清华大学熔模精密铸造技术培训总结.doc
《清华大学熔模精密铸造技术培训总结.doc》由会员分享,可在线阅读,更多相关《清华大学熔模精密铸造技术培训总结.doc(55页珍藏版)》请在冰豆网上搜索。
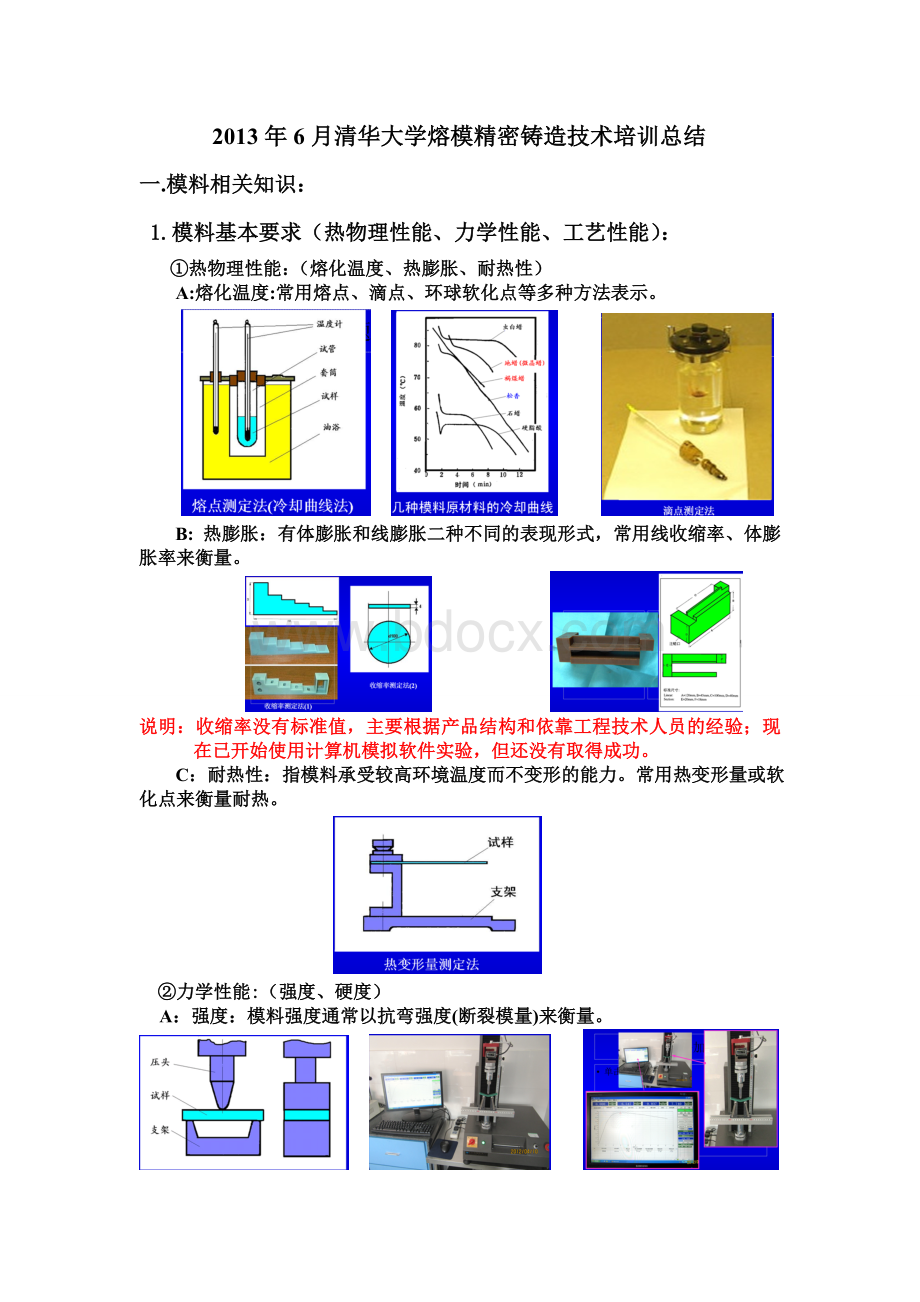
2013年6月清华大学熔模精密铸造技术培训总结
一.模料相关知识:
1.模料基本要求(热物理性能、力学性能、工艺性能):
①热物理性能:
(熔化温度、热膨胀、耐热性)
A:
熔化温度:
常用熔点、滴点、环球软化点等多种方法表示。
B:
热膨胀:
有体膨胀和线膨胀二种不同的表现形式,常用线收缩率、体膨胀率来衡量。
说明:
收缩率没有标准值,主要根据产品结构和依靠工程技术人员的经验;现在已开始使用计算机模拟软件实验,但还没有取得成功。
C:
耐热性:
指模料承受较高环境温度而不变形的能力。
常用热变形量或软化点来衡量耐热。
②力学性能:
(强度、硬度)
A:
强度:
模料强度通常以抗弯强度(断裂模量)来衡量。
B:
硬度(针入度):
在设定温度(例如20或25℃)和固定载荷(如100g)作用下,标准针在在规定时间(5s)刺入模料表面的深度(以0.1mm为单位)。
③工艺性能:
(蜡液粘度、蜡膏流动性、灰分)
A:
模料在液态下(例如99℃)的粘滞性。
B:
蜡膏流动性:
蜡膏充填压型型腔的能力。
通常以设定温度(例如压注温度)和恒定载荷(2kg)作用下,试样的变形程度代表蜡膏的流动性
C:
灰分:
模料经高温(900℃)焙烧后的残留物含量。
说明:
铸件的表面质量主要靠原材料保证,一定要把原材料管起来并且确保原材料的质量一定要合格,公司一定要重视原材料的管理,蜡料较为重要(病从口入)。
2.模料常用原材料(蜡质材料、树脂、高分子聚合物):
①蜡质材料:
在常温下为不透明或半透明的固体,有固定的熔点或狭窄的凝固温度区间,熔化后粘度较小,按来源又分为:
A:
矿物蜡(如石蜡、微晶蜡、地蜡、褐煤蜡等)。
B:
动植物蜡(如蜂蜡、虫白蜡、棕榈蜡等)。
C:
人造蜡(如硬脂酸)。
②树脂:
指非晶态有机物,在常温下为透明的脆性固体,没有固定的熔点,熔融后粘度较大。
常用的有松香及其衍生物和其他天然或人造树脂(如石油树脂、萜烯树脂等)。
③高分子聚合物(高聚物):
指分子量大于1万的高分子聚合物。
熔模铸造中常用的主要是聚烯烃,例如聚乙烯、EVA、聚苯乙烯等,其力学性能比蜡强韧得多,熔融后粘度大。
说明:
三类常用原材料中蜡和树脂是模料的基本组分,高聚物是添加剂。
精铸模料通常是由上述二种或二种以上原材料按一定比例混合而成的复杂混合物。
配制模料的最终目标是综合各种原材料的优点,实现优势互补,以满足熔模铸造的要求。
