陶瓷设计Word格式文档下载.docx
《陶瓷设计Word格式文档下载.docx》由会员分享,可在线阅读,更多相关《陶瓷设计Word格式文档下载.docx(20页珍藏版)》请在冰豆网上搜索。
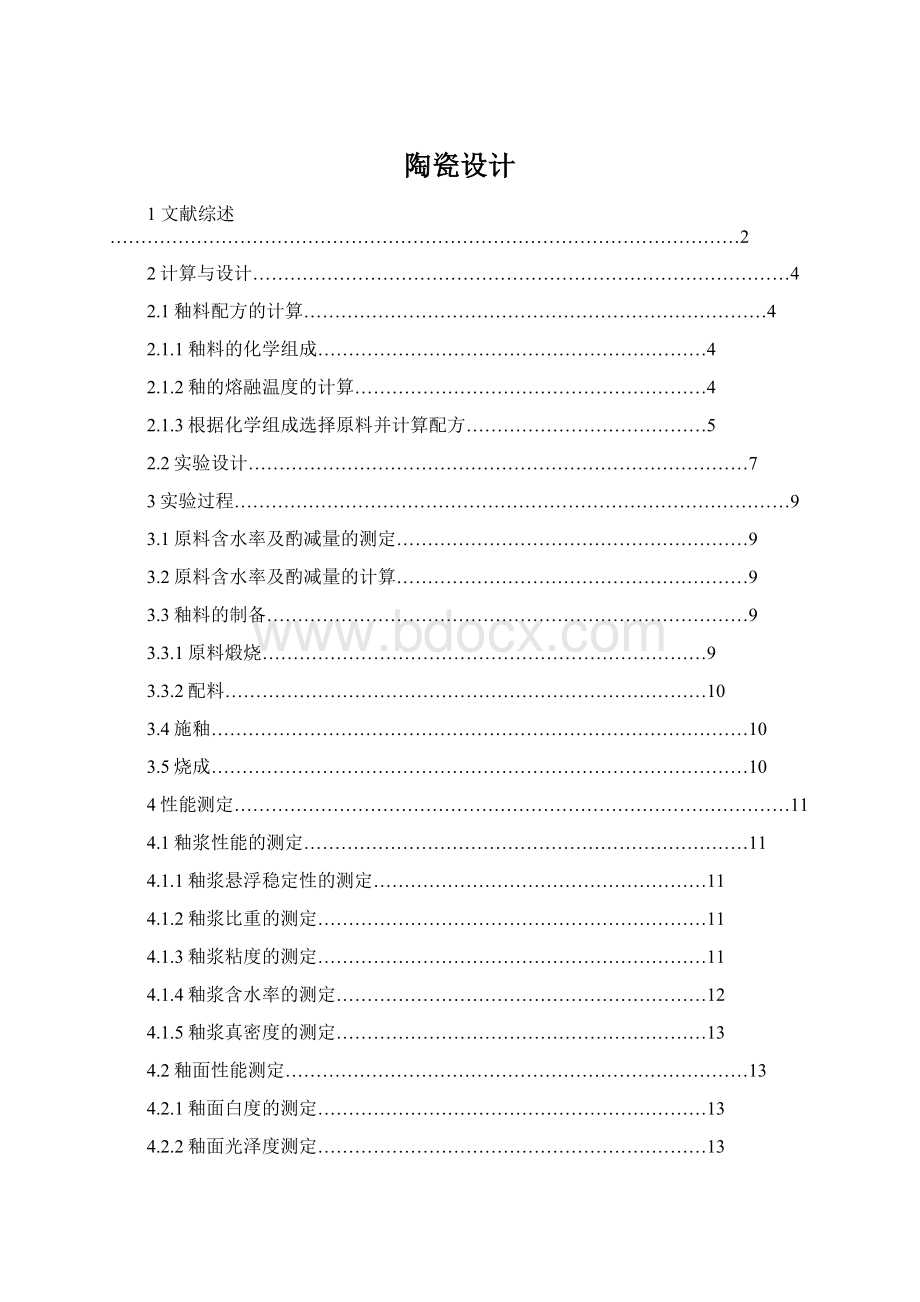
乳浊釉的发展历史悠久。
如欧洲陶瓷企业使用过的釉料乳浊剂经历了氧化锡、氧化锌、二氧化钛、磷酸盐、硅酸锆等过程。
因氧化锡作为乳浊剂的成本过高,其现今的使用量已越来越少。
在上世纪初,美国最先用锆英石作为釉料乳浊剂,后来英国开始使用锆英石取代氧化锡,降低了瓷砖装饰用釉料产品的成本。
在常规釉料中加入5%的氧化锡,可产生白里泛青的色调;
氧化锌广泛应用于锆英石釉中,以提高白度与乳浊度。
在高温卫生洁具釉料中,氧化锌具有强溶剂作用,能显著降低釉的粘度,因此目前仍在部分使用。
在釉中加入氧化钛,可以制成高档的白乳浊釉。
而磷化合物作乳浊剂可使釉不透明并可增加釉对光的折射率,增加釉料的光泽。
磷酸钙、骨灰、磷灰石均可适量配人釉料,使釉形成良好的乳浊与光亮效果。
此外锂灰石、锂瓷石、锂霞石等含锂化合物也是很好的乳浊釉用原料。
对于乳浊釉,不论慢烧还是快烧条件下,国内外研究得较多的是外加乳浊剂(TiO2、SnO2、ZrSiO4等)的单一微晶乳浊方式。
研究的思路主要是基于乳浊剂与基质玻璃相存在较大的折射率差值,在一定温度下,乳浊剂以细分散晶体形式存在,引起光散射,产生乳浊效果。
1958年,日本学者加藤悦三以钙釉和含锌钙釉为基础釉,研制成具有液相分离结构的骨灰乳浊釉:
1993年,聂曼云利用R20-R0-A12O3-SiO2系统开发出不含P205、TiO2、ZrSiO4等昂贵乳浊剂的应用于卫生瓷的分相乳浊白釉;
1995年,余丽达设计了全生料的KNaO-CaO(ZnO)-A1203-B203-SiO2系统分相乳浊釉,指出釉中熔析出的大量0.5~1.0pm的富硅液滴相充当了乳浊粒子;
1995年,陈德平等在1050℃、2h的烧成条件下用K20、Na20、CaO、ZnO、MgO、Al203、B203、Si02等常规化学组成的原料制成了乳浊白釉.该釉具有“分阶段多层次”的微分相结构,是釉面乳浊的原因所在王春玲在基础釉中外加6%氧化钛乳浊剂,采用湿法球磨,制得乳浊效果理想、釉面白度高、适用范围广的新型钛乳浊釉。
宫华、孙明采用三角配料法优化锆乳浊釉的配方,得到一种烧成温度为l230℃、性能稳定、白度较高、锆英石用量较少的锆生料乳浊釉。
西班牙学者JuditMolera和MarioVendrel应用WDS、SEM/EDX、XRD和XRF对伊斯兰锡釉陶器的化学成分和微观性能进行了分析。
认为伊斯兰西班牙乳浊釉中含有37-56%的PbO和4~l5%的SnO2,其乳浊机理是因为有小于lum的SnO2颗粒的存在。
目前研究最多的是锆乳浊釉,研究者在不同层面对锆釉中析出相的数量、尺寸和分布以及熔析行为等进行了研究。
美国学者BurnhaW.KingJR和AndrewL.Andrews通过实验研究了氧化锆瓷釉的两种乳浊机理:
一是在釉中有未溶解的氧化锆颗粒残留;
