最新同济大学飞机装配整理Word文件下载.docx
《最新同济大学飞机装配整理Word文件下载.docx》由会员分享,可在线阅读,更多相关《最新同济大学飞机装配整理Word文件下载.docx(28页珍藏版)》请在冰豆网上搜索。
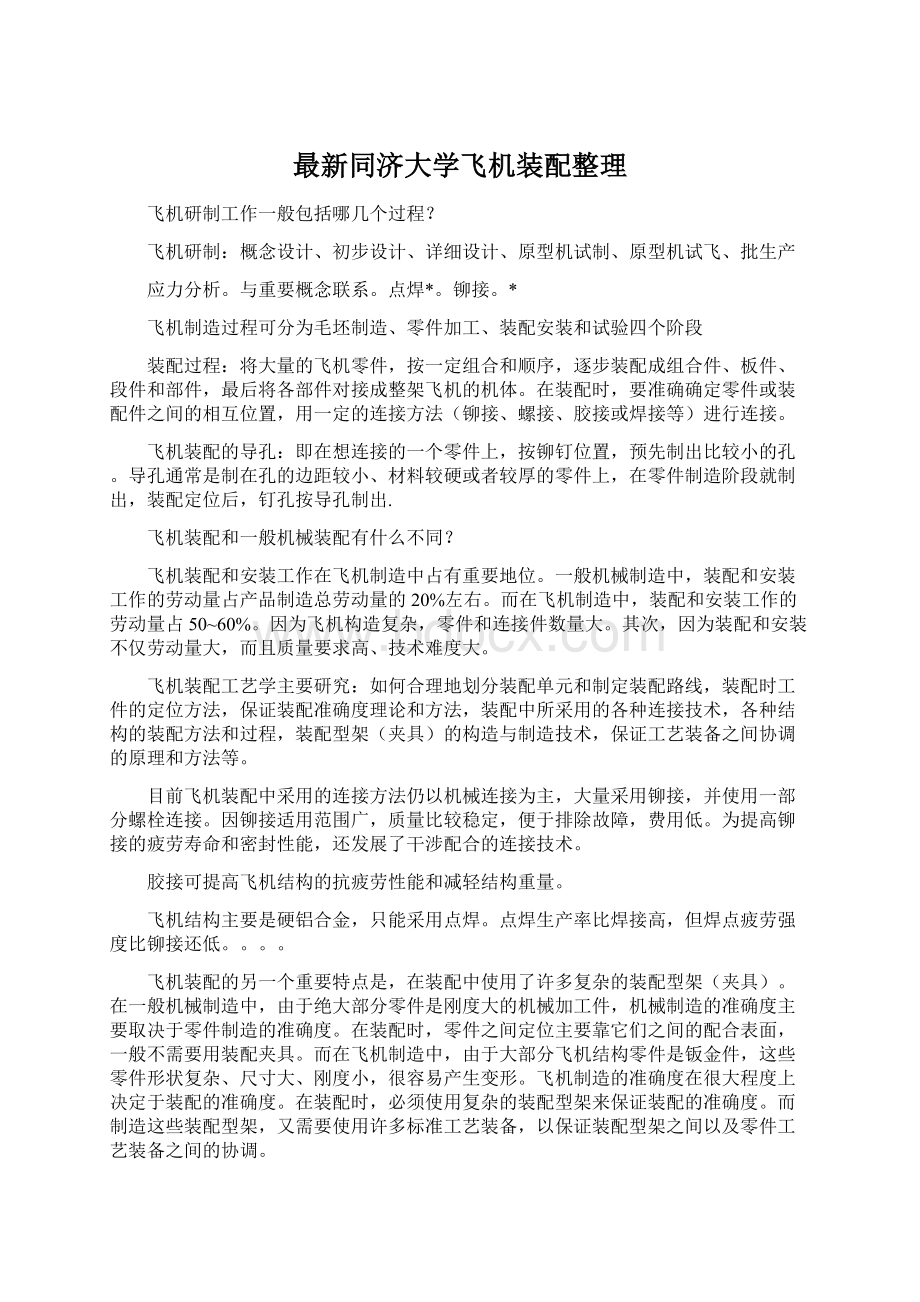
飞机装配过程一般是零件先装配成简单的组合件和板件,然后逐步地装配成比较复杂的段件和部件,最后将各部件对接成整架飞机。
根据飞机的结构和使用上的需要,飞机是由部件及可卸件组成的。
分离面:
工艺分离面、设计分离面
工艺分离面:
根据飞机装配需要由装配工艺员确定的分离面,特点:
多采用不可拆卸连接
设计分离面:
飞机各部分结构能沿一定的连接处分解的接合面统称分离面,如机翼与机身分离面,垂尾与方向舵的分离。
特点:
多采用可拆卸连接,以便于在使用和维护过程中迅速拆卸和重新安装
工艺分离面合理划分后有显著的技术经济效果。
部件划分为段件后:
(一)增加了平行装配工作面,可缩短装配周期
(二)减少了复杂的部件装配型架数量
(三)由于改善了装配工件的开敞性,因而提高装配质量
部件、钣金进一步划分为板件后,具有重要意义。
以铆接结构为例,结构划分为板件后;
一.为提高装配工作的机械化和自动化程度创造了条件
二.有利于提高连接质量
装配单元:
飞机结构分离面选定后,所确定的各个装配件,称为装配单元
装配单元的划分,主要考虑:
构造上的可能性与特殊要求;
有良好的开敞性与工作条件;
各装配单元应具有一定的刚度;
易于保证装配单元之间的相互协调;
减少部件总装工作量,以达到各装配阶段工作量的平衡,并简化型架结构。
第二节装配基准
在飞机装配过程中,使用哪两种装配基准,叙述每一种装配基准的装配过程和部件外形误差
两种装配的优缺点
以飞机骨架外形为基准:
首先将骨架在型架上定位好并进行铆接,使其具有一定的刚度,然后将蒙皮装上,并对蒙皮施加外力,使蒙皮与骨架铆接,其误差是从内向外积累的,故外形准确度差。
一般多用于低速飞机
最后的积累误差反映在部件外形上。
部件外形误差由以下几项误差积累而成:
一)骨架零件制造的外形误差
二)蒙皮的装配误差
三)蒙皮的厚度误差
四)蒙皮和骨架由于贴合不紧而产生的误差
五)装配连接的变形误差
以蒙皮外形为基准:
首先将蒙皮在型架(夹具)的外形卡板上定好位,再将骨架零件(或组件)贴靠到蒙皮上,并施加一定的压力使蒙皮贴于外形卡板上,之后将两半骨架连接起来。
