带传动测试实验台机械结构设计文档格式.docx
《带传动测试实验台机械结构设计文档格式.docx》由会员分享,可在线阅读,更多相关《带传动测试实验台机械结构设计文档格式.docx(20页珍藏版)》请在冰豆网上搜索。
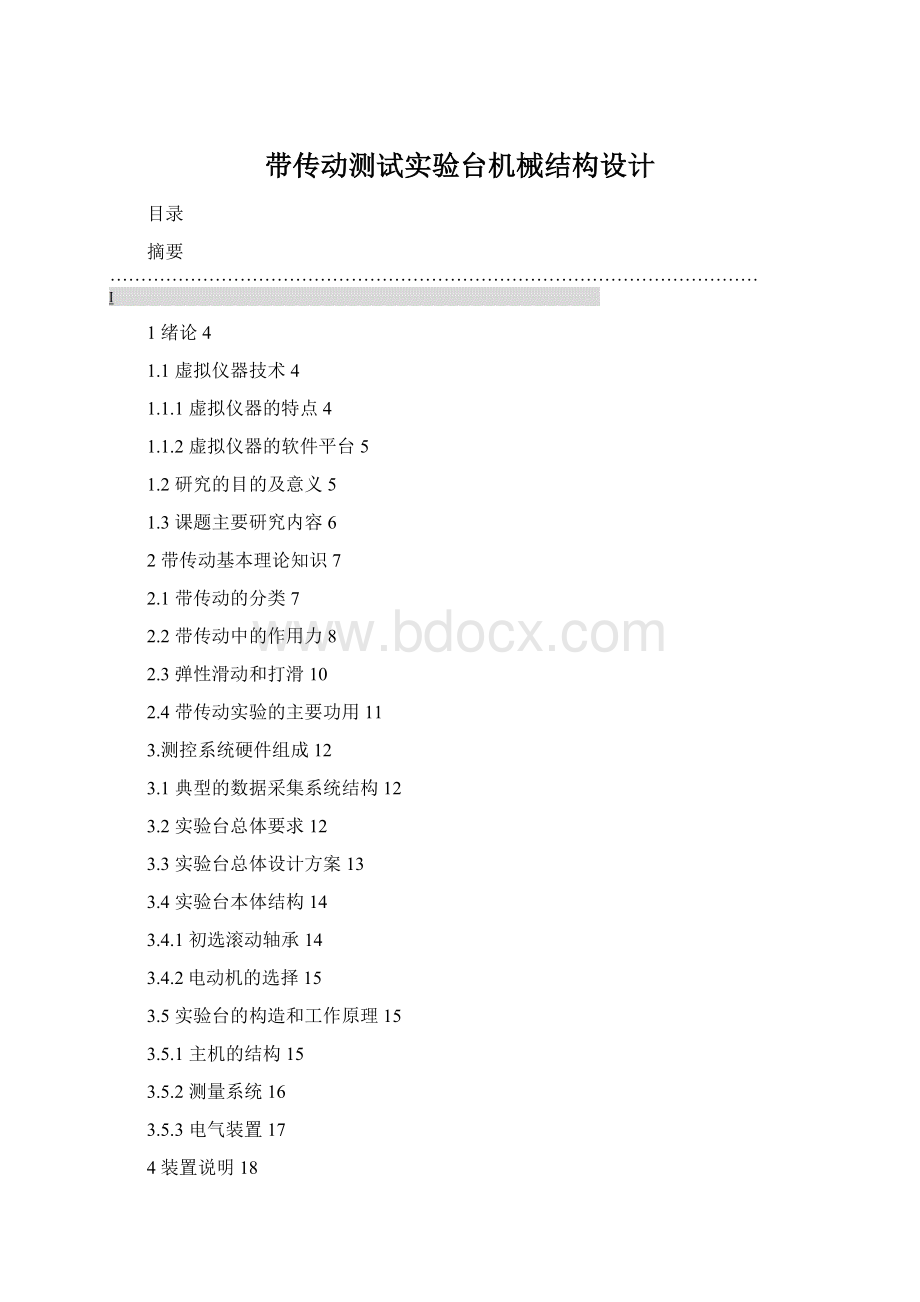
实验室原有的带传动试验台由于试验精度低、效率差,已不能适应教学改革的需要。
为此学校设立了基于虚拟仪器的带传动试验台的科研项目。
本论文就是以此项目为研究课题,详细论述了整个试验台改造的总体方案和工作原理。
在此基础上主要进行了机械结构的设计,进行了驱动电动机、支撑轴承等部件的选择,绘制了实验台总体装配图和零件图。
关键词:
带传动试验台机械结构直流电动机
StructureDesignofBeltDriveTest-Bed
Student:
Hao-CuipingDirector:
Song-Jian
Abstract:
Thebeltdriveexperimentisveryimportanttoengineeringstudentsinlearningthecurriculaof"
machinedesign"
.Throughtheexperimentthestudentscancomprehendtheprincipleofthebeltdriveandunderstandtheoperateperformanceofthetest-bed,creatinggoodfoundationoftheapplicationlater.Buttheoriginalbeltdrivetest-bedinthelaboratorydon'
tadapttotherequestofthereformineducationforitsinaccuracyandinefficiency,sothelaboratoryestablishedtheprojectsofreformingthetest-beds.Themethodandprocessofthereformarediscussedindetailinthisthesiswhichbasedontheprojects.Accordingtothecurrentconditionofthelaboratoryandtherequestoftheprojects,thispaperanalysesandcontrastssomereformproject,thenusingthemicrocomputerandsinglechipcomputerconstitutesthetwostagecontrolsystem.Themicrocomputerisusedtomonitorthewholesystemandreprocessthedata.
Keywords:
DriveTest-Bed,StructureDesign,DCmotor
1绪论
1.1虚拟仪器技术