二是锆化合物在烧成时结晶.表明了数量、特性及原料的选取是引起各种瓷釉样品乳浊的原因。
前苏联学者Yu.G.Shteinberg等对锆乳浊机理进行了研究,认为由于微晶析出氧化锆。
从而产生乳浊。
国内学者陈志强、苏宪君等认为硅酸锆作为陶瓷釉料乳浊剂,其粒度越细,乳浊效果越好.要满足生产高档建筑卫生陶瓷的要求,其最大粒径最好小于5-12um,平均粒径在lum左右,而且ZrSiO4纯度越高,乳浊效果越好,Fe203杂质的含量最好小于O.O5%。
但由于高质量硅酸锆价格昂贵,且其最大加入量也受到限制.过多引入将导致釉熔体高温粘度大、流动性差,容易出现针孔、釉面粗糙等缺陷,所以如何降低硅酸锆用量又不影响其乳浊效果一直是困扰人们的一个难题。
目前研究的一个热点是选择其它廉价乳浊剂(如天然磷灰石)来取代或部分取代锆英石研制低锆复合乳浊釉,以降低生产成本。
如马建杰、董宝军在实验的基础上。
提出了在乳浊釉中用磷灰石取代锆英石的可能性。
研究发现,磷灰石的引入可使釉的物理化学性能发生变化,克服了锆英石带来的釉面缺陷,使釉面的光泽度、白度等均有所提高。
刘雪东和王泽华设计了一系列适用于卫生瓷大生产使用的低锆复合乳浊釉,具有乳浊剂用量少、乳浊度高、成本低等优点,只用4%~6%超细锆英粉和氟磷增白剂,调整釉料硅铝比值为11~12,就可制备出符合要求的卫生瓷釉。
王境堂、郝国龙等采用锆英石及磷酸钙为复合乳浊剂,发现当石英为15-25%,钠长石10-20%,锆英石10~20%,磷酸钙1~5%等组成范围时可得到釉面平整光亮、白度高、乳浊效果好的生料釉。
由于陶瓷生产普遍采用高温作业(一般在1200℃以上),烧成燃料费用占生产成本的30%以上,因此,在陶瓷工业中,提质降耗和产品换代已经迫在眉睫,对低温釉的研究是实现这一目标的有效途径之一。
董大静讨论了低温一次烧成釉面砖坯釉料的选择及其相互适应性。
他指出,坯体应具备低温烧结性,烧成温度在l050-1100℃范围内;
坯体烧成后适宜的膨胀系数为7.O~7.5×
lO/℃。
面釉的烧成温度应与坯体的烧成温度相同.始熔温度要高于坯体的排气温度,膨胀系数应为5.5~6.0×
lO-6/℃,以使坯釉匹配。
此外,通过制定合理的烧成曲线可减少釉面缺陷。
李伟东和黄建国等提出了在低温快烧条件下制备自生乳浊釉的研究思路.从材料制备科学的观点出发,研究适合低温快速烧成(1000-l200℃、0.5~lh)的多元系统.通过优化组成设计及物理化学过程的控制.使釉熔体在烧成过程中产生一级或多级分相.还可能辅以少量高折射率微晶析出.从而形成大量微米至亚微米级不混溶微滴结构或微滴和微晶的复相结构.产生较强的乳浊效果。
基于以上考虑,积极寻找和开发新型陶瓷原料,降低企业生产成本,从而提高经济效益便成了陶瓷工作者的首要任务。
2计算与设计
2.1釉料配方的计算
2.1.1釉料的化学组成
表2-1釉料的化学组成(wt%)
化学成分
SiO2
Al2O3
CaO
MgO
K2O
Na2O
BaO
ZnO
ZrO2
合计
釉料
56.03
10.46
6.97
1.88
4.45
0.93
4.77
3.79
10.72
100
2.1.2釉的熔融温度的计算
釉的始融温度系数K
