9000kvA矿热炉硅锰合金冶炼工作标准Word文档下载推荐.docx
《9000kvA矿热炉硅锰合金冶炼工作标准Word文档下载推荐.docx》由会员分享,可在线阅读,更多相关《9000kvA矿热炉硅锰合金冶炼工作标准Word文档下载推荐.docx(26页珍藏版)》请在冰豆网上搜索。
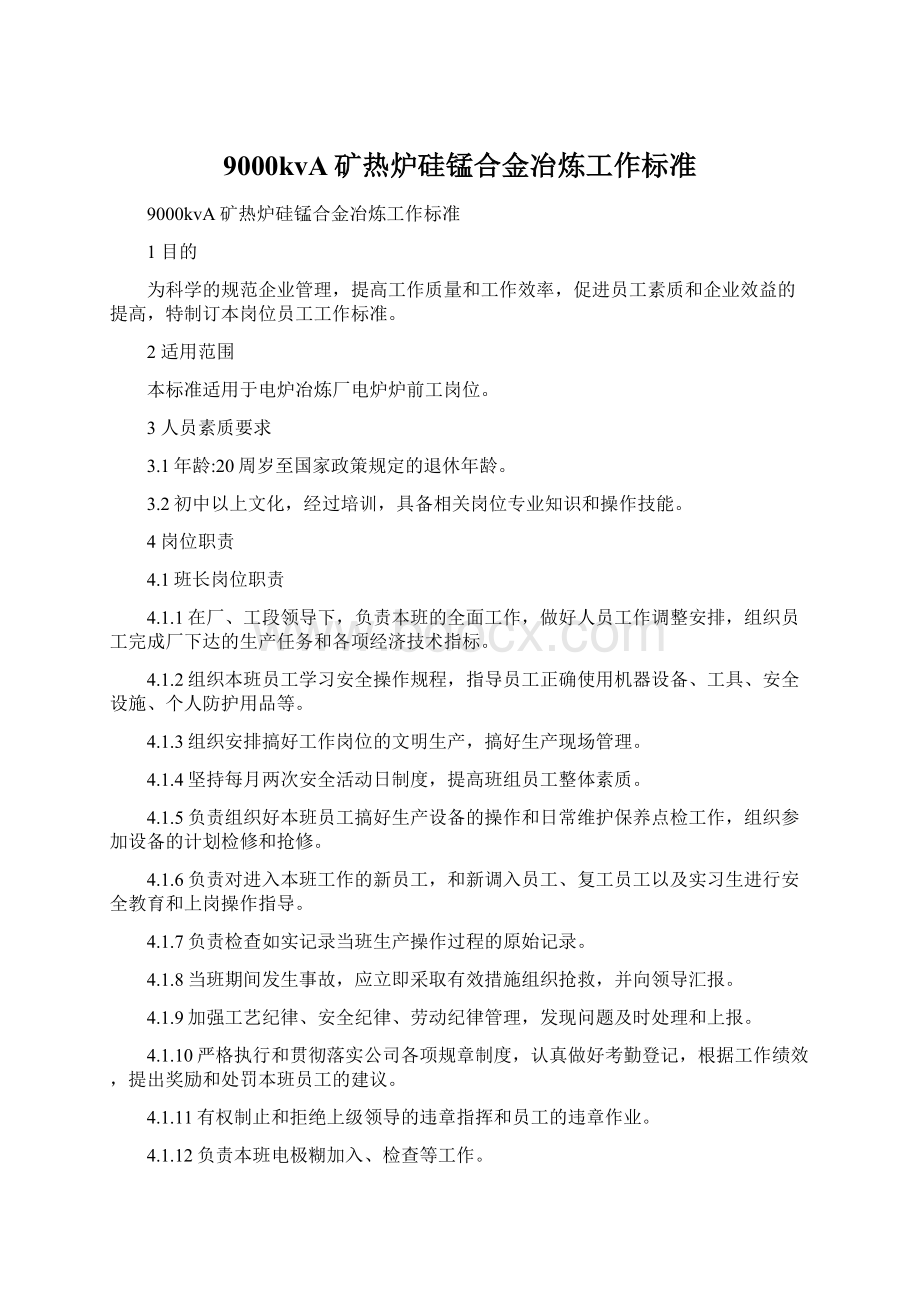
5.1.7负责本班组公用劳保用品、安全用具、安全资料、常用危险品的领用和保管。
5.1.8负责及时了解和上报班组发生的各类生产事故,积极组织抢救事故,保护好重大事故现场,参加和协助上级领导对本班组发生的各类生产事故进行调查分析,认真组织落实事故防范措施。
5.1.9认真做好班组安全管理台帐,总结研究安全生产工作,积极推行安全生产先进技术和经验。
5.1.10副班长协助班长抓好本班组安全生产工作,班长不在时,全面履行班长安全职责。
5.2班员岗位安全职责
5.2.1认真学习和遵守国家安全生产法规和公司及本单位制订的各项安全生产规章制度、安全操作规程。
对本人负责操作的设备、备件、安全工(用)具及自身安全负责。
5.2.2努力学习钻研安全生产技术知识,积极参加各种安全活动,做好新上岗员工的传、帮、带工作。
5.2.3参加安全生产管理,互相监督,制止他人违章作业,有权拒绝违章指挥。
主动提出改进安全生产的合理化建议和意见。
5.2.4按规定维护和正确使用各种安全装置和劳动保护用品、用具,严格执行岗位危险源(点)控制管理规定。
精心操作,做好作业记录。
5.2.5作业前认真做好安全检查和危险因素预测,积极采取事故防范措施,发现异常情况及时处理和报告。
5.2.6参加本岗位计划检修安全措施的制订,并认真严格执行。
负责外单位(岗位)检修人员在本岗位检修作业场所的安全指导和采取安全保护措施。
5.2.7发现险情和事故,要果断处理和立即向领导报告。
积极抢救事故并保护好现场,做好记录。
参加本岗位发生的各类生产事故分析会,认真落实事故防范措施。
5.2.8严格执行设备点检制度,加强设备维护,保持作业场所整洁,搞好文明生产,完成领导分配的安全生产工作任务。
6岗位交接班规定
6.1接班人员须提前10分钟到达生产岗位,穿戴好劳保用品,做好接班准备。
6.2.交接班必须做到“五不走”:
6.2.1安全生产工作、设备运转情况、操作情况、工具是否齐全,有无损坏、存在问题和上级指示以及通知事项未交清,交班人不能走;
6.2.2凡当班发生的设备及生产事故应由当班人员负责及时处理,并向接班人员详细说明事故情况,不得隐瞒,如特殊情况当班处理不了或者无法处理完时,应由交接班班长协商,共同处理或经接班的班长同意,可交给下一班继续处理,未交接落实好,交班人不能走;
6.2.3各班做好岗位卫生责任区的现场环境清洁卫生工作,现场不整洁,交班人不能走;
6.2.4接班人员未到岗位之前,交班人不能走,并及时向上一级领导请示汇报;