这种方法的误差是由外向内积累的,最终靠骨架的连接而消除。
这种方法的外形准确度高,一般适用于高速飞机
误差积累是由外向内:
误差积累:
一).装配型架卡板的外形误差
二).蒙皮(或壁板)和卡板外形之间由于贴合不紧而产生的误差
三).装配连接的变形误差
以蒙皮内形为基准:
首先将蒙皮压紧在型架(夹具)的内托板(以蒙皮内形为托板的外形)上,再将骨架零件(一般为补偿件)装到蒙皮上,最后将骨架零件与骨架(或骨架零件)相连接,这种方法与以蒙皮外形为基准相比较而言,基本相似,只是其外形比前者多了一道误差(蒙皮厚度公差)国外广泛采用它来装配大型飞机的机身等部件。
第三节装配定位
定位要求。
各个定位方法。
型架
确定零件、组合件、板件、段件之间的相对位置,这就是装配定位
在装配工作中,对定位要求是:
一)保证定位符合图纸和技术条件所规定的准确度要求;
二)定位和固定要操作简单且可靠
三)作用的工艺装备简单,制造费用少
定位方法:
基准零件,划线,装配孔,坐标定位孔,基准定位孔,装配型架(夹具)定位
基准零件
划线:
适合于零件刚度大,位置准确度要求不高的部位
装配孔
坐标定位孔:
定位孔分别配置在型架和零件上二装配孔在装配的两个零件上
基准定位孔:
基准定位孔是配置在两个组合件板件或者锻件,而装配孔在两个零件上
装配型架(夹具)定位:
最基本的一种定位方法。
准确度取决于装配型架的准确度,保证装配准确度先保证装配型架的准确度。
一般机械产品的装配夹具是为了提高生产率,而飞机装配型架的主要功能是确保零件组件在空间相对正确位置。
零件定位、校正零件组件的空间位置的准确度。
大力推广安装定位孔定位可以大大简化装配型架,且改善型架内工作的工作通路。
第四节装配工艺过程设计
第二章飞机装配准确度
基本概念。
是非。
较清楚了解几个准确度。
定义画出图形。
判断路线联系程度。
尺寸链。
分类。
有关。
无关。
有关误差。
随机。
飞机装配准确度:
指两个飞机零件、组合件或部件装配后的实际儿何形状和尺寸相符合的程度.部件气动力外形准确度、部件内部组合件和零件的位置.准确度、部件间相对位置的准确度。
相符合的程度越高,则协调准确度越高,协调误差越小.
飞机装配中的二次定位:
二次定位指装配过程中,某些外形及接头己经装配好,而下一个装配阶段又在另一个夹具(型架)上再次定位,称二次定位。
在成批生产中个,为扩大装配工作面采用分散装配凉则,固在夹具定位时存在着大量的二次定位.
