但是由于ABS组成中易产生挥发份的苯乙烯组分,而且由于ABS加工中呈现的黏度都相对来说比较高,因此排气方面需要做些改进
POM:
POM存在剪切敏感性及分解物具催化分解的能力,因此加工设备的螺槽应当进可能加深,使熔融温度控制在较低范围之内,比降解的可能性降到最低可能。
由于热塑性弹性体颗粒之间存在在很大的内摩擦力及比较搞的黏度,所以很容易在加工过程中产生缺料。
这将造成生产产量的波动和材料的降解。
一般通过提高喂料段的纵横比,强制冷却和震动喂料的方式来解决。
也有一些造粒的原材料是已经经过一次或者多次加工的弹性体。
这些原材料中或多或少存在着填充油、填料,树脂等成分。
虽然内摩擦力和黏度不至于象原料那么夸张,但是由于油的存在导致了材料喂料的输送困难,一般不建议把这类材料粉碎得太过于小。
同时增加喂料段螺杆的螺棱的摩擦系数也是必要的。
聚碳酸酯:
主要加工存在着粒子,粉体和破碎。
由于PC本身的莫氏硬度很大,加工时候的噪音会很大。
相信大家都领教过那种“咯吱咯吱”的声音了,有时候真让人头皮发麻,生怕一不小心螺杆就报销了。
目前国内市场上真正舍得用原料加工的厂家我估计应该不多吧?
大部分是粉料,回料加工。
这个时候材料的预烘干,破碎和加工设备的长径比要求都比较严格。
我曾经见过一个长径比只有24的单螺杆生产PC,虽然声音有点恐怖,但是生产出来的PC粒子无论外观还是透明度还是相当的不错。
同时由于PC的黏度问题,二次料的生产经常都会在粒子中带一点气体。
这就对设备的排气提出了一个比较严格的要求了。
着色是单螺杆生产中很重要的一个组成部分。
很多时候除了回收材料外,染色也是一个维持工厂运作的模式。
染色多为色粉染色,少数要求比较高的客户也会要求是色母染色。
染色的要求有二:
一为颜色的均匀性;
一为材料性能的维持。
我们一般碰上的是颜色的均匀性,也就是我们常说的分散好不好了。
色粉混合树脂后熔融造粒需要注意的在于色粉的预分散(也就是广东人叫的搓粉)。
一个色粉在后期加工分散好不好,很大程度上依赖于在配置这个色粉的过程中分散剂和预分散。
如果一个色粉没有预分散好,那么在熔融混合的过程中,配置这个色粉的几种基础色粉会由于没有混合均匀而导致材料各个区域的颜色不一(貌似通俗的称谓叫“花色”)。
因此共混厂家如果发现你用的色粉在生产过程中发生了花色的情况,恭喜你,你可能碰上一家不太专业的色粉供应厂家。
色母是已经过预分散处理并与载体混合在一起,理论上说不存在着分散不好的情况。
但是需要注意一点的是:
同一个颜色不同的载体在加工中会有不同的表现。
色母粒的本体MFR如果跟共混树脂的MFR差别太大(无论大小),都完全有可能导致混色的出现。
同时,如果色母粒本色柔韧性太好,在混合的过程中无法尽快的粉碎成细小的色母碎屑(暂且这么叫吧),那么即使色母粒和树脂之间的MFR匹配性好,也有可能导致最终产品的颜色深浅不一(貌似我们叫这种情况叫“混色”)。
上面是对单螺杆使用的一些建议和个人看法。
由于我对颜色方面了解不多,很多说法不太准确,期待有对颜色了解更深的成员给予更正。
20世纪40年代,同向旋转完全啮合双螺杆挤出机(以下简称同向)由Erdmenger发明出来。
到了50年代由W&
P申请了专利并进一步发展了这种设备。
此后由于历史宿命的偶然性,同向得到不断的完善,逐渐成为了聚合物工业,化学制品工业以及食品工业中必不可少的加工设备。
同向加工任务的总指导方针基本建议如下:
1.确定全部任务参数(配方、生产速度、产品生产的限定条件等);
2.确定每个单元操作步骤喂料、熔融、混合、改性组分的加入、排脱挥发份、建压排料、机头定形切粒);
ZSK型挤出机或者其他任意一种同向的几何参数限定为3个:
1.啮合处的间隙
2.内外直径比(OD/ID)
3.比扭矩(功率/容积比)
根据我们的经验,两螺杆是近距离啮合的,两螺杆之间的间隙是保证机械安全的最低要求;
OD/ID比值越大,螺杆的自由容积也越大,但相对来说传递扭矩的轴心有效直径也就越小。
OD/ID比值增大,机器内作用在物料上的平均剪切速率也将降低(类似僧多粥少?
