冷镦钢SAE1008钛成分控制docWord下载.docx
《冷镦钢SAE1008钛成分控制docWord下载.docx》由会员分享,可在线阅读,更多相关《冷镦钢SAE1008钛成分控制docWord下载.docx(11页珍藏版)》请在冰豆网上搜索。
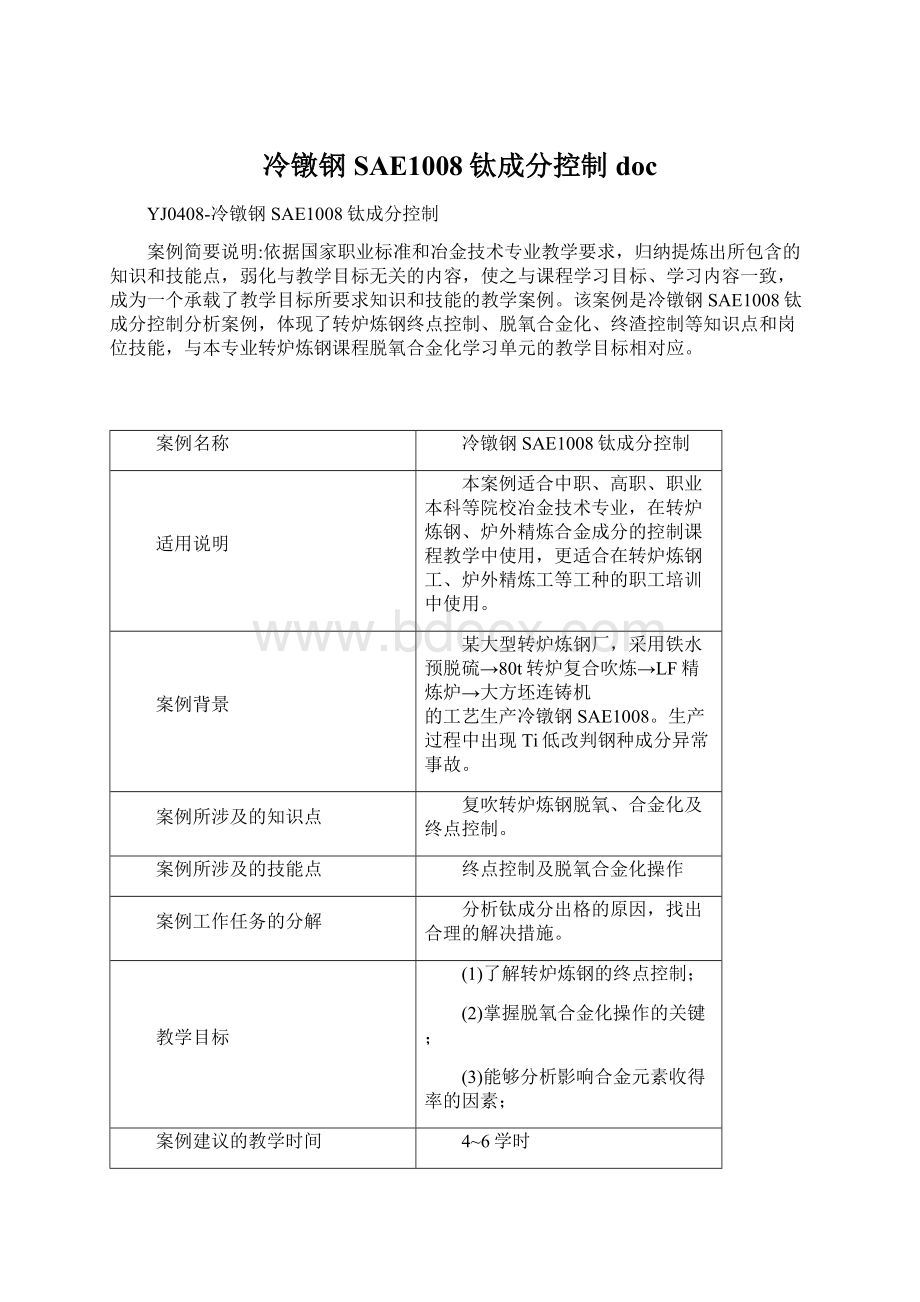
用冷镦钢系列产品生产的零部件、紧固件可满足从五金机具、家用电器、汽车、摩托车乃至航空航天机械的制造要求。
企业生产本钢种所用设备和工艺包括:
采用喷吹颗粒镁法铁水预脱硫,拥有三座混铁炉、三座转炉,容量50吨,一座80吨转炉;
采用炉后吹氩工艺、LF炉、RH炉精炼设备,小/大方坯连铸机。
本案例结合该厂生产冷镦钢SAE1008过程中钛成分控制进行工艺分析。
二、主要内容
(一)冷镦钢中钛元素的作用和要求
1、钛元素的作用
钛铁在炼钢过程中作为合金元素加入到钢水中,起到细化组织晶粒、固定间隙元素(C、N),提高钢材的强度,增加钢材的耐腐蚀性作用,而且还能够提高钢材的综合力学性能及良好的焊接性能等。
但是钢中钛含量与碳氮化钛夹杂有一定的关系,随着钛含量的降低,钢中的碳氮化钛夹杂相应减少。
氮化钛是一种硬而脆的夹杂物,它对钢的疲劳寿命特别有害。
在相同尺寸下,氮化钛比氧化物更有害。
研究表明,钛含量超过(30~50)×
10-6后钢的疲劳寿命就明显降低。
为提高冷镦钢质量,应减少其形成氮化钛夹杂物的可能性。
2、钛元素控制的要求
(1)控制炉渣氧元素的含量,前期使用脱氧剂进行脱氧,再加入钛铁合金,减少炉渣中钛氧化物的含量;
(2)控制钢水吸氮,减少氮化钛夹杂。
(二)案例分析
2015年2月27日到3月1日夜班,在5#LF炉连续生产了三个浇次SAE1008(加Ti)钢种,第三个浇次出现了一炉次Ti低改判钢种成分异常事故。
231502134炉次是5#LF炉处理,使用G053#钢包,包龄43次,上7#连铸机,为浇次第13炉。
231502134炉次在5#LF炉处理26min,加热4次,加热16分钟,软吹5分钟,具体处理过程如下:
表1具体处理过程记录表
时间
现场实绩
底吹气量NL/min
加热时间min/样品成分%
0:
48
钢包到站取样1
49
出样1
90
样1:
C-0.0569Si-0.0545Mn-0.3233Ti-0.00185
0:
59
钢包进站,定氧43.68ppm,温度1524℃,陆续加入硅铝铁24Kg,电石30Kg,高碳锰12Kg,硅铁44Kg;
开始加热,过程分批加入石灰共106Kg
90-260
加热10分钟
1:
09
加热结束,加入中铁铁120Kg
219
加热5分钟
14
结束加热,取样2,定氧1.7ppm,温度1560℃
240
15
继续加热
19
出样2
样2:
C-0.0702Si-0.1438Mn-0.3651Ti-0.07862
20
结束加热,测温1588℃
21
开始加热
加热2分钟
25
喂钙线130m,开出钢包车,开始软吹
81
26
钢包车开出
取样3,测温1601℃,开出准备起吊
31
软吹结束,钢包离站
34
出样3
样3:
C-0.0757Si-0.1466Mn-0.3683Ti-0.05130