第一节基本概念
飞机装配准确度的意义
1.飞机外形的准确度很大程度上取决于飞机装配的准确度。
2.在装配之后要保证各种操纵机构的安装准确度和各运动机构之间的间隙,直接影响飞机的各种操纵性能。
3.飞机装配中,除了结构的连接质量,例如铆接和焊接质量会直技影响飞机结构强度和疲劳寿命以外,在零件制造和装甲时程中的残余应力也会也会影响结构的强度和疲劳寿命.
一.飞机装配准确度要求
飞机各项性能指标:
空气动力性能、各种操纵性能、结构强度和耐久性能等
残余应力包括零件加工和成形过程中产生的残余应力和在装配过程中产生的残余应力。
装配过程中产生的残余应力包括由于铆接和焊接时有变形而在结构中产生残余应力,以及由于零件之间或零件与装配夹具之间形状和尺寸不协调,通过强迫装配在结构中产生变形和残余应力。
残余应力的作用
残余压应力的存在可以提高结构的疲劳强度。
残余拉应力将降低结构的疲劳强度。
飞机装配中对残余应力的控制
1)限制在结构中存在的总的残余应力和由于强迫装配所产生的残余应力。
2)装配过程中采用合理的装配顺序和工艺措施,可以减少结构的变形和残余应力
飞机装配的准确度还会直接影响产品的互换性。
飞机装配准确度要求:
飞机空气动力外形的准确度,各部件之间对接的准确度,部件内各零件和组合件的位置准确度
对飞机准确度要求包括:
1.飞机外形准确度和外形表面光滑度
1.1外形准确度要求(部件实际切面外形相对理论切面外形的偏差).
不同型别的飞机,其外形误差要求是不同的,主要与飞机速度大小.各部什的功能和结构特点有关系.一般翼面部件比机身部件的外形要求高,翼面部科中前缘段又比后段的要求高。
1.2外形波纹度的要求(一定范甩内波高的差,即相邻两波峰与波谷的平均高度差与波长的比值。
部件沿横向和纵向气动外形均有波纹度要求)外形表面平滑度的要求
1.3外形表面平滑度要求
a)蒙皮口盖对对缝间隙阶差的偏差.顺气流和垂直气流方向的偏差有不同要求。
b)螺栓(钉)头、铆钉头、焊点相对蒙皮凸凹量偏差。
2.各部件之间对接的准确度:
主要形式是叉耳式和围框式接头
2.1机身各段的同轴度要求。
2.2机翼、尾段位置要求(上、下反角、后掠角、安装角的偏差,以及对称性偏差)
2.3操纵面位置要求(操纵面相对定翼面外形阶差、剪刀差、缝隙间隙的偏差.通常被称为操纵面的吻合性要求)
3.部件内各零件和组合件的位置准确度
基准轴线位置要求〔框轴线、翼肋轴线,梁轴线、长?
