动力部汽轮机运行规程Word格式.docx
《动力部汽轮机运行规程Word格式.docx》由会员分享,可在线阅读,更多相关《动力部汽轮机运行规程Word格式.docx(138页珍藏版)》请在冰豆网上搜索。
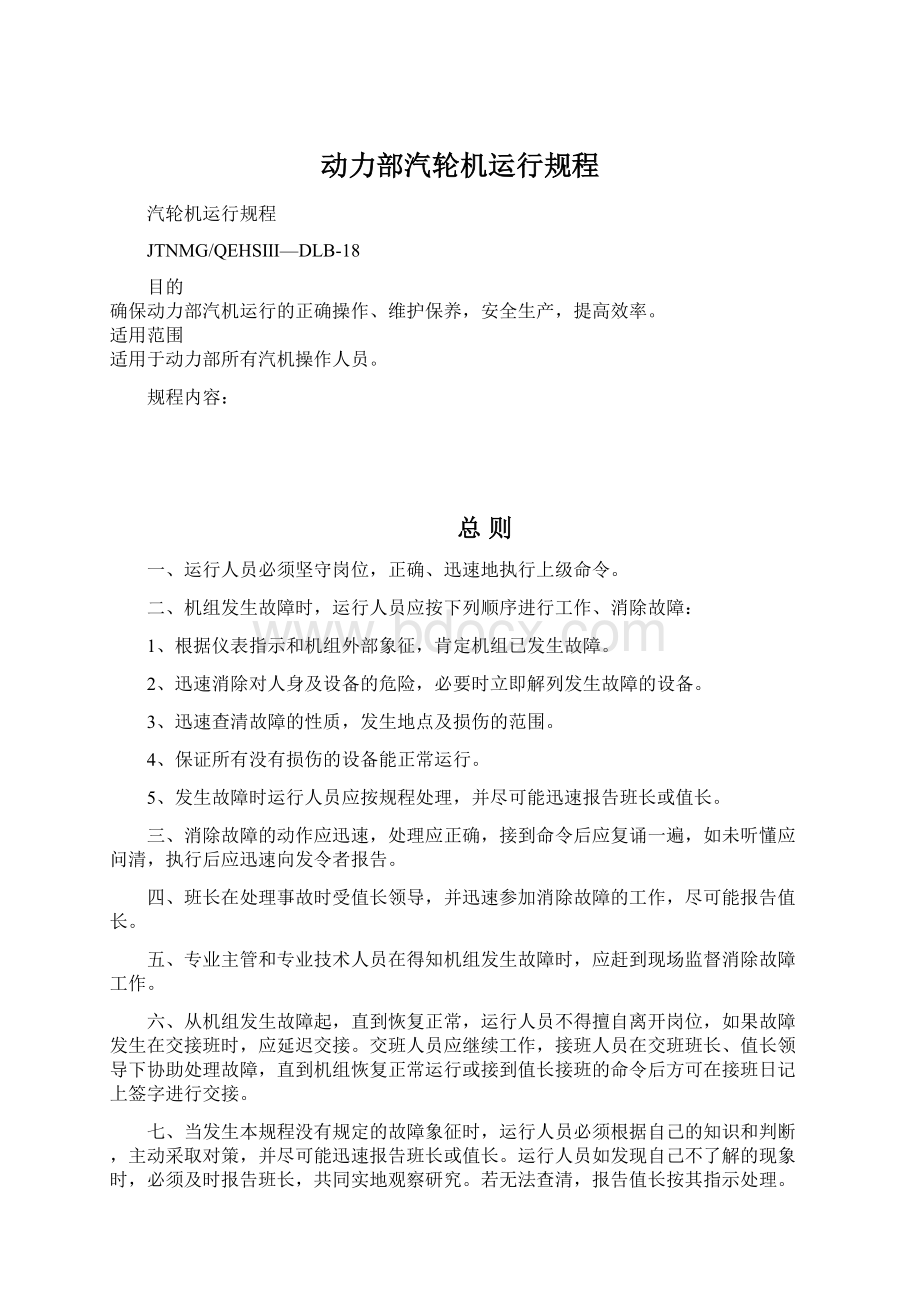
所有重要设备切换操作和监护,均应由合格人员担任,下级不能监护上级人员的操作。
三、在做系统隔离措施时,凡是高、低压在串联状况并无逆止门,禁止用低压侧阀门隔离。
应先关高压侧阀门,确认阀门无泄的情况下,方可关闭低压侧阀门;
有逆止门的情况下,也应先关闭高压侧阀门,确认高压侧阀门、逆止门无泄漏,方可关闭低压侧阀门。
若高压侧阀门不严密或逆止阀泄漏,应扩大安全措施,使高压系统彻底隔离,防止因积压造成管阀破裂。
汽轮机遇到下列情况,应采取措施消除,否则禁止启动
(特殊情况下由领导决定,订出相应原防范措施):
1、EH系统,保护装置失常,电动主汽门、自动主汽门、调速汽门,抽汽逆止门动作不正常。
缺少转速表或转速表不正常时;
不能维持空转运行或甩去全负荷后不能控制转速时;
主要表计或自动保护装置之一失灵;
任何一台油泵或其自启动装置有故障;
油质不合格或油温低于规定的极限值;
汽轮机转动部分有明显的金属磨擦声。
注:
1、主要表计指:
主蒸汽温度表、汽压表、流量表、转速表、真空表等。
2、自动保护装置指:
机组故障DEH中的ETS连锁各保护和DCS操作的各保护等应能自动停机的自动保护装置。
第一章汽轮机发电机组主要技术规范
第一节汽轮机主要技术规范、本体及系统说明
1、汽轮机组技术规范
序号
项目
单位
参数
名称
单抽汽凝汽式汽轮机
1
型号
CZK50-9.3/1.27
2
形式
高压、高温、单缸、单抽汽、冲动空冷式汽轮机
3
生产日期
2008年8月
4
进汽压力
主汽门前额定/最高/最低
MPa(a)
9.3/9.79/8.81
进汽温度
℃
535/540/525
功率
汽轮机功率额定/最大
MW
50/60
进汽量
汽轮机进汽量额定/最大
t/h
200/264
5
抽汽压力
汽轮机额定工业抽汽压力
1.27
6
压力变化范围
汽轮机额定工业抽汽压力变化范围
1.0~1.47
7
抽汽量
汽轮机额定工业抽汽量额定/最大
50/50
8
抽汽温度
汽轮机额定工业抽汽温度
286
9
排汽压力
汽轮机纯冷凝工况排汽压力
KPa(a)
15
11
给水温度
额定抽汽工况/纯冷凝工况
217/209
12
机组汽耗
汽耗﹙计算值﹚额定抽汽工况/纯冷凝工况
㎏/KW.h
5.260/3.976
13
机组热耗
热耗﹙计算值﹚额定抽汽工况/纯冷凝工况
KJ/KW.h
8397.2/10218.3
14
热耗﹙保证值﹚纯冷凝工况
10260.2
后汽缸排汽温度
(带负荷时/空负荷时)
<
65/<
100
16
汽轮机转向
(从机头向机尾看)
顺时针方向
17
汽机额定转速
r/min
