重庆大学先进制造课程论文Word文件下载.docx
《重庆大学先进制造课程论文Word文件下载.docx》由会员分享,可在线阅读,更多相关《重庆大学先进制造课程论文Word文件下载.docx(11页珍藏版)》请在冰豆网上搜索。
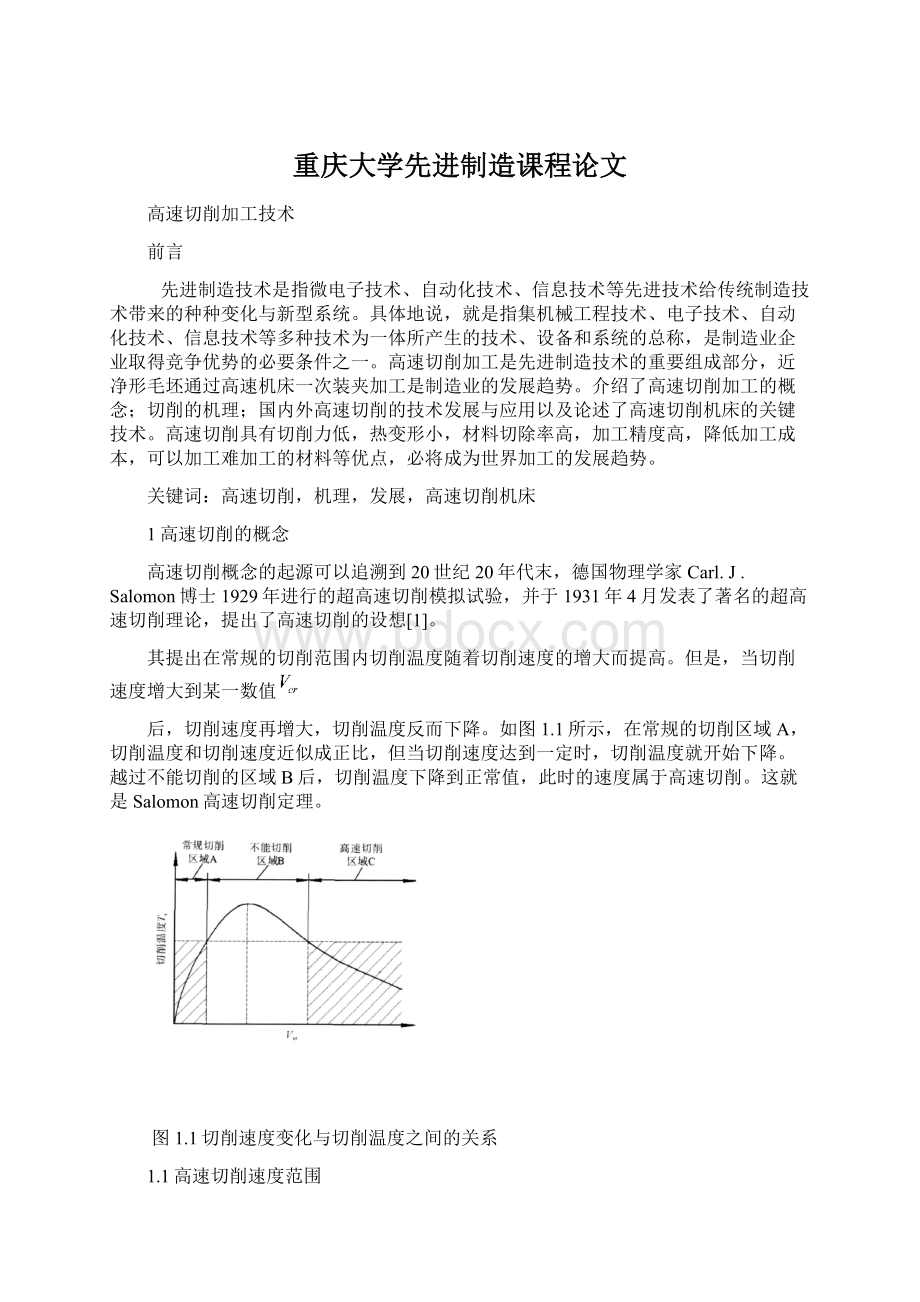
这就是Salomon高速切削定理。
图1.1切削速度变化与切削温度之间的关系
1.1高速切削速度范围
高速切削是一个相对的概念,很难就高速切削的速度范围给出确切的定义。
对于不同的加工方式、不同工件有不同的高速切削范围。
目前沿用的高速切削加工的定义主要有以下几种[1]。
(1)1978年,CIRP(国际生产工程研究院)切削委员会提出的以线速度500~7000m/min的切削速度进行加工为高速切削加工;
(2)对铣削加工而言,以刀具夹持装置达到平衡要求时的速度来定义高速切削加工.根据ISO1940标准,主轴转速高于8000r/min为高速切削加工;
(3)德国Darmstadt工业大学生产工程与机床研究所((PTW)提出将高于普通切削速度5一10倍的切削加工定义为高速切削加工;
(4)从主轴设计的观点,以Dn值(主轴轴径或主轴轴承内径尺寸D与主轴最大转速n的乘积)来定义高速切削加工.Dn值达((5~2000)
105mm
r/min时为高速切削加工。
(5)从刀具和主轴的动力学角度来定义高速切削加工.这种定义取决于刀具振动的主模式频率。
因此,高速切削加工不能简单地用某一具体的切削速度值来定义.切削条件不同,高速切削速度范围亦不同.1992年在CIRP会议上发表了不同材料大致可行的和发展的切削速度范围,如图1.2所示。
图1.2不同工件材料的切削速度范围
2高速切削的发展
高速切削由于具有切削力低,热变形小,材料切除率高,加工精度高,降低加工成本,可以加工难加工的材料等优点,目前已经成为全世界加工的趋势,国内外科研人员在高速切削的发展上做出了不可估量的贡献。
2.1国外高速切削
美国于1960年前后开始进行超高速切削试验,试验将刀具装在农炮里,从滑台上射向工件,或将工件当作子弹射向固定的刀具[1]。
1977年,在一台带有高频电主轴的加工中心上进行了高速切削试验。
1984年,德国国家研究技术部组织了以Darmstadt工业大学的生产工程与机床研究所和41家公司参加的两项联合研究计划,全面、系统地研究了超高速切削机床、刀具控制系统以及相关的工艺技术,实现了高速切削的突破,并且应用到生产实际中。
日本于20世纪60年代就着手超高速切削机理的研究,日本学者发现在超高速切削时,绝大部分切削热被切屑带走,工件基本保持冷态,其切屑比常规切屑热得多。
为后续基于切削形状的研究作为高速切削的突破口奠定了基础。
2.2国内高速切削
中国高速切削加工技术研究起步较晚。
20世纪80年代以来对高速切削刀具寿命与切削力,高速切削机理,高速硬切削和切屑形成机理,钦合金高速铣削、薄壁件高速铣削精度控制、铝合金高速铣削表面温度,高速主轴系统和快速进给系统,高温合金的高速切削等进行了初步研究并取得了令人鼓舞的成就。