轴线的实际位置与理论位置的偏差,即框、肋、梁、长?
装配位置要求)
4、部件结构件的配合准确度
4.1不可卸零件间配合要求〔零件贴合面之间的间隙偏差)
4.2叉耳对接接头配合要求(螺栓孔和螺栓之间一般为无公称间隙的高精度配合)
a)沿耳宽方向叉耳之间的间隙偏差
b)对接孔的同轴度偏差
4.3围框式对接头配合要求
a)对接面之间的间隙偏差
5.部件功能性准确度要求
产品图样和设计技术条价所规定的装配技术要求(重最、重心、重最平衡、清洁度、密封性、接触电阻、表面保护、操纵性等)。
三.制造准确度和协调准确度
简述制造准确度和协调准确度的定义
制造准确度:
飞机零件、组合件或部件的实际形状和尺寸与飞机图纸上所定的公称尺寸相符合的程度
协调准确度:
两个相配合的零件、组合件或部件之间配合部分的实际形状尺寸相符合程度
(是通过模线、样板和立体标准工艺装备建立起相互联系的制造路线)
飞机制造中保证协调准确度的重要性
一般机械制造中,配合尺寸之间的协调准确度是通过独立地控制各零件和组合件的制造准确度达的到。
飞机制造中由于结构尺寸大,形状复杂.如果以它们本身更高的制造准确度来达到,在经济上既不合理.技术上又很困难.实际上。
在飞机制造中.零部件之间配合表面的形状和尺寸的协调准确度往往比它们本身的制造准确度要求史严格。
在飞机制造中首要的是保证协调准确度。
协调准确度获得的途径
是通过模线、样板和立体标准工艺装备建立起相互联系的制造路线。
零部件配合的协调误差只和非共有的环节有关.所以设法减少非公共环节的数量,并提高非公共环节的准确度,就可以达到比较高的协调准确度.
影响装配精度的各种误差分类:
1)与定位方法无关的误差
1.连接引起的变形误差
2.温度变化引起的变形误差
2)与定位有关的误差:
1.进入装配的零件,组合件的制造误差
2.装配夹具的误差
3.工件和装配夹具之间的协调误差
对协调准确度的要求:
1.工件与工件之间
2.工件与装配夹具之间
3.相关工艺装备之间
三.装配尺寸链:
尺寸链就是在零件或装配件上各零件表面及其轴线之间的一组尺寸(或角度)按一定次序首位相接形成的封闭的链。
描述装配件中各零件尺寸相互关系的尺寸链称为装配尺寸链
四.影响装配准确度的各种误差的分类:
1与定位方法无关的各种误差
1.1零组件制造误差,包括各定位面的尺寸误差
1.2装配夹具的误差
1.3工件和装配夹具的协调误差
2.与定位方法有关的各种误差
2.1由于连接引起的变形误差
2.2由于温度变化引起的变形误差.
