网目实验法分析拉深件侧壁厚度变化规律Word格式.docx
《网目实验法分析拉深件侧壁厚度变化规律Word格式.docx》由会员分享,可在线阅读,更多相关《网目实验法分析拉深件侧壁厚度变化规律Word格式.docx(7页珍藏版)》请在冰豆网上搜索。
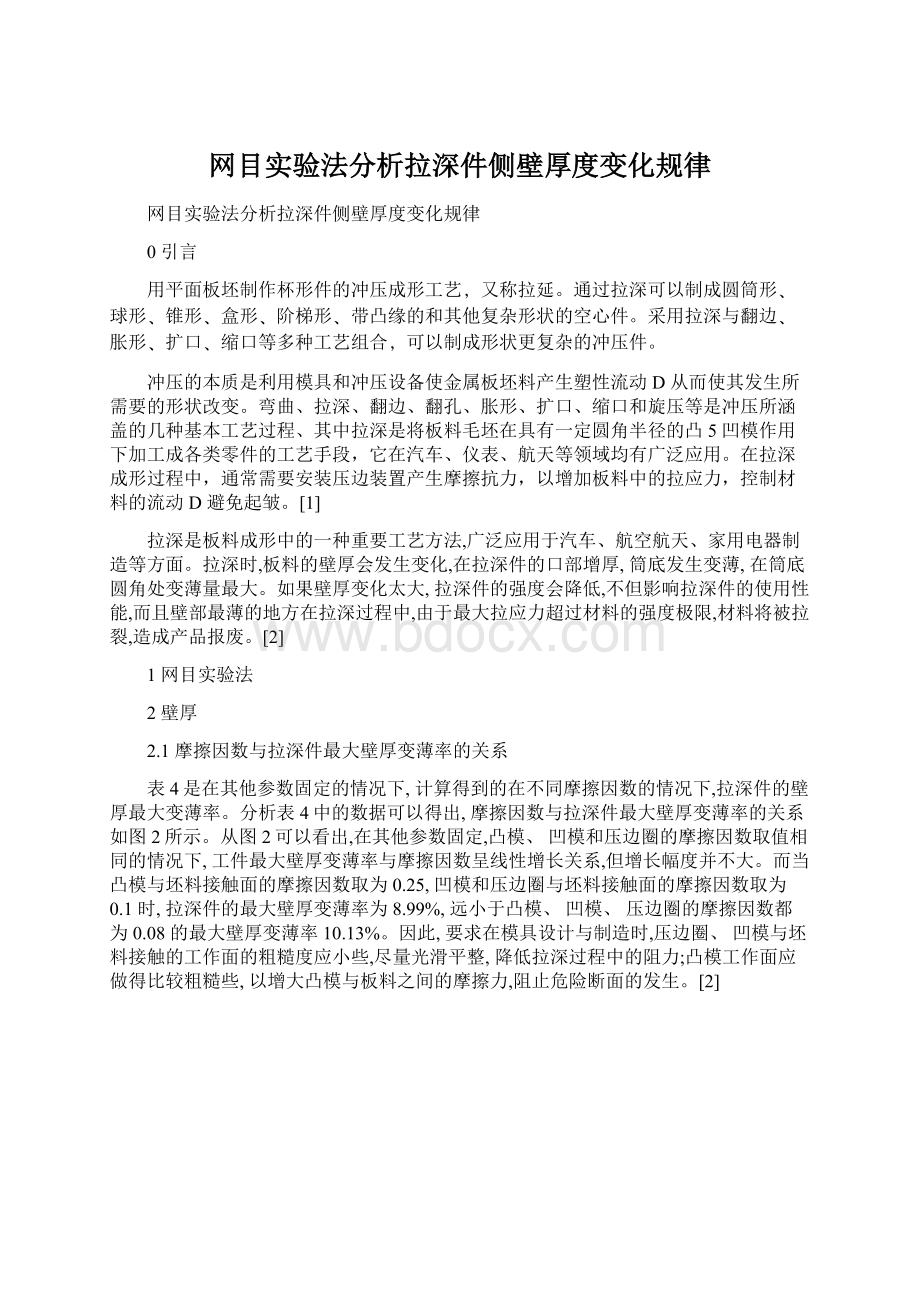
如果壁厚变化太大,拉深件的强度会降低,不但影响拉深件的使用性能,而且壁部最薄的地方在拉深过程中,由于最大拉应力超过材料的强度极限,材料将被拉裂,造成产品报废。
[2]
1网目实验法
2壁厚
2.1摩擦因数与拉深件最大壁厚变薄率的关系
表4是在其他参数固定的情况下,计算得到的在不同摩擦因数的情况下,拉深件的壁厚最大变薄率。
分析表4中的数据可以得出,摩擦因数与拉深件最大壁厚变薄率的关系如图2所示。
从图2可以看出,在其他参数固定,凸模、凹模和压边圈的摩擦因数取值相同的情况下,工件最大壁厚变薄率与摩擦因数呈线性增长关系,但增长幅度并不大。
而当凸模与坯料接触面的摩擦因数取为0.25,凹模和压边圈与坯料接触面的摩擦因数取为0.1时,拉深件的最大壁厚变薄率为8.99%,远小于凸模、凹模、压边圈的摩擦因数都为0.08的最大壁厚变薄率10.13%。
因此,要求在模具设计与制造时,压边圈、凹模与坯料接触的工作面的粗糙度应小些,尽量光滑平整,降低拉深过程中的阻力;
凸模工作面应做得比较粗糙些,以增大凸模与板料之间的摩擦力,阻止危险断面的发生。
2.2最大变薄处在与凸模圆角成45度线附近
从实验所测数据可知,最大变薄处在与凸模圆角成6#∃线的附近。
三次拉深所得最大变薄量分别为:
-11.1%、-21.7%、-28.0%。
即随拉深变形程度的增加,最大变薄量是增加的。
最大变薄量与该次总变形程度的关系见曲线图4所示。
首次拉深时最大变薄点在第二次拉深时,由坯料凸模圆角45度线上转移到筒壁上。
该点在第二次拉深过程中是先变厚,再变薄,而最终变形结果是变厚了。
首次拉深时的最薄点,即图3a上的A''点在第二次拉深时转移到图3b上的A点,在第三次拉深时转移到图3c上的A'点。
转移后的位置可近似的按该点所围板料中间层面积不变的假设进行计算.
经计算,A'点(图3b)处于圆角向直壁部分过渡处,其横坐标x=11.849mm。
图3a中的最大变薄点A转移到图3b中的A'点,A'点实测厚度为1.831,变薄量为-8.5%。
即该点由坯料的变薄量-11.1%增厚到-8.5%。
