有关水电站蜗壳安装焊接的常见缺陷讲解讲解Word格式.docx
《有关水电站蜗壳安装焊接的常见缺陷讲解讲解Word格式.docx》由会员分享,可在线阅读,更多相关《有关水电站蜗壳安装焊接的常见缺陷讲解讲解Word格式.docx(8页珍藏版)》请在冰豆网上搜索。
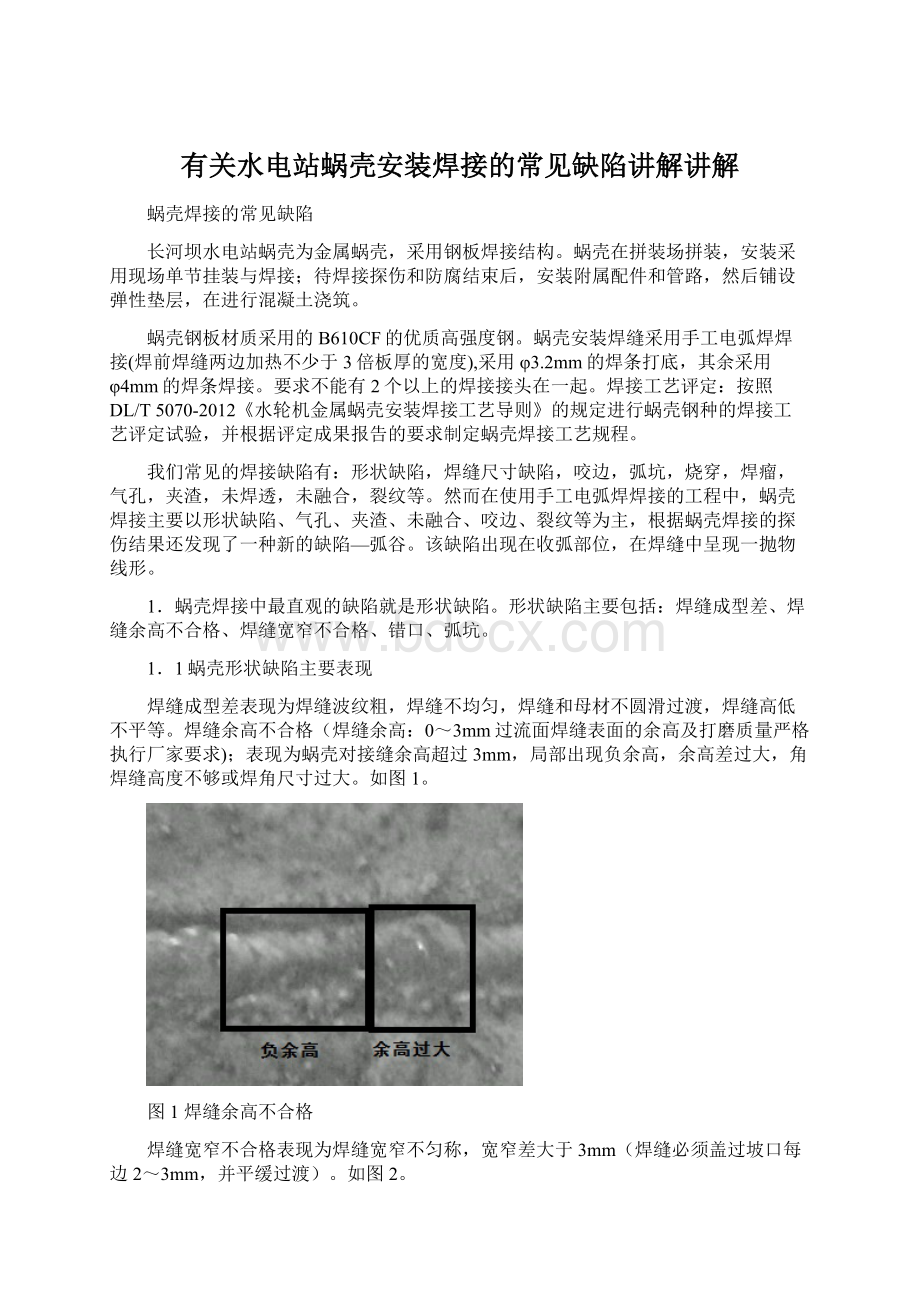
1.1蜗壳形状缺陷主要表现
焊缝成型差表现为焊缝波纹粗,焊缝不均匀,焊缝和母材不圆滑过渡,焊缝高低不平等。
焊缝余高不合格(焊缝余高:
0~3mm过流面焊缝表面的余高及打磨质量严格执行厂家要求);
表现为蜗壳对接缝余高超过3mm,局部出现负余高,余高差过大,角焊缝高度不够或焊角尺寸过大。
如图1。
图1焊缝余高不合格
焊缝宽窄不合格表现为焊缝宽窄不匀称,宽窄差大于3mm(焊缝必须盖过坡口每边2~3mm,并平缓过渡)。
如图2。
图2焊缝宽窄不合格
错口主要表现为焊缝两边母材不在同一平面上,错口量大于母材厚度10%或大于3mm。
如图3。
图4焊缝错口过大
弧坑主要表现为焊接收弧过程中形成表面凹坑,并伴随有表面气孔和夹渣。
如图5。
图5焊缝表面的弧坑
这些形状缺陷在我可焊接中最常见,影响外观质量和美观度。
1.2蜗壳焊接产生形状缺陷的原因
产生焊接成型差和焊缝余高不合格的原因是破口开设不当,装配间隙不均匀,电流过大或过小,焊接速度过大或过小,焊条摆动幅度过大或过小,焊条施焊角度选择不当。
焊缝宽窄不合格除了以上原因还有可能是因为焊接位置困难,妨碍焊工人员施焊。