五.随机误差的综合
1.极值法
2.概率法
第二节各种装配方法的装配度分析
一、在型架内以骨架外形为基准装配的准确度
1.装配夹具制造误差
2.骨架在装配夹具中的定位误差
3.蒙皮在骨架上的定位误差
4.蒙皮的厚度误差
5.装配过程中的变形误差
二、在型架内以蒙皮外形为基准装配的准确度
1.装配夹具的制造误差
2.蒙皮与装配夹具的协调误差
3.装配过程中的变形误差
三、按装配孔装配的准确度
1.基准零件的制造误差
2.其它各零件的制造误差(零件外形相对于坐标定位孔的误差)
2.1零件上装配孔的误斧
2.2零件外形误差
3.基准零件和其它零件的协调误差
4.蒙皮在骨架上的定位误差
5.蒙皮的厚度误差
6.装配过程中的变形误差
四、在夹其内按坐标定位孔装配的准确度
2.跨架零件的制造误差(零件外形相对于坐标定位孔的误差)
2.1零件上坐标定位孔位置误差.
3.骨架零件和装配夹具的坐标孔之间的协调误差
4.蒙皮在骨架卜的定位误差
五、按基准定位孔装配的准确度
2.基准组合件在装配夹具中的定位误差(主要取决于从准组合什装配夹具与产品装配夹具之间的协调误差)
3.其它组合件按基准定位孔在基准组合件上定位的误差
3.1其它组合件和爷准组合件之间基准定位孔的协调误差
3.2组合件外形相对于组合件上基准定位孔的误差
4.蒙皮的制造误差
六、小结
决定产品最后形状和尺寸准确度的各种误差中有系统误差和偶然误差。
装配夹具的制造误差可属于系统误差.而装配误差尺寸链中的大多数是属于偶然误差,如零件制造误差,定位误筹和变形误差。
定位误差取决于装配夹具定位面和有关零件表面之间形状和尺寸的协调误差。
在装配时一般通过装配夹具上的夹紧件施加夹紧力.使定位误差显著减小.所以定位误差是在装配夹具和零件之间协调的基础上乘以夹紧系数.
装配过程中的变形误差对装配们最后的准确度有很大影响。
由于变形误差是山于结构或工艺因素引起的,其大小很难通过理论分析和计算得出,只能根据经验给出一个近似值.
第三节装配误差中各环节的误差
第四节提高装配准配度的补偿方法
一、互换性概念
是指零件和装配件的儿何形状、尺寸及物理机械性能在一定的误差范围以内,在装配时不需要经过修配、补充加工或调整,在装配后完全能满足规定的技术要求。
二、采用补偿结构的原因
对一些复杂结构中准确度要求很高的某些重要尺寸,为了保证装配后能达到所要求的准确度,过分提高零件和装配件的制造准确度,有时经济上是不合理的.在技术上有时也难以做到。
因此在部件装配中采用各种补偿方法.以使最后达到所要求的准确度.
三、补偿方法
所谓补偿方法就是零件或装配件某些准确度要求高的尺寸,在装配时或装配后.通过修限、补充加工或调整,部分消除零件制造和装配误差,最后达到所要求的准确度。
四、补偿方法分类
一类是从工艺方面采取的补偿措施,称为工艺补偿;
另一类是从结构设计方面采取的补偿措施,称为设计补偿.
1、工艺补偿方法
1)装配时相互修配(修配补偿)
在零件或装配阶段难以达到给定的要求时,可以在装配中采用相互修配的方法来达到.
例如飞机蒙皮对缝间隙
修配工作一般是手工操作,在相互修配时。
有时要反复试装和修配。
不具有互换性
2)装配后精加工(余量补偿)
余量补偿的应用范围:
1)装配过程中由于零件制造误差、装配定位误差而累积形成的闭环尺寸误差.在该处安装的零件上箭要留出余量,以补偿误差积累.
2)在装配中有些准确度要求高的配合尺寸,在零件加工时用一般加工方法难以达到要求时,必须在装配中采用修配方法达到技术要求,此时需要在一个零件上留有余量进行补偿。
例如叉耳接头螺栓孔的位置尺寸推确度和配合精度要求都较高.各叉耳接头上的螺栓孔均留有一定的加工余量,在部件装配好后再对接头螺栓孔进行精加工,以消除零件加工和装配过程中产生的积累误差。
3)为消除装配中的定位误差和变形误差以及零件制造误差,达到组件或部件的协调互换,需要在对接面、对接孔或叉耳接头孔,叉耳侧面等处留余量,经过精加工,达到协调或互换要求.
