一篇比较详细塑料模具设计毕业论文Word文档格式.docx
《一篇比较详细塑料模具设计毕业论文Word文档格式.docx》由会员分享,可在线阅读,更多相关《一篇比较详细塑料模具设计毕业论文Word文档格式.docx(38页珍藏版)》请在冰豆网上搜索。
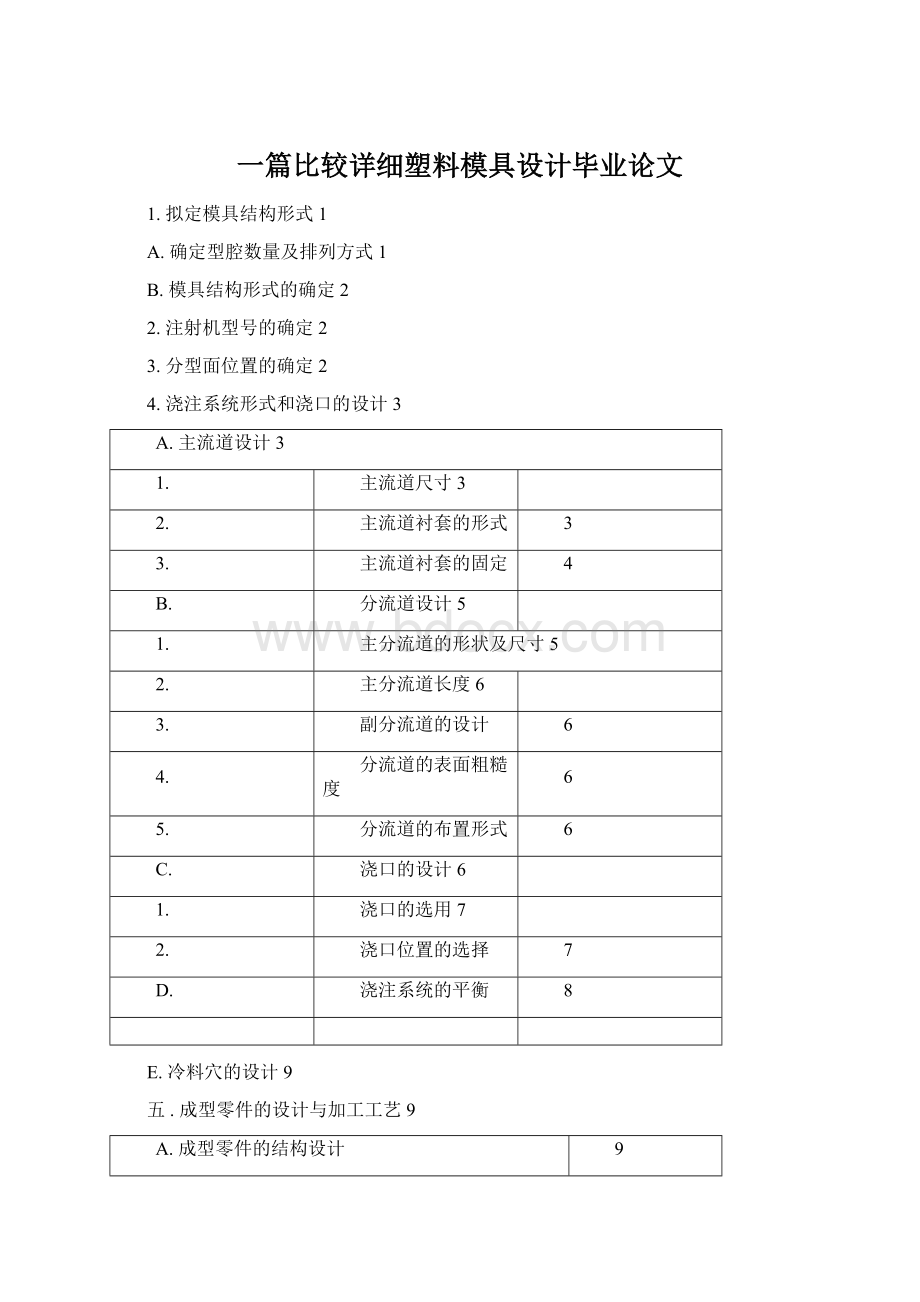
24
成型零件的加工工艺
27
前模仁的加工工
艺
28
行位1的加工工
一.拟定模具结构形式
确定型腔数量及排列方式型腔的数量是由厂方给定,为“一出四”即一模四腔,他们已考虑了本产品的生产批量(大批量生产)和自己的注射机型号。
因此我们设计的模具为多型腔的模具。
考虑到模具成型零件和抽芯结构以及出模方式的设计,模具的型腔排列方式如下图所示:
图
(1)
模具结构形式的确定由于塑件外观质量要求高,尺寸精度要求一般,
且装配精度要求高,因此我们设计的模具采
模具将会采用三个分模面,三个分
用多型腔多分型面。
根据本塑件电动机绝缘胶架的结构,型面。
注射机型号的确定一般工厂的塑胶部都拥有从小到大各种型号的注射机。
只占一小部分。
所以我们不必过多的考虑注射机型号。
型号和规格以及各参数如下:
注射量:
锁模力:
模板大小开模距离推出形式分型面位置的确定如何确定分型面,需要考虑的因素比较复杂。
由于分型面受到塑件在模具中的成型位置、注系统设计、塑件的结构工艺性及精度、嵌件位置形状以及推出方法、模具的制造、排气、操作工艺等多种因素的影响,因此在选择分型面时应综合分析比较,从几种方案中优选出较
为合理的方案。
选择分型面时一般应遵循以下几项原则:
中等型号的占大部分,小型和大型的具体到这套模具,厂方提供的注射机
95g
120T
400X550
推出位置:
推出行程:
1)分型面应选在塑件外形最大轮廓处。
2)便于塑件顺利脱模,尽量使塑件开模时留在动模一边。
3)保证塑件的精度要求。
4)满足塑件的外观质量要求。
5)便于模具加工制造。
6)对成型面积的影响。
7)对排气效果的影响。
8)对侧向抽芯的影响。
其中最重要的是第5)和第2)、第8)点。
为了便于模具加工制造,应尽是选择平直分型面工易于加工的分型面。
如下图所示,采用A—A这样一个平直的分型面,前模(即定模)做
成平的就行了,胶位全部做在后模(即动模),大简化了前模的加工。
A—A分型面也是整
个模具的主分模面。
下图中虚线所示的B—B和C—C分型面是行位(即滑块)的分型面。
这样选择行位分型面,有利于线切割行位以及后模仁和后模镶件这些成型零件。
分型面的选
择应尽可能使塑件在开模后留在后模一边,这样有助于后模设置的推出机构动作,在下图中,
从A—A分型,了B—B处的行位向左移开,C—C处的行位向右移开后,由于塑件收缩会包在后模仁和后模镶件上,依靠注射机的顶出装置和模具的推出机构推出塑件。
"
AA
—-—--______________
.B[:
1C
1/■一一\
图⑵
浇注系统形式和浇口的设计
主流道设计
主流道尺寸
另一端与分流道相连的一段带有锥度的流动通道。
主流
主流道是一端与注射机喷嘴相接触,道小端尺寸为3.5〜4mm。
主流道小端入口处与注射机喷嘴反复接触,属易损件,对材料要求较严,因而模具主流道部
分常设计成可拆卸更换的主流道衬套形式(俗称浇口套,这边称唧咀),以便有效的选用优
质钢材单独进行加工和热处理。