加工中心主轴转速普遍提高到8000r/min,最高可达12000r/min,数控车床的主轴最高转速提高到6000r/min,快速进给速度最高达40m/min,换刀时间减少到1.5s。
3高速切削的关键技术
实现高速切削加工的核心研究内容主要有:
高速切削机理、高速加工用刀具技术、高速机床技术等。
在大批量生产领域,薄壁零件加工领域,难加工材料领域,超精密微细加工领域得到了广泛的应用。
3.1高速切削机理
如图3.1所示,在高速切削过程中一般都有一个共同的特点,即形成锯齿形切屑。
对高速切削中形成的锯齿形切屑的解释主要有两大理论体系,即绝热剪切理论和周期脆性断裂理论。
目前也有对两大理论体系进行总结,认为绝热剪切理论适用于解释塑性材料或者是在切削过程中转化为塑性材料的脆性材料形成的锯齿形切屑,而周期脆性断裂理论适用于解释脆性材料的切屑形成。
图3.1锯齿形切削
3.1.1绝热剪切理论
1981一1982年,Komanduri及其合作者对钦合金和高强度钢的切屑形成过程进行了研究,提出一个锯齿形切屑形成的两阶段模型,如图3.2。
第一阶段包括第一变形区窄带内的绝热剪切失稳和应变局部化,导致了沿剪切面的突变型剪切断裂;
第二阶段包括在刀具进给的作用下通过位于其前方的楔形工件材料翻卷,屑片在其变形几乎可忽略的情况下逐渐形成[2-3]。
图3.2锯齿形切屑形成机理
3.1.2周期脆性断裂理论
M.C.Shaw和A.Vyas总结了锯齿形切屑形成的各种机理,最早提出周期脆性断裂理论,他们认为切削时先从切屑自由表面产生裂纹,并不断向刀尖扩展,在下一个裂纹产生时,前一个裂纹扩展停止,依次周期性产生,最终形成锯齿形切屑[4]。
3.2高速加工用刀具技术
高速切削技术的发展在很大程度上得益于超硬刀具材料的出现及发展。
由于高速切削的切削速度是传统切削速度的5~10倍,普通刀具不能胜任高速加工。
这就将刀具放在高速加工中的重要关键技术之一。
要求高速切削刀具具备高的耐热性、抗热冲击性、良好的高温力学性能及高的可靠性。
3.2.1高速切削刀具材料[5]
目前高速加工所用刀具材料主要是聚晶金刚石(CPD)、立方氮化硼(CBN)、陶瓷、Ti(C,N)基金属陶瓷、涂层刀具(CVD)和超细晶粒硬质合金等,这些刀具材料品种的增加和性能的提高,大大的促进了高速加工发展的脚步。
①聚晶金刚石(CPD)
PCD刀具材料具有高硬度、高耐磨性、高导热性及低摩擦系数等特点,PCD刀具可实现有色金属及耐磨非金属材料的高速、高精度、高稳定性加工。
多齿焊接式PCD刀具的切削刃对刀柄的跳动较小,尤其适合对各种有色金属零件的成形面、孔、阶梯孔等进行大批量高速加工。
PCD颗粒的大小对刀具的加工性能影响较大,如PCD粒径为10~25
的PCD刀具适于切削加工Si含量
12%的铝合金(切削速度v=300一1500m/min)及硬质合金;
PCD粒径为8~9
12%的铝合金(切削速度v=500~3500m/min)及通用非金属材料。
图3.3聚晶金刚石刀具