K=(a1ωa1+a2ωa2+·
·
+aiωai)/(b1ωb1+b2ωb2+·
+biωbi)
式中:
a1、a2·
ai—————易熔氧化物熔融温度系数
b1、b2·
bi—————难熔氧化物熔融温度系数
ωa1、ωa2·
ωai—————易熔氧化物质量分数
ωb1、ωb2·
ωbi—————难熔氧化物质量分数
表2-2釉熔融温度计算表
易熔氧化物
难熔氧化物
氧化物
质量分数
4.45
熔融温度系数
1.0
0.5
0.6
1.2
aiωai或biωbi
4.450
0.930
3.485
1.128
4.770
3.790
56.030
12.552
10.720
Σaiωai或
Σbiωbi
18.553
79.302
K
0.234
熔融温度
1266
由于根据此方法计算出的熔融温度比实际温度要高,所以最高烧成温度为1200℃
2.1.3根据化学组成选择原料并计算配方
(1)根据化学组成与实验室所拥有的原料进行选择,为长石、烧滑石、紫木节、石英砂、碳酸钙、碳酸钡、氧化锆、氧化锌。
表2-3原料的化学组成(wt%)
长石
66.61
17.35
0.35
0.26
13.39
2.16
—
滑石
62.04
0.17
0.22
32.56
0.09
紫木节
46.15
32.58
1.27
0.43
0.74
0.70
石英砂
99.74
碳酸钡
76.19
碳酸钙
63.73
氧化锆
97
氧化锌
99
表2-4基础釉配方的计算(wt%)
Ba0
配方化学组成
32.86
21.89
5.70
0.12
0.01
4.40
0.71
余量
34.14
4.76
6.85
1.87
0.05
5.59
3.37
1.82
30.77
6.84
14.61
6.74
0.19
0.06
0.18
24.03
6.65
-0.001
0.04
24.09
12.11
2.83
3.83
6.26
11.05
表2-5釉料基础配方(wt%)
原
料名称
含量
29.76
5.06
13.32
21.82
10.97
5.67
10.01
3.47
2.2实验设计
采取釉料的系统调试方法进行实验,主要是通过变化一个、两个或者多个主要的化学组成来设计一系列釉料配方,可以同时烧成这一系列的配方,根据烧成结果获得所需要的最佳配方。
表2-6-11号配方(基础配方,粗料)
组成
质量g
表2-6-22号配方(粗料)
6.00
7.00
12.00
表2-6-33号配方(粗料)
磷酸钙
1.20
表2-6-44号配方(细料)
表2-6-55号配方(细料)
31.80
20.00
1.60
表2-6-66号配方(细料)
33.00
18.80
4.47
表2-6-77号配方(细料)
2.00
表2-6-88号配方(细料)
33.80
8.32
20.80
10.50
3.97
表2-6-99号配方(细料)
10.32
22.80
2.47
表2-6-1010号配方(粗料)
钾长石
钠长石
22.00
11.00
8.00
21.00
6.00
4.00
表2-6-1111号配方(粗料)
30.00
10.00
221.00
表2-6-1212号配方(粗料)
