汽车主减速器设计跟研究探究文档.docx
《汽车主减速器设计跟研究探究文档.docx》由会员分享,可在线阅读,更多相关《汽车主减速器设计跟研究探究文档.docx(23页珍藏版)》请在冰豆网上搜索。
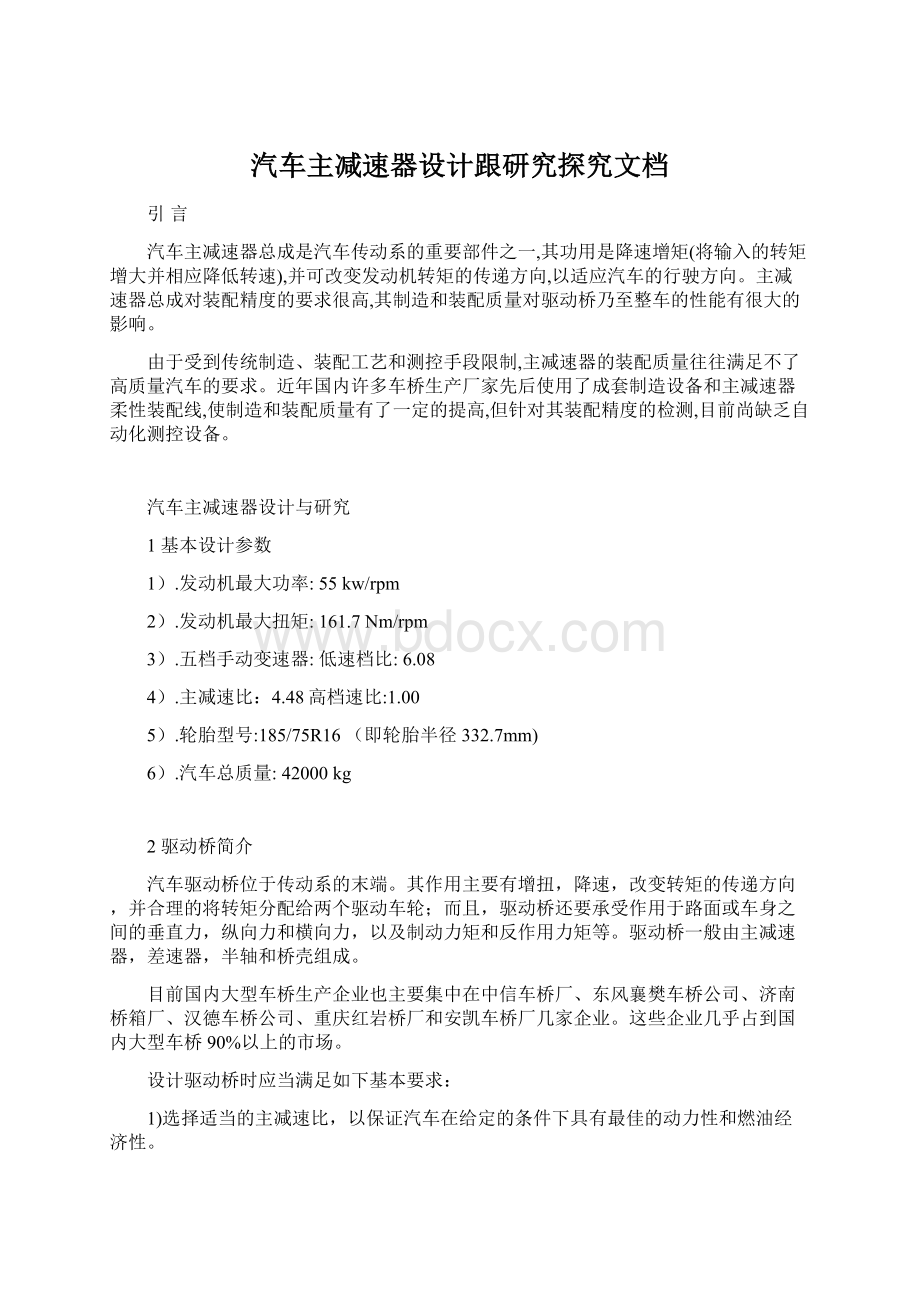
汽车主减速器设计跟研究探究文档
引言
汽车主减速器总成是汽车传动系的重要部件之一,其功用是降速增矩(将输入的转矩增大并相应降低转速),并可改变发动机转矩的传递方向,以适应汽车的行驶方向。
主减速器总成对装配精度的要求很高,其制造和装配质量对驱动桥乃至整车的性能有很大的影响。
由于受到传统制造、装配工艺和测控手段限制,主减速器的装配质量往往满足不了高质量汽车的要求。
近年国内许多车桥生产厂家先后使用了成套制造设备和主减速器柔性装配线,使制造和装配质量有了一定的提高,但针对其装配精度的检测,目前尚缺乏自动化测控设备。
汽车主减速器设计与研究
1基本设计参数
1).发动机最大功率:
55kw/rpm
2).发动机最大扭矩:
161.7Nm/rpm
3).五档手动变速器:
低速档比:
6.08
4).主减速比:
4.48高档速比:
1.00
5).轮胎型号:
185/75R16(即轮胎半径332.7mm)
6).汽车总质量:
42000kg
2驱动桥简介
汽车驱动桥位于传动系的末端。
其作用主要有增扭,降速,改变转矩的传递方向,并合理的将转矩分配给两个驱动车轮;而且,驱动桥还要承受作用于路面或车身之间的垂直力,纵向力和横向力,以及制动力矩和反作用力矩等。
驱动桥一般由主减速器,差速器,半轴和桥壳组成。
目前国内大型车桥生产企业也主要集中在中信车桥厂、东风襄樊车桥公司、济南桥箱厂、汉德车桥公司、重庆红岩桥厂和安凯车桥厂几家企业。
这些企业几乎占到国内大型车桥90%以上的市场。
设计驱动桥时应当满足如下基本要求:
1)选择适当的主减速比,以保证汽车在给定的条件下具有最佳的动力性和燃油经济性。
2)外廓尺寸小,保证汽车具有足够的离地间隙,以满足通过性的要求。
3)齿轮及其他传动件工作平稳,噪声小。
4)在各种载荷和转速工况下有较高的传动效率。
5)具有足够的强度和刚度,以承受和传递作用于路面和车架或车身间的各种力和力矩;在此条件下,尽可能降低质量,尤其是簧下质量,减少不平路面的冲击载荷,提高汽车的平顺性。
6)与悬架导向机构运动协调。
7)结构简单,加工工艺性好,制造容易,维修,调整方便。
3驱动桥结构形式及选择
驱动桥的结构型式按工作特性分,可以归并为两大类,即非断开式驱动桥和断开式驱动桥。
当驱动车轮采用非独立悬架时,应该选用非断开式驱动桥;当驱动车轮采用独立悬架时,则应该选用断开式驱动桥。
独立悬架驱动桥结构较复杂,但可以大大提高汽车在不平路面上的行驶平顺性。
3.1非断开式驱动桥
普通非断开式驱动桥,结构简单、造价低廉、工作可靠,广泛用在各种载货汽车、客车和公共汽车上,在多数的越野汽车和部分轿车上也采用这种结构。