②立方氮化硼(CBN)
CBN刀具具有极高的硬度及红硬性,是高速精加工或半精加工淬火钢、冷硬铸铁、高温合金等的理想刀具材料。
由于CBN刀具加工高硬度零件时可获得良好的加工表面粗糙度,因此采用CBN刀具切削淬硬钢可实现“以切代磨”。
刀具中CBN含量不同,用途也不同。
例如含量为50%,用于连续切削淬硬钢(45-65HRC);
含量为80%-90%,用于高速切削铸铁(v=500-1300mm/min)等。
图3.4立方氮化硼刀具
③陶瓷刀具材料
陶瓷刀具材料是通过在氧化铝和氮化硅基体中分别加入碳化物、氮化物、硼化物、氧化物等得到的,此外还有多相陶瓷材料,其中
基陶瓷和
基陶瓷刀具应用最为广泛。
陶瓷刀具可在200一1000m/min的切削速度范围内高速切削普通钢、淬硬钢、铸铁及其合金等。
基陶瓷刀具具有良好的耐磨性、耐热性和高温化学稳定性,不易与铁元素之间发生相互扩散或化学反应,其耐磨性和耐热性高于
基陶瓷刀具,因而
基陶瓷刀具适用范围最广,可用于对钢、铸铁及其合金的高速切削。
基陶瓷刀具的断裂韧性和抗热震性高于
基陶瓷刀具,适合于铸铁的高速切削。
图3.5陶瓷刀具材料刀具
④Ti(C,N)基金属陶瓷
金属陶瓷具有较高的室温硬度、高温硬度、化学稳定性和良好的耐磨性,广泛应用于金属材料的切削加工。
与TiC基金属陶瓷相比,Ti(C,N)基金属陶瓷晶粒更细,其高温抗蠕变性能也有明显的改善,切削刃锋利且强度高,在高速微进给,小切深切削条件下,有利于去除切屑和提高加工表面质量,可用于高速半精加工和精加工,是高硬度工模具净成型加工的首选刀具材料。
⑤涂层刀具(CVD)
涂层刀具是通过在刀具基体上涂覆金属化合物薄膜,以获得远高于基体的表面硬度和优良的切削性能。
常用的刀具基体材料主要有高速钢、硬质合金、金属陶瓷、陶瓷等;
涂层既可以是单涂层、双涂层或多涂层,也可以是由几种涂层材料复合而成的复合涂层。
硬涂层刀具的涂层材料主要有氮化钛(TiN),碳氮化钛(TiCN),氮化铝钛(TiAlN),碳氮化铝钛(TiAlCN)等,其中TiAlN在高速切削中性能优异,其最高工作温度可达800°
C,十分适合用于高速切削。
图3.6涂层刀具
⑥超细晶粒硬质合金
超细晶粒硬质合金是一种高硬度、高强度和高耐磨性兼备的硬质合金,它的WC粒度一般为0.2一1.0
以下,大部分在0.5
以下,是普通硬质合金WC粒度的几分之一到几十分之一,具有硬质合金的高硬度和高速钢的强度。
其硬度一般为90一93HRA,抗弯强度为2000~3500MPa,比含钴量相同的一般WC-Co硬质合金要高,与加工材料的相互吸附、扩散作用较小,特别适用于耐热合金钢、高强度合金钢以及其它难加工材料。
图3.7超细晶粒硬质合金刀具
4高速切削机床
高速机床技术主要包括高速单元技术和机床整机技术。
高速加工机床能否达到理想加工状态,主要取决于高速加工机床的关键单元。
高速加工机床单元技术的研究内容主要包括:
高速主轴单元、高速进给系统和高速CNC控制系统等。
高速机床整机技术研究内容主要包括:
机床床身、冷却系统、安全措施和加工环境等。
4.1高速主轴单元技术
高速切削是以主轴高速化为核心的多项先进技术的综合应用,它是一项复杂的综合技术。
涉及主轴的轴承承受力,润滑,热稳定性等方面。
高速主轴单元的性能将直接影响高速切削的功效,也关系着高速机床能否成功。
由于高速切削加工可以用Dn值(主轴轴径或主轴轴承内径尺寸D与主轴最大转速n的乘积)来定义。
所以早期的高速切削机床的主轴由Dn值作为设计的依据。
但目前,多数高速机床主轴采用内装式电机主轴,简称“电主轴”。
电主轴采用无外壳电机,将带有冷却套的电机定子装配在主轴单元的壳体内,转子和机床主轴的旋转部件做成一体,主轴的变速完全通过交流变频控制实现,将变频电机和机床主轴合二为一电主轴系统主要包括高速主轴轴承、无外壳主轴电机及其控制模块、润滑冷却系统、主轴刀柄接口等[6],如图4.1所示。
图4.1电主轴
电主轴具有如下主要特点:
(1)电主轴系统取消了高精密齿轮等传动件,消除了传动误差;
(2)减小了主轴的振动和噪声,提高了主轴的回转精度.电动机内置于主轴两支撑之间,可以较大地提高主轴系统的刚度,也就提高了系统的固有频率,从而提高了其临界转速.电主轴可以确保正常运行转速低于临界转速,保证高速回转时的安全;
(3)电主轴采用交流变频调速和矢量控制,具有输出功率大、调速范围宽和功率一扭矩特性好的特点;
(4)电主轴机械结构简单,转动惯量小,快速响应性好,能实现很高的速度、加速度和定角度的快速准停。
高速加工的最终目的是为了提高生产率,因此要求主轴在最短的时间内实现高转速的速度变化,也就是要求主轴回转时具有极大的角加速度,达到这个要求最经济的方法就是采用电主轴。
4.2高速进给系统
高速机床除了需要具有高速主轴系统,而且需要具有高速进给系统,这不仅是为了提高生产率,也是为了达到高速切削中刀具正常工作的条件,否则会造成刀具急剧磨损,破坏加工工件的表面质量.在进行高速切削时,为了保证零件的加工精度,随着机床转速的提高,进给速度也必须大幅度提高,以便保证刀具每齿进给量不变;
另一方面,由于大多数零件在机床上加工的工作行程不长,一般只有几十毫米到几百毫米,进给系统只有在很短的时间内达到高速和在很短的时间内实现准停才有意义[5]。
为了实现高速进给,除了可以继续采用经过改进的滚珠丝杠副外,以及采用直线电机驱动(图4.2a)和基于并联机构的新型高速进给方式(图4.2b)。
图4.2高速进给系统的方式
4.3高速CNC控制系统
高速切削的数控装置必须具备很高的运算速度和精度。
采用快速响应的伺服控制,以满足复杂型腔的高速度加工要求。
目前,主轴电机仍然是采用矢量控制技术的变频调速交流电机。
主轴数字控制系统和数字伺服驱动系统,应具有高速响应特征。
在高速加工中,输入的控制程序一般仍是标准ISONC代码。
但在高速条件下,传统的NC码存在很多问题,诸如应采用特殊的编程方法,解决目前计算机辅助制造直接输出的NC码存在的不兼容的问题。
4.4机床支撑技术
机床支撑技术主要指机床的支撑构件的设计及制造技术。