所谓虚拟仪器(VI,VirtualInstrument)是指通过应用程序将通用计算机与功1986年美国国家仪器公司(NI,NationalInstrnunents)首能化模块结合起来,用户可以利用计算机强大的数据处理、存储、图形环境和在线帮助功能,建立图形化界面的虚拟仪器软面板,完成对仪器的控制、数据分析、存储和显示,改变传统仪器的使用方式,提高仪器的功能和使用效率,大幅度降低仪器的价格,且使用户可以根据自己的需要定义仪器的功能[1]。
1.1.1虚拟仪器的特点
与传统仪器相比,虚拟仪器打破了传统仪器的“万能”功能概念,充分利用计算机技术;
强调“软件就是仪器”的新概念,软件在某种程度上可以完成传统仪器不可能实现的硬件测试功能;
仪器或系统的功能、规模可以由用户自己定义,虚拟仪器的开放性和功能软件的模块化,使得组建系统变得更加灵活、简单。
虚拟仪器是建立在当今世界最新的计算机和数据采集技术基础上的,技术更新很快。
虚拟仪器具有以下性能优点:
1软件是虚拟仪器的核心。
虚拟仪器的硬件确立后,它的功能主要是通过软件来实现的,所以美国国家仪器公司就曾提出一个著名的口号:
软件就是仪器。
2虚拟仪器的性价比高。
一方面,虚拟仪器能同时对多个参数进行实时高效的测量,而且,用户也可以随时根据需要调整虚拟仪器的功能,大大缩短了仪器在改变测量对象时的更新周期。
另一方面,采用虚拟仪器还可以减少测试系统的硬件环节,从而降低系统的开发成本和维护成本,因此,使用虚拟仪器比传统仪器更经济。
3虚拟仪器的出现,缩短了仪器厂商与用户之间的距离。
虚拟仪器使得用户能够根据自己的需要定义仪器的功能,利用虚拟仪器,用户可以组建更好的测试系统,并且更容易增强系统的功能。
由于PC机能提供远胜于仪器内部的处理能力,因此,借助于一台通用数据采集系统(或板卡),用户就可以通过软件构造几乎任意功能的仪器。
4虚拟仪器具有良好的人机界面。
在虚拟仪器中,测控操作是通过计算机屏幕上的、与传统仪器面板相似的友好图形界面来实现的。
5虚拟仪器具有和其它设备互联的能力。
如和总线或现场总线等的接口能力,此外,还可以将虚拟仪器接入网络,以实现对现场生产的监控和管理。
6虚拟仪器的硬、软件都具有开放性、模块化、可重复使用及互换性等特点。
因此,用户可以根据自己的需要灵活组合,大大提高了使用效率,减少了投资。
当然,虚拟仪器的特点还不止这些,作为新型仪器,还有许多传统仪器无法比拟的地方。
这使得虚拟仪器的应用领域非常广泛[2]。
1.1.2虚拟仪器的软件平台
虚拟仪器软件开发平台直接决定了虚拟仪器可实现的功能,开发方式,易用性和可扩充性。
虚拟仪器的开发软件通常可以分为通用软件和专用软件。
通用软件就是我们常见的高级汇编语言,比如VisualC++,VB,Delphi,Java等。
使用通用软件进行开发具有较高的自由度,可以定义出具有独特个性的虚拟仪器,但是开发周期往往比较长,开发难度比较大。
而专用软件一般是指专业的图形化编程软件,比如NI公司的LabVIEW、LabWindows/CVI或者HP公司的VEE等。
它们都向开发者提供了友好图形化开发界面,并且提供了大量的控件和仪器驱动程序可使用。
开发者甚至可以并不了解某种具体的开发语言就可以开发出一些简单的虚拟仪器。