唧咀都是标准件,只需去买就行了。
常用唧咀分为有托唧咀
和无托唧咀两种下图为前者,有托唧咀用于配装定位圈。
唧咀的规格有①12,①16,①20
等几种。
由于注射机的喷嘴半径为20,所以唧咀的为R21。
040
035
016
图⑶
主流道衬套的固定因为采用的有托唧咀,
所以用定位圈配合固定在模具的面板上。
定位圈也是标准件,
外径为
①120mm,内径①35mm。
具体固定形式如下图所示:
分流道设计
在多型腔或单型腔多浇口(塑件尺寸大)时应设置分流道,分流道是指主流道末端与浇口之间这一段塑料熔体的流动通道。
它是浇注系统中熔融状态的塑料由主流道流入型腔前,通过
截面积的变化及流向变换以获得平稳流态的过渡段。
因此分流道设计应满足良好的压力传递
和保持理想的充填状态,并在流动过程中压力损失尽可能小,能将塑料熔体均衡地分配到各
个型腔。
主分流道的形状及尺寸
主分流道是图(6)中水口板下水平的流道。
为了便于加工及凝料脱模,分流道大多设置在分型面上,分流道截面形状一般为圆形梯形U形半圆形及矩形等,工程设计中常采用梯形截面加工工艺性好,且塑料熔体的热量散失流动
阻力均不大,一般采用下面的经验公式可确定其截面尺寸:
H=-B
(式2)
式中B—梯形大底边的宽度(mm)
m—塑件的重量(g)
L—分流道的长度(mm)H—梯形的高度(mm)
梯形的侧面斜角a常取50-15°
在应用式(式1)时应注意它的适用范围,即塑件厚度在3.2mm以下,重量小于200g,且计算结果在3.2—9.5mm范围内才合理。
本电动机绝缘胶架的体积为3221.7324mm3,质量大约4g,分流道的长度预计设计成140mm
长,且有4个型腔,所以:
B=4O.2654』140"
3取b为8mm
2
H8^5
3取H为5mm
梯形小底边宽度取6mm,其侧边与垂直于分型面的方向约成10°
。
另外由于使用了水口板(即
我们所说的定模板和中间板之间再加的一块板),分流道必须做成梯形截面,便于分流道和
主流道凝料脱模。
实际加工时实,常用两种截面尺寸的梯形流道,一种大型号,一各小型号。
如下图所示:
图(5)
主分流道长度
分流道要尽可能短,且少弯折,便于注射成型过程中最经济地使用原料和注射机的能耗,减
少压力损失和热量损失。
将分流道设计成直的,总长140mm。
副分流道即图(6)中的主分流道以下的两个土字形的流道
副分流道中竖直方向上有锥度的流道的锥度为单边2°
其最底部直径为$6mm,水平方向
上下两层流道的直径为$4mm,这些都是根据经验取值,其总长度为38.15mm。
由于分流道中与模具接触的外层塑料迅速冷却,只有中心部位的塑料熔体的流动状态较为理
想,因面分流道的内表面粗糙度Ra并不要求很低,一般取1.6卩m左右既可,这样表面稍
不光滑,有助于塑料熔体的外层冷却皮层固定,从而与中心部位的熔体之间产生一定的速度
差,以保证熔体流动时具有适宜的剪切速率和剪切热。
实际加工时,用铳床铳出流道后,少为省一下模,省掉加工纹理就行了。
(省模:
制造模具
的一道很重要的工序,一般配备了专业的省模女工,即用打磨机,沙纸,油石等打磨工具将
模具型腔表面磨光,磨亮,降低型腔表面粗糙度。
)
分流道在分型面上的布置与前面所述型腔排列密切相关,有多种不同的布置形式,但应遵循
两方面原则:
即一方面排列紧凑、缩小模具板面尺寸;
另一方面流程尽量短、锁模力力求平衡。