4)有些部位,通过一定的协调方法或正常提高零件的制造准确度,使可达到装配技术要求,但在飞机研制、试制或批量不大时,出于考虑经济性.而留余量.通过修配达到其协调要求。
注意:
装配后精加工一般是在专用的精加工设备上进行。
适用:
在飞机装配中,对准确度要求较高的重要尺寸,一般为封闭尺寸.因零件加工和装配过程中误差积累的结果,在装配后达不到所要求的准确度。
用修配法劳动最大,且达不到互换件要求.采用精加工的工艺补偿方法。
工艺余量的确定原则
1)余量补偿是飞机装配中必不可少的一种手段,但会增加工作量并延长装配周期.因此.必须对不同的装配方法和各种措施进行综合技术经济分析后,才采用余量补偿.
2)采用余量补偿方法,不得影响产品的性能.如强度、重量、表向保护等。
3)合理确定留余量的零件和余量部位.以方便修配或便于机械化施工.
4)合理确定余量大小,保证以最小劳动量达到准确度要求。
5)修配工作量与飞机结构设计的工艺性有很大关系.要配合利用.
飞机装配中常用的补偿方法有哪几种?
补偿方法就是零件、组合件或部件的某些尺寸在装配时可进行加工或者调整,这可以部分抵消零件制造和装配的误差,最后能够达到技术条件所规定的准确度要求
一.工艺补偿方法:
装配时相互修配、装配后精加工
1.装配时相互修配
2.装配后精加工
二.设计补偿方法:
1.垫片补偿
2.间隙补偿
3.连接补偿件
4.可调补偿件
第三章铆接和铆接结构装配
优缺点。
各种对比。
工具设备不考
铆接的优点:
1.连接强度较稳定可靠
2.容易检查和排除故障
3.操作工艺易掌握
4.使用工具机动灵活、简单、价廉
5.适用于较复杂的结构的连接
6.适用于各种不同材料之间的连接
铆接的缺点
1.增加了结构重量
2.降低了强度
3.容易引起变形、蒙皮表面不够平滑
4.普通铆接疲劳强度低
5.普通铆接密封性能差
6.钻铆劳动强度大、生产效率低、劳动条件差
铆接种类
普通铆接
凸头铆钉铆接
埋头铆钉铆接
密封铆接
自密封铆钉铆接
缝内密封
缝外密封
表面密封
干涉铆接
无头铆钉铆接
特种铆接
单面铆接
环槽铆钉铆接
钛合金的铆接
第一节普通铆接
一.钻孔及锪窝huò
1.对铆钉孔的要求
1)铆钉孔直径>
铆钉杆直径0.1-0.3mm
原因:
便于放铆钉,钉杆较好地填满钉孔
2)铆钉孔的粗糙度RE值不大于6.3
3)铆钉孔不允许有棱角、破边和裂纹
4)铆钉孔的圆度、垂直度应在铆钉孔直径继续偏差内
5)铆钉孔不允许有毛刺
2.确定铆钉孔的位置
确定钉孔位置的方法:
1.按画线钻孔:
准确度低、效率低,但简易可行,适用于新机试制
2.按导孔钻孔:
工作效率高,常用于成批生产
3.按钻模钻孔:
能保证孔位置准确,且钻模上的导套有导向作用,还能保证孔的垂直度
3.埋头窝不能过深,如果过深,蒙皮受力后,会使铆钉松动,降低连接强度。
此外,埋头窝的轴线应垂直于工件表面,以保证铆接后表面平整。
二.制孔工具设备
三.铆接
普通铆接包括哪几种形式?
每一种形式有何优点或缺点?