值得强调指出的是,液态无析出物应作为模料配制是否成功的基本标志。
3.料分类及特点(模样模料、水溶性模料、特殊用途模料):
①模样蜡:
制作蜡模的蜡,又可分为蜡基模料、树脂基模料、填料模料三种:
A:
蜡基模料:
以石蜡-硬脂酸、石蜡-聚烯烃为代表。
此类模料一般成分比较简单,成本较低。
通常液态下粘度小,便于脱蜡和回收。
蜡膏属多相体系,流动性好,但制成蜡模的质量和尺寸稳定性较差,多与水玻璃制壳工艺配合生产质量要求较低的产品。
B:
树脂基模料:
此类模料一般成分比较复杂,成本较高。
通常液态下粘度较大,不利于脱蜡和回收。
蜡膏属均相体系,流动性较差,但制成蜡模的质量和尺寸稳定性好,多与硅溶胶或硅酸乙酯制壳工艺配合,用于生产质量要求较高的军用或商用精铸件。
国外模料大多属此类型。
C:
填料模料:
在上述二类模料本体中均匀混入一定数量(20%~40%)与之不相溶的固体粉末或水作为填料,用以减小蜡模收缩和缩陷,国外应用较为广泛。
但成本高,液态下粘度大,脱蜡较困难,也不便回收/再生,通常只能一次性使用,故国内很少应用。
②水溶性模料:
遇水溶解或溃散的材料制成的模料,主要用来制作蜡芯,成形蜡模的内腔和孔洞。
有尿素基和聚乙二醇基二种类型,前者价格便宜,通常自由浇注成形,效率低、效果较差,多用于制作要求较低而形状简单的蜡芯;后者价格较贵,可压注成形,效率高、效果好,多用于制作要求较高而形状复杂的蜡芯。
③特殊用途模料(浇道蜡、粘结蜡、修补蜡、样件蜡):
A:
浇道蜡:
专门用来制作浇道的模料。
其特点是熔点较低、粘度小。
脱蜡时能快速流出或渗入型壳中,从而减轻了蜡模膨胀对型壳产生的压力,缓解了型壳开裂的问题。
B:
粘结蜡:
组合模组时将需要连接处涂上这种蜡后便可相互粘结起来。
C:
修补蜡:
在室温下就柔软而具有可塑性,专门用来填补蜡模、浇道表面或蜡模—浇道接合处的缝隙、孔洞或修饰表面的针孔、流线等缺陷。
D:
样件蜡:
这种模料不但坚韧,能经受机械加工过程中必须的装卡、夹持,还具有优良的切削加工性能,可以用刀具方便地制作单件或少量蜡模而无需模具(压型),所以令成本大幅度下降。
4.模料回收和再生:
①蜡基模料(石蜡-硬脂酸)的回收处理:
A:
目的:
除水、除尘、还原皂化物
B:
方法:
沉降分离和过滤以去除水分和粉尘。
酸处理还原皂化物。
C:
预防模料变质的措施:
关键是防止硬脂酸皂化和模料过热。
②树脂基模料的回收处理:
A:
目的:
除尘、脱水
B:
方法:
静置沉降分离,蒸发脱水;
过滤和离心分离。
说明:
传统的脱水方法存在防止模料过热与脱水效率的矛盾。