[3]
2.3压环速度对壁厚的影响
压环速度与工件外壁最小厚度关系如同12所示。
工件最小厚度在凸模圆角与顶面相切出(如图13),说明压环使最小厚度位置发生了转移,表明压环能有效促进材料由外壁向内壁流动。
随着压环速度的增加,单位时间金属流入内壁的体积增多,因此,最小厚度也单调增加,但增加也有一定极限。
因为随着压环速度的增加,为了防止起皱现象,所需要的压边力需相应增加,这也增大了材料流动的阻力,不利于最小厚度的增加。
当过于增大压环速度,流动阻力大于材料抗拉强度时,便会发生拉裂现象。
[4]
2.4相对厚度对锥形零件拉深成形的影响
锥形壳体件又称锥形件,是一种广泛使用的零件,通常采用板材拉深成形工艺进行生产。
板材相对厚度、相对锥项直径、相对高度以及板材的物理性能是影响拉深成形工艺、模具结构以及锥形件破坏方式的因素。
生产实际表明,上述各因素中,板材相对厚度的大小是最为关键的因素。
相对厚度大的锥形件,拉深成形中,凸缘处、侧壁处产生压缩失稳破坏的可能性小。
弯曲变形应力高,小端圆角处破裂是制约拉深成形工艺成败的因素。
提高一次拉深变形量的措施是降低小端的弯曲应力,就模具结构而言,要增大凸凹模圆角半径,可不设压边装置,这类锥形件通常称为厚壁锥形件。
而相对厚度小的锥形件,拉深成形中,既有可能在小端部产生拉裂平破坏,又有可能在凸缘上压缩失稳破坏,还有可能在侧壁上产生压缩失稳破坏,通常称其为薄壁锥形件。
由于侧壁处于悬空状态,侧壁处的压缩失稳不像薄壁筒形件拉深凸缘处的压缩失稳,可通过在模具上添加压边圈来防止,一旦侧壁上产生压缩失稳,就意味着所制定的拉深工艺的失败和所设计、制造的模具作废。
[5][6]
3拉深
3.1杯拉深
圆杯拉深时凸缘变形区径向受拉,切向受压,当切向力超过临界失稳承载力,凸缘将沿切向隆起数个波纹。
波纹通过模具间隙时,可能因波阻太大引起筒壁断裂,也可能在筒壁上留下不可消除之波纹导致工件报废。
起皱问题可以通过在拉深模上安装压边圈并施以适当压边力来解决。
但压边力要合适,过小不足以抑皱,过大则可能拉断筒壁。
可见皱曲与防皱是拉深工艺和拉深模具设计中主要和必须考虑的问题。
能量方法已成为求解塑性皱曲问题的主流方法。
但以往有关研究引用的基本公式,或是料力学中的弯曲变形能量方程,或是板壳理论中的小弹性弯曲变形能量方程。
虽然在简化程度上有所区别,但关键简化有其共同点。
这种简化在塑性皱曲强度分析中引起的误差相当大,导致临界趋曲曲线远离生产中的经验数据。