错口产生的原因是因为焊缝两边母材对口不合格要求,焊工在对口不合适的情况下点固和焊接。
弧坑产生是因为焊接熔池不饱满收弧,停焊。
焊工对收弧情况判断不够,停弧时间把握不准。
1.3蜗壳焊接形状缺陷的防止
在蜗壳焊接中消除形状缺陷可以采取以下办法:
首先焊工必须熟悉图纸要求,保证焊缝表面干净无油污等。
其次焊工根据焊接位置和焊缝分类不同采取不同的操作技能要求,选择合适的电流参数和施焊角度。
第三焊工还要提高责任心,熟悉焊接场地。
对口过程中使用必要的测量工具(要求坡口间隙为2~4mm)。
对对口不合要求的不能点焊。
最后对已经形成的弧坑进行打磨补焊处理。
2.蜗壳焊接常见的气孔缺陷
在蜗壳焊接中出现的最多的缺陷就是气孔,气孔分表面和内部气孔,内部气孔对焊接质量影响最大,现在已内部气孔来说明蜗壳焊接的气孔缺陷。
气孔的产生主要来源是H2(氢气)和CO(CO是一氧化碳分子
Co的话就是钴元素
)。
而这些气孔多出现在打底焊缝中。
2.1蜗壳焊缝气孔缺陷的表现
其形状是沿焊缝柱状晶结晶方向的柱状气孔,如图6。
图6柱状气孔
打底焊层中内部和外部的的柱状气孔形状也有所不同,如图
7。
图7打底焊缝表层柱状气孔
柱状气孔绝大部分有成人字形排布的特征而且这种柱状气孔有时还会与夹渣混合在一起,如图8。
图8气孔与夹渣混合
这些气孔严重影响着蜗壳焊接质量。
当X射线检测出焊缝中的柱状气孔时,只能用炭弧气刨刨去气孔缺陷,再进行补焊来解决。
这种缺陷靠工艺是无法解决的。
为什么会出现这两种气孔那?
