电力设备行业深度分析.docx
《电力设备行业深度分析.docx》由会员分享,可在线阅读,更多相关《电力设备行业深度分析.docx(28页珍藏版)》请在冰豆网上搜索。
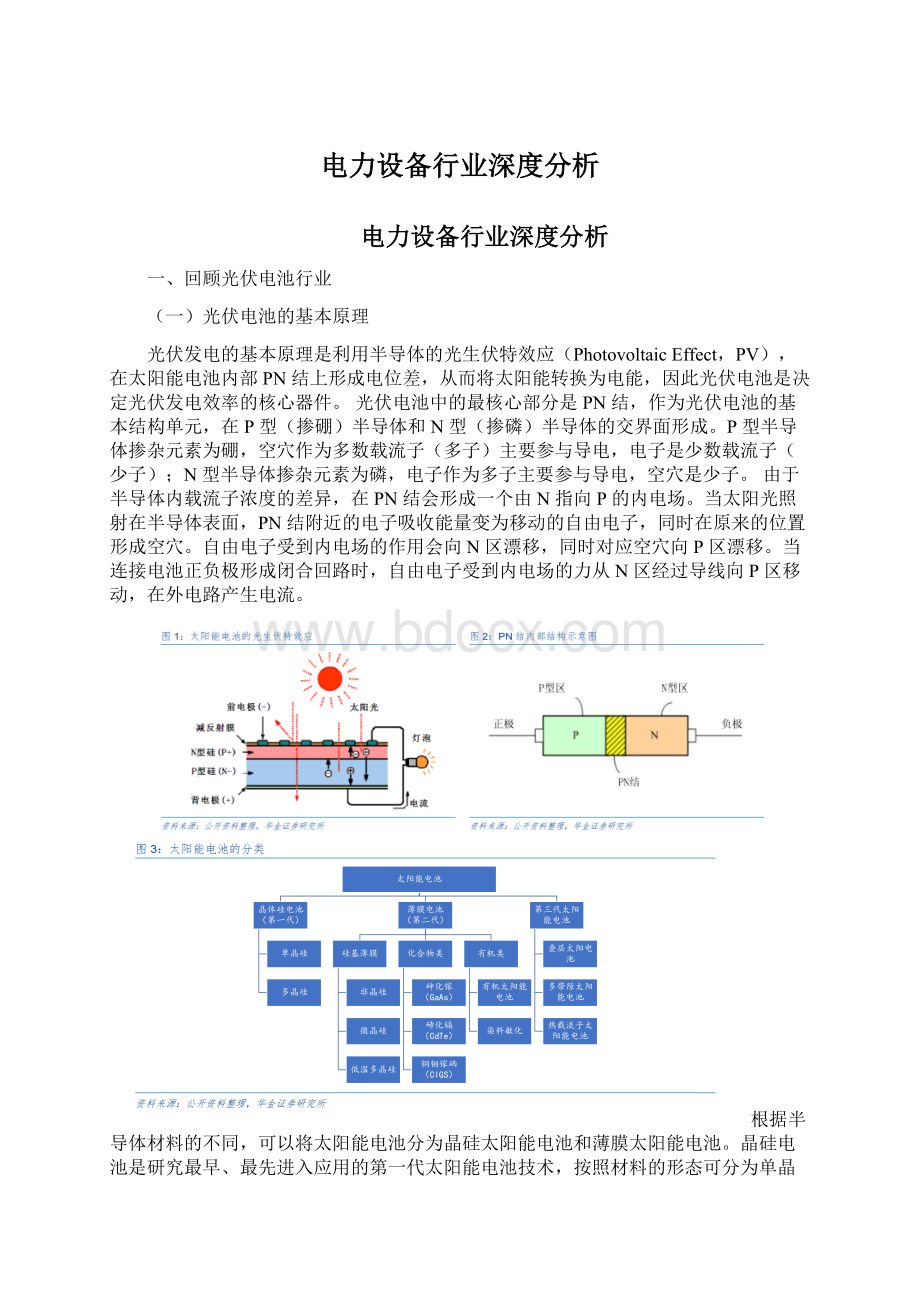
电力设备行业深度分析
电力设备行业深度分析
一、回顾光伏电池行业
(一)光伏电池的基本原理
光伏发电的基本原理是利用半导体的光生伏特效应(PhotovoltaicEffect,PV),在太阳能电池内部PN结上形成电位差,从而将太阳能转换为电能,因此光伏电池是决定光伏发电效率的核心器件。
光伏电池中的最核心部分是PN结,作为光伏电池的基本结构单元,在P型(掺硼)半导体和N型(掺磷)半导体的交界面形成。
P型半导体掺杂元素为硼,空穴作为多数载流子(多子)主要参与导电,电子是少数载流子(少子);N型半导体掺杂元素为磷,电子作为多子主要参与导电,空穴是少子。
由于半导体内载流子浓度的差异,在PN结会形成一个由N指向P的内电场。
当太阳光照射在半导体表面,PN结附近的电子吸收能量变为移动的自由电子,同时在原来的位置形成空穴。
自由电子受到内电场的作用会向N区漂移,同时对应空穴向P区漂移。
当连接电池正负极形成闭合回路时,自由电子受到内电场的力从N区经过导线向P区移动,在外电路产生电流。
根据半导体材料的不同,可以将太阳能电池分为晶硅太阳能电池和薄膜太阳能电池。
晶硅电池是研究最早、最先进入应用的第一代太阳能电池技术,按照材料的形态可分为单晶硅电池和多晶硅电池,其中单晶硅电池根据基体硅片掺杂不同又分为P型电池和N型电池。
目前应用最为广泛的单晶PERC电池即为P型单晶硅电池,而TOPCon、异质结、IBC等新型太阳能电池技术主要是指N型单晶硅电池。
(二)从太空到地面,光伏行业增长了1500倍
1839年法国科学家E.Becquerel发现液体的光生伏特效应算起,太阳能电池已经经过了180多年的漫长的发展历史。
1877年W.G.Adams和R.E.Day研究了硒(Se)的光伏效应,并制作第一片硒太阳能电池。
我国1958年正式开始研发太阳能电池,最初研发出的光伏电池主要用于空间领域。
1975年-1976年宁波、开封先后成立太阳电池厂,电池制造工艺模仿早期生产空间电池的工艺,太阳能电池的应用开始从空间降落到地面,但由于产品价格贵地面光伏市场小,20世纪70年代至20世纪90年代,行业发展几乎停滞。
直到2000年德国颁布《可再生能源法》带动欧洲地面光伏市场兴起,进而带动我国开始出现光伏产业链的配套公司,地面光伏市场才真正开始逐步发展起来。
2002年我国无锡尚德第一条10MW多晶硅电池产线宣布投产,我国光伏产业全面国产化进程正式开启。
2003年到2005年,在欧洲特别是德国市场持续拉动下,尚德和保定英利持续扩产,其他多家企业纷纷建立太阳电池生产线,使我国太阳电池的生产量迅速增长到达MW级别。