2:
22
出成品
中包成品:
C-0.08Si-0.14Mn-0.37Ti-0.044
出副样
中包副样成品:
C-0.07Si-0.14Mn-0.37Ti-0.043
3:
32
割样
割样:
C-0.08Si-0.14Mn-0.36Ti-0.041
查MES记录,本炉次处理过程底吹气量见下表:
表2本炉次处理过程底吹气量记录表
处理号
炉号
吹氩流量NL/min
记录时刻
51501859
231502134
90.51663971
2015-3-10:
52
90.3237381
57
90.70954132
2015-3-11:
02
260.0726013
07
260.4101868
12
219.9501953
17
240.7346954
81.25760651
27
(三)案例原因分析
从整个处理过程的温度、成分及底吹气量方面分析来看,存在以下几个原因:
(1)炉长对于新钢种(未完全脱氧情况下控制Ti)的生产经验不足;
(2)进站定氧温度低,未引起重视;
(3)生产节奏紧张情况下,加入钛铁时间相对于操作规范的加入时间偏早;
结合以上几个原因得出:
本炉次按照操作规范加入钛铁,但是没有考虑加入钛铁时的钢水温度,使得加入钛铁后长时间升温,导致钛损严重,是成分异常的主要原因。
(四)预防措施
1、车间完善该钢种操作规范,把钛铁加入时间相应后延,保证钢水温度,控制钛损;
2、转炉使用铝块进行完全脱氧,精炼炉使用铝粒进行脱氧操作。
(五)措施实施情况
231502475炉次是5#LF炉处理,使用G036#钢包,包龄61次,上7#连铸机,为浇次第10炉。
231502475炉次在5#LF炉处理28min,加热4次,加热14分钟,软吹7分钟,对比情况如下:
表3事故炉次与成功炉次成分控制对比
C%
Si%
Mn%
P%
S%
Ti%
协议
≤0.10
≤0.30
0.30-0.50
≤0.03
≤0.04
0.05-0.07
内控
0.06-0.08
0.30-0.40
≤0.025
≤0.035
0.055-0.065
事故炉次
0.08
0.14
0.36
0.018
0.011
0.041
成功炉次
0.07
0.15
0.34
0.006
0.054
两炉次重点参数对比:
表4事故炉次与成功炉次重点参数对比
重点参数
231502475炉次
231502134炉次
钛铁加入量
90Kg
120Kg
加如钛铁前钛含量
0.00799%
0.00185%
钛铁加入时温度
1594℃
1560℃
加入钛铁后钛含量
0.05952%
0.07862%
钛铁加入后加热时间
4.9min
12min
钛铁加入至喂丝间隔时间
9min
16min
软吹时间
7min
5min
成品钛含量
0.054%
0.044%
钛损
0.00552%
0.03462%
(六)措施总结
1、保证温度的前提下,减少钛铁加入后的加热时间,可以有效地降低钛损;
2、钛铁加入时间适当后延,其吸收率明显增高;
3、使用脱氧剂铝粒相比较硅铝铁的脱氧效果要好;
(七)工艺路线
1、生产工艺路线:
铁水预脱硫→80t转炉复合吹炼→LF精炼炉→大方坯连铸机。