这主要是因为蜗壳采用的是B610CF钢,含碳量很高,而Si,Mn(Si就是硅Mn锰)等脱氧元素几乎没有,碳元素经过高温反应而产生CO,水经焊接高温产生H2。
2.2蜗壳焊缝中气孔的防止
现在怎样防止这种缺陷就很明了了。
在焊接前对破口及破口两边至少30mm-50mm的边缘进行打磨,完全清楚破口内外的油污、油漆、氧化皮、水分等杂质,使其符合焊接要求。
而且焊接的焊条(E6015-G)必须按要求进行烘焙350℃1~2小时,焊接过程中进行保温(100~150℃),确保没有超标的水分。
还有焊接过程中严格控制焊层温度(不超过220℃)。
这样不但可以减少气孔的产生,也可以减少如图8所示的气孔与夹渣同时出现。
3.在蜗壳焊接中仅次于气孔缺陷的是夹渣
焊后残留在焊缝中的熔渣称为夹渣。
夹杂对焊缝的性能影响比较大。
因夹杂多数呈不规则状,会降低焊缝的塑性和韧性,其尖角会引起很大的应力集中,尖角顶点常导致裂纹产生。
3.1蜗壳焊缝中夹渣的产生和表现
蜗壳焊接夹渣缺陷的产生主要有两方面的原因。
3.1.1母材和焊接材料的原因,蜗壳母材和焊接材料的纯度对夹渣的影响表现为:
针形氧化物和硫磷化物,这些夹渣会使焊缝金属变脆,降低力学性能。
这是因为蜗壳焊接是在没有保护气的情况下的强氧化气氛中焊接,由于焊接化学冶金系统的不平衡性,使焊接过程中脱氧不足或不完全造成。
这种氧化夹杂物主要分布在焊缝柱状晶晶内也有分布在晶界的,由于氧化夹杂物的熔点比铁的低,所以在焊缝冷却过程中聚合成球状,形成球状氧化物。
如图9。
图9焊缝中球状氧化物
同时在焊接时,由于空气的侵入,会使焊缝即增氮又增氧。
这样,由于氮、氧碳和金属的复合化合物熔点偏高形成夹杂物。
焊缝中的这种夹杂物在蜗壳的多层多道焊热循环的作用下,会从打底层焊道向上层焊道发展聚合成为夹渣。
如图10。
图10焊缝中的夹渣
磷硫化物有很强的脆化作用,严重降低焊缝的力学性能。
3.1.2焊接工艺原因,焊接电流太小,焊渣与液态金属分不开;
焊接速度过快熔渣来不及上浮;
蜗壳多层焊接时对焊口清理不干净;
运条角度不正确。
3.2蜗壳焊缝中夹杂的防止
首先,按照厂家《焊接工艺指导书》和DL/T5070-2012《水轮机金属蜗壳安装焊接工艺导则》的规定选择正确焊接材料;
采用适当的焊接参数,适当地增大焊接电流(130~190Ma),必要时把电弧缩短,并增加电弧停留时间,使熔化金属和熔渣得到充分加热;
根据熔化情况,随时调整焊条角度和运条方法,使熔渣能上浮到铁水表面;
降低熔渣的熔点和粘度,防止夹渣产生。
其次,焊前将焊缝及两边至少30mm-50mm的边缘充分打磨,将焊缝中的氧化皮铁渣等其他杂物去除,如图11所示的焊缝很可能会产生大的夹杂缺陷。
图11焊缝未清理干净
将坡口及焊层间的熔渣清理干净,将凹凸处铲平。
4.蜗壳焊接的未融合缺陷
未融合是蜗壳焊接中很常见的一种缺陷,是指母材和焊缝金属,焊层之间的焊缝金属未融合的现象,即母材和焊缝金属,各焊层之间存在间隙。
4.1蜗壳焊接未融合产生的原因
蜗壳焊接未融合产生是因为焊接线能量过小,焊接速度过快或者操作手法不当。
4.2蜗壳焊接未融合缺陷的防治措施
适当增加焊接电流,增大焊接线能量;
适当降低焊接速度;
熟练焊接技能,操作手法适当;
加强练习,增强焊工责任心;
针对不同的焊接母材,焊材,采取不同的消除未融合的焊接措施。
5.蜗壳焊接的咬边缺陷。
焊缝和母材融合不好,出现沟槽,深度大于0.5mm,总长度大于焊缝的10%或大于验收标准要求的长度。
5.1蜗壳焊接咬边缺陷产生的原因
焊接线能量过大,电弧过长,焊条角度不当,焊条送进速度不合适都是产生咬边的原因。
5.2防止咬边缺陷产生的措施
根据焊接位置和焊接规范的要求,选择合适的焊接参数(电流不超过190A);
控制电弧长度,尽量使用短弧焊接;
焊条送进速度和焊接参数协调;
主要焊缝边缘和母材融合时的焊条角度;
对检查中发现的咬边现象,进行打磨,补焊处理,使之符合焊接标准;
加强焊工管理,增强焊工责任心。
6.蜗壳焊缝中危害最大的裂纹缺陷