3000
18
临界转速
汽轮机单跨/轴系临界转速(一阶/二级)
1630/1800
19
轴承震动
汽轮机轴承处允许最大震动
mm
0.025
20
过临界转速时轴承处允许最大震动
0.1
21
汽机中心高度
汽轮机中心高度(距离运转平台)
800
22
本体重量
汽轮机本体总重
t
127
23
汽机上半总重
﹙连同隔板上半等﹚
24
汽机下半总重
﹙不连同隔板下半等﹚
26
25
转子重量
汽轮机转子总重
汽轮机本体最大尺寸﹙长×
宽×
高﹚
8614×
5360×
3528
生产厂家:
南京汽轮机电机(集团)有限责任公司
本机共18级,其中,高中压部分9级(1调节级+8压力级),低压部分9级(1回转隔板+8压力级)。
绝对压力单位为MPa(a),表压单位MPa。
2汽轮机结构及系统性能说明
2.1结构概述
汽轮机结构包括静止部分和转子部分。
其静止部分又包括前、中、后气缸,隔板套、隔板、前后轴承座、前后轴承和前后汽封等。
前汽缸借助前端的猫爪与前轴承座相连。
前轴承座支承在前座架上。
后汽缸则支承在后汽缸座架上,后轴承箱则支承在后轴承箱座架上。
为了确保机组在运行中的膨胀和对中,前座架上布置了轴向导向键,使机组在运行中可以自由向前膨胀和上下膨胀。
在后汽缸座架上有横向销,后汽缸尾部有轴向导板,保证了汽缸在膨胀时的对中。
同时横向销与汽轮机中心线的交点形成了机组的膨胀死点。
转子部分包括主轴和套装叶轮叶片以及联轴器,它前后支承在前轴承和后轴承上,在汽缸中与喷嘴组及各级隔板组成了汽轮机的通流部分,并借助联轴器与发电机转子相连。
前端的支承点为推力轴承前轴承,在运行中形成转子的相对死点。
汽轮机端联轴器还装有盘车装置的传动齿轮,在起动前和停机后可以进行电动及手动盘车。
2.1.1转子
本机转子是一种柔性转子,其高温高压部分采用叶轮与主轴整锻而成:
低压部分采用了套装结构,其中还包括联轴器。
整锻转子主要是强度高而结构紧凑,套装叶轮主要是叶片较长,轮缘强度要求高而结构比较复杂。
本机所有叶片采用准四维设计的叶型。
2.1.2喷嘴、隔板、隔板套
喷嘴、隔板、隔板套均装在汽缸内。
它们和转子组成了汽轮机的通流部分,也是汽轮机的核心部分。
高压喷嘴组分成四段,通过T型糟道分别入四只喷嘴室内。
每一段喷嘴组一端有定位销作为固定点,另一端可以自由膨胀并焊有密封环。
本机的隔板采用了三种形式:
高压部分采用了窄喷嘴和宽叶型汽叶组成的分流叶栅,以提高隔板的强度和确保通流部分的经济性;
铣制静叶的内外围带焊接式,最后与隔板内外环焊接而成。
低压部分静叶两端直接和隔板体焊接在一起。
为了简化汽缸结构及降低汽缸的应力,并有利于启动及负荷变化,本机组采用了多级隔板套。
在隔板套中再装入隔板。
隔板与隔板套、隔板套与汽缸之间的联接均采用了悬挂销。
隔板和隔板套的底部均有固定键以保证运行中的对中性。
2.1.3汽封
机组的前汽封和隔板汽封,均采用了梳齿式汽封结构。
