半密闭电石炉自动上下料系统资料.docx
《半密闭电石炉自动上下料系统资料.docx》由会员分享,可在线阅读,更多相关《半密闭电石炉自动上下料系统资料.docx(9页珍藏版)》请在冰豆网上搜索。
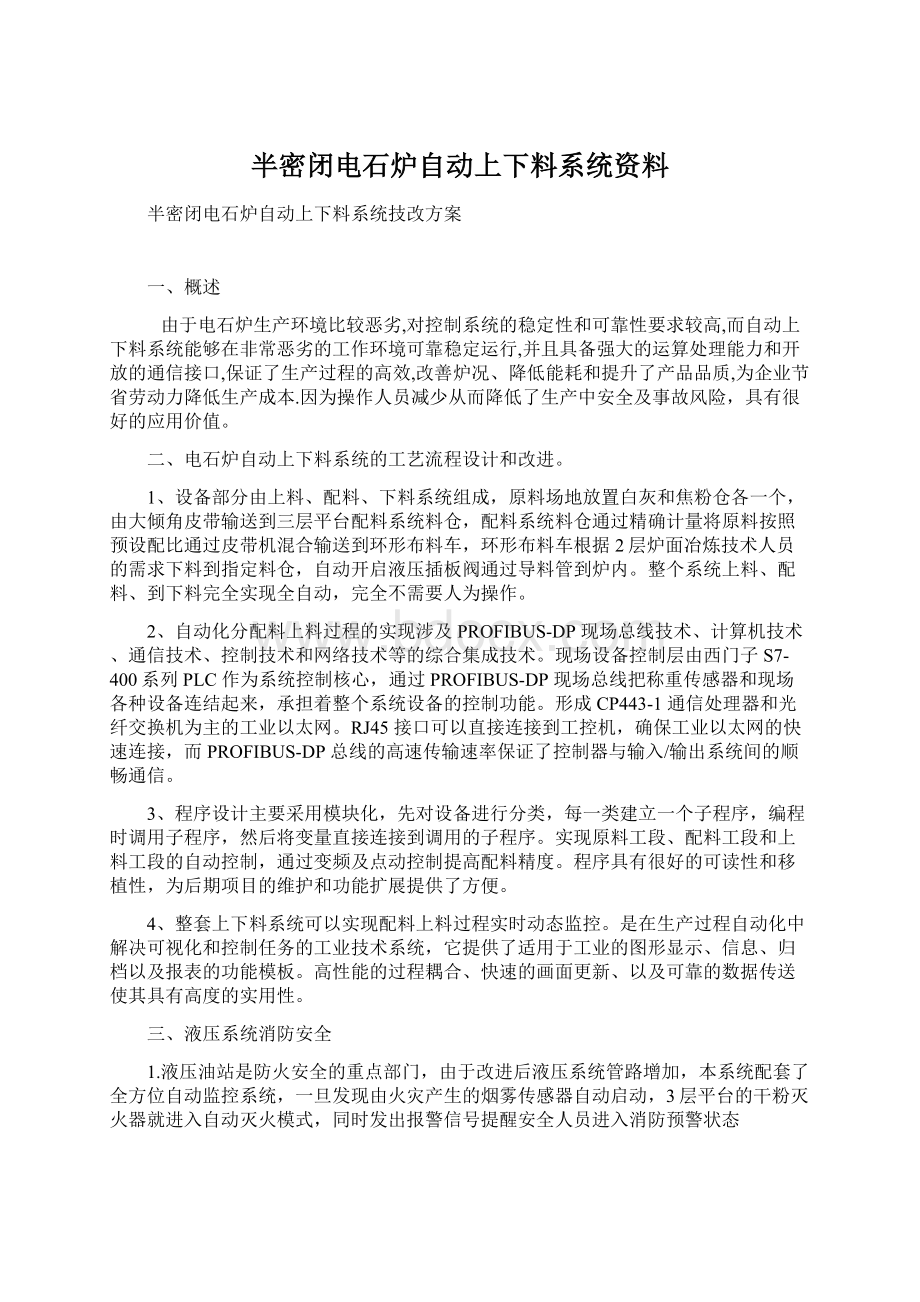
半密闭电石炉自动上下料系统资料
半密闭电石炉自动上下料系统技改方案
一、概述
由于电石炉生产环境比较恶劣,对控制系统的稳定性和可靠性要求较高,而自动上下料系统能够在非常恶劣的工作环境可靠稳定运行,并且具备强大的运算处理能力和开放的通信接口,保证了生产过程的高效,改善炉况、降低能耗和提升了产品品质,为企业节省劳动力降低生产成本.因为操作人员减少从而降低了生产中安全及事故风险,具有很好的应用价值。
二、电石炉自动上下料系统的工艺流程设计和改进。
1、设备部分由上料、配料、下料系统组成,原料场地放置白灰和焦粉仓各一个,由大倾角皮带输送到三层平台配料系统料仓,配料系统料仓通过精确计量将原料按照预设配比通过皮带机混合输送到环形布料车,环形布料车根据2层炉面冶炼技术人员的需求下料到指定料仓,自动开启液压插板阀通过导料管到炉内。
整个系统上料、配料、到下料完全实现全自动,完全不需要人为操作。
2、自动化分配料上料过程的实现涉及PROFIBUS-DP现场总线技术、计算机技术、通信技术、控制技术和网络技术等的综合集成技术。
现场设备控制层由西门子S7-400系列PLC作为系统控制核心,通过PROFIBUS-DP现场总线把称重传感器和现场各种设备连结起来,承担着整个系统设备的控制功能。
