铁路桥梁转体施工关键技术Word下载.docx
《铁路桥梁转体施工关键技术Word下载.docx》由会员分享,可在线阅读,更多相关《铁路桥梁转体施工关键技术Word下载.docx(11页珍藏版)》请在冰豆网上搜索。
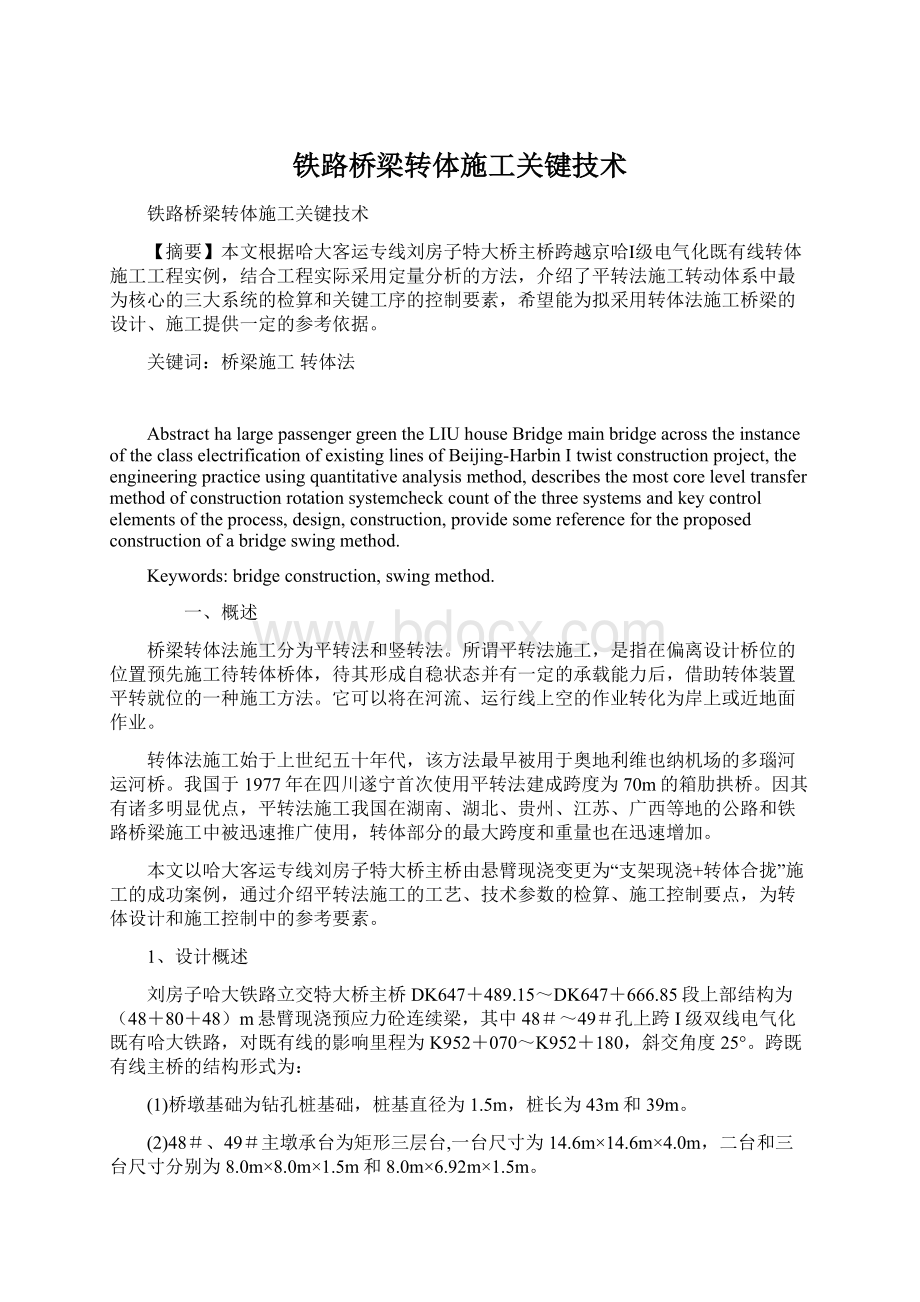
(4)上部结构为(48+80+48)m现浇预应力砼连续梁。
设计为单箱单室连续梁。
箱梁顶宽13.4m,翼缘板长3.35m,支点处梁高6.60m,跨中梁高3.80m,梁高及底板厚按二次抛物线变化。
腹板厚100cm(支点)~48cm,底板厚度为100cm(支点)~40cm,顶板厚度40cm~65cm。
箱梁0#块梁段长度为12m,合拢段长度为2.0m,边跨直线段长度为7.75m。
2、施工方案的变更
客运专线在上跨施工对既有京哈铁路的运营有着重大影响,为减少和避免施工干扰,安全、高效的完成主桥施工,故提出对刘房子大桥主桥悬臂现浇施工变更为转体施工的工艺,即:
首先将48#、49#主墩承台变更为矩形双层台,一台尺寸为14.6m×
4.0m,二台尺寸为8.0m×
3.0m,并在上下承台间设置转动体系,转体工作空间高度为0.8m。
承台间转动体系设置完成后,沿平行于既有线位置施工桥梁上承台、墩身及托盘,并支架现浇待转体桥身部分,桥梁旋转至设计轴线后,依次浇筑边跨和中跨合拢段成桥。
二、平转法转动体系的设计
本桥转体结构采用在上下承台间设置平转法转动体系,用钢板转盘平面铰形式的中心支承转动、辅以保险平衡脚稳定的方案,承重采用中心支承。
平转法转动体系主要有承重系统、顶推牵引系统和平衡系统三大部分构成。
1、承重系统由上转盘、下转盘和转动球铰构成,上转盘支承转体结构,下转盘与桩基础相连,通过上转盘以钢轴为中心相对于下转盘转动,达到转体目的。
在平衡状态下,不考虑撑脚承受重力;
在偏心状态,部分撑脚受力。
承重体系的设置如下:
球铰下转盘钢板直径300cm、厚30mm,材质Q345D,安装时精确定位并布置于下承台顶面,埋入砼17mm,露出砼13mm。
在下转盘钢板顶面内嵌20mm厚四氟乙烯滑板,滑板嵌入13mm,其顶面高出下转盘钢板顶面7mm,高于下承台顶面20mm。
上转盘同样采用直径300cm、厚30mm,材质Q345D钢板,安装于上承台底部的砼底部。
上下转盘的盘心设置定位钢转轴,钢轴直径15cm,材质Q345D,以保证上下转盘能同心旋转。
转铰构造图(单位cm)
转铰安装实体图
2、顶推牵引系统:
顶推牵引系统由牵引设备、牵引反力支座、顶推反力支座构成;
牵引设备采用两台ZLD100型100t连续千斤顶作为牵引千斤顶,两台普通YCW100型100t千斤顶作为启动助推千斤顶。
牵引反力支座布置于承台以外,用现浇钢筋混凝土浇筑而成,牵引索预埋于布置于上承台,上承台是转铰、撑脚与上转盘相连接的部分,又是转体牵引索直接施加牵引力的部位。