这种汽封结构的转子上面的汽封高低槽与汽封环的长短齿相配,形成了迷宫式汽封。
这种结构形式其汽封环的长短齿强度较高、汽封性能良好,同时便于维护和检修。
2.1.4轴承
本机轴承有两只径向椭圆轴承。
推力轴承与汽轮机前轴承组成了径向推力联合轴承,它是多层球面结构的椭圆轴承,安装在前轴承座内。
后轴承为圆柱面结构的椭圆轴承。
每个轴承的下半设有顶轴高压油通入小孔,孔周刮有油囊,作为顶起转子的压力区。
推力轴承采用可倾瓦式推力瓦块,每个主推力瓦块和径向轴承的轴瓦均有测温元件,在运行中可监视轴承合金的温度。
同时轴承的回油也布置了测温元件,以反应轴承回油温度。
2.1.5前轴承座
前轴承座为焊接结构。
它是汽轮机头部的主要部套。
其内部除了布置推力支持轴承和油泵组外,调节部套和各保安部套以及控制油系统都安装在该部套上,并有各种测点,是汽轮机现场的操作台。
汽轮机前汽缸借助猫爪结构支承在前轴承座上。
为了阻断汽缸猫爪对前轴承座的热传导,避免前轴承座升高影响汽缸中心升高,在猫爪下的滑键可通入冷却水,以达到阻断热传导的目的。
2.1.6汽缸
本机组的汽缸是由前汽缸和后汽缸组成的。
前缸和中缸为铸钢件,后汽缸为焊接件。
在设计中前汽缸有良好的对称形状,避免了水平中分面法兰的过厚过宽,以尽量减少热应力和热变形引起的结合面漏汽。
前汽缸与中汽缸的连接是借助垂直法连接的,连接后采用密封焊。
为确保密封良好,法兰面上十字交叉部位开有密封槽,在现场灌注密封涂料﹙耐温300℃以上,且耐压0.7MPa以上﹚,以加强汽密封。
蒸汽室、喷嘴室与前汽缸焊为一体。
四个蒸汽室分别布置在机组的前部左上、下侧和右上下侧,并由四根导汽管与主汽门相连。
中汽缸为简单的分上下半的圆筒结构,下半部有两个工业抽汽口,右侧配有一个支座和杠杆连接口,以固定旋转隔板油动机和安装旋转隔板调节连杆。
借助后部的垂直法兰与后汽缸相连。
后汽缸由各种钢板,钢管等焊接而成,用排汽接管与空冷器相连,左右两侧支承在后汽缸座架上。
在后汽缸上半装有排大气装置,当背压高于大气压时能自动打开,保护设备安全。
后轴承箱为焊接结构,内部有支承轴承和安放联轴器的空间及联轴器罩壳,上面装有盘车装置,通过后轴承箱座架直接座落在汽轮机平台上。
2.1.7盘车装置
盘车设备采用两级齿轮减速的机械传动式的低速装置。
其盘车转速约为4-6r/min。
启动时,大小齿轮啮合后即开启阀门提供润滑油,这是按动启动电机的按钮机组进入盘车状态。
冲动转子后,当转子速度超过盘车速度时,盘车齿轮能自动退出,并切断电机的电源和装置的润滑油。
在无电源情况下,电机的后轴伸出端装有手轮,可进行手动盘车。
投入盘车前应先投入轴顶油泵。
必须注意:
在连续盘车时必须保证润滑油的连续供给。
2.1.8主汽门
主汽门是有主汽门、自动关闭器及主汽门座架组成。
由锅炉来的蒸汽通过主蒸汽管进入主汽门汽室中的滤网、流过阀门后分四路流向调节阀。
主汽阀为单阀座型,为减小阀碟上的提升力,采用了带减压式预起阀的结构。