15.00
以上的12个配方中,1号配方是根据基础化学组成计算而得,其余配方是根据前一号实验结果针对每种烧成后出现的缺陷加以改进而得。
3实验过程
3.1.原料含水率及酌减量的测定
(1)取坩埚并分别编号a、b、c、d、e、f、i、j,称量坩埚的重量计做m1
(2)取所需的各个试样至于坩埚中,称量坩埚和试样的重量之和计做m2
(3)将盛有试样的坩埚置于干燥箱内干燥三个小时,取出迅速称量其重量计做m3
(4)将盛有试样的坩埚置于炉内灼烧一个小时,取出迅速称量其重量计做m4
3.2.原料含水率及酌减量的计算
(1)湿试样的重量m5=m2-m1
干燥后试样的重量m6=m3-m1
灼烧后试样的重量m7=m4-m1
(2)所得测量结果如下
表3-1原料含水率及灼减量
m1/g
34.8393
35.0948
34.3857
32.5328
28.8137
37.4216
29.5269
31.2576
m2/g
39.9171
39.2182
41.2322
36.3613
34.5396
43.7832
35.3905
37.5639
m3/g
39.9072
39.1752
41.1548
36.3548
34.5330
43.7763
35.3768
37.5467
m4/g
39.8900
38.9103
40.1929
36.3418
32.0869
41.9678
m5/g
5.0778
4.1234
6.8465
3.8285
5.7259
6.3616
5.8636
6.3063
m6/g
5.0679
4.0804
6.7691
3.8220
5.7193
6.3515
5.8499
6.2891
m7/g
5.0507
3.8156
5.8072
3.8090
3.2732
4.5462
含水率﹪
1.04
1.13
0.16
0.23
0.27
灼减量﹪
0.34
6.49
14.21
42.77
28.42
0.00
3.3.釉料的制备
3.3.1原料煅烧
对滑石进行煅烧:
滑石主要提供镁,高温时有助融效果,而且膨胀系数小,同时可以提高釉面白度。
但是自然状态下的滑石是一种层片状物质,直接引入不利于粉磨,还会引起成分的定向排布,使釉浆的组分不均匀,造成釉面缺陷。
经煅烧处理的滑石层片状结构已经破坏,可以避免缺陷。
3.3.2配料
按照釉料配方精确称量长石、烧滑石、紫木节、石英砂、碳酸钙、氧化锆、氧化锌,并按1:
0.6的料水质量比取水,将原料与水混合,并置于球磨机中研磨。
3.4.施釉
采用浸釉和浇釉两种方法进行施釉,保证釉浆厚度适中,且坯体底面无釉,以方知少城时粘连,然后进行自然干燥。
3.5.烧成
根据实际情况确定烧成制度,进行烧成。
表3-2试验操作过程
烧成
次序
配方
配料总量
g
加水量
ml
研磨时间
min
260目筛余
烧成温度
℃
保温时间
釉层薄厚
第1炉
配方1
60
15
1200
20
适中
配方2
70
薄
配方3
80
厚
第2炉
配方4
25
厚,不均
配方5
配方6
配方7
配方8
配方9
第3炉
配方10
配方11
薄,不均
配方12
4性能测定
4.1.釉浆性能的测