2007年我国光伏新增装机约20MW,之后十多年我国通过补贴等多种政策的扶持,到2019年我国光伏新增并网达30.1GW,较2007年增长超1500倍。
近二十年光伏电池市场主要以技术更成熟的晶硅电池为主,2008年前后由于晶硅电池上游多晶硅料出现紧缺,导致晶硅电池成本高企,薄膜电池作为第二代电池受到市场关注,市场份额一度出现回暖。
但随着2008年-2009年和2010年-2011年两轮多晶硅料价格的断崖式下跌,晶硅电池成本得以大幅下降,度电成本大幅降低,成为目前光伏电站市场的绝对主流。
而薄膜电池仅保存了特定市场的极小份额。
多晶硅价格暴跌后,多晶硅片经济性曾一度领先单晶。
但从2015年-2016年开始,以隆基为首的单晶厂商实现技术突破,大幅降低了单晶硅片单片成本。
由于单晶硅电池具备更高的转化效率,导致单晶硅片对应的单瓦成本实现反超,比多晶更低,后又出现以PERC电池为代表的高效单晶硅电池,进一步推动了单晶硅对多晶硅的替代,单晶硅电池市场份额自2016年起开始持续攀升。
(三)两轮多晶硅料的价格暴跌,奠定晶硅电池发展基础
2004年之前,绝大部分多晶硅产量用于半导体产业,太阳能级多晶硅需求仅用电子级硅的边角料即可满足,因此,多晶硅产能主要受半导体产业影响。
2003年德国光伏补贴政策出台,带动了德国太阳能光伏应用市场,从2004年起在以欧洲、日本、美国为代表的太阳能光伏应用市场的带动下,太阳能级硅的需求呈现较快速度增长。
据赛迪顾问数据,2004年全球光伏电池产量达1195MW,到2009年全球光伏电池产量增长到10400MW,增长近9倍,我国光伏电池产量2009年达3460MW,较2005年增长近25倍。
早期硅料产业被海外7家厂商垄断:
虽然光伏市场呈现了跨越式增长,但由于原料多晶硅制作技术难度大,工艺复杂,且核心技术集中在Hemlock(美国)、Wacker(德国)、Tokuyama(日本)、REC(挪威)、MEMC(美国、意大利)、Mitsubishi(日本、美国)和Sumitomo(日本)七家厂商手中。
即使厂家产量扩增,但一般多晶硅的生产线建设期在2年左右,经过后期的不断调试,完全达产则需要3-5年时间。
因此全球原料多晶硅市场一直由传统7大厂商垄断,其市场份额约占市场总额的70%以上。
2005年-2008年硅料出现价格暴涨,光伏薄膜电池实现高增长:
2005年硅料价格约100美元/kg,2006年第四季度多晶硅突破300美元/kg后,2007年底升至400美元/kg,2008年9月,多晶硅价格最高时接近500美元/kg。
在硅料价格暴涨的同时,光伏薄膜电池性价比逐渐凸显,市占率从2005年的6.5%爬升至2009年的19.5%。
自主研发硅料逐步投产,2008年-2010年硅料价格迎来第一轮暴跌:
在全球多晶硅供应不足,价格持续上涨情况下,中国掀起多晶硅投资热潮。