6.2.5凡设立交接班薄或记录报表的岗位,交接班的人员要签字留名,记录未交清,交班人不能走。
7岗位技术操作规程
7.1生产工艺操作规程
7.1.1产品技术条件:
7.1.1.1牌号和化学成份
7.1.1.1.1硅锰合金产品牌号和化学成份按国家标准GBT4008—1996《硅锰合金》中技术要求控制,其化学成份见下表。
牌号
化学成分(%)
Mn
Si
C
P
S
Ⅰ
Ⅱ
Ⅲ
不大于
FeMn64Si27
60.0~67.0
25.0~28.0
0.5
0.10
0.15
0.25
0.04
FeMn67Si23
63.0~70.0
22.0~25.0
0.7
FeMn68Si22
65.0~72.0
20.0~23.0
1.2
FeMn64Si23
20.0~25.0
FeMn68Si18
17.0~20.0
1.8
FeMn64Si18
FeMn68Si16
14.0~17.0
2.5
FeMn64Si16
0.20
0.30
0.05
注:
硫为保证元素,其余均为必测元素。
7.1.1.1.2需方对化学成份有特殊要求,可另行商定。
7.1.2冶炼原理:
硅锰合金冶炼,从其根本上来说就是在适当的高温下,利用适当的还原剂还原炉料中的锰、硅的氧化物的过程。
入炉原料中锰、铁的高价氧化物在电炉的高温条件下,受热分解或被CO还原成低价氧化物:
MnO2→Mn2O3→Mn3O4→MnO
Fe2O3→Fe3O4→FeO
由于炉料中SiO2较高,MnO与SiO2结合成硅酸盐:
MnO+SiO2=MnSiO3
2MnO+SiO2=Mn2SiO4
因此,锰硅合金生产过程的还原反应,主要是炉渣中液态硅酸盐与碳质还原剂的反应。
主要反应有:
MnO·
SiO2+4/3C=1/3Mn3C+SiO2+CO
SiO2+2C=Si+2CO
1/3Mn3C+Si=MnSi+1/3C
总反应议程式:
MnO·
SiO2+3C=MnSi+3CO
7.1.3原料技术条件:
7.1.3.1入炉原料的化学成份见桂康公司颁发的《桂林康密劳铁合金有限公司原燃辅料管理制度》中“硅锰合金”原料要求。
7.1.3.2入炉原料的粒度要求:
7.1.3.2.1锰矿石及富锰渣:
粒度5~60mm,﹤5mm的粉末≤8﹪,≥60mm块矿≤10%。
7.1.3.2.2焦炭:
粒度5~25mm,﹤5mm的粉末≤8﹪,>25mm焦丁≤5﹪。
7.1.3.2.3硅石:
粒度5~40mm,〈5mm的粉末≤8﹪,不得带有泥土及其它夹杂物。
7.1.3.2.4白云石:
粒度10~40mm,﹤5mm的粉末≤8﹪,>40mm的块≤10﹪。
7.1.3.2.5莹石:
粒度5~40mm,﹤5mm的粉末≤8﹪,>40mm的块≤10﹪。
7.1.4生产工艺流程图:
7.1.5配料计算举例:
7.1.5.1硅锰合金化学成分:
Mn66%,Si18%,C1.8%,P0.18%。
7.1.5.2原料化学成分
名称
Mn%
P%
Fe%
SiO2%
CaO%
MgO%
Al2O3
混合锰矿
35
0.08
6.0
23.90