上承台内预埋牵引索固定端采用P型锚具,同一对牵引索的锚固端设置于同一直径线上并对称于圆心,每根索的预埋高度应和牵引施加点的高度一致。
每根索埋入转台的长度为2.5m,每根索的出口点也应对称于转盘中心。
牵引索外露部分应圆顺地缠绕在上承台周围,互不干扰地露出于上承台,在转体前做好保护措施。
顶推力施加于撑脚,反力支座为保险脚。
牵引设施平面布置图(单位cm)
3、平衡系统由结构本身、上承台下端预埋的钢管混凝土圆形撑脚、保险脚、大吨位千斤顶、滑道及梁顶两端放置的6m3的备用平衡水箱构成。
(1)撑脚
为了增强转体过程中结构的稳定性,防止结构发生较大倾斜,在上转盘底面沿距转动中心半径为R=325cm的圆周均匀设置了8个双φ60cm圆形钢管混凝土撑脚,径向夹角为45°
,上承台撑脚距下承台滑道顶面15mm,钢撑脚焊接于上承台主筋之上,埋入上承台50cm,露出部分长为78.5cm,其内浇筑C50微膨胀混凝土。
当转体发生倾斜时,撑脚先支承于下转盘的滑道上,防止转体进一步侧倾。
为减小撑脚底面与滑道的摩擦,撑脚底面钢板与滑道的接触面部分应由工厂加工定做,接触面应刨平,粗糙度不低于6.3级,镀铬后刨光处理。
上转盘撑脚平面布置图
撑脚安装
(2)保险脚
为了进一步防止转体时的侧倾风险,在下承台表面环道两侧均匀布置12个保险脚,保险脚沿圆周方向的夹角30°
,径向厚度为40cm。
同时,保脚起到助推千斤顶的反力支座的作用。
下转盘保险脚布置图(单位cm)
(3)滑道
为了减小撑脚与下转盘的接触摩擦,撑脚支承面必须置于同一水平面内,从而使转体能平稳运行。
在下承台顶面设置外径3.65m,宽0.8m的环形可调式滑道,滑道由型钢支架、24mm厚的滑道钢板及5mm厚的不锈钢板贴面三部分组成。
滑道钢板通过高强螺栓镶嵌与型钢支架上,四氟板通过环氧树胶加压粘贴于滑道钢板上。
可调式滑道通过型钢支架的粗调及高强螺栓的微调,来实现四氟板表面高程误差0.5mm。
(4)备用大吨位千斤顶及水箱
为了防止突发荷载作用于转体上,引起转体失衡,调整失衡状况下转体的运行姿态,在桥墩对称轴线方向,滑道外侧设置4台大吨位备用千斤顶,及时调整转体过程中转体的运行姿态。
同时在梁端部设置两个带刻度、容积为6m3的备用水箱,做为调整转体失衡的备用措施。
三、转体施工
1.施工准备
⑴转体过程中的液压及电器设备出厂前要进行测试和标定,并在厂内进行试运转。
⑵设备安装就位。
按设备平面布置图将设备安装就位,连接好主控台、泵站、千斤顶间的信号线,接好泵站与千斤顶间的油路,连接主控台、泵站电源。
⑶设备空载试运行。
根据千斤顶施力值(启动牵引力按静摩擦系数μs=0.1,转动牵引力,按动摩擦系数μd=0.06考虑)反算出各泵站油压值,按此油压值调整好泵站的最大允许油压,空载试运行,并检查设备运行是否正常;
空载运行正常后再进行下一步工作。
⑷安装牵引索。
将钢绞线牵引索顺着牵引方向绕上转盘后穿过千斤顶,并用千斤顶的夹紧装置夹持住。