以洛阳中硅高科为首,自主研发的多晶硅技术成功实现产业化后,多晶硅已成为全国的投资热点。
国内多晶硅规模迅速扩大,促使国外多晶硅生产的单项技术和设备也开始优惠进入中国,技术和装备水平不断提高,多晶硅产量迅速扩大,2006年中国多晶硅产量仅387吨,2007年达到1130吨,2008年达到4210吨,2009年中国多晶硅产量达到20000吨。
截至2008年,全国共有16个省市自治区布局投资了33个多晶硅建设项目,而2008年多晶硅实际产量只有4000多吨。
截至2009年底,中国已建成原料多晶硅产能接近5万吨,大大小小的项目以及规划项目不下40个,江西、四川、江苏等省已经成为国内多晶硅项目的主要分布地区。
由于光伏产业的过度投资,导致多晶硅价格呈现“过山车式”的波动。
到2008年末多晶硅价格已经跌至每公斤150美元左右。
2009年3月,多晶硅价格最低时到过每公斤50美元,跌幅近90%。
国内有实力的产商扩产,2010年-2012年多晶硅料第二轮暴跌:
2010年国家《多晶硅行业准入条件》的出台,进一步提高了行业进入门槛,多晶硅行业在国内又呈现出几个大企业垄断的局面,保利协鑫、江西赛维LDK和洛阳中硅产能位列全国前三。
且业内仍有具有一定影响力、资金雄厚的多晶硅企业仍在不断投资。
受海外新增装机增速下滑影响,在2011年末,多晶硅料再次出现断崖式下跌,从2010年9月的近700元/kg下跌到2012年的约100元/kg,跌幅超85%。
随硅料成本的大幅下行,晶硅电池组件成本大幅下降,成为太阳能电池中的绝对主流:
晶硅电池相对于薄膜电池起步更早、效率更高。
随两轮多晶硅价格的大幅下行,多晶电池片成本快速下降,更便宜的多晶硅电池组件,大幅降低了度电成本,成为目前光伏市场绝对主流。
单晶硅电池效率持续攀升,BOS成本优势也逐渐显现:
随着组件成本的快速下降,提升电池组件转换效率摊薄BOS(除组件外系统成本)成本显得越来越重要。
2015年光伏领跑者计划启动,推动了高效率电池发展,之后三年内单晶PERC电池占比迅速提升。
到2019年,单晶电池市占率达到65%,二十年来首次超过多晶电池。
(四)金刚线切割大幅降低单晶硅片成本,奠定单晶电池发展基础
2010年至今,受益于各种降本增效技术的应用,光伏作为曾经昂贵的清洁能源现在正变得越来越廉价,目前全球大部分地区已经实现平价上网,部分地区光伏度电成本甚至低于化石燃料度电成本。
如果以2015年作为单多晶技术变革的分水岭,2011年-2015年全球光伏新增装机年复合增速为15%,2015年-2019年全球新增装机复合增速达到23%。
回顾单晶硅对多晶硅的替代,核心在于金刚线的切割技术的普及,大幅降低了单晶硅片成本。
金刚线当时主要是替代砂浆切割技术。
金刚线技术增切速、降线耗:
传统的砂浆钢线切割切速仅有0.4mm/分钟。