本模具的流道布置形式采用平衡式,如下图:
八
LOT
渤
■.X\
图⑹
浇口的设计
浇口亦称进料口,是连接分流道与型腔的通道,除直接浇口外,它是浇注系统中截面最小的
部分,但却是浇注系统的关键部分,浇口的位置、形状及尺寸对塑件性能和质量的影响很大。
浇口的选用
浇口可分为限制性和非限制性浇口两种。
我们将采用限制性浇口。
限制性浇口一方面通过截
面积的突然变化,使分流道输送来的塑料熔体的流速产生加速度,提高剪切速率,使其成为
理想的流动状态,迅速面均衡地充满型腔,另一方面改善塑料熔体进入型腔时的流动特性,调节浇口尺寸,可使多型腔同时充满,可控制填充时间、冷却时间及塑件表面质量,同时还
起着封闭型腔防止塑料熔体倒流,并便于浇口凝料与塑件分离的作用。
从图⑹中可看出,我们采用的是侧浇口。
侧浇口又称边缘浇口,国外称之为标准浇口。
侧
浇口一般开设在分型面上,塑料熔体于型腔的侧面充模,其截面形状多为矩形狭缝,调整其
截面的厚度和宽度可以调节熔体充模时的剪切速率及浇口封闭时间。
这灯浇口加工容易,修
整方便,并且可以根据塑件的形状特征灵活地选择进料位置,因此它是广泛使用的一种浇口
形式,普遍使用于中小型塑件的多型腔模具,且对各种塑料的成型适应性均较强;
但有浇口
痕迹存在,会形成熔接痕、缩孔、气孔等塑件缺陷,且注射压力损失大,对深型腔塑件排气不便。
具体到这套模具,其浇口形式及尺寸如图(7)所示。
浇口各部分尺寸都是取的经验值。
实际加工中,是先用圆形铳刀铳出直径为①4的分流道,再将材料进行热处理,然后做一个铜公(电极)去放电,用电火花打出这个浇口来的。
模具设计时,浇口的位置及尺寸要求比较严格,初步试模后还需进一步修改浇口尺寸,无论
采用何种浇口,其开设位置对塑件成型性能及质量影响很大,因此合理选择浇口的开设位置
是提高质量的重要环节,同时浇口位置的不同还影响模具结构。
总之要使塑件具有良好的性
能与外表,一定要认真考虑浇口位置的选择,通常要考虑以下几项原则:
1)尽量缩短流动距离。
2)浇口应开设在塑件壁厚最大处。
3)必须尽量减少熔接痕。
4)应有利于型腔中气体排出。
5)考虑分子定向影响。
6)避免产生喷射和蠕动。
7)浇口处避免弯曲和受冲击载荷。
8)注意对外观质量的影响。
根据本塑件的特征,综合考虑以上几项原则,每个型腔设计两个进浇点如图(8)和图(9)
所示,进浇点1的分流道开在行位上,进浇点2的分流道开在后模模仁上。
I-
(8)
图(9)
对于中小型塑件的注射模具己广泛使用一模多腔的形式,设计应尽量保证所有的型腔同时得到均一的充填和成型。
一般在塑件形状及模具结构允许的情况下,应将从主流道到各个型腔的分流道设计成长度相等、形状及截面尺寸相同(型腔布局为平衡式)的形式,否则就需要通过调节浇口尺寸使各浇口的流量及成型工艺条件达到一致,这就是浇注系统的平衡。
显然,我们设计的模具是平衡式的,即从主流道到各个型腔的分流道的长度相等,形状及截面尺寸都相同。
冷料穴的设计在完成一次注射循环的间隔,考虑到注射机喷嘴和主流道入口这一小段熔体因辐射散热而低于所要求的塑料熔体的温度,从喷嘴端部到注射机料筒以内约10-25mm的深度有个温度逐渐升高的区域,这时才达到正常的塑料熔体温度。
位于这一区域内的塑料的流动性能及成型性能不佳,如果这里温度相对较低的冷料进入型腔,便会产生次品。