阀壳上设有阀前压力测点。
阀后压力温度及阀壳壁温测点。
阀杆漏汽分别接至除氧器和汽封加热器。
自动关闭器由油动机和断流式错油门组成。
来自主油泵的安全油作用在错油门下部,当克服弹簧阻力时打开油动机进油口使安全油进入油动机活塞下部。
当油压足够时便将主汽门打开。
油动机行程通过杠杆反馈到错油门活塞,这时它可停留在任意中间位置上,因而自稳定性能较好。
自动关闭器设有活动试验滑阀,在长期运行时,可以活动主汽门,以防卡涩。
油动机壳体下有冷却水腔室,以阻断蒸汽热量向自动关闭器传导。
2.1.9调节汽阀
本机组有四只独立调节汽阀,均采用带减压式预起阀的单阀座,以减小提升力。
本机采用高压抗燃油调节系统,四只高压调节汽阀由上海新华DEH控制系统控制四只阀的开启顺序和升程。
2.1.10后汽缸冷却装置
当汽轮机在空负荷或低负荷运行时,其排汽温度往往高于60℃,本汽轮机的后汽缸布置了喷水装置。
当排汽温度高于80℃时,可通入冷却水以降低后汽缸温度,确保后汽缸的安全运行。
3主热力系统概述
3.1主热力系统
从锅炉来的高温高压新蒸汽,经由新蒸汽管道和电动隔离阀至主汽门。
新蒸汽通过主汽门后,经四根导汽管流向四个调节汽阀。
蒸汽在调节汽阀控制下流进汽轮机内各喷嘴膨胀作功。
其中部分蒸汽中途被抽出机外作工业用抽汽和回热抽汽用,其余部分继续膨胀作功后排入空冷器,并凝结成水。
借助凝结水泵经汽封加热器,进入高压除氧器,然后经给水泵升压后送入两个高压加热器,最后进入锅炉。
汽封加热器和高压加热器均具有旁路系统,必要时可以不通过任何一个加热器。
凝结水泵后有一路再循环凝结水可进入排汽装置上部。
在低负荷运行时,此回水可保持冷凝器内一定的水位以维持凝结水泵的正常工作。
在启动时还可以用作冷却主汽门等的疏水和蒸汽。
3.2汽封系统:
轴封系统为自密封系统,自密封溢流到空冷器中。
这样布置的优点是能保证有足够的压差将溢流导入空冷器中,而不溢出前轴封,保证前轴封不漏汽、不油中带水。
机组的汽封系统分前汽封和后汽封。
前汽封有三段汽封环组成两档汽室;
后汽封有三段汽封环组成两档汽室。
其中:
前汽封一漏去除氧器﹙CY﹚,二漏入自密封系统﹙SSR﹚,三漏去轴封加热器﹙CF2﹚。
阀杆漏汽的一漏入除氧器﹙CY﹚,二漏入轴封加热器﹙CF2﹚。
后轴封漏汽:
共三段两个漏汽口,一漏来自自密封系统,二漏入汽封加热器。
3.3自密封系统
汽轮机前后汽封的自密封接口用管子与汽封压力均压箱相连接。
压力均压箱由高压新蒸汽供给。
在启动或低负荷时,由新蒸汽减温减压后经均压箱向汽轮机前后汽封供汽。
在高负荷时,由前汽封漏汽提供给后汽封供汽,其蒸汽流量足以满足后汽封密封要求,在这种情况下,压力均压箱压力高时,压力均压箱溢流调节阀投入工作,维持自密封系统压力,系统正常压力是0.13Mpa。
3.4疏水系统
汽轮机本体及各管道的疏水根据压力的高低分别送入高低压集水管后,排入排汽装置。
3.5真空系统