先用1~5kN逐根对钢绞线预紧,再用牵引千斤顶在2MPa油压下对该束钢绞线整体预紧,使同一束牵引索各钢绞线持力基本一致。
⑸拆除上、下转盘间的固定装置及支垫。
⑹拆除所有支架及约束后,全面检查转体结构各关键受力部位是否有裂缝及异常情况。
若出现重心偏移,经采用配重或在上转盘下设置竖向调整以满足转动必须条件。
处理完毕对转体结构的静置观察、监测时间应>
2h。
安装好转体观测仪器,并调试正常。
⑺防超转机构的准备。
在平转就位处应设置限位机构,防止转体到位后继续往前走。
⑻辅助顶推措施的准备。
根据现场条件,将2台1000kN辅助转体千斤顶对称、水平地安放到合适的反力座上,根据需要在启动、止动、姿态微调时使用。
2.试转体
⑴预紧钢绞线。
用100T连续千斤顶将钢绞线以1~5kN的力预紧,预紧应采取对称方式的进行,并应重复数次,以保证各根各根钢绞线受力均匀。
预紧过程中应注意保证钢绞线平行地缠于上转盘。
⑵打开主控台及泵站电源,启动泵站,用主控台控制两台千斤顶同时施力转体。
若不能转动,则施以事先准备好的辅助顶推千斤顶同时出力,以克服超静摩阻力来启动桥梁转动,若还不能启动,则应停止试转,另行研究处理。
⑶转体时,记录试转时间和速度,根据实测结果与计算结果比对进行调整转速,即应做好两项重要数据的测试工作。
试转过程中,检查转体结构是否平衡稳定,有无故障,关键受力部位是否发生变形开裂等异常情况。
如有异常情况发生,则应停止试转,查明原因并采取相应措施整改处理后方可继续试转。
3.正式转体
⑴同步转体控制。
①同时启动,现场设同步启动指挥员,采用对讲机进行通讯指挥。
②连续千斤顶公称油压相同,转体采用同种型号的两套液压设备,转体时控制好油表压力。
③进行同步观测。
⑵结构旋转到距设计位置约5°
时应放慢转速,改用手动控制牵引千斤顶,距设计位置相差1°
时,可停止外力牵引转动,借助惯性就位。
为保证转体就位正确,预埋限位型钢且加橡胶缓冲垫,即使发生转体过位,还可以利用下盘保险柱做支撑,用千斤顶反推就位。
⑶转体过程监测。
本测试采用动态位移测试法获得每对撑脚处在转体过程任一时刻(或状态)的竖向位移值,并据此确定转体过程中任一时刻(或状态)梁体有可能发生的竖向刚体位移。
指导调整转动梁体由于不平衡力矩或其他偶发因素可能导致的梁体倾斜量。
⑷转体就位采用经纬仪中线校正,中线偏差不大于2cm。
⑸转体就位后采用临时支墩对箱梁进行支护。
4.封固转盘
经过转体和精确定位阶段后,测量组的数据表明转体高程、轴线偏位均符合设计要求,立即在8个保险柱两侧下转盘承台上焊接型钢反力架(事先精确定位预埋钢板),打入钢楔块,并将其临时锁定。
保证转体单元不在产生位移。
清洗底盘上表面,焊接预留钢筋,立模浇筑封固混凝土(C50微膨胀砼)、使上转盘与底盘连成一体。
混凝土塌落度保持在8~10cm。
5.箱梁合拢
先施工边跨合拢段,然后施工中跨合拢段,解除墩梁临时固结成桥。
施工方法略。
四、转动体系主要部件的取值及检算