平均数越大,分得越少?
);
比扭矩的变化可以直接影响混合中的一些基本参数。
例如:
提高比扭矩,可以是机器在更高的充满度下工作,这样为达到同样的产品,完全可以在更低的主机转速下运转。
但是在这样的情况下,就很有可能出现排料温度过低。
因此目前设备中最大的比扭矩为11.3(W&
P系列第6代)。
对于使用过同向的技术人员来说,同向的加工重点:
螺杆基本上都是由组合式部件组成(轴心,螺纹块,啮合块等)。
根据不同的加工需要对应做不同的混合组合。
而一般加工段的长度也是取决于单元操作的数量和消耗功率的大小。
混合低黏度甚至超低黏度的物料时,长径比(L/D)可达到60:
1。
而加工一些一般物料时,L/D在24到48之间。
一般的设备L/D比都在32-40之间。
机筒为什么采用矩形截面而不采用单螺杆的原形截面。
这个问题我最初接触同向的时候也有提过。
但是带我的师傅只说了一点:
"
为了保证温度的均匀性和差异最小性。
当时一直不理解。
直到有一天拆组合看到内部截面才真正明白过来。
的缺矩形截面的温度梯度差别远远比圆形的要小。
(如果对这个还有怀疑,可以私下找我,我把截面的温度梯度分布图发给你)。
这里说说螺杆组合件。
有了螺杆和机筒的配合才能完成工艺操作单元的特定任务。
一旦同向的中心距,螺纹数量以及OD/ID比值确定后,除了极少个别的特殊元件,无论是螺纹套还是啮合块,横截面都是固定的。
螺杆螺纹套:
标准螺杆螺纹套的螺距大约在0.5D到2.0D之间。
宽螺距元件一般用于挤出机的喂料段和排气段,窄螺距元件主要用在物料需要压缩或者填充大量填料的部位上游。
如啮合块或者密封环的上游或者操作段之间(如喂料和真空之间)。
螺纹套的螺距可以增大。
随着螺距增大,将使停留时间和填充程度减小,停留时间变窄,拖拽流增大,同时对压力的增加更加敏感(压力增大导致漏流或者逆流的可能性增加。
)。
但是在正常的压力情况下(或者在上游输送压力和下游阻碍压力平衡的情况下),宽螺距的螺纹的输送能力还是要比窄螺距的螺纹输送能力大。
除了用于输送螺杆螺纹套之外,还设计了用于特殊情况的几种输送元件。
例如应付喂料困难和输送低密度物料的SK螺纹套;
用于阻止漏流的SF元件。
目前还有一种窄螺纹元件,用于反应型加工过程中输送黏度近似于水的物料。
上面是同向的螺纹部分,下面是啮合块部分。
螺杆上的螺纹套都是由连续的螺纹组成的。
而啮合块则是有侧面象圆盘的元件一个一个叠和而成的。
其几何外型是非连续的。
捏合块的特征参数包括了总长度、啮合盘数量、啮合盘错列角。
我们通常用KB表示啮合盘,而且在KB后面加上特定的数值表示啮合盘的实际形态。
例如:
KB45/5/40表示啮合盘交错角为45度,共有5片啮合盘,啮合块长度为40mm。
啮合块最主要的工作任务就是分散混合和分配混合。
(分散和分配的概念可以参照前面单螺杆中的解释)。
而同样长度不同错列角度,同样错列角度同样长度不同啮合片厚度等条件对应着啮合元件的不同分散、分配能力。
我们可以按组一个一个对比:
1.同样长度不同错列角的分散能力是:
60>
45>
30>
90(这里的数值表示错列角。
)
分布能力是:
90
2.同样错列角同样长度不同啮合片厚度的:
分散能力是:
厚片大于薄片
薄片大于厚片
当然,并不是所有啮合块都符合上述的说法的。
但是可以根据上述的对比方法进行类比。
(不排除有错误的啊。
我又不是老耿。
况且老耿也不一定就全对。
实践,实践最重要!