本机组为直接空冷凝汽式结构,汽轮机中的真空系统由空冷器、凝结泵和真空泵抽气器组成。
其作用是维持汽轮机在一定的工作背压下运行,同时把凝结水送回锅炉参加热力循环。
真空系统的空气由两部分组成:
一部分是蒸汽中含有的少量空气,这部分空气的含量取决于机组的除氧效果;
另一部分是大气中的空气从机组真空部分的不严密处漏入。
空气吸入量的多少,取决于机组的严密性,因此机组在电厂安装时,必须对真空系统所有焊缝和法兰接口作严密性检查,确认无泄漏。
机组投运后真空严密性试验每月一次,要求关闭抽气器后真空度下降速度不超过0.2KPa/min.
汽封系统中的不凝结气体由轴封风机抽出排入大气,不得接入抽气器尾部,以免影响真空系统的工作。
3.6调节系统﹙上海新华DEH控制﹚
4供油系统
供油系统的作用是机组各轴承提供润滑油和向保安系统提供压力油,同时还向盘车装置和顶轴装置供油。
油系统采用的工质为GB/T1120-89L-STA46#透平油,透平油质量必须符合GB/7596-2000《电厂用运行中汽轮机油质量标准》的要求。
本系统采用传统的汽轮机转子直接驱动的主油泵-----注油器供油线,主油泵出口的压力油驱动注油器工作,润滑油系统主要用于向汽轮机发电机组各轴承提供润滑油,向调节保安部套提供压力油,向顶轴装置中的油泵提供充足的油源。
在正常运行时,润滑油系统的全部需油量由主油泵和注油器提供。
4.1供油系统
供油系统主要由润滑油主油箱、主油泵、高压启动油泵、交流电动辅助油泵、注油器、冷油器、直流事故油泵、顶轴装置、油烟分离装置和净油化装置等组成。
在正常运行时,润滑油系统的全部需有量由主油泵和注油器提供。
主油泵的出口压力油分为两路:
一路向汽轮机机械式超速危急遮断装置供油:
另一路作为注油器的射流动力油。
注油器有两只,一只向润滑系统供油,一只向主油泵进口供油。
主油泵向保安系统提供的一路油,经过危急遮断复位及挂闸装置一固定节流孔在危急遮断油路中建立起压力,称为保安油。
当危急遮断装置动作时,会在瞬间使保安油路泄油失压。
由于有节流孔,此时流入该油路的压力油不足以影响快速泄油失压:
另一方面,流过节流孔的油量很少,因而也不会造成主油泵出口油压和油量的过大变化,以维持其它用油部件的正常供油量和油压。
润滑油经过轴承和盘车装置后,油温将升高,因此润滑油系统中设有两台冷油器。
正常运行时,一台冷油器工作,另一台备用,因此可以轮换进行清洗和维护。
可以在运行中进行冷油器的切换,但备用冷油器在切换时必须充满油,以防止在切换后的瞬间造成轴承断油而引起事故。
在需要时,两台冷油器可并联运行。
油温反映了轴承的工作情况,影响着机组的安全运行,因此必须将轴承回油温度限制在一个允许的范围内。
一般情况下,要求所有轴承回油温度低于65℃。
为了达到这个要求,需要调节冷油器的冷却水量,以保持冷油器的出口油温为38~42℃。
如果冷油器的出口油温在这个范围内,而轴承回油温度仍达到65℃以上时,则可能发生故障,这时必须检查原因。