9
1.1
4.3
焦碳
固定碳%
灰分%
挥发分%
82
15
2
灰份组成
6
45
4
3
硅石
0.008
97
焦碳含水量约10%左右。
7.1.5.3计算依据
7.1.5.3.1元素分配见下表:
元素
入合金%
入渣%
挥发%
80
10
Fe
95
5
50
44
85
7.1.5.3.2出铁口排碳及炉口烧损10%。
7.1.5.3.3炉渣碱度:
R3=0.70
7.1.5.5计算:
以100kg混合锰矿为计算基础,求需要焦碳、硅石量、熔剂量,并计算出炉渣碱度。
7.1.5.5.1合金重量:
100×
35%×
80%/66%=42.42kg
合金中硅量:
42.42×
18%=7.64kg
合金中磷含量:
100×
0.08%×
85%/42.42×
100%=0.16%
7.1.5.5.2焦碳用量
化合物
反应
用碳量kg
MnO
MnO+C=Mn+CO
0.35×
(0.80+0.10)×
12/55=6.87
SiO2
SiO2+2C=Si+2CO
7.64×
24/28=6.55
FeO
FeO+C=Fe+CO
6%×
95%×
12÷
56=1.22
硅锰合金
含碳
1.8%=0.76
合计:
15.40
考虑出铁口排碳,炉口烧损折合成含水10%焦炭:
15.4÷
0.82÷
0.9÷
0.9=23.18kg
7.1.5.5.3硅石用量:
(7.64÷
0.5×
60÷
28-23.9)÷
0.97=8.84kg
7.1.5.5.4炉渣碱度:
R3=(CaO+MgO)/SiO2=(9+1.1+23.18×
0.15×
(0.04+0.012))/32.74×
.44=0.71
7.1.5.5料批组成:
混合锰矿100kg
硅石8.84kg
焦碳23.18kg
7.1.6主要设备参数:
7.1.6.14#电炉炉体参数:
电极直径:
900mm;
极心园直径:
2550mm;
炉壳直径:
6600mm;
炉膛直径:
5200mm;
炉膛高度:
2200mm;
炉壳高度:
4280mm;
电极升降速度:
500mm/min;
电极行程:
1000mm;
最大行程:
1200mm。
7.1.6.24#电炉电气参数:
档位
容量(kVA)
一次电压
(V)
一次电流
(A)
二次电压
二次电流
1
8379
35000
138.2
108
44794
8690
143.3
112
9000
148
116
120
43301
124
41904
128
40595
7
132
39365
8
136
38207
140
37115
7.1.7配料操作
7.1.7.1上料工接班后首先应检查矿槽储料情况,核对炉料配比,校对磅秤和电子秤,确保称量准确。
7.1.7.2炉料配比调整,必须由生产部和二级厂工艺员计算确定,炉长和值班员根据炉况可以适当调整。
7.1.7.3每批料上料顺序:
富锰渣锰矿焦炭硅石白云石莹石。
7.1.7.4配料要求:
7.1.7.4.1人工加料时,配料采取平铺直取混匀法,各种原料按顺序分层平铺在炉台上,高度不超过300mm。
7.1.7.4.2用料管加料时,炉料按顺序倒入料斗中混匀,为保证混料效果,料批批重应适当缩小。
7.1.7.4.3每次配料应及时做好记录,交班时应主动交清本班用料量、附加料及炉料变化等情况。
7.1.8冶炼操作
7.1.8.1炉面操作
7.1.8.1.1人工加料要做到“勤、轻、准、匀”,料管下料要做到少放、勤推,坚持2至3人加料或放料,不允许空烧、冒白火。
7.1.8.1.2料面应保持一定的锥度,料面高度应控制在平炉口左右为宜。
7.1.8.1.3出炉后要及时、快速地整理料面和下放电极,发现料面有结块或不透气的部位要用钢钎疏忪,尽量缩短辅助时间,减少热停炉时间。
7.1.8.2正常炉况征兆:
7.1.8.2.1炉面火焰分布均匀,电流稳定,满负荷操作,电极下插深度适当(9000kVA电炉电极下插深度1000~1400mm),三相电极消耗速度比较均匀,三相电极下插深度基本一致。
7.1.8.2.2出铁和排渣顺畅,温度高,渣、铁流动性好,渣、铁易分离。
7.1.8.2.3合金成分比较稳定,炉渣三元碱度(CaO+MgO)/SiO2约在0.5~0.95之间,MnO在10%以下。
7.1.8.3炉况异常的征兆及处理方法:
7.1.8.3.1还原剂过剩的征兆及处理
(1)还原剂过剩的征兆
a、电流稳定上涨,电极难插,刺火塌料增多,炉内料面冒火不均匀。
b、电极消耗慢,电极端部粗。
c、合金中含Si高,含C低,渣中MnO、SiO2偏低。
d、严重过剩时,合金中的Si反而下降,渣中MnO升高,产量低,出炉困难。
(2)处理方法:
减少料批中的焦炭量。
严重过剩时,应加净矿洗炉。
7.1.8.3.2还原剂不足的征兆及处理:
(1)还原剂不足的征兆
a、电流波动大且易偏低,电极插入炉料过深,炉内翻渣多。
b、电极下放量明显增加,电极消耗快,电极端部尖。
c、出铁温度降低,渣量过大,渣铁分离差,渣中MnO、SiO2高。
d、合金中Si低、C高。
增加料批中的焦炭量或者从备用料管中下净焦炭直接加入炉内。
7.1.8.3.3炉内翻渣的原因及处理:
(1)炉内翻渣的原因:
a、出铁时排渣不彻底,炉内积渣过多。
b、还原剂不足,或炉料碱度过低,系统性能差,电极插入炉料过深。
c、炉料湿,粉料过多,炉料透气性差。
d、炉缸容积缩小。
e、低熔点熟料入炉比例过高,炉料成渣打早,软件包熔带上移。
(2)处理方法:
a、出炉时必须加强人工拉渣,尽可能将炉内积渣排出。
b、必须及时调整配比,改善炉料导电性能,以达到冶炼要求。
c、若炉缸缩小,应及时洗炉扩大炉缸。
d、调整炉料结构,确保精料入炉。
7.1.8.4合金成分控制
7.1.8.4.1合金成分按产品技术标准或合同订单要求进行控制,发现合金成分波动时,应及时调整配比。
7.1.8.4.2当合金含硅偏低、碳高时,应增加料批中的硅石和焦碳的数量;
合金中硅高、碳低时则相反处理。