相对而言,使用专用软件开发虚拟仪器系统编程容易,开发周期短。
本课题选用的LabVIEW(LaboratoryVirtualInstrumentEngineeringWorkBench)被称为“科学家与工程师的语言”,是直观的前面板与流程图式编程方法的结合,是构建虚拟仪器的理想工具。
LabVIEW不仅为测试、测量以及过程控制领域提供了大量仪器面板对象,而且用户还可以方便地将现有的控制对象改成适合自己工作领域的控制对象。
LabVIEW基于数据流编译型图形编程环境,解决了其它按解释方式工作的图形编程环境速度慢的问题。
LabVIEW提供了功能强大的函数库,从低层的I/O接口控制子程序,到大量的仪器驱动程序,从基本的数学函数、字符串处理函数到高级的分析库,均可供用户直接调用。
此外,LabVIEW还支持Windows95/98/NT,Macintosh,HP等操作系统平台,在不同平台上开发的应用程序可直接进行移植;
提供了DLL接口和CIN接口,使用户在LabVIEW平台上能调用其他软件平台编译的模块;
提供对OLE的支持[3]。
正是由于LabVIEW的众多优点,使得它已经成为在数据采集、检测、数据分析等方面领先的开发平台,在世界范围内得到广泛应用。
1.2研究的目的及意义
在工科院校中,实验是一种重要的教学手段。
学生通过做试验,可以加深对所学知识的理解,增强学习的兴趣,提高动手能力,锻炼在实践中发现问题、分析问题和解决问题的能力。
大部分工科院校中的机械设计基础实验,所用的测试仪器、设备数量少,不能满足学生需要,且设备比较陈旧,更新慢。
传统仪器下的实验教学,已严重滞后于信息时代和工程实际的需要。
带传动是机械传动中广泛使用的重要方式,也是工科院校机械设计课程中的基础实验之一。
主要分析滑动率和传动效率随负载变化的情况,通常在保持主动轮转速和带预紧力不变的前提下,用逐渐加载的方法,不断增加带传动的有效拉力,使带在轮上的弹性滑动不断增加,传动效率也随之变化。
传统的带传动实验方法多采用“传感器+二次仪表”的模式,靠人工测试和控制。
这种仪器功能单一,只有测量显示数据功能,不能直接得到滑动率和传动效率随负载变化的特性曲线,需要自己根据记录下的数据手工描绘变化趋势;
而且这些仪器功能模块全部都是以硬件(或固化的软件)的形式存在,无论是开发还是应用,都缺乏灵活性。
我校现用的带传动实验台是由单片机控制,LED显示,数据经RS232串口传输到计算机进行数据处理得到特性曲线的实验系统,使得系统分别有一个独立的测控面板和一个数据处理面板。
不仅交互性差,而且测量误差大,目前已经出现实验结果和理论相悖的情况。
所以有必要研制一种新的带传动实验台来替代原来的实验台。
随着微电子技术、计算机技术、软件技术、网络技术的高度发展及其在仪器仪表中的应用,仪器仪表结构将冲破传统思维模式,发生质的变化。
电子测量仪器的发展在经历了模拟仪器;
数字化仪器;
智能仪器后,虚拟仪器(VI,VirtualInstruments)成为测量仪器发展的最新阶段。
虚拟仪器可视化的编程技术为人与试验台的交互开启了方便之门。