在启动和停机过程中,当主轴转速小于2700~2800r/min时,主油泵不能提供足够的油压和油量,故注油器也达不到正常出力,此时应启动高压启动供油泵和交流电动辅助油泵,以满足系统供油需要。
辅助油泵有高压启动油泵,交流润滑油泵。
高压启动油泵提供保安系统用油,交流润滑油泵提供低压轴承润滑油的全部油量。
供油系统中还设有事故备用油泵。
在交流电源或交流电动油泵发生故障时,它是保证汽轮发电机组轴承润滑油供应的最后油源。
油系统是由大量各种管道、阀门和其它设备组成的复杂系统,即使是很小的有害颗粒亦可使轴承受到破坏,从而导致代价高昂的检修费。
因此,润滑油系统除运行时投入净油装置以保证油质外,在机组启动前还需对整个系统进行彻底的清洗,包括机械清洗和油清洗,并达到规定的油清洁度。
机组设有顶轴装置。
在盘车装置投入前投入顶轴油泵系统。
在盘车投入时,顶轴装置使盘车阻力距减小,并避免轴颈和轴瓦之间的干摩擦。
为了防止保安系统因压力油降低而引起停机事故,所以当主油泵出口油压降低至1.7Mpa时,由压力保护开关控制使高压交流油泵自动启动投入运行。
当运行中发生故障,润滑油压下降时,由润滑油压力控制器使交流润滑油泵自动启动,系统另备有一台直流润滑油泵,当润滑油压下降而交流润滑油泵不能正常投入工作时,由润滑油压力控制器使直流润滑油泵自动启动,向润滑系统供油。
正常的运行油压为:
0.08-0.15Mpa
油压降低时的要求:
小于等于0.078Mpa发信号
小于0.069Mpa交流润滑油泵自启动。
小于0.058Mpa直流润滑油泵自启动。
小于0.0396Mpa自动停机
小于0.0294Mpa停盘车装置
注意:
机组正常运行时,电动辅助油泵都应停止,除非在特殊情况下,允许自动启动。
在润滑油路中设有一个低压油过压阀,当润滑油压高于0.15Mpa左右即能自动开启,将多余油量排回油箱,以保证润滑油压维持在0.08-0.15Mpa之间。
4.2润滑油系统的主要设备
4.2.1润滑油主油箱
润滑油主油箱是一个由钢板焊制成的容器,箱体上布置有高压启动油泵、交流辅助电动油泵、直流事故油泵、油烟净化排放装置、电加热装置以及远传液位指示器、温度计等监视和控制装置。
该油箱的容量为﹙运行时﹚:
19.2m³
,总储油量为:
20.2m³
。
油箱的容量应保持在交流电源失掉且冷油器断水时机组能安全停机,即容量要足够大,以使冷油器断水时,机组在整个停机惰走过程中,轴承油温不超过设置值,以保证轴瓦的安全。
同时油箱是的容量还要能保证机组在甩负荷时容纳回油。
在正常运行时,要求回油在油箱中停留时间足够长,以利于油中杂质的分离。
当油位在正常油位上下+90mm或者-200mm范围之外时,远传液位指示器的高低油位报警器发出报警信号。
提醒运行人员注意。
除此之外,远传液位指示器还能输出4~20mA或1~5V的标准信号送计算机或显示仪表,供集中控制监视用。
注油器以及各电动油泵的出口油均装有滤网,防止杂质进入油系统。