7.1.8.4.3合金中锰低磷高,应调整锰矿的配比,增加含锰高、含磷低、含铁低的锰矿用量。
7.1.8.4.4合金中锰高时,可增加含铁高的锰矿。
7.1.8.4.5每炉合金分析Mn、P、Si、C元素;
炉渣每班做一次全分析,分析MnO、SiO2、CaO、MgO、Al2O3等元素,并及时做好记录。
7.1.9配电操作:
7.1.9.1正常时,4#电炉变压器使用第五至第七档。
刚放下电极送电时,电流应从低到高缓慢增加以焙烧电极,电极焙烧好以后,应保持深电极、满负荷用电。
7.1.9.2如果变压器本身质量比较好或者附有可超负荷说明,则在确保设备安全的情况下,一般可超负荷30~45%。
7.1.9.3送电前,应适当提起三相电极。
送电时,先合隔离开关,后合油开关或真空开关,保证合闸冲击电流不超过额定电流的20%。
7.1.9.4一般停电时,应先将电流降低到额定电流的20%以下,方可跳开油开关或真空开关。
停电时间较长时,要拉下隔离开关。
非紧急情况下,不允许满负荷跳闸。
7.1.9.5正常运行时,要尽量保持三相电流平衡,三相不平衡度一般不应超过±
10%。
7.1.9.6变压器油温应控制温升在60℃以下(采用电阻法测量),油温过高时,要采取强制冷却措施。
7.1.9.7在电力系统突然停电时,应立即断开油开关或真空开关,以免来电时,带负荷过高送电冲击变压器。
7.1.10电极维护、电极事故种类及处理方法:
7.1.10.1电极的维护:
7.1.10.1.1自焙电极使用标准电极糊或密闭电极糊,破碎粒度为50~150mm,电极糊内要严防混入各种杂物。
7.1.10.1.2电极壳上部要保持一定的长度,过低时要及时接长电极壳,接长电极壳时要保持其圆度和垂直度。
焊接时电极壳胁片要对齐,电极壳焊缝应平整。
7.1.10.1.3每班检查糊柱高度,糊柱高度应保持在铜瓦上部2.0~3.0米,电极壳上口应加盖,防止杂物及大量灰尘落入电极内。
7.1.10.1.4铜瓦冷却水温度一般控制在≤60℃。
如电极烧结程度差或因停电需对电极糊进行保温时,可适当提高冷却水温度。
7.1.10.1.5发生热停炉时,在停电后应及时关小铜瓦冷却水;
送电前应先将铜瓦冷却水打开。
恢复送电时,负荷应逐步升高;
停电检修或超过24小时以上的热停炉时,应采取措施(将电极座入酌热的炉料中或燃烧木柴等)加强对电极保温。
7.1.10.2电极事故类型及处理:
电极事故一般分四种:
硬断、软断、漏糊和悬糊四种类型。
7.1.10.2.1硬断原因及处理
(1)硬断的原因
a、电极糊混入其它杂物或落入大量灰尘,影响电极烧结后的强度;
b、电极烧结过快或电极糊灰分过高,电极烧结后强度下降;
c、热停炉时间过长,电极保温措施不力,或电极周围漏水严重,检修后恢复送电时负荷上升过快,电极受急冷急热影响产生裂纹。
(2)处理方法
a、如硬断部分短,可以将断头压入料层内任其逐步消耗;
b、如硬断部分长,应将断落部分拉出;
硬断后如果电极工作端长度不够,应下放电极。
采用边生产边焙烧的方法,使其逐步上升负荷。