把虚拟仪器技术用于带传动实验系统,我们所需要的只是一些必要的硬件加上通用计算机,利用软件就可以大大突破传统仪器在数据处理、显示、传送和存储等方面的限制,达到传统仪器无法比拟的使用效果,提高系统的自动化程度。
我们还可以随心所欲地根据自己的要求设计自己的仪器系统,满足多种多样的应用需求。
此外,该试验台的建成将较大程度地提高我系教学、科研的实验手段的现代化水平,能很好地为人才培养和科学研究服务。
在新型的控制方案中将充分体现计算机资源和数字化技术的灵活运用。
1.3课题主要研究内容
本课题将以应用研究为目的,针对带传动实验要求,对整个带传动测控系统进行软硬件设计与集成。
课题主要包括以下研究内容:
(1)带传动主动轮转速的闭环控制;
(2)无级加载方式的选择与实现;
(3)运动参数的实时测量方式的选择与实现;
(4)实验系统的软件设计与系统集成。
2带传动基本理论知识
2.1带传动的分类
带传动是通过中间挠性曳引元件传递运动和动力的一种机械传动。
它使用的挠性曳引元件是各种有较大弹性的传动带。
按工作原理,带传动分为摩擦型普通带传动和啮合型同步带传动。
普通带传动的主要优点是:
有缓冲和吸振作用;
运行平稳、噪声小;
结构简单,制造成本低;
可通过增减带长以适应不同的中心距要求。
普通带传动过载时带会在带轮上打滑,对其他机件有保护作用。
它的缺点是:
传动带的寿命较短;
传递相同圆周力时,外廓尺寸和作用在轴上的载荷比啮合传动大;
带与带轮接触面间有相对滑动,不能保证准确的传动比。
因而普通带传动一般仅用来传递动力。
同步带传动中带和带轮是靠啮合传动的,因而无相对滑动,能克服上述缺点,用来传递动力。
但是同步带传动对制造安装要求较高[4]。
根据横截面形状,摩擦型普通带传动可分为平带传动,V带传动和特殊截面带(如多楔带、圆带等)传动三大类,见图2.1。
平带的横截面为扁平矩形,其工作面是与轮面相接触的内表面。
V带的横截面为等腰梯形,其工作面是与轮槽相接触的两侧面,带与轮槽底面不接触。
由于轮槽的楔形效应,预拉力相同时,V带传动较平带传动能产生更大的摩擦力,故具有较大的牵引能力,在一般机械传动中应用最广。
多楔带是平带和V带的组合结构,其楔形部分嵌入带轮上的楔形槽内,靠楔面摩擦工作,摩擦力和横向刚度较大,兼有平带和V带的优点,常用于传递功率较大而又要求结构紧凑的场合,也可用于载荷变动较大或有冲击载荷的传动。
圆带的牵引能力小,一般用于轻、小型机械,如缝纫机等。
a)平带b)V带c)多楔带d)圆带
图2.1带横截面形状
根据带的布置型式可分为开口传动(两轴平行,同向回转)、交叉传动(两轴平行,反向回转)和半交叉传动(两轴交错,不能逆转),见图2.2。
图2.2带布置形式
考虑到制造和安装等要求,本实验系统采用普通平带开口传动方式。
2.2带传动中的作用力
带传动有主动轮、从动轮和传动带组成。
安装时,应给传动带施加一定的初拉力,靠带与带轮间的摩擦力来传递运动和动力。
带在工作前张紧,其两边拉力均为F0(图2.3a),F0称为初拉力。
工作时,由于要克服工作阻力,带在绕上主动轮的一边被进一步拉紧,其拉力F0增大到F1,F1称为紧边拉力;