金刚线切割可采用1.0~1.2mm/分钟以上的大切速,切割效率大幅度提升2-3倍以上。
同时,随金刚线切片技术的发展,单片硅片耗线量也在成倍下降,由原先的3米/片已经降到现在的1.5米/片。
切割成本的下降使金刚线技术快速普及。
细线化、薄片化提高硅片产量:
金刚线基本以每年10-20um的速度在细线化,当时国内先进企业已实现母线80um金刚线切片量产,日本当时已有厂家开始小范围使用母线70um金刚线。
薄片化可大幅提高每公斤单晶出片率、提升切片产能,为单多晶硅片成本逆转提供有力支撑。
当切割硅片的方法由砂浆切割转变为金刚线切割时,按当时的120元/kg的硅料的成本计算,每一片,硅料的成本就可以每片降低0.59元。
考虑到金刚线线径逐年变细,切割速度增快,产能大幅增加,产品的折旧成本也会有所减小。
据测算,当硅片厚度由180μm下降至160μm,硅片生产的折旧成本将下降0.26元/片。
在隆基股份的单晶硅片出来之前,保利协鑫是当之无愧晶硅龙头。
2015年底协鑫多晶硅和多晶硅片产能分别达到7万吨和14GW,市占率分别高达30%和40%,均列全球第一。
对比两家公司的发展,可以明显发现自2015年金刚线切割开始普及,明显提升了单晶硅片的成本下降速度,按当时的电池片效率估算硅片的单瓦成本,2016年单晶对多晶实现了成本优势的反超。
隆基得益于领先的成本优势,借助高效PERC单晶电池的载体和领跑者计划培养的市场,在硅片价格下跌时,仍能连续6个季度保持毛利率攀升,2015年至2018年,隆基营收年复合增速达到55%,净利润年复合增速达到70%。
协鑫紧随其后完成了金刚线切割技改并推出铸锭单晶硅片,但仍未能逆转局势。
隆基凭借良好的现金流顺势扩大产能,2019年隆基硅片产能超越协鑫,成为全球硅片龙头。
二、PERC电池的提效降本之路
(一)从PERC电池的应用看新技术的导入
以前太阳能电池效率大都通过改进电池正面获得,因此当正面带来的效率提升越来越难,研发人员将目光转向了电池背面的钝化。
由于切割硅片会在其表面产生大量悬空键,引起载流子在此大量复合从而影响电池效率,钝化就是通过降低表面载流子的复合,来提升电池的效率。
钝化可通过化学钝化和场效应钝化两种方式实现。
化学钝化主要是使悬空键饱和,可以通过提供一个可使表面硅原子达到饱悬空键状态的表层,或沉积高氢介质膜,使氢填补悬空键的空穴,从而实现钝化目的。
场效应钝化是指在表面附近制造一个电场,以排斥相同极性的少数载流子,从而降低载流子的复合。
PERC电池(PassivatedEmitterandRearCell,PERC)结构从常规铝背场电池(BSF)结构演变而来,通过在BSF的背面叠加钝化层(AlOx)实现转换效率的大幅提升。
最早起源于上世纪八十年代,由澳洲新南威尔士大学的MartinGreen研究团队首次正式提出,当时即达到22.8%的实验室电池效率。
2006年PERC电池