(包括锤铆和压铆)
普通铆接缺点:
增加结构重量;
降低强度;
容易引起变形;
疲劳强度低,密封性差
凸头铆钉铆接基本工序:
定孔位、制孔、放铆钉、铆接
埋头铆钉铆接基本工序:
定孔位、制孔、制窝、放铆钉、铆接
1.铆钉及铆钉长度的选择
2.锤铆:
分正铆和反铆
正铆优点:
在铆接埋头铆钉时表面质量好,因为铆枪直接打在钉杆上,蒙皮不受锤击。
缺点是需要较重的顶铁才能在铆接才能在铆接时顶住铆钉,劳动强度大,另外铆枪必须置在工件内部,使用范围受到限制,所以一般是在铆接蒙皮表面时才用正铆。
反铆优点是,顶铁重量轻,且在反铆过程中,部分锤击力之间打在钉头周围的零件表面上,能够促使工件贴紧,故在铆接骨架结构时一般都用反铆。
(1.铆接质量不稳定;
2.铆接变形大;
3.劳动强度大,噪音大,振动大,劳动条件差;
4.劳动生产率低。
)
铆枪存在问题:
1)铆接质量不稳定
2)铆接变形大
3)劳动强度大
4)劳动生产率低
3.压铆
压铆是用静压力镦粗铆钉杆,形成镦头
压铆有下列优点:
1)铆接质量稳定,与操作者技术水平关系较小,表面质量好
2)劳动生产率高
3)工件变形较小
4)工人的劳动条件好
4.压铆机
第二节密封铆接
材料。
工艺期限。
型号不考
密封铆接包括哪几种密封形式
一.密封形式:
紧固件自身密封、缝内密封、缝外密封、表面密封
表格见课本
1缝内密封
2缝外密封
3表面密封
4紧固件自身密封
二.密封材料
密封胶配好后的工艺期限要宽:
按工艺期限分为
活性期
施工期
初始硫化期
2.密封胶在缝外填角、铆钉头堆胶时,要有良好的堆砌性能。
3.有较长的储存期
三.密封试验
第三节无头铆钉铆接
一.概述
埋头窝采用这种形状有两个原因:
1.既保证铆钉有一定的连接强度,埋头窝的锥度又要尽量小,这样易于填满埋头窝,保证密封性能和干涉配合均匀;
2.可以减少压铆力,否则压铆力容易出现裂纹,且易引起工件变形。
叙述无头铆钉的优点,影响无头铆钉干涉量的因素有哪几种?
采用无头铆钉是为了在自动铆接机输送铆钉方便,其优点还有:
1.铆接后沿铆钉杆全长可形成较均匀的干涉配合,提高了连接件的疲劳寿命。
钉孔和钉杆之间的干涉配合,在钉孔和钉杆之间产生了一定的内应力,降低了最大应力与最小应力之间的差值。
(干涉量,相对干涉量)
2.采用无头铆钉干涉配合的铆接,能够可靠地保证铆钉自身的密封性。
影响干涉量的因素:
干涉量太小,不能太大,也不能太小,太小不起作用,太大产生的预应力引起结构变形,对于铝合金,一般干涉量取1.5~3.0%
1.铆接前铆钉的外伸量。
钉杆越长,干涉量越大。
2.钉孔间隙和埋头窝深度。
间隙大、埋头窝深,干涉量相应减少;
间隙太小,则装订困难。
3.铆模形状。
不宜用平铆模,而采用凹铆模。
二.干涉配合对疲劳寿命的影响
最佳干涉量产生的预应力:
1.使应力的变化幅度减少到最少,同时减少平均应力
2.由于干涉量产生的预应力,不会引起结构变形
3.预应力小于产生应力腐蚀的临界值;
4.干涉量大于孔切削刀痕的深度
三.影响干涉量的因素
无头铆钉铆接后所获得的干涉量的大小和均匀程度,与以下工艺参数有关:
1.铆接前钉与孔的间隙和埋头窝深度
2.铆接前铆钉的外伸量
3.铆模形状
必考。
干涉。
为什么能提高