带的另一边被放松,其拉力由F0减小到F2,F2称为松边拉力(图2.3b)。
a)b)
图2.3带的两边拉力
带的两边拉力之差,称为带传动的有效拉力F,即
F=F1-F2(2-1)
有效拉力F(N)与带传动传递的功率P(KW)及带速v(m/s)的关系为
(2-2)
该式说明,带速一定时,有效拉力越大,则带传动传递的功率也越大,即带传动的工作能力越强[5]。
带的有效拉力等于带轮接触弧上摩擦力的总和。
在一定条件下,摩擦力有一极限值,当需要传递的有效拉力超过该值时,带就会在轮面上打滑。
打滑是带传动的主要失效形式之一。
带工作时松、紧边拉力不等,但总长度不变,故紧边增加的长度与松边减少的长度相等,假设带的材料服从胡克定律,则紧边增加的拉力与松边减少的拉力相等。
即
F1-F0=F0-F2
F1+F2=2F0(2-3)
图2.4带的受力分析
取一微带段dl(上图2.4),带上各力的平衡条件为垂直方向
中,dF是紧边拉力增量;
为带轮给微带段的正压力;
q为带的线质量。
取dl=Rda,
≈
略去二阶无穷小,上式为
水平方向
中,
为带与带轮间的摩擦因子。
取
≈1,得
在摩擦力的极限状态即将要打滑时,积分上式,得
(2-4)
中,a为包角,即带与带轮接触弧所对应的中心角;
e为自然对数的底[6]。
若带速v<
10m/s,则通常可忽略离心力qv2,此时上式简化为F1/F2=
即为著名的欧拉公式。
联立式2-1、2-3和2-4,可得反映带传动工作能力的最大有效拉力为Fmax,即
(2-5)
该式说明:
1)最大有效拉力与初拉力F0成正比。
控制初拉力对带传动的设计和使用是很重要的。
F0过小不能传递所需载荷,而且容易颤动;
F0过大使带的磨损增加,寿命减短。
2)最大的有效拉力随包角
、摩擦因子
(与带、带轮的材料及工况有关)的增大而增大,通常设计时要求
≥1200,本系统
=1800。
3)离心力qv2使最大有效拉力减小[7],本系统由于带速v<
10m/s,故可忽略离心力的影响[8]。
2.3弹性滑动和打滑
带是弹性体,在拉力作用下会产生弹性伸长。
由于紧边拉力大于松边拉力,所以紧边的弹性伸长量必然大于松边的弹性伸长量。
如图2.5所示,带在A1点绕上主动轮到B1点离开的过程中,带所受拉力由F1逐渐降至F2,其弹性伸长量也随之减小,带在带轮上微微向后收缩,而主动轮的圆周速度v1保持不变,所以带的速度逐渐落后于主动轮的圆周速度,从绕上主动轮时的速度v1逐渐降至v2,在带和主动轮之间局部出现相对滑动。
这种现象亦发生在从动轮上,当带在A2点绕上从动轮到B2点离开的过程中,带以速度v2绕上从动轮时,使从动轮以圆周速度v2转动,由于带从松边过渡到紧边,弹性伸长量逐渐增大,使带微微向前拉伸,即带的速度超前于从动轮的圆周速度,带和从动轮之间局部出现相对滑动。
这种因带的两边拉力不等而使带弹性变形量不等,引起带与带轮之间局部微小的相对滑动称为弹性滑动[9]。
由于带传动工作时,紧边和松边的拉力不等,所以弹性滑动是不可避免的。
带在带轮上相对滑动的方向
图2.5带传动的弹性滑动
弹性滑动除造成功率损失和带的磨损外,还导致从动轮的圆周速度v2低于主动