图示脱水机较好地解决了这一矛盾,脱水温度控制在<110℃。
过滤:
应采用层数>20的多层过滤。
前面的滤网由金属丝编织而成,过滤较粗大的颗粒和氧化树脂;后面的则是一次性使用的纸质纤维材料,过滤细小颗粒。
离心分离:
采用高速离心机将粉尘和水分离出去,获得灰分<0.05%的纯净蜡液,较之于过滤法,此法效率较高,且无需专门除水工序,更适合生产厂家现场使用。
离心机需经常清理,定期清除附着在内壁上的固体沉积物。
③模料回收和再生:
在回收旧蜡中加入适量新的原材料,使其性能经严格检测达到标准规定的要求。
由此所得产品称为再生蜡。
通常必须检测4项性能:
线收缩率、灰分、软化点、针入度。
二.制模工艺相关知识:
1.蜡膏制备:
①蜡基模料制膏方法要点:
蜡液+蜡屑---快速搅拌----保温静置。
②树脂基模料制膏方法要点:
A:
小容积蜡缸:
蜡液长期保温静置
B:
大容积蜡缸:
分区温度控制,慢速搅拌。
说明:
具有足够的制冷能力、恰当的搅拌方法、严格的分区温度控制,以便最终获得温度合适、状态均匀的连续膏条,是树脂基模料制膏的关键。
(下面这张图片为宣传设备的广告图片,说明设备的精良且稳定)
2.制模工艺参数对蜡模表面质量的影响:
①压蜡温度:
与蜡膏物理性能和状态直接相关,控制模料流动充型性能,影响蜡模表面质量;与模料膨胀/收缩总量有关,进而对蜡模表面缩陷产生影响。
②压注压力:
压力是蜡膏流动的直接驱动力。
控制模料流动速度,影响蜡模表面质量,同时,提供压实和补缩压力,提高蜡模表面复制压型型腔的能力,减小缩陷。
③流动速度:
指压型射蜡嘴处蜡膏流动的线速度。
过快造成紊流、喷溅,过慢则造成冷隔。
④充型时间:
指从开始压注到充满压型型腔所需的时间。
它与流动速度有直接关系,但又是二个不同的概念。
蜡模充型通常以快些为好,以提高模料的复形能力和蜡模表面光洁度。
充型之所以宜快,是因为蜡模清晰的轮廓、光滑的表面是在充满型腔的最后瞬间才完成的。
此时,模料必须保持足够的流动性,表面任何部位都不能结有硬皮。
说明:
以适当的流动速度较快地充型,这就存在一个注蜡口大小和型腔体积及蜡模壁厚相匹配的问题。
⑤压型温度:
对蜡模冷却速度有直接影响,与蜡模表面清晰完整,是否产生缩陷、变形或开裂相关。
3.制模工艺参数对蜡模尺寸的影响
①压蜡温度:
温度越高收缩越大,蜡基模料尤甚。
②压注压力:
压力增大收缩率减小。
压力小时影响大,压力超过1.2MPa后影响不明显。
③流动速度:
流动速度对蜡模尺寸无明显影响。
④充型时间:
充型越快收缩越大。
⑤压型温度:
压型温度越高收缩越大。
⑥起模时间:
起模时间越长,收缩率越小。
说明:
工艺参数主要靠设备精度来保障,注意选择设备时要谨慎!