2、铁水经过脱硫后进入混铁炉,生产前化验分析,铁水条件满足如下条件才具备生产:
硫含量不大于0.04%;
磷含量不大于0.120%;
3、转炉总装入量控制在52±
2t。
废钢比控制在35%以下。
转炉终点控制如下:
表5转炉终点成分控制
钢种
C
P
S
SAE1008-Ti
≤0.06%
≤0.025%
≤0.035%
4、根据吹氩站温度要求及出钢温降等确定出钢温度,参考温度不低于1600℃。
5、出钢前必须进行定氧操作,根据终点氧含量加入相应数量铝块。
6、转炉出钢脱氧合金化控制要求:
6.1当钢包内钢水量约12t时,从转炉炉后加入全部铝块(可根据终点情况等调整)。
6.2当钢包内钢水量约18t时,依次加入下列合金和顶渣:
200Kg中碳锰铁→顶渣。
7、满足LF炉进站成分控制要求;
8、LF炉使用铝粒和碳化钙对炉渣脱氧,待下次加热停止后蘸样观察渣子颜色,根据颜色判断是否继续加入脱氧剂;
9、白渣形成后,加入中钛铁或高钛铁,可根据钢水成分调整加入量;
10、LF进行加热升温,满足连铸机浇注所需要的温度;
11、LF炉调整钢水成分,满足钢种标准/内控要求;
12、连铸机使用优质塞棒和水口,提高钢水质量;
13、连铸机严格保护浇注,防止钢水二次氧化、增氮和浇注絮流事故;
14、连铸机使用专用保护渣和中间包钢水覆盖剂;
15、铸坯进行缓冷或全封闭保温车热送。
三、分析路径
该案例是质量事故案例,本事故案例体现了转炉炼钢终点控制、脱氧合金化、终渣控制等知识点和岗位技能,与冶金技术专业《转炉炼钢》课程脱氧合金化学习单元的教学目标相对应。
根据国家职业标准关于合金工的要求,对应教学目标,从此生产案例归纳提炼出所包含的知识和技能点,弱化与教学目标无关的内容,使之与课程学习目标、学习内容一致,成为一个承载了教学目标所要求知识和技能的教学案例。
采用分析生产现场操作记录表的手段,引导学生通过自学、讨论、对比、讲授等方式学习脱氧合金化相关知识,掌握脱氧合金化操作技能,达到教学目标要求。
四、教学目标
(1)了解高质量钢种冶炼应关注的问题;
(2)掌握冷镦钢冶炼操作要点;
(3)学习综合考虑钢种质量保证的措施,根据设备、原材料,选择工艺路线。
(4)全面复习所学知识,并将知识转化为能力。
五、教学方式方法
现场调研、问题讨论、点评、案例分析、讲授、课堂练习、大作业。
具体教学过程设计如下:
(一)课前计划
(1)学生掌握知识:
铁水预处理、转炉炼钢、LF精炼、连续铸钢生产的基本原理、工艺、设备;
(2)学生分组,指定组长;
(3)与现场联系,进行现场教学准备,包括安全教育、劳保用品、行走路线,现场兼职教师,现场教室等;
(4)安全教育,教师带领学生下厂调研,记录10炉冷镦钢冶炼工艺参数,收集钢种生产相关资料;
(5)学生根据所学知识和实习、调研中获得的资料,总结该钢种生产的操作要点;
(6)与技术人员交流,请技术人员讲授该钢种生产中出现的事故。
(7)教室设置成学习岛,准备投影,为每组准备2张0开白纸,大号记号笔1支、作业纸每人2张。
(二)课中计划
(1)学生按小组就座学习岛周围,选举记录人、发言人。