高速机床设计的关键是如何在降低运动部件惯量的同时,保持基础支撑部件的高静刚度、动刚度和热刚度。
通过计算机辅助设计,特别是应用有限元分析及优化设计理论,能获得质量轻、刚度高的机床床身、立柱和工作台结构。
对精密高速机床,国内外有的采用聚合物混凝土来制造床身和立柱,或者采用大理石材料的床身(图4.3),以上方法可以有效的增加床身的阻尼,减少机床的振荡。
图4.3大理石床身
4.5辅助单元技术
辅助单元技术包括快速工件装夹、安全装置、高效冷却润滑液过滤、切屑处理和工件清洁等技术。
高效冷却的方法目前已经出现了高速干切削的机床,另动力学的快速冷却至零下的方法正在与机床的冷却想结合。
5总结
高速切削加工的在大批量生产领域,薄壁零件加工领域,难加工材料领域,超精密微细加工领域的应用,使得高速切削加工成为必然的制造发展趋势。
特别是在军工方面,我国长期面临由于精度不高,大量的军工零件形状复杂等原因,在军工方面还显得落后。
通过对高速切削加工的机理,以及其关键技术的学习,我明白了先进制造的重要性,也更加明白作为一名当代的机械工程师,身负的重任。
下一步,我将规划好余下的研究生生活,扎扎实实的学习好专业知识,多利用寒暑假的时间去工厂实地学习,充实自己的大脑,为祖国的制造工业贡献自己微薄的力量。
参考文献
[1]李长河.丁玉成.高速切削加工技术发展与关键技术[J].青岛理工大学学报.2009(30):
7-15
[2]于静.董海.高速切削机理的研究现状[J].工具技术.2011(15):
3-6
[3]肖大武.李英雷.绝热剪切研究进展[J].实验力学.2010(25):
463-471
[4]李智慧.师俊平.金属材料脆性断裂机理的实验研究[J].应用力学学报.2012(29):
48-53
[5]李鹏南.张厚安.高速切削刀具材料及其与工件匹配研究关[J].工具技术.2008(42):
21-24
[6]容隶莹.机床高速主轴关键技术的探讨[J].湖南农机.2011(38):
59-61
[7]李子艳.高速切削机理及若干问题研究[D].天津;
天津大学.2006.01
[8]苏国胜.高速切削中切削速度对工件材料力学性能和切屑形态的影响机理[J].中国科学.2012(42):
1305-1317
[9]齐智勇.数控高速切削的关键技术[J].现代制造.2014(11):
65-68
[10]张伯霖.数控机床高速化的研究与应用[J].中国机械工程.2001(11):
1132-1136
[11]杨辉.高速加工机床进给驱动系统的研究[D].安徽;
合肥工业大学.2006.10
[12]潘建新.周志雄.高速主轴及其润滑冷却形式[J].润滑与密封.2006(6):
162-164
[13]卢蔚红.高速切削技术在模具加工中的运用[J].技术应用.2010
(1);
110-113
[14]袁玉福.高速切削加工在机械加工中的应用[J].科技创新与应用.2014(29):
101
[15]郝世美.人造石精密机床床身动静态性能研究及结构强化[D].山东;
山东大学.2013.06