1、基本参数的选取
(1)转体设计总重力为G=47000kN(取1.15安全系数,重量包括:
上承台、墩身、梁体、水箱、临时安全围挡等)。
(2)球铰水平投影半径D/2=1.15m。
(3)上转盘(牵引束力偶臂)外径D1=7.3m。
(4)滑道中心线直径(助推力作用力臂)D2=6.5m。
(5)按《公路桥涵施工技术规范JTJ041-2000》第16.4条,取动摩擦系数f1=0.05,静摩擦系数f2=0.10。
(6)设计转角速度V≤1.2m/min。
(7)梁端旋转线距离:
39.3m。
2、承重系统主要部件设计
待转体时解除了所有临时约束,球铰为整个待转体桥体的承重结构,此时为球铰最大受力阶段。
球铰设计依据为:
(1)球铰竖向反力计算
a.工况一:
转体平衡时
b.工况二:
转体失去平衡时
式中:
—球铰轴心处竖向反力
—撑脚竖向反力
—转体部分重量
—偏心矩
—撑脚中心线至转动中心的距离
取以上两种工况最不利者控制球铰的竖向承载能力(即不考虑撑脚受力)。
G=(上承台+墩身+箱梁及临时设施等)×
1.15=47000KN
(2)球铰平面半径计算
—球铰平面直径
—撑脚竖向反力
—球铰接触面积折减系数,取0.65
—球铰下混凝土的标准抗压强度
上下承台采用C40砼,其轴心抗压强度26MPa,则转盘直径为:
考虑施工中风荷载及施工误差因素,导致转体结构失去平衡,需进行平衡配重,故应有一定的安全储备,球铰设计竖向承载能力采用48000KN,按G=48000KN计算球铰平面直径D=1.87m。
考虑结合构造及滑道的空间布置要求,球铰选用725所设计生产的48000kN转体球铰,球铰平面直径D=2.3m,设计最大静摩擦系数0.1,最大动静摩擦系数0.06。
3、牵引系统主要部件设计
转体处于平衡状态,当施加的外力偶矩大于球铰处静摩擦力产生的阻力力矩时转体发生转动,为使连续千斤顶加力均匀,转体发生转动时匀速转动,外力偶矩由牵引力偶距及助推力偶矩组成。
⑴转体牵引力按式下式计算:
T=(2×
f×
G×
R/3)/D
T-牵引力(KN)
G-转体总重力(KN)
f-摩擦系数,取动摩擦系数f1=0.05,静摩擦系数f2=0.10。
R-铰柱半径(m)
D-牵引力偶臂(m)
⑵转体竖向反力计算
为保证转体结构的稳定,确保转体下的净空,不考虑偏心。
G=47000KN
⑶转体结构动摩擦力矩计算
转体结构球铰处动摩擦力产生的力矩M1
M1=2fGR/3=2×
0.05×
47000×
1.15=1801.67KNm
⑷平转牵引钢铰线束牵引力计算
考虑动摩擦力矩全部由两束牵引钢铰线索承受,则有平转牵引钢铰线索牵引力T1为:
T1=M1/D=1801.67/7.30=246.8KN
⑸转体结构静摩擦力矩计算
转体结构球铰处静摩擦力产生的力矩Mj
Mj=2f2GR2/3=2×
0.1×
1.15=3603.33KNm
⑹平转助推力计算