形成CP443-1通信处理器和光纤交换机为主的工业以太网。
RJ45接口可以直接连接到工控机,确保工业以太网的快速连接,而PROFIBUS-DP总线的高速传输速率保证了控制器与输入/输出系统间的顺畅通信。
3、程序设计主要采用模块化,先对设备进行分类,每一类建立一个子程序,编程时调用子程序,然后将变量直接连接到调用的子程序。
实现原料工段、配料工段和上料工段的自动控制,通过变频及点动控制提高配料精度。
程序具有很好的可读性和移植性,为后期项目的维护和功能扩展提供了方便。
4、整套上下料系统可以实现配料上料过程实时动态监控。
是在生产过程自动化中解决可视化和控制任务的工业技术系统,它提供了适用于工业的图形显示、信息、归档以及报表的功能模板。
高性能的过程耦合、快速的画面更新、以及可靠的数据传送使其具有高度的实用性。
三、液压系统消防安全
1.液压油站是防火安全的重点部门,由于改进后液压系统管路增加,本系统配套了全方位自动监控系统,一旦发现由火灾产生的烟雾传感器自动启动,3层平台的干粉灭火器就进入自动灭火模式,同时发出报警信号提醒安全人员进入消防预警状态
2.站内全体员工应熟练掌握“三懂”、“三会”的防火知识,并做到经常检查防火器材,做好记录,灭火器要保持完好。
3.卸油时,应使用专用工具开启油泵盖,严禁使用易发生火花的工具开启,防止产生火花发生火灾事故。
4.液压站内的电气设备应采用防爆型设备,各种开关需设在站内的必须采取防爆措施。
5.站内严禁有跑、冒、滴、漏的现象发生,保持站内地面清洁无油脂、油污。
6.油站内的储油缸的油量不得超过容积的90%.