轮的圆周速度v1,其降低程度用滑动率ε表示
(2-6)
考虑弹性滑动影响的传动比为
(2-7)
其中,
、
为主、从动轮的转速;
为主、从动轮直径。
滑动率ε反映了弹性滑动的大小,而弹性滑动的大小与传递载荷的大小及带的结构、材料等因素有关,通常不能得到恒定的ε值,一般可取1%~2%,粗略计算时可忽略不计。
实际传动比不是常数。
弹性滑动和打滑是两个截然不同的概念。
弹性滑动是由带工作时紧边和松边存在拉力差,使带的两边弹性变形量不相等,从而引起的带与轮之间局部而微小的相对滑动,这是带传动在正常工作时固有的特性,因而是不可避免的。
打滑则是由于过载引起的带在带轮上的全面滑动。
打滑时带的磨损加剧,从动轮转速急剧降低甚至停止运动,致使传动失效。
打滑是不希望产生的[10]。
2.4带传动实验的主要功用
在带传动实验中,当负载达到或超过临界承载能力时,则带与带轮间就发生显著的相对滑动,即产生打滑。
打滑将使带的磨损加剧,从动轮转速急剧降低,甚至使传动失效。
因此,在实际生产中,必须明确带传动在什么状况下会产生打滑。
那么,通过带传动实验系统准确测出打滑时的速度及载荷,则是关键所在。
本实验系统就是分析带传动过程中的弹性滑动和打滑现象;
掌握滑动率和机械效率的测试原理和方法;
了解改变预紧力对带传动能力的影响。
其中滑动率由(2-6)式得出:
(2-8)
为了方便制造安装和计算,取主、从动轮直径相等。
传动效率
(2-9)
—主动轮、从动轮的功率;
—主、从动轮的转矩;
—主、从动轮的转速。
因此,只需测试主、从动轮的转速,转矩就可以计算出滑动率
和传动效率
。
事实上,带传动的滑动率和传动效率并不是常数,而是随传递功率大小的改变而变化。
为寻求其变化规律,通常在保持主动轮转速和带预紧力不变的前提下,用逐渐加载的方法,不断增加带传动的有效拉力,使带在轮上的弹性滑动不断增加,从动轮的转速不断降低,传动效率也随之变化[11]。
3测控系统硬件组成
3.1典型的数据采集系统结构
基于节约成本,高性价比、灵活通用性强,本系统选择DAQ系统为测试系统的主框架。
在一个实际的数据采集系统中,要用计算机来监控现场的各种参数,首先就要用传感器把各种物理信号测量出来,且转换成电信号,再经过A/D转换,送入计算机中进行分析处理,其系统结构如图3.1。
图3.1模拟输入输出通道系统
传感器:
将各种现场物理量测量出来并转换成电信号(模拟电压或电流)。
放大器:
把传感器输出的信号放大到ADC所需的量程范围。
低通滤波器:
用于降低噪声、滤去高频干扰,以增加信噪比。
多路开关:
在实际应用中,常常要对多个模拟量进行转换,而现场信号的变化通常比较缓慢,没有必要对每个通道单独配置一个A/D转换器。
这时可以采用一个多路开关,通过计算机控制,把多个现场信号分时地切换到A/D转换器上,达到共享A/D转换器以节省硬件的目的。
采样保持器:
对高速变化的信号进行A/D转换时,为了保证转换的精度,需要使用采样保持器。
周期性的采样连续信号,并在A/D转换期间保持不变。
A/D转换器:
将模拟信号转换成数字信号的芯片[12]。
3.2实验台总体要求