裂纹分表面裂纹很内部裂纹,内部裂纹对焊接性能影响远远比表面裂纹大,现在以内部裂纹来说明蜗壳焊接裂纹缺陷。
在蜗壳焊接中裂纹出现的几率比较低,但在蜗壳组装、焊接、后热处理等工序控制不当时会出现冷裂纹和再热裂纹。
因为蜗壳本身采用的是高强钢焊接。
而且在焊接前都要经过预热,预热温度根据板材厚度决定。
焊接的冷裂纹主要在屈服极限大于300MPa的低合金钢和高强度钢中产生。
钢材的强度越高,焊接产生冷裂纹的可能性越大。
B610CF的再热敏感温度为600℃。
再热次数和温度越高裂纹产生倾向也越大。
6.1蜗壳焊接裂纹产生的原因和表现
6.1.1冷裂纹
蜗壳在不利的条件下焊接时,焊接熔池中溶解了较多的氢,焊缝金属快速冷却后,大部分氢快速过饱和溶剂与焊缝金属中。
在焊接残余应力作用下,氢逐渐向产生应力与应变集中的热影响区扩散,并在某些微区聚集。
而低合金钢热影响区又往往存在马氏体淬硬组织,他的塑性变形能力很低。
当氢的浓度达到某一临界值时,变脆的金属即使是微小的应变也经受不起,而在残余应力的作用下就会开裂。
危险的是这些开裂面会进一步扩展,而且在裂纹的端部会有氢凝聚导致新的开裂,最终发展成宏观裂纹,称为氢致裂纹。
冷裂纹是一种最危险的缺陷,具有延迟性。
有的甚至在焊缝无损探伤后才形成,而造成不可弥补的漏检。
如图12。
图12氢致冷裂纹
6.1.2再热裂纹
由于蜗壳焊接中Mo(钼)、V(钒)、Ti(钛)、Nb(铌)这些元素的碳、氧化合物经高于1300℃的焊接热循环而固溶,在焊后快速冷却时来不及充分析出,但在SR(锶)处理后在晶内沉淀析出,使晶内强化。
应力松弛引起的塑性变形优先在晶界发生,在拘束应力作用下产生再热裂纹。
蜗壳焊接接头存在较大的拘束应力和残余应力,这是产生再热裂纹的主要原因。
6.2蜗壳焊接裂纹的防止
焊前对蜗壳焊缝区进行预热(板材厚度25~30mm预热温度为60~80℃,板材厚度>
30~38mm预热温度为80~100℃);
焊后控制近缝区的冷却速度,使之不易形成淬硬组织;
建立低氢的焊接条件(使用国产低氢型高强钢焊条)等可以减少冷裂纹。
在蜗壳施工过程中合理的安排组装和焊接顺序(管节之间的环缝焊接→凑合节纵缝焊接→凑合节环缝焊接(凑合节有两条安装环缝;
焊接顺序是先焊接其中的第一条环缝,第一条环缝焊接完成后再焊接第二条环缝)→蝶形边焊接→蜗壳与钢管之间的环缝焊接),减少接头拘束度,防止咬边,未焊透,未融合等缺陷;
必要时消减焊缝余高来减少应力集中;
每条焊缝一次性完成等可以减少再热裂纹。
其次可适当的改变工艺条件。
7.在蜗壳焊接中除了上面所说的焊接缺陷,还通过对X射线探伤结果的观察,还发现一中新型的焊接缺陷—弧谷,这里所说的弧谷不是焊缝表面的弧坑,它是存在焊缝与母材边沿相接处的。
该缺陷都出现在收弧的位置,在焊缝中有意抛物线型的阴影。
如图13。
图13 弧谷
7.1蜗壳焊接中弧谷产生的原因
电弧焊的熔池呈半椭球形状,焊接时熔池内的金属液体在电弧吹力作用下焊条前方的金属液体由椭球底部向前运动,沿母材熔深边缘向上,然后向中心运动。
然而,焊接工艺对焊接电压、电流和提前角都有上限和下限值,而上下限之间有一个最佳点,如果焊工使电压和电流都处在上限值,而提前角处在下限值,这时熔池温度增高,金属液体流动速度加快,把母材熔化冲刷成一个窄而神的抛物面空间,当电流停止时,熔池前方的液体因提前角小又自然流入弧坑,前沿金属一面冷却,不能把弧谷填满,即使能填满也不能熔化母材而结合成一体,所以形成了抛物面型气罐。
7.2弧谷产生的防止
首先,把电压、电流和提前角处于最佳值。
操作时只要把三者调到最佳点,收弧就不会产生弧谷。
大多数弧谷深度在5mm左右,与裂纹一样产生危害性,所以也应该进行返修。
蜗壳焊接完毕要经过焊接检验,超标缺陷要进行返修。
同一部位焊缝缺陷返修次数一般不应超过两次,特殊情况下超过两炊以上的焊缝返修处理应报经施工现场监理工程师批准,并做好记录,详细记录焊缝的编号、缺陷的位置、长度、性质等,并分析缺陷产生的原因及返修处理结果。