他们的具体结构、特别是桥壳结构虽然各不相同,但是有一个共同特点,即桥壳是一根支承在左右驱动车轮上的刚性空心梁,齿轮及半轴等传动部件安装在其中。
这时整个驱动桥、驱动车轮及部分传动轴均属于簧下质量,汽车簧下质量较大,这是它的一个缺点。
3.2断开式驱动桥
断开式驱动桥区别于非断开式驱动桥的明显特点在于前者没有一个连接左右驱动车轮的刚性整体外壳或梁。
断开式驱动桥的桥壳是分段的,并且彼此之间可以做相对运动,所以这种桥称为断开式的。
断开式驱动桥的簧下质量较小,又与独立悬挂相配合,致使驱动车轮与地面的接触情况及对各种地形的适应性比较好,减小车轮和车桥上的动载荷及零件的损坏。
但是,由于与其相配的独立悬挂的结构复杂,故这种结构主要见于对行驶平顺性要求较高的一部分轿车及一些越野汽车上,且后者多属于轻型以下的越野汽车或多桥驱动的重型越野汽车。
由于本设计车辆为小型客车,所以选用断开式驱动桥。
4主减速器的结构设计
4.1主减速器的齿轮类型及选择
a螺旋锥齿轮b双曲面齿轮c圆柱齿轮传动d螺杆传动
图1.1主减速器的几种齿轮类型
主减速器的齿轮有螺旋锥齿轮,双曲面齿轮(见图1.2),圆柱齿轮和蜗轮蜗杆等形式。
在此选用螺旋锥齿轮传动,其特点是主、从动齿轮的轴线垂直交于一点。
由于轮齿端面重叠的影响,至少有两个以上的轮齿同时啮合,因此可以承受较大的负荷,加之其轮齿不是在齿的全长上同时啮合,而是逐渐有齿的一端连续而平稳的地转向另一端,所以工作平稳,噪声和振动小。
而螺旋锥齿轮还存在一些缺点,比如对啮合精度比较敏感,齿轮副的锥顶稍有不吻合就会使工作条件急剧变坏,并加剧齿轮的磨损和使噪声增大;但是当主传动比一定时,主动齿轮尺寸相同时,双曲面齿轮比相应的螺旋锥齿轮小,从而可以得到更大的离地间隙,有利于实现汽车的总体布置。
另外,螺旋锥齿轮与双曲面锥齿轮相比,具有较高的传动效率,可达99%。
(a)螺旋锥齿轮传动;(b)双曲面齿轮传动
图1.2螺旋锥齿轮与双曲面齿轮传动
本设计选择格里森式螺旋锥齿轮(弧齿),主从动齿轮螺旋角相等。
4.2主减速器的减速形式
为了满足不同的使用要求,主减速器的结构形式也是不同的(见图1.3)。
按参加减速传动的齿轮副数目分,有单级式主减速器和双级式主减速器、双速主减速器、双级减速配以轮边减速器等。
双级式主减速器应用于大传动比的中、重型汽车上。
单级式主减速器应用于轿车和一般轻、中型载货汽车。
单级主减速器由一对圆锥齿轮组成,具有结构简单、质量小、成本低、使用简单等优点。
由于i0=4.48<6,所以采用单级主减速器。
图1.3单级主减速器(左)、双级主减速器(右)
4.3主减速器主减速器主,从动锥齿轮的支承形式
主动锥齿轮的支承形式可分为悬臂式和跨置式两种。
悬臂式安装通常在负荷较小的小客车和轻型载荷汽车上采用,所以本设计采用悬臂式的主动锥齿轮支撑方式(见图1.4)。