无论是传动试验或实验室中未知因素的探索试验还是已知因素的验证试验,都应该使试验条件与传动的实际工作条件一致,而工作条件中主要是载荷和速度。
因此试验若是在规定的载荷和速度下,传动件象工作时那样转动,即在运转情况下试验则最符合实际。
试验台应该满足下面的主要要求:
1能研究和试验比较多的影响因素,能适应试验目的和要求,尽可能做到一机多能;
2要有适宜的准确度。
试验台的载荷、速度和各种测量应有足够的准确度。
准确度应与试验目的相适应,脱离实际的过高的准确度也是不合适的;
3要尽量符合传动实验的实际工作情况,真实性好;
4要有足够的强度和刚度,使用性能好;
5要节省人力物力,经济性好。
试验台的成本应在满足试验要求下尽量降低。
试件的拆换,各个参数的测量、试验台的维护等等要省力方便,且节约动力消耗。
实验台的测控应满足以下几个条件:
1采样精度高,数据准确;
2采样范围宽,能实现不同频率下的采样;
3自动处理分析数据,得出分析结果。
能够在线实时控制转速、负载的变化,响应速度快,抗干扰能力强;
4操作方便,易于控制[13]。
3.3实验台总体设计方案
本实验台主要用于科研和教学。
主动轮由直流电机驱动,采用PWM(脉宽调速)系统实现无级调速;
从动轮经磁粉制动器实现无级加载。
光电脉冲传感器测量转速,为了得到0~5V的脉冲信号,使用放大整形电路对波形进行整改。
拉力传感器间接测量转矩,由于拉力传感器信号微小,使用变送器对其进行放大。
信号进入计算机前经过滤波电路消除干扰影响。
数据采集卡和定时计数卡把采集到的信号送计算机,并把计算机发出的控制信号经过驱动电路对电机进行闭环控制,对磁粉制动器进行开环控制。
整个过程由软件控制[14]。
总体方案图见图3.2。
图3.2系统总体方案图
3.4实验台本体结构
实验台本体结构如图3.3所示。
主动轮安装在直流电机主轴上,从动轮安装在磁粉制动器主轴上。
其中主动轮的机座设计成浮动结构,安装在滑动导轨上,与牵引钢丝绳、定滑轮、砝码一起组成带传动预紧力调节机构,改变砝码大小,即可准确地预定带传动的预紧力。
直流电动机和磁粉制动器均为悬挂支撑,当传递载荷时,作用于电机和制动器定子上的力矩迫使拉钩作用于拉力传感器(序号13),使传感器输出按一定比例变化的电信号。
转速传感器(光电传感器)分别装在主、从动轮背后的环形槽(本图未表示出)中,当带轮转动时由此产生脉冲信号[15]。
图3.3带传动实验台
3.4.1初选滚动轴承
滚动轴承的类型应根据所受载荷的大小、性质、方向,轴的转速及其工作要求进行选择。
若只受径向载荷或主要是径向载荷而轴向载荷较小,轴的转速较高,则选择深沟球轴承。
若轴承承受径向力和较大的轴向力或需要调整传动件(如锥齿轮、蜗杆蜗轮)的轴向位置,则应选择角接触球轴承或者圆锥滚子轴承。
由于圆锥滚子轴承装拆调整方便,价格较低,故应用最多。
在本设计中考虑到轴上零件的定位和固定选用的轴承类型是6210[16]。
3.4.2电动机的选择
Y系列电动机为全封闭自扇冷式笼形三项异步电动机,使按照国际电工委员会标准设计的,具有国际互换性的特点。
用于空气不含易燃、易炸或腐蚀性气体的场所。
在本设计中考虑到额定功率、