考虑动摩擦力矩与静摩擦力矩间的差值全部由上转盘撑脚处的两台助推千斤顶承受,则有助推力T2为:
T2=(Mj-M1)/D2=(3603.33-1801.67)/6.5=277.87KN
⑺牵引索钢铰线检算
①φ15.2-7牵引束钢铰线性质:
标准强度:
fytp=1860MPa
每束根数:
n=7
单根截面面积:
A=140mm2
钢铰线锚下控制应力:
fk=0.75fytp=1860MPa
②单束钢铰线容许拉力T1:
T1=nAfk=7×
140×
1395/1000=1367KN>246.8KN
安全系数K1:
K1=T/T1=1367/246.8=5.5。
满足要求。
根据计算采用:
牵引千斤顶:
2台1000KN连续千斤顶(考虑侧向风荷载对转体的阻力,设备有一定的储备);
则动力系数η1:
η1=T1/F1=277.18/1000=0.28满足要求。
助推千斤顶:
2台YCW100型千斤顶。
⑻惯性制动距离计算
在转体就位前,张拉千斤顶应停止牵引,全靠惯性转动就位,此时阻止整个转体继续转动的力量是下转盘对转体的动摩擦力,摩擦力对转盘中心的力矩的作用使梁体停转。
因梁端旋转线距离为39.3m,若梁体梁端以V=1.1m/min=0.028rad/min的速度转动时,其动能为W1:
W1=GV2/2=47000×
0.028×
0.028/2=18.424
在摩擦力矩作用下,设止动所需的转角为a,则摩擦力矩提供
W1=αM1
α=W1/M1=18.424/1801.67=0.01rad
则此时梁端中心差距为:
L=Rα=39.3×
0.01=0.39m
在止动阶段,当梁体中心线相差分别为0.39m时应停止牵引,利用惯性就位。
由于梁体转体重量与实际偏心距现都无法准确确定,故在转体称重后应根据转体实距偏心距再行调整。
4、转体时间计算:
转体角度为25°
,箱梁辐射最大半径为39m。
设计线速度为≤1.2m/min,再考虑箱梁的平稳和安全取线速度为1.0m/min。
梁端转体总弧长(25×
3.14159/180)×
39=17.00m
转体时间为:
17.00/1.0=17min。
五、转体施工的注意事项
1、球铰竖直度和转盘水平程度的控制:
球铰中钢轴的高程调整好以后,要求钢轴线为一铅直线,且确保下转盘周边高程处于同一水平面内,误差≤0.5mm,先用s3级水准仪对下球铰周边平面十字线的四点进行粗调,然后,用精度为0.1mm电子水平仪进行精确调整。
2、滑道偏差控制:
环道滑板设计为24mm厚钢板+5mm厚不锈钢板,撑脚底部固定10mm厚四氟滑板。
利用已浇注与承台砼中的定位钢支架精确定位钢板,并利用调节螺栓调整顶面标高、平整度。
使每块板高程误差≤1mm,高差≤0.2mm,然后安装第2块,要求同前。
滑道板接缝高差要求≤0.5mm,两块之间的高差≤0.4mm,直至全部装完。
装完后将整个滑道检测1遍,确保滑道任何位置高差≤1mm/2m达到要求后将下滑板固定,复测无误后进行混凝土浇筑。