[7][8]
3.2薄壁锥形件拉深
薄壁锥形件的拉深成形过程如图1所示,凸模下压与板坯接触后,板坯首先发生胀形变形,随后凸模的作用转化为毛坯侧壁的经向拉应力;
图1中C是拉深开始时凹模口M处的材料在拉深变形中的位置,PC是拉深开始时悬空部分材料在经向拉应力的作用下逐渐向凸模侧壁靠近中的位置,完成悬空部分材料的成形;
CB是从凹模口拉入的材料,在经向拉应力的作用下逐渐向凸模侧壁靠近中的位置,完成凸缘处材料的成形。
[9]
3.3变薄拉深
数值模拟在金属塑性加工领域中被广泛应用,可以预测坯料在成形过程中的应力应变分布、厚度的变化以及起皱破裂等成形缺陷,给设计者的工艺分析和模具设计提供可靠的科学依据,从而大大提高了模具的设计质量、缩短了模具设计周期;
可以利用逆算法确定零件毛坯形状和展开尺寸、计算零件回弹量、确定压边力大小、优化工艺方案和参数,降低了产品的生产成本,提高了产品的生产质量。
由于中厚板冲压成形过程中在凹模圆角处有明显的弯曲效应,不满足薄壳假设的基本要求,因此需要采用体单元或者体壳单元来解决这一问题。
对于变薄拉深成形问题,为了获取更加精确的板内部应力应变信息、坯料上下表面与模具间更加精确的接触信息,需要采用实体单元或者实体壳单元。
但是利用体单元模拟成形问题的计算时间较长,在板料成形领域一直没有得到广泛的应用。
近十年来,不少学者对体单元进行了研究,开发了具有实用价值的单点积分和多点积分的实体单元模型。
[10][11]
3.4干膜润滑拉深
干膜润滑拉深使钢板(包括不锈钢板)和铝、铜板材料的拉深成形性能都有不同程度的提高这时润滑液被挤到“凹陷”处去了,成为边界摩擦或边界润滑。
而始终有润滑剂分开的两金属表面的摩擦叫做流体摩擦或流体润滑。
显然,机油润滑时,边界摩擦成分大,而垫干膜润滑时流体摩擦成分大,随着膜的延伸率大,强度高,变形时能近乎流体摩擦,摩擦阻力小,粘结现象也较难产生,模具寿命可以提高。
故采用干膜润滑拉深,其拉深性能得以改善。
采用干膜润滑拉深法,拉深件的表面摩擦与划伤要比机油润滑时大为减轻,模具寿命提高,虽需要逐件放薄膜,稍稍增加了工作量,但它与这种方法提高经济效益相比,影响甚微。
这种方法及随之而进行的实验和分析总结的另一个意义是:
为冶金部门生产出较高拉深性能并防锈的板材——涂复塑料薄膜的板材提供了一种方向和依据。
[12]
3.5板料拉深
板料成形是材料加工技术中的重要分支之一,拉深是板料冲压成形中的主要成形方式,在汽车、航空航天、家用电器、石油化工等诸多领域均有广泛的应用。