至于此外的几个特殊的元件:
例如左旋螺纹,左旋啮合盘等.....这些都会在接下来的分散分配混合优化中提到。
除了影响分散和分布能力外,不同宽度的啮合盘对物料输送的能力也有差异。
当压力存在的情况下,宽啮合盘的输送能力衰减得比窄啮合盘快。
但是在稳定压力流体场合中,宽啮合盘的输送能力比窄啮合盘的输送能力要强。
这种情况与螺纹中拖拽流的情况很相似。
其外,影响轴向有效流量的因素除了啮合盘厚度外,还跟啮合盘的错列角有很大的关系。
错列角与轴向流量的关系大概为:
90(由前至后表示输送能力的降低)。
这里特别提到90度啮合盘的例子。
因为90度基本上在压力稳定的条件下是正负输送平衡的一个元件。
这是一个很有用的特性。
在需要大混合的场合下,保持压力的稳定(当然这是不可能的,生产中不可能有稳定的压力场,总是从下料往机头输送)或者保持压力差尽可能下。
90度的正负平衡就能够提供充分的混合时间了。
一直以来啮合盘都是双突棱外观而且延续了相当长的一段时间。
1989年W&
P公司开发了特殊的3突棱啮合块并申请了专利(感觉洋鬼子这点比咱们更具有知识产权意识啊。
应当向他们学习)。
这种设计最大的优点在于改善双突棱系统中作用于物料的力的均匀性,利用该专利能够获得更均匀更一致的剪切速率且不影响自洁性。
(这里我的个人理解是:
比扭矩是定死的。
由两个突棱来分配,这样的剪切平均程度也许不如三个突棱分配的平均吧?
或许四突棱,五突棱的分配效果更均匀更好?
只是限于加工的方便性和加工精度的限制,才没有更进一步发展成多突棱?
)这个结果的几何特点和作用基本如下:
1.为了保证小间隙的自洁特性,3突棱啮合块中的每一个啮合盘相对于轴心都是偏心设计的。
因此很容易理解,三突棱中的一个或者两个突棱与机筒的距离比标准元件要大(实际上三突棱中的两个突棱与机筒的距离是标准的3-5倍)
2.采用偏心结构设计,而比扭矩是固定值,平均剪切速率必然是与双突棱相同的。
但是由于任何一个捏合盘中的两个突棱与机筒的距离增大了,所以同样口径的三突棱的OD/ID值要比双突棱的小(这点有点空间想象能力应该很好理解),所以三突棱的做高与最低剪切速率的差异自然比双突棱的小(剪切速率的最大值出现在突棱处。
而最小值出现在突棱根部。
)因此三突棱更适合用于加工热敏性材料(剪切速率差别越小,等同于材料收到剪切过热分解的风险也越小。
此外,由于三突棱中的两个突棱间隙比正常的要大,因此可填充物料的空间比双突棱也就多。
因此突棱与突棱之间的压力梯度也就得到有效的降低。
此外,三突棱由于具有三种啮合作用(突棱/突棱,突棱/突棱顶,突棱/突棱底){注意:
这里的突棱顶与突棱底是指相对与轴心的距离大小而言。
因为没有更明确的解释,我只好临时做两个词来凑数}
3.三突棱啮合盘中有两个突棱的顶端间隙增大了,而且三突棱的啮合盘的突棱宽度比双突棱的窄,因此在同样的转速下能够是更多的物料通过高剪切区。
在啮合盘长度相等的情况下,三突棱的分配作用不如双突棱(这点我刚开始也很不理解。
三个突棱怎么说分割效果也要比两个好啊。