为保证滑板下混凝土的密实度,要求混凝土具有良好的施工性能,并在下滑板预留排气孔。
环道钢板安装示意图
螺栓调整定位环道钢板大样图
环道定位支架工程图片
环道钢板调整安装图片
3、撑脚和滑到的间隙设置
撑脚不与滑道面接触,设置较小的间隙,一旦有侧倾则起支承作用。
一般要求此间隙为2~20mm,间隙越小对滑道面的高差要求越高我们按照撑脚与下滑道的间隙为15mm控制。
在转体前,为了防止重力对球铰、转盘钢板面的产生的变形作用,预留间隙采用钢板及四氟滑板填充,使其与承重系统一起承受结构自重,减少了磨盘钢板的受压比例,待转提前抽出。
4、球铰的球面摩擦力要求
上下转盘弧形接触面的钢板应打磨,为进一步减小摩擦力,可在钢板面设置抗压强度为100Mpa的聚四氟乙烯滑动片,再涂以二硫化铜或黄油四氟粉等润滑剂,以减小摩擦系数(一般在可控制在0.03~0.06之间)。
聚四氟乙烯滑动片安装完成后,保证其顶面位于同一球面上,误差≯1mm。
检查合格后,在球面上各聚四氟乙烯滑动片间涂抹黄油聚四氟乙烯粉,使黄油聚四氟乙烯粉均匀充满聚四氟乙烯滑动片之间的空间,并略高于聚四氟乙烯滑动片,保证其顶面有一层黄油聚四氟乙烯粉。
整个安装过程应保持球面清洁,严禁将杂物带至球面上。
将上球铰的两段销轴套管接好,用螺栓固定牢固。
将上球铰吊起,在凸球面上涂抹一层聚四氟乙烯粉,然后将上球铰对准中心销轴轻落至下球铰上,用倒链微调上球铰位置,使之水平并与下球铰外圈间隙一致,去除被挤出的多余黄油,并用宽胶带将上下球铰边缘的缝隙密封,防止杂物进入球铰摩擦部分。
球铰现场贴片
上球铰安装
5、启动阶段和转动时力矩的施加
尽可能的减小转动摩阻力和提高转动力矩是保证平转顺利实施的两个关键。
转动力可以是推力,也可以是拉力。
转动力施力点设置于设置于承台以外,采用连续式千斤顶,以获得较大的力臂和连续的动力。
推力由助推千斤顶施加,用于客服启动时的静摩擦力,但千斤顶行程短,转动过程中千斤顶安装的工作量又很大,为保证平转过程的连续性,所以采用采用连续式千斤顶和助推千斤顶相结合的方式进行。
6、转体平面位置就位控制
根据理论计算结果,距离设计轴线39cm位置,停止施加牵引力,靠惯性运动就位。
为了直观反映桥梁设计轴线情况,可在梁顶部用醒目油漆标出设计轴线,若两端梁体顶面标出的轴线呈同一直线,说明转体到位。
若梁体转动后未到设计轴线或转过,采用两台助推千斤顶在对称位置逐步顶推,直至到达设计轴线位置。
7、梁体侧倾、上仰及下挠纠偏
平面位置就位后,梁体可能会出现侧倾,纠偏采用350t千斤顶以下承台为反力支座施加竖向推力,顶推后使梁顶面前后、左右保持等高,然后采取支撑加固措施,撤除千斤顶。
【结语】根据刘房子特大桥主桥转体成功实施的施工实践,作者认为平转法体现出了安全可靠、实施快捷、造价低廉的特点。
在施工中,做好转体体系的三大系统的控制措施,将能确保安全稳妥的实施转体。
注:
文章内所有公式及图表请用PDF形式查看。