7.站内严禁存放易燃易爆物品和随意动用明火,因需要动用明火时,必须领取“动火证”后方可动火,并负责动火过程中的防火监护工作。
8.站内严禁吸烟,保持通风良好。
四、电石炉自动加料系统的重要性
兰炭和石灰配比精确度的提高是降低能耗、提高产品质量的有效手段,而上料布料的稳定性是保证电石炉安全运行的关键。
过去电石生产主要是以人工操作为主,不断提高配料上料过程的自动化水平是工业化发展的必然趋势。
国家对电石生产的控制比较严格,电石生产过程中的新技术水平己经成为国家对电石行业准许生产的决定因素之一。
在未来几年,国家可能强制电石生产过程完全自动化。
为了保证电石炉长期稳定生产,对电石生产配料上料控制系统进行技术研究和设计,提高自动配料和上料控制系统的自动化水平具有重要意义。
五、小型电石炉配料下料过程中存在的主要缺点为:
1、下料过程兰炭和石灰不能完全叠加到一块,甚至兰炭下完以后,石灰才开始下料。
如果混合不均匀,熔融状态的混合物产生的CO气体不能及时溢出,当气体压力不断升高后,会导致塌料喷火现象或者直接导致喷料,对工人的人身安全产生严重威胁,如果长期塌料喷火现象严重,设备破坏程度较大,可能会发生漏水现象。
水在几万安培电流的电离作用下产生氢气(HZ)和氧气(Oz),氢气、氧气和一氧化碳气体的大量增加会产生爆炸,后果不堪设想。
2、称重设备精度低,人为影响因素较多,物料配比不能很好的掌握,从而导致不合格品多,生产成本大大增加。
3、石灰和兰炭粉尘大,除尘设备除尘效果不好,工作环境差。
随着国家实施低碳经济战略,成熟的技术应用是高耗能产业面临的重要问题,配料上料自动化程度有利于加强资源节约和管理,大力推进节能降耗。
电石行业是高耗能高污染行业,但同时又是中国的基础原料行业,需要加强整顿,却又不可缺少。
十二五期间,电石总量仍将受到严格控制,淘汰落后产能也仍将继续,《电石单位产品能源消耗限额》将继续成为行业需要遵守的标准。
未来电石企业需要努力降低单耗,提升能源利用率,既能达到节能降耗的目的,又能提升企业的综合竞争力
六、我们现有配料系统改进
配料上料下料是电石生产的一个重要环节,配料岗位的工作质量直接影响到电石炉的产、质量及设备维护。
其重要性从以下几个方面来体现:
1、配料:
电石生产是按一定合理配比来进行生产的,配料时若不注意配料的准确性,会影响到下一个班的正常生产。
我们专门针对电石炉现有原料焦粉水分过大白灰强度不达标导致混合在一起时间容易发生反应,于是我们在配料方面让混合料在短时间内进入炉膛内部
2、兰炭和石灰混合不均匀也将使炉料的局部配比发生变化,同样影响生产控制。
我们通过减轻一个批次配料的总重量分多批次进行下料
3、料封:
层炉面操作人员通过现场观察在生产需要时进行及时下料 ,下料后操作人员要将料面封料避免明火喷出造成热能损耗。
通过计算机技术和自动化技术相结合改进电石生产的工艺和配料精度,是为了改善电石的品质,提高市场竞争力,降低电能的消耗,改善工作环境、劳动强度和工作效率。
对电石炉配料上料控制策略的研究,具有较高的现实价值。
七、自动上下料系统现状
1、 随着自动控制技术的不断发展,国内外电石炉的配料上料技术基本上经历了四个阶段,分别为手动操作、电气控制、单片机远程操作、工控机集中控制等。
第一阶段,各个设备之间相互独立,基本没有联系。
现场的操作员凭经验来决定是否调整设备。
每个操作工只能同时操作一至两台称量斗,称量斗的相关配料数据只能通过人工来记录,这样配料精度不能完全保证合格。
第二阶段,出现了小型化的微机配料上料电动组合控制方式。
但是这种组合控制方式存在着很大的缺点:
①电子线路及其复杂;②由于电石生产过程中环境恶劣,电子元件不断老化,抗干扰能力开始下降,配料精度难以保障。
第三阶段,大规模集成芯片技术不断发展,生产工艺不断成熟和完善。
以集成电路为基础的单片机配料上料控制系统电路变得简单可靠。
同时单片机的信息传送速率大大加强,价格便宜,具有较高的竞争力,能满足不断发展的配料技术需求。
第四阶段,工控机PC的研制成功,使集中式配料控制系统整体结构简单,监控软件与工控机的结合,使人机界面更加友好,交互功能更加强大。
集中控制对主机及其测控电路要求较高,而且需要专业性自动化人才。
总之,我国电石炉生产主要以中小企业为主,而且存在位置分散、产能低下、设备粗放、管理混乱等缺点。