该机组要求油温必须在10℃以上时才能启动油系统,因此在油箱上装设了侵没式电加热器,用以在低温环境下维持油箱内足够的油温。
控制油范围为27~38℃。
油箱是封闭式的,并且依靠排烟风机的抽吸维持一下内以及回油系统内有一定的负压。
油箱在顶部开有维护用人孔,在底部设有排油口和疏水口。
在长期停机期间,渣滓和水都会沉淀到油箱底部,因此在油系统运行前应从排油口排出少量油,将水和杂质带出。
正常运行过程中也会有沉淀,一般要求定期排污。
4.2.2主油泵
润滑油系统的主油泵安装在汽轮机高压转子前端短轴上,为双吸式离心泵,泵轮直接由汽轮机轴带动,它供油量大、出口压头稳定,轴向推力小,且对负荷的适应性好。
在额定转速或者接近额定转速时,主油泵供给润滑油系统的全部压力油,包括压力油总管、机械式超速遮断和手动遮断压力油总管、高压用油。
这种主油泵不能自吸,因此在汽轮机启、停阶段要依靠开启电动机驱动的辅助油泵供给机组用油和主油泵的进口油。
在正常运行时主油泵由注油器提供一定压力的进口油。
如果主油泵的吸油管道中进入了气体,泵的正常工作会破坏。
从而将造成润滑油系统的工作不稳定,因此主油泵的进口必须保持一定的正压。
离心油泵的出口油压基本上与转速的平方成正比,随着汽轮机转速的升高,主油泵的出口压力也升高。
当汽轮机转速达到90%额定转速时,主油泵和注油器就能提供润滑油系统的全部油量。
这时要进行辅助油泵和主油泵的切换,切换时应严密监视主油泵出口油压,当油压值异常时应采取紧急措施,以防止烧瓦。
汽轮机在额定转速下,主油泵进口油压为:
0.08-0.15Mpa时,出口油压为:
1.9-2.05Mpa,油泵体积流量为3000L/min。
4.2.3注油器
注油器挂装在主油箱上盖板,其吸油室浸在油面以下,它实质上是一个射流泵,其优点是结构简单、工作稳定、易于制造和调整。
缺点是噪声大且效率不高。
注油器由喷嘴、混合室、喉部和扩散段等基本部分组成。
喷嘴的进口与提供动力油的主油泵的出口相连。
工作时主油泵来的压力油以很高的速度从喷嘴射出,在混合室中形成一个负压区,油箱中的油被吸入混合室。
同时,由于油的黏性,高速油流带动吸入混合室的油进入注油器喉部,从油箱中吸入的油量基本等于主油泵供给喷嘴进口的动力油量,油流通过喉部进入扩压管以后速度降低,部分功能又转变为压力能,使压力升高,最后将有一定压力的油供给系统使用。
为了防止喷嘴被杂质堵塞和异物进入系统,在注油器的吸油侧装有一个可拆卸的多孔钢板滤网,在一定程度上,这个滤网还起着稳定注油器工作的作用。
供油系统在注油器扩压管后装有逆止阀,它在注油器不工作时,可以防止油从系统中倒流回注油器而进入油箱。
在混合室吸油孔的上方,装有一可上下自由移动的逆止板,当主油泵和注油器正常工作时,混合室中是负压,逆止板被顶起,油箱中的油可通过8个吸油孔吸入混合室。
而在机组启停等过程中电动辅助油泵工作时,逆止板落下,阻止了系统中的油经吸油孔倒流回油箱。
这个逆止