7.1.10.2.2软断原因及处理
(1)软断原因
a、电极下放量过长,电极烧结差,负荷控制不当,电流过大引起软断。
b、电极糊挥发分过高,电极烧结慢。
c、电极焊接质量差,脱焊后造成已烧结部分全部脱落。
d.、放电极时,电极下冲或电极锥套压紧力不够,电极下滑。
事故发生后,应立即停电进行检查。
a、如断落部位与电极壳错位不大时,可将电极套在断头上,倒放电极,将铜瓦夹住断头,加木柴焙烧或采用电阻焙烧;
b、如错位过大,则将断电极拉出挖清炉内电极糊,将电极壳重新焊底,加入新电极糊,用木柴重新焙烧电极。
7.1.10.2.3漏糊原因及处理
(1)漏糊原因
a、电极壳焊接质量差,电极糊从焊缝裂口处漏出。
b、电极壳变形大,下放电极时铜瓦将电极壳划破或铜瓦与电极壳接触不良,打弧烧穿电极壳,电极糊从破裂处漏出。
c、下放电极时,由于压放系统失灵而下滑,产生电弧烧穿电极壳,导致漏糊。
发现漏糊应立即停电,查明原因和漏糊位置。
a、如漏糊位置靠近铜瓦,且孔不大时,则可用石棉绳或火泥等堵塞,倒放电极,将孔夹在铜瓦内。
b、如孔大,应用石棉绳将孔堵住后再将孔焊好,再送电生产。
7.1.10.2.4悬料原因及处理方法
(1)悬糊原因
a、电极糊熔点过高。
b、电极糊加入块度过大。
c、电极糊柱控制高度过高。
发现悬糊后,应采用木棒或重锤敲打电极,使悬糊落下。
7.1.11电极操纵
7.1.11.1电极压放程序:
a、选择开关拨到要压放的那相电极;
b、气囊开关拨到上紧下松;
c、汽缸开关拨到铜瓦松;
d、电极升降开关拨到上,直到放出所需长度为止;
e、汽缸开关拨到铜瓦紧;
f、气囊开关拨到上松下紧。
7.1.11.2电极倒拨程序:
a、电极选择开关拨到要倒拔的那相电极;
d、电极开关拨到下,直到倒回所需长度为止;
7.1.12炉前操作
7.1.12.1出炉
7.1.12.1.1出炉前必须烤干铁水包,准备好出炉工具,做好堵眼用泥球。
7.1.12.1.2开炉眼时,先用钢钎修好炉眼外部,再用氧气管烧开炉眼。
7.1.12.1.3出铁时,要注意铁、渣流量。
流量小时,及时进行人工拉渣,出尽残铁、残渣。
7.1.12.1.4堵眼时,先用钢钎修大炉眼外部,泥球要堵深堵牢,以防跑眼。
7.1.12.2炉前浇注(采用低温、慢速、细流的原则进行浇注。
)
7.1.12.2.1浇注前要准备好取样勺、吊铁环、扒渣用等工具。
7.1.12.2.2浇注时,每块铁锭要推清表面渣子和高碳层。
每隔一锭要用取样勺取一次液体样,所取的样冷却后混合送化验室分析。
7.1.12.2.3浇注后,应将铁水包内的残余渣铁清理干净。
7.1.12.2.4吊铁时要掌握时间,不准漏铁。
每炉产品分炉堆放,不准混炉号。
7.1.12.2.5吊铁后,锭模用石灰水挂模以便合金脱模。
7.1.12.2.6吊铁完毕,应及时将炉前工具放整齐。
如是移动铁水包应及时将铁水包放回出铁流槽下面,防止跑眼,避免事故发生。
7.1.13合金精整
7.1.13