摩擦力是拉深件成形中重要的外力之一,拉深过程中常出现的质量缺陷如起皱、开裂、细颈、表面划痕、擦伤等,都与摩擦特性掌握不好有关。
因此,在实际生产中要考虑模具与板料之间的相互作用问题,避免因为摩擦不良等问题造成的加工件不合格和模具的过早报废。
模拟软件可以在板金和冲压模具行业产生巨大的作用,采用有限元技术来研究分析拉深过程越来越广泛。
本文推导拉伸件成型中使用的润滑模型,并通过大型非线性有限元软件ETA/Dynaform分析典型S型汽车拉伸件成型过程中的润滑特性。
在稳定变形阶段,板料在法兰的外缘部分变薄量较小,所以油膜是稳定减小的,在压边力合适不产生褶皱的情况下,可以维持较好的润滑状态,不会影响产品的表面质量;
法兰中间部分变薄加大,保证充分供油的情况下,将有较好的厚度维持润滑;
在圆角部分,板料变薄剧烈,将有大量新生的金属表面出现,如不能保证充分供油,将影响润滑状态,进而破坏产品表面质量。
[13]
参考文献
[1]王东哲,娄臻亮,张永清,何丹农.板材变压边力拉深成形方盒件数值模拟,2001.10
[2]喻祖建.数值模拟分析工艺参数与拉深件壁厚变化的关系.2005.11
[3]赵振铎,刘清津.筒形件多次拉深壁厚尺寸变化规律研究.1997.1
[4]王新云,欧阳坤,夏巨谌,胡国安.冲锻成形过程拉深增厚工艺的有限元分析.2008.12
[5]任运来,吕亚臣,彭加耕,朱磊.相对厚度对锥形零件拉深成形的影响.2010.4
[5]H.D.Azodi,H.MoslemiNaeini,M.H.Parsa,G.H.Liaghat.Analysisofruptureinstabilityinthehydromechanicaldeepdrawingofcylindricalcups.2007
[7]龚志钰,李章政.材料力学.北京&
科学出版社.1999
[8]熊志卿,杨征宇.杯拉深凸缘皱曲预测与控制.2001.7
[9]任运来,聂绍珉,李硕本.薄壁锥形件拉深成形条件研究.2004.12
[10]苗量,陈文琳,李桂兰.基于有限元逆向法和正向法的板料成形过程中合理毛坯形状的确定.2006.2
[11]许江平,柳玉起,章志兵,杜亭.变薄拉深过程模拟的有限元动力显式算法.2008.10
[12]昊裕农,柯美元,杨亘.提高拉深模具使用寿命和零件合格率的一种有效方法.2006.6
[13]王成,曲庆文,尹明虎,赵海星.板料拉深成型中的润滑特性分析.2010.5