曲轴加工工艺设计.docx
《曲轴加工工艺设计.docx》由会员分享,可在线阅读,更多相关《曲轴加工工艺设计.docx(29页珍藏版)》请在冰豆网上搜索。
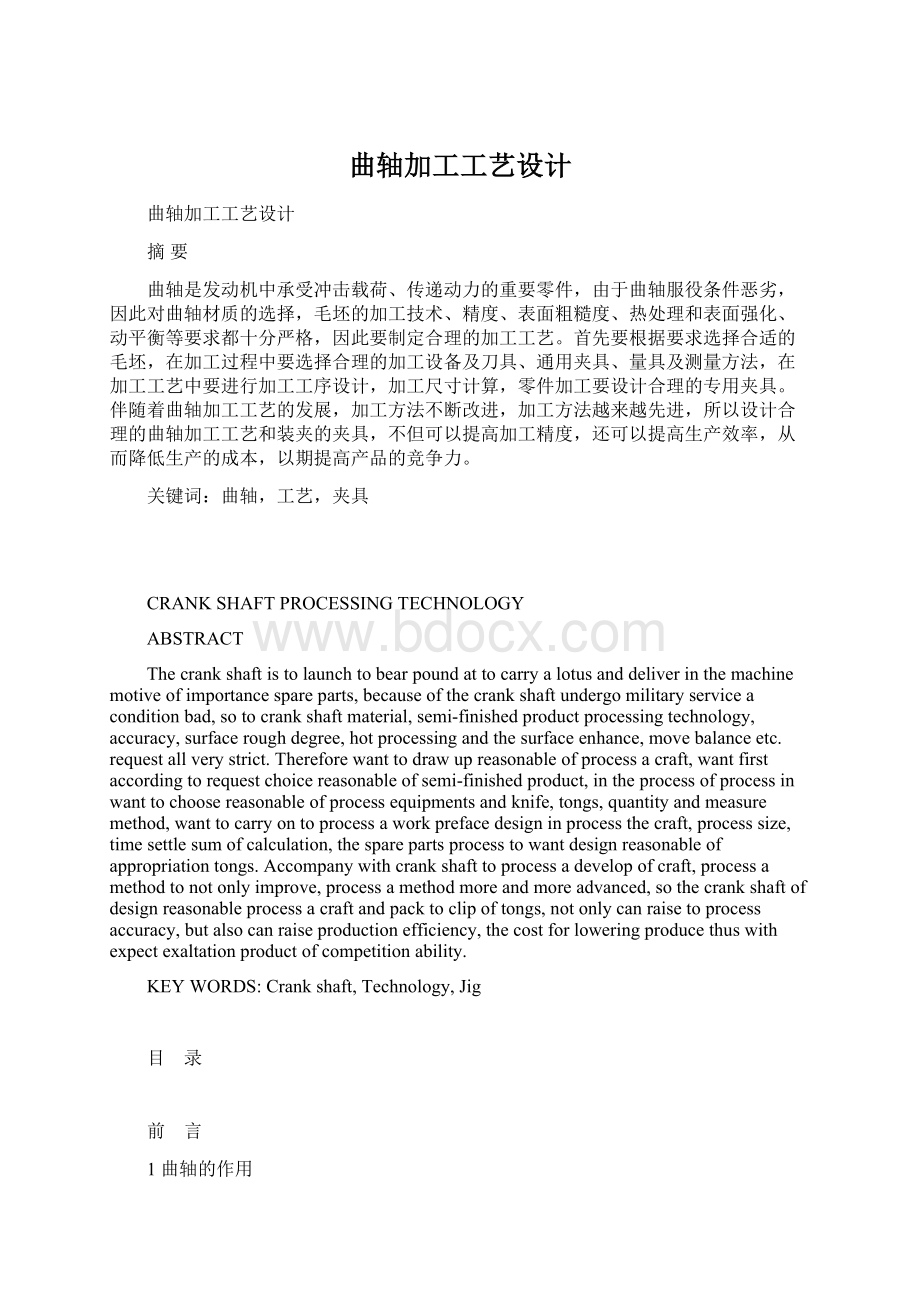
曲轴加工工艺设计
曲轴加工工艺设计
摘要
曲轴是发动机中承受冲击载荷、传递动力的重要零件,由于曲轴服役条件恶劣,因此对曲轴材质的选择,毛坯的加工技术、精度、表面粗糙度、热处理和表面强化、动平衡等要求都十分严格,因此要制定合理的加工工艺。
首先要根据要求选择合适的毛坯,在加工过程中要选择合理的加工设备及刀具、通用夹具、量具及测量方法,在加工工艺中要进行加工工序设计,加工尺寸计算,零件加工要设计合理的专用夹具。
伴随着曲轴加工工艺的发展,加工方法不断改进,加工方法越来越先进,所以设计合理的曲轴加工工艺和装夹的夹具,不但可以提高加工精度,还可以提高生产效率,从而降低生产的成本,以期提高产品的竞争力。
关键词:
曲轴,工艺,夹具
CRANKSHAFTPROCESSINGTECHNOLOGY
ABSTRACT
Thecrankshaftistolaunchtobearpoundattocarryalotusanddeliverinthemachinemotiveofimportancespareparts,becauseofthecrankshaftundergomilitaryserviceaconditionbad,sotocrankshaftmaterial,semi-finishedproductprocessingtechnology,accuracy,surfaceroughdegree,hotprocessingandthesurfaceenhance,movebalanceetc.requestallverystrict.Thereforewanttodrawupreasonableofprocessacraft,wantfirstaccordingtorequestchoicereasonableofsemi-finishedproduct,intheprocessofprocessinwanttochoosereasonableofprocessequipmentsandknife,tongs,quantityandmeasuremethod,wanttocarryontoprocessaworkprefacedesigninprocessthecraft,processsize,timesettlesumofcalculation,thesparepartsprocesstowantdesignreasonableofappropriationtongs.Accompanywithcrankshafttoprocessadevelopofcraft,processamethodtonotonlyimprove,processamethodmoreandmoreadvanced,sothecrankshaftofdesignreasonableprocessacraftandpacktoclipoftongs,notonlycanraisetoprocessaccuracy,butalsocanraiseproductionefficiency,thecostforloweringproducethuswithexpectexaltationproductofcompetitionability.
KEYWORDS:
Crankshaft,Technology,Jig
目 录
前 言
1曲轴的作用
曲轴是内燃机最重要零件之一,它与汽缸、活塞和连杆等零件组成的发动机的动力装置。
曲轴的作用是将做功冲程经连杆传来的力变成扭矩,并带动发动机其他机件运动和向外输出动力。
曲轴转速为发动机每个工作行程都有很大的燃气压力,通过活塞、连杆突然传递到曲轴上,以一定的频率反复冲击到曲轴上,因此曲轴作为发动机的重要部件,在传递动力的过程中主要承受交变周期性的弯曲-转载荷和一定的冲击载荷的作用,同时承受不但变形的气体压力、活塞和连杆运动所产生的惯性力和离心力作用,即曲轴的各部件产生变形、扭转、剪切、拉伸等复杂交变应力,因此将造成曲轴扭转振动和弯曲振动,同时在一定的条件下还会产生很大的附加应力,因此受力十分复杂。
曲轴的主轴颈、连杆轴颈和曲轴臂各处受到较严重的磨损,受力各不相同。
2发动机曲轴加工工艺的历史发展演变
20世纪70年代以前,发动机曲轴粗加工采用的加工方式是多刀车床车削曲轴主轴颈和连杆轴颈。
采用这种方式加工精度较低、柔性很差、工序质量稳定性低,且容易产生较大的内部应力,难以达到合理的加工余量。
在粗加工后一般需要进行去应力回火处理,释放应力。
因此粗加工需要给后续精加工工序留较大的加工余量,以去除弯曲变形量。
曲轴精加工采用的是普通磨削工艺,一般采用MQ8260曲轴磨床粗磨-半精磨-精磨-抛光。
通常靠手工操作,加工质量不稳定,废品率较高。
20世纪70年代到80年代左右,曲轴粗加工采用CNC车削、CNC外铣加工,加工状况有所改善。
精加工仍以普通磨床磨削工艺为主。
20世纪80年中期又出现了CNC内铣工艺,CNC内铣加工性能指标要高于CNC外铣加工,尤其是对于锻钢曲轴,内铣更有利于断屑。
精加工工艺多采用半自动曲轴磨床,头架和尾座同步传动,加工精度有一定的提高。
1985年到1990年左右开发出了曲轴车拉、车-车拉工艺,该工艺具有精度高、效率高等优点,特别适合于平衡块侧面不需要加工且轴颈有沉割槽(包括轴向沉割槽)的曲轴,加工后曲轴可直接进行精磨,省去粗磨工序。
曲轴精加工已少量采用数控磨床磨削工艺,尺寸的一致性得到改善。