为克服这一现象的影响,用一个井穴将主流道延长以接收冷料,防止冷料进入浇注系统的流道和型腔,把这一用来容纳注射间隔所产生的冷料的井穴称为冷料穴。
冷料穴一般开设在主流道对面的动模板上(也即塑料流动的转向处),其标称直径与主流道大端直径相同或略大一些,深度约为直径的1-1.5倍,最终要保证冷料的体积小于冷料穴的体积,冷料穴有六种形式,常用的是端部为Z字形和拉料杆的形式,具体要根据塑料性能合理选用。
本模具中的冷料穴的具体位置和形状如图(6)中所示。
实际上只要将分流道
顺向延长一段距离就行了。
成型零件的设计与加工工艺模具中决定塑件几何形状和尺寸的零件称为成型零件,包括凹模、型芯、镶块、成型杆和成型环等。
成型零件工作时,直接与塑料接触,塑料熔体的高压、料流的冲刷,脱模时与塑件间还发生摩擦。
因此,成型零件要求有正确的几何形状,较高的尺寸精度和较低的表面粗糙度,此外,成型零件还要求结构合理,有较高的强度、刚度及较好的耐磨性能。
设计成型零件时,应根据塑料的特性和塑件的结构及使用要求,确定型腔的总体结构,选择分型面和浇口位置,确定脱模方式、排气部位等,然后根据成型零件的加工、热处理、装配等要求进行成型零件结构设计,计算成型零件的工作尺寸,对关键的成型零件进行强度和刚度校核。
成型零件的结构设计本套模具的成型零件包括前模仁,后模仁,两个行位,四个镶件。
由前面分析分型面的确定可知,成型零件总体上可分为前模仁V平的,即图
(2)中A—A
分型面以上的部分〉,左边一个行位<图
(2)中B—B分型面以左的部分〉,右边一个行
位<图
(2)中C—C分型面以右的部分〉,后模仁<图
(2)中B—B分型面和C—C分型
面以下的部分〉这三大部分,另外在后模仁上必须镶四个镶件上来碰穿前模仁,以形成电动
机绝缘胶架中间部位的长方形的孔。
前模仁的设计前模仁总体上就是一长方体,底面是平的,其面积至少要能盖住四个型腔,由于有四个型腔,模仁受的压力较大,据经验厚度需设计厚点,另外还要考虑到固定前模仁的螺丝孔的位置、运水(冷却水道)的布置、两个分流道孔、斜导柱从前模仁穿过的斜孔以及前模仁固定到前模框中的固定形式等。
设计前模仁的宽160mm,厚25mm,长260mm。
最终设计结构如下图,上面对称有两条运水,因此在前模框上钻对应两条运水的四个孔,也就是说,长型的水咀穿过这四个孔,再通过螺纹牙,锁紧到前模仁上的。
/、送/
u
oI
11
11h4
ii
ici
i1
严严7、1■
卜f1I11“
1[|
b11i
fiai
I1
11[1
i■:
1I1
111
1jj
C11
W11
11
厂严、11
1II
1<
1
.1厂X、
◎'
H气
.1i
I1
II
1[1
\1
III
p£
II1
o
图(10)
行位1的设计
行位1,即图
(2)中B—B分型面左边部分的成型零件。
其成型的关键部位的形状如下图虚线路径所示,即为行位成型部分的总体截面形状。
注意其
尺寸是已经由产品图放过缩水的,即产品图放大(1+平均缩水)的倍数。
图(11)
整个行位截面形状设计成下图所示的样子,总长120mm,总高39mm,由于我们设计的斜
导柱的倾斜角a为20°
,所以行位的锁紧角a=a+2°
〜3°
=20°
+2°
=22°
图(12)
下图是上图从左边方向看过去的样子,即表达了行位长度方向的情况。
总长为260mm,每
边还有5mm是导向用的。