后来想想,实际上三突棱只有一个突棱能起到切割的作用,另外两个与机筒的距离忒远了点)。
三突棱混合中为了提高充满度,一般采用低转速而不采用左旋螺纹。
而低转速在一定程度上也降低了剪切过度导致降解的可能。
。
这也算是三突棱的一个比较大的优点。
特殊元件:
窄突棱啮合盘不适合分配混合,因此W&
P公司又设计了TME(涡轮混合元件)或ZME(Zahnmisch元件)等齿型混合元件,以进行全机筒的自洁。
这些元件用齿数和齿向的角度的表征。
TME(怕怕,一不小心就打成TMD了。
)有利于物料的分流以及界面的生成,ZME有利于增大物料的输送能力。
两种元件的主要作用都是以最小的能量,达到最大的分配效果(这个时候基本上已经没有分散效果了。
这个世界没这么完美的马,跑得快还不吃草。
自洁型ZME在原来垂直于轴心的基础上改变成倾斜一定角度,这样元件的自洁性能比未改善前大大提高。
节流阀
节流阀被设计出来的最主要目的是:
改善加工变量,控制能量输入,优化混合质量。
目前主要的节流阀主要分为:
1、线性节流阀(压力随着啮合程度的增加而线性增加)2、非线性节流阀(压力随着啮合程度的增加呈指数形式增加)
前面对各个部分的功能进行了初步的介绍。
实际上这些都不是重要的,重要的是把这些部件个功能集中一起共同作用,这才能完成我们希望的操作(共混加工)。
(本来这里有几个组合的。
全是图片!
郁闷。
)无论混合段是捏合块组成还是有齿状混合元件(TME)组成,束缚元件的存在都会大大的提高物料的停留时间和填充程度。
有时(其实不能说有时,应该说是大部分时候),特定的单元混合操作采用分段控[由输送螺纹把捏合段分成两段或者更多]。
这样做的好处在于:
能够将上一捏合段因剪切而变稀或者因为剪切导致温度过高引发的物料黏度下降的情况恢复过来,保证物料在下一混合段内有足够的高弹性进行更有效率的混合。
这样能够大大提高混合效率,降低能耗。
同向的喂料是饥饿式设计,产量与螺杆的转速无关。
因此,我们对混合机的停留时间、填充程度和能够能够进行严格控制。
当然,最理想的操作条件是当喂料达到最大的时候,这个时候挤出机的生产能力得到了充分的发挥。
ZSK型混合机的加料口并不限定于第一个加料口(其实不光是ZSK,目前很多同向的加料口都不仅仅只是在第一个加料口啦。
中国人的双螺杆也有2个,3个下料口的啦。
),可以根据原料和配方的不同,在整个加工段设置多个加料口,原料可以是固态的,也可以是液态的,下面就根据共混加工的一个完整流程分别介绍各个单元的操作。
喂料单元:
在混料工艺中,第一段机筒加入的物料通常都是固态聚合物。
典型的形状有颗粒状,片状和粉状。
但在某些时候也可以先加入高黏度的液体物料(这个我发誓,我从来没做过这样的事情。
打死我也不敢在没加任何固态物料的情况下往机器里加液体。
所以大家没有十足把握,千万别做这种事情!
)大多数的颗粒和片状物喂料都相当容易。
这是因为颗粒和片状物料的本体密度都相对比较大,而且尺寸在一维、二维或者三维上远远小于挤出机的螺槽深度[注意前面说的一维、二维或者三维尺寸上远远小于挤出机的螺槽深度。
因为如果不这样。
即使本体密