(2)采用头脑风暴法,每人总结一条操作要点,按顺时针顺序轮流发言,记录人将操作要点在0开白纸上按铁水预处理、转炉炼钢、炉外精炼、连续铸钢分工序记录。
要求每人发言,可以轮空,直到所有人员无法补充为止,时间15~20分钟;
(3)整理完成后,小组发言人上台展示0开白纸上的记录,并向全体师生汇报交流该钢种操作要点;
发言学生汇报完成后,同组学生可以补充。
汇报完成,本组自评,其它组进行点评打分,现场技术人员参与对学生汇报的操作要点评价,指出优点和不足,每组时间8~10分钟;
(4)技术人员讲授实际生产该类钢种事故案例,时间20分钟;
(5)教师讲授帘线钢的用途、性能要求、成分控制要求,生产操作要点,时间45分钟。
(三)课后计划
布置作业,见六(三)。
六、思考题及考评
(一)课前思考题
布置课前思考题,保证学生下厂调研知道找什么材料、看什么操作、思考为什么如此操作。
(1)对冷镦钢成分、质量有哪些要求?
(2)生产冷镦钢各岗位有哪些关键的操作要点?
(3)冶炼过程中影响合金元素收得率的因素有哪些?
(二)课堂练习
课堂提问或者集体回答,目的:
及时复习、巩固知识,检查教学效果。
练习题
1、向钢中加入一种或几种合金元素,使其达到成品钢成份要求的操作称为(
)。
答案:
合金化
2、金属在冷加工变形中,金属的变形抗力指标,随着变形程度的增加而(
升高
3、LF钢包精炼炉的主要冶金效果(
升温;
脱硫;
成分微调;
降低钢中气体及夹杂物含量
4、钛铁在炼钢过程中作为合金元素加入到钢水中,起到细化组织晶粒、固定间隙元素(C、N),提高钢材的强度,增加钢材的耐腐蚀性作用,而且还能够提高钢材的综合力学性能及良好的焊接性能等。
()√
5、冷镦钢,又称铆螺钢或冷顶锻钢,是利用金属的塑性,采用冷镦加工成型工艺生产互换性较高的标准件用钢。
6、出钢过程中在钢包内合金化时,影响合金收得率的主要因素是()。
A.出钢时间长短B.钢水温度高低
C.下渣量及渣中氧化铁含量多少
答案C
7、下列元素脱氧能力由弱到强的顺序为()
A.Cr<Mn<V<Si<B<TiB.Cr<Mn<V<Si<Ti<B
C.Cr<Mn<B<Si<V<TiD.Cr<Mn<Ti<Si<V<B
A
(三)课后作业
课后作业,复习巩固知识、提升能力。
(1)每人记录10炉以上冷镦钢的冶炼操作数据(包括铁水预处理、转炉炼钢、炉外精炼LF、连续铸钢)。
(2)每人结合自己调研结果,选择冷镦钢生产流程中的某一岗位生产操作,结合所学知识编写详细的操作要点。
(3)总结钢的成产过程中合金元素控制的关键操作
(四)评价建议
学生考核评价实施表
评价方式
评价内容
评价结果
得分
过程性
评价
(100%)
学生出勤(10%)
迟到一次及以下
8~10
迟到三次
5~7
缺勤
课堂参与
(50%)
小组评价
(20%)
小组合作融洽,讨论能达到预定的目标
16~20
小组合作比较融洽,讨论基本达到预定的目标
10~15
小组合作相对融洽或不融洽,讨论未达到预定的目标
1~9
展示评价
展示内容全面,条理清楚、语言流畅
4~20
现场教学
(10%)
遵守现场规章制度,有良好的安全意识。
0~10
完成作业(30%)
思路清晰,格式规范,内容正确
自我评价(10%)