20世纪90年代中期又开发出CNC高速外铣,它对平衡块侧面需要加工的曲轴,比CNC车削、CNC内铣、车-车拉的生产效率还要高。
另外,CNC车-车拉工艺加工连杆轴颈要二道工序,CNC高速外铣只要一道工序就能完成,具有以下优点:
切削速度高(可高达350m/min)、切削时间较短、工序循环时间较短、切削力较小、工件温升较低、刀具寿命高、换刀次数少、加工精度更高、柔性更好。
所以CNC高速外铣将是曲轴主轴颈和连杆轴颈粗加工的发展方向。
精加工使用数控磨床,采用静压主轴、静压导轨、静压进给丝杠(砂轮头架)和线性光栅闭环控制等控制装置,使各尺寸公差及形位公差得到可靠的保证,精加工还广泛使用数控砂带抛光机进行超精加工,经超精加工后的曲轴轴颈表面粗糙度至少提高一级精度。
20世纪90年代开发的CBN高速磨削。
英国LANDIS公司生产的曲轴磨床,磨削速度高达120m/s,用扒皮法一次装夹从毛坯到精磨完毕,耗时仅几分钟的时间,这将会出现以磨代替其它粗加工工艺的新局面。
进入21世纪以后,复合加工工艺已进入曲轴制造业中。
复合机床应具有工序集成功能,多种加工集成功能。
奥地利WFL公司生产的卧式车铣复合加工中心(M40G型)能在曲轴硬化前“一次装夹,全部加工”,加工后的曲轴可直接转入精加工工序;曲轴精加工方面,也出现了工序集成的CBN数控磨床,即一次装夹磨削全部曲轴主轴颈和连杆轴颈(摆动跟踪磨削)。
由以上演变可以看出,曲轴的加工工艺正向着高速、高效、复合化方向发展。
目前较为流行的粗加工工艺是主轴颈采用车-车拉工艺和高速外铣,连杆颈采用高速随动外铣,全部采用干式切削;精加工采用数控磨床加工,具有自动进给、自动修正砂轮、尺寸和圆度自动补偿、自动分度和两端电子同步驱动等功能。
主轴颈和连杆颈可一次装夹全部磨削完毕;超精加工采用数控砂带抛光机,带尺寸控制装置。
3曲轴加工工艺现状
曲轴是发动机的关键零件之一,其结构复杂,生产批量大,品种更换频繁,精度要求高。
主轴连杆颈的尺寸精度为IT6~IT7,圆度≤0.005mm,表面粗糙度Ra0.2~0.4。
因此,一条先进的曲轴生产线不仅要实现柔性换产以面对市场需求,还要满足工艺要求,保证加工精度,最终生产出合格的产品。
锻钢曲轴生产线拥有世界顶级的数控机床、先进的加工工艺及日臻完善的管理制度,不仅大幅提升了曲轴的加工效率,实现了柔性快速换产能力,而且更好地保证了曲轴的加工质量。
当前,曲轴的质量主要通过机加工和热处理的过程控制来保证,其途径大致有以下三种:
1.人为检测:
指通过专业质检人员(或操作人员自检、互检)对每道工序按照工艺要求进行在线测量,及时调整工艺参数,避免不合格产品周转到下道工序或出现批量废品。
2.设备控制:
指依靠较高设备精度保证当前工序的加工精度,是保证尺寸精度、形状精度和位置精度的有效方式,也是先进曲轴加工生产线的标志之一。
3.工艺保障:
工艺是机加工过程中将曲轴毛坯转化成成品的法律准绳,是产品质量的根本保证,也是提高加工效率的前提。
通过不断地改进人们发现:
人为检测相对难度较低,但是后期改善效果不明显。
通过先进设备控制加工精度已在锻钢生产线和部分铁轴生产线上实施,改善效果可观。
对于工艺保障,由于国内外锻钢曲轴的加工工艺大同小异,且刀具、砂轮、切削液、淬火涨量、加工参数及加工余量等影响质量因素涉及改善周期长、优化空间小及普及性差等特点,因此要通过加工工艺的改进、优化来提高产品质量。
第1章零件加工工艺设计
1.1零件工艺分析
从曲轴的形状来看,其横断面会沿轴线方向急剧变化,应力的分布极不均匀,尤其是曲柄臂和曲轴颈、过渡圆角部分以及油孔附近会产生应力集中。
曲轴要承受自身的扭转振动所引起的附加力,曲轴在长期的运行过程中,在应力集中区产生疲劳破坏,因此弯曲和疲劳断裂是主要的破坏形式,曲轴连杆轴颈、主轴颈及轴承副在较高的比压下进行高速的相对旋转,轴颈与曲轴过渡处疲劳引起的裂纹,将会造成磨损发热和烧伤,其中曲轴表面的磨削下当将产生严重后果。
[7]
根据曲轴的工作状况,为保证曲轴进行可靠的工作,曲轴必须有足够的强度、硬度、良好的耐磨性和高的抗疲劳性能,质量要小,各工作标表面要求耐磨、润滑良好。
具体来讲曲轴应具有以下力学性能:
(1)具有足够的强度,减少轴颈的翘曲变形,提高自抗振能力。
(2)表面有高的硬度、弯曲疲劳强度、扭转强度和耐磨性。
(3)有良好的抗疲劳强度和冲击性。
(4)有良好的润滑作用。
曲轴失效的形式主要有以下两种:
(1)疲劳破坏。
一是在轴颈与轴柄过渡圆角处产生疲劳裂纹;二是轴颈中部的油道内壁产生环行的裂纹,逐渐发展为曲柄处的断裂。
(2)轴颈表面严重磨损。
连杆的大端通过剖分式滑动轴承(轴瓦),安装在Φ68g10(mm)的连杆轴颈中,连杆小头整体套装在活塞中的活塞销中。
曲轴两端Φ70m6(mm)的主轴颈用来安装轴承,将曲轴支承在发动机箱体中。
Φ70m6(mm)的主轴颈外侧的环形槽内嵌放弹性挡圈,可实现主轴承的轴向定位。
主轴右侧的锥形轴安装齿轮或皮带轮,将发动机产生的转矩传递给工作机构,实现动力输出。
左侧Φ30s(mm)的轴颈上安装正时齿轮,驱动正时齿轮箱中的各种正时齿轮,实现发动机的配气正时,燃油供给正时,并驱动润滑系统、冷却系统,完成发动机正常工作时需要的各种辅助功能,其轴颈Φ30s7(mm)环形槽内放置弹性挡圈,实现正时齿轮的轴向定位,右端的主传动齿轮或皮带轮用M44X2-6H螺母压装在Φ50h10的锥形轴上,同样也可以实现轴向定位,曲柄下端4个M12X1.2-5H螺纹孔,用来安装一对平衡块,实现曲轴高速回转时所必需的动平衡要求。
[3]
M33X1.5的螺纹孔用来安放油堵,实现连杆轴颈处滑动轴承的润滑。
同样主轴颈Φ70m6(mm)上的斜油孔内,也需安放油堵,才能形成封闭的油滑油路,可靠的实现曲轴高速旋转时,连杆滑动轴承所需要的润滑,圆柱螺纹Rp