左边是沙轮越程槽的放大图,宽2mm,深1mm,因为与此槽相
邻的两个面都是要磨削加工的。
图中两个圆是运水的螺丝孔。
17mm,图中1、2处地
F图是行位中设置的冷却水道,运水孔的直径为①6,距行位的顶面
PT-
方是要用铜料堵住的,运水的接口处是
的英制内螺纹,用来接水咀(一种标准件,
用来与外界冷却水相连接的象螺母一样的东西)
,冷却水流的路径如图中的箭头所示。
丄T―i—
昌|!
——…一——…气.J
r:
:
it■I1
I11IJ
nIi'
图(14)
下面开始设计此行位上成型型腔的形状与工作尺寸。
首先设计绝缘胶架上如下图所示的部
分。
下图是该部分的尺寸图,产品厚度为0.6mm,放了18%。
的缩水后厚度为0.6X(1+0.018)
=0.6108-0.61mm,一般情况下精确至切、数点后两位即’丝’就可以了。
成型型腔的工作
尺寸就是产品图的尺寸再乘以(1+平均缩水率)。
这是对于产品图上未注公差的尺寸而言。
图(15)
下图是上图放大(1+0.018)倍后的图形,因此型腔上的凹槽的尺寸也就跟下图是一模一样的。
厚度方向也相应的为0.61mm。
接下来设计下图所示的结构。
产品图上这部分结构也没有公差要求,
行了。
这部分结构凸中出来的,在行位上的相应位置就要凹进去。
1,1=11凹住[oO
r-~I往
L..□
图(17)
行位上这部分结构的最终结构如下图:
图(18)
另外,行位上面定位的孔,由于定位珠是标准件,定位孔是随着定位珠来的。
其截面形状和
尺寸如下图所示:
图(19)
最后,还要设计斜导柱孔,因为斜导柱是选用的标准件,直径为020,而斜导柱孔要比斜导
柱单边要大50丝,所以直径为$21,斜度为20°
另外还要开流道,其尺寸前面已经介绍。
最终的形状如下图所示。
更详细的情况请参见零件图纸。
行位2,即图
(2)中C—C分型面右边部分的成型零件。
其成型的关键部位的形状如下图粗线路径所示,即为行位成型部分的总体截面形状。
同样其
尺寸是已经由产品图(即图中的粗线)放过缩水的,即产品图放大(1+平均缩水)的倍数。
图(21)
其整个截面总体尺寸与锁紧角和行位1的相同,只有一个地方不同。
长度方向的情况、运水的位置和行位1的完全相同,这里就不再多说了。
请参见图(13)和
图(14)。
行位2与行位1不同的结构如下图双点画线所示,这部分结构从产品图上看也没有公差要求,因此也只须放缩水就行了。
图(23)
下图所示的结构必须注意,由于塑件出模方向是向上,下图中双点画线框中的一个长方形的
孔必须以抽芯的方式形成,因此在行位2的相应位置上就要作出一个凹出来的长方体,并且
会高出图(21)中所示的成型部位的截面形状。
图(24)
下图是此部分结构在行位上的详细放大图。
图(25)
其它方面如流道、定位孔、斜导柱孔等的形状与位置尺寸和行位1的完全一样。
最终设计的
行位2的形状如下图所示。
图(26)
后模仁,即图
(2)中B—B和C—C分型面下面部分的成型零件。
s/\E
图(27)
其整个截面总体尺寸如下图所示,中间凸出来的是成型部位。
左边要与图(12)所示的行位
1相吻合,右边要与图(22)所示的行位2相吻合。
注意下图所示的结构也可以不这样做,即中心线左边的部分只做到24.13伽,右边的部分做
到26.88mm,也就是说总体长度由图示的132mm变成了24.13+26.88=51.01mm。
后模板上