采用悬臂式安装时,为保证齿轮的刚度,主动齿轮的轴颈应尽可能的加大,并使两轴承间距b比悬臂距离c大2.5倍以上,同时b不能小于所支承的齿轮大端节圆直径的70%。
图1.4主动锥齿轮悬臂式
从动锥齿轮采用圆锥滚子轴承支承(见图1.5)。
为了增加支承刚度,两轴承的圆锥滚子大端应向内,以减小尺寸c+d。
为了使从动锥齿轮背面的差速器壳体处有足够的位置设置加强肋以增强支承稳定性,c+d应不小于从动锥齿轮大端分度圆直径的70%。
为了使载荷能均匀分配在两轴承上,应是c等于或大于d。
图1.5从动锥齿轮支撑形式
5主减速器齿轮参数设计与强度校核
5.1主减速器齿轮计算载荷的确定
5.1.1按发动机最大转矩和最低挡传动比确定从动锥齿轮的计算转矩Tce(N·m):
(1-1)
式中:
iTL—发动机至所计算的主减速器从动锥齿轮之间的传动系的最低挡传动比,iTL=ig1·i0=6.018×4.48=26.96;
Ttpd—发动机的输出的最大转矩,根据第三章取161.7N·m;
ηT—传动系上传动部分的传动效率,在此取0.93;
n—该汽车的驱动桥数目在此取1;
Kd—由于猛结合离合器而产生冲击载荷时的超载系数,对于一般的载货汽车,矿用汽车和越野汽车以及液力传动及自动变速器的各类汽车取Kd=1.0,当性能系数fp>0时可取Kd=2.0,fp根据式(1-2)可得;
(1-2)
式中:
M—汽车满载时的总质量,在此取42000kg;
fP—汽车的性能系数。
所以根据上式可得:
=50.65>16
fp=-0.3465<0即Kd=1.0
由以上各参数可求Tce:
==4054.27N·m
5.1.2按驱动轮打滑转矩确定从动锥齿轮的计算转矩Tcs(N·m):
(1-3)
式中:
G2—汽车满载时一个驱动桥给水平地面的最大负荷,预设后桥所承载23692.3N的负荷;
φ—轮胎对地面的附着系数,对于安装一般轮胎的公路用车,取φ=0.85;对于越野汽车取1.0;对于安装有专门的防滑宽轮胎的高级轿车,计算时可取1.25;
rr—车轮的滚动半径,在此滚动半径为0.3327m;
ηLB,iLB—分别为所计算的主减速器从动锥齿轮到驱动车轮之间的传动效率和传动比,ηLB取0.9,由于没有轮边减速器iLB取1.0。
所以根据上式可得:
==7444.52N·m
5.1.3按汽车日常行驶平均转矩确定从动锥齿轮的计算转矩Tcf(N·m):
对于公路车辆来说,使用条件较非公路车辆稳定,其正常持续的转矩根据所谓的平均牵引力的值来确定:
(1-4)
式中:
Ga—汽车满载时的总重量,取4200×9.8=41160N;
GT—所牵引的挂车满载时总重量(N),但仅用于牵引车的计算,此处为0;
fR—道路滚动阻力系数,取0.012;
fH—汽车正常行驶时的平均爬坡能力系数,对于货车公交车可取0.05~0.09,在此取0.07;
fP—汽车的性能系数在此取0。
所以根据上式可得:
即,Tcf==1247.67N·m
注意:
当计算锥齿轮最大应力时,计算转矩取前面两种的较小值,即;当计算锥齿轮的疲劳寿命时,取。
5.2主减速器锥齿轮的主要参数选择
主减速器锥齿轮的主要参数有主、从动齿轮的齿数z1和z2,从动锥齿轮大端分度圆直径d2、端面模数mt、主从动锥齿轮齿面宽b1和b2、中点螺旋角β、法向压力角α等。
5.2.1主、从动锥齿轮齿数z1和z2
选择主、从动锥齿轮齿数时应考虑如下因素:
1)为了磨合均匀,z1,z2之间应避免有公约数。
2)为了得到理想的齿面重合度和高的轮齿弯曲强度,主、从动齿轮齿数和应不小于40。
3)为了啮合平稳,噪声小和具有高的疲劳强度对于商用车z1一般不小于6。
4)主传动比i0较大时,z1尽量取得小一些,以便得到满意的离地间隙。
5)对于不同的主传动比,z1和z2应有适宜的搭配。
查阅资料可知对于传动比为i0=4.48的汽车来说,主动齿轮的齿数初选z1=9,从动齿轮齿数z2=40。
5.2.2主、从动锥齿轮节圆直径及端面模数的选择
对于单级主减速器,增大尺寸d2会影响驱动桥壳的离地间隙,减小d2又会影响跨置式主动齿轮的前支承座的安装空间和差速器的安装。
d2可根据经验公式初选,即:
(1-5)
式中:
KD2—直径系数,一般取13.0~16.0
Tc—从动锥齿轮的计算转矩(N·m),为Tce和Tcs中的较小者
所以Tc=4054.27N·m。
所以d2=(13.0~16.0)=(207.3~255.1)mm
初选d2=230mm则mt=d2/z2=230/40=5.75mm
查阅《机械设计通用手册》,mt选取6,则d2=240mmd1=mtz1=54mm
同时,mt还应满足:
=(1-6)
式中:
模数系数Km=(0.3~0.4)
此处,mt=(0.3~0.4)=(4.78~6.38)。
所以模数mt=6符合条件
5.2.3主,从动锥齿轮齿面宽b1和b2
锥齿轮齿面过宽并不能增大齿轮的强度和寿命,反而会导致因锥齿轮轮齿小端齿沟变窄引起的切削刀头顶面过窄及刀尖圆角过小,这样不但会减小了齿根圆角半径,加大了集中应力,还降低了刀具的使用寿命。
此外,安装时有位置偏差或由于制造、热处理变形等原因使齿轮工作时载荷集中于轮齿小端,会引起轮齿小端过早损坏和疲劳损伤。
另外,齿面过宽也会引起装配空间减小。
但齿面过窄,轮齿表面的耐磨性和轮齿的强度会降低。
对于从动锥齿轮齿面宽b2,推荐不大于节锥距R的0.3倍,R==123mm
b2≤0.3R=36.9mm,而且b2应满足b2≤10mt=60mm,一般推荐采用:
b2=0.155D2=0.155×240=37.2mm取b2=36mm
一般习惯使锥齿轮的小齿轮齿面宽比大齿轮稍大,使其在大齿轮齿面两端都超出一些,通常小齿轮的齿面加大10%较为合适,在此取b1=40mm
5.2.4中点螺旋角β
螺旋角沿齿宽是变化的,轮齿大端的螺旋角最大,轮齿小端螺旋角最小。
弧齿锥齿轮副的中点螺旋角是相等的,选β时应考虑它对齿面