!
三、制模设备:
1.制模设备分类:
压蜡设备常分为气压和液压两大类型。
一般认为气压设备结构较简单,价格便宜,但压力受限制(<0.6MPa),主要适用于蜡基模料;而液压设备价格较贵,但压力大(通常>1MPa),结构紧凑,主要适用于树脂基模料。
①气压压蜡机(气力式压蜡机、气动活塞式压蜡机):
A:
气力式压蜡机:
B:
气动活塞式压蜡机
②液压压蜡机(换缸压蜡机、免换蜡缸压蜡机、全自动压蜡机)
A:
换缸压蜡机:
B:
免换蜡缸压蜡机:
C:
全自动压蜡机:
2.制模设备控制系统:
控制系统是压蜡机的神经中枢,也是评判其优劣的关键所在。
①温度控制:
制模过程温度控制要求准确可靠(控温精度±0.25℃),反应灵敏。
例如,先进的压蜡机压蜡温度显示的应是蜡温而不是油温,设置改变后响应要快(1℃/min)。
压型温度应显示出压型中靠近型腔部位的温度,而不仅是压板温度。
②压力和流动控制:
近期目标是实现压力和流动相互独立,各自单独控制。
中期目标是实现根据流速变化进行压力补偿,同时实现分段式压力控制(关键是找准切换点)。
长期目标是实现计算机实时控制。
四、熔模铸造型芯技术:
1.熔模铸造型芯的基本要求(耐火度、热膨胀率、化学稳定性、强度、易脱除):
①耐火度:
型芯应具有足够高的耐火度,以保证它在铸造高温下不软化和变形,一般情况下用于精铸铸钢件的型芯耐火度应达到1400℃以上。
②热膨胀率:
型芯在加热过程中热膨胀应小而均匀,以免造成型芯开裂或变形。
一般来说其热膨胀系数应小于4×10-6(1/℃)。
③化学稳定性:
型芯在高温下与金属液不产生化学反应,避免污染合金,防止铸件表面产生化学粘砂或反应性气孔。
④强度:
型芯应具有足够的室温和高温强度,保证压射蜡模时型芯不折断,浇注时能承受高温金属液的冲击、浮力和压力。
⑤易脱除性:
铸件铸成后通常型芯都是要脱除的。
为了便于脱除,型芯必须有相当大的孔隙率(约20%~40%),而不能是完全致密的。
这是陶瓷型芯跟一般陶瓷制品的重要区别。
2.型芯分类和特点(8种):
①热压注陶瓷型芯:
A:
成形方法:
在耐火粉料中加入热塑性材料(如蜡)为增塑剂制成陶瓷料浆,用热压注法制成型芯坯体,再经高温烧结成型芯。
B:
脱芯方法:
化学腐蚀。
C:
应用:
内腔形状复杂而精细的高温合金和不锈钢铸件,定向凝固和单晶空心叶片。
说明:
这种型芯做的较好的厂家广东佛山非特新材料有限公司。
②传递成形陶瓷型芯:
A:
成形方法:
在陶瓷粉末中混入低温(热固性树脂)和高温粘结剂,高压压入热芯盒中成形。
其优点是不用烧结。
B:
脱芯方法:
化学腐蚀。
C:
应用:
主要适合真空熔铸高温合金铸件。
③灌浆成形型芯(以硅酸乙酯水解液为粘结剂)-1:
A:
成形方法:
陶瓷粉料中加入粘结剂(硅酸乙酯水解液)和固化剂(例如氧化钙、氧化镁、醋酸铵、乙醇胺等),灌注入芯盒后自行固化成形。
B:
脱芯方法:
机械方法。
C:
应用:
内腔形状较宽厚的铸件。
③灌浆成形型芯(以磷酸盐为粘结剂)-2:
A:
成形方法:
陶瓷粉