开的框也相应变窄。
两条运水直接做到模板上。
这样做可以节约一部分模仁材料。
但是由于
所有的成型零件都要经过热处理的,硬度达到HRC48〜52,而模板是没有经热处理的。
两
个高硬度的行位在模板上滑动,时间一长会将行位下的模板金属磨损掉,行位便会下降,其
后果不堪设想。
所以后模仁两边要延伸出来一部分为好。
这样便能保证两行位与后模仁长期
后模仁的长度方向的情况与总体尺寸如下图所示,其中两条运水直径为$6mm,6个螺丝孔
为M10用来将后模仁固定在后模框上,深度从底面上来15mm。
流道尺寸前面已论述,中
间直径为$6mm,两边为$4mm。
图(29)
下面将设计后模仁上用于成型的型腔部分。
后模仁上要加工的成型型腔的部分不多。
首先须
在后模仁上开一长方形的通孔,用于配后模仁的镶件上来。
至于开孔的路径在产品图中的具
体位置如下图中粗虚线框所示,此虚线框的大小也就是后模仁镶件的大小
图(30)
上图的这个产品图是放过缩水的。
但图中特意标注出来的尺寸,在产品图中是有公差要求的,
说明这里是要与别的零件相装配的,不能简单的放一下缩水就行了的。
在产品图中此尺寸为
13.00a0mm。
这个尺寸为孔的尺寸,基准尺寸为13mm,计算型腔工作尺寸时,一般取公差
的上限或上下偏差值的中值再加上基准尺寸后所得的值为新的基准尺寸,然后再将新的基准
尺寸乘以(1+缩水)从而得到型腔的工作尺寸。
在这里,我们先取此尺寸公差的上下偏差
值的中值0.05m,再加上基准尺寸13m得13.05m,然后乘以(1+0.018)等于13.285m即为后模仁上开孔尺寸或后模仁镶件尺寸。
在后模仁上还要加工出如下图所示胶位的型腔出来,这片胶位的位置就在后模仁上开的镶件
孔的两边。
这部分尺寸没有公差要求,只需将产品图放缩水就行了。
图(32)
最后要在后模仁上设计顶针孔的大小与位置,顶针就是脱模推出机构,即将塑件从后模上顶
出。
如下图所示。
图中八支顶针上下对称,直径都为02mm。
顶针孔在高度方向的形式与尺寸如下图所示。
图中高度为40m的部分直径为02.5m,40
mm以上的部分直径才是02mm,用于与顶针相配合。
这样做的目的是为了减少配合的接触面积。
图(34)
最终设计的形状如下图所示:
图(35)
后模仁镶件就是镶在后模仁的镶件孔中,再顶到前模仁上,以形成绝缘架中间的孔的成型零
件。
它的总体截面外形及尺寸前面已确定,如图(30)中的粗虚线框所示。
另外后模镶件在产品
中的形状与位置如下图所示,图中的粗虚线框也就表示了镶件在另一方向的总体截面形状。
简单的说,塑件哪里是空的镶件就要到哪个位置。
图(36)
镶件上的结构基本上都是与成型有关的结构。
在镶件上要做出如下图中粗虚线框所示的胶位
来,对称的另外一边也要做出同样形状的胶位。
图(37)
上述结构设计完后镶件就成了下图所示的样子。
同样必须注意,下图中特意标出来的尺寸,
920
在产品图上是有公差要求的,其尺寸为
9.2Uq0omm,同样取上下偏差的中值加上基准尺寸,
图(40)
当然还要做一个M6的螺丝孔以通过螺钉固定在
最终设计的后模仁镶件的形式如下图所示,后模框上。
图(41)
此部分内容是本毕业设计的特色所在。
成型零件结构设计完后,就要开始零件的下材料和加工制作等。
由于此塑件电动机绝缘胶架
的材料的主要成分是尼龙66,要求有优良的力学性能,抗冲击强度高,良