电石生产过程中配料上料控制系统精确度不高,整个生产系统稳定性差,所以提高电石生产过程中配料上料的自动化水平迫在眉睫,是未来几年发展的必然趋势。
2、存在的问题和难点
为了保证配料上料的过程可靠性,口料仓、皮带机、称量斗等某些设备在设计的初期就实现了设备的多套性和冗余性。
但对几家电石企业的调查和分析从技术方面讲还存在以下主要问题和难点:
(I>从配料系统设备的电气控制角度来分析,好多现场设备的功率以及过流过压保护与实际的运行状态不符合,电机经常出现故障或烧毁,需要技术人员现场测试调试。
在设计单位调试成功后没有经过长期运行和测试存在大量实际性问题,而相关技术人才紧缺。
(2>国内电石生产企业的整个工艺水平落后粗糙,能简单的实现电石的半自动化生产,受工艺影响整个生产的完全自动化及高级管理根本无法实现。
(3)称量斗的动态称量中存在的两个难点是称重准确度和称重速度,如果称重速度过快,则电机振动给料机振幅过大,在空中自由落体的物料太多,对称重传感器冲击过大严重影响称量精度。
所以,我们必须按照工艺要求采用两级振动降低称重速度,提高称量精度。
在称重动作完成后延迟几秒,把称量斗稳定后的重量作为最终的重量。
然后最终重量减去配料初始称量斗的重量就是本次配料的实际重量。
高速度和高准确度称量一直是配料行业的难题
(4)电石炉环型加料车料仓料位检测一直是困扰行业上的一大难题。
八、自动化操控系统改进的经济性和安全性
电石炉配料上料控制系统智能化、配比精确化、上料布料稳定化方向的分析和研究。
根据目前电石企业中存在的问题,对生产工艺改进,设计出操作简单、维修方便、控制稳定的操作系统。
主要内容包括以下几个方面:
(1>对内蒙古自治区内的电石生产企业进行调查和研究,发现缺点和问题,并对存在的控制缺陷改进,在继承前人优点的前提下,实现生产工艺和控制系统的双向改进。
(2>配料上料过程分成三段,实现原料工段、配料工段和上料布料工段设备的组起、组停和单机启动。
对配料过程进行动态补偿,提高称量斗的配料精度。
原料、配料和上料过程的程序设计采用模块化,在以后的项目中完全可以移植,为相类似的项目提供借鉴的机会。
(3)分析和研究PROFIBUS-DP总线的技术特点、总线通讯模型、主从站结构等内容。
设计出以57-300/400系列西门子PLC为核心的系统,通过PROFIBUS-DP现场总线把称重传感器和现场各种设备连结起来,承担着整个系统设备的控制功能。
CP443-1通信处理器和光纤交换机为主的工业以太网,RJ45接口可以直接连接到工控机,确保工业以太网的快速链接,而PROFIBUS-DP总线的高速传输速率保证了控制器与输入/输出系统间的顺畅通信[f5l
(4)运用WinCC组态监控功能,实现配料上料过程实时动态监控、实时报警、模拟量归档、生产报表和用户管理等功能,监控画面的快速更新及可靠的数据传送使其具有高度的集中管理的特点。
(5)对动态称重系统进行分析,在动态称重测量的基础上,对定量下料自动控制系统进行研究,提出相应的解决方案并建立数学模型。
(6)电石炉自动上下料系统的经济性;原有人工加料系统每班需要12个工人进行加料,而且工人劳动强度大生产环境恶劣,造成工作效率生产效率低下,改为自动加料系统后每班只需3人可以轻松布料,不但省去了人力投入同时提高了生产效率,因为设备的自动化的提高大大降低了人力的投入从而降低了生产过程中的安全隐患。
九、配料上料工艺及设备
首先将符合电石生产要求分别送入焦粉料仓和白灰料仓,输送到配料系统料仓,当称重系统完成两种原料的称重及配比后,石灰和兰炭经过传送皮带被输送到车间的环形加料车内,再由环形加料车将石灰和兰炭的混合料加入到11个炉顶料仓内,物料经过炉顶料仓的料管在重力作用下自由下落到电石炉内。
电石炉内有三根电极,每根电极外面由钢板焊接而成,钢板内部由电极糊填充。
电石炉的高压变压器将35KV的高压电变换成低压高电流的电能,并将电能提供给三根充满电极糊的电极。
工业上一般使用电炉熔炼法,电炉熔炼法是将兰炭与氧化钙(Ca0)置于2200 0C左右的电炉中熔炼,生成碳化钙(CaC2)。
1、原料系统工艺流程
原料的烘干及破碎是电石生产的一个重要环节,配料岗位的工作质量直接影响到电石炉的产、质量及设备维护。
而原料的好坏(包括颗粒的大小湿度的大小等)也直接